
8
11. Библиографический список рекомендуемой литературы
Основной
1.Большаков В.А., Попов В.Н. Гидравлика. Общий курс. – Киев:
Высш. шк., 1989. – 215 с.
2.Гейер В.Г., Дулин В.С., Заря А.Н. Гидравлика и гидропривод. – М.:
Недра, 1991. – 331 с.
3.Гидравлика, гидромашины и гидропривод: Учебник для машиностроительных вузов / Т.М. Башта, С.С. Руднев, Б.Б. Некрасов и др. – М.: Машиностроение, 1982. – 423 с.
4.Свешников В.К., Усов А.А. Станочные гидроприводы: Справочник. – М.: Машиностроение, 1988. – 512 с.
5.Свешников В.К. Станочные гидроприводы: Справочник. – М.: Машиностроение, 1995. – 448 с.
6.Сундуков Г.В. Гидравлика и гидропневмопривод. Иллюстративнодидактические материалы. – Тула: ТулГУ, 2003. – 64 с.
7.Столбов Л.С., Перова А.Д., Ложкин О.В. Основы гидравлики и гидропривод станков. – М.: Машиностроение, 1988. – 256 с.
8.Трифонов О.Н., Иванов В.И., Трифонова Г.О. Приводы автоматизированного оборудования. – М.: Машиностроение, 1991. – 336 с.
Дополнительный
1.Башта Т.М. Машиностроительная гидравлика. – М.: Машиностроение, 1971. – 672 с.
2.Башта Т.М. Гидропривод и гидропневмоавтоматика. – М.: Машиностроение, 1972. – 320 с.
3.Бирюков Б.Н. Гидравлическое оборудование металлорежущих станков. – М.: Машиностроение, 1979. – 112 с.
4.Богданович Л.Б. Гидравлические приводы. – Киев: Высш. шк., 1980. – 231 с.
5.Брон Л.С., Тартаковский Ж.Э. Гидравлический привод агрегатных станков и автоматических линий. – М.: Машиностроение, 1974. – 328 с.
6.Справочное пособие по гидравлике, гидромашинам и гидроприводам / Я.М. Вильнер, Я.Т. Ковалев, Б.Б. Некрасов и др.; Под ред. Б.Б. Некрасова. – Минск: Высш. шк., 1985. – 382 с.
7.Кузнецов В.Г. Приводы станков с программным управлением. – М.: Машиностроение, 1983. – 248 с.
8.Навроцкий К.Л Теория и проектирование гидро- и пневмоприводов. – М.: Машиностроение, 1991. – 384 с.
9.Проектирование гидравлических систем: Учебное пособие / Г.М. Иванов, С.А. Ермаков, С.Л. Коробочкин и др. – М.: Машиностроение, 1992. – 224 с.
10.Слюсарев А.Н. Гидравлические и пневматические элементы и приводы промышленных роботов. – М.: Машиностроение, 1990. – 167 с.
9
11. Юшкин В.В. Основы расчета объемного гидропривода. – Минск:
Высш. шк., 1982. – 93 с.
Стандарты
1. ГОСТ 2.704-76. Правила выполнения гидравлических схем. – Введ. 01.01.78. – М.: Изд-во стандартов, 1986. – 17 с.
2. ГОСТ 2.780-96. Обозначения условные графические. Кондиционеры рабочей среды. Ёмкости гидравлические и пневматические. –
Введ. 01.01.98. – М.: Изд-во стандартов, 1997. – 8 с.
3.ГОСТ 2.782-96. Обозначения условные графические. Машины гидравлические и пневматические. – Введ. 01.01.98. – М.: Изд-во стандартов, 1997. – 19 с.
4.ГОСТ 2.781-96. Обозначения условные графические. Аппараты гидравлические и пневматические, устройства управления и приборы контрольно-измерительные. – Введ. 01.01.98. – М.: Изд-во стандартов, 1997. – 34 с.
5.ГОСТ 2.784-96. Обозначения условные графические. Элементы трубопроводов. – Введ. 01.01.98. – М.: Изд-во стандартов, 1997. – 6 с.
6.ГОСТ 17752-81. Гидропривод объемный и пневмопривод. Термины
иопределения. – Введ. 01.01.82. – М.: Изд-во стандартов, 1982. – 71 с.
7.ГОСТ 17398-72. Насосы. Термины и определения. – Введ. 01.01.73. – М.: Изд-во стандартов, 1978. – 36 с.
8.ГОСТ 28567-90. Компрессоры. Термины и определения. – Введ. 01.07.91. – М.: Изд-во стандартов, 1990. – 26 с.
10
II. Методические указания по выполнению контрольной работы
1. Введение
Целью выполнения данной контрольной работы является закрепление теоретических и практических знаний по курсу "Гидравлика ", полученных студентами в процессе лекционных и лабораторных занятий. При выполнении контрольно-курсовой работы студенты приобретают навыки проектирования и расчета различных гидравлических устройств. При этом студенты знакомятся со справочной литературой и стандартами, в которых содержатся сведения по устройству гидравлической аппаратуры, по условным изображениям на схемах и чертежах различных устройства гидропривода и т.п. Выполнение контрольной работы обеспечивает студенту более успешную работу над выпускной квалификационной работой бакалавра.
Гидроприводы машин разрабатываются, как правило, с использованием унифицированных и стандартных аппаратов, поэтому в контрольно-курсовой работе, наряду со знаниями по выбору элементов гидропривода, студенты приобретают навыки расчета силовых гидравлических насосов, двигателей и соединительных трубопроводов. При выполнении контрольно-курсовой работы студент должен находить наиболее экономичные конструктивные решения.
2. Объем и содержание контрольной работы
Контрольная работа выполняется по индивидуальному заданию, образец которого приведен в приложении 1. Контрольная работа оформляется в виде расчетно-пояснительной записки, причем для подготовки и оформления рекомендуется использовать соответствующие программные средства персонального компьютера. Наличие графической части устанавливается преподавателем.
Контрольная работа оформляется на листах бумаги формата А4 на русском языке. Примерный объем записки – 15 – 25 страниц в зависимости от содержания задания и способа оформления. Записка должна содержать следующие составные части и разделы, которые указаны в порядке их следования:
1)титульный лист;
2)содержание;
3)текст задания на проектирования с перечислением всех исходных
данных;
4)принципиальную схему проектируемого гидропривода;
5)описание структуры и режимов работы проектируемого гидропривода и его элементов с указанием уравнений гидропотоков;
11
6)описание выбора режима работы гидропривода, типа и номинального давления рабочей жидкости;
7)расчет параметров гидродвигателя (-ей);
8)расчет необходимого расхода рабочей жидкости;
9)расчет насосной установки, выбор приводного двигателя;
10)расчет трубопроводов;
11)расчет гидравлических потерь;
12)описание выбора гидроаппаратов (клапанов, распределителей, манометров и т.п);
13)расчет потребляемой мощности и КПД гидропривода;
14)тепловой расчет гидропривода с определением объема гидробака;
15)библиографический список использованной литературы в соответствии с ГОСТ 7.1-84;
В тексте пояснительной записки и расчетах должно соблюдаться единство обозначений и терминологии, принятых в физике и гидравлике. Все расчеты рекомендуется проводить единицах СИ с необходимой точностью. Текст и расчеты должны сопровождаться необходимыми поясняющими схемами и рисунками. Расчетные формулы внутри текста не рекомендуются, они должны выноситься в отдельные строки. Расчетные формулы следует сначала записать в буквенных обозначениях, а затем подставить численные значения входящих в нее величин. Промежуточные расчеты приводить не обязательно.
Для оформления пояснительной записки рекомендуется использовать текстовый процессор Word или аналогичный; поля: слева 25 мм, сверху, снизу, справа – по 20 мм; шрифт Times 14 пт.; межстрочное расстояние – 1 интервал; абзацный отступ – 1,25см. Абзацы выравниваются по ширине, заголовки – по центру. Точки после заголовков обычно не ставятся. Страницы пояснительной записки должны быть пронумерованы, начиная с титульного листа, на титульном листе номер не ставится.
Текст записки разбивается на разделы, подразделы и пункты, которые нумеруются арабскими числами и разделяются между собой точками, например, 2.4.1. Все иллюстрации, таблицы и формулы, содержащиеся в записке, нумеруются в пределах раздела двумя числами, например: Рис. 2.3 – третий рисунок второго раздела. Номер формулы заключается в круглые скобки и помещается справа от формулы, например, (4.2). Как правило, нумеруются только те формулы, на которые есть ссылки в тексте.
Ссылки на используемые литературные и методические источники помещаются в тексте записки в квадратных скобках, например [1] или [2, с. 112], где первое число означает порядковый номер источника в библиографическом списке, а второе число – номер страницы, с которой осуществляется цитирование.
Вкачестве примера оформления библиографического списка использованных источников может служить библиографический список, приведенный в данных методических указаниях. В этот список можно
12
включать все использованные при выполнении курсовой работы источники, включая стандарты, методические указания и конспекты лекций.
Студент должен подписать задание на контрольную работу и титульный лист работы перед сдачей преподавателю и указать дату окончания выполнения работы.
3. Общие указания по выполнению контрольной работы
3.1. Введение
Во введении необходимо отразить достоинства гидравлических приводов и их преимущества по сравнению с другими типами приводов – механическими, электромеханическими и пневматическими.
Принципиальная схема гидропривода в соответствии с заданием приводится в контрольной работе в виде отдельного рисунка в масштабе, удобном для её понимания. Вычерчивание элементов схемы производится в соответствии с требованиями ЕСКД на условные обозначения принципиальных гидравлических схем.
Описание принципиальной схемы начинается о того, что изображено на рисунке в статическом состоянии. Затем производится описание схемы в рабочем состоянии. При этом рассматриваются различные положения распределительного устройства. Последовательно описывается работа всех устройств в положении, изображенном на схеме, а затем – при реверсировании распределителя. После этого описывается поведение системы при перегрузке.
3.2. Выбор рабочей жидкости
Рабочая жидкость служит для передачи энергии от гидронасоса к гидродвигателю, для смазки механизмов и деталей гидравлических устройств, а также для отвода тепла от источников его выделения. К рабочей жидкости предъявляются ряд требований, сводящихся, в основном, к малому изменению ее физико-механических свойств в процессе эксплуатации гидропривода. Основными из этих требований являются следующие:
1)хорошие смазывающие свойства трущихся поверхностей;
2)малое изменение вязкости рабочей жидкости в широком диапазоне изменения рабочих температур и давлений;
3)соответствие вязкости рабочей жидкости посадкам и зазорам внутри гидроагрегатов чтобы избежать чрезмерной утечки жидкости при очень малой вязкости или чрезмерных потерь на трение при слишком большой её вязкости;
4)нейтральность рабочей жидкости по отношению к материалам гидроагрегатов, уплотнениям, покрытиям и прочим элементам гидропривода;
13
5)рабочая жидкость должна быть безопасна как в пожарном отношении, так и для обслуживающего персонала;
6)содержание загрязнений в жидкости, особенно абразивных частиц, должно быть минимальным.
В качестве рабочих жидкостей гидравлических систем в основном используются минеральные масла, получаемые в результате переработки нефти. Наиболее широко в машиностроительных гидроприводах применяются масла индустриальные по ГОСТ 20799-88 марок 12, 20, 30.
При эксплуатации гидропривода необходимо предусмотреть очистку масла от поступающих загрязнений и продуктов износа гидроагрегатов.
3.3. Выбор рабочих давлений
Давление рабочей жидкости в гидроприводе до 5 МПа называется низким, от 5 до 10 МПа – средним, от 10 до 30 МПа – высоким и выше 30 МПа – сверхвысоким. Давление в гидроприводе определяется нагрузкой на выходной элемент гидродвигателя и гидравлическими сопротивлениями, существующими в трубопроводах и гидроаппаратах. Рабочее давление зависит от соотношений между этими величинами.
При более высоких выбранных рабочих давлениях конструкции гидравлических машин получаются более компактными, масса их меньше за счет уменьшения размеров. Однако применение повышенного рабочего давления в гидроприводе осложняется трудностями, связанными с эффективностью уплотнений, с конструкцией клапанов, с необходимостью принимать во внимание упругость рабочей жидкости и др. Следует иметь ввиду, что объемный насос может работать в пределах от наименьшего до наибольшего рабочего давления, допускаемого его конструкцией.
В гидроприводах технологических машин различного назначения применяются давления до 35 МПа и в некоторых случаях – до 50 Мпа. В гидроприводах металлорежущих станков и кузнечно-прессового оборудования в большинстве случаев применяются низкие и средние давления и частично – высокие.
3.4. Основные законы движения жидкости.
При различных гидравлических расчетах большое значение имеет правильное определение режима течения жидкости в гидравлическом агрегате. Режим течения жидкости определяется по числу (критерию) Рейнольдса:
Re = |
υd |
= |
|
4 Q |
|
|
|
|
|
, |
(1) |
||
ν |
πd ν |
где υ,Q – средняя скорость, м/с, и расход рабочей жидкости, м3 /c;
d – внутренний диаметр трубопровода, м;
14
ν – кинематическая вязкость жидкости, м2 /с.
При числе Рейнольдса меньше критического, то есть при Re <Reкр режим течения жидкости будет ламинарным, при Re >Reкр – турбулентным. За критическое значение числа Рейнольдса для круглых гладких труб принимают Reкр =2300.
Для правильного определения потерь, например, давления, по числу
Рейнольдса и относительной шероховатости |
o внутренних стенок трубы |
||
определяет зону сопротивления: |
|
|
|
o = |
d |
, |
(2) |
|
|
|
где – абсолютная шероховатость стенок трубопровода. При расчетах гидропривода используют уравнение Бернулли, уравнение неразрывности потока жидкости и формулы для определения потерь напора и давления по длине трубопровода и в местных сопротивлениях.
4. Расчет гидроцилиндра
4.1. Общие положения
Силовые гидроцилиндры являются гидродвигателями, осуществляющими прямолинейное возвратно-поступательное движение выходного звена (штока). Силовые гидроцилиндры подразделяются на гидроцилиндры одностороннего действия, двухстороннего действия и дифференциальные гидроцилиндры. Основными рабочими элементами каждого силового гидроцилиндра является шток с поршнем (плунжером) и цилиндр. Один из них крепится к объекту неподвижно, а второй совершает возвратно-поступательное движение под давлением рабочей жидкости, действующей на поршень (плунжер), или под действием внешней нагрузки.
При проектировании силовых гидроцилиндров проводятся следующие конструктивные решения и расчеты:
1)выбирается или задается тип гидроцилиндра, ход штока, способ его крепления;
2)определяется или задается внешняя нагрузка, действующая вдоль оси на шток гидроцилиндра;
3)определяется или задается величина рабочего давления в гидроцилиндре;
4)определяются силы, потребные для преодоления внешней нагрузки
вобоих сторонах движения штока;
5)определяется потребные площади поршней по найденным величинам потребной силы и рабочего давления;
6)определяется диаметр штока и толщина стенки цилиндра;
7)выбирается тип уплотнений поршня и штока;
15
8)по условиям компоновки определяется максимально допустимые габаритные размеры гидроцилиндра;
9)по заданной скорости перемещения штока определяется расход рабочей жидкости;
10)разрабатываются рабочие чертежи гидроцилиндра (при наличии в задании соответствующего требования);
11)производится проверочный расчёт гидроцилиндра на прочность и устойчивость после приведения размеров к стандартным размерам.
4.2. Выбор типа гидроцилиндра
Выбор типа гидроцилиндра производится в зависимости от требований, предъявляемых к работе исполнительных устройств технологической машины. Если поршень гидроцилиндра может быть возвращен в исходное положение под действием пружины или под действием силы тяжести, то применяет силовые гидроцилиндры одностороннего действия.
При необходимости надёжного выполнения исполнительным устройством рабочих движений как при выдвижении штока, так и при его втягивании применяет гидроцилиндры двухстороннего действия с односторонним или двухсторонним штоком.
Длина хода L поршня (штока) гидроцилиндра определяется необходимой величиной линейного или углового перемещения рабочего органа машины, приводимого в движение силовым гидроцилиндром. Обычно длина хода берется в пределах L = (4 − 6)D и в некоторых случаях может
быть и больше, достигая 20D ( D – диаметр поршня).
4.3. Расчет диаметра поршня и величины рабочего давления
Усилие, действующее на шток гидроцилиндра, и величина рабочего давления в его поршневой полости связаны уравнением:
|
|
F = Pp Sηн , |
(3) |
где S = |
πD2 |
– площадь поршня, м2 ; |
|
4 |
|
||
ηн |
|
|
|
– механический КПД гидроцилиндра, учитывающий потери на |
|||
трение в |
уплотнениях поршня и штока. Величина механического |
КПД |
находится в пределах ηн =0,85 ... 0,95.
Из уравнения (З) можно найти рабочее давление или площадь поршня:
Pp = |
F |
, |
(4) |
|
ηнS |
||||
|
|
|
S = |
F |
ηн . |
(5) |
P |
|||
|
p |
|
|
16
Диаметр поршня вычисляется по формуле:
P p |
= |
|
|
F |
. |
(6) |
|
η |
н S |
||||||
|
|
|
|
Диаметр штока принимается равным (0,3 ... 0,7) D и затем проверяется из условий прочности штока на продольный изгиб.
В некоторых случаях бывает необходимо знать усилие Fвт ,
развиваемое поршнем при втягивании штока в цилиндр. Это усилие определяется по выражению:
Fвт = |
π |
(D2 |
−d 2 )Ppηн . |
(7) |
|
4 |
|
|
|
Расход жидкости, подаваемый в поршневую полость гидроцилиндра, и скорость движения поршня гидроцилиндра связаны соотношением:
Q =υпS . |
(8) |
Фактический расход жидкости, подаваемый в гидроцилиндр, будет:
Qф = |
Q |
, |
(9) |
ηоб
или
Q =Qфηоб ,
где ηоб – объемный КПД, учитывающий утечки рабочей жидкости в зазорах в подвижных соединениях гидроцилиндра поршня и штока. Величина объемного КПД гидроцилиндра находится в пределах ηоб = 0,98 … 0,99.
Скорость поршня, при подаче жидкости в поршневую полость, равна
υп = |
Q |
= |
|
4Q |
|
|
||||
|
|
|
. |
|
(10) |
|||||
S |
π 2 |
|
||||||||
|
|
|
|
|
|
D |
|
|
||
При подаче рабочей жидкости в штоковую полость гидроцилиндра, |
||||||||||
скорость υшт поршня будет равна |
|
|
|
|
Q |
|
|
|||
υшт = |
|
|
|
|
. |
(11) |
||||
|
|
|
|
|
|
|||||
n(D2 − d 2 ) |
||||||||||
|
|
|
|
4.4. Расчет гидроцилиндра на прочность
Силовые гидроцилиндры при работе подвергаются действию внутреннего давления рабочей жидкости и внешней нагрузки. На прочность должны рассчитываться все детали и элементы силового гидроцилиндра – цилиндры (гильзы), крышки, поршни, штоки, узлы крепления и пр. Элементы
гидросистемы рассчитываются на так называемое условное давление Py ,
которое превышает рабочее на 20–30% : |
|
Py =(1,2 … 1,3) Pp . |
(12) |
Это делается о целью создания большей гарантии от гидравлических ударов, толчков и т.п.

