
- •ОБЩИЕ ПОЛОЖЕНИЯ И КЛАССИФИКАЦИЯ БЕТОНОВ
- •ЗАДАНИЕ НА ПОДБОР СОСТАВА БЕТОНА
- •ТРЕБОВАНИЯ К СЫРЬЕВЫМ МАТЕРИАЛАМ
- •ХАРАКТЕРИСТИКА БЕТОННЫХ СМЕСЕЙ
- •Лабораторная работа № 3
- •Лабораторная работа № 4
- •ВЛИЯНИЕ ПОВТОРНОГО ВИБРОУПЛОТНЕНИЯ СМЕСИ НА СВОЙСТВА ТЯЖЕЛОГО БЕТОНА
- •Лабораторная работа № 5
- •ВЛИЯНИЕ ВИДА И РАСХОДА ПЛАСТИФИЦИРУЮЩИХ ДОБАВОК НА СВОЙСТВА ТЯЖЕЛОГО БЕТОНА
- •Контрольные вопросы
- •Библиографический список
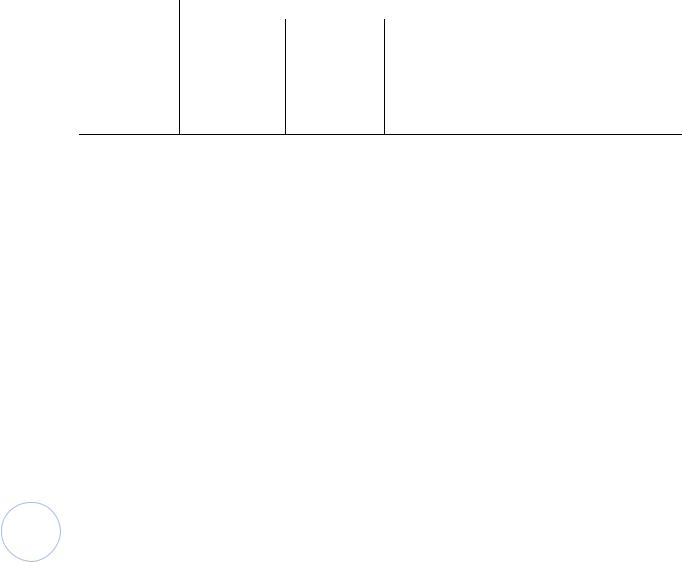
бень). Для В50 и выше – особо высококачественный щебень из не затронутых выветриванием пробных изверженных пород с шероховатой поверхностью излома при дроблении (мелкокристаллические граниты и т.п.).
Таблица 4
Наибольшая крупность щебня (гравия), применяемого при производстве железобетонных конструкций
|
|
Вид конструкций |
|
|
|
Допускаемая наибольшая круп- |
|
|||||
|
|
|
|
|
ность заполнителя НКЩ, мм |
|
||||||
|
|
|
|
|
|
|
|
|||||
|
Ребристые конструкции, многопустотные панели, |
|
|
|
|
|
|
|||||
|
элементы тонкостенных оболочек, балки и другие |
|
10 |
|
|
|
||||||
|
изделия с размерами ребер, стенок, полок до 25 мм |
|
|
|
|
|||||||
|
|
|
|
|
|
|
||||||
|
или с многорядной арматурой |
|
|
|
|
|
|
|
|
|
|
|
|
То же, армированные с наименьшими размерами |
|
|
|
|
|
|
|||||
|
ребер, стенок, полок от 25 до 80 мм, с расстоянием |
|
20 |
|
|
|
||||||
|
между стержнями арматуры более 15 мм |
|
|
|
|
|
|
|
|
|||
|
Крупноразмерные изделия (колонны, балки, риге- |
|
|
|
|
|
|
|||||
|
ли, фундаментные плиты, блоки и др.) с расстоя- |
|
40 |
|
|
|
||||||
|
нием между стержнями арматуры более 30 мм |
|
|
|
|
|
|
|
||||
|
|
|
|
А |
|
|
|
|
Таблица 5 |
|||
|
Содержание фракций крупного заполнителяИв щебеночной смеси |
|||||||||||
|
|
Соотношения между фракциями, % при размере фракций, мм |
|
|
||||||||
|
НКЩ, мм |
|
|
Д |
|
|
|
|
|
|||
5 – 10 |
10 – 20 |
20 – 40 |
|
40 – 80 |
80 – 120 |
|
||||||
|
10 |
100 |
– |
|
|
– |
|
– |
– |
|
|
|
|
20 |
25 – 40 |
60 – 75 |
|
– |
|
– |
– |
|
|
||
|
40 |
15 – 25 |
20 – 35 |
40 – 65 |
|
– |
– |
|
|
|||
|
80 |
10 – 20 |
15 – 25 |
20 – 35 |
|
35 – 55 |
– |
|
|
|||
|
|
|
б |
|
|
|
|
|
|
|||
|
120 |
5 – 10 |
10 – 20 |
15 – 25 |
|
20 – 30 |
25 – 35 |
|
||||
|
Для приготовленияибетонной смеси и поливки |
|
бетона в |
|
|
|
||||||
|
|
процессе твер- |
||||||||||
дения допускается применять воду из хозяйственного водопровода, рек |
или естественных водоемов, имеющую водородный показатель рН не ме- |
|
нее четырех и содержащуюС |
минеральные соли не более 5 г/л, в том числе |
сульфатов не более 2,7 г/л. Болотные и сточные воды применять без очистки запрещено. Морскую воду с содержанием солей не более 3,4% разрешается применять в том случае, если допускается появление высолов на поверхности бетона [8].
ХАРАКТЕРИСТИКА БЕТОННЫХ СМЕСЕЙ
Бетонные смеси характеризуются следующими технологическими показателями качества: удобоукладываемостью, средней плотностью, расслаиваемостью, пористостью, температурой, сохраняемостью свойств во времени и объемом вовлеченного воздуха.
9
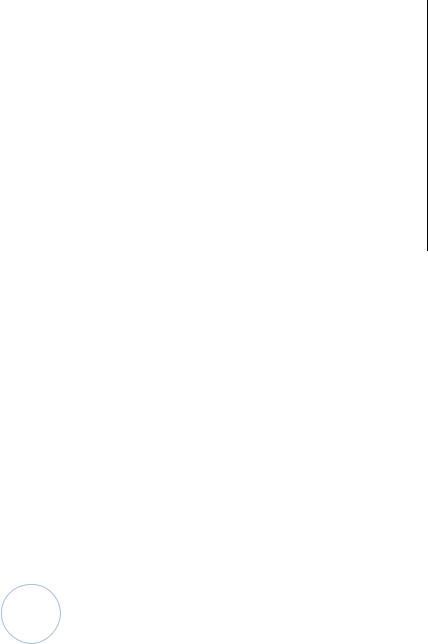
Удобоукладываемость характеризуется подвижностью или жесткостью смеси. Классификация бетонных смесей в зависимости от их удобоукладываемости приведена в табл. 6.
