
- •Методичний посібник для самостійної роботи студентів з предмету «Ремонт машин» ( I,II розділи )
- •Тема1.1: Вступ. Загальні положення по ремонту.
- •Методичні вказівки
- •4.Види дефектів машин
- •Тема 1.2: Види і методи ремонту
- •Види ремонту
- •3.Види майстерень
- •Тема 1.3 Організація технічного контролю
- •Методичні вказівки
- •Контроль геометричних параметрів :
- •Тема 2.1 Загальні поняття про виробничий процес.
- •Методичні вказівки
- •При великій різноманітності техніки, загальна схема технологічного процесу їх ремонту має такий вигляд:
- •Тема 2.2 Підготовка машини до ремонту.
- •Про стан машини , зданої в ремонт
- •Про стан агрегатів і вузлів, здаваних у ремонт
- •Приймально-здавальний акт № ______ на прийом до капітального ремонту машини
- •Приймально-здавальний акт № ______ на прийом до капітального ремонту агрегатів і вузлів
- •Вимоги до майданчика зберігання ремонтного фонду
- •Тема 2.3 Розбирання машин та агрегатів
- •Методичні вказівки
- •4.Організація робочих місць. Тб при виконанні робіт
- •Вимоги до пневматичного інструменту
- •Вимоги до ручного електроінструменту
- •Вимоги безпеки при експлуатації підйомників , домкратів
- •Вимоги безпеки при експлуатації лебідок
- •Тема 2.4 Миття та очистка деталей
- •Методичні вказівки
- •Способи очистки
- •3. Миття деталей від бруду і паливно-мастильних матеріалів
- •4.Очистка деталей від нагару
- •Тема 2.5 дефектація та сортування деталей
- •Методичні вказівки
- •Особливості дефектації типових деталей
- •Тема 2.6 Комплектування деталей
- •Методичні вказівки
- •Тема 2.7 Складання та випробовування агрегатів.
- •Методичні вказівки
- •Технологія складання різних видів з’єднань.
- •Тема 2.8 Загальне складання та випробування машин
- •Методичні вказівки
- •Тема 2.9 фарбування агрегатів і машин , видача їх із ремонту
- •Методичні вказівки
- •Тестові завдання для перевірки знань
Тема 2.5 дефектація та сортування деталей
Основна ціль дефектації і сортування деталей . Види дефектів і їх, характеристика . Поняття про граничне-допустиме зношення деталей . Технічні умови на дефектацію деталей . Способи контролю: сутність , інструмент , обладнання .
Сортування деталей за результатами дефектації . Відомість дефектації: її призначення й зміст .
Організація робочих місць , техніка безпеки .
Методичні вказівки
1. ДЕФЕКТАЦІЯ – процес виявлення технічного стану деталей порівнянням фактичних показників з даними технічної документації ( технічними умовами, кресленням деталі тощо).
Мета дефектації – визначення технічного стану деталей і сортування їх на відповідні групи : придатні, ті, що підлягають відновленню на даному підприємстві, і непридатні.
ДЕФЕКТ – це кожна окрема невідповідність продукції вимогам, встановленим нормативною документацією.
За наслідками дефекти поділяються на :
критичні – дефекти при , яких використовувати продукцію за призначенням практично не можливо або забороняється відповідно до вимог техніки безпеки.
значний – дефект який істотно впливає на використання продукції за призначенням і на довговічність.
молозначний – дефект який істотно не впливає на використання продукції за призначенням і на довговічність.
За місцем розташування дефекти поділяються :
зовнішні – деформації, поломки, зміна геометричної форми, зміна розмірів.
внутрішні – тріщини від втомленості, втрата механічних властивостей (пружності) .
За можливістю виправлення дефекти поділяються на:
поправні – дефекти, усунення яких технічно можливе і економічно доцільне.
непоправні – дефекти , усунення яких технічно не можливе і економічно не доцільне.
За причинами виникнення дефекти поділяються на три класи :
конструктивні – невідповідність вимогам технологічного завдання або встановленим правилам розробки продукції . Причина таких дефектів : помилковий набір матеріалу виробу, неправильне визначення розмірів деталей , режими термічної обробки і т.д. Ці дефекти – наслідок недосконалості конструкції та помилок конструювання.
виробничі - невідповідність вимогам нормативної документації на виготовлення (ремонт) чи поставку продукції . Виробничі дефекти поділяються на шість груп :
Дефекти плавлення і лиття ( усадочні раковини, шлакові включення, газові пори і т.д. )
Дефекти, що виникають під час обробки деталей тиском ( поверхневі і внутрішні тріщини, закати, розшарування і т.д.)
