
ОТПиРТиТТМиО(Федотов)
.pdf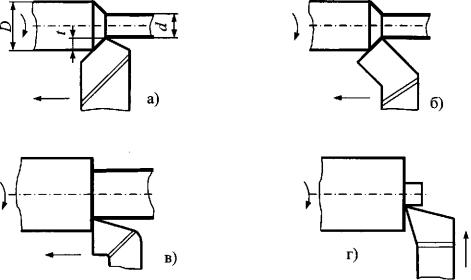
30
6. РАБОТА № 4. ИССЛЕДОВАНИЕ ВЛИЯНИЯ РЕЖИМА ТОЧЕНИЯ НАПЛАВЛЕННЫХ ДЕТАЛЕЙ НА КАЧЕСТВО
ОБРАБОТАННОЙ ПОВЕРХНОСТИ
6.1. Цель работы
Получение практических навыков оценки влияния режима точения на плавленных деталей на качество обработанной поверхности.
6.2. Обработка наплавленных поверхностей заготовок точением
Предварительную обработку наплавленных поверхностей восстанавли ваемых деталей типа «ступенчатый вал» осуществляют точением.
В условиях ремонтного производства обработку производят на универ сальных токарных станках, используя схемы обработки, приведенные на рис. 6.1.
Рис. 6.1. Схемы обработки при точении резцами: а - прямым проходным правым; б - отогнутым проходным; в - проходным упорным; г - подрезным правым
Токарные резцы имеют определенную форму и углы режущей части: пе редний угол у, задний угол а, угол заострения β, а также главный и вспомога тельный углы в плане φ и φ1 (рис. 6.2). Углы выбирают в зависимости от марки обрабатываемого материала, условий и режима обработки, жесткости техноло гической системы.
Для изготовления резцов наиболее широко используют быстрорежущие стали, твердые сплавы, композиционные материалы [6.1].
Быстрорежущие стали - это легированные инструментальные стали с вы соким содержанием вольфрама. Маркируются буквами и цифрами, например: Р12, Р9К9, Р6М5, Р6М5К5 и др. Цифра после буквы «Р» указывает на среднее содержание вольфрама в процентах. Остальные буквы и цифры означают то же, что и в марках легированных сталей.
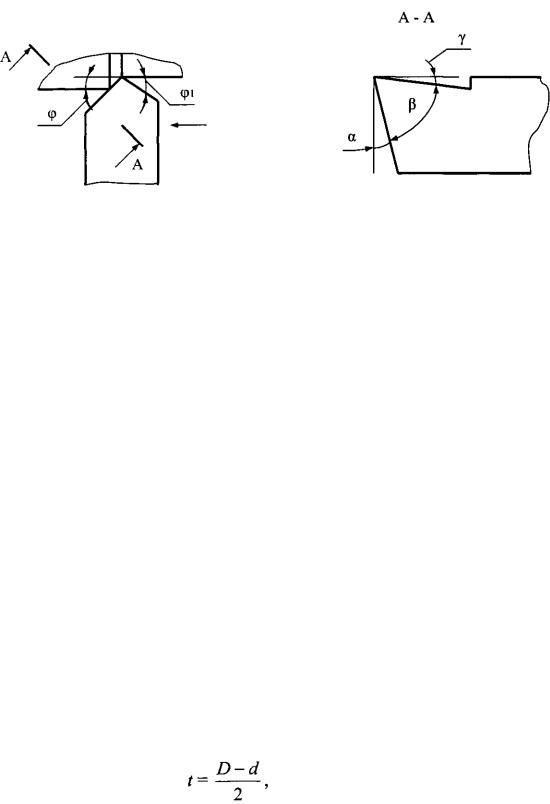
31
Рис. 6.2. Углы проходного резца
Твердые сплавы выпускаются чаще в виде сменных пластинок различных форм и размеров, получаемых методом порошковой металлургии (прессовани ем и спеканием). Основой для них служат порошки карбидов тугоплавких ме таллов (вольфрама, титана, тантала), сцементированных кобальтом. Выпуска ются три группы твердых сплавов: вольфрамовые - ВК (ВКЗ, ВК4, ВК6 и др.) - для обработки чугунных заготовок, титановольфрамовые - ТК (Т5К10, Т15К6 и др.) и титанотанталовольфрамовые - ТТК - для обработки стальных заготовок. В обозначениях марок твердых сплавов используют буквы: В - карбид вольф рама, К - кобальт, первая буква Т - карбид титана, вторая буква Т - карбид тан тала. Цифры после букв указывают на содержание компонентов в процентах; остальное в сплаве - карбид вольфрама.
