
конспект лекций ТОМ
.pdfтовок.
Закрепление — приложение сил и пар сил к заготовке или изделию для обеспечения их положения, достигнутого при базировании.
Установка— процессбазированияизакреплениязаготовкиилиизделия. Погрешность установки — отклонение фактически достигнутого -сложения
заготовки или изделия при установке от требуемого.
Выбор технологических баз имеет цель наметить как сами базы, такипорядок их смены (если это необходимо). От правильности решения вопроса о технологических базах в значительной степени зависят точность взаимного расположения обрабатываемых поверхностей, точность размеров, степень сложности и конструкция приспособлений, производительность обработки.
Исходными данными для выбора баз являются: чертеж детали со всеми необходимыми требованиями, вид и точность заготовки, условие расположения и работы детали в машине.
Основныепринципы, которымицелесообразноруководствоватьсяпри выборе технологических баз.
1. Использовать принцип совмещения баз, когда в качестве технологических баз, принимают основные, т. е. конструкторские базы, используемые для определения положения детали в изделии. В случае несовпадения конструкторских и технологических баз возникают погрешность базирования и необходимость перерасчета допусков, заданных конструктором в сторону их ужесточения. При этом рассматриваются и решаются технологические размерные цепи.
Погрешность базирования равна сумме погрешностей размеров,
соединяющих конструкторские и технологические базы. Формулы для расчета погрешности базирования для некоторых схем установки приведены на рис. 3.8.
Для других схем формулы приведены в справочниках технолога. следует отметить, что погрешность базирования (как, впрочем, и любая другая погрешность) рассчитывается для конкретных размеров.
Погрешность базирования равна нулю в следующих случаях:
32

