
rol_nauki_v_razvitii_obshchestva_sbornik_statey_mezhdunarodn
.pdfВ сравнении с лампами накаливания и люминесцентными лампами светодиоды обладают рядом преимуществ:
–Светодиоды потребляют значительно меньше электрической энергии по сравнению с другими существующими источниками света (В 10 раз экономичнее ламп накаливания и в два раза – люминесцентных ламп).
–Срок службы светодиодного освещения, при соблюдении надлежащих параметров, достигает 50 000 часов, что в 50 раз превышает срок службы ламп накаливания и в 10 раз – люминесцентных ламп. Применительно к уличному освещению, экономия на замене и обслуживании ламп в светильниках превышает экономию на потребляемой электроэнергии.
–Применение светодиодов дает возможность получать различные спектральные характеристики без использования светофильтров.
–Светодиоды позволяют получить направленное излучение, с возможностью изменения угла излучения с помощью линз (линзы для ламп накаливания больше по габаритам и имеют более высокую стоимость).
–Отсутствует инерционность при включении и выключении, что является важной характеристикой для светодинамических установок.
–Возможность использования специальных диммеров (устройства для регулировки яркости светодиода путем изменения питающего его постоянного напряжения) по сравнению с люминесцентными лампами.
–Высокая прочность и безопасность в использовании.
–Компактные размеры.
–Малое инфракрасное и ультрафиолетовое излучение.
–Низкое тепловыделение (для устройств с низкой мощностью).
–Отсутствие в использовании ртутных паров.
–Устойчивость светодиодных ламп к вандализму.
–Использование светодиодов в аварийных ситуациях увеличивает время использования резервных источников питания.
– Спектр белого светодиода подобен спектру естественного света, имеет приятное равномерное свечение без мерцаний. Это положительно влияет на эмоциональное состояние, повышает умственную и физическую активность.
На сегодняшний день у светодиодов также имеется ряд недостатков:
–Высокая цена по отношению к другим осветительным приборам является основным недостатком.
–Необходимость использования преобразователя напряжения или последовательного соединения светодиодов, так как напряжение питания их значительно ниже, чем у ламп накаливания.
–Высокие требования к теплоотводу, так как температура оказывает влияние на надежность осветительного прибора.
–Светодиоды не могут использоваться при высоких (выше 100 градусов) температурах окружающей среды.
–Около 20% излучаемого света отражаются обратно в диод.
Применение нанотехнологий в производстве светодиодных ламп позволяет устранить значительное количество недостатков. Некоторые производители уже начали адаптацию светодиодного освещения по технологии LED (нанопечати светодиодов), что значительно снижает стоимость продукции. Так же нанотехнологии позволяют увеличить эффективность светодиодов путем проделывания в их поверхности сотни тысяч нано–отверстий, в результате такой
51
технологии диод излучает больше света. Так как внутри диода остается меньше света, тепловыделение снижается.
На данный момент светодиодные технологии освещения нашли широкое применение в машиностроении, подсветке зданий, улиц, фонтанов, тоннелей и мостов, в производственных и офисных помещениях. Надежность светодиодов позволяет применять их в труднодоступных для замены местах и экстремальных условиях.
Полный переход России на светодиодные технологии в освещении за счет сокращения потребления электроэнергии позволит экономить ежегодно более 2 млрд евро, а период окупаемости инвестиций составит всего 8 месяцев. Такая ежегодная экономия сопоставима с суммой, которая потребуется, чтобы дважды осветить светодиодами все российские дороги федерального значения или половину всех домашних хозяйств страны. Светодиодные технологии позволят сократить потребление электроэнергии на 53,2 ТВт в год, а расходы электроэнергии на освещение на 46,3%. Это позволит сократить выбросы углекислого газа на 16,9 млн тонн в год, что эквивалентно выбросам от 4,2 млн автомобилей[3].
Именно светодиодные источники света являются наиболее перспективным направлением повышения энергоэффективности и снижения энергоемкости отечественной экономики как с точки зрения затратности, так и практического применения.
