
- •1 Физическая технология топлив
- •1.1 Подготовка нефти к переработке
- •1.1.1 Описание работы электрообессоливающей установки (элоу) (рисунок 1)
- •1.2 Первичная переработка нефти
- •1.2.1 Описание работы установки авт-1 (рисунок 2)
- •1.2.2 Описание работы установки элоу-ат-6 (рисунок 3)
- •1.2.3 Описание работы установки элоу-атв-6 (рисунок 4)
- •1.2.4 Описание работы установки элоу-авт-4 по переработке газового конденсата (рисунок 5)
- •3 Химическая технология топлив и углеродных материалов
- •3.1 Термические процессы
- •3.1.1 Описание работы установки термического крекинга нефтяных остатков (рисунок 6)
- •3.1.2 Описание работы установки замедленного коксования (рисунок 7)
- •3.1.3 Описание работы установки термоконтактного коксования (рисунок 8)
- •3.1.4 Описание работы установки термического пиролиза легкого углеводородного сырья (рисунок 9)
- •3.2 Каталитические процессы
- •3.2.1 Каталитический крекинг а) Описание работы установки г-43-102 каталитического крекинга вакуумного газойля (рисунок 10)
- •Б) Описание работы установки г- 43-107 по переработке вакуумного газойля (рисунок 11)
- •3.2.2 Описание работы установки каталитического риформинга (рисунок 12)
- •3.2.3 Описание работы установки гидроочистки нефтяных дистиллятов (л-24-7) (рисунок 13)
- •3.2.4 Описание работы установки гидрокрекинга вакуумного газойля (рисунок 14)
- •I вариант гидрокрекинга - бензиновый, II вариант – дизельный
- •3.3 Получение индивидуальных продуктов
- •3.3.1 Описание технологической схемы сернокислотного алкилирования изобутана олефинами (рисунок 15)
- •3.3.2 Полимеризация (олигомеризация) пропан-пропиленовой фракции (рисунок 16)
- •3.3.3 Каталитическая изомеризация легких парафинов нормального строения (рисунок 17)
- •3.3.4 Производство метилтретбутилового эфира (мтбэ) (рисунок 18)
- •3.4 Переработка твердых топлив
- •3.4.1 Полукоксование твердых топлив (рисунок 19)
- •3.4.2 Газификация каменного угля (рисунок 20)
- •3.5 Производство нефтяных масел
- •3.5.1 Процесс деасфальтизации гудрона в сжиженном пропане (рисунок 21)
- •3.5.2 Селективная очистка масляного сырья фенолом (рисунок 22)
- •3.5.3 Селективная очистка масел фурфуролом (рисунок 23)
- •3.5.4 Депарафинизация масляного сырья в кетон-ароматическом растворителе (рисунок 24)
- •3.5.5 Депарафинизация масляного сырья комплексообразованием с карбамидом (рисунок 25)
- •3.5.6 Адсорбционная очистка масел (контактная очистка) (рисунок 26)
- •Список используемых источников
- •Содержание
- •Редактор л.А. Маркешина
- •450062, Республика Башкортостан, г. Уфа, ул. Космонавтов, 1
3.1.4 Описание работы установки термического пиролиза легкого углеводородного сырья (рисунок 9)
Пиролиз – наиболее жесткая форма термического крекинга нефтяного и газового сырья, осуществляется обычно при температуре 700-900 оС с целью получения углеводородного газа с высоким содержанием непредельных. Время контакта сырья составляет 0,2-0,5 с.
Сырье (бензин, этан) предварительно нагревается в теплообменнике 1 и поступает в конвекционную камеру печи пиролиза 4. На выходе из камеры конвекции в сырье добавляется водяной пар разбавления. На выходе из печи температура продуктов составляет 830-850 0С, которые затем поступают в закалочно–испарительный аппарат (ЗИА) 3. В межтрубное пространство этого аппарата подается водяной конденсат, который затем идет в паровой барабан, где происходит отделение пара от конденсата, конденсат возвращается в ЗИА. Пар подогревается в печи 5 и используется в виде пара разбавления или в компрессорах.
