
ОТПиРТиТТМиО(Федотов)
.pdf20
принимают равным Рг ; коэффициент восстановления рассчитывают: Кв=1- Кг. Результаты вычислений заносят в табл. П 2.6.
4.6. Содержание отчета
Отчет по работе выполняют по форме приложения 2.
В выводах по работе необходимо дать предложения по сокращению числа контролируемых параметров; оценить коэффициенты годности и восстановле ния детали.
4.7.Вопросы для самопроверки
1)С какой целью проводят дефектацию деталей ремонтного фонда?
2)Какие сведения должны содержать карты дефектации?
3)При каком значении коэффициента корреляции считают, что между кон тролируемыми параметрами существует тесная корреляционная связь?
4)Каким образом связаны коэффициенты годности и восстановления дета
лей?
5)От каких факторов зависит коэффициент корреляции контролируемых параметров?
6)Какой критерий может быть использован для оценки точности совпаде ния практической и теоретической кривых распределения размеров изношен ных деталей?
БИБЛИОГРАФИЧЕСКИЙ СПИСОК
4.1.Масино, М.А. Организация восстановления автомобильных деталей / М.А. Масино. - М.: Транспорт, 1981. - С. 35 - 48.
4.2.Белов, МА Лабораторные работы по технологии машиностроения. Ч. 1. Осно вы технологии машиностроения: Учебное пособие / М.А. Белов, А.Н. Унянин, Ю.В. Псигин, О.Г. Крупенников; под общ. ред. Л.В. Худобина. - Ульяновск: УлГТУ, 1997.-С. 14-23.
4.3.Солонин, И.С. Математическая статистика в технологии машино строения / И.С. Солонин. - М.: Машиностроение, 1972. - С. 72 - 78.
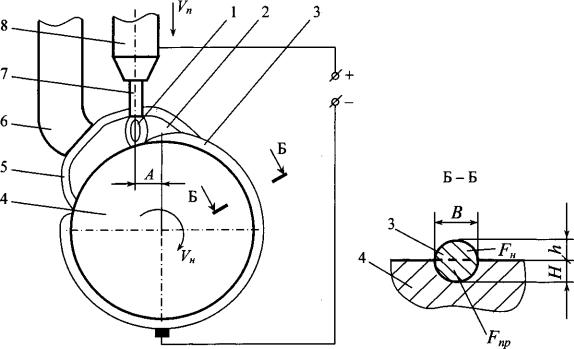
21
5. РАБОТА № 3. ВОССТАНОВЛЕНИЕ ИЗНОШЕННЫХ ДЕТАЛЕЙ АВТОМОБИЛЕЙ НАПЛАВКОЙ ПОД СЛОЕМ ФЛЮСА
5.1. Цель работы
Ознакомление с устройством и работой установки для наплавки под сло ем флюса, выбор условий и режима наплавки и исследование зависимостей вы ходных параметров процесса от условий его проведения.
5.2. Общие сведения
Сущность способа наплавки под слоем флюса заключается в том, что электрическая дуга горит под слоем расплавленного флюса в газовой полости, образующейся между электродной проволокой и восстанавливаемой поверхно стью детали, и изолирующей расплавленный металл от атмосферного воздуха [5.1]. Восстанавливаемая деталь цилиндрической формы в процессе наплавки вращается с определенной окружной скоростью Vu (рис. 5.1). Электродная про волока 7 автоматически подается в зону наплавки со скоростью Vn и поступа тельно перемещается вдоль оси детали 4. Под действием теплоты, выделяю щейся при горении электрической дуги 1, плавятся электродная проволока и металл детали, а также часть флюса, попавшего в зону горения дуги. Вокруг этой зоны образуется полость 2, заполненная парами металла, флюса и газами. Их давление поддерживает флюсовый свод 5, образующийся над слоем рас плавленного металла, и представляющий собой оболочку из расплавленного флюса.
