
1576
.pdfМ – АГБ-смесь с добавлением минерального вяжущего (цемента, извести и др.);
К – АГБ-смесь с добавлением комплексного вяжущего (битумная эмульсия или вспененный битум с цементом).
Кроме того, различают щебёночные АГБ-смеси – смеси, содержащие более 35 % щебня, и песчаные АГБ-смеси – смеси, содержащие менее 35 % щебня.
Сфера применения холодной регенерации
Технологию ХР применяют на дорогах различных категорий:
-для усиления дорожной одежды на всю ширину проезжей части;
-для усиления дорожной одежды только на полосах грузового движения с устройством общего защитного слоя;
-для усиления дорожной одежды на городских дорогах, где нежелательно увеличение вертикальных отметок покрытия;
-при реконструкции автомобильных дорог, связанной с уширением проезжей части.
Ремонт покрытий способом ХРМ позволяет ликвидировать такие дефекты покрытия, как волны, наплывы, колея. При введении стабилизаторов можно перевести дорожные одежды с переходными типами покрытия (4–5 категории) в дорожные одежды облегчённого типа с усовершенствованным покрытием (3–4 категории), а последние
– в капитальные дорожные одежды с асфальтобетонным покрытием.
Технология ХР предусматривает восстановление монолитности (сплошности) пакета асфальтобетонных слоёв дорожной одежды на всю толщину или часть её (от 6 до 50 см), без разогрева асфальтобетона или АГ. Поверх регенерированного слоя обычно укладывают одноили двухслойное асфальтобетонное покрытие или устраивают поверхностную обработку.
При глубокой ХР в процессе фрезерования асфальтобетонного покрытия часто захватывают и слой дискретного материала основания. Если содержание АГ в такой смеси менее 40 % (эта граница достаточно условна), то получаемый материал принято называть укреплённым материалом (по аналогии с укреплённым крупнообломочным грунтом).
ХР асфальтобетонных покрытий выгодно отличается от традиционных способов ремонта с повторной укладкой слоёв и ГР своей экономичностью. Технология ХР по ресурсосбережению не имеет себе равных – она позволяет наиболее эффективно использовать материал старой дорожной одежды. Устранение трещин в старом покрытии на всю или большую часть глубины исключает появление отражённых трещин в новых слоях покрытия. Кроме того, проведение работ без разогрева материала наносит минимальный вред окружающей среде и органоминеральному материалу.
1.2. Зарубежный и отечественный опыт использования холодной регенерации дорожных покрытий на дороге
Зарубежный опыт холодной регенерации покрытий
11
Способы холодной регенерации слоёв дорожной одежды получили значительное развитие за рубежом. Если в 70–80-х годах ХХ в. эту технологию практиковали для ремонта второстепенных дорог, то в последнее время эти способы находят всё более широкое применение на дорогах высших категорий.
За рубежом развитие способов ХР шло по двум направлениям: совершенствование оборудования и расширение видов регенерирующих добавок.
В конце 1970-х годов, до появления машин для холодного фрезерования покрытий (холодные фрезы) в США, старую дорожную одежду разламывали на куски. Кусковой материал измельчали в передвижных молотковых дробилках за 2–3 прохода до максимального размера гранул 50 мм. Затем АГ собирали в валик, вводили восстановитель в виде катионной эмульсии нефтяных масел, перемешивали компоненты, раскладывали смесь автогрейдером, после чего смесь уплотняли. В зависимости от толщины пакета битумоминеральных слоёв разлом покрытия осуществлялся на всю толщину (если она была менее 5 см) или послойно. После формирования регенерированного слоя (с закрытием движения) сверху укладывали слой износа или усиления.
Часто размельчённый материал верхних битумоминеральных слоёв, предварительно обработанных восстановителем, смешивали с материалом нижних несвязных слоёв с добавлением маловязкого битума, цемента или шлаковых вяжущих. Перемешивание материалов и раскладку смеси осуществляли автогрейдером. Для укладки смеси использовали также погрузчик с асфальтоукладчиком. Этот способ нашёл применение в США и Нидерландах.
Появление холодных фрез дало толчок к развитию технологии ХР. В начале 80-х годов ХХ в. фирма Barber-Green в США разработала роторный профилировщик, совмещающий операции рыхления покрытия, измельчения АГ и перемешивания его с вяжущим за один проход. Эта машина регенерировала асфальтобетонные слои покрытия одновременно со слоем основания из необработанных материалов общей толщиной до 28 см.
