
- •1 Физическая технология топлив
- •1.1 Подготовка нефти к переработке
- •1.1.1 Описание работы электрообессоливающей установки (элоу) (рисунок 1)
- •1.2 Первичная переработка нефти
- •1.2.1 Описание работы установки авт-1 (рисунок 2)
- •1.2.2 Описание работы установки элоу-ат-6 (рисунок 3)
- •1.2.3 Описание работы установки элоу-атв-6 (рисунок 4)
- •1.2.4 Описание работы установки элоу-авт-4 по переработке газового конденсата (рисунок 5)
- •3 Химическая технология топлив и углеродных материалов
- •3.1 Термические процессы
- •3.1.1 Описание работы установки термического крекинга нефтяных остатков (рисунок 6)
- •3.1.2 Описание работы установки замедленного коксования (рисунок 7)
- •3.1.3 Описание работы установки термоконтактного коксования (рисунок 8)
- •3.1.4 Описание работы установки термического пиролиза легкого углеводородного сырья (рисунок 9)
- •3.2 Каталитические процессы
- •3.2.1 Каталитический крекинг а) Описание работы установки г-43-102 каталитического крекинга вакуумного газойля (рисунок 10)
- •Б) Описание работы установки г- 43-107 по переработке вакуумного газойля (рисунок 11)
- •3.2.2 Описание работы установки каталитического риформинга (рисунок 12)
- •3.2.3 Описание работы установки гидроочистки нефтяных дистиллятов (л-24-7) (рисунок 13)
- •3.2.4 Описание работы установки гидрокрекинга вакуумного газойля (рисунок 14)
- •I вариант гидрокрекинга - бензиновый, II вариант – дизельный
- •3.3 Получение индивидуальных продуктов
- •3.3.1 Описание технологической схемы сернокислотного алкилирования изобутана олефинами (рисунок 15)
- •3.3.2 Полимеризация (олигомеризация) пропан-пропиленовой фракции (рисунок 16)
- •3.3.3 Каталитическая изомеризация легких парафинов нормального строения (рисунок 17)
- •3.3.4 Производство метилтретбутилового эфира (мтбэ) (рисунок 18)
- •3.4 Переработка твердых топлив
- •3.4.1 Полукоксование твердых топлив (рисунок 19)
- •3.4.2 Газификация каменного угля (рисунок 20)
- •3.5 Производство нефтяных масел
- •3.5.1 Процесс деасфальтизации гудрона в сжиженном пропане (рисунок 21)
- •3.5.2 Селективная очистка масляного сырья фенолом (рисунок 22)
- •3.5.3 Селективная очистка масел фурфуролом (рисунок 23)
- •3.5.4 Депарафинизация масляного сырья в кетон-ароматическом растворителе (рисунок 24)
- •3.5.5 Депарафинизация масляного сырья комплексообразованием с карбамидом (рисунок 25)
- •3.5.6 Адсорбционная очистка масел (контактная очистка) (рисунок 26)
- •Список используемых источников
- •Содержание
- •Редактор л.А. Маркешина
- •450062, Республика Башкортостан, г. Уфа, ул. Космонавтов, 1
3.3.4 Производство метилтретбутилового эфира (мтбэ) (рисунок 18)
Процесс предназначен для получения октанповышающей кислородсодержащей добавки к товарным автомобильным бензинам.
Процесс осуществляется в реакторе 5 со стационарным слоем катализатора, совмещенным с двумя ректификационными колоннами 6 и 7. Как правило, используют два реактора, работающих поочередно.
Сырье бутан-бутиленовая фракция (ББФ) с температурой 60 ºС поступает в реактор 5, под каждый из трех слоев катализатора подается свежий и циркулирующий метанол с температурой 60 ºС.
С куба реактора 5, снабженного кипятильником, отводится целевой продукт МТБЭ. С верха реактора отводится отработанный ББФ, метанол и увлеченный МТБЭ. Продукты конденсируются в конденсаторе-холодильнике 11 и поступают в сепаратор 8, где отделяются газы. Сконденсированные продукты частично поступают в реактор в виде холодного орошения, а балансовое количество в емкость 3, из которой метанол и отработанный ББФ разделяются в экстракторе 6 водой при температуре 40 ºС и давлении 0,9 МПа.
Отработанная ББФ, отводимая сверху экстрактора 6, после охлаждения в конденсаторе-холодильнике 6 и разделении в сепараторе 9 отправляется в товарный парк.