Рис. 3.1. Схема процесса наплавки: 1 - электрическая дуга; 2 - газовая полость; 3 - наплавленный слой; 4 - восстанавливаемая деталь; 5 - оболочка из жидкого флюса; 6 - устройство для подачи флюса; 7 - наплавочная проволока (элек трод); 8 - мундштук
22
Оболочка из расплавленного флюса предохраняет металл наплавки и око лошовной зоны от кислорода и азота воздуха и препятствует разбрызгиванию жидкого металла. Благодаря малой теплопроводности расплавленного флюса замедляется процесс охлаждения наплавляемого металла. Это облегчает всплы тие на поверхность шлаковых включений и растворенных в металле газов, в ре зультате качество наплавленного слоя улучшается.
Электрод 7 рекомендуют смещать относительно оси восстанавливаемой детали на величину А, равную 5 ... 8 мм, в сторону, противоположную направ лению ее вращения, чтобы затруднить стекание расплавленного металла и флюса с поверхности детали. По мере продвижения дуги происходит остывание расплавленного металла, его кристаллизация и формирование шва в виде вали ка (см. рис. 5.1). Жидкий флюс превращается в шлаковую корку, которую затем отделяют от детали. Нерасплавленная часть флюса может быть использована повторно.
Достоинствами наплавки под флюсом являются высокая производитель ность процесса и качество наплавленного слоя, незначительные потери на угар и разбрызгивание и возможность получения наплавленного слоя большой (до 5 мм) толщины.
К недостаткам относятся: невозможность наплавки деталей диаметром менее 40 мм, поскольку расплавленные флюс и шлак не успевают затвердеть и стекают с поверхности детали; нагрев детали до высокой температуры; необхо димость применения дорогостоящих флюсов и специальной электродной про волоки, что значительно удорожает процесс; затраты времени на такие вспомо гательные работы, как приготовление флюса и отбивание шлаковой корки.
Наплавку под слоем флюса применяют для восстановления деталей, имеющих значительный износ, или деталей последнего ремонтного размера (наплавка шеек коленчатых и распределительных валов, полуосей и валов ко робок перемены передач).
Целесообразно наплавлять наружные поверхности деталей вращения диаметром свыше 45 мм.
5.3.Электроды и флюсы для наплавки
Вкачестве электрода используют сварочную и наплавочную проволоку, порошки и прутки для наплавки, порошковую проволоку и наплавочные ленты. Условные обозначения марок сварочной и наплавочной проволок состоят из индекса «Св» (сварочная) и «Нп» (наплавочная) и следующих за ним цифр и букв. Первые две цифры показывают среднее содержание углерода в сотых до лях процента. Последующие цифры и буквы указывают на содержание в прово локе главных элементов. Легирующие элементы в составе проволоки имеют те же обозначения, что и при маркировке стали, например: Н - никель, С - крем ний, Т - титан, Ф - ванадий, X - хром, Ц - цирконий, Ю - алюминий. Если цифра после буквы отсутствует, то это означает, что данный элемент содержит ся в небольших количествах (менее одного процента). Буква А в конце услов ных обозначений марок низкоуглеродистой и легированной проволок указыва-
23
ет на повышенную чистоту металла по содержанию серы и фосфора. Например, в сварочной проволоке Св-06Х19Н9Т содержится: углерода 0,06 %, хрома 19 %, никеля 9 % и небольшое количество титана.
Наплавочные проволоки изготавливают из углеродистой (Нп-30, Нп-40 и др.), легированной (Нп-30ХГСА, Нп-30Х5 и др.) и высоколегированной стали (Нп-4Х13, Нп-60ХЗВ10Ф и др.). Для восстановления деталей из среднеуглеродистых и малоуглеродистых сталей применяют малоуглеродистые (Св-08 и Св-15), марганцовистые (Св-08Г, Св-15Г, Св-10Г2) и кремниемарганцовистые (Св-12Г2С) проволоки и ленты. Детали из легированных сталей наплавляют специальными легированными проволоками (Нп-30ХГСА, Св-ЗХ13, Св-2Х13 и
ДР-)-
Флюсы, применяемые для автоматической наплавки, по способу приго товления делятся на плавленые и неплавленые (керамические). Плавленые флюсы получают путем сплавления компонентов шихты в электрических или плазменных печах с последующей грануляцией. В зависимости от преобла дающего содержания легирующих элементов эти флюсы делятся на высоко кремнистые (SiO2 > 30 %), низкокремнистые (SiO2 < 30 %), марганцовистые (MgO > 2 %). В ремонтном производстве наиболее широко используют марган цовистые и высококремнистые флюсы, позволяющие получить наплавленный слой твердостью 300 ... 400 НВ. Включение в плавленые флюсы графита и ферросплавов позволяет легировать наплавленный металл кремнием, марган цем, углеродом, хромом, никелем, титаном и т.д.