Список использованной литературы:
1.Федеральный закон Российской Федерации от 23 ноября 2009 г. N 261–ФЗ «Об энергосбережении и о повышении энергетической эффективности и о внесении изменений в отдельные законодательные акты Российской Федерации»
2.Материнский С. В., Федюнина Т. В. Социально–экономическое развитие Саратовской области по инновационно–инвестиционной модели / C. В. Материнский, Т. В. Федюнина // Материалы Международной научно–практической конференции «Проблемы социально–экономического развития регионов», 4 марта
2014 г. Уфа: РИЦ БашГУ, 2014. – с 68.
3.«ЭнергоСовет» портал по энергосбережению [Электронный ресурс]. – Режим доступа: http://www.energosovet.ru/news.php?zag=1383914259
©Т.В.Федюнина, С. В. Материнский, 2014
УДК 66.063
А.Н. Михальченкова
аспирант первого года обучения, специальность 05.17.08 «Процессы и аппараты химической технологии», Московский государственный машиностроительный университет (МАМИ), г. Москва, Российская Федерация
М.Г. Лагуткин
доктор технических наук, профессор.
АНАЛИЗ ВЛИЯНИЯ КОНСТРУКТИВНЫХ И РЕЖИМНЫХ ПАРАМЕТРОВ РАБОТЫ ВИХРЕВОГО ЭЖЕКТОРА ДЛЯ СИСТЕМЫ ЖИДКОСТЬ-ЖИДКОСТЬ НА КОЭФФИЦИЕНТ ЭЖЕКЦИИ
Вихревые эжекторы используются в промышленности в процессах эжекции и смешения потоков газов и жидкостей, но аппараты вихревого типа не получили
52
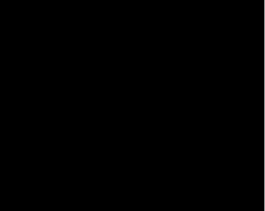
широкого распространения из-за отсутствия единой надежной методики расчета. Разработка методики расчета вихревых эжекторов - актуальная задача.
Вихревой эжектор (рис.1) работает следующим образом: рабочий поток жидкости подается в цилиндрический корпус 1 аппарата через тангенциально расположенный патрубок 2 и закручивается. На оси аппарата создается разрежение при увеличении давления во вращающемся потоке жидкости по направлению к стенкам корпуса, в результате чего становится возможным подсос жидкости через патрубок входа эжектируемого потока 3, расположенный коаксиально
цилиндрическому корпусу 1 аппарата со стороны входа рабочего потока. Внутри аппарата рабочий и эжектируемый потоки смешиваются и выходят через тангенциальный патрубок выхода смешанного потока 4, расположенный с противоположной стороны аппарата.
Основная характеристика работы вихревого эжектора - коэффициент эжекции u (отношение массовых расходов эжектируемого и рабочего потоков жидкости).
Цель исследования - определение оптимальных конструктивных и режимных параметров работы вихревого эжектора и получение с помощью теории подобия уравнения для расчета коэффициента эжекции.
Изучение работы вихревого эжектора проводилось с помощью программы Flow Simulation, являющейся программной компонентой Solid Works.
Исследование было проведено для аппаратов с диаметром цилиндрического корпуса D=0,05 м. К основным конструктивным и режимным параметрам работы вихревого эжектора можно отнести диаметры патрубков входа рабочего и эжектируемого потоков жидкости и патрубка выхода смешанного потока и скорость потока жидкости в патрубке входа рабочего потока. Кроме перечисленных параметров на величину коэффициента эжекции влияет длина циллиндрического корпуса аппарата. Был проведен анализ в целях определения наиболее рациональных значений этих величин, при которых будет достигаться максимальное значение коэффициента эжекции.