Таблица 6
Классификация бетонных смесей в зависимости от их удобоукладываемости
Марка по удобо- |
|
Норма удобоукладываемости по показателю |
Допускаемые |
||||||||
|
|
|
|
|
подвижности, см |
отклонения, |
|||||
укладываемости |
|
жесткости, с |
|
|
|||||||
|
осадка конуса |
|
расплыв конуса |
с (см) |
|||||||
|
|
|
|
|
|||||||
|
|
|
|
Жесткие смеси |
|
|
|
||||
Ж5 |
|
51 и более |
|
|
– |
|
|
|
– |
± 3 |
|
Ж4 |
|
31 – 50 |
|
|
|
– |
|
|
|
– |
± 3 |
Ж3 |
|
21 – 30 |
|
|
|
– |
|
|
|
– |
± 3 |
Ж2 |
|
11 – 20 |
|
|
|
– |
|
|
|
– |
± 3 |
Ж1 |
|
5 – 10 |
|
|
|
– |
|
|
|
– |
± 2 |
|
|
|
|
Подвижные смеси |
|
|
|||||
П1 |
|
– |
|
|
1 |
– 4 |
Д |
– |
±1 |
||
|
|
|
|
|
|
||||||
П2 |
|
– |
|
|
5 |
– 9 |
|
|
|
– |
± 1 |
|
|
|
|
|
А |
И– |
|
||||
П3 |
|
– |
|
|
10 |
– 15 |
|
|
± 2 |
||
П4 |
|
– |
|
|
16 |
– 20 |
|
|
|
– |
± 2 |
П5 |
|
– |
|
б |
|
|
|
– |
± 2 |
||
|
|
|
21 и более |
|
|||||||
Р1 |
|
– |
|
|
|
– |
|
|
34 и менее |
± 3 |
|
Р2 |
|
и |
|
|
– |
|
|
35 – 41 |
± 3 |
||
|
– |
|
|
|
|
|
|||||
Р3 |
|
– |
|
|
|
– |
|
|
42 – 48 |
± 3 |
|
Р4 |
|
С |
|
|
|
– |
|
|
49 – 55 |
± 3 |
|
|
– |
|
|
|
|
|
|||||
Р5 |
|
– |
|
|
|
– |
|
|
56 – 62 |
± 3 |
|
Р6 |
|
– |
|
|
|
– |
|
|
63 и более |
± 3 |
Подвижность (жесткость) бетонной смеси |
Таблица 7 |
||
|
|
||
в зависимости от вида бетонной конструкции |
|
|
|
|
|
|
|
Конструкция |
Подвижность (жесткость) |
||
ОК, см |
Ж, с |
|
|
|
|
||
1 |
2 |
3 |
|
Сборные железобетонные на жестких смесях с немед- |
0 |
20 – 10 |
|
ленной распалубкой |
|
||
|
|
|
|
Подготовка под фундаменты и полы, дорожные и аэро- |
1 – 2 |
10 – 6 |
|
дромные покрытия |
|
||
|
|
|
|
Массивные неармированные и с редко расположенной |
2 – 4 |
6 – 4 |
|
арматурой |
|
||
|
|
|
|
Каркасные железобетонные (плиты, балки, колонны) |
4 – 8 |
4 и менее |
|
10

Окончание табл. 7
|
1 |
|
2 |
3 |
|
Железобетонные с |
густо расположенной |
арматурой |
8 – 10 |
Менее 2 |
|
(бункеры, силосы и др.) |
|
||||
|
|
|
|||
Элементы кассетные |
и для объемно-сборного домо- |
12 – 18 |
– |
||
строения |
|
|
|||
|
|
|
|
||
Буронабивные сваи, шахтные стволы, конструкции, |
|
|
|||
сильно насыщенные арматурой и закладными деталями |
20 – 24 |
– |
|||
(стены АЭС, швы и др.), препятствующими укладке сме- |
|||||
|
|
||||
си |
|
|
|
|
Подвижность или жесткость бетонной смеси устанавливают для вибрируемых смесей по табл. 7 и уточняют в зависимости от характера и размеров конструкций, степени армирования, способа транспортировки и интенсивности уплотнения смеси [14].
Лабораторная работаИ№ 1
ПОДБОР СОСТАВА ТЯЖЕЛОГОД БЕТОНА
Цель работы – изучить методику подбора составов тяжелого бетона на сырьевых материалах различного качества и подвиж-
•цилиндры мерные вместимостьюб: 250 мл и 1000 мл по ГОСТ 1770;
•весы по ГОСТ 29329или ГОСТ 24104–2001;
•нормальный ли увел ченный конус и загрузочная воронка;
•металлическаяСл нейка по ГОСТ 427;
•кельма типа КБ по ГОСТ 9533 и секундомер;
•гладкий жесткий лист размерами не менее 700х700 мм из водонепроницаемого материала (металл, пластмасса и т.п.);
•прямой металлический гладкий стержень диаметром 16 мм, длиной 600 мм с округленными концами.
•формы с размером ребра 100 мм и вибростол;
•штангенциркуль по ГОСТ 166;
•гидравлический пресс с максимальным усилием 50 – 500 кН (5 – 50 тс) по ГОСТ 28840.ности бетоннойАсмеси.Приборы и оборудование
Порядок выполнения работы
1)расчет состава тяжелого бетона на 1 м3 смеси и на 7 л;
2)определение подвижности или жесткости смеси;
3)определение фактической плотности бетонной смеси;
4)формовка шести образцов с размером ребра 100 мм;
11

5)определение размера образцов, их массы, плотности и испытание на предел прочности при сжатии.
Исходные данные для расчета и подбора состава тяжелого бетона
задаются преподавателем.
1.Средняя расчетная прочность бетона к определенному возрасту Rб.
2.Подвижность или жесткость бетонной смеси ОК (Ж).
3.Класс прочности или марка цемента.
4.Вид и наибольшая крупность зерен крупного заполнителя НКЩ.
5.Насыпная и истинная плотности заполнителей.
6.Модуль крупности применяемого песка Мкр.
7.Условия эксплуатации сооружения, позволяющие выбрать вид применяемого цемента.
Взадании могут быть включены следующие дополнительные данные:
1.Длительность и режимы твердения бетонаИ, требуемая доля марочной прочности к заданному сроку (распалубочная, передаточная прочности).
2.Марки бетона по морозостойкостиД, водонепроницаемости, водопоглощению, влажности, истираемости и т.д.
3.Ограничения по составу бетонаАи применяемым материалам.
1.Расчет состава тяжелого бетона
Воснову способа положеныбтри функциональные и две экспериментально установленные закономерности [1].
Принцип абсолютныхио ъемов заключается в том, что сумма абсо-пор или пустот:С
Щ / ρщ + П / ρп + Ц / ρц + В ≈ 1. |
(1) |
Принцип фаз состоит в том, что каркасом бетона является крупный заполнитель, пространство между зернами которого, заполняет цементнопесчаный раствор, несколько раздвигающий при этом зерна каркаса:
Щ Vмз |
= |
Ц |
α+ |
П |
+ В. |
(2) |
|
|
|||||
ρщ |
|
ρц |
ρп |
|
Закон прочности бетона заключается в том, что прочность бетона зависит от трех основных факторов: активности цемента, водоцементного отношения и качества заполнителей, связанных линейной зависимостью:
12

R |
|
A R |
Ц |
− 0,5 |
|
при |
В |
|
0,4, |
(3) |
|||
= |
|
В |
|
|
≥ |
||||||||
Ц |
|||||||||||||
б |
|
ц |
|
|
|
|
|
|
|
|
|||
Rб |
|
A1 Rц |
Ц |
+ 0,5 |
|
при |
|
В |
|
0,4. |
|
||
= |
|
В |
|
|
|
< |
(4) |
||||||
|
Ц |
||||||||||||
|
|
|
|
|
|
|
|
|
|
|
Расчет состава ведут на 1000 л уплотненной бетонной смеси, изготовленной на высушенных заполнителях с отсевом от мелкого заполнителя зерен крупнее 5 мм, а от крупного – мельче 5 мм с разделением крупного заполнителя на отдельные фракции. Состав на таких заполнителях называют номинальным. Его определяют на трех лабораторных составах: начальном и двух дополнительных.
