
283
.pdfПЛАЗМЕННАЯ НАПЛАВКА ФАСОК КЛАПАНОВ АВТОМОБИЛЬНЫХ ДВИГАТЕЛЕЙ
Методические указания к лабораторной работе по дисциплине
«Восстановление деталей сваркой и наплавкой»
Федеральное агентство по образованию Сибирская государственная автомобильно-дорожная академия
(СибАДИ)
Кафедра «Конструкционные материалы и специальные технологии»
ПЛАЗМЕННАЯ НАПЛАВКА ФАСОК КЛАПАНОВ
АВТОМОБИЛЬНЫХ ДВИГАТЕЛЕЙ
Методические указания к лабораторной работе
по дисциплине «Восстановление деталей сваркой и наплавкой»
Составители М. Я. Швец, В.П. Делис, И.С. Лексутов
(в авторской редакции)
Омск
СибАДИ
2012
1
УДК 621.791:621.8 ББК 30.616
Рецензент: канд. техн. наук, доц. В.И. Гурдин.
Работа одобрена методической комиссией факультета «АТ» в качестве методических указаний к лабораторной работе по дисциплине «Восстановление деталей сваркой и наплавкой» для студентов специальностей.
Плазменная наплавка фасок клапанов автомобильных двигателей: Методические указания к лабораторной работе по дисциплине «Восстановление деталей сваркой и наплавкой» / Составители: М. Я. Швец, В.П. Делис, И.С. Лексутов. – Омск, 2012, - 17 с.
Рассматривается способ восстановления деталей автомобиля плазменной наплавкой с применением порошковых самофлюсующихся материалов.
Табл. 1. Ил. 8. Библиогр.: 4 назв.
Составители: М.Я. Швец, В.П. Делис, И.С. Лексутов, 2012
2
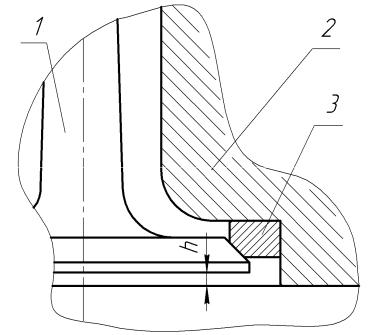
1. ПЛАЗМЕННАЯ НАПЛАВКА ФАСОК КЛАПАНОВ АВТОМОБИЛЬНЫХ ДВИГАТЕЛЕЙ
Цель работы: ознакомление с технологией восстановления фаски тарелки клапана плазменной наплавкой
1.1.Общие сведения
Ресурс работы клапанов автотракторных двигателей лимитируется главным образом износом его фаски. Частые ремонтные перешлифовки клапана приводят к увеличению глубины погружения «h» (рис. 1). Из-за этого увеличивается объем камеры сгорания, что приводит к снижению степени сжатия, а значит, и к ухудшению основных показателей работы двигателя.
Рис. 1. Схема установки клапана: 1 – клапан; 2 – крышка блока цилиндров; 3 – прокладка
Восстановить первоначальную геометрию тарелки клапана можно наплавкой [1-4]. В основе лежит способ плазменной наплавки жаропрочными порошковыми твердыми сплавами за счет подачи порошка в электрическую дугу. Относительно низкая температура плавления порошков (1100 - 1250) С
и наличие в них флюсующих добавок, малая глубина проплавления основы
(0,1 – 0,4) мм [3], позволяет при минимальном перемешивании металлов получить высококачественные наплавленные слои толщиной 2-2,2 мм с
3
гарантированными механическими свойствами. На базе станка У-151
конструкции ИЭС. Им. Е.О. Патона была разработана установка модели ОКС-1192 для автоматической наплавки фаски тарелки клапана.
1.2.Установка для наплавки ОКС-1192
Монтажная схема установки ОКС-1192 (рис. 2) включает: источник постоянного тока 14 с напряжением холостого хода 90-120 (В)
максимальным рабочим током до 500 А. Регулировка рабочего тока осуществляется балластным реостатом 13 типа РБ-300 с номинальным током до 300 А В качестве защитного плазмообразующего транспортирующего газа применяют аргон. Установка ОКС-1192 состоит из двух блоков: автоматики управления режимами наплавки и рабочего.
В рабочий блок входят: вращатель стола 8, порошковый питатель 2,
бункер для порошка 1, плазмотрон 5, ротаметры для определения расхода газа 3,4. К блоку управления относятся: приборная панель 9, балластный реостат 13, блок автоматики 12, блок питания 14.