Отгонка циркулирующего метанола от воды осуществляется в ректификационной колонне 7 (температура низа колонны 120 ºС, температура верха 70 ºС). Метанол выводится сверху колонны 7. Часть его используется как орошение колонны, а балансовая часть циркулирует. Вода снизу колонны 7 после охлаждения подается в экстрактор 6 для разделения ББФ и метанола.
Примерный материальный баланс процесса
Взято, % масс.
ББФ 95,00
в том числе
изо-бутилен 10,00
свежий метанол 5,00
Получено, % масс.
МТБЭ 14,00
Отработанная ББФ 85,00
в том числе
изо-бутилен 0,05
Потери 1,00
Рисунок 18 - Производство метилтретбутилового эфира
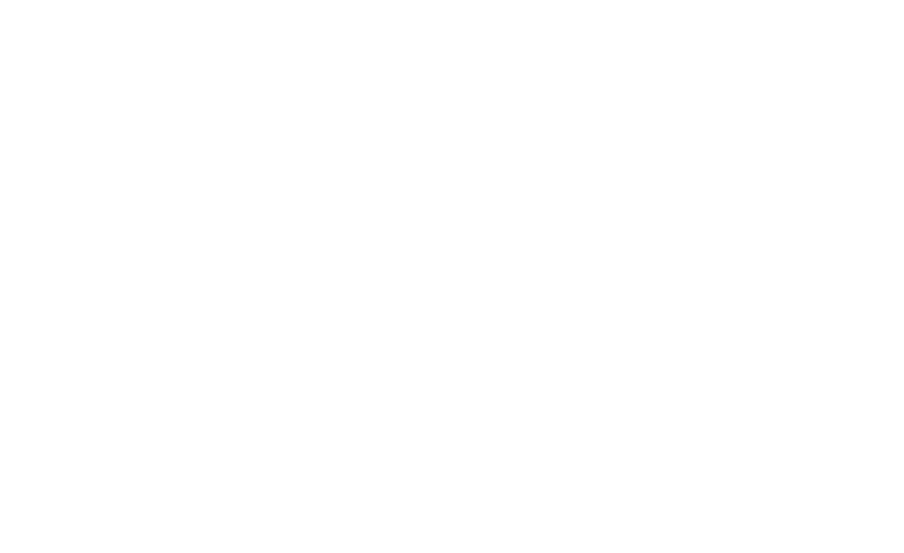
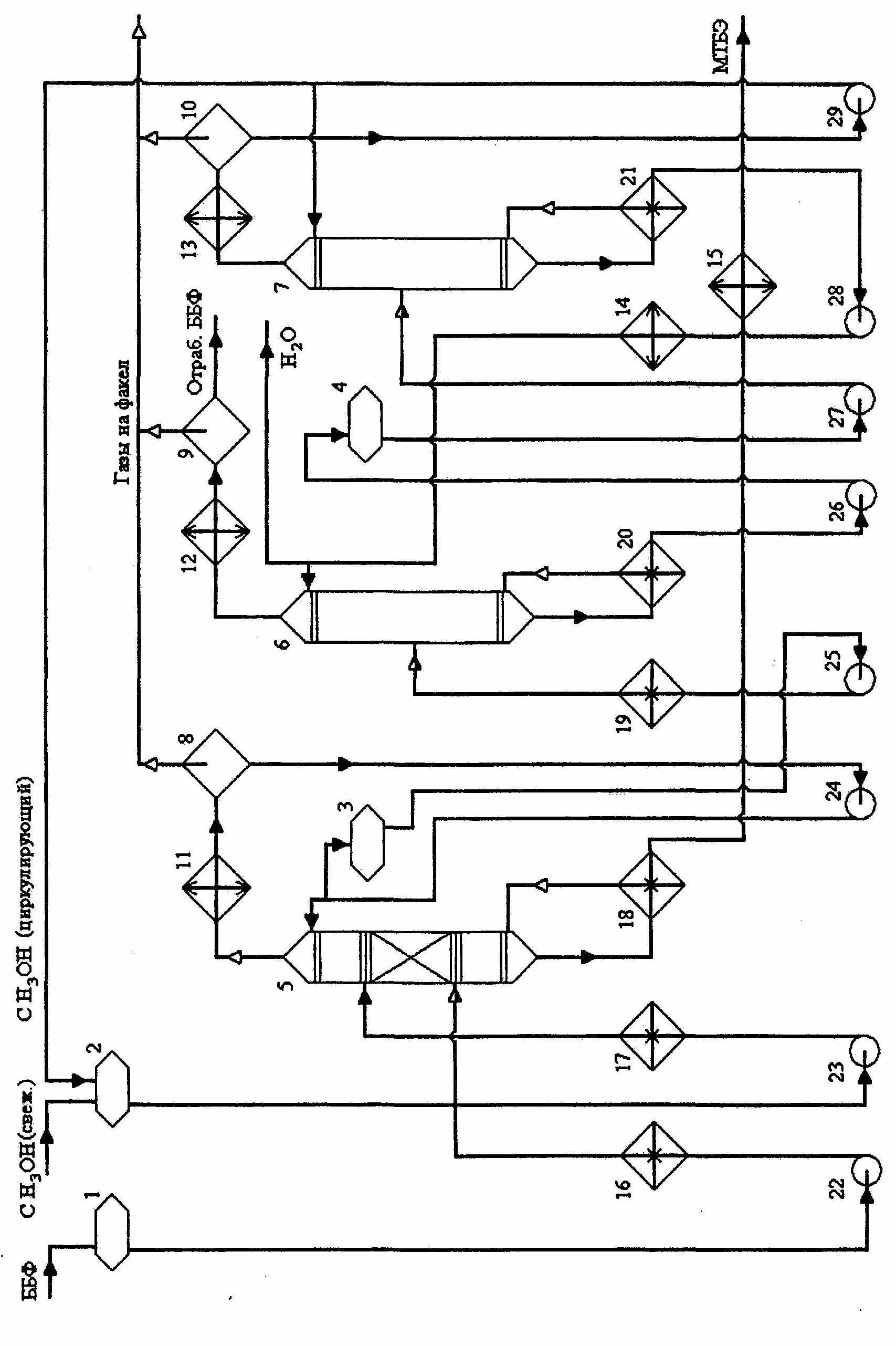
3.4 Переработка твердых топлив
3.4.1 Полукоксование твердых топлив (рисунок 19)
Полукоксование - процесс термической переработки твердых горючих ископаемых при высоких температурах без доступа воздуха. При этом происходит распад органической массы топлива, сопровождающийся выделением газообразных и жидких продуктов, вследствие чего получаемый твердый остаток по составу и свойствам существенно отличается от исходного топлива. Полукоксование проводится в интервале 500-550 °С. Конечными продуктами процесса являются газ, смола, пирогенетическая вода (т.е. вода, образующаяся в результате термического распада топлива) и твердый остаток-полукокс. Из жидких фракций (смолы) и газовых смесей путем разделения и очистки которых можно получить товарные продукты либо использовать их в качестве сырья для синтеза моторных топлив и органических продуктов.