Во второй половине 80-х годов ХХ в. широкое применение в США получает тяжелая фреза фирмы Bomag объединения AMCA International. Она выполняла те же операции, что и роторный профилировщик, но имела меньшие размеры и глубину фрезерования до 25 см. На машине мог быть установлен грохот для отделения и повторного измельчения гранул крупнее 50 мм. Органическое вяжущее в виде эмульсии вводили под кожух фрезерного барабана в количестве 2–3 % от массы укрепляемого материала через шланг из идущей впереди автоцистерны. Для распределения смеси использовали автогрейдер.
Основной проблемой в технологии ХРМ является перемешивание АГ с необработанными каменными материалами (новыми или старыми из несвязного слоя основания) и восстановителем. Чтобы улучшить качество перемешивания, в смесь следует добавлять небольшое количество воды, что облегчает обработку щебня битумом.
В США технологии ХР уделяется достаточно большое внимание. В середине 70-х годов ХХ в. была создана Ассоциация по регенерации и восстановлению асфальтобетонных покрытий (ARRA), участники которой на ежегодных семинарах обмениваются информацией о достижениях в этой отрасли. В 1993 г. был учреждён объединённый комитет № 38 по ХР, курирующий проектные, строительные и научноисследовательские работы.
12
Во Франции технология ХР получила развитие после ознакомительной поездки французских специалистов в 1981 г. в США. На следующий год был опробован способ ХРМ с применением битумной эмульсии на дороге с интенсивностью движения 5 тыс. авт./сут. Через два года наблюдений был сделан вывод, что работоспособность регенерированного слоя не хуже, чем слоя из обычного асфальтобетона.
Дальнейшее совершенствование технологии ХР во Франции связано с разработками фирмы Beugnet, которой в 1986 г. была подана заявка на способ Факир, предусматривающий регенерацию дорожной одежды с применением цемента при помощи двух машин. Был создан комплект из двух машин: ARC-Dosage – машины для хранения, дозировки и распределения цемента или других сыпучих материалов по покрытию и ARC-600 – машины для фрезерования покрытия, перемешивания АГ с цементом и водой и распределения АГБ-смеси на дороге. Машина ARC-600 могла фрезеровать покрытие на глубину до 33 см шириной 2 м. Комплект мог двигаться со скоростью 5 м/мин. Способ Факир предназначался для усиления дорожной одежды.
Опыт показал экономические преимущества технологии ХР с добавкой цемента для ремонта дорог с невысокой интенсивностью движения. Он был распространён на дороги более высоких категорий. Способом Факир в 1990 г. было регенерировано 300 тыс. м2 дорожных одежд.
На основании опыта Франции по развитию ХР можно сгруппировать разные способы с учётом типа применяемого вяжущего следующим образом: Новакол, Режешап и Ресикол – с добавлением эмульсии; Факир – с добавлением цемента; Флексосим – с добавлением комплексного вяжущего. Эти способы включают ХР: фрезерование покрытия; перемешивание АГ с вяжущим и укладку смеси, отличаясь используемым оборудованием и количеством основных машин в комплекте.
В ФРГ технологию ХР начали применять с 1986 г. с появлением стабилизёра 2000VC-R, созданного на базе холодной фрезы 2000VC фирмы Wirtgen. Стабилизёр 2000VC-R оснащён ёмкостью для воды, устройством для дозирования воды или эмульсии и устройством для распределения смеси. Машину можно было использовать для укрепления грунтов цементом, известью, битумом, битумной эмульсией. Глубина фрезерования достигала 30 см, рабочая скорость 5 м/мин. Стабилизёр мог работать в четырёх режимах: с подачей АГ в автомобили-самосвалы; с укладкой АГ в валик между гусеницами; с укладкой АГ в валик сбоку от обрабатываемой полосы; с распределением АГБ-смеси на ширину обрабатываемой полосы с предварительным уплотнением. При работе с применением эмульсии её в количестве 4–6 % подают под кожух перед вращающимся фрезерным барабаном. Глубина фрезерования асфальтобетона в этом случае достигает 10 см.
Способ ХР с использованием цемента применяли в основном для ремонта дорог с тонким слоем покрытия с захватом несвязного материала основания. Цемент в количестве 4 % от массы обрабатываемого материала распределяли по покрытию специальным цементораспределителем. Глубину фрезерования можно было доводить до
30 см.