1. Водоцементное отношение определяют по формулам, полученным |
||||||||||||||||
путем преобразования формул (3) и (4): |
И |
|
|
|||||||||||||
|
|
|
|
|
|
|
||||||||||
|
В |
= |
|
|
|
A Rц |
|
|
|
при |
В |
|
≥ |
0,4, |
(5) |
|
|
Ц |
R |
|
+ |
0,5 A |
R |
Ц |
|||||||||
|
|
|
|
|
|
|
||||||||||
|
|
|
б |
|
|
|
ц |
|
|
|
|
|
|
|
||
|
|
|
|
|
|
А |
|
|
|
|
|
|
|
|||
|
В |
= |
|
|
|
A1 Rц |
|
|
|
при |
|
В |
< |
0,4, |
(6) |
|
|
Ц |
|
R |
б |
|
ДR |
|
Ц |
|
|
|
|||||
|
|
|
− |
0,5 A |
|
|
|
|
||||||||
|
|
|
|
|
|
|
1 |
ц |
|
|
|
|
|
|
|
где А и А1 – коэфф ц енты, уч тывающие качество заполнителей, которые |
||||
принимают по табл. 8; Rц – класс прочности цемента, МПа; Rб – проекти- |
||||
руемая прочность бетона, МПа. |
|
|
|
|
и |
|
Таблица 8 |
||
Значение коэффициентов А и А1 в зависимости от качества материалов |
||||
|
|
|
|
|
Характеристика исходных материалов для бетона |
А |
|
А1 |
|
С |
|
|
|
|
Высококачественные (щебень из плотных и прочных горных по- |
|
|
|
|
род, песок оптимальной крупности, отвечающий соответствующим |
0,65 |
|
0,43 |
|
стандартам, портландцемент высокой активности без добавок или с |
|
|
||
|
|
|
|
|
минимальным количеством добавки, заполнители промыты) |
|
|
|
|
Рядовые (гравий, соответствующий техническим требованиям |
|
|
|
|
ГОСТ, портландцементы средней активности, шлакопортландце- |
0,6 |
|
0,4 |
|
менты высокой активности) |
|
|
|
|
Пониженного качества (крупный заполнитель пониженного |
0,55 |
|
0,37 |
|
качества, мелкий песок, низкоактивные цементы) |
|
|
||
|
|
|
|
|
Полученные значения В/Ц сверяют с граничными условиями по В/Ц, |
||||
отбрасывая не соответствующий условию результат. |
|
|
|
|
13
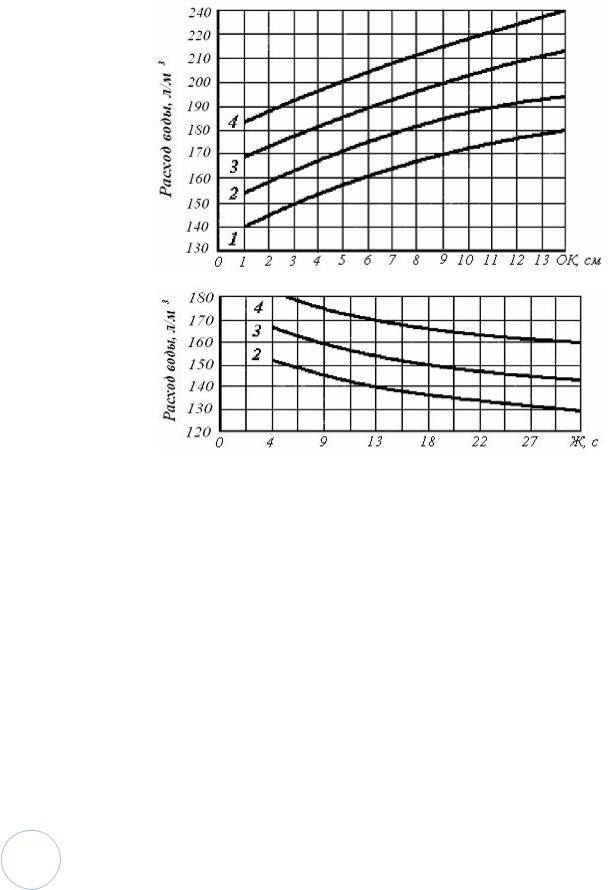
2. Расход воды для получения требуемой подвижности бетонной смеси определяют в зависимости от заданной ее подвижности (жесткости), вида и наибольшей крупности заполнителя с помощью рис. 1 или табл. 9 с учетом соответствующих поправок, указанных в примечании к рис. 1 или табл. 9.
а
|
|
|
|
|
И |
|
|
|
|
Д |
|
б |
|
|
А |
|
|
|
|
б |
|
|
|
|
и |
|
|
|
|
|
С |
|
|
|
|
Рис. 1. Водопотребность бетонной смеси, приготовленной на гравии с наибольшей крупностью:
а – пластичные бетонные смеси; б – жесткие бетонные смеси;
1 – 80 мм; 2 – 40 мм; 3 – 20 мм; 4 – 10 мм
Примечания: 1. Зависимости получены для бетона на гравии,
песке средней крупности с водопотребностью 7% и при расходе портландцемента до 400 кг/м3 бетона. 2. Если применяют мелкий песок с водопотребностью свыше 7%, то расход воды увеличивают на 5 л на каждый процент увеличения водопотребности; при применении крупного песка с водопотребностью ниже 7% расход воды уменьшают на 5 л на каждый процент уменьшения водопотребности. 3. При применении щебня расход воды увеличивают на 10 л. 4. При использовании пуццолановых цементов расход воды увеличивают на 15 – 20 л. 5. При перерасходе цемента свыше 400 кг расход воды увеличивают на 10 л на каждые 100 кг цемента.
14
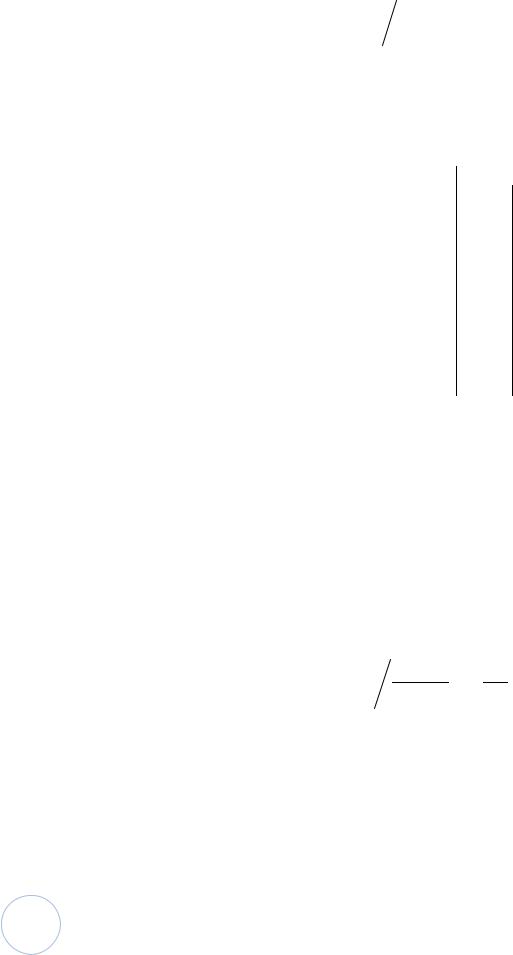
3. Расход цемента определяют по формуле
|
|
|
|
|
Ц = |
В |
|
В |
, |
|
|
|
|
(7) |
||
|
|
|
|
|
|
|
|
|
|
|||||||
|
|
|
|
|
|
|
|
|
Ц |
|
|
|
|
|
|
|
где В – расход воды, л/м3. |
|
|
|
|
|
|
|
|
Таблица 9 |
|||||||
|
|
|
|
Водопотребность бетонной смеси |
|
|
|
|||||||||
|
|
|
|
|
|
|
|
|
||||||||
|
|
|
|
|
|
|
|
|
|
|
|
|
|
|||
ОК, см |
Ж, с |
|
|
Расход воды, л/м3, при крупности, мм |
|
|
|
|||||||||
|
|
гравия |
|
|
|
|
щебня |
|
|
|||||||
|
|
|
10 |
|
20 |
|
40 |
|
80 |
10 |
20 |
|
40 |
|
80 |
|
|
– |
40 – 50 |
150 |
|
135 |
|
125 |
|
120 |
160 |
150 |
|
135 |
|
130 |
|
|
– |
25 – 35 |
160 |
|
145 |
|
130 |
|
125 |
170 |
160 |
|
145 |
|
140 |
|
|
– |
15 – 20 |
165 |
|
150 |
|
135 |
|
130 |
175 |
165 |
|
150 |
|
145 |
|
|
– |
10 – 15 |
175 |
|
160 |
|
145 |
|
140 |
185 |
175 |
|
160 |
|
155 |
|
2 |
– 4 |
– |
190 |
|
175 |
|
160 |
|
155 |
200 |
190 |
|
175 |
|
170 |
|
5 |
– 7 |
– |
200 |
|
185 |
|
170 |
|
165 |
210 |
200 |
|
185 |
|
180 |
|
8 – 10 |
– |
205 |
|
190 |
|
175 |
|
170 |
215 |
205 |
|
190 |
|
185 |
||
10 |
– 12 |
– |
215 |
|
205 |
|
190 |
|
180 |
225 |
215 |
|
200 |
|
190 |
|
|
|
|
|
|
|
|
|
|
|
И |
|
|
|
|
||
12 |
– 16 |
– |
220 |
|
210 |
|
197 |
|
185 |
230 220 |
|
207 |
|
195 |
||
16 |
– 20 |
– |
227 |
|
218 |
|
208 |
|
192 |
237 |
228 |
|
213 |
|
202 |
|
|
|
|
|
|
Д |
|
|
|||||||||
Примечания: 1. Расход воды приведен для смеси на портландцементе с нормальной |
||||||||||||||||
густотой цементного теста 26 – 28% и на песке с Мкр = 2,2. 2. При изменении нормаль- |
ной густоты цементного теста на каждыйАпроцент в меньшую сторону расход воды уменьшается на 3 – 5 л, в большую сторону – увеличивается на 3 – 5 л/м3. 3. При изме-
нении модуля крупности песка на каждые 0,5 в меньшую сторону расход воды увели- |
|||
чивается на 3 – 5 л, в большую сторонуб– уменьшается на 3 – 5 л. |
|
||
Если расход цементаина 1 м3 бетона окажется ниже допускаемого (см. |
|||
табл. 3), то необходимо увеличить его до требуемой нормы. |
|
||
4. Расход щебня (гравия) определяют по формуле, полученной реше- |
|||
нием системы уравненийС(1) и (2): |
|
|
|
Щ = 1000 |
Vмз α |
1 |
|
ρнас. щ |
+ ρщ , |
(8) |
где Vмз – объем межзерновых пустот, подставляется в долях единицы; α – коэффициент раздвижки зерен, определенный по результатам испытаний пластичных бетонных смесей с различными расходами цемента и водоцементными отношениями, принимается по табл. 10; ρнас. щ и ρщ – соответственно насыпная и истинная плотности щебня, кг/л.