Композиционные материалы (природные и синтетические алмазы) обла дают самой большой из известных в природе материалов твердостью, тепло стойкостью (до 850 °С) и низким коэффициентом трения. Однако алмазы обла дают повышенной хрупкостью и интенсивно изнашиваются при резании чер ных металлов. Последнее свойство объясняется диффузией углерода алмаза в железе при высокой температуре. Поэтому алмазные резцы при точении заго товок из черных металлов не применяют.
Кубический нитрид бора (КНБ) по твердости приближается к алмазу, но вдвое превосходит его цо теплостойкости и обладает химической инертностью к углероду и железосодержащим материалам. Поэтому КНБ используют при обработке заготовок, обладающих высокой твердостью.
Элементами режима резания при точении являются глубина резания t, подача S и скорость резания V [6.1].
где D и d - размеры обрабатываемой и обработанной поверхности соответст венно, мм.
Подача S (мм/об) - величина перемещения инструмента за один оборот заготовки.
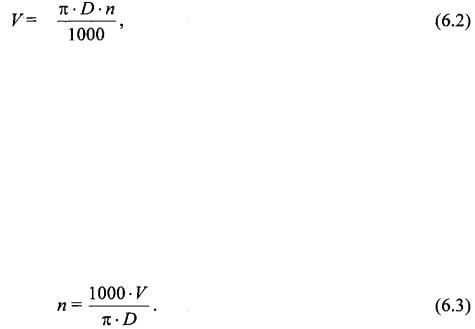
32
Скорость резания определяют по формуле
где п - частота вращения заготовки, об/мин.
Режимы резания назначают на основании исходных данных: чертежа де тали, размеров и материала заготовки, типа, материала и геометрии инструмен та, а также паспортных данных станка в следующем порядке:
1.Определяют глубину резания t, мм.
2.Назначают подачу S, мм/об и корректируют ее, исходя из данных стан ка, принимая ближайшую из имеющихся на станке.
3.Скорость резания V рассчитывают или назначают по нормативным таб лицам в зависимости от свойств обрабатываемого материала, принятых значе ний глубины резания и подачи.
4.Определяют частоту вращения заготовки по формуле
Затем подбирают ближайшее меньшее или большее (если оно не превы шает на 5 % расчетное) значение п по станку.
5.По принятой частоте вращения по формуле (6.2) рассчитывают дейст вительную скорость резания.
6.При предварительной обработке с большими значениями t и S выпол няют проверку режима по мощности, соблюдая условие:
Nрез Nшп, |
(6.4) |
где Nрез и Nmu - мощность, необходимая на резание и мощность на шпинделе станка соответственно, кВт.
Предварительную обработку наплавленных деталей рекомендуют выпол нять резцами с пластинами из твердого сплава с углами:
у = 8... 10°,а=10... 15°Д = 65...75°.
Применение в качестве материала инструмента поликристаллических сверхтвердых материалов позволяет существенно увеличить производитель ность обработки и улучшить качество обработанных деталей. При выборе ре жима обработки наплавленных наружных цилиндрических поверхностей дета лей можно ориентироваться на данные, приведенные в табл. 6.1.
В качестве критериев оценки технологической эффективности токарных операций используют: составляющие Рy и Рz силы резания, износ резца по зад ней и передней поверхностям, период стойкости резца, параметры качества, в том числе шероховатости обработанной поверхности.
К высотным параметрам шероховатости относятся: среднее арифметиче ское отклонение профиля Ra, мкм; высота неровностей профиля по десяти точ кам Rz, мкм; наибольшая высота неровностей Rmax. Шероховатость измеряют с помощью профилометров или профилографов.