В 1993 г. фирма Wirtgen на базе ремиксера создала смеситель-укладчик CR4500, позволяющий обрабатывать полосу шириной от 3 до 4,5 м. Смеситель-укладчик CR4500 оборудован емкостями для воды, эмульсии и цемента, приёмным бункером для нового минерального материала, фрезерным барабаном, смесителем цемента с водой для получения теста, двухвальным смесителем АГ с вяжущим и несвязным материалом и распределительно-уплотняющим рабочим органом. Сначала обычная
13
дорожная фреза фрезерует покрытие. АГ раскладывают автогрейдером и прикатывают для возможного пропуска построечного транспорта. Смеситель-укладчик взрыхляет АГ, перемешивает его с остальными компонентами, распределяет смесь на ширину регенерируемой полосы и предварительно уплотняет слой. Запасы рабочих материалов непрерывно пополняются из емкостей специального автомобиля, сцепленного с основной машиной. При таком способе исключается необходимость распределения цемента по покрытию перед фрезерованием; смесь по однородности не уступает смесям, полученным на стационарных смесительных установках.
Учитывая американский опыт создания и использования стабилизёров, фирма Wirtgen выпустила в 1994 г. машину на колёсном ходу WR2500, которая может осуществлять укрепление грунтов цементом и известью, измельчение старой дорожной одежды с увлажнением смеси, а также регенерировать дорожную одежду с добавлением эмульсии, вспененного битума, цемента и комплексного вяжущего. Ширина обработки 2,5 м. В зависимости от глубины фрезерования геометрия рабочей камеры может изменяться, что позволяет достичь требуемой производительности без перегрузки машины. WR2500 имеет приспособление для измельчения крупных кусков асфальтобетона. После прохода стабилизёра автогрейдер планирует слой смеси.
В 1994 г. была разработана вспомогательная установка WM400 для приготовления цементного теста (суспензатор), перемещаемая стабилизёром. Она позволила исключить операцию распределения цемента по поверхности регенерируемого покрытия. Несколько лет назад появилась новая модификация стабилизёра – WR2500К. Он отличается встроенным приспособлением, позволяющим распределять минеральное вяжущее непосредственно перед фрезерным барабаном.
Фирма Wirtgen разработала мобильную установку КМА 150 для приготовления холодных смесей различного типа. С использованием данной установки реализуется способ ХР в установке.
Из других стран, освоивших технологию ХРМ с применением битумной эмульсии или цемента, следует отметить Англию, использовавшую грунтовые фрезы МРН-100 и МРН-60 фирмы Bomag. В 1984 г. в Англии было регенерировано 4 тыс.м2 покрытия, а в 1988 г. уже 250 тыс.м2 на 30 объектах. Причем чаще применялся способ ХРМ с захватом слоя несвязного основания.
В Австралии фирмой Road Recycters разработана машина массой 35 т, которая выполняет все операции по способу ХР с использованием эмульсии.
Стабилизёр WR2500 с 1996 г. используется в разных странах (Бельгии, Бразилии, Испании и др.). В Бельгии на одной из дорог пакет слоёв старого асфальтобетонного покрытия измельчили с превращением его в слои основания без добавления вяжущего (способ гранулирования). Был также укреплён слой старого основания с примене-
нием CaCl2.
В Испании при ремонте кольцевой дороги С-612 между городами Мединой де Риосеко и Виллафрегос регенерацию осуществляли на глубину 15 см с использованием комплексного вяжущего, включающего цемент, битумную эмульсию и воду в следующей пропорции: 2, 3 и 1 % соответственно. Дорога сразу была открыта для движения, а защитный слой асфальтобетона толщиной 5 см был уложен только на 21-й день.
14
ВНорвегии крупнейшая дорожно-строительная фирма Nodest Vei в 1996–97 гг. произвела работы с использованием стабилизёра на 400 тыс.м2; 25 % этого объёма было выполнено с применением вспененного битума.
ВГолландии, имеющей большой опыт ХР, при реконструкции одной из дорог применили следующую технологию. Стабилизёром дорожную одежду отфрезеровали на глубину 25 см, а измельчённый материал экскаватором переместили на обочину. На обнажённое земляное полотно положили геотекстиль и сверху уложили слой песка толщиной 10 см. Поверх песчаного слоя распределили удалённый материал старой дорожной одежды, спланировали автогрейдером и укрепили цементом (3 %) и битумной эмульсией (3 %). По регенерированному слою выполнили поверхностную обработку, а затем уложили слой асфальтобетонной смеси. По сравнению с исполь-
зованием стационарных установок затраты были сокращены на |
45 %. |
Приведённые примеры показывают возможность реализации самых разнообразных схем ХР с применением стабилизёров. Это позволяет технологу выбрать наиболее экономичный способ производства работ применительно к конкретным условиям.