15

|
Значения коэффициента раздвижки зерен α |
|
Таблица 10 |
||||||
|
|
|
|
||||||
|
|
|
|
|
|
|
|
||
Расход цемента, кг/м3 |
|
Водоцементное отношение |
|
|
|||||
0,3 |
0,4 |
0,5 |
0,6 |
|
|
0,8 |
|||
|
|
|
0,7 |
|
|||||
250 |
|
– |
– |
– |
1,26 |
|
1,32 |
|
1,38 |
300 |
|
– |
– |
1,3 |
1,36 |
|
1,42 |
|
– |
350 |
|
– |
1,32 |
1,38 |
1,44 |
|
– |
|
– |
400 |
|
1,31 |
1,4 |
1,46 |
– |
|
– |
|
– |
500 |
|
1,44 |
1,52 |
1,56 |
– |
|
– |
|
– |
600 |
|
1,52 |
1,56 |
– |
– |
|
– |
|
– |
Примечания: 1. При |
других значениях Ц и В/Ц коэффициент α находят интерполя- |
цией. 2. При использовании мелкого песка с водопотребностью более 7% коэффи-циент α уменьшают на 0,03 на каждый процент увеличения водопотребности песка. Если ис-
пользуется крупный песок с водопотребностью менее 7%, коэффициент α увеличивают на 0,03 на каждый процент уменьшения водопотребности песка.
Для жестких бетонных смесей при расходе цемента менее 400 кг/м3 коэффициент α принимают равным 1,05 – 1,15, в среднем 1,1. Значение α
меньше 1,05 принимают в случае использования мелких песков с Мк <32. |
|||||||||
Для составов жестких смесей с расходом цемента более 400 кг/м |
зна- |
||||||||
чение α назначают не менее 1,1. |
|
|
|
И |
|
||||
|
|
|
|
|
|
|
|
||
5. Расход песка определяют по формуле, полученной преобразованием |
|||||||||
уравнения (1): |
|
|
|
Д |
|
|
|
|
|
|
|
АЦ |
Щ |
|
|
|
|
||
П |
= 1000 − |
|
−В− |
|
ρ |
|
, |
(9) |
|
ρц |
|
||||||||
|
|
|
|
ρщ |
|
п |
|
|
|
|
|
|
|
|
|
|
|
|
|
|
б |
|
|
|
|
|
|
где ρц |
– плотность цемента при отсутствии экспериментальных данных |
||
|
и |
|
|
принимается равной 3,1 кг/л; ρп – истинная плотность песка, кг/л. |
|
||
6. Расчетную плотность бетонной смеси определяют по формуле |
|
||
|
С |
ρб.с. = Ц + Щ + П + В. |
(10) |
|
|
7. Расход материалов на замес, из которого должно быть отформовано заданное количество кубов с размером ребра 100, 150 или 200 мм, берется с избытком не менее 10%.
Для изготовления трех кубов с размером ребра 150 мм (объем куба 3,38 л) готовят замес объемом 12 л, для чего расходы всех компонентов, рассчитанные на 1000 л бетонной смеси, умножают на 0,012. Для изготовления шести кубов с ребром 100 мм готовят замес объемом 7 л из расчета объема бетонной смеси, необходимой для заполнения конуса при определении удобоукладываемости бетонной смеси.
16
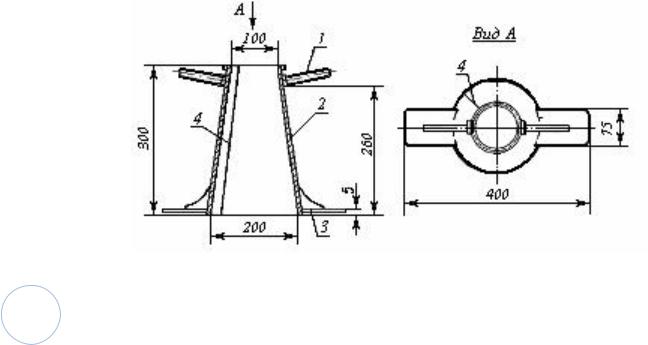
2. Определение подвижности или жесткости смеси
Материалы для всех лабораторных замесов должны быть одни и те же. Их испытывают до начала подбора состава бетона, определяя значе-
ния ρц, ρщ, ρп, ρнас.щ, Vм.з, Rц, A, A1. Сырьевые материалы следует дозировать по массе с погрешностью не более 1%. Воду и водные растворы до-
бавок дозируют по массе или по объему.
Приготовление опытных замесов начинают c перемешивания сухих материалов и затем постепенно добавляют в замес расчетное количество воды и водного раствора добавки. Перемешивание производят в лабораторном смесителе. Опытные замесы тяжелого бетона объемом до 15 л допускается производить вручную на предварительно увлажненном противне с перемешиванием в течение 3 – 5 мин.
бетонной смеси. Определение удобоукладываемости и изготовление
После окончания перемешивания отбирают пробы для проверки удобоукладываемости, а также других, предусмотренныхИзаданием свойств
добавлением тех или иных компонентов в необходимых количествах до получения смеси с заданнымибсвойствами [15].
контрольных образцов бетона начинают не позднее чем через 10 мин и заканчивают не позднее чем через 30 минДпосле окончания перемешивания
смеси. Бетонную смесь, которая не удовлетворяет заданной удобоукладываемости, допускается корректироватьАпри вторичном перемешивании с
Подвижность бетонной смеси характеризуется измеряемой в сантиметрах величиной осадкииконуса (ОК), отформованного из бетонной смеси.
Подвижность бетонной смеси с зернами заполнителя наибольшей крупности до 40 мм включ тельно определяют на обычном конусе.
ОпределениеСОК про зводят в следующей последовательности. Очищенный и протертый влажной тканью конус 2 ставят на ровную площадку и заполняют его бетонной смесью в три слоя одинаковой высоты, уплотняя каждый слой штыкованием металлическим стержнем 25 раз (рис. 2).
Рис. 2. Конус для определения подвижности бетонной смеси:
1 – ручка; 2 – корпус прибора; 3 – упоры; 4 – сварной шов
17
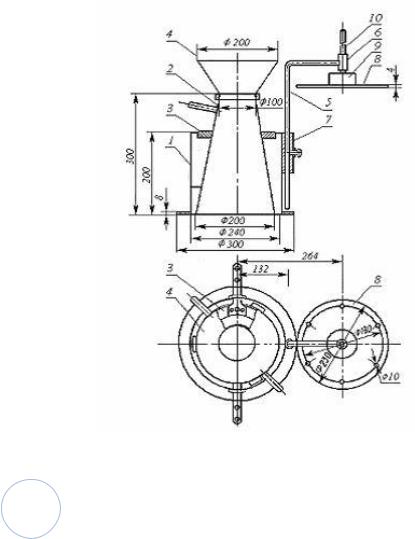
После уплотнения бетонной смеси в конусе снимают загрузочную воронку, избыток смеси срезают кельмой вровень с верхними краями конуса и заглаживают поверхность бетонной смеси. Время от начала заполнения конуса до его снятия не должно превышать 3 мин. Конус плавно снимают с отформованной бетонной смеси и устанавливают рядом с ней. Время, затраченное на подъем конуса, должно составлять 5 – 7 с.