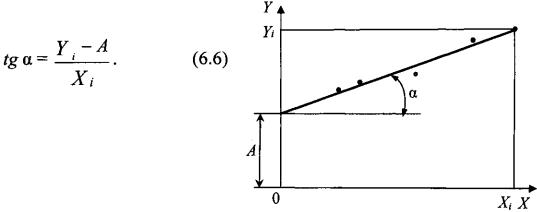
33
|
|
|
|
|
Таблица 6.1 |
|
|
Режимы обработки наплавленных деталей [6.2] |
|
|
|||
|
|
|
|
|
|
|
Твердость |
Материал режу |
|
Режимы резания |
|
|
|
наплавленного |
щей части |
Глубина |
|
Подача |
Скорость |
|
слоя, HRC |
инструмента |
t, мм |
|
S, мм/об |
V, м/мин |
|
|
Т15К6 |
2 ... 3 |
|
0,1 ... 0,4 |
90 ... 120 |
|
До 30 |
Т17К8 |
|
|
|
|
|
|
ВК60М |
2 ... 3 |
|
0,1 ... 0,2 |
130 ... 170 |
|
|
СТИМ-3Б |
|
|
|
|
|
30...45 |
СТИМ-3Б |
1,5 ... 2 |
|
0,2 |
100 |
|
Свыше 45 |
ПСТМ |
|
|
|
|
|
|
Киборит |
1,5 ... 2 |
|
0,2 ... 0,25 |
120 ... 130 |
|
|
|
|
|
|
|
|
Значительное влияние на шероховатость оказывает подача S и скорость резания V.
При исследовании влияния какого-либо входного параметрах (например, подачи S или скорости резания V) на критерий технологической эффективности операции Y (например, параметр шероховатости) на основе экспериментальных данных определяют Y = f (X), называемые эмпирическими формулами (зависи мостями).
Процесс подбора эмпирических формул включает графическую обработ ку результатов исследований, в ходе которых ориентировочно выбирают тип формулы, и вычисление параметров формул (коэффициентов).
Изменение параметров качества следует, в первую очередь, описывать
наиболее простыми функциями, к которым относится линейная |
|
Y=A+BX, |
(6.5) |
где АиВ- постоянные коэффициенты. |
|
Для определения коэффициентов А и В можно, в частности, использовать графический метод (рис. 6.3). Для этого на график наносят экспериментальные точки и строят прямую линию так, чтобы она проходила по возможности ближе ко всем точкам (см. рис. 6.3).
Параметр А определяют как ординату точки пересечения прямой с осью У, а тангенс угла наклона прямой к оси ОХ (см. рис. 6.3):
Для определения параметров А и
tg а можно применить также другой гра фический метод. В уравнение (4.5) под ставляют координаты двух крайних точек прямой линии графика. Получают систе му двух уравнений, из которых вычисля ют коэффициенты AnB = tga.
Рис. 6.3. Графическое изображение коэффициентов эмпирического урав нения
34
Пример. Подобрать эмпирическую формулу, если при исследовании про цесса получены следующие результаты (табл. 6.2).
Таблица 6.2 Значения входного и выходного параметра процесса
Значения |
Х1 |
Х2 |
Х3 |
X4 |
Х5 |
X6 |
Х7 |
|
входного |
||||||||
|
|
|
|
|
|
|
||
параметра |
0,1 |
0,2 |
0,3 |
0,4 |
0,5 |
0,6 |
0,7 |
|
х, |
||||||||
|
|
|
|
|
|
|
||
Значения |
Y1 |
Y2 |
Y3 |
Y4 |
Y5 |
Y6 |
Y7 |
|
выходного |
||||||||
|
|
|
|
|
|
|
||
параметра |
12,1 |
19,2 |
25,9 |
33,3 |
40,5 |
46,4 |
54,0 |
|
Y, |
||||||||
|
|
|
|
|
|
|
Графический анализ показывает, что в прямоугольных координатах точки расположены вблизи от прямой линии. Подставив крайние значения парамет ров (Х\9 Y\, Х7, Y7) в уравнение (6.5), получим систему из двух уравнений:
Аo + 0,7A1 = 54,0; Аo + 0,1A1 = 12,1,
откуда A1 = 41,9 / 0,6 = 69,8 и Аo= 12,1-0,1 -69,8 = 5,12.