Развитие технологии ХР за рубежом идёт также по пути поиска различных вяжущих и добавок.
В США в качестве вяжущего часто используют медленно- и среднераспадающиеся битумные эмульсии типа CMS, медленногустеющие разжиженные битумы типа МС800 или цемент. Применение цемента или извести в количестве 1–3 % в сочетании с битумной эмульсией даёт положительный результат. Повышается прочность АГБ на ранней стадии формирования регенерированного слоя, что важно для его сопротивления циклическим нагрузкам в первое время после открытия движения.
Во Франции, наряду с эмульсиями Комподил СКРЕГ и Режешап, включающими маловязкий битум, фирма Deucol Emulsiontechnik GmbH производит эмульсию Режестаб, на основе специального битума и ароматических масел, для восстановления свойств старого битума в АГ.
Фирма Colas в 1986 г. предложила комбинированное вяжущее «Стабиколь». Оно представляет собой смесь гидравлического вяжущего с битумной эмульсией. Различают 3 класса такого вяжущего: 50, 90, 120, содержащих соответственно 21,7, 33,4 и 40 % битума; 43,5, 37 и 33,3 % цемента; остальное вода. Выбор вяжущего зависит от поставленной задачи: восстановить свойства постаревшего битума или обогатить битумом регенерируемый слой, включающий АГ и песчано-гравийную смесь, обработанную цементом, или повысить прочность необработанного материала основания без потери эластичности.
Вспененные битумы для ХР впервые были применены в США. Их использование менее распространено, чем эмульсий. Более широкому использованию вспененных битумов для ХР способствовало появление стабилизёров, оснащённых специальным устройством для вспенивания битума. Важным достоинством способа ХР с применением вспененного битума является возможность немедленного открытия дороги для движения транспортных средств.
Интерес представляет добавление в укрепляемую смесь синтетических волокон в сочетании с эмульсией или цементом для повышения сопротивляемости регенерированного слоя циклическим воздействиям транспортных средств и мороза.
15
Одно из последних направлений – применение реактивных эмульсий. В период устройства слоя вязкость эмульсионного битума низкая; затем происходит реакция окисления и полимеризации и вязкость битума резко возрастает.
Отечественный опыт холодной регенерации покрытий
Отечественный опыт по технологии ХР невелик и до 1997 г. не выходил за рамки опытных работ. Большинство публикаций по этому вопросу связано с работами Г.С.
Бахраха [3–6, 8, 9].
Первый отечественный технический документ «Руководство по восстановлению асфальтобетонных покрытий и оснований автомобильных дорог способами холодной регенерации», разработанный Г.С. Бахрахом в ГП РосдорНИИ, утверждён ФДС России в 1997 г. Новая технология проведения ремонтных работ была реализована при реконструкции головного участка автомагистрали М1 «Беларусь».
На начальной стадии исследований основная идея заключалась в попытках возвращения пленкам старого битума клеящих свойств при температуре воздуха 10–20 ºС.
Вкачестве пластификатора использовалось отработанное моторное масло; наилучшие результаты были получены при его дозировке 0,3–0,6 % от массы АГ.
В1991 г. было отремонтировано два участка асфальтобетонного покрытия с введением цемента. Первый участок протяжённостью 260 м построили на дороге IV категории в Московской обл. На асфальтобетонном покрытии, лежащем на плотном слое песчано-щебёночной смеси толщиной 25 см, наблюдалась сплошная сетка трещин. Перед фрезерованием по покрытию вручную распределяли цемент М400 из расчета 2,5 % от массы регенерируемого слоя. Фрезерование осуществляли на глубину 15 см с захватом 6–7 см слоя основания при скорости движения фрезы 5 м/мин. Оптимальная влажность смеси составила 7 %. Уплотнение производили пневмокатком массой 10 т и трёхвальцовым катком массой 12 т. Движение по участку было открыто сразу после уплотнения слоя. Учитывая жаркую погоду, в течение недели участок периодически поливали. Через месяц была выполнена подгрунтовка поверхности жидким битумом, а на следующий день уложено асфальтобетонное покрытие.