Установка обеспечивает высокую производительность наплавки.
Время цикла наплавки составляет 25-30 сек.
1.3.Принцип работы установки ОКС – 1192
В наплавочной установке, функциональная схема которой показана на рис. 3, используется плазменная дуга постоянного тока прямой полярности.
Плазменную струю получают по схеме прямого действия, где неплавящийся вольфрамовый электрод 6 является катодом, а клапан 7 – анодом.
Тепловая эффективность струи в широких пределах зависит от величины тока и напряжения, скорости истечения газа, размеров канала внутреннего сопла 5 и расстояния до фаски клапана 7. Плазменная струя,
обладающая более высокой температурой позволяет выполнять наплавку с минимальными тепловложениями в изделие и уменьшить глубину проплавления фаски клапана.
4
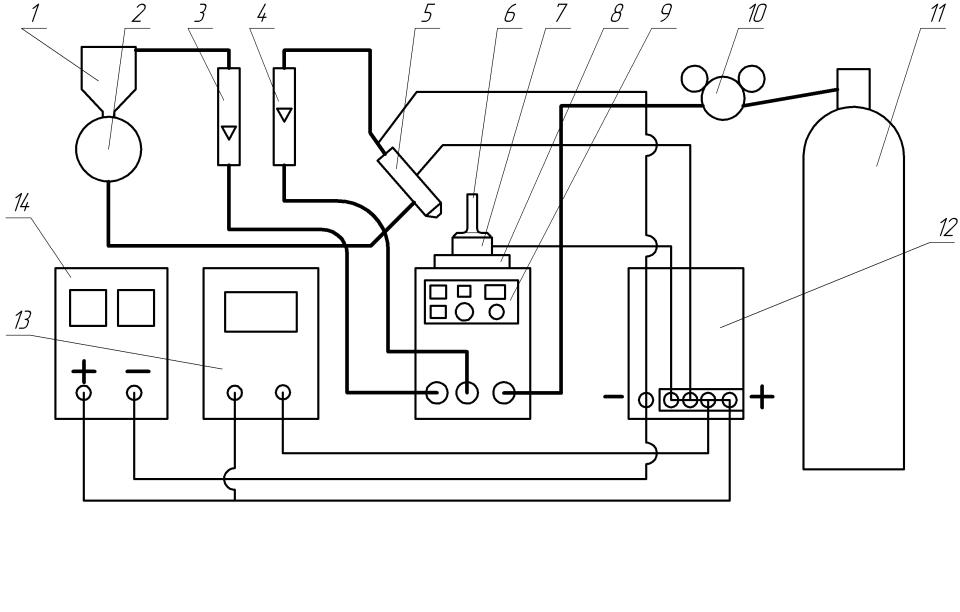
5
Рис. 2. Монтажная схема установки ОКС-1192: 1 – бункер; 2 – порошковый питатель; 3, 4 – ротаметры; 5 – плазмотрон; 6 – клапан; 7 – сменный стол; 8 – вращатель; 9 – приборная панель; 10 – редуктор; 11 – газовый баллон; 12 – блок автоматики; 13 – балластный реостат; 14 – блок питания

Наплавочный порошок, находящийся в герметичном бункере 1, через порошковый питатель 2 транспортируется газом в кольцевой зазор между внутренним соплом 5 и защитным соплом 4 плазмотрона 3. На выходе из плазмотрона порошок изменяет траекторию движения из-за столкновения с конической частью защитного сопла 4 и попадает в столб дуги, расплавляясь на фаске клапана, образует валик, геометрия которого зависит от режимов наплавки. Клапан 7 размещается на водоохлаждаемом сменном столе 8,
установленном на вращателе 9 скорость вращения которого задается в зависимости от диаметра тарелки клапана и режимов наплавки. Источник питания 14 включен в цепь установки ОКС–1192 через дроссель 15,
служащий для защиты электросхемы источника от высоковольтного высокочастотного напряжения, которое вырабатывает осциллятор 11,
служащий для бесконтактного возбуждения дуги в плазмотроне.
Рис. 3. Упрощенная функциональная схема установки ОКС-1192. 1 – бункер с порошком; 2 – порошковый питатель; 3 – плазмотрон; 4 – защитное сопло плазмотрона; 5 – внутреннее сопло плазмотрона; 6 – электрод; 7 – клапан; 8 – сменный стол; 9 – вращатель; 10 – устройство выведения кратера (УВК); 11 – осциллятор; 12 – реостат РБ-300; 13 – токоограничительный реостат; 14 – источник питания; 15 – дроссель
6
Процесс наплавки полностью автоматизирован за исключением установки и снятия клапана со стола. Установив клапан 7 на стол 8 и
включив источник питания 14 в цепь, нажимается кнопка «Пуск».