Эмпирическая формула примет вид Y=5,12 + 69,8 X.
6.3.Содержание работы
Впроцессе выполнения лабораторной работы студент назначает условия
ирежим точения, проводит исследование влияния указанных преподавателем элементов режима резания на качество обработанной поверхности детали.
6.4.Средства технологического оснащения
-Токарный станок модели 1Е611.
-Заготовки - валики с наплавленной поверхностью.
-Профилограф-профилометр мод. 201.
6.5.Порядок выполнения работы
-Выбирают марку материала и углы режущей части резца.
-Определяют глубину резания t, ориентируясь на данные табл. 6.1.
-Назначают подачу S, ориентируясь на данные табл. 6.1, и корректируют ее по данным станка.
-Рассчитывают или назначают скорость резания V.
35
-Определяют частоту вращения заготовки п по формуле (6.3) и коррек тируют ее по данным станка.
-По формуле (6.1) рассчитывают действительную скорость резания V.
-При необходимости выполняют проверку режима по мощности.
-Изучают устройство токарного станка.
-Ориентируясь на согласованный с преподавателем входной параметр процесса резания, влияние которого на качество обработки предстоит изучить, устанавливают диапазон его варьирования и значения параметра X1, X2 ... Xn.
Среднее значение диапазона варьирования должно соответствовать на значенному по нормативам значению, максимальное и минимальное значения его не должны отличаться от среднего более, чем на 30 %.
-С помощью учебного мастера обрабатывают наплавленные поверхно сти, контролируя выходные параметры процесса, выбранные в качестве крите риев оценки технологической эффективности операции точения.
Результаты измерений заносят в табл. П 4.1.
-Для каждого выходного параметра подбирают коэффициент А и tg а линейной функции (6.5), используя графический метод или составляя систему двух уравнений.
Дают заключение относительно влияния входного параметра на выход
ные.
6.6. Содержание отчета
Отчет по лабораторной работе выполняют по форме приложения 4.1.
В выводах по работе необходимо проанализировать полученные резуль
таты.
6.7.Вопросы для самопроверки
1)Какими методами рекомендуют осуществлять предварительную обработ ку наплавленных поверхностей?
2)Какие материалы служат для изготовления режущей части инструмента используемого для обработки наплавленных поверхностей?
3)В зависимости от каких факторов выбирают углы токарных резцов?
4)В какой последовательности назначают элементы режима резания на плавленных поверхностей?
5)Какие параметры используют в качестве критериев оценки технологиче ской эффективности токарных операций?
6)На что указывают цифры после букв в обозначениях марок твердых спла
вов?
7)На что указывают цифры после букв в обозначениях марок быстрорежу щих сталей?
8)В зависимости от каких факторов выбирают скорость резания?
9)Какие факторы оказывают доминирующее влияние на шероховатость об работанных поверхностей?
36
10) Какие параметры служат для оценки шероховатости обработанных деталей?
БИБЛИОГРАФИЧЕСКИЙ СПИСОК
6.1.Грановский, Г.И. Резание металлов: Учебник для машиностр. и приборостр. спец. вузов / Г.И. Грановский, В.Г. Грановский. - М.: Высш. шк., 1985.
-С . 22-27, 154-160.
6.2.Восстановление автомобильных деталей: Технология и оборудование / В.Е. Канарчук, А.Д. Чигринец, О.Л. Голяк, П.М. Шоцкий - М.: Транспорт, 1995.-С. 266-269.
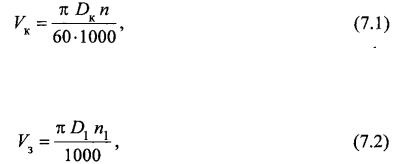
37
7. Работа № 5. ИССЛЕДОВАНИЕ ВЛИЯНИЯ РЕЖИМА ШЛИФОВАНИЯ
НАПЛАВЛЕННЫХ ДЕТАЛЕЙ НА КАЧЕСТВО ОБРАБОТАННОЙ ПОВЕРХНОСТИ
7.1. Цель работы
Получение практических навыков оценки влияния режима шлифования наплавленных деталей на качество обработанной поверхности.