17
Приближенно, толщина стенки δ y цилиндра определяется по формуле:
δ y = |
Py D |
, |
(13) |
|
|||
|
2σдоп |
|
|
где σдоп – допустимое напряжение, для углеродистой |
конструкционной |
||
стали принимается равным σдоп =(400...500)10 5 Па. |
|
||
Наружный диаметр цилиндра будет равен |
|
||
Dм = D + 2σy |
(14) |
Величины, полученные по формулам (13) и (14), округляются в большую сторону до нормализованных значений. Силовые гидроцилиндры, имеющие значительный ход штока ( L >10 d ), должны также рассчитываться на продольную устойчивость.
5. Расчет трубопроводов
Расчет трубопровода проводится с целью определения его геометрических размеров и потерь давления. Исходными данными для расчета трубопровода являются давление рабочей жидкости, ее расход, скорость течения, а также количество местных сопротивлений. При расчете трубопроводов большое значение имеет правильный выбор скорости течения жидкости. В случаях малых скоростей жидкости увеличиваются размеры, вес и стоимость трубопровода и всей смонтированной на нем гидроаппаратуры. Наоборот, большие скорости жидкости приводят к уменьшению размеров трубопровода, но одновременно и к большим затратам энергии, что может повести к значительному нагреву рабочей жидкости. На практике были найдены наиболее удовлетворительные скорости течения рабочей жидкости, которые равны:
–во всасывающем трубопроводе υвс = 0,5 ... 1,5 м/с;
–в сливном трубопроводе υсл = 1 ... 2 м/с;
–в напорном трубопроводе υн = 3 … 5 м/с.
При этом большие значения υн берутся для гидросистем с большим
давлением рабочей жидкости (10 МПа и выше).
По выбранной или заданной соответствующей скорости определяются внутренние диаметры соответствующих трубопроводов:
всасывающего |
d вс=1,13 |
Qф |
, |
(15) |
||
|
|
|
|
υ |
|
|
|
|
|
|
вс |
|
|
напорного |
dн =1,13 |
Qф |
, |
|
|
(16) |
υ |
|
|
||||
|
|
|
|
|
|
|
|
|
н |
|
|
|
|
сливного |
dсл =1,13 |
Qф |
|
. |
|
(17) |
υ |
|
|
||||
|
|
|
|
|
|
|
|
|
сл |
|
|
|
|