Осадку конуса определяют, укладывая металлическую линейку наверх конуса и замеряя расстояние от нижней грани линейки до верха бетонной смеси с погрешностью до 5 мм. Осадку конуса бетонной смеси определяют дважды. Вычисляют с округлением до 10 мм как среднеарифметическое значение двух определений ОК из одной пробы, отличающихся между собой не более чем: на 10 мм при ОК до 9 см включительно; на 20 мм при ОК = 10 – 15 см; на 30 мм при ОК = 16 см и выше. При большем расхождении результатов определение повторяют на новой порции бетонной смеси той же пробы. Если после снятия конуса бетонная смесь разваливается, то испытание повторяют на новой пробе.
Если ОК равна 0, то смесь признают не обладающей подвижностью, и она должна характеризоваться жесткостью. Жесткость бетонной смеси
(Ж) характеризуется временем вибрации в секундах, необходимым для |
||||
|
|
|
|
И |
вибрирования и уплотнения предварительно отформованного конуса бе- |
||||
тонной смеси в приборе для определения жесткости (рис. 3). |
||||
|
|
|
Д |
|
|
|
А |
|
|
|
б |
|
Рис. 3. Прибор для определения |
|
и |
|
|
||
|
|
жесткости бетонной смеси: |
||
|
|
1 – цилиндрическое кольцо с |
||
С |
|
|
|
|
|
|
|
фланцем в основании; 2 – конус; |
|
|
|
|
3 – кольцо-держатель с ручка- |
|
|
|
|
ми; 4 – загрузочная воронка; |
5 – штатив; 6 – направляющая втулка; 7 – фиксирующая втулка с зажимным винтом; 8 – диск с шестью отверстиями; 9 – стальная шайба; 10 – штанга
18

Жесткость бетонной смеси с зернами заполнителя наибольшей крупностью до 40 мм включительно определяют на лабораторной виброплощадке в следующей последовательности. Устанавливают на виброплощадку и жестко закрепляют цилиндрическое кольцо прибора 1, в которое вставляют конус 2 и закрепляют его ручками 3, заводя их в пазы кольца, после чего устанавливают воронку 4.
Заполнение конуса прибора бетонной смесью, уплотнение и снятие конуса с отформованной смеси производят так же, как при определении подвижности.
Поворотом штатива 5 диск 8 устанавливают над отформованным конусом бетонной смеси и плавно опускают его на поверхность конуса смеси. Штатив закрепляют в фиксирующей втулке 7 зажимным винтом. Затем одновременно включают виброплощадку, секундомер и наблюдают за уплотнени-
ка, в этот момент секундомер выключают. Жесткость бетонной смеси вычис-
ем и выравниванием бетонной смеси. Вибрирование производят до тех пор, пока не начнется выделение цементного теста изИлюбых двух отверстий дис-
20%. При большем расхождении результатов определение повторяют на новой порции бетонной смеси той жеАпробы. Общее время испытания дважды определенной жесткости не должно превышать 10 мин.
ляют с округлением до 1 с как среднеарифметическое результатов двух определений из одной пробы смеси, отличающихсяДмежду собой не более чем на
опытный замес добавляют по 5 – 10% цемента и воды с соблюдением при-
нятого В/Ц. Если удобоукладываемостьи получилась более требуемой, то в замес добавляется песок ще ень – по 5…10% от расчетного в принятом
Если удобоукладываемостьбсмеси получилась меньше требуемой, то в
соотношении. Путем нескольк х попыток добиваются заданной удобоукладываемости смесиС.
3. Определение фактической плотности бетонной смеси
Определение фактической плотности свежеприготовленной бетонной
смеси с заданной подвижностью производится путем ее укладки в мерный цилиндр, размеры которого принимают в зависимости от наибольшей крупности заполнителя (табл. 11).
Вместимость и размеры мерного цилиндра |
Таблица 11 |
||||
|
|
||||
в зависимости от наибольшей крупности заполнителя |
|
|
|||
|
|
|
|
|
|
Наибольшая крупность зерен |
Вместимость цилин- |
Внутренний размер сосуда, мм |
|||
фракции заполнителя, мм |
дра, см3, не менее |
Диаметр |
|
Высота |
|
20 |
1000 |
108 |
|
108 |
|
40 |
5000 |
185 |
|
185 |
|
80 (70) |
10000 |
234 |
|
234 |
|
19

После чего вибрируют на лабораторной виброплощадке до прекращения оседания бетонной смеси и появления на ее поверхности тонкого слоя цементного теста [15].
После уплотнения избыток бетонной смеси срезают металлической линейкой и выравнивают поверхность на уровне краев мерного цилиндра. Цилиндр с бетонной смесью взвешивают с погрешностью не более 5 г. Определения плотности бетонной смеси производят два раза и вычисляют как среднеарифметическое значение результатов двух определений, отличающихся между собой не более чем на 2%. При большем расхождении результатов испытание повторяют на новой пробе бетонной смеси.
Фактическую плотность бетонной смеси, г/см3, вычисляют по формуле
|
|
|
|
|
ρб.с |
= |
m2 − m1 |
|
, |
|
|
|
(11) |
||
|
|
|
|
|
|
||||||||||
|
|
|
|
|
|
|
|
vц |
И |
|
|||||
|
|
|
|
|
|
|
|
|
|
|
|
|
|
|
|
|
|
|
|
|
|
|
|
Д |
|
||||||
где m2, m1 – массы цилиндра соответственно с бетонной смесью и пустого, |
|||||||||||||||
г; vц – объем цилиндра, см3. |
|
|
|
|
|
|
|
|
|
|
|||||
Зная фактическую среднюю плотность полученной бетонной смеси и |
|||||||||||||||
|
|
|
|
|
|
А |
|
|
|
|
|
|
|
||
расход материалов на пробный замес, определяют фактический расход ма- |
|||||||||||||||
териалов на 1 м3 бетона [2]: |
|
|
|
|
|
|
|
|
|
|
|||||
|
|
ρб.с |
|
|
б |
|
|
|
|
|
ρб.с |
|
|
||
Ц |
= |
|
|
|
mц, |
|
|
Щ = |
|
|
|
mщ, |
(12) |
||
|
|
и |
|
|
|
|
|
|
|
∑m |
|
||||
|
|
∑m |
|
|
|
|
|
|
|
|
|
|
|||
|
С |
|
|
|
|
|
|
|
|
ρб.с |
|
|
|||
П |
= |
ρб.с |
mп, |
|
|
В = |
|
|
mв, |
(13) |
|||||
|
|
∑m |
|
|
|
|
|
|
|
|
∑m |
|
где ∑m – суммарная масса всех материалов в замесе, кг; mц,, mщ, mп, mв –
расходы соответственно цемента, щебня, песка и воды на пробный замес, кг.
Фактический расход сырьевых компонентов на 1 м3 бетона и на замес (7 л) заносят в табл. 12.
Таблица 12
|
|
Результаты расчета |
|
|
|
|
|
||||
|
|
|
|
|
|
|
|
|
|
|
|
|
Плотность бетонной |
|
|
Расход материалов, кг |
|
||||||
Вид бетона |
смеси, кг/м3 |
на 1 м3 (1000 л) |
|
|
на замес, л |
|
|||||
|
расчетная |
фактическая |
Ц |
Щ |
П |
|
В |
Ц |
Щ |
П |
В |
Тяжелый |
|
|
|
|
|
|
|
|
|
|
|
20

4. Формовка и хранение контрольных образцов
Из откорректированной бетонной смеси готовят контрольные образцы. На каждый срок испытания изготавливают не менее трех образцов в стальных или чугунных формах с точностью размеров ± 1% и тонким слоем смазки. Углы между гранями должны составлять 90 ± 2°. Укладку бетонной смеси заканчивают не позднее чем через 30 мин после изготовления смеси. Уплотнение бетонной смеси производят на лабораторной виброплощадке с частотой колебаний 2900 ± 100 кол/мин и амплитудой под нагрузкой 0,5 ± 0,05 мм. Формы должны быть жестко закреплены на виброплощадке механическим или магнитным захватом.