Дефекти термічної, хіміко-термічної та електрохімічної обробки (термічні тріщини, перепал, відшарування покриття, невідповідність шару і т.д.)
Дефекти механічної обробки (дрібні тріщини, шліфувальні тріщини, порушення геометричних розмірів)
Дефекти, що виникли під час монтажу, демонтажу ( погнутість, обломи різьби, порушення посадок і т.д.)
Дефекти у з’єднанні металів ( раковини, пори, шлакові включення, зміщення кромок, перегрів, не проварювання , відшарування і т.д.)
До експлуатаційних належать дефекти, що виникають в результаті спрацювання і втомленості металу , корозії і т.д.
Стан деталей , спряжень і комплектних груп можна визначати оглядом , перевіркою на дотик, за допомогою вимірювальних інструментів.
Вибір засобів контролю має ґрунтуватися на забезпеченні заданих показників процесу контролю й аналізу затрат на реалізацію контролю при заданій якості виробу.
Вибір засобів контролю включає :
аналіз характеристик об’єкта контролю і показників процесу контролю;
визначення попереднього складу контролю;
визначення остаточних складу засобів контролю, їх економічного обґрунтування, складання технологічної документації.
Залежно від виробничої програми , стабільності вимірювальних параметрів можна використовувати універсальні, механізовані чи автоматизовані засоби контролю.
У ремонті найбільше застосування набули універсальні вимірювальні прилади та інструменти :
механічні прилади ( лінійки, штангенциркулі, мікрометри і т.д.)
оптичні прилади ( окулярні мікрометри, мікроскопи, оптиметри і т.д.)
пневматичні прилади ( довжиноміри)
електричні прилади .
Методи неруйнівного контролю для виявлення внутрішніх дефектів деталей :
магнітний – ґрунтується на принципі “магнітного розсіювання” :
магнітопорошковий – грунтується на виявленні магнітних полів розсіювання за допомогою феромагнітних порошків. Визначають тріщини які утворені в результаті термічної обробки , а також неметалеві включення ( шириною 0,001…0,03мм і глибиною 0,01…0,04мм). Застосовують три способи намагнічування деталей( циркуляційне намагнічування – коли крізь деталь пропускають струм ; подовжнє – коли деталь вміщують між полюсами електромагнітів або в поле соленоїда ; комбінований ) .
Ремонтних підприємствах широке розповсюдження отримав
універсальний магнітний дефектоскоп М-217.
На ремонтних заводах застосовуються магнітні дефектоскопи МДА-3-408, ПДМ-70, МД-50, ЦВН-3, ДМП-2 та ін.
Магнітна дефектоскопія має ряд недоліків : суб’єктивність , неможливість виявлення внутрішніх дефектів, вплив конфігурації деталі на результати контролю та ін.
радіаційний метод ґрунтується на реєстрації і аналізі іонізуючого випромінювання після взаємодії з контролюючим об’єктом
- рентгенівський метод – використовується рентгенівське випромінювання . - гамма дефектоскопія використовуються радіоактивні ізотопи .
Промисловість випускає широку номенклатуру засобів радіаційного контролю: РАП-150/300 (стаціонарні), РИ-10, РУП-100-10(пересувні) . Для гамма дефектоскопії РИД, ГУП, Гаммарид.
капілярні методи неруйнівного контролю ( метод проникнення рідини ) ґрунтується на капілярному проникненні рідини у порожнини поверхневих дефектів і реєстрація індикаторного рисунка. Суть методу полягає в тому , що на попередньо очищену поверхню наносять рідину з великими змочувальними властивостями і капілярним тиском, в результаті рідина проникає в найдрібніші тріщини і пори . Після видалення лишок рідини на поверхню наносять проявник ( порошок з великою абсорбуючою здатністю ). Залишок рідини з люмінофором після опромінення ультрафіолетом в місцях тріщин, пор – флуоресціює . Для дефектації використовують люмінесцентні розчини – “Люм-1 водозмиваючим “ , “Люм-2”, порошки : оксид магнію, силікагель, тальк . Цим комплектом можна виявити непомітні тріщини , нерівності , подряпини тощо.
вихрострумовий грунтується на аналізі взаємодії вихрострумового перетворювача з електромагнітним полем вихрових струмів, що наводять в контрольованому об’єкті. До об’єкту підносять котушку по якій тече змінний струм , у металі наводяться вихрові струми. Електромагнітне поле вихрових струмів має протилежний напрямок порівняно з навідним. Внаслідок цього вихрові струми впливають на загальний опір котушки збудження , що знаходиться поблизу виробу. Визначення величини й характеру змін внесених опорів і є основною для виявлення дефекту, або відмінностей у фізичній чи хімічній структурі металу.