18
Полученные при расчете значения диаметров округляется, как правило, в большую сторону до ближайшего стандартного значения.
Толщина стенки σ трубопровода проверяется из условия прочности по формуле:
σ = |
Pdk |
, |
(18) |
2σд |
где P – максимальное давление в трубе, Па; d – внутренний диаметр трубы, м;
k– коэффициент безопасности (запаса);
σд – допускаемое напряжение на растяжение материала трубы, Па.
При расчете потерь давления в трубопроводах используется уравнение,
учитывающее, что суммарные потери равны сумме потерь напора на трение |
||
по длине ∑hпдлi |
и потерь напора в местных сопротивлениях |
∑hпмi : |
Pп |
= γ ∑ h п = γ ( ∑ h пдл i + ∑ h пм i ), |
(19) |
где γ – удельный вес рабочей жидкости, Н/м3 ; |
(20) |
|
|
γ = ρg |
ρ - плотность жидкости, кг/м3 ;
g – ускорение свободного падения, 9,81 м/с2 .
Для определения потерь давления необходимо знать режим течения жидкости и зону сопротивлений. Потери напора на трение по длине в соответствующем трубопроводе определяется по формуле Дарси-Вейсбаха:
|
|
hдлi |
= λi |
|
liυi2 |
. |
(21) |
||
|
|
|
|
||||||
|
|
|
|
|
|
di 2g |
|
||
Потери напора в местных сопротивлениях определяются по формуле |
|||||||||
Вейсбаха: |
|
|
|
υ 2 |
|
|
|
||
|
|
h |
=ξ |
|
|
|
|
||
|
|
i |
|
i |
, |
|
(22) |
||
|
|
пмi |
|
2g |
|
||||
|
|
|
|
|
|
|
|
||
где υi |
– средняя скорость течения жидкости, м/с; |
|
|||||||
li , di |
– длина и внутренний диаметр трубопровода, м; |
||||||||
λi |
– |
коэффициент сопротивления трения, |
зависящий от режима |
||||||
течения жидкости и относительной шероховатости |
c трубопровода. При |
определении относительной шероховатости величину абсолютной шероховатости можно принять для стальных труб =0,03 ... 0,05 мм, для труб из цветных металлов =0,002 ... 0,01 мм;
ξi – коэффициент местного сопротивления, зависящий от режима
течения жидкости и вида местного сопротивления.
Суммарные потери давления для соответствующего трубопровода вычисляются по формуле:

|
|
|
19 |
|
|
|
∑hпi = |
υi |
2 |
(λi |
li |
+∑ξi ) . |
(23). |
|
|
|||||
|
2g |
|
di |
|
Для определения коэффициента сопротивления трения λ по формуле
(1) находим число Рейнольдса, по которому устанавливаем режим течения жидкости и соответствующую зону сопротивлений в трубопроводе. При
ламинарном течении жидкости коэффициент λ |
определяется по |
||||
эмпирической формуле: |
|
||||
λ = |
64 |
, |
(24) |
||
Re |
|||||
или по формуле |
|
||||
λ = |
75 |
. |
(25) |
||
Re |
Формула (25) учитывает охлаждение слоев жидкости, прилегающих к стенкам трубопровода, и поэтому является более предпочтительной. При турбулентном режиме течения жидкости учитываются следующие зависимости.
1. Зона гидравлически гладких труб, когда величина выступов
шероховатости труб меньше толщины ламинарной пленки |
δпл , |
||||||||||||||||||||||
определяемой по уравнению |
|
|
= 30d . |
|
|
|
|
||||||||||||||||
|
|
|
|
|
|
|
|
δпл |
|
(26) |
|||||||||||||
|
|
|
|
|
|
|
|
|
|
|
R |
|
|
|
λ |
|
|
|
|
||||
|
|
|
|
|
20d |
|
|
|
|
e |
|
|
|
|
|
|
|
|
|
|
|
||
|
|
При этом Reкр <Re < |
|
и коэффициент λ определяется по формуле: |
|||||||||||||||||||
|
|
||||||||||||||||||||||
|
|
|
|
|
|
|
|
λ = 0,3164 ; |
|
(27) |
|||||||||||||
|
|
|
|
|
|
|
|
|
|
4 Re |
|
|
|
|
|
|
|
|
|
|
|||
|
|
2. Переходная зона (не |
|
полностью |
шероховатые трубы), |
когда |
|||||||||||||||||
20 |
d |
< Re < 500 |
d |
, коэффициент λ определяется по формуле: |
|
|
|
||||||||||||||||
|
|
|
|
|
|||||||||||||||||||
|
|
|
|
λ = 0,11( |
|
+ |
68 |
|
)0.25 . |
|
(28) |
||||||||||||
|
|
|
|
d |
|
|
|
||||||||||||||||
|
|
|
|
|
|
|
|
|
|
Re |
|
|
|
|
|
|
|
|
|
|
|
||
|
|
3. Зона гидравлически |
шероховатых |
труб, когда Re |
≥500 |
d |
, |
||||||||||||||||
|
|
|
|||||||||||||||||||||
коэффициент λ определяется по формуле |
|
|
|
|
|
|
|
|
|||||||||||||||
|
|
|
|
λ = |
|
|
|
|
1 |
|
|
|
|
|
|
, |
|
(29) |
|||||
|
|
|
|
(1,14 + 2 lg |
d |
) |
2 |
|
|||||||||||||||
|
|
|
|
|
|
|
|
|
|
|
|||||||||||||
|
|
|
|
|
|
|
|
|
|
|
|
|
|
|
|||||||||
или по формуле, близкой к предыдущей: |
|
|
|
|
|
|
|
|
|
|
|||||||||||||
|
|
|
|
|
|
|
|
λ = 0,11( |
d |
)0,25 . |
(30) |
||||||||||||
|
|
|
|
|
|
|
|
|
|
|
|
|
|
|
|
|
|
|
|
20
6. Подбор агрегатов гидропривода
Основными параметрами, по которым осуществляется подбор гидроагрегатов, являются давление (напор) и расход (подача) жидкости.
6.1. Подбор гидронасоса
При выборе насоса, кроме давления и расхода, принимают во внимание ряд требований, такие, например, как надёжность в эксплуатации, удобство монтажа, обслуживания, затраты энергии, КПД и ряд других.
Давление, развиваемое насосом, определяется по формуле
Pн = Pp +γ ∑hП , |
(31) |
где Pp – рабочее давление, определяемое выражением (4);
∑hП – суммарные потери, равные сумме потерь во всасывающем, напорном и сливном трубопроводах:
∑hП =∑hПвс |
+ ∑h Пн + ∑hПсл . |
(32) |
|
Теоретическая подача насоса определяется по формуле |
|
||
Qm = |
Qф |
, |
(33) |
|
|||
η |
|
|
|
|
обн |
|
|
где Qф – фактическая подача, определяется по формуле (9);
ηоб – объемный КПД насоса, зависящий от типа насоса и выбираемый
по справочным данным.
Мощность, потребляемая насосом, определяется по формуле
|
N П |
= |
|
PнQф |
(кВт), |
(34) |
|
|
1000 |
||||||
|
Pн – давление насоса, Па; |
|
|
|
|
||
где |
|
|
|
|
|
|
|
|
Qф – подача насоса, м3 /с. |
|
|
|
|
|
|
|
Полная потребляемая мощность насосом будет равна |
|
|||||
|
Nдв = |
|
N П |
, |
|
(35) |
|
|
|
|
|
||||
|
η – полный КПД насоса, |
|
|
η |
|
|
|
где |
определяется по справочным |
данным в |
зависимости от типа и модели насоса.
По этим данным, округленным в большую сторону, подбирается типоразмер насоса, и определяется его полная техническая характеристика.
6.2. Выбор гидрораспределителя
Гидрораспределители осуществляют подачу рабочей жидкости под давлением в одну из полостей гидроцилиндра и одновременно отвод её из
21
противоположной полости в резервуар. Наибольшее распространение получили золотниковые распределители, основным преимуществом которых является простота управления, высокий объемный КПД, а также уравновешенность золотника в радиальном и в осевом направлении.
Гидрораспределители подбираются по наибольшему рабочему давлению и номинальному расходу. Для подбора гидрораспределителя давление вычисляется по формуле (31), а расход – по формуле (9).
Потери давления в гидрораспределителе определяются из его технической характеристики. С целью снижения массы иногда допускают увеличение расхода через гидрораспределитель, но не более чем на 40% относительно указанного в его технической характеристике наибольшего расхода. В этом случае потери давления будут увеличиваться и определяться по приближенной формуле:
PГ.Р. |
= Pн ( |
Qф |
)2 , |
(36) |
|
||||
|
|
Qн |
|
где Qн и Pн – соответственно расход и потери давления при номинальном
режиме, указанном в технической характеристике гидрораспределителя. Если величина потерь, определенная по формуле (36), окажется
значительной, необходимо изменить величины номинального давления и расхода рабочей жидкости.
6.3. Выбор предохранительного клапана
Предохранительный клапан обеспечивает защиту гидропривода от перегрузок. Предохранительный клапан подбирается по максимальным значениям давлению и расхода рабочей жидкости. Давление настройки предохранительного клапана выбирается таким, чтобы оно было больше на 20 ... 40% рабочего давления в гидроприводе. При использовании предохранительного клапана в качестве переливного, давление настройки клапана обеспечивается на 10...15% больше рабочего давления.
6.4. Выбор фильтра
Тип фильтра выбирается по требуемой тонкости фильтрации рабочей жидкости, по ее расходу и давлению. Наибольшая долговечность работы агрегатов гидропривода обеспечивается при установке фильтров с тонкостью фильтрации 0,01 мм и менее. Однако такие фильтры имеют малую пропускную способность.
Наибольшее распространение получили пластинчатые и сетчатые фильтры с тонкостью фильтрации 0,06 ... 0,15 мм. Обычно эти фильтры устанавливаются в сливной магистрали, и через фильтр проходит весь расход жидкости. На входе в резервуар устанавливается заливной фильтр, обеспечивающий тонкость фильтрации 0,1 ... 0,2 мм. Тонкость фильтрации
22
рекомендуется техническими характеристиками насосов. Расход жидкости через фильтр определяется по уравнению (9). Фильтры тонкой очистки (тонкость фильтрации менее 0,01 мм) устанавливаются в ответвлении напорного трубопровода, через которое проходит не более 10 ... 20% общего расхода рабочей жидкости. На входе в гидронасос устанавливают сетчатый фильтр грубой очистки с большой пропускной способностью.
6.5. Резервуар для рабочей жидкости
Емкость резервуара для рабочей жидкости определяется из условия, чтобы обеспечить помещение достаточного количества рабочей жидкости для заполнения всех объемов гидроагрегатов, а также изменение объемов в процессе работы и вследствие температурного расширения. Объем резервуара должен обеспечить достаточную теплоотдачу окружающей среде, чтобы температура масла в гидроприводе не повышалась выше 50–60°С. Поэтому обычно в гидроприводах объем резервуаров выбирается равным 2- 3-трехминутной производительности насоса или рассчитывают объем резервуара по различным эмпирическим формулам, приводимым в литературе. Для уменьшения объема резервуар может оснащаться охлаждающим устройством. Резервуар заполняется рабочей жидкостью не более чем на 80–85% геометрического объема с целью компенсации теплового расширения жидкости.
7.Библиографический список
1.Абрамов Е.И., Колесниченко К.А., Маслов В.Т. Элементы гидропривода: Справочник. – Киев: Техника, 1979. – 320 с.
2.Бирюков Б.Н. Гидравлическое оборудование металлорежущих станков. – М.: Машиностроение, 1979. – 112 с.
3.Богданович Л.Б. Гидравлические приводы. – Киев: Высш. шк., 1980.
–231 с.
4.Брон Л.С., Тартаковский Ж.Э. Гидравлический привод агрегатных станков и автоматических линий. – М.: Машиностроение, 1974. – 328 с.
5.Справочное пособие по гидравлике, гидромашинам и гидроприводам / Я.М. Вильнер, Я.Т. Ковалев, Б.Б. Некрасов и др.; Под ред. Б.Б. Некрасова. – Минск: Высш. шк., 1985. – 382 с.
6.Кузнецов В.Г. Приводы станков с программным управлением. – М.: Машиностроение, 1983. – 248 с.
7.Навроцкий К.Л Теория и проектирование гидро- и пневмоприводов.
–М.: Машиностроение, 1991. – 384 с.
8.Проектирование гидравлических систем: Учебное пособие / Г.М. Иванов, С.А. Ермаков, С.Л. Коробочкин и др. – М.: Машиностроение, 1992. – 224 с.
23
9.Свешников В.К. Станочные гидроприводы. – М.: Машиностроение, 1995. – 448 с.
10.Юшкин В.В. Основы расчета объемного гидропривода. – Минск:
Высш. шк., 1982. – 93 с.