Признаком достаточности виброуплотнения является прекращение оседания бетонной смеси, выравнивание ее поверхности и появление на
ней тонкого слоя цементного теста. Поверхность образца заглаживают |
|
кельмой. |
И |
|
Образцы, предназначенные для твердения в нормально-влажностных
условиях, после изготовления до распалубливания хранят в формах, покрытых влажной тканью или другим материалом, исключающим возможность испарения из них влаги, в помещении с температурой воздуха равной 20 ± 5 °С [16].
ют не ранее чем через 24 ч и не позднее Дчем через 72 ч.
При определении прочности бетона на сжатие образцы распалублива-
После распалубливания о разцы должны быть помещены в камеру,
обеспечивающую у поверхностей о разцов нормальные условия, т.е. тем- |
|
|
А |
б |
|
и |
|
пературу – 20 ± 2 °С относ тельную влажность воздуха – 95 ± 5%. Образцы укладывают на подкладки так, чтобы расстояние между образцами и стенками камерыСбыло не менее 5 мм. Площадь контакта образца с подкладками, на которых он установлен, не должна составлять более 30% площади опорной грани образца. Образцы в камере нормального твердения не должны непосредственно орошаться водой. Допускается хранение образцов под слоем влажного песка, опилок или других систематически увлажняемых гигроскопичных материалов.
Образцы, предназначенные для твердения в условиях тепловлажностной обработки, должны быть помещены в формах в тепловой агрегат (пр о- парочную камеру, автоклав, отсек формы или кассеты и т.д.) и твердеть вместе с конструкциями (изделиями) или отдельно по принятому на производстве режиму.
После окончания тепловой обработки образцы распалубливают и испытывают или хранят в нормальных условиях.
Допускаются другие условия твердения образцов, например в воде или в условиях, аналогичных условиям твердения бетона в монолитных конст-
21

рукциях, если эти условия установлены стандартами, техническими условиями или технологическими регламентами на производство работ.
5. Определение размера образцов, плотности и испытание на предел прочности при сжатии
В помещении для испытания образцов следует поддерживать температуру, равную 20 ± 5 °С, и относительную влажность воздуха не менее 55%. Образцы должны быть выдержаны до испытания при указанных условиях в распалубленном виде в течение 24 ч, если они твердели в воде, и в течение 4 ч, если они твердели в воздушно-влажностных условиях или в условиях тепловой обработки [16].
Перед испытанием образцы подвергают визуальному осмотру, устанавливая наличие дефектов в виде трещин, сколов ребер, раковин и инородных включений. Образцы, имеющие трещины, сколы ребер глубиной более 10 мм, раковины диаметром более 10 мм и глубиной более 5 мм, а также следы расслоения и недоуплотнения бетонной смеси, испытанию не подлежат. Наплывы бетона на ребрах опорных поверхностей образцов
должны быть удалены абразивным камнем. |
И |
|
|||
|
|
|
|
|
|
Производят взвешивание образцов и измеряют грани по серединам с |
|||||
погрешностью не более 1%. Плотность образцов, г/см3, определяют: |
|
||||
|
|
|
Д |
(14) |
|
|
|
ρ = m / v, |
|
||
|
|
А3 |
. |
|
|
m – масса образца, г; v – о ъем о разца, см |
|
||||
Прочность бетона в контрол руемом возрасте характеризуют классами |
|||||
|
б |
|
|
|
|
по прочности на сжат е, осевое растяжение и растяжение при изгибе [11], |
|||||
и |
|
|
|
|
|
С |
|
|
|
|
|
причем основным является класс по прочности на сжатие. Класс бетона – гарантированная его прочность с обеспеченностью 0,95. Класс по прочности на сжатие контролируют во всех случаях, а по другим характеристикам прочности – если установлено нормами проектирования конструкции. Прочность на сжатие контролируют на кубах с высотой ребра 100, 150, 200, 250 и 300 мм или цилиндрах с таким же размером диаметра и большей или равной диаметру высотой [16].
Опорные грани выбирают так, чтобы сжимающая сила при испытании была направлена параллельно слоям укладки бетонной смеси в формы. На опорные (боковые) грани образцов-кубов наносят осевые линии, по которым центрируют образец при испытании.
Нагружение образцов проводят непрерывно с постоянной скоростью нарастания нагрузки до его разрушения. При этом время нагружения образца до его разрушения должно быть не менее 30 с. Образцы устанавливают на нижнюю опорную плиту центрально по оси пресса и совмещают
22
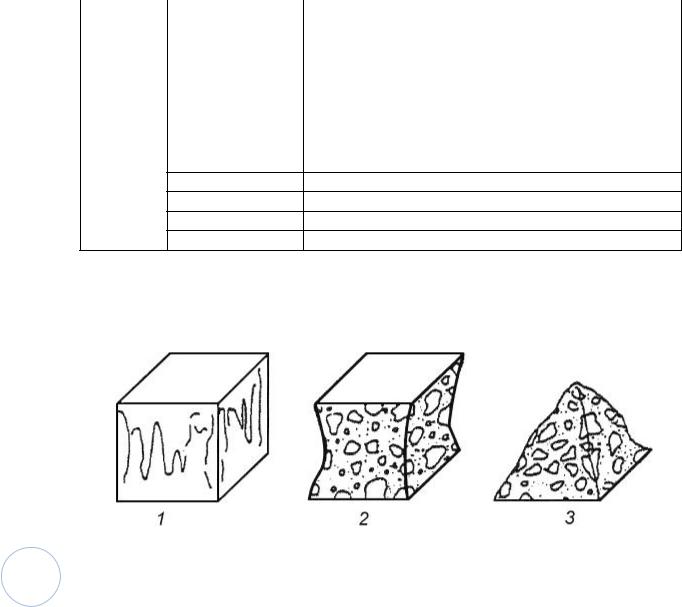
верхнюю плиту испытательной машины с верхней опорной гранью образца так, чтобы их плоскости полностью прилегали одна к другой. Образец нагружают при постоянной скорости нарастания нагрузки, равной 0,6 ± 0,2 МПа/с, до его разрушения.
Рабочую площадь сечения образцов определяют как среднеарифметическое значение площадей двух противоположных граней. Предел прочности при сжатии тяжелого бетона, МПа вычисляют для каждого образца по формуле
Rсж = |
F |
αм 0,098, |
(15) |
|
S |
||||
|
|
|
где F – разрушающая нагрузка, кгс; S – средняя площадь рабочего сечения
образца, cм2; αм – масштабный коэффициент для приведения прочности |
||||||||||
образцов |
бетона |
к |
прочности в образцах |
базовых размера и формы |
||||||
(табл. 13). За базовый принимают образец размером 15x15x15 см. |
|
|
||||||||
|
|
|
|
Значения масштабного коэффициента |
Таблица 13 |
|||||
|
|
|
|
|
|
|||||
|
|
|
И |
|
||||||
Форма |
|
Размер образца, |
Минимальное значение масштабного коэффициента |
|||||||
образца |
|
мм |
|
|
|
|
|
|
||
|
|
|
70 |
|
|
|
0,85 |
|
|
|
|
|
100 |
|
|
|
0,95 |
|
|
||
|
|
|
|
|
|
|
Д |
|
|
|
Куб (раз- |
150 |
|
|
|
1,00 |
|
|
|||
мер ребра) |
|
200 |
|
А |
1,05 |
|
|
|||
|
|
250 |
|
|
1,08 |
|
|
|||
|
|
300 |
|
|
|
1,10 |
|
|
||
|
100 |
× |
200 |
б |
|
1,16 |
|
|
||
Цилиндр |
|
150 |
300 |
|
1,20 |
|
|
|||
(диаметр |
|
200 |
× |
400и |
|
|
1,24 |
|
|
|
высоту)× |
|
250 |
× |
500 |
|
|
|
1,26 |
|
|
|
|
300 |
× |
600 |
|
|
|
1,28 |
|
|
С×
Возможные варианты разрушения образцов приведены на рис. 4 и 5. В случае разрушения образца по одной из дефектных схем, указанных на рис. 5, при определении средней прочности серии этот результат не учитывают.
