
ОТПиРТиТТМиО(Федотов)
.pdf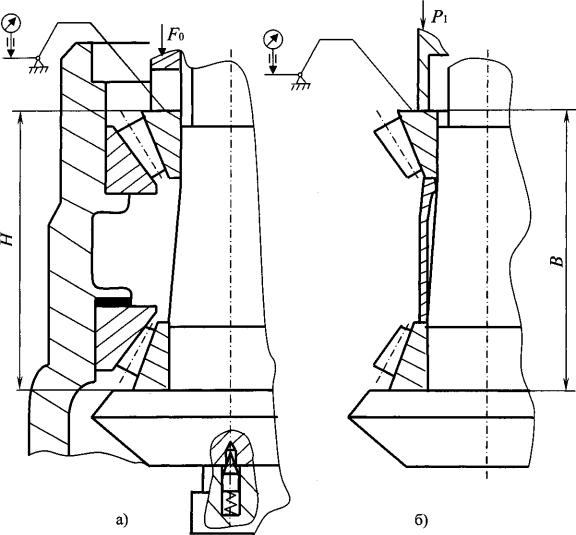
10
Рис. 3.3. Схема измерения размеров Н (а) и В (б) деталей, образующих наружный и внутренний контуры
Ориентируясь на полученное значение А7, подбирают размер неподвиж ного ступенчатого компенсатора.
В ряде конструкций автомобилей используется бесступенчатое регулиро вание натяга с помощью деформируемого распорного элемента (втулки), уста навливаемого во внутреннем контуре. Деформируясь, этот элемент компенси рует погрешности звеньев размерной цепи.
При сжатии этого элемента с определенной осевой силой элемент теряет устойчивость (в точке С); на участке СЕ размеры элемента могут значительно измениться при небольшом увеличении осевой силы Р\\ точка Е соответствует пределу прочности элемента (рис. 3.4).
Следовательно, деформируемый распорный элемент выполняет свое слу жебное назначение при деформации на участке СЕ, а максимальная возможная компенсация равна ΔlЕ - Δlс.
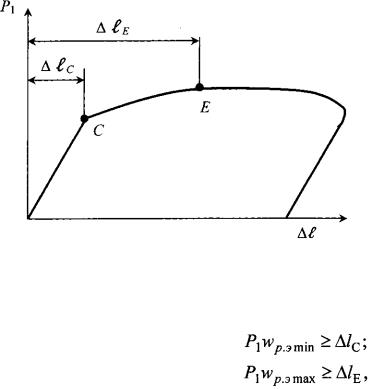
11
Рис. 3.4. Зависимость деформа ции сжатия А£ деформируемого распорного элемента от при кладываемой к нему силы Pi
Таким образом, создание необходимого предварительного натяга в под шипниковом узле ведущей шестерни с деформируемым распорным элементом достигается при выполнении условий:
где wp.э min, Wp.Эmax — минимальная и максимальная податливость распорного
элемента.
В процессе изготовления (сборки) бесступенчатое регулирование осуще ствляется следующим образом. На измерительной позиции измеряется действи тельный момент трения Мтр.д в предварительно собранном наружном контуре (см. рис. 3.3, а), нагруженном силой F0, с передачей информации о Мтр.д на сбо рочную позицию. На сборочной позиции устанавливается деформируемый рас порный элемент, сальник и осуществляется затяжка гайки. При достижении в контуре момента, равного Мтр.д + ттр., где ттр. - момент сил трения в сальнике, привод затяжки гайки отключается.
При регулировании натяга в подшипниковом узле автомобиля в процессе ремонта с использованием неподвижного ступенчатого компенсатора собирают узел, изменяя размер компенсатора, и контролируя момент сопротивления про ворачиванию (момент трения) и осевой люфт. При правильной регулировке осевой люфт должен отсутствовать, а момент сопротивления проворачиванию должен находиться в пределах, регламентируемых техническими требования ми.
При бесступенчатом регулировании натяга затягивают гайку фланца, пе риодически контролируя момент сопротивления подшипников проворачиванию ведущей шестерни. Если момент сопротивления окажется ниже нормы, то под тягивают гайку. При превышении нормированного значения заменяют распор ную втулку, поскольку она получила недопустимо большую деформацию. За тем повторяют сборку с соответствующими регулировками.