24
Приложение 1
Образец бланка задания на контрольную работу
ГОУ ВПО "Тульский государственный университет"
Кафедра "Автоматизированные станочные системы"
Гидравлика
ЗАДАНИЕ на контрольную работу
"Расчет объемного гидропривода поступательного движения"
Вариант ____ |
|
Студенту группы _______________ |
____________________ |
(индекс группы) |
(фамилия, инициалы) |
Исходные данные для расчета:
1)тип гидронасоса – ___________________________________________
2)тип гидродвигателя – ________________________________________
3)нагрузка (мощность) на рабочем органе - _______________________
4)скорость рабочего органа – ___________________________________
5)длина напорного трубопровода, м – ____________________________
6)длина сливного трубопровода, м – _____________________________
7)тип гидрораспределителя – ___________________________________
8)способ управления гидрораспределителем – _____________________
9)режим работы гидропривода – ________________________________
Содержание отчета:
1)принципиальная схема гидросистемы;
2)описание по схеме порядка работы агрегатов гидросистемы;
3)расчет основных параметров агрегатов гидросистемы;
4)расчет трубопроводов;
5)расчет гидроцилиндра;
6)подбор основных агрегатов гидросистемы.
Задание выдал: ________________________ |
_____________________ |
(подпись руководителя)(Ф.И.О. руководителя) |
|
Задание получил: ___________________ |
_______________________ |
(подпись студента, дата) |
(Ф.И.О. студента) |

25
Приложение 2
Образец титульного листа контрольной работы
Федеральное агентство по образованию ГОУ ВПО "Тульский государственный университет"
Кафедра "Автоматизированные станочные системы"
Гидравлика
КОНТРОЛЬНАЯ РАБОТА "Расчет объемного гидропривода поступательного движения"
Выполнил студент группы _________________ ________________
Проверил преподаватель __________________ ________________
Тула 2008

26
Приложение 3
Образец содержания контрольной работы
ИСХОДНЫЕ ДАННЫЕ ДЛЯ РАСЧЕТА
1)Тип гидронасоса – пластинчатый;
2)гидродвигатель – один поршневой гидроцилиндр двухстороннего действия с двухсторонним штоком;
3)максимальная нагрузка на рабочем органе – 38 кН;
4)максимальная скорость рабочего органа – 0,33 м/с;
5)суммарная длина напорного трубопровода, м – 5,0;
6)суммарная длина сливного трубопровода, м – 5,0;
7)гидрораспределитель – один трехпозиционный;
8)способ управление гидрораспределителем – электромагнитный;
9)тип напорного и сливного трубопроводов – жесткие стальные;
10)фильтр – один, установлен в сливной гидролинии;
11)режим работы гидропривода – продолжительный;
12)режим нагружения гидропривода – средний;
13)тип рабочей жидкости – минеральное масло;
14)температура окружающего воздуха – +5 – +40°С.
1.Принципиальная схема гидравлического привода
Ц
5 6
РII I III
МН |
3
КП 2
Н M
1
7
4
8
AT
Ф
Б
Рис. 1. Принципиальная схема гидравлического привода
Условные обозначения элементов гидравлического привода: Б – резервуар для рабочей жидкости (гидробак); Н – насос гидравлический нерегулируемый; М – приводной асинхронный электродвигатель;
КП – клапан предохранительный переливной регулируемый; МН – манометр;
Р – трехпозиционный 4-линейный гидравлический распределитель с дистанционным электромагнитным управлением;
27
Ц – гидравлический цилиндр двухстороннего действия с двухсторонним штоком; АТ – аппарат теплообменный (маслоохладитель); Ф – фильтр масляный полнопоточный.
Условные обозначения трубопроводов:
1– всасывающий трубопровод;
2– напорный трубопровод;
3, 4 – участки сливного трубопровода; 5, 6 – трубопроводы, соединяющие распределитель с гидроцилиндром.
2. Описание работы гидравлического привода
Первичной частью гидропривода является насос Н пластинчатого типа, создающий напор рабочей жидкости, в качестве которой используется минеральное масло. Насос приводится в действие от асинхронного электродвигателя М. Энергия рабочей жидкости преобразуется в механическую работу с помощью гидравлического двигателя объемного типа – гидравлического цилиндра Ц, штоки которого соединены с рабочим органом технологической машины (на схеме не показан). Гидропривод имеет разомкнутую циркуляцию рабочей жидкости, резервуаром рабочей жидкости служит масляный бак Б закрытого типа. Жидкость в баке находится под атмосферным давлением.
Для управления механизмами, приводимыми в движение гидроприводом, для обеспечения заданных скоростей и схемы движения, последовательности работы механизмов посредством соответствующего изменения давления и расхода рабочей жидкости в данном гидроприводе предусмотрены направляющий (распределитель Р) и регулирующий (предохранительный клапан КП) гидравлические аппараты. Перемещение золотника распределителя вправо или влево осуществляется посредством двух электромагнитов. В среднее (исходное) положение золотник устанавливается при обесточенных электромагнитах с помощью двух пружин.
Необходимые качественные показатели и состояние рабочей жидкости (вязкость, температура, степень очистки) поддерживаются кондиционерами рабочей жидкости: масляным фильтром Ф и маслоохладителем АТ. Охлаждение масла также осуществляется в масляном баке Б.
Гидропривод работает следующим образом. Насос Н всасывает масло из бака Б и подает его под давлением в гидроцилиндр Ц через распределитель Р. Распределитель имеет две рабочие и одну нейтральную позицию, обозначенные на схеме римскими цифрами I, II, III. При установке золотника распределителя в среднее положение I под
действием пружин образуется следующий гидропоток: |
|
(Р − I )3( АТ)4(Ф)8(Б) |
. |
(Б)1(Н)2 |
|
(КП)7(Б) |
|
В среднем положении распределителя рабочие полости гидроцилиндра заперты, а насос разгружается – перекачивает масло с небольшим давлением через распределитель по сливному трубопроводу в бак. В этом положении распределителя происходит холостой ход гидропривода.
При установке распределителя в положение II включается ход поршня гидроцилиндра вправо по схеме. При этом образуется следующий гидропоток:
(Б)1(Н)2 |
(Р − II )5(Ц →) /(Ц)6(Р)3( АТ)4(Ф)8(Б) |
. |
|
||
|
(КП)7(Б) |
|
28
Масло подается в левую по схеме полость гидроцилиндра, при этом масло из правой полости сливается в бак.
При установке распределителя в положение III включается ход поршня гидроцилиндра влево по схеме. При этом образуется следующий гидропоток:
(Б)1(Н)2 |
(Р − III )6(Ц ←) /(Ц)5(Р)3( АТ)4(Ф)8(Б) |
. |
|
||
|
(КП)7(Б) |
|
Масло подается в правую по схеме полость гидроцилиндра, при этом масло из левой полости гидроцилиндра сливается в бак.
Поскольку данный гидропривод является нерегулируемым, то избыток масла от нерегулируемого насоса при рабочем ходе поршня гидроцилиндра сливается в бак через переливной клапан КП, который также предохраняет агрегаты гидропривода от перегрузки при недопустимо высоком давлении масла. Давление масла при работе гидропривода контролируется с помощью манометра МН.
3.Выбор номинального давления и марки рабочей жидкости
Впервую очередь необходимо определить режимы работы данного гидропривода. Поскольку задан средний режим нагружения гидропривода, то он характеризуется следующими характеристиками:
– интенсивность использования рабочего органа машины – 100 – 200 включений
вчас;
–коэффициент использования номинального давления kд – 0,4 – 0,7;
–коэффициент продолжительности работы гидропривода под нагрузкой kн –
0,3 – 0,5.
Исходя из того, что был задан пластинчатый гидронасос, то номинальное давление рабочей жидкости выбирается равным 6,3 МПа, что соответствует нормальному ряду номинальных давлений по ГОСТ 6540-68.
Выбор марки рабочей жидкости определяется режимом работы гидропривода, температурными условиями его работы, номинальным давлением рабочей жидкости. Проектируемый гидропривод предназначен для работы при положительных температурах окружающей среды, а максимальная температура рабочей жидкости не должна превышать 70°С. Перечисленным условиям соответствует минеральное масло марки МГ20, которое предназначено для применения в гидроприводах, работающих при положительных температурах в закрытых помещениях. Масло МГ20 обладает следующими номинальными техническими характеристиками:
–кинематическая вязкость при 50°С – 20 мм2/с (20 сСт);.
–температура застывания – –40°С;
–температура вспышки – 180°С;
–плотность при 50°С – 895 кг/м3.
4. Расчет гидравлического цилиндра
Внутренний диаметр гидроцилиндра, или диаметр поршня, определяется в зависимости от направления действия рабочего усилия на рабочий орган машины. Гидроцилиндр с двухсторонним штоком совершает рабочий ход при выталкивании штока в обоих направлениях движения поршня, поэтому внутренний диаметр цилиндра D (мм) рассчитывается по следующей формуле [4, формула 4.2]:

