
326
.pdf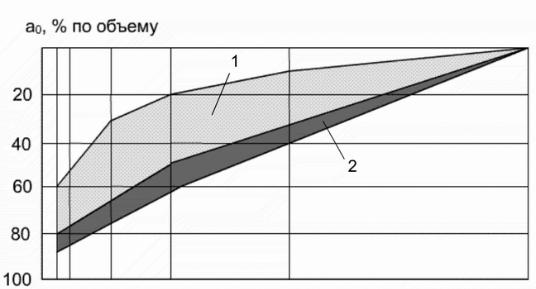
8
При расчете составов легкого бетона используют понятие плотности в куске, т. е. плотности зерен легкого заполнителя с учетом их пористости. Плотность в куске легких заполнителей в зависимости от вида заполнителя может колебаться от 0,7 до 1,8 г/см3.
Истинная плотность пористых заполнителей составляет 2,6...2,7 г/см3. Общая пористость легких заполнителей – 40...75 %, причем большинство пор обычно сообщаются между собой и открыты для доступа воды. Закрытая пористость не превышает 10...20 %. Пустотность легких пористых заполнителей зависит от их зернового состава и для обычных песка и щебня составляет 30...45 %. В легких бетонах используют крупный пористый заполнитель (гравий или щебень) стандартных фракций 5...10, 10...20, 20...40 мм и легкий песок, получаемый дроблением крупных фракций заполнителя или обжигом в печах кипящего слоя (для керамзитового песка). Зерновой состав песка должен соответствовать рекомендациям (рис. 2) (1 – желательный, 2 – допустимый). Зерна дробленого песка не имеют спекшейся оболочки и поэтому обладают повышенной водопотребностью и пониженной прочностью. Кроме того, выход дробленого песка из 1 м3 гравия составляет всего 0,4...0,7 м3 , что приводит к удорожанию материала.
Рис. 2. Зерновой состав пористого песка (а0 – полные остатки по объему)
Пористая структура заполнителей значительно снижает их прочность (обычно в 50...100 раз). Ориентировочно прочность керамических пористых заполнителей типа керамзита можно определять по формуле
Rз 150 2 . |
(1) |
9
Опытным путем прочность пористых заполнителей определяют сдавливанием в стальном цилиндре диаметром 150 мм. При этом получают условную прочность материала (дробимость). Действительная прочность зерен заполнителя превышает условную: для керамзита – в 3...5 раз, для аглопорита – в 20...30 раз.
Между показателем дробимости Rдр и насыпной плотностью ρн существует ориентировочная статистическая зависимость
Rдр |
22. |
(2) |
|
2 |
|||
|
|
||
н |
|
|
Влияние легкого заполнителя на свойства бетона определяется всем комплексом его свойств, особенностями строения, составом бетона. Большое влияние оказывает не только общий объем пористости, но и ее характер; мелкопористые заполнители позволяют получать бетоны более прочные и экономичные по расходу цемента. Наличие более плотной и прочной наружной оболочки на зернах некоторых заполнителей, например керамзита, улучшает свойства заполнителя и эффективность его применения в бетоне. В последние годы проводятся работы по уменьшению водопоглощения легкого заполнителя путем поверхностной обработки его полимерами или гидрофобизирующими веществами, что также способствует экономии цемента в легких бетонах.
Технологические характеристики заполнителя. Существующие стан-
дартные испытания дают в основном качественную оценку заполнителя и отвечают лишь на вопрос, пригоден ли данный заполнитель для бетона заданной марки (класса). Для количественной оценки влияния заполнителя на свойства и экономичность бетона (не касаясь частных случаев, таких, как влияние заполнителя на морозостойкость, усадку и т. д.) необходимо знать влияние данного заполнителя на подвижность или водопотребность бетонной смеси, а также на прочность бетона при сжатии.
Если подобное влияние выразить какой-либо количественной характеристикой заполнителя, то можно было бы значительно уточнить технологические и технико-экономические расчеты, эффективнее использовать компьютерные технологии. Б. Г. Скрамтаевым и Ю. М. Баженовым был предложен способ испытания заполнителя непосредственно в бетоне, что обеспечивает получение наиболее достоверных технологических характеристик заполнителя: водопотребности и коэффициента прочности песка.
10
2. ТЕХНИЧЕСКИЕ ТРЕБОВАНИЯ
Щебень и гравий должны изготовляться в соответствии с требованиями ГОСТ 8267-93 по технологической документации, утвержденной предприятием-изготовителем.
2.1. Основные параметры и размеры
Щебень и гравий выпускают в виде следующих основных фракций:
от 5 (3) до 10 мм; св. 10 до 20 мм; св. 20 до 40 мм; св. 40 до 80 (70) мм и смеси фракций от 5 (3) до 20 мм.