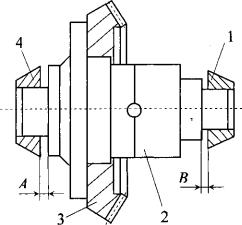
12
3.3.Содержание работы
Впроцессе выполнения работы студент изучает сборочный чертеж кони ческого редуктора моста автомобиля, формулирует служебное назначение ко нического редуктора, анализирует технические требования, предъявляемые к редуктору, разрабатывает методы их контроля, выявляет и составляет размер ные цепи, с помощью которых решается задача обеспечения натяга подшипни ковых узлов дифференциала и ведущей шестерни, составляет схему сборки, выполняет разборку и сборку редуктора, производя при этом регулировку под шипников дифференциала и ведущей шестерни, оформляет маршрутную карту сборки.
3.4.Средства технологического оснащения
-Оправки для выпрессовки и запрессовки подшипников.
-Молоток 0,5 кг, ГОСТ 2310-77.
-Ключ динамометрический.
-Динамометр пружинный, ГОСТ 13837-79.
-Стойка с индикатором часового типа, цена деления 0,001 мм.
-Тиски с винтовым зажимом.
3.5.Последовательность действий при регулировке подшипников дифференциала редуктора моста автомобиля УАЗ в процессе ремонта
-Напрессовывают внутренние кольца подшипников на шейки собранно го дифференциала таким образом, чтобы между торцами коробки дифферен циала и торцами колец остались зазоры 3,5 ... 4,0 мм (рис. 3.5).
-Устанавливают дифференциал в картер, затем прокладку и крышку кар тера и, проворачивая крышку, прикатывают подшипники. Затем болтами и гай
ками соединяют крышку с картером.
-Отворачивают болты, снимают крыш ку, вынимают из картера дифференциал и щупом замеряют зазоры А и В между торцами колец подшипников и коробкой дифферен циала (см. рис. 3.5).
-Подбирают пакет прокладок толщи ной, рассчитанной по формуле (в мм)
S = A+ В + 0,01.
-Разделяют подобранный пакет про кладок примерно пополам. Снимают внутрен ние кольца подшипников дифференциала. Ус-
Рис. 3.5. Схема к регулировке танавливают пакеты прокладок на шейки ко- подшипников дифференциала: 1, робки дифференциала и напрессовывают 4 - внутреннее кольцо подшип- внутренние кольца подшипников до упора,
ника; 2 - дифференциал; 3 - ве домая шестерня
13
3.6. Последовательность действий при регулировке подшипников ведущей шестерни моста автомобиля УАЗ в процессе ремонта
-Напрессовывают на ведущую шестерню 1 (см. рис. 3.1) подшипники. Распорную втулку и регулировочные прокладки располагают между внутрен ними кольцами подшипников.
-Устанавливают регулировочное кольцо 2 (см. рис. 3.1) ведущей шес
терни 1.
-Запрессовывают ведущую шестерню в сборе с подшипниками в картер до упора. Устанавливают на шестерню маслоотгонное кольцо и фланец и затя гивают гайку с моментом 160 ... 200 Нм. При правильно отрегулированном уз ле осевой люфт должен отсутствовать, а пружинный динамометр должен пока зывать усилие 15 ... 30 Н при проворачивании с его помощью шестерни за от верстие во фланце. Для уменьшения натяга добавляют прокладки, для увеличе ния - убирают. Используемые размеры прокладок и соответствующие им уси лия при проворачивании заносят в протокол.
-После окончания регулировки снимают фланец, устанавливают крышку переднего подшипника ведущей шестерни и закрепляют ее болтами. Устанав ливают фланец, затягивают и шплинтуют гайку.
3.7.Порядок выполнения работы
-Изучают сборочный чертеж моста автомобиля УАЗ и формулируют служебное назначение конического редуктора.
-Анализируют технические требования, предъявляемые к редуктору. В случае необходимости вносят дополнения и исправления.
-Разрабатывают методы контроля технических требований и приводят соответствующие схемы контроля с описаниями.
-Составляют размерные цепи, с помощью которых решаются задачи обеспечения натяга подшипниковых узлов дифференциала и ведущей шестер ни.
-Составляют схемы разборки и сборки редуктора.
-Разбирают редуктор.
-Выполняют регулировку подшипников дифференциала.
-Выполняют регулировку и сборку подшипников ведущей шестерни.
-Выполняют окончательную сборку редуктора.