29
D = 35,7 |
|
P |
|
, |
|
p |
|
|
|||
|
− p |
|
η |
мц |
|
|
|
||||
|
ψ |
|
ш |
||
|
|
|
|
|
где P – заданное рабочее усилие, кН; p – рабочее давление масла на входе в
гидроцилиндр, МПа; ψ = |
D2 |
– коэффициент мультипликации, равный отношению |
||
D2 |
−d 2 |
|||
|
|
площадей поршня в поршневой и штоковой полостях гидроцилиндра; d – диаметр штока; ηмц – механический КПД гидроцилиндра; pш – противодавление, возникающее
вследствие вытекания масла из гидроцилиндра и определяемое сопротивлением движению масла по сливной гидролинии. Предварительно можно принять pш = 0,3 ... 0,5 МПа.
Механический КПД для неизношенного гидроцилиндра принимаем равным 0,95. Тогда расчетный внутренний диаметр гидроцилиндра будет равен
D = 35,7 6,3 |
38 |
≈109,7 мм. |
|||
|
|||||
|
|
|
−0,5 |
0,95 |
|
1,33 |
|||||
|
|
|
Полученную величину округляем в большую сторону до ближайшего нормального (стандартного) значения: D =110 мм. Диаметр штока при ψ =1,33 будет равен d =50 мм.
Диаметры штоков с обоих сторон поршня равны.
После округления диаметров цилиндра и штока вычислим развиваемое гидроцилиндром рабочее усилие при номинальном давлении масла:
P =10 |
−3 |
|
π |
D |
2 |
|
|
p |
− p |
|
|
|
|
3,14159 |
|
2 |
6,3 |
|
|
≈ 38,25 кН . |
|||
|
|
|
|
|
|
|
|
η |
|
= |
|
110 |
|
|
|
|
|
− 0,5 |
0,95 |
||||
|
4 |
|
|
|
|
4000 |
|
1,33 |
|||||||||||||||
|
|
|
|
|
|
ψ |
|
ш |
|
мц |
|
|
|
|
|
|
|
Расчетное усилие на штоке гидроцилиндра получилось не меньше, чем заданная нагрузка на рабочем органе машины.
Определим расход масла, потребляемого гидроцилиндром. Для получения заданной скорости υ (м/мин) скорости поршня в полость гидроцилиндра с площадью поршня F (м2) следует подать теоретический расход (л/мин) при условии, что объемный
КПД неизношенного гидроцилиндра с новыми уплотнениями η o |
= 0 , 98 : |
|||||
Qц = |
103 υ F |
=1000 19,8 |
3,14159 |
(1102 |
−502 ) 10−6 |
≈152 л/мин |
|
4 0,98 |
|||||
|
ηo |
|
|
|
где υ = 0,33 60 =19,8 м/мин – максимальная заданная скорость поршня.
Поскольку гидроцилиндр имеет двухсторонний шток, то такой же объем масла будет вытесняться в сливной трубопровод из противоположной полости гидроцилиндра.
5.Выбор гидронасоса
Впроектируемом однопоточном гидроприводе один насос обеспечивает питанием единственный гидродвигатель, поэтому его расчетная подача должна быть не менее
30
теоретического расхода масла, подаваемого в гидроцилиндр: Qн = Qц =152 л/мин. Величина Qн равна расходу гидропривода.
По справочнику [3] выбираем однопоточный пластинчатый насос двойного действия модели Г12-26АМ, который характеризуется следующими основными техническими параметрами:
–рабочий объем – 224 см3;
–номинальная подача – не менее 200 л/мин;
–номинальное давление на выходе из насоса – 6,3 МПа;
–максимальное давление – 7,0 МПа;
–номинальная частота вращения вала – 960 мин-1;
–максимальная частота вращения вала – 960 мин-1;
–минимальная частота вращения вала – 600 мин-1;
–номинальная потребляемая мощность – 24,5 кВт;
–затрачиваемая мощность при давлении на выходе из насоса, равном нулю, – 4,8 кВт;
–объемный КПД при номинальном режиме работы – не менее 0,95;
–полный КПД при номинальном режиме работы – не менее 0,87;
–технический ресурс – не менее 2000 часов;
–масса – 40 кг.
Исходя из продолжительного режима работы гидропривода для привода насоса выбираем асинхронный электродвигатель с короткозамкнутым ротором типа 4А200М8У3 с синхронной частотой вращения 750 мин-1 (асинхронная частота вращения 720 мин-1) и номинальной мощностью 18 кВт [1]. Подача насоса Г12-26АМ при частоте вращения приводного вала 720 мин-1 будет равна:
Qн = nдв qн ηон = 720 224 0,95 =153216 см3/мин или Qн ≈153 л/мин.
Максимальное давление, которое может развивать насос при перегрузках, ограничивается предохранительным клапаном. Предохранительный клапан должен открывается при давлении, превышающем расчетное давление насоса, на 15 – 30 %. Исходя из указанного условия и технических параметров насоса Г12-26АМ, давление настройки предохранительного клапана устанавливается равным 7,0 МПа. Поскольку насос Г12-26АМ имеет постоянную производительность, то избыток подаваемого насосом в гидроцилиндр масла будет сливаться в бак через переливной золотник предохранительного клапана.
6.Расчет гидролиний
6.1.Расчет диаметров трубопроводов
Расчет гидролиний состоит в определении внутреннего диаметра трубопроводов и потерь давления, возникающих при движении рабочей жидкости по трубопроводам и другим элементам гидропривода. Расчет трубопроводов производится по участкам, на которые разбивается гидравлическая схема гидропривода. Под участком понимается часть гидролинии между разветвлениями, пропускающая постоянный расход и имеющая постоянный диаметр. Участок может представлять собой прямолинейный участок трубы либо на нем могут быть присутствовать различные местные сопротивления (колена, тройники, крестовины, штуцеры и другие).
Внутренний диаметр (мм) жесткой металлической трубы или гибкого резинометаллического рукава предварительно определяется по формуле

31
d = 4,6 Qv ,
где Q – расход жидкости на рассматриваемом участке, л/мин; v – средняя скорость
жидкости, м/с. Полученное значение диаметра округляется до величины, определяемой ГОСТ 8732-78 и ГОСТ 8734-75. Затем по принятому диаметру определяется действительная средняя скорость (м/с) масла в трубопроводе:
v = 21 dQ2 .
Средняя скорость масла во всасывающих и сливных трубопроводах выбирается в зависимости от назначения трубопроводов, а в напорных, кроме того, – в зависимости от длины трубопровода и давления масла. Принятые и вычисленные значения расходов, диаметров и скоростей представлены в таблице 1, в которой номер участка соответствует номеру трубопровода по принципиальной схеме гидропривода (см. рис. 1). Предварительно были приняты следующие значения скоростей масла в трубопроводах: во всасывающем – 1 м/с, в напорном – 5 м/с, в сливном – 2 м/с.
|
|
|
Исходные данные для расчета гидравлических потерь |
Таблица 1 |
|||||||
|
|
|
|
||||||||
Номер |
|
Назначение |
Скорость масла, м/с |
|
Расход, |
|
Диаметр, мм |
Длина |
|||
участка |
|
|
|
|
л/мин |
|
|
|
|
участка, м |
|
|
|
допустимая |
вычисленная |
|
вычисленный |
|
принятый |
||||
1 |
|
Всасывающая |
0,5 – 1,5 |
0,87 |
|
153 |
|
57 |
|
60 |
0,5 |
|
|
гидролиния |
|
|
|
|
|
|
|
|
|
2, 5, 6 |
|
Напорная |
3 – 6 |
4,1 |
|
153 |
|
25 |
|
26 |
2,0; 2,0; |
|
|
гидролиния |
|
|
|
|
|
|
|
|
1,0 |
3, 4, 7, |
|
Сливная |
1,4 – 2,25 |
1,6 |
|
153 |
|
40,2 |
|
43 |
2,0; 1,0; |
8 |
|
гидролиния |
|
|
|
|
|
|
|
|
1,0; 1,0 |
|
Исходя из номинального |
давления |
рабочей |
жидкости в |
гидроприводе (менее |
10 МПа) в качестве трубопроводов выбираем тонкостенные трубы стальные бесшовные холоднодеформированные по ГОСТ 8734-75 из углеродистой конструкционной стали марки 20 [3]. Определим необходимую толщину стенки δ (мм) напорного трубопровода по формуле:
|
|
δ = |
pmax d |
, |
|
|
|
|
|
2 σ Д |
|
||
где pmax – |
максимальное давление |
масла, МПа |
(в рассчитываемом гидроприводе |
|||
pmax = 7 МПа); σД – допустимое напряжение материала трубы на разрыв, МПа (для стали |
||||||
20 примем σД |
= 400 МПа). Тогда толщина стенки трубы будет равна |
|||||
|
δ = |
7 26 |
≈ 0,25 мм. |
|||
|
|
|||||
|
|
2 400 |
|
|||
По результатам расчета выбираем толщину |
стенок трубопроводов 1 мм. Тогда |
обозначение напорного трубопровода – 28×1, сливного трубопровода – 45×1, где числа 30 и 45 – наружный диаметр трубы в мм.

32
6.2. Расчет гидравлических потерь
Гидравлические потери, возникающие при прохождении масла по трубопроводам и гидроаппаратам, складываются из потерь на гидравлическое трение pт , потерь в
местных сопротивлениях pм и потерь в гидроаппаратах pга .
Потери давления на трение (Па) определяются по формуле Дарси-Вейсбаха
pт = 0,5 ρ λ L v2 d ,
где ρ – плотность масла, кг/м3; λ – коэффициент гидравлического трения (коэффициент
Дарси); L – длина участка трубопровода, м; v – средняя скорость масла, м/с; d – внутренний диаметр трубопровода, м.
Для вычисления коэффициента гидравлического трения необходимо определить режим течения жидкости в трубопроводе по числу Рейнольдса:
Re = vνd ,
где ν – кинематическая вязкость выбранного масла, м2/с. Вычисляем Re для напорного и сливного трубопроводов:
для напорного – |
Re = |
4,1 26 10 |
−3 |
|||
|
2 10−5 |
= 5740 ; |
||||
|
|
|
|
|
|
|
для сливного – |
Re = |
1,6 |
43 10−3 |
= 3600 . |
||
|
2 |
10−5 |
||||
|
|
|
|
|
Так как для обоих трубопроводов выполняется условие Re > Reкр = 2300 , то
движение масла в напорном и сливном трубопроводах является турбулентным. Следовательно, величина коэффициента гидравлического трения λ зависит от числа
Рейнольдса и значения относительной шероховатости внутренней поверхности трубы d ,
где – средняя эквивалентная шероховатость стенок трубопровода. Для стальных новых и чистых трубопроводов принимаем = 0,03 мм. Если пренебречь шероховатостью
стенок, считать трубы гидравлически гладкими можно при выполнении условия
Re d ≤ 20 .
Имеем для напорного трубопровода – Re d = 5740 026,03 = 6,2 ≤ 20 ,
для сливного трубопровода – Re d = 3600 043,03 = 2,4 ≤ 20 .
Следовательно, оба трубопровода можно считать гидравлически гладкими и вычислить коэффициент λ по формуле Блазиуса:
λ = 04,3164Re .