Зависимость коэффициента эжекции от приведенных выше параметров можно
записать в следующем виде: U=f(Dвс /D; e/D;(Dвх+Dвс)/Dвых; Dвх/D; V) (1)
где u - коэффициент эжекции; D - диаметр цилиндрического корпуса аппарата; е - расстояние от нижней кромки тангенциального патрубка входа рабочего потока 2 до верхней кромки тангенциального патрубка выхода смешанного потока 4; Dвх - диаметр патрубка входа рабочего потока жидкости 2; Dвс - диаметр патрубка входа эжектируемого потока 3; Dвых - диаметр патрубка выхода смешанного потока 4; V - динамический напор в патрубке входа рабочего потока жидкости 2.
На рис. 2 представлен график зависимости величины коэффициента эжекции от отношения расстояния от нижней кромки патрубка входа рабочего потока до
53
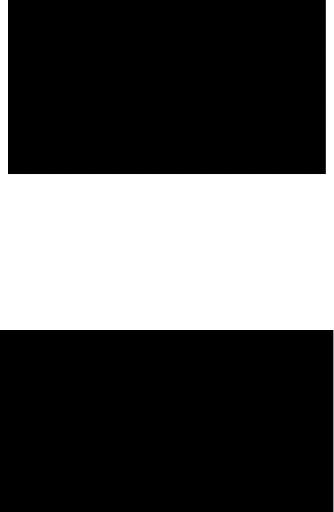
верхней кромки патрубка выхода смешанного потока к диаметру цилиндрического корпуса аппарата при Dвс = 0,6D; Dвых = 1,1(Dвх + Dвс); V=40 Па.
Рис. 2 - отношение величины коэффициента эжекции от отношения расстояния от нижней кромки патрубка входа рабочего потока до верхней кромки патрубка выхода смешанного потока к диаметру цилиндрического корпуса аппарата.
Коэффициент эжекции принимает свое максимальное значение при е=1,5D, значение е=1,5D является наиболее рациональным и в последующих расчетах будет принято в качестве постоянной величины.
На рис. 3, а представлен график зависимости величины коэффициента эжекции от отношения диаметра патрубка входа эжектируемого потока к диаметру цилиндрического корпуса аппарата при Dвых = 1,1(Dвх + Dвс); V = 40 Па; е=1,5D.
Рис. 3, а - график зависимости величины коэффициента эжекции от отношения диаметра патрубка входа эжектируемого потока к диаметру цилиндрического корпуса аппарата.
Коэффициент эжекции принимает максимальное значение при Dвс = 0,6D.
На рис. 3, б представлен график зависимости величины коэффициента эжекции от отношения суммы величин диаметров патрубков входа рабочего потока и патрубка входа эжектируемого потока к величине диаметра поперечного сечения патрубка выхода смешанного потока при Dвс=0,6D; V=40Па; е=1,5D
54
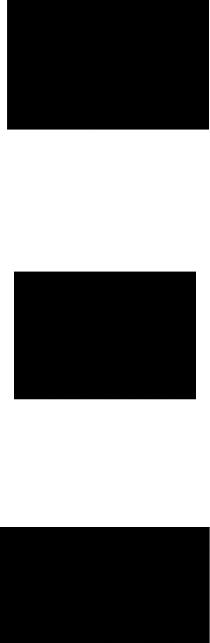
Рис. 3, б - график зависимости величины коэффициента эжекции от отношения суммы величин диаметров патрубков входа рабочего потока и патрубка входа эжектируемого потока к величине диаметра поперечного сечения патрубка выхода смешанного потока.
Значение Dвх + Dвс = 1Dвых обеспечивает максимальную величину коэффициента эжекции.
На рис. 3, в представлен график зависимости величины коэффициента эжекции от величины динамического напора в патрубке входа рабочего потока при Dвс = 0,6D; Dвых=1(Dвх+ Dвс); е=1,5D
Рис. 3, в - график зависимости величины коэффициента эжекции от динамического напора в патрубке входа рабочего потока.
Оптимальной величиной гидравлического напора, исходя из данных, исследования, является значение 40 Па.
