
ТКМ -ММФ / Лекция по ОМД
.pdf
Очистка поковок. Готовые поковки необходимо очистить от окалины для выявления дефектов штамповки и улучшения условий механической обработки деталей. Очистку поковок производят в дробеструйных установках, галтовочных барабанах или травлением.
Правка поковок. В результате термической обработки, неравномерного охлаждения после штамповки, застревания поковки в ручье и последующего извлечения ее, при обрезке облоя, а также ударов при транспортировке или
передаче в технологической линии может происходить искажение формы (коробление). Горячую правку поковок производят на специально выделенном оборудовании (молот или пресс) или на обрезном прессе совместно с обрезкой облоя или после нее. Иногда правку поковок осуществляют в чистовом ручье основного штампа после обрезки облоя, что снижает стойкость ручья и производительность поточной линии. Холодную правку производят на гидравлических прессах после термической обработки и очистки поковок от окалины.
Калибровку применяют для повышения точности формы и размеров поковки, снижения шероховатости поверхности. В результате калибровки объем механической обработки существенно уменьшается, а в ряде случаев устраняется совсем. Производят калибровку чаще в холодном состоянии путем незначительной пластической деформации на чеканочных прессах.
Готовые поковки после контроля и необходимых испытаний передаются на склад готовой продукции и затем в механические цеха на дальнейшую обработку.
2.5. Оформление чертежа поковки
Чертеж поковки разрабатывается на основании чертежа детали. Поскольку детали частично или полностью подвергаются механической обработке, то в соответствие с существующими ГОСТами на размеры деталей назначают припуски на механическую обработку и предельные отклонения размеров (допуски). Часто по технологическим соображениям с целью упрощения конфигурации поковки (по сравнению с конфигурацией детали) назначают напуски. Кроме того, в отличие от чертежа детали на чертежах поковок сопряжения обязательно должны быть плавными.
Для механических испытаний поковок необходимо предусматривать специальный припуск – пробу. Пример поковки с припусками, напуском и ²пробой² приведен на рис. 15.
Изготовление данной поковки строго по контуру вала было бы нерентабельно, так как в этом случае потеря времени на точную ковку и увеличение времени работы кузнечного
оборудования не окупались бы Рис. 15. Поковка многоступенчатого вала получаемой экономией металла
и некоторым сокращением объема механической обработки. Напуски особенно часто назначают при ковке поковок с наличием фланцев, буртов, уступов, выемок и проточек (рис. 15). В связи с этим ГОСТ 7062-90 и ГОСТ 7829-70 предусматривают минимальные размеры выступов, фланцев, буртов, выемок и уступов в зависимости от размеров смежных участков поковки. При этом следует иметь в виду, что вопрос о необходимости назначения напусков решают после начисления припусков.
58
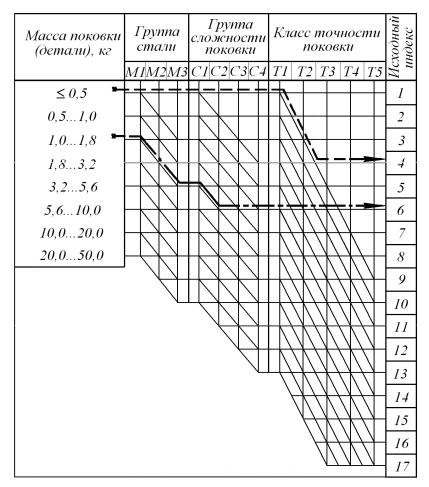
Припуски и допуски на размеры поковок выбирают согласно стандартам в зависимости от типа поковок, их массы или наибольшей длины и типа оборудования. Так для поковок, изготавливаемых ковкой на прессах, значения припусков и допусков регламентированы ГОСТ 706290. Для поковок, получаемых ковкой на молотах, припуски и допуски определяются по ГОСТ
7829-70.
Указанные выше ГОСТы регламентируют припуски и допуски и на другие виды поковок, а также на предельные размеры уступов, фланцев, буртов, выемок и т. п.