33
Имеем для напорного трубопровода – λ = 0,31644 5740 = 0,036 , для сливного трубопровода – λ = 0,31644 3600 = 0,041.
Используя расчетные значения коэффициентов λ , определим потери давления на трение в напорном и сливном трубопроводах:
pтн = 0,5 895 0,036 5 4,12 0,026 ≈48360 Па;
pтс = 0,5 895 0,041 5 1,62 0,043 ≈5220 Па.
Вычислим потери давления в местных сопротивлениях. Местными сопротивлениями в напорном трубопроводе являются золотниковый распределитель, разветвление трубопровода, вход в трубопровод, изгибы трубы. Местными потерями в сливном трубопроводе являются выход из гидроцилиндра, распределитель, масляный фильтр, маслоохладитель, изгибы трубы. Потери давления в местных сопротивлениях (в Па) определяются по формуле Вейсбаха
pм = 0,5 ρ ξ v2 ,
где ρ – плотность масла, кг/м3; ξ – коэффициент местного сопротивления; v – средняя
скорость масла за местным сопротивлением, м/с.
Расчет потерь давления в местных сопротивлениях и в гидроаппаратах сведены в таблицы 2 и 3 соответственно.
|
|
Расчет потерь давления в местных сопротивлениях |
|
Таблица 2 |
|||||||||||||
|
|
|
|
||||||||||||||
Гидролиния |
|
Вид |
|
|
Коэффициент |
|
Скорость |
|
Потери |
|
Суммарные |
||||||
|
сопротивления |
|
|
местного |
|
масла v , м/с |
|
давления |
|
|
потери |
||||||
|
|
|
|
|
сопротивления ξ |
|
|
|
|
|
|
pм , Па |
|
|
давления |
||
|
|
|
|
|
|
|
|
|
|
|
|
|
|
|
|
∑ pм , Па |
|
Напорная |
Вход |
|
в |
|
0,8 |
|
|
|
4,1 |
|
1468 |
|
4770 |
||||
|
гидроцилиндр |
|
|
|
|
|
|
|
|
|
|
|
|
|
|
||
|
Разделение |
|
1,5 |
|
|
|
|
|
|
2752 |
|
|
|
||||
|
потоков |
|
|
|
|
|
|
|
|
|
|
|
|
|
|
||
|
Закругленное |
|
0,15 |
|
|
|
|
|
275×2=550 |
|
|
|
|||||
|
колено – 2 шт. |
|
|
|
|
|
|
|
|
|
|
|
|
|
|
||
Сливная |
Выход |
|
из |
|
0,6 |
|
|
|
1,6 |
|
687 |
|
1947 |
||||
|
гидроцилиндра |
|
|
|
|
|
|
|
|
|
|
|
|
|
|
||
|
Закругленное |
|
0,15 |
|
|
|
|
|
172×2=344 |
|
|
|
|||||
|
колено – 2 шт. |
|
|
|
|
|
|
|
|
|
|
|
|
|
|
||
|
Вход в маслобак |
|
0,8 |
|
|
|
|
|
|
916 |
|
|
|
||||
|
|
|
Потери давления в гидроаппаратах |
|
|
|
|
Таблица 3 |
|||||||||
|
|
|
|
|
|
|
|
||||||||||
Наименование |
|
Марка и |
|
|
Параметры гидроаппарата |
|
∑ pм , |
||||||||||
гидроаппарата |
|
типоразме |
|
|
|
|
|
|
|
|
|
|
|
|
|||
|
|
табличные |
|
|
в гидроприводе |
|
|||||||||||
|
|
|
|
|
МПа |
||||||||||||
|
|
|
р |
|
|
|
|
|
|
|
|
|
|
|
|
||
|
|
|
|
Q , л/мин |
|
p |
, МПа |
|
Q , л/мин |
|
p , МПа |
|
|||||
|
|
|
|
|
|
|
|
|
|||||||||
Золотниковый |
|
|
Р25 |
|
160 – 200 |
|
|
16 |
|
153 |
|
|
6,3 |
|
|
0,25 |
|
распределитель типа 4/3 |
|
|
|
|
|
|
|
|
|
|
|
|
|
|
34
Наименование |
Марка и |
|
Параметры гидроаппарата |
|
∑ pм , |
|||
гидроаппарата |
типоразме |
|
|
|
|
|
||
табличные |
в гидроприводе |
|||||||
МПа |
||||||||
|
р |
|
|
|
|
|
||
|
Q , л/мин |
p , МПа |
Q , л/мин |
|
p , МПа |
|||
|
|
|
||||||
Масляный фильтр |
ФС-7 |
160 |
6,3 |
153 |
|
0,5 |
0,25 |
|
Маслоохладитель |
ТВ4000 |
100 |
0,63 |
153 |
|
0,5 |
0,1 |
При последовательном соединении участков трубопроводов общая потеря давления определяется как сумма всех потерь на трение и в местных сопротивлениях на всех участках:
pΣ = 48360 + 5220 + 4770 +1947 + 250000 + 250000 +100000 = 660297 Па.
7. Подбор основных агрегатов гидропривода
Полезный (геометрический) объем масляного бака определяется из условия трехминутной номинальной производительности насоса:
VБ = 3 Qн = 3 153 = 459 л (дм3).
Всоответствии с ГОСТ 16770-71 выбираем номинальную вместимость масляного бака 500 дм3 [3]. Объем заливаемого в бак масла – не менее 400 л.
Вкачестве гидрораспределителя выбираем распределитель 1Р203 исполнения 64 с электрогидралическим управлением, который имеет следующие технические характеристики:
– условный проход – 20 мм;
– номинальный расход – 200 л/мин;
– номинальное давление – 32 МПа.
Выбор марки масляного фильтра осуществляется исходя из номинальной производительности насоса (153 л/мин), давления в сливном трубопроводе (0,5 МПа) и допустимой тонкости фильтрации для пластинчатых насосов. Выбираем фильтр сетчатый ФС-7 с номинальной тонкостью фильтрации 40 мкм с номинальным расходом 200 л/мин и номинальным давлением 0,63 МПа, предназначенного для установки в сливной магистрали гидропривода [3].
Вкачестве предохранительного и переливного клапана выбираем гидроклапан давления Г54-25 исполнения 1, имеющий следующие основные параметры:
– номинальный/максимальный расход масла – 160/250 л/мин;
– давление настройки – 1,2–10 МПа.
Вкачестве манометра выбираем стрелочный манометр по ГОСТ 8625-77 с верхним пределом измеряемого давления 10 МПа [3].
8.Расчет мощности и КПД гидропривода
Полная мощность гидропривода равна мощности, потребляемой насосом, и определяется по формуле
Nн = |
pн Qн |
= |
6,3 153 |
≈18,55 |
кВт. |
|
60 ηн |
60 0,87 |
|||||
|
|
|
|
Полный КПД гидропривода вычисляется как произведение его механического, объемного и гидравлического КПД:

35
ηГП =ηм ηо ηг .
Механический КПД гидропривода равен произведению механических КПД последовательно включенных насоса, распределителя и гидроцилиндра:
ηм =ηмн ηмр ηмц = 0,87 0,90 0,95 ≈ 0,74 .
Аналогичным образом вычисляется объемный КПД гидропривода:
ηо =ηон ηор ηоц = 0,95 0,95 0,95 ≈ 0,85.
Гидравлический КПД гидропривода зависит от суммы гидравлических потерь p во всех последовательно включенных гидроагрегатах и трубопроводах:
ηг |
pн − |
p |
= |
6,3 −0,56 |
= 0,91. |
pн |
|
6,3 |
|||
|
|
|
|
Таким образом, полный КПД гидропривода равен
ηГП = 0,74 0,85 0,91 ≈ 0,57 .
9.Тепловой расчет гидропривода
Вся энергия, затраченная на преодоление различного рода сопротивлений в гидроприводе, в конечном итоге превращается в теплоту, поглощаемую маслом, что вызывает его нагрев и нежелательное уменьшение вязкости. Будем считать, что полученная маслом теплота должна отдаваться в окружающую среду через поверхность стенок масляного бака. Если площадь стенок оказывается недостаточной, то устанавливается воздушно-масляный или водомасляный теплообменник (маслоохладитель). Предположим также, что бак имеет форму прямоугольного параллелепипеда.
Тепловой поток (кВт) через стенки маслобака эквивалентен потерянной мощности и с учетом режима работы гидропривода определяется по формуле
G = Nн kн (1 −ηГП ).
Количество тепла (кДж), которое может быть передано от нагретого масла окружающему воздуху, определяется по формуле
Q = 3600 G t ,
где t – время работы гидропривода, ч.
Если масло охлаждается только в гидробаке, то установившаяся температура tм масла, которая не должна превышать 70°С, определяется по формуле
tм = tв + |
Q |
≈ tв + |
4 |
Q |
, |
|
K Fб |
3 Vм2 |
|

36
где tв – температура окружающего воздуха, ºС; K – коэффициент теплопередачи от масла к окружающему воздуху, приведенный к охлаждаемой поверхности гидробака; Fб – охлаждаемая поверхность бака, м2; Vм – объем масла в баке, м3. При отсутствии интенсивной местной циркуляции воздуха около бака K = 63 кДж/(м2 ч град) [2].
Если принять, что t =1ч, tв = 20°C , kн = 0,5 , то температура масла при работе гидропривода в номинальном режиме составит
tм = tв + Nн kн (1 −ηГП ) t = 20 + 18,5 3600 0,5 (1 −0,57) 1 ≈85°C . |
|
4 3 Vм2 |
4 3 4502 |
Выбранный объем гидробака не обеспечивает охлаждение масла для заданных режимов работы гидропривода. Поэтому необходима установка дополнительного теплообменника. Количество тепла, выделяемого за 1 час работы гидропривода, равно
Q =18,5 3600 0,5 (1 − 0,57)=14320 кДж.
Исходя из расчетного количества выделяемого тепла, в качестве маслоохладителя выбираем теплообменник типа ТВ4000, который имеет воздушное охлаждение от электродвигателя с вентилятором. Технические данные теплообменника ТВ4000:
–количество отводимого тепла при температуре масла, превышающей температуру окружающего воздуха на 30°С, – 16×106 Дж/ч;
–номинальный/максимальный расход масла – 200/220 л/мин;
–максимальное давление масла на входе – 0,63 МПа;
–максимальная температура масла на входе – 70°С.
Таким образом, теплообменник типа ТВ4000 может рассеять 16000 кДж/ч избыточного тепла, что превосходит количество выделяемого тепла (14320 кДж). Установившаяся температура масла в гидробаке при установке теплообменника будет равна tм ≈85 −30 = 55°C .
10. Проверочный расчет гидропривода
Поскольку невозможно точно подобрать элементы гидропривода, которые обеспечивали бы точные значения заданных параметров гидропривода. Цель проверочного расчета – установить действительные значения упомянутых параметров при выбранных агрегатах гидропривода. При этом проверяется усилие P на штоке гидроцилиндра, скорость поршня V гидроцилиндра, рабочее давление насоса pн .
Максимальное усилие на штоке гидроцилиндра после выбора нормализованных диаметров поршня и штока с учетом потерь давления на трение и в местных сопротивлениях в напорном трубопроводе:
P = ( pн |
− p) |
π (D2 − d 2 ) |
= (7 − 0,66) |
3,14159 |
(1102 −502 ) |
≈ 47,7 кН. |
||
4 |
4 |
103 |
|
|||||
max |
|
|
|
Для определения скорости рабочего органа машины вычисляем истинный расход масла, поступающий в гидроцилиндр:
QД = Qн −∑Qут ,

