
Ахметов и др. Технология и оборудование процессов переработки нефти и газа (2006)
.pdf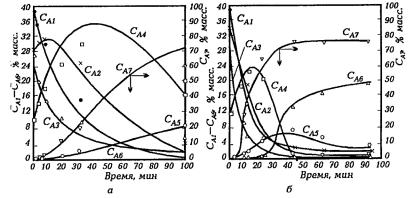
Рис. 5.2. Изменение концентрации групповых компонентов дистиллятного крекинг-остатка Красноводского НПЗ от продолжительности термолиза при давлении 0,1 МПа
и температуре 420 (а) и 490°С (б):
СА1 — легкие масла; СА2 — полициклические ароматические углеводороды; СА3— смолы; СА4 — асфальтены; СА5 — карбены; СА6 — карбоиды; СА7 — летучие (данные Г.Г. Валявина)
Влияние температуры. Поскольку значения энергии активации отдельныхреакцийтермолизаразличаютсямеждусобойвесьмасущественно, то температура как параметр управления процессом позволяет не только обеспечить требуемую скорость термолиза, но прежде всего регулировать соотношение между скоростями распада и уплотнения и, что особенно важно, между скоростями реакций поликонденсации, тем самым свойства фаз и условия кристаллизации мезофазы. При этом регулированием продолжительности термолиза представляется возможным обрывать на требуемой стадии «химическую эволюцию» в зависимости от целевого назначения процесса. С позиций получения кокса с лучшей упорядоченностью структуры коксование сырья целесообразно проводить при оптимальной температуре. При пониженной температуре ввиду малой скорости реакций деструкции в продуктах термолиза будут преобладать нафтено-ароматические структуры с короткими алкильными цепями, которые будут препятствовать дальнейшим реакциям уплотнения и формированию мезофазы. При температуре выше оптимальной скорость реакций деструкции и поликонденсации резко возрастают. Вследствие мгновенного образования большого числа центров кристаллизации коксующийся слой быстро теряет пластичность, в результате чего образуется дисперсная система с преобладанием мелких кристаллов. Возникающие при этом сшивки исвязимеждусоседнимикристалламизатрудняютперемещениеирост ароматических структур. Более упорядоченная структура кокса получается при средней (оптимальной) температуре коксования (=480°С),
581

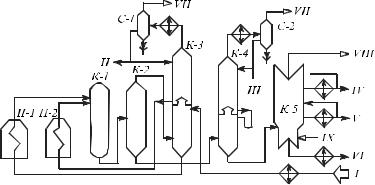
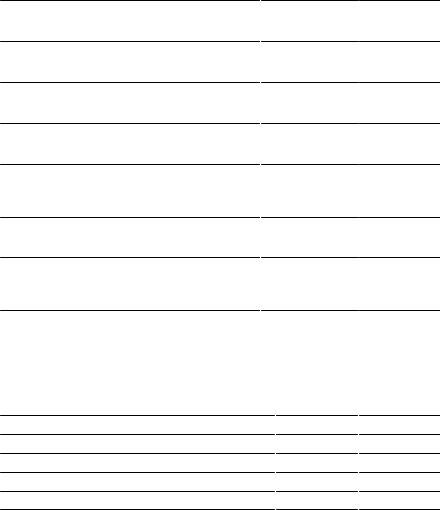
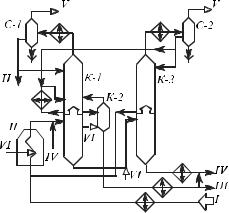