По согласованию изготовителя с потребителем выпускают щебень и гравий в виде фракций от 10 до 15 мм; св. 15 до 20 мм; св. 80 (70) до 120 мм и св. 120 до 150 мм, а также смеси фракций от 5 (3) до 15 мм; св. 5 (3)
до 40 мм; св. 20 до 80 (70) мм.
2.2. Содержание дробленных зерен в щебне из гравия и форма зерен
2.2.1.Щебень из гравия должен содержать дробленые зерна в количестве не менее 80 % по массе. Допускается по согласованию изготовителя с потребителем выпуск щебня из гравия с содержанием дробленых зерен не менее 60 %.
2.2.2.Форму зерен щебня и гравия характеризуют содержанием зерен пластинчатой (лещадной) и игловатой форм.
Щебень в зависимости от содержания зерен пластинчатой и игловатой форм подразделяют на четыре группы, которые должны соответствовать указанным в табл. 2.
|
|
Таблица 2 |
|
Содержание зерен пластинчатой (лещадной) и игловатой форм |
|
|
|
|
Группа |
|
В процентах по массе |
щебня |
|
Содержание зерен пластинчатой (лещадной) и игловатой форм |
1 |
|
До 15 включ. |
2 |
|
Св. 15 до 25 |
3 |
|
25...35 |
4 |
|
35...50 |
Примечание. По согласованию изготовителя с потребителем допускается выпуск щебня из изверженных горных пород, содержащего св. 50 %, но не более 65 % зерен пластинчатой (лещадной) и игловатой форм.
11
2.2.3. Гравий не должен содержать зерен пластинчатой и игловатой форм более 35 % по массе.
2.3.Прочность
2.3.1.Прочность щебня и гравия характеризуют маркой, определяемой по дробимости щебня (гравия) при сжатии (раздавливанием) в цилиндре.
Щебень и гравий, предназначенные для строительства автомобильных дорог, характеризуют маркой по истираемости в полочном барабане.
2.3.2.Марки по дробимости щебня из осадочных и метаморфических пород должны соответствовать требованиям, указанным в табл. 3, а по дробимости щебня из изверженных пород в табл. 4.
Допускается определять марку щебня из осадочных и метаморфических пород как в сухом, так и в насыщенном водой состоянии.
При несовпадении марок по дробимости прочность оценивают по результатам испытания в насыщенном водой состоянии.
|
|
|
|
|
|
|
Таблица 3 |
|
Марка по дробимости щебня из осадочных и метаморфических пород |
||||||
|
|
|
|
|
|
||
|
Марка по дробимости щебня |
Потеря массы при испытании щебня, % |
|||||
|
из осадочных и |
|
в сухом состоянии |
|
в насыщенном водой |
||
|
метаморфических пород |
|
|
состоянии |
|||
|
|
|
|
|
|||
|
|
|
|
|
|
|
|
|
1200 |
|
|
До 11 включит. |
|
До 11 включит. |
|
|
1000 |
|
|
Св. 11 до 13 |
|
Св. 11 до 13 |
|
|
800 |
|
|
13…15 |
|
13…15 |
|
|
600 |
|
|
15…19 |
|
15…20 |
|
|
400 |
|
|
19…24 |
|
20...28 |
|
|
300 |
|
|
24…28 |
|
28…38 |
|
|
200 |
|
|
28…35 |
|
38…54 |
|
|
|
|
|
|
|
|
Таблица 4 |
|
Марка по дробимости щебня из изверженных пород |
||||||
|
|
|
|
|
|
||
|
Марка по дробимости |
|
|
Потеря массы при испытания щебня, % |
|||
|
щебня из изверженных |
|
из интрузивных пород |
|
из эффузивных пород |
||
|
пород |
|
|
|
|
|
|
|
1400 |
|
|
До 12 включ. |
|
|
До 9 включ. |
|
1200 |
|
|
Св. 12 до 16 |
|
|
Св. 9 до 11 |
|
1000 |
|
|
16...20 |
|
11...13 |
|
|
800 |
|
|
20...25 |
|
13...15 |
|
|
600 |
|
|
25...34 |
|
15...20 |
12
Марки по дробимости щебня из гравия и гравия должны соответствовать требованиям, указанным в табл. 5.
|
|
Таблица 5 |
Марка по дробимости щебня из гравия и гравия |
||
|
|
|
Марка по дробимости |
Потеря массы при испытании, % |
|
щебня из гравия и гравия |
щебня из гравия |
гравия |
1000 |
До 10 включ. |
До 8 включ. |
800 |
Св. 10 до 14 |
Св. 8 до 12 |
600 |
14...18 |
12...16 |
400 |
18...26 |
16...24 |
2.3.3. Марки по истираемости щебня и гравия должны соответствовать требованиям, указанным в табл. 6.