Рис. 4. Удовлетворительные разрушения образцов
23
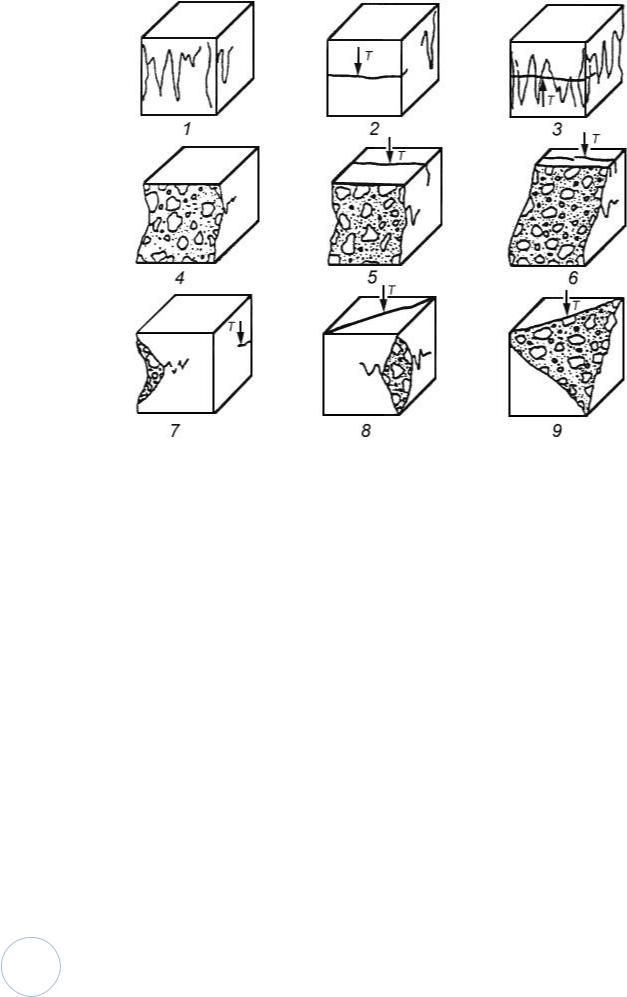
|
|
|
А |
И |
|
|
|
|
|
|
|
||
|
|
б |
|
|
|
|
|
Рис. 5. НеудовлетворительныеДразрушения образцов |
|
||||
|
и |
|
|
|
|
|
Между классом бетона В и его прочностью в партии Rср имеется зави- |
||||||
симость |
С |
|
|
|
|
|
|
В = Rср · (1 |
– t · vср), |
(16) |
|||
|
|
где Rср – средний предел прочности при сжатии бетона, МПа; t – коэффициент, характеризующий принятую при проектировании обеспеченность класса бетона, при обеспеченности равной 0,95, t = 1,64; vср – средний внутрисерийный коэффициент вариации прочности бетона, определяемый по результатам испытания любых последовательных 30 серий образцов одного класса, % [16]:
vср = |
Wср |
100, |
(17) |
|
|||
|
d Ri,ср |
|
где Wср – средний размах в прочности образцов, МПа; d – коэффициент, принимаемый в зависимости от числа образцов n в каждой серии по табл. 14; Ri, ср – средняя прочность образцов, МПа.
24

Значения коэффициента d |
|
Таблица 14 |
||||
|
|
|
||||
|
|
|
|
|
|
|
Число единичных значений п |
2 |
3 |
4 |
5 |
6 |
|
Значение коэффициента d |
1,13 |
1,69 |
2,06 |
2,33 |
2,5 |
|
Средний размах в прочности образцов, МПа, определяется по формуле
|
30 |
|
|
|
Wср = |
∑Wi |
, |
(18) |
|
i =1 |
||||
30 |
||||
|
|
|
где Wi – размах единичных значений прочности при сжатии бетона в контролируемой партии, МПа, находится по формуле
|
|
|
|
|
|
|
И |
|
|
Wi = Ri,max – Ri,min, |
(19) |
||||||
|
|
|
|
Д |
|
|||
где Ri,max и Ri,min – максимальное и минимальное значения прочности бето- |
||||||||
на в каждой серии образцов, МПа. |
|
|
|
|
|
|
||
Средняя прочность образцов, МПа вычисляется по формуле |
|
|||||||
|
|
А |
|
|
||||
|
|
|
|
30 |
R |
|
|
|
|
б |
∑ i |
|
(20) |
||||
|
Ri, ср |
= |
j =1 |
|
|
, |
||
|
30 |
|
|
|||||
и |
|
|
|
|
|
|||
|
|
|
|
|
|
|
||
где Ri – предел прочности етонных о разцов в каждой серии, МПа. |
|
|||||||
С |
|
|
|
|
|
|
|
|
За нормативное пр н мают значение v =13,5%. При указанных значе- |
||||||||
ниях t и v класс бетона определяют по формуле |
|
|||||||
|
В = Rср · 0,778. |
|
(21) |
Если неоднородность изготавливаемого бетона выше нормативной, т.е. v > 13,5%, то чтобы обеспечить назначенный для данной конструкции класс бетона, необходимо увеличить расчетную прочность бетона с соответствующим увеличением расхода цемента, что является экономически невыгодным.
Если возраст бетона отличается от расчетного (28 сут), то для обычно-
го портландцемента средних марок может быть применена формула |
|
|||
R |
= R lg 28 |
, |
(22) |
|
28 |
n |
lg n |
|
|
|
|
|
|
где n – возраст бетона в сутках, который должен быть более трех суток.
25
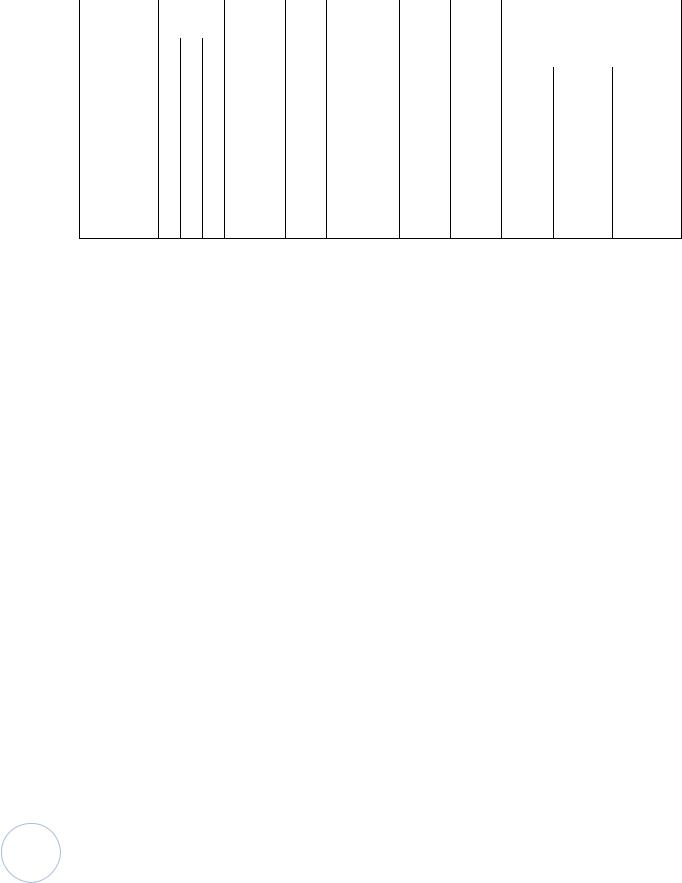
По результатам испытаний образцов из тяжелого бетона строится зависимость предела прочности при сжатии от времени твердения образцов. Полученные данные заносятся в табл. 15.
|
|
|
Результаты испытания образцов |
|
Таблица 15 |
|||||
|
|
|
|
|
|
|||||
|
|
|
|
|
|
|
|
|||
|
Раз- |
|
Плот- |
|
Предел прочности при |
|||||
|
мер, см |
|
3 |
ность |
2 |
сжатии Rсж, МПа, по |
||||
Номер образца |
А В Н Объемобразца, |
см Массакг, |
Нагрузка, кгс Площадь, см |
|||||||
образца, |
|
истечении, сут |
||||||||
кг/м3 |
|
|
|
|
||||||
14 |
28расч |
28фактич |
||||||||
1 |
|
|
|
|
|
|
– |
– |
|
|
2 |
|
|
|
|
|
|
– |
– |
|
|
3 |
|
|
|
|
|
|
– |
– |
|
|
4 |
|
|
|
|
|
– |
|
|
|
|
5 |
|
|
|
|
|
– |
|
|
|
|
6 |
|
|
|
|
|
– |
|
|
|
|
Средние |
|
|
|
|
|
|
|
|
|
|
значения |
|
|
|
|
|
|
|
|
|
В заключение определяется класс бетона, делаютсяИвыводы о влиянии времени твердения тяжелого бетона на предел прочности при сжатии, дается сравнительная оценка фактической прочности образцов и прочнос-
ти, определенной расчетным методом. |
Д |
|
|
|
|
Ла ораторная работа № 2 |
||
|
А |
|
ВЛИЯНИЕ СООТНОШЕНИЯ ФРАКЦИЙ КРУПНОГО |
||
ЗАПОЛНИТЕЛЯбНА ОСНОВНЫЕ СВОЙСТВА |
||
ТЯЖЕЛОГО БЕТОНА |
||
и |
|
|
Цель работы – исследовать влияние расхода различных фракций круп- |
||
ного заполнителя на основные свойства смеси и тяже- |
||
Слого бетона. |
|
|
Приборы и оборудование:
•цилиндры мерные вместимостью 250 и 1000 мл по ГОСТ 1770;
•весы по ГОСТ 29329 или ГОСТ 24104–2001;
•формы с размером ребра 100 мм;
•лабораторный вибростол;
•штангенциркуль по ГОСТ 166;
•гидравлический пресс с максимальным усилием 50 – 500 кН (5 – 50 тс) по ГОСТ 28840.