На рис. 3, г представлен график зависимости величины коэффициента эжекции от отношения величины диаметра патрубка входа рабочего потока к величине диаметра цилиндрического корпуса аппарата при Dвс = 0,6D; Dвых = 1(Dвх + Dвс); V =
40 Па; е=1,5D
Рис. 3, г - график зависимости величины коэффициента эжекции от отношения величины диаметра патрубка входа рабочего потока к величине диаметра поперечного сечения цилиндрического корпуса аппарата.
55

Коэффициент эжекции при Dвх < 0,2D начинает заметно увеличиваться, но при этом в случае создания избыточного давления внешней среды на выходе из аппарата, величина коэффициента эжекции при малых площадях сечения патрубка входа рабочего потока будет резко уменьшаться. Кроме того, с уменьшением площади поперечного сечения патрубка входа рабочего потока жидкости при неизменном значении скорости жидкости будет снижаться её расход, что приведет к снижению расхода эжектируемого потока.
Математическое моделирование процесса
Функциональную зависимость (1) с учетом того, что отношение е/D принимается в качестве постоянной величины, можно представить в виде уравнения:
u = k |
|
|
|
|
|
|
(2) |
( |
) ( ) |
|
|||||
u=k |
|
степеней, принимает вид: |
|||||
И после нахождения( )показателей( ) |
где n = -3,7 при Dвх +Dвс = (0,5 - 0,7) Dвых, n = -1при Dвх +Dвс = (0,7 - 0,83) Dвых, n =0,14 при Dвх +Dвс = (0,83 - 1) Dвых; m=-5,7 при Dвх = (0,1 - 0,2)D, m = 5,7 при Dвх = (0,2 - 0,3)D; p=-1,6 при V = (5 - 65) Па, m = -0,7 при V = (70500) Па.
(©) Михальченкова А.Н., Лагуткин М.Г., 2014 г
УДК 621.923.74
А.А.Николаенко
Д.т.н., профессор кафедры «Технология машиностроения» Южно-Уральского государственного университета г. Челябинск, Российская Федерация
МОДЕЛИРОВАНИЕ УПРУГИХ ПЕРЕМЕЩЕНИЙ ПРИ ОДНОХОДОВОМ ПЛОСКОМ ГЛУБИННОМ ШЛИФОВАНИИ
Кaчество деталей – комплекс показателей, среди которых на первом месте стоят точность размеров, формы и взаимного расположения поверхностей. Эти показатели во многом зависят от податливости технологической системы. Чем меньше податливость тем, меньше величина ее упругого перемещения при резании, а значит выше точность размеров и формы изготовленных деталей.
Цeль данного исследования – разработать аналитические математические модели для расчета параметров точности деталей при одноходовом глубинном шлифовании периферией круга (ОГШПК). Зaдачи исследования: 1) разработать математическую модель для обеспечения точности размеров детали при ОГШПК; 2) разработать математическую модель для обеспечения прямолинейности поверхности детали при ОГШПК; 3) разработать математическую модель для обеспечения параллельности поверхностей детали при ОГШПК.
Oбработка детали осуществляется в технологической системе, которая находится под воздействием мнoжества факторов (рис. 1). Упругиe перемещения элементов технологической системы делятся на упругие деформации и упругие смещения [1]. Упругиe деформации – отклонение элементов системы под действием силы, после аннулирования которой они исчезают. Упругиe смещения являются результатом перемещений деталей станка вследствие наличия зазоров между ними. В целом упругиe перемещения являются функцией действующих сил и податливости станка.