7.1. Обработка заготовок наплавленных деталей шлифованием
Окончательную обработку наплавленных поверхностей восстанавливае мых деталей осуществляют шлифованием.
В условиях ремонтного производства обработку деталей типа «ступенча тый вал» производят на круглошлифовальных станках, используя два основных способа: многопроходное с продольной подачей и врезное шлифование.
Главным движением при всех способах шлифования является вращение шлифовального круга. Рабочую (окружную) скорость круга (скорость резания) определяют по формуле [7.1, 7.2]:
где D - диаметр шлифовального круга, мм; п - частота вращения круга, мин" .
Скорость вращения заготовки детали рассчитывают по зависимости [7.1,
7.2]:
где Dx - максимальный диаметр обрабатываемой поверхности (диаметр заго
товки при круглом наружном шлифовании), мм; n1 - частота вращения заготов ки, мин-1.
Многопроходному шлифованию с продольной подачей подвергают заго товки деталей, имеющие обрабатываемые поверхности сравнительно большой длины L (L > H, где Н - высота шлифовального круга). Обрабатываемая заго товка перемещается вдоль своей оси со скоростью продольной подачи Snp. В конце двойного или каждого хода шлифовальный круг перемещают в направ лении, перпендикулярном оси заготовки, на величину, равную поперечной по даче Sn. Перебеги, во избежание образования «завалов» по краям обработанной поверхности детали, должны быть равными 11 = l2 = 0,3H(рис. 7.1, а).
Один или несколько проходов выполняют без поперечной подачи (выха живающие проходы), что позволяет повысить точность и уменьшить высотные параметры шероховатости обработанной поверхности.
При обработке с врезной подачей шлифовальный круг перемещается в направлении, перпендикулярном оси заготовки, со скоростью врезной подачи Vs. В конце цикла шлифования подачу выключают и осуществляют выхажива-
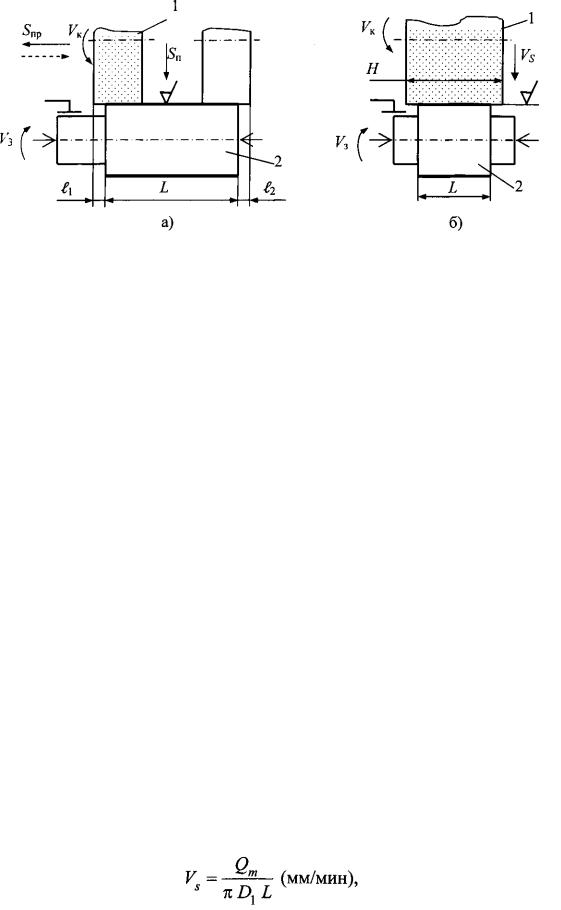
38
ние в течение определенного времени (рис. 7.1, б). Этот метод более произво дителен в сравнении со способом шлифования с продольной подачей. Точность
Рис. 7.1. Схемы способов круглого наружного шлифования: а, б - с продольной и врезной подачей соответственно; 1 - шлифовальный круг; 2 - заготовка
в значительной степени зависит от макрогеометрии рабочей поверхности шли фовального круга, поэтому круг необходимо править чаще, чем при обработке с продольной подачей. Этим способом осуществляют обработку поверхностей относительно небольшой длины (L < Н).