Припуски и допуски на поковки, получаемые горячей объемной штамповкой, назначают в зависимости от массы детали, группы материала, степени, сложности поковки С1-C4 и
класса точности, которые определяют индекс поковки, и шероховатости поверхности детали
(ГОСТ 7505-89). Различают три группы материалов: |
|
||||
М1 – |
сталь углеродистая или легированная с содержанием углерода до 0,35% или леги- |
||||
рующих элементов до 2 %; |
|
|
|||
М2 – |
сталь с содержанием углерода 0,35–0,65 % или легирующих элементов 2–5 %; |
||||
М3 – сталь, содержащая углерода свыше 0,65 % или легирующих элементов более 5 %. |
|||||
ГОСТ 7505-89 предусматривает поковки пяти классов точности: |
|
||||
Т1 – |
поковки, подвергаемые дополнительной калибровке; |
|
|||
Т2 – |
поковки, получаемые закрытой (безоблойной) штамповкой на кривошипных прес- |
||||
сах и автоматах; |
|
|
|
|
|
Т3 – |
поковки, получаемые выдавливанием или в закрытых штампах на молотах; |
||||
Т4, Т5 – поковки, штампуемые в открытых штампах (облойная штамповка) на КГШП, |
|||||
молотах и горизонтально-ковочных машинах. |
|
|
|||
Исходный |
индекс ука- |
|
Таблица 1 |
||
зывают на чертеже |
поковки. |
|
|||
Определение индекса поковки |
|
||||
Определение индекса поковки |
|
||||
|
|
||||
производится по табл. 1, вы- |
|
|
|||
бирая соответствующую стро- |
|
|
|||
ку и смещаясь по горизонтали |
|
|
|||
вправо или по |
утолщенным |
|
|
||
наклонным |
линиям |
вправо – |
|
|
|
вниз до пересечения с верти- |
|
|
|||
кальными линиями, соответ- |
|
|
|||
ствующим |
заданным группе |
|
|
||
стали М, степени сложности С |
|
|
|||
и классу точности Т. |
|
|
|
||
Пример: |
1. |
Поковка |
|
|
|
массой 0,5 кг, группы стали |
|
|
|||
М1, степени сложности С1, |
|
|
|||
класса точности Т3 имеет |
|
|
|||
индекс 4 (пунктирная линия). |
|
|
|||
2. Поковка массой 1,5 |
|
|
|||
кг (М3, С2, Т1) имеет индекс 6 |
|
|
|||
(штрихпунктирная линия). |
|
|
|||
На штампуемые поков- |
|
|
|||
ки назначают напуски на вы- |
|
|
|||
емки, если они препятствуют |
|
|
|||
раскрытию штампа, а также на |
|
|
|||
глубокие выемки, совпадаю- |
|
|
|||
щие с движением ползуна, ес- |
|
|
|||
ли h > 0,8d' (см. рис. 10, в). |
|
|
|||
Сквозные |
отверстия и |
|
|
59
углубления выполняют в поковках, если их наименьший размер или диаметр больше или равен высоте поковки, но не менее 30 мм. В противном случае назначают напуск, а наметки под отверстия будут глухими (полусферическими с радиусом 0,5d').
На все поверхности, перпендикулярные плоскости разъема штампа, назначают штамповочные уклоны, равные 7о для наружных и 10о для внутренних поверхностей. Если штамповка
производится на кривошипном прессе с выталкивателем, то уклоны составляют соответственно
5о и 7о.
На основании полученных размеров поковки оформляют поковочный чертеж, при этом должны быть соблюдены следующие общепринятые правила выполнения чертежей поковок:
1.Габаритный контур готовой детали вычерчивают на чертеже поковки тонкими штрихпунктирными линиями. Контур поковки вычерчивают линиями нормальной толщины по ее расчетным номинальным размерам.
2.Номинальные размеры по длине поковки с уступами проставляют от одной или ограниченного количества баз. Один концевой уступ включают в размер общей длины поковки.
3.Расчетные (номинальные) размеры поковки с выбранными допусками обозначают над размерной линией.
4.Номинальные размеры поковок, изготавливаемых ковкой на прессах, округляют до чисел, оканчивающихся на 5 или 0.
5.Верхнее или нижнее отклонения размеров обозначают цифрами со знаком ²плюс² или ²минус², расположенными справа и выше номинального размера поковки.
6.На чертеже поковки указывают исходные базовые поверхности.
Определение массы и размеров исходной заготовки
Для правильного выбора исходного материала необходимо знать массу и размеры заготовки, из которой можно изготовить заданную поковку с наименьшим расходом металла и при надлежащем качестве. Массу и размеры исходной заготовки определяют на основе разработанного чертежа поковки, исходя из ее размеров и объема, а также технологии получения.