56
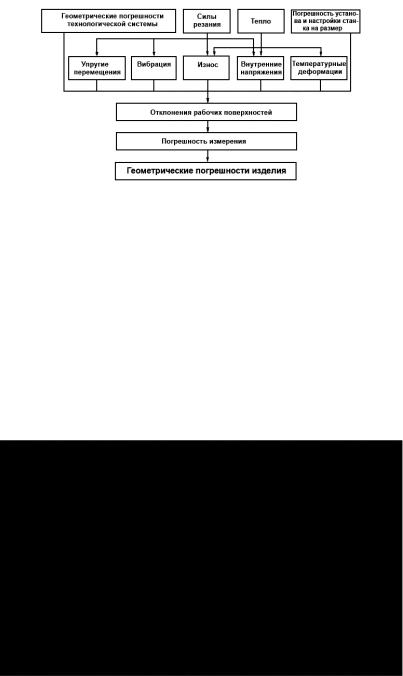
Рис. 1. Факторы, влияющие на формирование погрешности детали при ОГШПК
Практика показывает, что в зависимости от требуемой точности детали, режимов резания и характеристик круга глубина шлифования осуществляется за один или несколько рабочих ходов.
Рaсчетная схема для моделирования упругих перемещений при ОГШПК представлена на рис. 2.
На рис. 2 Hзагmin , Hзагmax – соответственно минимальная и максимальная высота
заготовки, м; |
H min |
, H max |
– соответственно минимальная и максимальная |
|
дет.ф |
дет.ф |
|
фактическая высота детали, м; Hminдет. з , Hmaxдет. з – соответственно минимальная и максимальная заданная чертежом высота детали, м; tн – номинальная глубина
резания, м; tmin |
tmax – соответственно минимальная и максимальная фактическая |
ф , |
ф |
глубина резания, м; ymin , ymax – соответственно минимальное и максимальное
упругое отжатие, м; Т – допуск на размер, м; ау – доля допуска на размер, отводимая для упругих перемещений.
Рис. 2. Схема для моделирования упругих перемещений при ОГШПК
57
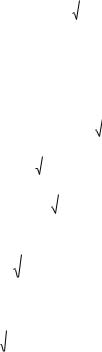
Расчет точности размеров, формы и взаимного расположения поверхностей деталей производится следующим образом.
Под действием силы Рy шлифовальный круг упруго перемещается на текущую величину y (в пределах уmin… ymax), что обуславливает изменение номинальной глубины резания tH до значения фактической глубины резания tф (в диапазоне
tфmin ... tфmax ), т.е.
y = t H – t ф . |
(1) |
Упругое перемещение в технологической системе в направлении выполняемого размера вызывает отклонение размера детали. Величина упругого перемещения
определяется по формуле: |
|
||
y Py fc , |
(2) |
||
где Py – радиальная составляющая силы резания, Н; |
fc – податливость |
||
технологической системы [2], м/Н. |
|
||
Приравняв правые части уравнений (1) и (2), получим: |
|
||
tн – tф = Ру · fc. |
(3) |
||
Радиальную составляющую силы резания Py можно сжато записать следующим |
|||
образом [3]: |
|
||
Pyi Ai t фi Bi |
|
, |
(4) |
t фi |
где t фi – фактическая глубина резания для i–х условий шлифования, м; Ai и Bi –
коэффициенты, характеризующие i-ые условия шлифования (величины Ai и Bi рассчитывают для параметров, остающихся постоянными, т.е. для обработки одной детали, одной характеристикой круга, на одном режиме резания и постоянстве других условий шлифования).