при совмещении технологических баз с конструкторскими ; для размеров, получаемых мерным инструментом или блоком инструмен-
тов; длядиаметральных размеров;
при работе методом пробных промеровирабочихходов, т. е. когданастройка положения инструмента производится для каждой заготовки (случай работы на ненастроенном станке).
а,б – на плоские поверхности; в – на оправку; г – в призму; д – в центрах
Рисунок 3.8 – Погрешности базирования при различных схемах ус-
тановки
2.Соблюдать принцип постоянства базы, т. е. использовать на всех основных операциях одни и те же базы. Для выполнения этого принципа часто создают базы, не имеющие конструкторского назначения (например, центровые гнезда у валов и др.).
33
3.Базы должны обеспечивать хорошую устойчивость и надежность установки заготовки.
Основные рекомендации о порядке выбора баз и о задачах, решаемых при этом, представлены в табл. 2.1.
Таблица 2.1– Основные рекомендации о порядке выбора баз и решаемые при этом задачи
Порядок вы- |
Рекомендации по выбору баз |
Задачи, решаемые пра- |
|||||
бора баз |
|
|
|
вильным выбором баз |
|||
|
|
|
|||||
Выбор баз |
При анализе чертежа найти по- |
Применение схемы уста- |
|||||
для завер- |
верхность и элементы, относи- |
новки, |
соответствующей |
||||
шающих |
тельно которых задано и наи- |
положению детали в изде- |
|||||
операций |
более строго лимитировано по- |
лии в процессе эксплуата- |
|||||
техпроцесса |
ложение большинства |
других |
ции, исключающей появ- |
||||
|
поверхностей и элементов. Как |
ление |
погрешности |
бази- |
|||
|
правило, именно эти поверхно- |
рования |
и обеспечиваю- |
||||
|
сти и элементы, обозначенные |
щей |
выполнение |
конст- |
|||
|
на чертеже зачернённым тре- |
рукторских требований |
|||||
|
угольником и принимаются за |
|
|
|
|
||
|
базы |
|
|
|
|
|
|
|
|
|
|
||||
Выбор баз |
1.Поверхности, |
остающиеся |
1. Обеспечивается пра- |
||||
для первой |
необработанными (черные по- |
вильность взаимного рас- |
|||||
операции |
верхности) и связанные разме- |
положения системы об- |
|||||
|
рами с обработанными поверх- |
работанных поверхностей |
|||||
|
ностями, принимаются как ба- |
детали относительно не- |
|||||
|
зы на первой операции |
|
обработанных |
|
|||
|
2.Поверхности, |
принимаемые |
2. Подготавливаются базы |
||||
|
в качестве баз |
должны |
иметь |
для дальнейших опера- |
|||
|
|
|
|
|
|
|
|
34
|
достаточные размеры, более |
ций |
|
|
высокую степень точности и |
3.Обеспечиваются |
воз- |
|
наименьшую шероховатость |
можно малые и равномер- |
|
|
3.На поверхностях, принимае- |
ные припуски |
|
|
мых в качестве баз, не должны |
|
|
|
быть расположены прибыли, |
|
|
|
литники, швы |
|
|
|
4.Необработанные поверхности |
|
|
|
в качестве баз должны исполь- |
|
|
|
зоваться только один раз на |
|
|
|
первой операции |
|
|
|
|
|
|
Выбор баз |
Базы должны быть связаны с |
Подготовка баз для за- |
|
для проме- |
обрабатываемой поверхностью |
ключительных операций |
|
жуточных |
кратчайшей размерной цепью |
|
|
операций |
|
|
|
|
|
|
|
Материализация схемы базирования заключается в выборе типа опор, их количества и расположения относительно заготовки в соответствии со схемой базирования, разрабатываемой технологом.
Конструктором выбираются также тип и место расположения зажимов. При разработке схемы установки используются условные обозначения по ГОСТ 3.1107—81. «Графические обозначения опор, зажимов и установочных устройств».
Схема базирования является техническим заданием на проектирование установочного приспособления. При этом на операционном эскизе на поверхностях и элементах заготовки могут указываться как опорные точки по ГОСТ 21495-76, так и условные обозначения по ГОСТ 3.1107-81.
35
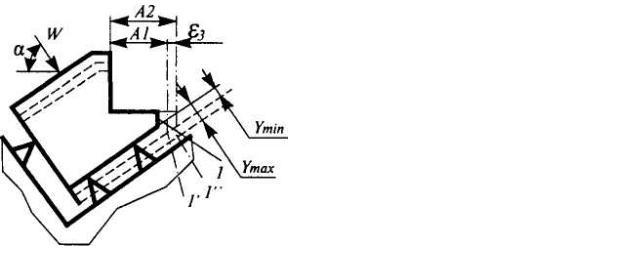
3.1 Погрешностьзакрепленияεз,
Погрешность закрепления ε3 возникает из-за нестабильности смещений отдельных заготовок под действием силы зажима. Погрешность закрепления численно равна разности предельных смещений измерительной базы в направлении получаемого размера под действием силы зажима заготовки.
Схема появления погрешности закрепления при обработке углового паза показана на рис. 3.9.
Под действием силы зажима W измерительная база 1смещается. В силу различных причин, о которых будет сказано ниже, это смещение будет разным для каждой заготовки. Положение измерительной базы, соответствующее наименьшему смещению, обозначено 1, а наибольшему 1”. В результате этого, при обработке заготовки на на строенном станке появляется погрешность закрепления εз = (γmax –γmin)cos α
где α — угол между направлением действия силы зажима и направлением получаемого размера. При расчете погрешности ε, учитываются, как правило, только смещения из-за контактных деформаций в стыках заготовка — установочные элементы. Величина этих смещений определяется по экспе-
риментальной зависимости:
γ = cNWn
Рисунок 3.9 – Схема появления погрешности закрепления
где Nw — сила зажима, приходящаяся на опору (нагрузка на опору);
с — коэффициент, характеризующий вид контакта, материал, шероховатость поверхности и верхний слой заготовки; п — показатель степени (оп-
36

ределяется экспериментально).
Экспериментальные зависимости между нормальной нагрузкой NW и смещением у для различных опор приведены в справочной литературе.
3.2 Погрешность положения заготовки εпр, вызываемая неточностью приспособления
Эта погрешность возникает из-за неточности изготовления и сборки деталей приспособления, их износа и ошибок установки приспособления на станке.
Погрешность εпр численно равна разности предельных состояний измерительной базы относительно установленного на размер инструмента, возникающей вследствие перечисленных причин.
В общем случае погрешность положения заготовки, вызываемая неточностью приспособления, рассчитывается по формуле
εпр = εус2 +εиз2 +εду2 +εи2 +εс2 ,
где εус — погрешность установочных элементов, вызываемая неточностью их изготовления и сборки; εиз — погрешность положения направляющих элементов, вызываемая неточностью их изготовления и сборки; εду — погрешность, возникающая в результате неточности изготовления и сборки делительных устройств; εи – погрешность, возникающая в результате износа детали приспособления (в основном установочных и направляющих элементов); εс — погрешность установки приспособления на станке.
В качестве примера рассмотрим мечет погрешности установки, определяющей отклонение от соосности отверстий D2 и D3 для детали, приведенной на рис. 3.10.
Обработка производится в следующем порядке. На первом этапе за один установ растачиваются отверстия D1 и D2. Затем при базировании на жёсткий палец отверстием D1 обрабатывается поверхность D3.
37