Второй участок протяжённостью 76 м был отремонтирован в Москве у выхода из станции метро «Речной вокзал» на полосе остановки автобусов. На асфальтобетонном покрытии толщиной 28 см имелась колейность глубиной до 8–12 см и поперечные трещины с шагом около 7 м и шириной раскрытия 2–7 см. Сначала фрезой удалили слой асфальтобетона толщиной 5–7 см с использованием АГ в другом месте. Цемент М400 распределяли вручную в количестве 6–8 %, глубина регенерации составила 10 см. Уплотнение проводили комбинированным катком фирмы ABG массой 18 т. Движение транспорта было открыто сразу после уплотнения. Через 20 дней была сделана подгрунтовка, а ещё через месяц уложили слой песчаного асфальтобетона.
Наиболее значимый проект по применению технологии ХР был реализован в 1996– 97 гг. на головном участке автомагистрали М1 «Беларусь». Проект финансировался Мировым банком реконструкции и развития (МБРР).
Исследование свойств АГБ и обследование участков автомагистрали М1 «Беларусь» выполнены под руководством Г.С. Бахраха и подробно изложены в обзорах [7–9].
В результате обследования было установлено:
16
1.Приведённый модуль упругости дорожной конструкции на крайних полосах составлял 343+17 и 315+21 МПа, на остальных 450+30 МПа. Требуемый модуль составлял 315 МПа.
2.Сопоставление двух смежных участков на 33 и 34 км со слоем из АГБ и пористого асфальтобетона показало, что АГБ имеет более высокое значение модуля упругости
400+40 МПа, чем пористый асфальтобетон |
382+12 МПа. |
3.Сквозные температурные трещины появились на асфальтобетоне уже после первой зимы. В феврале-марте 1999 г. на участке 17–31 км среднее расстояние между трещинами составило 30-60м, на участке 32–38 км – 50–90 м. Меньшее количество трещин на втором участке объясняется использованием в асфальтобетоне битума, модифицированного 3 % ДСТ. На 38–42 км, где в основании лежал цементобетон, расстояние между поперечными трещинами было 6–12 м. Следовательно, слой из АГБ с цементом не является трещинопрерывающим.
4.Количество отражённых трещин на участках с основанием, усиленным по способу ХР, значительно меньше, чем на участках, усиленных по традиционной технологии.
5.АГБ имеет достаточно высокую устойчивость к колееобразованию.
6.По АГБ-слою с применением цемента или комплексного вяжущего до наступления осеннего дождливого периода необходимо устраивать защитный слой из плотного асфальтобетона.
Для окончательных выводов об эксплуатационных свойствах АГБ-слоёв требуются более длительные наблюдения.
Тем не менее отечественный опыт свидетельствует о преимуществах технологии ХР для ремонта асфальтобетонного покрытия по сравнению с традиционной технологией укладки на старое покрытие нового слоя.
17
1.3.Преимущества и недостатки асфальтогранулобетонов
сразличным типом структур
Анализ отечественных и зарубежных исследований структуры АГБ и ее влияние на технологические, физико-механические и эксплуатационные свойства этого материала позволил установить преимущества и недостатки различных типов структур, образующихся в АГБ [3].
1.Физико-механические свойства АГБ типа А (без добавления вяжущего) определяются структурно-механическими свойствами АГ. Вследствие пониженной уплотняемости смеси, АГБ типа А имеет высокую пористость (8–14 %) и низкую прочность. Преимуществом АГБ такого типа является возможность открытия движения транспортных средств сразу после уплотнения регенерированного слоя.
2.Относительно невысокая прочность и её зависимость от температуры, пластичность, способность к ползучести – основные недостатки, присущие материалу с коагуляционными микроструктурными связями. Эти свойства характерны для АГБ с вяжущим в виде маловязкого битума. Тем не менее, как и в первом случае, движение транспорта может быть открыто сразу после уплотнения слоя АГБ на жидком битуме.
3.В АГБ типа М вяжущим является цемент. Основной вклад в прочность АГБ этого типа вносят жесткие кристаллизационные связи, образуемые цементным камнем. При содержании цемента менее 5 % раздвижка гранул АГБ может быть незначительной. В этом случае увеличивается доля коагуляционных межгранулярных контактов. Если битум в АГ не слишком состарился, то некоторую эластичность АГБ могут придавать коагуляционные связи внутри АГ.