Таблица 6
Марка по истираемости щебня и гравия
Марка по |
Потеря массы при испытании, % |
||
истираемости щебня и |
щебня |
гравия |
|
гравия |
|||
|
|
||
И1 |
До 25 включ. |
До 20 включ. |
|
И2 |
Св. 25 до 35 |
Св. 20 до 30 |
|
И3 |
35...45 |
30...40 |
|
И4 |
45...60 |
40...50 |
2.4. Содержание зерен слабых пород
Содержание слабых пород в щебне и гравии в зависимости от вида горной породы и марки по дробимости не должно быть более указанного в табл. 7.
2.5.Морозостойкость
2.5.1.Морозостойкость щебня и гравия характеризуют числом циклов замораживания и оттаивания, при котором потери в процентах по массе щебня и гравия не превышают установленных значений.
Допускается оценивать морозостойкость щебня и гравия по числу циклов насыщения в растворе сернокислого натрия и высушивания. При несовпадении марок морозостойкость оценивают по результатам испытания замораживанием и оттаиванием.
13
2.5.2. Щебень и гравий по морозостойкости подразделяют на следу-
ющие марки: F15; F25; F50; F100; F150; F200; F300; F400.
|
Таблица 7 |
Содержание зерен слабых пород |
|
|
|
Вид породы и марка по дробимости щебня и |
Содержание зерен слабых |
гравия |
пород |
|
|
Щебень из изверженных, метаморфических и |
|
осадочных горных пород марок: |
|
1400; 1200; 1000 |
5 |
800; 600; 400 |
10 |
300 |
15 |
Щебень из гравия и валунов и гравий марок: |
|
1000; 800; 600; |
10 |
400 |
15 |
2.6. Содержание пылевидных и глинистых частиц
Содержание пылевидных и глинистых частиц (размером менее 0,05 мм) в щебне и гравии в зависимости от вида горной породы и марки по дробимости должно соответствовать указанному в табл. 8.
2.7.Наличие вредных компонентов и примесей
2.7.1.Щебень из попутно добываемых вскрышных и вмещающих пород и некондиционных отходов горных предприятий по переработке руд (черных, цветных и редких металлов металлургической промышленности) и неметаллических ископаемых других отраслей промышленности должен быть устойчивым против всех видов распадов.
Устойчивость структуры щебня против всех видов распадов должна соответствовать требованиям, указанным в табл. 9.
2.7.2.Щебень и гравий должны быть стойкими к воздействию окружающей среды. Щебень и гравий, предназначенные для применения
вкачестве заполнителей для бетонов, должны обладать стойкостью к химическому воздействию щелочей цемента.
Стойкость щебня и гравия определяют по минералогопетрографическому составу исходной горной породы и содержанию вредных компонентов и примесей, снижающих долговечность бетона и вызывающих коррозию арматуры железобетонных изделий и конструкций.
14
|
Таблица 8 |
|
Содержание пылевидных и глинистых частиц |
||
|
|
|
Вид породы и марка по дробимости щебня |
Содержание пылевидных и глинистых |
|
и гравия |
частиц |
|
Щебень из изверженных и |
|
|
метаморфических пород марок: |
|
|
св. 800 |
1 |
|
св. 600 до 800 включ. |
||
1 |
||
Щебень из осадочных пород марок: |
||
|
||
от 600 до 1200 включ. |
2 |
|
200, 400 |
||
3 |
||
Щебень из гравия и валунов и гравий |
||
|
||
марок: |
|
|
1000 |
1 |
|
800 |
||
1 |
||
600 |
||
2 |
||
400 |
||
3 |
||
|
||
|
|
Примечание. Допускается в щебне марок по дробимости 800 и выше из изверженных, метаморфических и осадочных пород увеличение на 1% содержания пылевидных частиц при следующих условиях:
–если при геологической разведке месторождения установлено отсутствие в исходной горной породе глинистых и мергелистых включений и прослоев;
–при предъявлении предприятием-изготовителем заключения специализированной лаборатории об отсутствии глинистых минералов в составе частиц размером менее 0,05 мм.
|
Таблица 9 |
Потеря массы при распаде |
|
|
|
Марка по дробимости щебня |
Потеря массы при распаде, % не |
|
более |
1000 и выше |
3 |
800, 600 |
5 |
400 и ниже |
7 |
15
3. МЕТОДЫ ФИЗИКО-МЕХАНИЧЕСКИХ ИСПЫТАНИЙ
3.1. Отбор проб
Масса лабораторной пробы при приемочном контроле должна быть не менее указанной в табл. 10.
Масса лабораторной пробы |
Таблица 10 |
|
|
||
|
|
|
Наибольший номинальный размер зерен D, мм |
|
Масса пробы, кг |
|
|
|
10 |
|
5,0 |
20 |
|
10,0 |
|
|
|
40 |
|
20,0 |
|
|
|
Св. 40 |
|
40,0 |
Указанную пробу используют для всех испытаний, предусмотренных при приемочном контроле.