3.8.Содержание отчета
Отчет по работе должен содержать титульный лист, формулировку слу жебного назначения изделия, технические требования и схемы контроля, схемы размерных цепей, регламентирующих натяг подшипниковых узлов ведущей шестерни и дифференциала, схемы разборки и сборки редуктора, протокол с
14
размерами прокладок и соответствующими усилиями, маршрутную карту сбор ки.
3.9.Вопросы для самопроверки
1)С какой целью создается натяг в подшипниковых узлах конических ре дукторов мостов?
2)Какие виды компенсаторов используют в процессе регулирования под шипниковых узлов конических редукторов мостов?
3)Какова последовательность действий при регулировании подшипниковых узлов с использованием неподвижного ступенчатого компенсатора?
4)Какова последовательность действий при бесступенчатом регулировании подшипниковых узлов?
5)Каким образом контролируют натяг в подшипниковом узле автомобиля в процессе ремонта?
6)Каким образом размер неподвижного ступенчатого компенсатора влияет на натяг подшипников ведущей шестерни?
7)Какое усилие должен показывать пружинный динамометр при правильно отрегулированном в процессе ремонта натяге в подшипниковом узле ведущей шестерни автомобиля УАЗ?
БИБЛИОГРАФИЧЕСКИЙ СПИСОК
3.1.ГОСТ 23887-79. Сборка. Термины и определения. - М.: Изд-во стан дартов, 1982.-С. 2- 16.
3.2.Худобин, Л.В. Разработка технологических процессов сборки в кур совых и дипломных проектах: учебное пособие /Л.В. Худобин, В.Ф. Гурьянихин, В.Р. Берзин. - Ульяновск: УлГТУ, 1995. - С. 6 - 36.
3.3.Механизация и автоматизация сборки в машиностроении / А.В. Во ронин, И.А. Гречухин, А.С. Калашников и др. - М.: Машиностроение, 1985. -
С.143156.
3.4.Технология автомобилестроения: учебник для вузов / А.Л. Карунин, Е.Н. Бузник, О.А. Дащенко и др./ Под. ред. А.И. Дащенко. - М.: Академический проект: Трикста, 2005. - С. 547 - 575.
15
4. РАБОТА № 2. СТАТИСТИЧЕСКАЯ ОЦЕНКА СОСТОЯНИЯ ДЕТАЛЕЙ РЕМОНТНОГО ФОНДА
4.1. Цель работы
Получение практических навыков минимизации числа контролируемых параметров и определения коэффициентов структурного состава деталей ре монтного фонда с применением статистических методов.
4.2. Общие сведения
Под дефектом детали понимают всякое отклонение ее параметров от зна чений, установленных в нормативно-технической документации.
Дефектацию проводят с целью определения технического состояния де талей и сортировки в соответствии с техническими требованиями на три груп пы: годные, подлежащие восстановлению и негодные. Технические требования на дефектацию содержатся в руководствах по капитальному ремонту автомо билей и их сборочных единиц. Они составляются в виде карт, содержащих сле дующие сведения о детали: ее наименование и номер, материал, твердость по верхностей, перечень возможных дефектов и эскиз детали с указанием мест расположения дефектов, способы выявления дефектов и необходимые для это го средства, размеры по рабочему чертежу, допустимые без ремонта размеры, рекомендуемые способы устранения дефектов.
Одной из задач, возникающих при дефектации сложных деталей с боль шим числом контролируемых параметров, является сокращение числа этих па раметров до рационального минимума. Минимизация числа контролируемых параметров возможна, если установлена взаимосвязь дефектов по этим пара метрам.
Для установления взаимосвязи контролируемые параметры деталей одно го типоразмера оценивают в соответствии с техническими требованиями на де фектацию, а результаты заносят в следующую таблицу.