Неплавленые (керамические) флюсы представляют собой механическую смесь легирующих, раскисляющих и шлакообразующих компонентов, соеди ненных в общую массу жидким стеклом. Эти флюсы содержат до 50 % неокисленных элементов, что значительно расширяет возможность легирования на плавленного слоя. К недостаткам керамических флюсов относятся их сравни тельно высокая стоимость и значительные потери легирующих элементов, так как часть их остается в шлаковой корке.
5.4. Условия и режим наплавки
При назначении условий и режима наплавки исходят из размеров детали, формы восстанавливаемой поверхности, величины ее износа и качества на плавленного слоя.
Для получения требуемой твердости наплавленного слоя необходимо, в первую очередь, правильно подобрать марку электродной проволоки и флюса (приложение 3).
Вылет электрода, особенно при наплавке тонкой проволокой, влияет на глубину проплавления и форму шва. С увеличением вылета электрода умень шается глубина проплавления и возрастает доля наплавленного металла в шве.
Ориентировочно величину вылета можно определить как |
|
|
l = |
(10-12)d, |
(5.1) |
где d - диаметр проволоки, мм. |
|
|
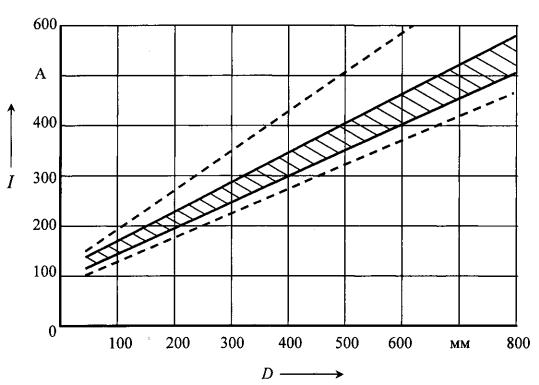
24
Величину смещения электрода (см. рис. 5.1) определяют по формуле
[5.2]: |
|
|
A = |
(0,05-0,07)D, |
(5.2) |
где D - диаметр восстанавливаемой поверхности детали, мм.
Электрод рекомендуют наклонять под углом 6 ... 8° в сторону, совпа дающую с направлением вращения детали, что позволяет получить валик пра вильной геометрической формы. При больших значениях угла появляются «непровары» по краям валика.
К элементам режима наплавки относятся: сила I сварочного тока, ско рость Vn подачи электродной проволоки и окружная скорость (частота враще ния) детали.
Силу тока назначают в зависимости от диаметра D детали (рис. 5.2) или толщины стенки в месте наплавки. С увеличением тока увеличивается объем жидкой ванны, возрастает глубина Н проплавления детали, но ширина валика В (см. рис. 5.1) изменяется незначительно. Это приводит к увеличению высоты h валика.
100 |
200 |
300 |
400 |
500 600 |
мм |
800 |
||
|
|
|
D |
|
|
—• |
|
|
|
|
|
|
|
|
|
||
Рис. 5.2. Зависимость силы сварочного |
тока I от диаметра детали D: |
пунктирные линии - граница зоны допустимых значений, заштрихованная зона - зона оптимальных значений
Увеличение тока приводит к повышению устойчивости горения дуги, по вышению вероятности деформации деталей и проплавления тонкостенных де талей, увеличению доли основного металла и, соответственно, уменьшению концентрации легирующих компонентов в наплавленном слое.