Происходит предварительная продувка магистрали аргоном с последующим двухэтапным возбуждением дуги. Первой возбуждается слаботочная дежурная дуга между электродом 6 и внутренним столом 5, при помощи высоковольтного разряда тока в межэлектродном зазоре, вырабатываемого осциллятором 11. Выдуваемые аргоном продукты ионизации дежурной дуги достигают фаски клапана, замыкая цепь «электрод – изделие». Возбуждение рабочей дуги происходит током 100–140 А, который устанавливается балластным реостатом 12. Токоограничительный реостат 13 уменьшает ток дежурной дуги до 10 – 20 А, что увеличивает долговечность плазмотрона.
Плазмообразующий газ, подаваемый во внутреннее сопло с расходом
(1,5–2) л/мин обжимает рабочую дугу, уменьшая перегрев внутреннего сопла. После возбуждения рабочей дуги автоматически включается порошковый питатель 2 и вращатель сменного стола. Порошок транспортируется аргоном в плазмотрон при расходе газа (5-7) л/мин.
Геометрия защитного сопла 4 позволяет фокусировать вдуваемый в столб дуги порошок и направлять его на фаску клапана.
В конце цикла наплавки, когда стол 8 совершил полный оборот,
включается устройство выведения кратера 10, которое плавно снижает ток дуги при постоянном расходе порошка. Это препятствует образованию усадочного кратера в наплавляемом валике. После обрыва рабочей дуги отключаются источник питания, порошковый питатель, вращатель стола.
Реле времени в цепи подачи газа обеспечивает кратковременную продувку магистрали аргоном, предохраняя от окисления разогретый электрод.
Наплавленный клапан заменяется следующим, и цикл повторяется. Средняя производительность установки за рабочую смену составляет 100–120
клапанов.
7
1.4.Устройство плазмотрона ВСХИЗО
Образование плазмы происходит при нагреве газа до температуры термической ионизации (более 6000 К). Такой нагрев возможен в центральной части сварочной дуги, и в большей степени под действием энергии сжатой дуги. Сжатие дуги происходит в канале внутреннего сопла 9
плазмотрона (рис. 4) при протекании необходимого расхода плазмообразующего газа. Плазмотрон состоит из двух водоохлаждаемых частей, разделенных изолятором 7. Верхняя часть представляет собой катод,
состоящий из вольфрамового электрода 1, шаровой цанги 2, резьбового зажима 3, медного водоохлаждаемого токосъемника 5, трубок подвода и отвода воду 4, 8. Шаровая цанга 2 обеспечивает подачу плазмообразующего аргона в плазмотрон, и позволяет центровать нижний конец электрода 1 в
канале сопла 9. При фиксации цанги 2 зажимом 3 электрод, установленный в рабочем положении, надежно контактирует с токопроводящим проводником от минусовой клеммы источника.
Между нижней и верхней частями плазмотрона расположен изолятор 7,
изготовленный из текстолита. Защитное сопло 10 выполняет важную функцию – обеспечение защиты наплавляемого слоя от атмосферы воздуха,
при подаче расплавленного порошкового материала на фаску тарелки клапана. Эта конструктивная особенность плазмотрона ВСХИЗО, в отличие от других конструкций, позволяет до (50-60) % сохранить общий расход газа,
уменьшить размеры плазмотрона и улучшить качество защиты сварочной ванны. Порошок подается в кольцевой зазор плазмотрона через трубку 11,
впаянную в защитное сопло со смещением для создания тангенциальной закрутки газового потока. Кроме смещения, трубка установлена с наклоном
7-8 градусов к нормали относительно оси электрода. Это обеспечивает винтообразное движение газового потока. На наружной поверхности сопла 9
равномерно располагаются каналы – уловители порошка, которые позволяют повысить равномерность распределения порошка в кольцевом зазоре и изменить характер его движения от кругового к прямолинейному.
8

Рис. 4. Плазмотрон ВСХИЗО: 1 – электрод вольфрамовый; 2 – цанга; 3 – зажим; 4, 8 – трубки подачи воды; 5 – токосъемник; 6 – втулка резьбовая; 7 – изолятор; 9 – внутреннее сопло; 10 – защитное сопло; 11 – трубка порошкового питателя; 12 – изделие
9