Прочностные свойства АГБ типа М с матрицей из цементного раствора существенно выше, чем у АГБ с органическим вяжущим. Причём прочность в этом случае возрастает со временем и при увеличении содержания цемента. К недостаткам этих материалов следует отнести низкую морозостойкость, отсутствие механизма залечивания микротрещин. Движение по регенерированному слою в течение первых 1–2 суток твердения запрещено. После набора минимально требуемой прочности и устройства подгрунтовки желательно сразу уложить слой (слои) покрытия.
4.Процесс структурообразования АГБ типа К на комплексном вяжущем (цемент + эмульсия) близок к процессам структурообразования цементоасфальтобетона и крупнообломочного грунта, укрепленного комплексным вяжущим. Контакт между гранулами в АГБ в этом случае осуществляется через пленки из эмульгированного битума или через продукты гидратации цемента. Свойства АГБ типа К зависят от баланса коагуляционных и кристаллизационных связей и занимают промежуточное поло-
18
жение между свойствами АГБ типов Э и М. Недостаток материала – движение по регенерированному слою следует открывать после достижения им минимальной несущей способности; короткий период существования тиксотропной коагуляционной структуры минерального вяжущего (1,5– 2 ч) сокращает технологический разрыв между перемешиванием и уплотнением АГБ-смеси.
Таким образом, тип структуры и свойства АГБ зависят в основном от структуры и свойств применяемого вяжущего материала.
На рис. 1.1 представлена неполная структурная схема применения регенерирующих добавок при холодной регенерации асфальтобетонов на дороге.
Наиболее перспективным технологическим решением является использование комплексных добавок (разжиженный битум + медленнотвердеющие минеральные вяжущие) для получения асфальтогранулобетона типа К.
Контрольные вопросы
1.В чем заключается способ холодной регенерации асфальтобетонных покрытий?
2.Какими двумя способами осуществляют регенерацию старого асфальтобетона?
3.В чем заключается преимущество регенерации асфальтобетонных покрытий по сравнению с традиционной технологией ремонта?
4.Какие типы асфальтобетонных смесей приготавливают на дороге дорожной фрезой?
5.В чем заключается преимущество холодной регенерации асфальтобетонных покрытий по сравнению с горячей технологией?
6.По каким двум направлениям шло развитие способов холодной регенерации?
19
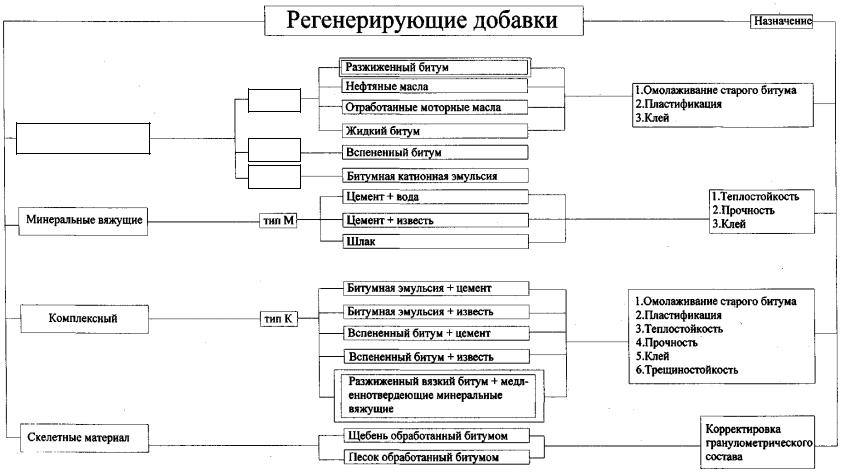
Тип Б
Органические
Тип В
Тип Э
Минеральные вяжущие |
|
Тип М |
|
|
|
|
|
|
Комплексные |
|
|
|
Тип К |
|
|
|
|
|
|
|
|
|
Разжиженный вязкий битум + мед- |
|
|
|
леннотвердеющие минеральные |
|
|
|
вяжущие |
|
|
|
|
|
Скелетные материалы |
|
Щебень, обработанный битумом |
|
|
|
|
|
|
|
|
|
|
|
Песок, обработанный битумом |
|
|
|
|
|
Рис. 1.1. Структурная схема применения добавок при холодной регенерации асфальтобетона на дороге
20