В данном случае погрешность базиро вания равна несоосности между отверстиями и , погрешность закрепления отсутствует, наибольшая часть погрешности составляет максимально возможный зазор между пальцем и отверстием
Рисунок 3.10 – Установка втулки на торец и жёсткий палец
3.3 Базированиезаготовкивприспособлении
Базирование заготовки в приспособлении производится, как правило, двумя или тремя базами, причем оно сводится, по существу, к базированию ее отдельных баз. Обнаружено, что в группе баз значимость каждой из них для данной операции неодинакова. Среди них выделяется основная база. Заготовка, устанавливаемая этой базой в приспособление, получает почти полную ориентацию, лишаясь трех или четырех степеней свободы. Для лишения заготовки остальных степеней свободы используются другие, вспомогательные базы. Основную базу необходимо выделять из группы баз еще и потому, что способ ее базирования принципиально отличается от способа базирования остальных баз. Например, если в качестве баз на операции используют два отверстия, причем одно из них принято за основную базу, то схема базирования по первому отверстию принципиально отличается от схемы базирования по второму отверстию, выполняющему роль дополнительной базы.
Вместе с тем обнаружено, что для разных заготовок может быть ис-
38
пользована одна и та же схема базирования основной базы, если в качестве нее приняты одинаковые по форме поверхности. Таким
образом, способ базирования основной базы определяется в основном ее формой. Например, если у заготовок различной конфигурации в качестве основной базы принята нижняя обработанная поверхность, то при проектировании приспособлений для всех заготовок может быть предусмотрен один и тот же способ базирования — на две опорные пластины.
В связи с этим представляется возможным рассматривать типовые способы базирования основной базы определенной формы безотносительно к форме и размерам заготовок, тем более что круг поверхностей, используемых в качестве основной базы, ограничен тремя видами — плоской поверхностью, цилиндрическим отверстием и цилиндрической наружной поверхностью.
Основную базу выбирает конструктор приспособления. Иногда это делает технолог при разработке технологического процесса, проставляя на операционном эскизе значками тип опорного элемента и число опорных точек. За основную базу предпочтительно брать поверхность, которая обеспечивает заготовке устойчивое положение в приспособлении даже при базировании только одной этой базы. Наиболее полно такому требованию отвечает плоская поверхность заготовки, располагающаяся снизу и обладающая достаточной протяженностью. Если у заготовки такой поверхности нет, выбирают другую поверхность достаточной протяженности — боковую плоскую поверхность, цилиндрическое отверстие либо цилиндрическую наружную поверхность.
На выбор основной базы влияет также точность исходных размеров и допускаемых отклонений расположения обрабатываемой поверхности. За основную следует принимать базу, от которой заданы наиболее точные исходные размеры. На первой операции, когда у заготовки еще нет ни одной обработанной поверхности, за основную базу приходится принимать необработанную поверхность, на последующих операциях — обработанную с наименьшей шероховатостью.
39

Рисунок 3.11 – Выбор основной базы.
Примеры, иллюстрирующие выбор основной базы, приведены на рис. 3.11, где ОБ — основная база, А и В — вспомогательные базы, а обработанная поверхность изображена утолщенной линией.
Из двух баз, представленных на рис. 3.11, а, за основную принята нижняя поверхность. Из трех баз (см. рис. 3.11, б) за основную принята нижняя поверхность, имеющая два участка, один из которых устанавливается на два опорных штыря, а другой — на сблокированную опору. На рис. 3.11, в за основную базу принята обработанная наружная цилиндрическая поверхность, которой заготовка устанавливается на призму, а на рис. 3.11, г — точно обработанное цилиндрическое отверстие, которым заготовка надевается на цилиндрическую оправку, закрепленную на корпусе приспособления.
40

4 КАЧЕСТВО ПОВЕРХНОСТИ ДЕТАЛЕЙ МАШИН И ЗАГОТОВОК
4.1 Влияние технологических факторов на величину шероховатости
На шероховатость поверхности заготовок и деталей оказывают влияние многие технологические факторы. При обработке резанием величина, форма и направление неровностей зависят от методов, режимов и схемы обработки. Каждому методу соответствует определенный диапазон шероховатостей. Из параметров режимов резания наиболее существенное влияние на величину шероховатости оказывают скорость главного движения резания и подача.
Влияние скорости главного движения резания на шероховатость зависит от наростообразования на режущей кромке инструмента, а также от захвата и отрыва слоев, расположенных под режущей кромкой (для стали), и хрупкого выламывания частиц материала (для серого го чугуна и твердых цветных сплавов). Зависимость величины шероховатости от скорости главного движения резания представлена на рис. 4.1, а.
График показывает, что при скоростях порядка 15...30 м/мин имеет место увеличение шероховатости. Причиной является наростообразование на резце.
Рисунок 4.1. Влияние технологических факторов на величину микроне-
ровностей: а —скорости резания; б— подачи; в—радиуса закругления резца
41