37
где Qн – подача выбранного насоса; ∑Qут – суммарные утечки во всех гидроаппаратах,
включенных между насосом и гидроцилиндром. Примем, что внутренние утечки в распределителе Р-25 при номинальном давлении не превышают 1 % от номинального расхода, а внутренние утечки в гидроцилиндре не превышают 2 %. Тогда скорость поршня гидроцилиндра при номинальной подаче насоса с учетом утечек равна
c = |
4 103 Qн |
4 (153 −153 0,03) 1000 |
м/с. |
||
60 π (D2 − d 2 ) |
= |
3.14159 60 (1102 −502 ) |
≈ 0,33 |
Таким образом, расчетные значения усилия на штоке гидроцилиндра и его скорость не ниже заданных при полном КПД гидропривода, равном 0,57. В правильно спроектированном гидроприводе должно быть ηГП = 0,6 −0,8 . Поэтому можно считать,
что расчет данного гидропривода выполнен верно.
11.Библиографический список
1.Асинхронные двигатели серии 4А: Справочник / А.Э Кравчик, М.М. Шлаф, В.И. Афонин, Е.А. Соболенская. – М.: Энергоатомиздат, 1982. – 504 с.
2.Брон Л.С., Тартаковский Ж.Э. Гидравлический привод агрегатных станков и автоматических линий / Л.С. Брон, Ж.Э. Тартаковский. – М.: Машиностроение, 1974. – 328 с.
3.Свешников В.К. Станочные гидроприводы: Справочник / В.К. Свешников. – М.: Машиностроение, 1995. – 448 с.
4.Юшкин В.В. Основы расчета объемного гидропривода: Учеб. пособие / В.В. Юшкин. – Минск: Высш. шк., 1982. – 93 с.
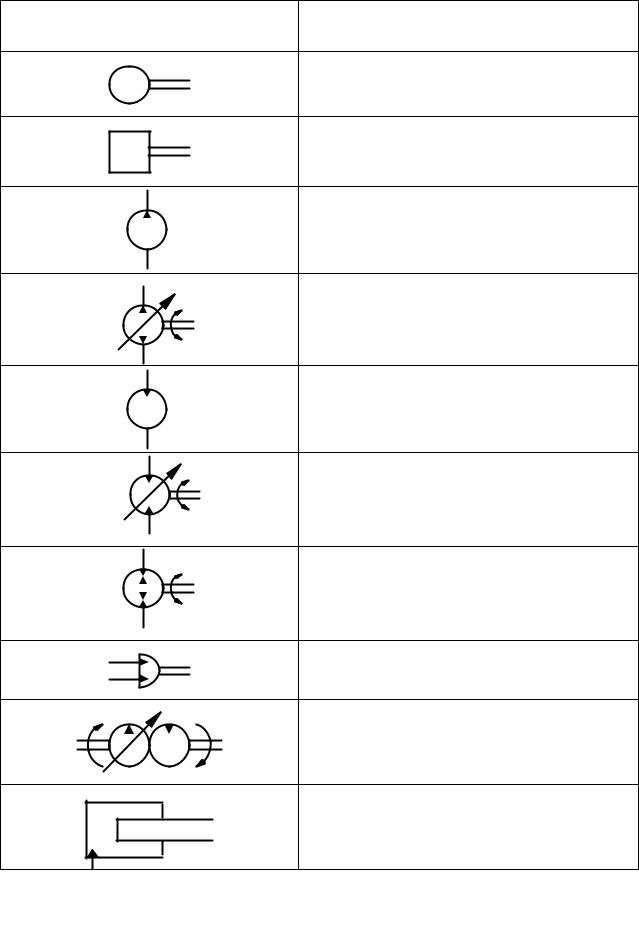
38
ПРИЛОЖЕНИЕ 4
Условные графические обозначения элементов гидроприводов
Обозначение |
Наименование |
Приводящий двигатель электрический
Приводящий двигатель неэлектрический
Насос гидравлический нерегулируемый с нереверсивным потоком
Насос гидравлический регулируемый с реверсивным потоком и реверсивным приводным валом
Гидромотор с нереверсивным потоком нерегулируемый
Гидромотор реверсивный с реверсивным потоком регулируемый
Насос-мотор гидравлический реверсивный
Гидродвигатель поворотный
Гидравлическая передача неразделенного типа с регулируемым насосом и нерегулируемым гидродвигателем
Гидроцилиндр плунжерный

39
Обозначение |
Наименование |
Гидроцилиндр одностороннего действия с односторонним штоком и возвратной пружиной
Гидроцилиндр двустороннего действия с односторонним штоком
Гидроцилиндр двустороннего действия с односторонним штоком и двусторонним торможением поршня в конце рабочего хода
Гидроцилиндр двустороннего действия с двухсторонним штоком
Гидроцилиндр двустороннего действия с двухсторонним штоком с двусторонним торможением поршня в конце хода
Телескопический гидроцилиндр одностороннего действия
Телескопический гидроцилиндр двустороннего действия
Гидравлический преобразователь
Гидравлический аккумулятор пружинный
Гидравлический аккумулятор газовый
Фильтр с индикатором загрязненности
Фильтр с магнитным сепаратором

40
Обозначение |
Наименование |
Сепаратор
Вентиль нормально закрытый нерегулируемый
Вентиль нормально открытый регулируемый
Теплообменный аппарат
Указатель давления
Манометр
Термометр
Измеритель расхода жидкости
Указатель уровня жидкости
Дренажная гидролиния
Распределитель 2/2 с механическим управлением
Распределитель 2/2 с электромагнитным управлением
Распределитель 3/2 с гидравлическим управлением
Распределитель 4/2 с электромагнитным управлением
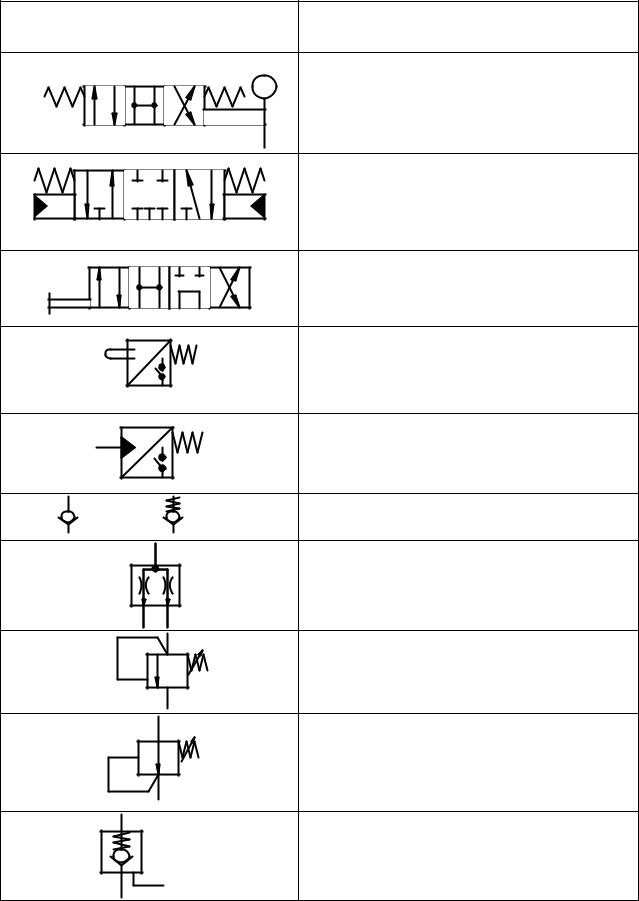
41
Обозначение |
Наименование |
Распределитель 4/3 с ручным управлением
Распределитель 5/3 с электро-гидравлическим управлением
Распределитель 4/4 с ручным управлением
Конечный выключатель
Реле давления
Клапан обратный
Делитель потока
Клапан напорный (предохранительный или переливной) прямого действия регулируемый
Клапан редукционный регулируемый
Гидравлический замок односторонний

|
42 |
|
|
Обозначение |
Наименование |
Гидравлический замок двусторонний
Дроссель нерегулируемый
Дроссель регулируемый
Регулятор расхода (потока)
Клапан "ИЛИ"
Клапан "И"
Гидробак открытого типа с сапуном
Гидробак закрытого типа с подведенными гидролиниями
Вращающееся соединение трубопроводов
Подвод рабочей жидкости
Отвод рабочей жидкости
Гибкий трубопровод
Соединение трубопроводов
Обход трубопроводов
Направление потока
43
ПРИЛОЖЕНИЕ 5
Буквенные позиционные обозначения основных элементов гидроприводов
Наименование |
Обозначение |
Устройство (общее обозначение) |
А |
|
|
Гидроаккумулятор |
АК |
Аппарат теплообменный |
АТ |
|
|
Гидробак |
Б |
Влагоотделитель |
ВД |
|
|
Вентиль |
ВН |
Гидродвигатель (поворотный) |
Д |
Делитель потока |
ДП |
|
|
Дроссель |
ДР |
Гидрозамок |
ЗМ |
|
|
Гидроклапан |
К |
Гидроклапан давления |
КД |
|
|
Гидроклапан обратный |
КО |
Гидроклапан редукционный |
КР |
|
|
Гидромотор |
М |
Манометр |
МН |
Насос |
Н |
|
|
Насос аксиально-поршневой |
НА |
Насос пластинчатый |
НП |
|
|
Насос радиально-поршневой |
НР |
Насос шестеренный |
НШ |
|
|
Гидропреобразователь |
ПР |
Гидрораспределитель |
Р |
|
|
Реле давления |
РД |
Гидроаппарат золотниковый |
РЗ |
Гидроаппарат клапанный |
РК |
|
|
Регулятор потока |
РП |
Сепаратор |
С |
|
|
Сумматор потока |
СП |
Термометр |
Т |
|
|
Гидроусилитель |
УС |
Фильтр |
Ф |
Гидроцилиндр |
Ц |
|
|