Температура продукта на выходе из ЗИА 350-400 0С. После ЗИА продукты пиролиза направляют в колонну предварительного разделения продуктов 6. В ней пирогаз отделяют от пироконденсата. Перед входом в колонну в продукт впрыскивают тяжелую смолу пиролиза. Температура на входе в колонну составляет 180 0С. Тепло горячей смолы пиролиза, циркулирующей в кубе колонны 6, обычно используется для получения пара низкого давления. Температура верха колонны 6 порядка 100 0С. Пирогаз после охлаждения до 40 0С поступает в сепаратор 7. Жидкие продукты отправляются в отстойник 8, где происходит расслоение воды и углеводородов. Часть углеводородов возвращается в 6 в виде орошения, а балансовое количество идет на разделение в депентанизатор 22. Водный слой из 8 поступает в отстойник 9, откуда вода дренируется в промышленную канализацию, углеводородный слой возвращается в 7. Газы из сепаратора 7 проходят четырехступенчатое компримирование с последующим охлаждением и сепарацией потоков. Давление на выходе из последней ступени 1,4 МПа. Газы под таким давлением поступают на отмывку в скруббер 12, где происходит удаление кислых газов (сероводорода, углекислого газа) водой. После промывки пирогаз проходит следующую ступень компримирования до давления 4,0 МПа, затем направляется в адсорбер 13 на осушку (в качестве адсорбера используют цеолиты) и идет на газораспределение. В колонне 14 из пирогаза выделяют водород и метан. В холодильном блоке 15 водород отделяется от метана. С низа колонны 14 выводится фракция C2 и выше, которая поступает в этановую колонну 16, где выделяют этан-этиленовую фракцию (ЭЭФ). Кроме этана и этилена, смесь содержит ацетилен. На большинстве установок пиролиза ацетилен селективно гидрируют до этилена в ректоре 17 на палладиевом катализаторе. В колонне 18 продукты реактора 17 разделяют на этан и этилен. Этан возвращается