Перед назначением режима шлифования выбирают характеристику шли фовального круга, его форму и размеры. Материал абразивного зерна, твер дость и связка круга определяются маркой материала шлифуемой заготовки и его твердостью. Зернистость круга зависит, в первую очередь, от требуемых параметров микрогеометрии обработанной поверхности. Окончательную обра ботку наплавленных поверхностей заготовки рекомендуют осуществлять кру гом из электрокорунда белого, зернистостью 25 ... 40, твердостью СМ2 ... С1 на керамической связке [7.3].
Режим шлифования выбирают по нормативам [7.1 - 7.3]. При этом ориен тируются на материал заготовки и его твердость, группу обрабатываемости это го материала шлифованием, размеры шлифуемой поверхности детали, допуск выдерживаемого размера, параметры шероховатости обработанной поверхно сти, припуск на обработку, тип и модель станка.
Окончательное шлифование поверхностей заготовок, наплавленных элек тродной проволокой Св-08Г, Нп-65Г, Нп-30ХГСА, рекомендуют осуществлять, используя следующие режимы: рабочая скорость шлифовального круга VK = 35 м/с; скорость заготовки V3 = 20 ... 25 м/мин; режущая способность шлифоваль ного круга Qm = 1000... 1500мм3/мин [7.3].
Скорость врезной подачи, соответствующая оптимальной режущей спо собности шлифовального круга при круглом наружном шлифовании, опреде ляют по зависимости:
39
где D1 и L - диаметр заготовки и длина обрабатываемой поверхности, мм. Следует иметь в виду, что скорость врезной подачи при окончательном
шлифовании не должна превышать Vs = 0,15 мм/мин [7.3].
С целью снижения погрешности геометрической формы и высотных па раметров шероховатости обработанной поверхности в конце цикла шлифования рекомендуется осуществлять выхаживание в течение 0,10 ... 0,15 мин.
Для восстановления режущей способности шлифовального круга произ водят его правку. Правку круга при круглом наружном шлифовании осуществ ляют методом обтачивания, используя следующие режимы [7.1, 7.2]: при прав ке алмазом - 6 проходов со скоростью продольной подачи Vsп = 0,3 м/мин и по перечной подачей Sn = 0,02 мм/дв. ход, а также 4 выхаживающих прохода (без поперечной подачи); при правке алмазно-металлическим карандашом - 4 про хода при Vsn= 0,4 м/мин и Sn = 0,03 мм/дв. ход и 4 выхаживающих прохода.
В качестве критериев оценки технологической эффективности операций шлифования используют: 1) критерии, учитывающие производительность об работки; 2) критерии, учитывающие качество обработанных деталей; 3) крите рии, одновременно учитывающие производительность обработки и качество обработанных деталей.
К критериям первой группы относятся: режущая способность шлифо вального круга, коэффициент шлифования, составляющие силы шлифования, удельная мощность шлифования, скорость изнашивания шлифовального круга, период стойкости круга, контактная температура и др. В качестве критериев второй группы используют параметры шероховатости обработанной поверхно сти, отклонение формы, величину и знак остаточных напряжений в поверхно стном слое материала детали, дефекты поверхности в виде прижогов, трещин и др. Критерии третьей группы имеют сложную структуру и используются редко.
Шероховатость поверхности характеризуется высотными и шаговыми па раметрами. К высотным параметрам относятся: Ra - среднее арифметическое
отклонение профиля (мкм); Rz - высота неровностей профиля по десяти точ кам (мкм); Rmax - наибольшая высота неровностей (мкм). Шаговые парамет ры: Sm - средний шаг неровностей (мм); St - средний шаг по вершинам про филя (мм); tp - относительная опорная длина профиля. Показателями откло нения формы цилиндрических поверхностей являются овальность и огранка, которые являются характеристиками комплексного показателя - отклонения от круглости поперечного сечения поверхности.
Радиальную Ру и касательную Pz составляющие силы шлифования при круглом наружном шлифовании измеряют с помощью тензометрических дат чиков, наклеенных на центры для установки заготовки. Сигнал с датчиков уси ливается усилителем и регистрируется с помощью осциллографа или компью тера.
Размерный износ Ик шлифовального круга измеряют с помощью индика торной головки, закрепленной на стойке, установленной на столе шлифоваль ного станка (рис. 7.2).