|
|
|
44 |
|
|
|
ПРИЛОЖЕНИЕ 6 |
Исполнения гидравлических распределителей по гидросхемам |
|||
Исполнение по |
Число |
Число |
Условное обозначение распределителя без |
гидросхеме |
позиций |
линий |
механизма управления |
14 |
3 |
4 |
|
24 |
3 |
4 |
|
34 |
3 |
4 |
|
44 |
3 |
4 |
|
54 |
3 |
4 |
|
64 |
3 |
4 |
|
74 |
3 |
4 |
|
94 |
3 |
4 |
|
104 |
3 |
4 |
|
134 |
3 |
4 |
|
154 |
3 |
4 |
|
573 |
2 |
3 |
|
574 |
2 |
4 |
|
45
ПРИЛОЖЕНИЕ 7
Правила составления и описания принципиальной гидравлической схемы
Схема – это конструкторский документ, на котором показаны в виде условных изображений или обозначений составные части изделия и связи между ними. ГОСТ 2.70176 Единой системы конструкторской документации (ЕСКД) для гидравлических и пневматических приводов устанавливает три вида схем: структурные, принципиальные и схемы соединений. Принципиальная схема определяет полный состав (номенклатуру) элементов и связей между ними и, как правило, дает детальное представление о принципах работы изделия. Для объемного гидропривода его принципиальная схема является основным техническим документом.
Гидравлическое оборудование на принципиальных схемах изображается в виде стандартизированных условных графических обозначений. Правила выполнения принципиальных гидравлических схем регламентированы стандартами ЕСКД и состоят в следующем.
Принципиальная схема гидропривода (гидросхема) изображается без соблюдения масштаба. Условные графические обозначения показывают только целевое назначение элементов без указания их конструктивных исполнений и рабочих параметров. Действительное пространственное расположение составных частей гидропривода не учитывается либо указывается приближенно. Графические обозначения элементов гидропривода следует располагать на поле схемы таким образом, чтобы получить линии связи минимальной длины, а также наименьшее число их изломов и взаимных пересечений. Соотношение размеров условных обозначений стандартами не регламентируется и выбирается в зависимости от размеров гидросхемы и ее насыщенности гидромашинами и гидроаппаратами. Условные графические обозначения могут быть повернуты на любой угол. На поле схемы допускается помещать различные технические данные, дополнительно раскрывающие устройство и принцип работы гидропривода (технические требования, таблицы, диаграммы и т.п.). В приложении 4 приведены основные условные графические обозначения гидравлических машин и элементов гидроприводов, которые следует использовать при выполнении принципиальной схемы проектируемого гидропривода.
Все элементы и устройства гидропривода изображаются на принципиальной схеме, как правило, в исходном положении: распределители – в нейтральной позиции, поршни гидроцилиндров – перед совершением рабочего хода и т.п. Напорная, всасывающая и сливная гидролинии изображаются, как правило, на схеме сплошными основными линиями, а гидролинии управления и дренажные – более тонкими пунктирными линиями.
Гидравлические цилиндры могут располагаться на схеме гидропривода в горизонтальном или вертикальном положении, что определяется их реальным расположением в составе гидрофицированной машины. Распределители на схеме гидропривода также могут быть изображены как в горизонтальном, так и в вертикальном положении; в первом случае гидролинии подходят к распределителю вертикально, во втором – горизонтально. Позиции распределителей на схеме и в уравнении гидропотоков указываются римскими цифрами (I, II, III и т.д.).
Каждый элемент или устройство гидропривода на схеме должен иметь буквенноцифровое позиционное обозначение, состоящее из буквенного обозначения (прописные буквы) и порядкового номера элемента, проставленного после букв (начиная с единицы в пределах группы элементов или устройств, которым на схеме присвоено одинаковое буквенное обозначение). Обозначения (идентификаторы) наиболее распространенных элементов гидроприводов, которые также следует использовать при выполнении схемы гидропривода и описании его работы, приведены в приложении 5.
46
Порядковые номера элементам схемы следует присваивать в соответствии с последовательностью их расположения на схеме сверху вниз и слева направо. Нумерация элементов начинается с единицы в пределах каждого одинакового буквенного идентификатора, например: Н1, Н2, Н3 и т.д., Ц1, Ц2, Ц3 и т.д. При необходимости допускается изменять последовательность присвоения порядковых номеров в зависимости от размещения элементов в изделии или от направления движения рабочей жидкости. Если какой-либо элемент гидропривода присутствует на схеме в единственном числе, то единичный порядковый номер такому элементу можно не присваивать. Буквенноцифровые обозначения проставляются на схеме рядом с условными графическими обозначениями элементов и устройств с правой стороны или над ними. Порядковые номера гидролиниям присваиваются начиная с единицы и, как правило, по направлению потока рабочей жидкости. При внесении изменений в схему последовательность присвоения порядковых номеров может быть нарушена.
Для упрощения принципиальной гидравлической схемы путем сокращения длины изображения линий слива и дренажа допускается условное обозначение гидробака повторять около условного графического обозначения соответствующего элемента. При сокращении длины изображения линий напора обозначение источника питания (насоса) повторно не приводят, а на входе соответствующего элемента или устройства показывают обозначение подвода рабочей жидкости.
В условном обозначении распределителя указывают следующие элементы: позиции запорно-регулирующего элемента; внешние гидролинии, подводимые к распределителю; проходы (каналы) для рабочей жидкости; элементы управления. Число позиций изображают соответствующим числом квадратов (прямоугольников). Проходы изображают прямыми линиями со стрелками, показывающими направление потока рабочей жидкости в каждой позиции, а места соединений проходов выделяют точками; закрытый проход изображают тупиковой линией с поперечной черточкой. Внешние гидролинии подводятся только к исходной позиции. Способы управления распределителем указывают соответствующими знаками, примыкающими к торцам обозначения распределителя.
Правило чтения условного графического обозначения распределителя состоит в следующем: чтобы представить принцип работы распределителя в рабочей позиции, необходимо мысленно в условном обозначении на схеме передвинуть соответствующий квадрат (прямоугольник) на место квадрата (прямоугольника) в исходной позиции, оставляя гидролинии в неизменном положении. Истинные направления потока рабочей жидкости укажут проходы рабочей позиции. Условные обозначения едины для золотниковых, крановых и клапанных распределителей и не отражают конструкцию запорно-регулирующих элементов. В приложении 6 приведены принципиальные схемы основных конструктивных исполнений двух- и трехпозиционных распределителей.
Управляющие электромагниты золотниковых гидравлических распределителей рекомендуется обозначать ЭМ1, ЭМ2 и т.д.
Для выполнения принципиальной гидравлической схемы с помощью персонального компьютера можно воспользоваться графическим редактором Microsoft Visio, который содержит библиотеку стандартных условных обозначений элементов гидравлических и пневматических систем.
Данные обо всех элементах проектируемого гидропривода заносятся в перечень элементов, который оформляется в виде таблицы. Связь перечня с условными графическими обозначениями осуществляется через позиционные обозначения. Таблица заполняется сверху вниз. Перечень элементов помещают на первом листе схемы над основной надписью (на расстоянии не менее 12 мм). Если перечень элементов оформляется как самостоятельный документ, то он выполняется на листах формата А4 и помещается в пояснительную записку после принципиальной схемы.
47
Вграфе "Поз. обозначение" указывают позиционные обозначения элементов схемы, а в графе "Наименование" – наименование элементов. Элементы в перечень записывают в алфавитном порядке буквенных позиционных обозначений. В пределах каждой группы, имеющей одинаковые буквенные позиционные обозначения, элементы располагают по возрастанию порядковых номеров. Элементы одного типа с одинаковыми гидравлическими параметрами, имеющие на схеме порядковые номера, допускается записывать в перечень в одну строку. В этом случае в графу "Поз. обозначение" вписывают только позиционные обозначения элементов с наименьшим и наибольшим порядковыми номерами (например, ЗМ1, ЗМ2; МН1 … МН4), а в графу "Кол." – общее количество таких элементов.
Вграфе "Примечание" рекомендуется указывать технические характеристики элементов: давление, подачу насоса, расход жидкости, тонкость фильтрации и т.п.
Пример заполнения перечня элементов представлен в табл. П7.1:
Таблица П7.1 Перечень элементов принципиальной схемы гидропривода (пример)
Поз. |
Наименование |
Кол. |
Примечание |
обозначение |
|
|
|
|
|
|
|
АТ |
Теплообменник воздушный Г44-24 |
1 |
Qном = 70 л/мин |
|
ТУ2-053-0221244-050-89 |
|
|
… |
|
|
|
Н1 |
Насос шестеренный Г11-23 |
1 |
pном = 2,5 МПа |
|
ГОСТ 15107-79 |
|
Qном = 38 л/мин |
|
|
|
|
Н2 |
Насос шестеренный Г11-24 |
1 |
pном = 2,5 МПа |
|
ГОСТ 15107-79 |
|
Qном = 72 л/мин |
|
|
|
|
… |
|
|
|
Ц1, Ц2 |
Гидроцилиндр 3.2-100.800 |
2 |
D =100 мм |
|
ОН 22-176-79 |
|
L = 800 мм |
… |
|
|
|
Принципиальная схема гидропривода должна сопровождаться текстовым описанием его работы. Описание гидропривода, имеющего несколько режимов работы (например, холостой ход, рабочий ход и т.п.), должно содержать столько частей, сколько режимов работы обеспечивает гидропривод. Например, гидропривод может иметь три режима работы: "Холостой ход", "Выдвижение штока гидроцилиндра", "Опускание штока гидроцилиндра". Описание каждого движения гидродвигателя должно сопровождаться записью уравнения потока рабочей жидкости (гидропотока).
Запись условных обозначений в уравнении гидропотока производится, как правило, слева направо. Уравнение гидропотока при разомкнутой циркуляции рабочей жидкости обычно выражает две части – сливную и нагнетательную, если обе полости гидродвигателя содержат рабочую жидкость, но может отражать только одну часть, если рабочая жидкость подается лишь в одну полость гидродвигателя, а вторая сообщается с атмосферой. При этом части уравнения отделяются наклонной чертой (/).
Уравнение гидропотока содержит позиционные обозначения элементов схемы, гидролиний, позиций распределителей, направлений движения выходных звеньев гидродвигателей, а также направлений перемещений золотников распределителей. Обозначения элементов схемы (гидромашин и гидроаппаратов) в совокупности с их позициями и направлениями их перемещений указываются в круглых скобках, например:
48
(Н), (ДР1), (КП2), (М), (Б) – обозначения насоса Н, дросселя ДР1, предохранительного клапана КП2, нереверсивного гидромотора М и гидробака Б соответственно;
(Ц1→) – поршень (шток, цилиндр, корпус) гидроцилиндра (Ц1) движется вправо по схеме;
(Ц1←) – поршень (шток, цилиндр, корпус) гидроцилиндра (Ц1) движется влево по
схеме;
(Ц1 ↑) – поршень (шток, цилиндр, корпус) гидроцилиндра (Ц1) движется вверх по
схеме;
(Ц1 ↓) – поршень (шток, цилиндр, корпус) гидроцилиндра (Ц1) движется вниз по
схеме;
(М1 3) – вал реверсивного гидромотора вращается по часовой стрелке (в прямом направлении);
(М1 4) – вал реверсивного гидромотора вращается против часовой стрелки (в обратном направлении);
(Д 3) – вал поворотного гидродвигателя Д поворачивается по часовой стрелке (в прямом направлении);
(Д 4) – вал поворотного гидродвигателя Д поворачивается против часовой стрелки (в обратном направлении);
…5 (Ц1→)/(Ц1) 6 … – масло по трубопроводу (гидролинии) 5 поступает в гидроцилиндр Ц1, его поршень (шток, цилиндр, корпус) движется вправо по схеме, масло из его противоположной полости вытесняется в трубопровод (гидролинию) 6;
…7 (М1 3)/(М1) 8 … – масло по трубопроводу (гидролинии) 7 поступает в реверсивный гидромотор, его вал вращается по часовой стрелке (в прямом направлении), выходящее из гидромотора масло вытесняется в трубопровод (гидролинию) 8;
4...
...3 – разветвление гидропотока 3 на два гидропотока 4 и 5;
5...
...4
6... – слияние двух гидропотоков 4 и 5 в один гидропоток 6.
...5
Гидролинии (трубопроводы) на принципиальной схеме гидропривода и в уравнениях гидропотоков номеруются арабскими цифрами. При этом нумерация трубопроводов, входящих в устройство и выходящих из устройства, должны быть различными. При слиянии и разветвлении нескольких трубопроводов нумерация является общей, т.е. не изменяется.
Для двухпозиционных распределителей рекомендуется за исходную позицию при составлении описания работы гидропривода принимать позицию I распределителя. Для трехпозиционных распределителей с электрическим управлением исходной позицией является средняя позиция с номером II. Примеры записи позиций распределителей:
(Р1–I) – распределитель Р1 находится в позиции I;
(Р2–II) – распределитель Р2 находится в позиции II;
(Р1→III) – распределитель Р1 переключается вправо по схеме в позицию III; (Р2←II) – распределитель Р2 переключается влево по схеме в позицию II; (Р1↓III) – распределитель Р1 переключается вниз по схеме в позицию III; (Р3↑I) – распределитель Р3 переключается вверх по схеме в позицию I.
Разветвление гидролиний и объединение некскольких гидролиний в уравнении гидропотоков обозначается с помощью фигурных скобок {}.
Пример построения фразы и уравнения гидропотока при описании работы гидропривода плоскошлифовального станка:
(Ф1)2(Р1 − I )3(КО2)4(Ц1 →) /(Ц1)5( ДР1)6(Р1 − I )7(Б)
поток масла (Н1)1
(КП1)8(Б)
49
перемещает поршень гидроцилиндра Ц1 вправо и сообщает столу станка продольную подачу.
Расшифруем уравнение гидропотока в вышеприведенном примере. Масло от насоса Н1 поступает по трубопроводу 1 в фильтр Ф1, далее по трубопроводу 2 подводится к распределителю Р1, золотник которого находится в позиции I. Далее масло по трубопроводу 3 подводится к обратному клапану КО2 и по трубопроводу 4 нагнетается в левую полость гидроцилиндра Ц1, перемещая его поршень вправо. Масло из правой полости гидроцилиндра Ц1 вытесняется в трубопровод 5, проходит через дроссель ДР1, по трубопроводу 6 поступает к распределителю Р1, проходит через его позицию I и по трубопроводу 7 сливается в бак Б. Поток масла от трубопровода 1 ответвляется к переливному клапану КП1 и через трубопровод 8 сливается в бак Б.