Порядок выполнения работы
Преподаватель делит студентов на четыре – пять бригад. Каждая бри-
26
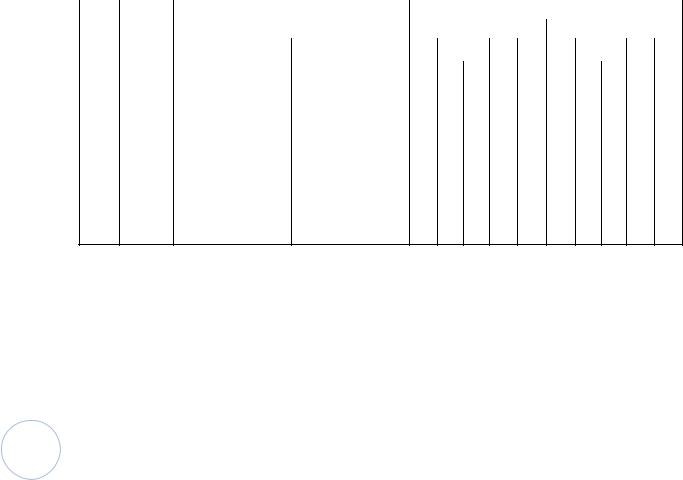
гада получает индивидуальное задание на изготовление образцов из тяжелого бетона с различным соотношением фракций крупного заполнителя (5 – 10 мм и 10 – 20 мм от 0 до 100% с шагом 25%). Формовка образцов производится на составе тяжелого бетона, подобранном в лабораторной работе № 1.
Выполнение работы осуществляется в следующей последовательности:
1)пересчет расхода крупного заполнителя в зависимости от содержания в смеси той или иной фракции;
2)изготовление образцов из тяжелого бетона с размером ребра 100 мм;
3)определение размера образцов, их массы, плотности и испытание на предел прочности при сжатии.
1. Расчет расхода крупного заполнителя
Первая бригада |
И |
рассчитывает расход крупного заполнителя со сто |
процентным содержанием фракции 10 – 20 мм. Вторая – производит расчет крупного заполнителя с соотношением между фракциями 5 – 10 мм и 10 – 20 мм соответственно 25 и 75% по массе. Третья – использует тот же
размер фракций, но соотношение составляет 50 на 50%, четвертая – 75 на |
||||||||||||||
|
|
|
|
|
|
А |
|
|
|
|
|
|||
25% по массе. Пятая бригада рассчитывает расход крупного заполнителя |
||||||||||||||
со стопроцентным содержанием фракции 5 – 10 мм по массе. |
|
|
|
|||||||||||
|
|
|
|
|
б |
Д |
|
Таблица 16 |
||||||
|
|
|
|
|
|
|
|
|||||||
|
|
|
|
|
Результаты расчета |
|
|
|
|
|
||||
|
|
|
|
|
|
|
|
|
|
|
|
|
|
|
|
|
|
|
и |
|
|
|
|
|
|
|
|
|
|
|
|
крупногоВид заполнителя |
Соотношен я между фракция- |
|
|
|
Расход материалов, кг |
|
|
|||||
|
бригадыНомер |
ми, % при размере фракций, мм |
на 1 м3 (1000 л) |
на замес, л |
|
|||||||||
|
С |
|
|
|
|
|
|
|
|
|
|
|||
|
|
|
|
|
мм10–5 |
мм20–10 |
|
мм10–5 мм20–10 |
|
|
||||
|
|
|
|
|
|
|
|
|
Щ |
|
Щ |
|
|
|
|
|
|
5 – 10 |
|
10 – 20 |
|
Ц |
|
П В Ц |
|
П В |
|||
|
|
|
|
|
|
|
|
|
|
|
|
|
|
|
1 |
Щебень |
0 |
|
|
100 |
|
|
|
|
|
|
|
|
|
|
2 |
25 |
|
|
75 |
|
|
|
|
|
|
|
|
|
|
4 |
75 |
|
|
25 |
|
|
|
|
|
|
|
|
|
|
3 |
|
50 |
|
|
50 |
|
|
|
|
|
|
|
|
|
|
|
|
|
|
|
|
|
|
|
|
|
|
|
|
5 |
|
100 |
|
|
0 |
|
|
|
|
|
|
|
|
Примечание. Допускается использовать другие соотношения между фракциями и размер фракций.
Пересчет расхода крупного заполнителя, кг по массе в зависимости от содержания в смеси той или иной фракции, осуществляется по формуле
27

Щфр. = |
Фр Щ |
, |
(23) |
|
100 |
||||
|
|
|
где Фр – содержание определенной фракции крупного заполнителя в бетонной смеси, %; Щ – расход щебня, рассчитанный и подобранный в лабораторной работе № 1, кг.
Результаты расчета расхода крупного заполнителя в зависимости от соотношения между фракциями заносятся в табл. 16.
2. Приготовление образцов из тяжелого бетона
Требования к формам, параметрам виброуплотнения, изготовлению, распалубливанию и хранению образцов из тяжелого бетона должны соот-
ветствовать лабораторной работе № 1 (подразд. 4). |
|
|
И |
3. Определение размера образцов, плотности |
|
и предела прочности при сжатии |
|
Определение размера образцов из тяжелого бетона, их плотности и ис- |
|
А |
|
пытание на предел прочности при сжатии производится в соответствии с |
|
лабораторной работой № 1 (подразд. 5). |
|
б |
|
По результатам испытаний образцовДиз тяжелого бетона строятся зави-
симости предела прочности при сжатии и средней плотности от соотношения между фракциями крупного заполнителя. Полученные данные заносятся в табл. 17.
|
|
|
|
Результаты испытания образцов |
|
Таблица 17 |
|||||||
|
|
|
|
|
|
||||||||
|
|
|
и |
|
|
|
|
|
|
||||
бригадыНомер |
Номеробразца |
Соотношения между |
Размер, |
Объемобразца, см |
Масса, кг |
Плот- |
Нагрузка, кгс |
Площадь, см |
Предел |
||||
5 – 10 |
|
10 – 20 |
|
см |
|
кг/м3 |
Rсж, МПа |
||||||
|
|
фракциями, % при |
|
|
3 |
|
ность |
|
|
прочно- |
|||
|
|
размере фракций, мм |
|
|
|
|
|
образ- |
|
2 |
сти при |
||
|
|
|
С |
А |
В |
Н |
|
|
ца, |
|
|
сжатии |
|
|
|
|
|
|
|
|
|
|
|||||
|
|
|
|
|
|
|
|
|
|
|
|
|
|
1 |
2 |
3 |
|
4 |
5 |
6 |
7 |
8 |
9 |
10 |
11 |
12 |
13 |
|
1 |
0 |
|
100 |
|
|
|
|
|
|
|
|
|
1 |
2 |
|
|
|
|
|
|
|
|
|
|
||
3 |
|
|
|
|
|
|
|
|
|
|
|
|
|
|
|
|
|
|
|
|
|
|
|
|
|
|
|
|
Средние значения |
|
|
|
|
|
|
|
|
|
|||
2 |
1 |
25 |
|
75 |
|
|
|
|
|
|
|
|
|
2 |
|
|
|
|
|
|
|
|
|
|
|||
|
3 |
|
|
|
|
|
|
|
|
|
|
|
|
|
Средние значения |
|
|
|
|
|
|
|
|
|
28