При выборе силы тока по рис. 5.2 следует ориентироваться на заштрихо ванную зону; пунктирным линиям соответствуют допустимые значения силы
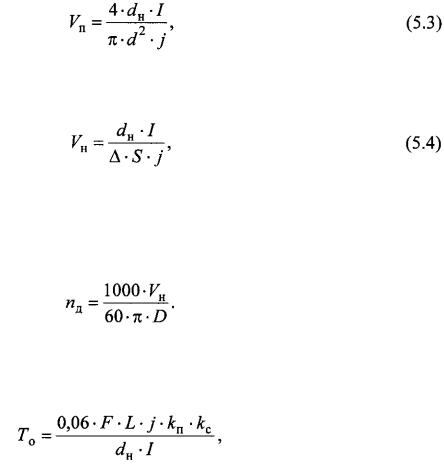
25
тока. По назначенной силе тока подбирают диаметр электродной проволоки (табл. 5.1).
Таблица 5.1
Зависимость между силой тока и диаметром электродной проволоки
Сила тока I, А |
90 ... 100 |
120... 300 |
160 ... 400 |
180 ...450 |
220 ... 500 |
|
|
|
|
|
|
Диаметр электрод |
|
|
|
|
|
ной проволоки d, |
1,2 |
1,6 |
2,0 |
2,5 |
3,0 |
мм |
|
|
|
|
|
|
|
|
|
|
|
Скорость подачи электродной проволоки при наплавке (м/ч) [5.2]:
где dH - коэффициент расплавления (наплавки), г/(А ч), dH = (14 ... 18) г/(А ч); j - плотность материала проволоки, г/см3.
Окружная скорость детали (м/ч):
где А - толщина наплавленного слоя, мм (в зависимости от величины износа принимается равной (1 ... 4) мм); S - величина продольной подачи наплавочной головки на оборот детали (шаг наплавки), мм (принимается равной (2 ... 6) диа метрам проволоки [5.2]).
Частота вращения наплавляемой детали (мин-1):
Рассчитанные и принятые параметры режима наплавки корректируют в соответствии с технологическими возможностями установки для наплавки.
По скорректированным параметрам вычисляют основное технологиче ское время наплавки (мин) [5.3]:
(5.6)
где F = πd2 /4 - площадь поперечного сечения шва (валика), мм2; L - длина
шва, мм; кп - коэффициент разбрызгивания металла (kп = 0,9); kс - коэффици ент, учитывающий сложность работы (кс =1 при автоматической сварке (на плавке) и ручной сварке (наплавке) плоскостей сверху; кс = 1,5 при ручной на плавке цилиндрических деталей диаметром 40 ... 50 мм и сварке на горизон тальной плоскости снизу; кс = 1,3 при ручной наплавке цилиндрических дета лей диаметром более 50 мм и сварке на вертикальной плоскости).
Длину L наплавленного шва определяют по формуле:
L = π D n, |
(5.7) |
где п - количество швов на наплавляемой поверхности:
|
|
|
26 |
|
|
|
|
|
|
|
|
n = b/S, |
|
|
(5.8) |
||
где b - длина наплавляемой поверхности, мм. |
|
|
|
|
||||
Назначение режима наплавки производят согласно табл. 5.2. |
|
|
||||||
|
|
|
|
|
|
|
Таблица 5.2 |
|
|
Режим наплавки цилиндрических деталей [5.2] |
|
|
|||||
|
|
|
|
|
|
|
|
|
Диаметр |
Сила тока I, А, при |
На |
|
Окружная |
Скорость |
|
Продоль |
|
диаметре электрод |
|
скорость |
подачи |
|
ная пода |
|||
детали D, |
пряже |
|
|
|||||
ной проволоки d, мм |
|
детали VH, |
электрода |
|
ча S, |
|||
мм |
ние, В |
|
|
|||||
1,2-1,6 |
2,0-2,5 |
|
м/ч |
Vn, м/ч |
|
мм/об |
||
|
|
|
|
|||||
50 ... 60 |
120-140 |
140-160 |
26-28 |
|
16-24 |
77 |
|
3 |
65 ... 75 |
150-170 |
180-220 |
26-28 |
|
16-28 |
87 |
|
3,5-4,0 |
80 ... 100 |
180-220 |
230-280 |
28-30 |
|
16-30 |
104 |
|
4 |
150 ... 200 |
230-250 |
300-350 |
30-32 |
|
16-32 |
140 |
|
5 |
250 ... 300 |
270 - 300 |
350-380 |
30-32 |
|
16-35 |
200 |
|
6 |
|
|
|
|
|
|
|
|
|
5.5. Качество наплавленного слоя
Наиболее распространенным дефектом наплавки, существенно снижаю щим эксплуатационные характеристики поверхностного слоя, являются трещи ны, возникающие как в наплавленном слое, так и в основном материале. Веро ятность возникновения трещин определяется химическим составом и физикомеханическими свойствами основного и наплавочного материалов, режимом наплавки и условиями охлаждения.