на пиролиз. В колонне 19 выделяют пропан-пропиленовую фракцию (ППФ), которая также селективно гидрируется с целью удаления алкена (СН2=С=СН2) и метилацетилена (СН≡С−СН3). В колонне 20 происходит разделение пропана и пропилена.
Из остатка колонны 19 последовательно выделяют в колонне 21 фракцию C4, а в колонне 22 фракцию C5 и пироконденсат.
Примерный материальный баланс процесса пиролиза, %
Сырье – прямогонный бензин 100,0
Получено:
водород-метановая фракция 17,7
этилен 25,5
пропилен 16,2
пропан 1,0
бутан-бутилены 12,2
фракция нк – 150 оС 19,9
150 – 250 оС 1,5
остаток > 250 оС 3,3
потери 2,7
Рисунок 8 – Принципиальная схема установки термоконтактного коксования
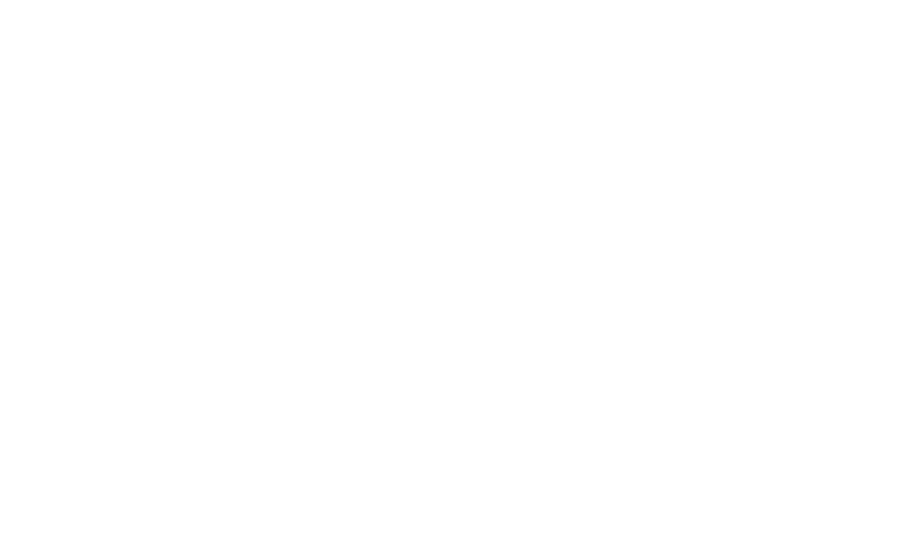
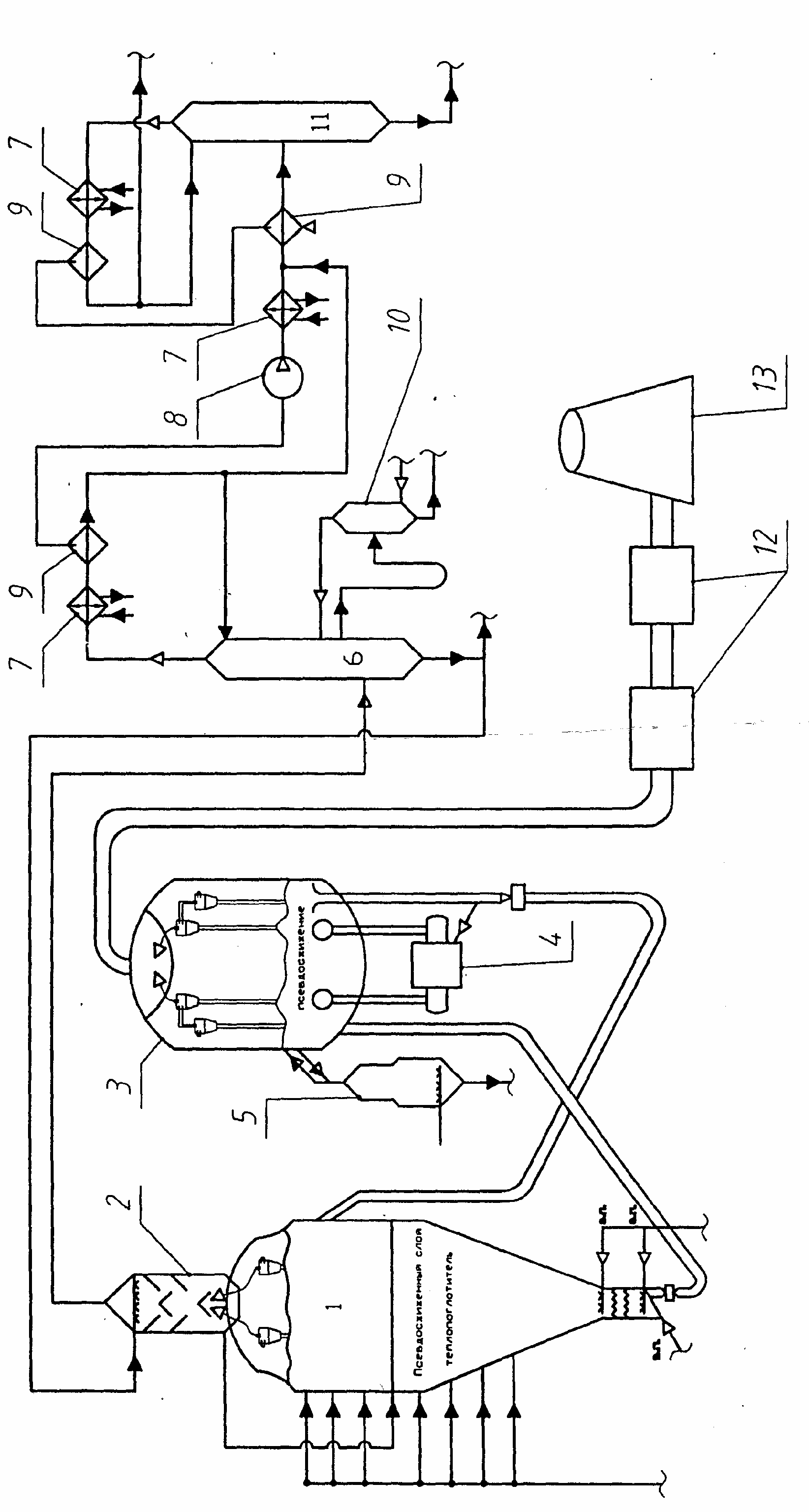
Рисунок 9 – Принципиальная технологическая схема пиролиза легкого углеводородного сырья
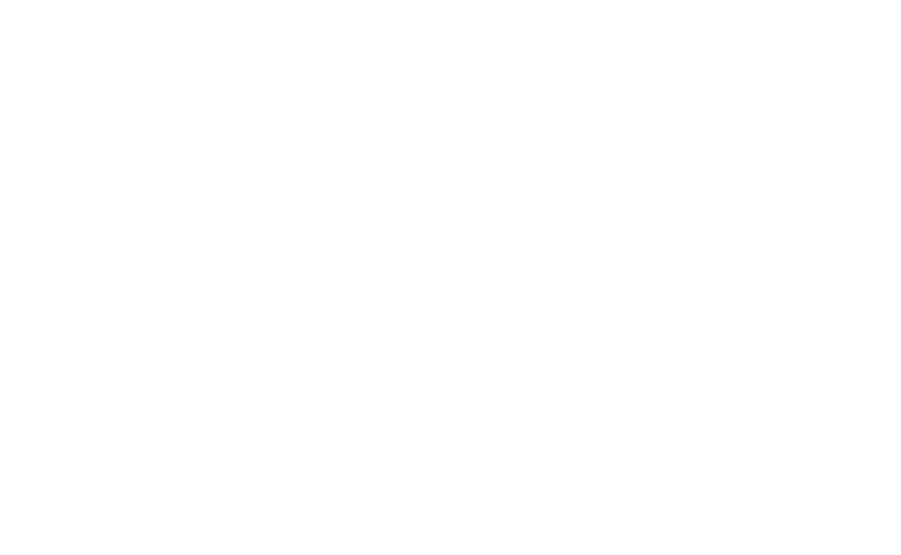
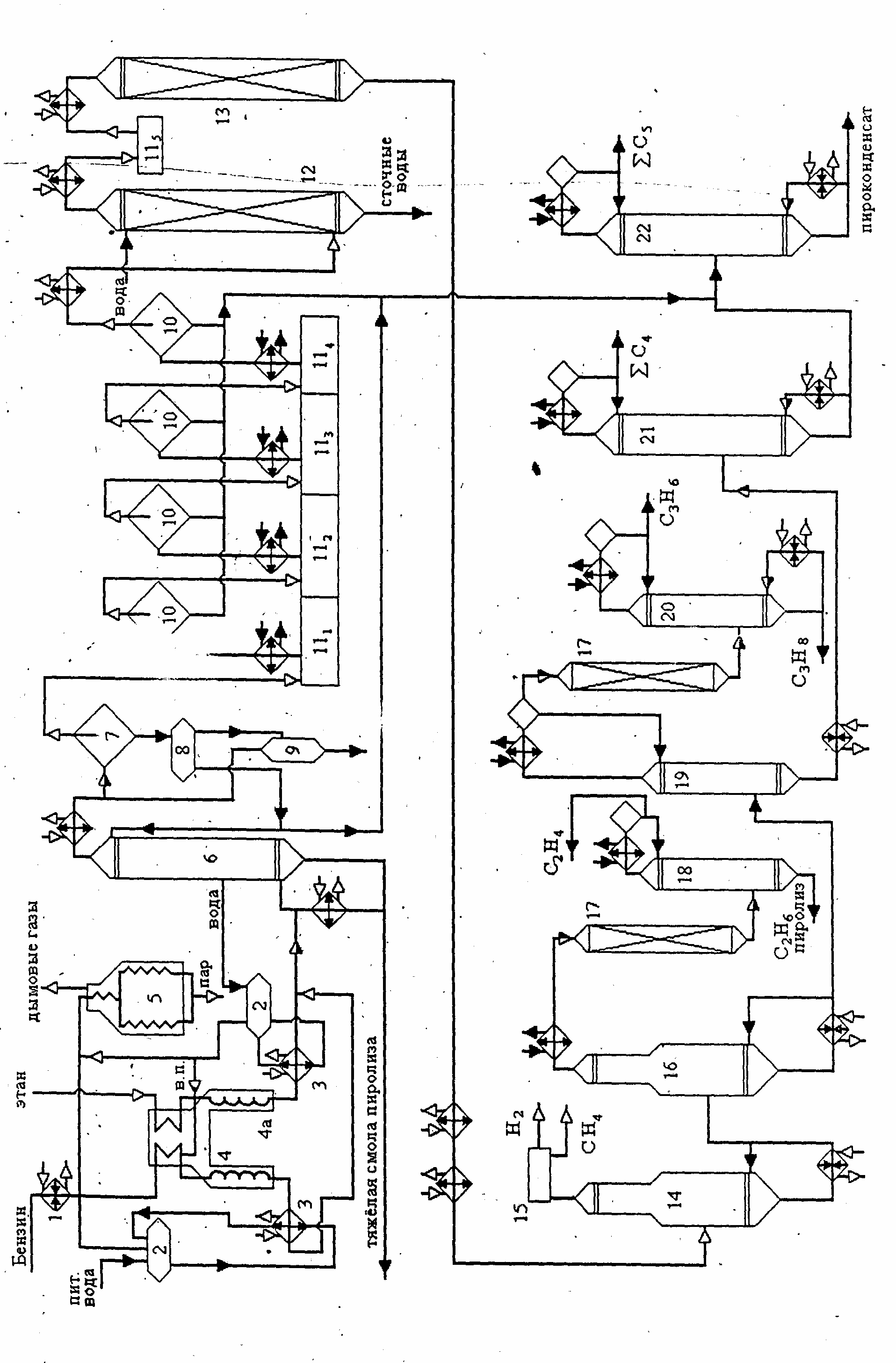