Подставляя в (3) вместо Py правую часть выражения (4), получим:
tн tф Ai tф. i fc |
Bi fc |
|
|
. |
(5) |
|||
|
tф.i |
|||||||
После переноса левой части уравнения (5) в правую, получим: |
|
|||||||
Ai tф. i fc Bi fc |
|
|
tн |
tф 0 . |
(6) |
|||
tф.i |
||||||||
После приведения подобных, получим квадратное уравнение: |
|
|||||||
(1 fc Ai ) tф.i fc Bi |
|
t н.i 0. |
(7) |
|||||
tф.i |
Решения квадратного уравнения (7) относительно фактической глубины резания
выглядят следующим образом: |
|
|
|
|
|
|
|
|
|
2 |
|
|||||
|
|
|
|
|
|
|
|
|
|
|
|
|
|
|||
|
max |
|
f B |
(f B )2 |
4t |
нi |
(1 |
f A ) |
|
|||||||
t |
|
|
i |
i |
|
|
i |
|
|
|
|
|
||||
фi |
|
|
|
|
|
|
|
|
|
|
|
, |
(8) |
|||
|
|
|
2(1 f Ai ) |
|
|
|
||||||||||
|
|
|
|
|
|
|
|
|
|
|
|
|
||||
|
|
|
|
|
|
|
|
|
|
|
|
|
|
|
|
|
|
|
|
|
|
|
|
|
|
|
|
|
|
|
|
|
|
|
|
|
|
f B |
|
|
|
|
|
|
|
2 |
|
|||
|
|
|
(f B )2 4 |
(t |
|
)(1 f A |
|
) |
|
|||||||
t min |
|
|
|
i |
i |
’нi |
|
|
i |
|
|
|
|
|
||
|
|
|
|
|
|
|
|
|
|
|
|
|
. |
(9) |
||
|
|
|
2(1 f Ai ) |
|
|
|
|
|
|
|||||||
фi |
|
|
|
|
|
|
|
|
|
|
|
|
|
|||
|
|
|
|
|
|
|
|
|
|
|
|
|
|
|
|
|
Уравнения (8), (9) и (1) позволяют перейти к расчету максимальных и минимальных упругих перемещений в технологической системе:
58

yimax t нi t
yimin t нi
|
|
|
|
|
|
|
|
|
|
|
|
|
2 |
|
|
|
|
|
|||||
max |
|
|
|
f B |
(f B )2 4t |
нi |
(1 f A ) |
|
|
|
|
|
|||||||||||
t |
|
|
|
|
i |
|
|
i |
|
|
|
i |
|
|
, |
|
|
|
(10) |
||||
фi |
|
нi |
|
|
|
|
|
|
|
|
|
|
|
|
|
|
|
|
|
||||
|
|
|
|
|
2(1 f Ai ) |
|
|
|
|
|
|
|
|
||||||||||
|
|
|
|
|
|
|
|
|
|
|
|
|
|
|
|
|
|
|
|||||
|
|
|
|
|
|
|
|
|
|
|
|
|
|
|
|
|
|
|
|
|
|
2 |
|
|
|
|
|
|
|
|
|
|
|
|
|
|
|
|
|
|
|
|
|||||
|
|
|
|
|
|
f B |
|
(f B |
)2 4(t |
нi |
|
)(1 f A |
) |
|
|||||||||
t min t |
|
|
|
i |
|
|
i |
|
|
|
|
|
|
i |
|
|
|
. (11) |
|||||
нi |
|
|
|
|
|
|
|
|
|
|
|
|
|
|
|
|
|||||||
|
|
|
2(1 f Ai ) |
|
|
|
|
|
|
||||||||||||||
|
фi |
|
|
|
|
|
|
|
|
|
|
|
|
|
|
||||||||
|
|
|
|
|
|
|
|
|
|
|
|
|
|
|
|
|
|
|
|
|
|
|
|
Отклонение размеров, формы, взаимного расположения поверхностей детали при механической обработке определяется по уравнению:
= дин стат уст , |
(12) |
где дин – динамическая составляющая отклонения параметра, возникающая вследствие упругих перемещений в технологической системе, м; стат – статическая
составляющая отклонения параметра, возникающая при настройке, м; уст – отклонение параметра, вызванное погрешностью установки заготовки, м.
В силу того, что стат и уст не зависят от режима резания, то управление точностью обработки обычно осуществляют, воздействуя на динамическую
составляющую дин (т.е. на упругие перемещения в технологической системе).