В наплавленном слое могут также появляться поры, вызванные загрязне нием наплавочных материалов, их влажностью, применением чрезмерно боль ших токов и длины дуги. Подрезы, шлаковые включения, наличие «несплавле ний» вызываются в основном неправильно назначенным режимом или его не соблюдением.
5.6. Содержание работы
Студент выполняет работу согласно выданному преподавателем варианту задания. Студент назначает и рассчитывает условия и режим наплавки, а затем экспериментально исследует, как влияет на толщину h наплавленного слоя и его качество один из элементов режима наплавки (/, VH, Vn или S).
5.7.Средства технологического оснащения
-Заготовки-валики, материал - сталь 45, 180 ... 190 НВ.
-Проволока сварочная Св. 15 ГСТЮЦА Ø 1,6 мм ГОСТ 2246-70.
-Флюс АП-20П ГОСТ 9087-81.
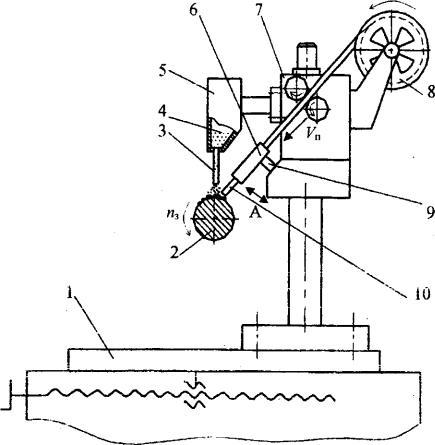
27
-Штангенциркуль ШЦ-1 ГОСТ 166-89, 0-125 мм.
-Головка наплавочная вибродуговая ОКС-6569М.
-Секундомер.
Головка смонтирована на суппорте 1 токарно-винторезного станка 1К62 (рис. 5.3). Перед наплавкой заготовку 2 закрепляют в патроне станка. Для уста новки заготовки относительно большой длины дополнительно используют центр, закрепленный в задней бабке станка.
Для придания мундштуку 6 и проволоке 10 колебательного движения от носительно заготовки служит вибратор 9.
Ид
Рис. 5.3. Схема установки для наплавки под флюсом: 1 - суппорт токарного станка 1К62; 2 - заготовка; 3 - флюсопровод; 4 - флюс; 5 - бункер; 6 - мундштук; 7 - привод переме щения проволоки; 8 - катушка; 9 - вибратор; 10 - проволока
5.8.Порядок выполнения работы
-Изучают конструкцию и порядок работы на установке для наплавки.
-Определяют условия и режим наплавки: силу тока, скорость подачи электродной проволоки; окружную скорость и частоту вращения детали; вели чины вылета и смещения электрода, используя данные табл. 5.1 - 5.3 и зависи мости (5.3)-(5.5).