Для здійснення вихрострумового контролю промисловість випускає прилади ППД-1МУ, ВД-20Н-СТ, ВД-20Н-Д.
Нині промисловість випускає портативні прилади , маса яких 150…180г. Принцип дії показаний на схемі .
1.-датчик
2.- генератор
3.- детектор
4.- мультивібратор
5.- індикатор
6.- головні телефони
Працює прилад так. Датчик 1 встановлюється на об’єкт перевірки
( дефектації). У контор генератора вносять додатковий комплексний опір . Режим роботи генератора ВЧ підбирають поблизу точки генерації . Якщо датчик проходить над тріщиною , внаслідок впливу внесеного опору змінюється комплексний опір , причому зменшується добротність контуру і відбувається зрив генерації. У цьому випадку від низького рівня сигналу, що надійшов через АМ-детектор 3 , спрацьовує мультивібратор 4 , який працює в очікувальному режимі . Генеровані мультивібратором імпульси надходять на вхід індикаторного пристрою, де прослуховуються у головних телефонах 6 і спрацьовує індикатор 5.
ультразвуковий метод – ґрунтується на властивості ультразвуку відбиватися від границі двох середовищ, в тому числі і від дефекту . Відрізнять два методи ультразвукової дефектоскопії : просвічуванням
( тіньовий) ; імпульсний .
В практиці використовуються дефектоскопи, що працюють по тіньовому методу і методу віддзеркалення.
По тіньовому методу деталь 3 (рис. 3.6) поміщається між
випромінювачем 2 і приймачем 5, які мають п'єзоелектричні
пластини. В разі відсутності дефекту ультразвукові коливання
передаються деталі, а від неї на п'єзоелектричну пластину
приймача 5 і далі на індикатор 7 (стрілка відхиляється від нуля).
Якщо дефект знайдений, ультразвукові хвилі 4 не відбиваються
і не потрапляють на п'єзоелектричну пластину приймача 5,
внаслідок чого за дефектною ділянкою деталі утворюється
звукова тінь і індикатор 7 дефектоскопа не дає показів.
В ремонтному виробництві використовують ультразвукові дефектоскопи – ДУК-66ПМ, УД-10УА. Максимальна глибина прозвучування для стальних деталей 2,6м , а мінімальна – 7мм.
Метод віддзеркалення полягає в тому, що імпульсний
генератор 6 (рис. 3.7) збуджує п’єзо елемент 3. Досягнувши дна
контрольованого виробу l, ультразвукові коливання відбиваються від нього і повертаються до приймальної пластини 2, в якій виникає слабкий електричний струм. Отриманий сигнал підсилюється підсилювачем 4 і подається на електронно-променеву трубку 5. При пуску генератора 6 на екрані з'являється початковий імпульс у вигляді вертикального піку, після чого наступає пауза ( генератор вимикається до подальшого імпульсу). При виявленні дефекту на екрані на відстані
1 від першого імпульсу з'являється другий, який відбивається від
дефекту, а в кінці розгортки на відстані l2 - імпульс донного сигналу. Таким чином, відстань l1 відповідає глибині залягання
дефекту, а відстань l2 - товщині виробу (в певному масштабі). В
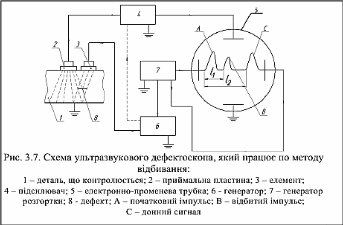
ремонтному виробництві і автомобілебудуванні широко використовують дефектоскопи УЗД-10, УЗД-10М і ін.
Рентгенівська дефектоскопія не знайшла широкого розповсюдження в ремонтному виробництві, оскільки променеві установки дорогі і для роботи з ними потрібне спеціальне навчання обслуговуючого персоналу.
Гідравлічним методом виявляють тріщини в блоках, головках блоків циліндрів двигунів і інших корпусних деталях. При гідравлічному випробуванні деталь встановлюють на універсальний стенд, всі технологічні отвори закривають заглушками, насосом закачують у внутрішню порожнину воду під тиском 0,5 МПа. Постійність тиску протягом 5 хв. свідчить про відсутність тріщин. Пневматичним методом виявляють приховані тріщини в паливних баках, шинах, радіаторах і ін. У внутрішню порожнину деталі накачують повітря (0,1 МПа) і занурюють її у
воду. Пухирці повітря вказують на наявність дефекту. У разі контролю крупних деталей ( паливних баків) на поверхню останніх наносять мильний розчин. Спучування мильних пухирців вказує на ділянки пошкодження.