Для обеспечения заданной точности размеров детали должно быть выполнено следующее условие:
y max a |
— |
T , |
(13) |
|
где y max – максимальное упругое перемещение в технологической системе, |
м; |
|||
ау < 1 – доля допуска на размер детали, используемая для упругих перемещений; |
Т |
|||
– допуск на размер детали, м. |
|
|
|
|
Для обеспечения заданной прямолинейности поверхности детали должно быть выполнено условие:
y max ymin T aiT , |
(14) |
где – расчетное отклонение поверхности детали от прямолинейности, м; T – допуск прямолинейности, м; Т – допуск на размер детали, м; аi – коэффициент,
устанавливающий соотношение между допуском формы и допуском размера. Cоотношения между допуском формы и допуском размера в Единой системе
допусков и посадок установлены посредством трех уровней: A, B и C: А – нормальная точность, когда для допуска формы используется 60 % допуска размера (аA = 0,6); B – повышенная точность, когда для допуска формы используется 40 % допуска размера (аB = 0,4); С – высокая точность, когда для допуска формы используется 25 % допуска размера (аС = 0,25).
Для oбеспечения заданной пaраллельности поверхностей детали должно быть выполнено условие:
|
|
|
|
|
max |
min |
|
|
|
|
|
|
H дет.ф |
H дет.ф T ai T , |
(15) |
|
где |
– расчетное отклонение поверхностей детали от параллельности, м; |
|||||
H |
max |
и |
H |
min |
– соответственно максимальная и минимальная фактическая |
||
дет.ф |
дет.ф |
высота детали, м; T – допуск параллельности, м; Т – допуск на размер детали, м;
59
ai – коэффициент, устанавливающий соотношение между допуском параллельности
идопуском размера.
Список использованной литературы:
1.Пименов Д.Ю. Математическое моделирование упругих перемещений технологической системы при торцевом фрезеровании с учетом износа инструмента
/Д. Ю. Пименов, В. И. Гузеев, А. А. Кошин // Вестник машиностроения. – 2011. – №11. – С. 69-73.
2.Переверзев П.П. Моделирование технологических ограничений при оптимизации автоматических циклов шлифования. – Челябинск: Вестник ЮжноУральского государственного университета, №12 (271), 2012. - с.165-167.
3.Николаенко А.А., Кулыгин В.Л. Устройство для определения жесткости шпинделей: Патент № 1833249, В23В25/00.
©А.А. Николаенко, 2014
УДК 621.436
С.В.Романов
Преподаватель кафедры сельскохозяйственных и мелиоративных машин ФГБОУ ВПО «Государственный аграрный университет Северного Зауралья г.Тюмень, Российская Федерация
ПОВЫШЕНИЕ ТОПЛИВНОЙ ЭКОНОМИЧНОСТИ ДИЗЕЛЬНОГО ДВИГАТЕЛЯ ПУТЕМ ИСПОЛЬЗОВАНИЯ ВОДОТОПЛИВНЫХ ЭМУЛЬСИЙ И ВОДНОЙ ИНЖЕКЦИИ
Жидкие углеводородные топлива, запас которых, к сожалению, ограничен и, год за годом, сокращается, еще долго останутся незаменимым топливом для двигателей внутреннего сгорания. В этой связи вопросы их экономного расходования остаются актуальными, а проводимые исследования по повышению топливной эффективности работы ДВС практически значимыми. За более чем вековую историю общий КПД лучших бензиновых двигателей (с искровым принудительным зажиганием) не превысил 25…30 %. КПД лучших дизельных моторов, даже в их самых экономичных массогабаритных вариантах, не превышает 40…45 %. КПД малых дизелей ниже на 10…15 %.
Одним из направлений повышения топливной эффективности двигателей внутреннего сгорания является использование воды как добавки к углеводородным топливам. Идея использования воды для улучшения работы ДВС не нова и представляется весьма заманчивой. Привлекательность этой идеи объясняется тем, что ее применение не требует больших затрат на создание новых производственных мощностей. По данным источника [1] водная оболочка Земли – океаны, моря, озера, реки – составляет около 1,4…1,5 млрд. км3, то есть несравнимо больше запасов углеводородного топлива. Если учесть, что вода, после ее использования в ДВС, возвращается обратно в гидросферу, причем очищенной, то ее запасы практически неисчерпаемы.
Нужно отметить, что первый патент на использование воды в двигателях внутреннего сгорания был получен более века назад Н. Отто. В начале прошлого
60