28
Таблица 5.3
Твердость наплавленного слоя в зависимости от материала проволоки и марки флюса [5.1]
Материал детали |
Марка электродной |
Марка флюса |
Твердость наплав |
||
проволоки |
ленного слоя |
||||
|
|
||||
Сталь 40 |
Нп-ЗОХГСА |
АН-348А |
280 |
...300НВ |
|
Сталь 40 |
Нп-65, Нп-80 |
АН-348А |
280 |
...300НВ |
|
Сталь 40 |
Св-08 |
АН-348А |
170 |
...220НВ |
|
Сталь 40 |
Св-08 |
Полуметаллический |
400 |
...500НВ |
|
Сталь 40Х |
Нп-ЗОХГСА |
АН-348А |
280 |
...300НВ |
|
Сталь 40 |
Св-08 |
АНК-18 |
40 ...43 HRC |
||
|
|
|
|
|
-По формуле (5.6) рассчитывают основное технологическое время на
плавки.
-Подготавливают установку для наплавки к работе.
-Подготавливают деталь к наплавке (поверхность детали очищают от за грязнений, смазки и ржавчины).
-Устанавливают назначенные силу сварочного тока, скорость подачи электродной проволоки, частоту вращения детали, величины вылета и смеще ния электрода.
-Устанавливают деталь в патрон станка и (при необходимости) на зад
ний центр, замеряют ее диаметр и производят наплавку, проводя не менее трех параллельных опытов и контролируя основное технологическое время Г0Э.
-Устанавливают значение одного из элементов режима (по согласованию
спреподавателем) на 10 ... 20 % ниже, а затем на 10 ... 20 % выше назначенно
го и производят наплавку, проводя не менее трех параллельных опытов и кон тролируя основное технологическое время Го3.
-Измеряют диаметр наплавленной детали и вычисляют толщину наплав ленного слоя hэ как полуразность диаметров после и до наплавки, усреднив
значения параллельных опытов.
-Оценивают качество наплавленного слоя, визуально (или с использова нием магнитного дефектоскопа) контролируя на наплавленной поверхности на личие трещин, пор, подрезов, шлаковых включений и т.д.
-Заносят полученные результаты в таблицу, выполненную по форме табл. П 3.1.
-Определяют расхождение между расчетным Т0 и экспериментальным T0э значениями основного технологического времени наплавки и оценивают причины его возникновения.
-Систематизируют полученные результаты и строят необходимые гра
фики.
-Вывод по работе заносят в отчет (приложение 3).
29
5.9. Содержание отчета
Вторую (после титульной) и последующие страницы отчета выполняют в соответствие с приложением 3.
В выводах по работе сравнивают расчетные и экспериментальные значе ния основного технологического времени наплавки, оценивают расхождение и анализируют его причины, а также обсуждают полученные зависимости тол щины наплавленного слоя и параметров его качества от элементов режима на плавки.
5.10.Вопросы для самопроверки
1)С какой целью в зону наплавки подается флюс?
2)Какую толщину наплавленного слоя можно получить при наплавке под слоем флюса?
3) Почему невозможно произвести наплавку деталей диаметром менее
40мм?
4)С какой целью и на какую величину рекомендуют смещать электрод от носительно оси восстанавливаемой детали?
5)Какие факторы определяют скорость подачи электродной проволоки при наплавке?
6)Какие факторы определяют окружную скорость детали при наплавке?
7)В зависимости от каких факторов назначают силу тока при наплавке?
БИБЛИОГРАФИЧЕСКИЙ СПИСОК
5.1.Сварка в машиностроении: Справочник. В 4 т. / Редкол. Г.А. Никола ев и др. - М.: Машиностроение, 1978. Т. 2 / Под ред. А.И. Акулова, 1978. - С. 9
-32.
5.2.Восстановление автомобильных деталей: Технология и оборудование
/В.Е. Канарчук, А.Д. Чигринец, О.Л. Голяк, П.М. Шоцкий. - М.: Транспорт, 1995.-С. 140-148.
5.3.Дюмин, И.Е. Ремонт автомобилей / И.Е. Дюмин, Г.Г. Трегуб // Под ред. И.Е. Дюмина. - М.: Транспорт, 1998. - С. 101 - 110.