3.2. Определение зернового состава щебня (гравия)
Зерновой состав щебня (гравия) определяют путем рассева пробы на стандартном наборе сит.
Средства контроля и вспомогательного оборудования
1.Весы настольные циферблатные по ГОСТ 29329 или ГОСТ 24104.
2.Шкаф сушильный.
3.Сита и проволочные круглые калибры с отверстиями размерами, соответствующими номинальным размерам зерен данной фракции: 1,25D; D; 0,5(D+d); d, а также 2,5 и 1,25 мм.
Для определения зернового состава отдельных фракций щебня (гравия) должны применяться сита с круглыми или квадратными отверстиями на круглых или квадратных обечайках с диаметром и стороной не менее 300 мм. Стандартный набор сит для щебня (гравия) КСИ должен включать сито с квадратными отверстиями размером 1,25
ммпо ГОСТ 6613 и сита с круглыми отверстиями диаметром 2,5; 5(3); 7,5; 10; 12,5; 15; 20; 25; 30; 40; 50; 60; 70; 80 мм.
Для определения размера зерен крупнее 70 (80) мм следует применять проволочные кольца – калибры различного диаметра в зависимости от ожидаемой крупности щебня (гравия): 90; 100; 110; 120 мм и более.
16
Для рассева фракций от 5 (3) до 20 мм применяют сито с размером отверстий 10 мм.
Порядок подготовки и проведения испытания
Для испытания используют лабораторную пробу по табл. 10, высушенную до постоянной массы.
Пробу просеивают ручным или механическим способом через сита с отверстиями указанных выше размеров, собранные последовательно в колонку, начиная снизу с сита с отверстиями наименьшего размера, при этом толщина слоя щебня (гравия) на каждом из сит не должна превышать наибольшего размера зерен щебня (гравия).
Продолжительность просеивания должна быть такой, чтобы при контрольном интенсивном ручном встряхивании каждого сита в течение 1 мин через него проходило не более 0,1 % общей массы просеиваемой навески. При механическом просеивании его продолжительность для применяемого прибора устанавливают опытным путем.
При ручном просеивании допускается определять окончание просеивания следующим способом: каждое сито интенсивно трясут над листом бумаги. Просеивание считают законченным, если при этом практически не наблюдается падение зерен щебня (гравия).
Обработка результатов испытания
По результатам просеивания вычисляют частный остаток на каждом сите (аi), %, по формуле
a |
mi |
100, |
(1) |
|
|||
i |
m |
|
где mi – масса остатка на данном сите, г; m – масса пробы, г.
Определяют полные остатки (Ai) на каждом сите в процентах от массы пробы, равные сумме частных остатков на данном и на всех ситах с большими размерами отверстий:
Ai = ai + a(I+1) + a(I+2) + … + an, |
(2) |
где a, a(I+1), a(I+2),…,an – частные остатки на i-м сите и всех ситах стандартного набора с большими размерами отверстий;
i, i+1, i+2,…,n – порядковые номера сит стандартного набора.
При определении зернового состава сухим способом сумма частных остатков на ситах при проходах через нижнее сито не должна отличаться больше чем на 2 % от массы навески, определяемой перед испытанием. В случае выполнения этого условия для расчета частного остатка вместо
17
значения массы навески используют сумму частных остатков на ситах и проход. При большей величине указанной разности испытание проводят вторично.
3.3.Определение содержание дробленных зерен
вщебне из гравия
Содержание дробленных зерен в щебне из гравия оценивают количеством зерен, поверхность которых околота более чем наполовину.
Средства контроля
1.Весы настольные циферблатные по ГОСТ 29329.
2.Лупа минералогическая по ГОСТ 25706.
Порядок подготовки проведения испытания
Из лабораторной пробы от каждой фракции испытываемого щебня берут аналитические пробы массой не менее:
0,25 кг – для щебня размером фракции от 5(3) до 10 мм;
1,0 кг – |
то же |
св. 10 |
до 20 мм; |
5,0 кг – |
то же |
св. 20 |
до 40 мм; |
20,0 кг – |
то же |
св. 40 |
мм. |
Пробу в воздушно-сухом состоянии просеивают через сито с отверстиями размерами, равными D и d, и взвешивают остаток на сите с отверстиями, равными d.
Визуальным осмотром (применяя, в необходимых случаях, лупу) определяют дробленые зерна, поверхность которых околота более чем наполовину.
Обработка результатов испытания
Дробленые зерна взвешивают и определяют их содержание их в пробе (Щ) с точностью до 1 % по формуле
Щ |
mi |
100, |
(3) |
|
m
где mi – масса дробленых зерен, г;
m – масса остатка на сите с отверстиями, равными d, г.