Объем поковки Vп находят по ее номинальным размерам. При сложной конфигурации объем определяют как сумму объемов Vi всех (n) отдельных простых геометрических тел (цилиндр, сфера, параллелепипед):
n
Vп = ∑ Vi.
i =1
Выбор заготовки для штампованной поковки
Для выбора заготовки под штамповку необходимо разработать чертеж поковки, найти ее объем Vп. Объем исходной заготовки Vисх будет больше объема поковки Vп на величину объема отходов: облоя Vоб, угара Vуг, удаляемых перемычек Vпер, клещевины Vкл
Vисх = Vп + Vуг + Vоб + Vпер + Vкл.
Потери металла на угар Vуг зависят от способа нагрева и составляют при нагреве в газовых печах 1–2 %, а при индукционном нагреве – 0,5–1 % от объема поковки.
Облой после штамповки расположен по всему периметру поковки, его поперечные размеры определяют размеры выбранной облойной канавки. Площадь поперечного сечения облоя Fоб выбирают для молотовых штампов несколько меньше площади сечения облойной канавки Fок, а для прессовых – в z раз больше площади поперечного сечения мостика Fм
Fоб = ζFок ; Fоб = zFок ,
где ζ = 0,6–0,8; z = 1,5–2,5 – коэффициенты заполнения облойной канавки, большие значения которых соответствуют более сложным поковкам (группа С4), а меньшие– простым поковкам (группа С1).
Объем облоя находят по формуле Vоб = Fоб Пп
60

где Пп – периметр поковки в плоскости разъема штампа (в плане), который определяют как сумму внешних частей периметров простых геометрических фигур поковки
n
Пп = ∑ Пфпi . i =1
Клещевину как искусственное увеличение исходной заготовки предусматривают в специальных случаях для удобства захвата поковки клещами при переносе из одного ручья штампа в другой. Длина клещевины составляет от 0,5 до одного диаметра.
Объем перемычки отверстия Vпер необходимо учесть в балансе металла Vпер = Sперt ,
где Sпер – площадь перемычки в плане; t – толщина перемычки, назначаемая обычно 0,1 ее ши-
рины или диаметра, но не менее 4 мм.
Выбор размеров исходной заготовки производят по сортаменту проката, задаваясь диаметром dисх или стороной квадрата аисх, находя по закону постоянства объема длину
lисх = Vисх . При этом с целью обеспечения удовлетворительного качества отрезки на пресс-
Fисх
ножницах должно выполнятся условие lисх > 1,25dисх .
Диаметр или сторону квадрата проката назначают с учетом возможной укладки в ручей штампа в зависимости от типа поковки: круглые в плане, штампуемые осадкой; поковки с утолщением, получаемые высадкой; поковки, получаемые выдавливанием и поковки удлиненной формы, штампуемые плашмя.
Для круглых в плане поковок, получаемых осадкой, диаметр исходной заготовки можно ориентировочно определить как
dисх = (0,8 − 1)3 Vисх
и проверить на устойчивость при осадке lисх ≤ 2,5dисх .
Для поковок с утолщениями, получаемыми высадкой, диаметр исходной заготовки выбирают равным или несколько меньше диаметра стержня поковки, чтобы заготовку можно было расположить в ручье штампа.
Если поковки получают выдавливанием, то диаметр исходной заготовки выбирают равным или несколько меньше наибольшего диаметра поковки.
Диаметр исходной заготовки для удлиненных поковок, штампуемых плашмя, назначают в соответствии с эпюрой диаметров или эпюрой поперечных сечений и выбранным способом фасонирования заготовки.
Если фасонирование осуществляют в ковочных вальцах или протяжном ручье молотового штампа, то диаметр исходной заготовки выбирают по стандарту равным или на 3–5 % больше наибольшего размера эпюры диаметров после выравнивания местных перепадов поперечных сечений.
При отсутствии заготовительных ручьев диаметр исходной заготовки назначают на
|
|
Vисх |
|||
2…5 % больше, чем средний по эпюре диаметров: |
dср |
= 1,13 |
|
|
, чтобы длина исходной |
l |
|
||||
|
|
|
э |
заготовки была несколько меньше длины ручья.
61