Метод Cogas один из перспективных процессов, в котором сочетаются многоступенчатый пиролиз угля и последующая частичная газификация полукокса.
Уголь, предварительно высушенный, измельченный (размер частиц 3 мм) и нагретый до 350 °С, подвергают полукоксованию в псевдоожиженном слое последовательно в трех пиролизеpax 1, 2 и 3 при температурах 450, 540 и 870 °С соответственно. Продукты полукоксования отбирают только из двух первых аппаратов, а парогазовую смесь из третьего используют в качестве теплоносителя в первом и втором. В свою очередь, теплоносителем для третьего пиролизера служат продукты, получаемые при газификации полукокса в газогенераторе 4. В этом аппарате газифицируют не весь полукокс. Некоторую его часть направляют в печь 5, где он частично сжигается в воздухе, а нагретая при этом оставшаяся часть полукокса возвращается в газогенератор 4 как твердый теплоноситель.
Примерный материальный баланс процесса
Полукокс 54,4% (масс.)
Смола 23,6% (масс.)
Пирогенетическая вода 7% (масс.)
Газ 15% (масс.)
в том числе СО 21,1% (об.)
Н2 51% (об.)
СН4 20,9% (об.)
С2Н6 6,0% (об.)
1, 2, 3 – пиролизеры; 4 – газогенератор; 5 – печь
Рисунок 19 – Принципиальная схема процесса полукоксования твердых топлив
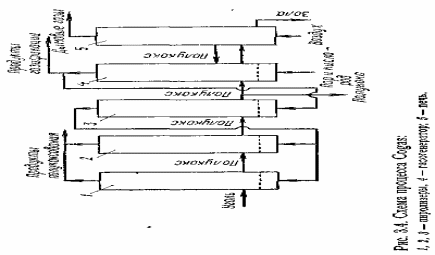