Результаты обследования деталей партии №
№ детали |
|
|
Контролируемый параметр |
|
|
|||
|
X1 |
Х2 |
|
. . . |
Xi |
|
. . . |
ХK |
1 |
1 |
0 |
|
|
0 |
|
|
1 |
2 |
0 |
1 |
|
|
1 |
|
|
1 |
N-1 |
0 |
1 |
|
|
0 |
|
|
0 |
N |
1 |
0 |
|
|
0 |
|
|
1 |
Обозначения, принятые в табл.:
К - число контролируемых параметров; Xj - обозначение j-го контролируемого параметра; 0 - значение параметра, при котором деталь считается годной без
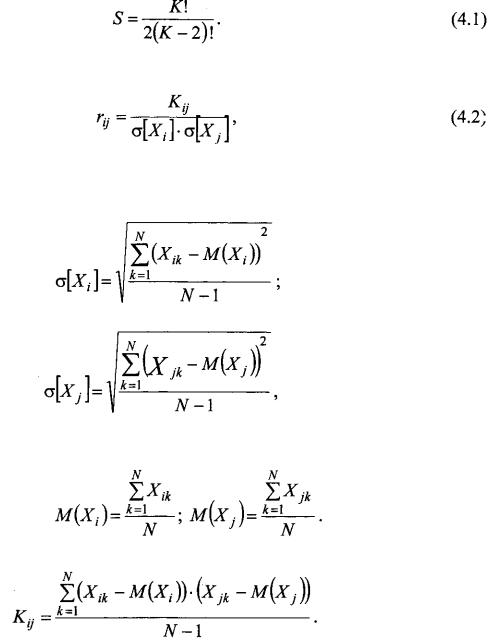
16
ремонта; 1 - значение параметра, при котором деталь считается дефектной (подлежащей восстановлению или негодной); N- число деталей в партии.
Для оценки взаимосвязи дефектов определяют значения коэффициентов корреляции по каждой паре контролируемых параметров. Число коэффициен тов корреляции рассчитывают по формуле:
Для случая парной корреляции коэффициент корреляции можно опреде лить по зависимости:
где Кij - оценка корреляционного момента параметров Xi и Xj, σ[Xi] и σ[Xj] средние квадратические отклонения параметров Xi и Xj вычисляемые по зависимостям:
(4.3)
(4.4)
где Xik и Xjk - значения i-го и j-го параметра k-й детали; M(Xi) и M(Xj) - ма тематическое ожидание i-го и j-го параметра соответственно:
Значение Ktj рассчитывают по формуле:
(4.5)
В тех случаях, когда rij> 0,66, можно считать, что между параметрами
существует хорошая связь, что позволяет прогнозировать значение одного па раметра по значению коррелирующего с ним другого параметра.
Определение объемов ремонтного фонда деталей связано с вычислением коэффициентов годности Кr и восстановления деталей Кв.
Рассмотрим случай, когда необходимость восстановления определяется износом поверхности детали. За численные значения коэффициентов Кг и Kh можно принять вероятности появления годных деталей и деталей, требующих
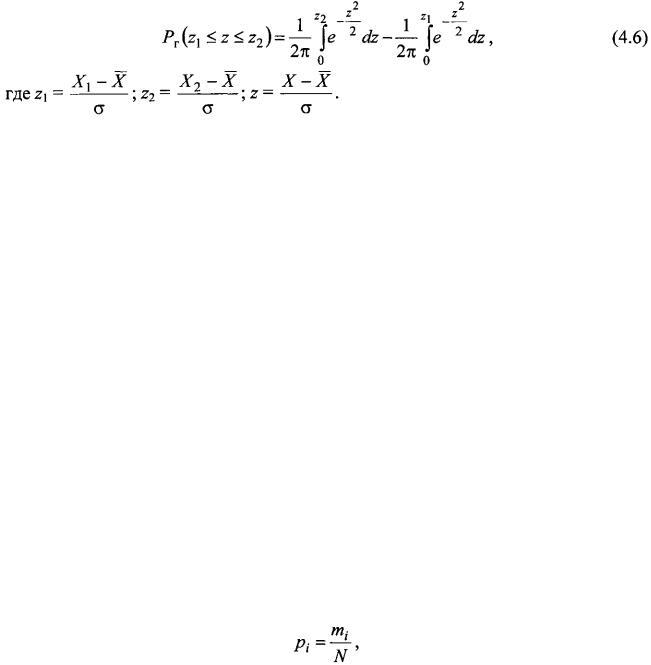
17
восстановления, которые можно представить как противоположные несовмес
тимые события:
Рг + / > » = 1 ,
где Рги Рв- вероятность появления годной и требующей восстановления дета ли.
Если закон распределения износа какой-либо поверхности детали подчи няется закону нормального распределения (что имеет место в большинстве случаев), то задача определения Рг может быть выполнена с помощью функции Лапласа, которая позволяет определить вероятность нахождения случайной ве личины, подчиняющейся нормальному закону распределения, в каком-либо ин тервале [4.1]. Эта вероятность соответствует площади под кривой распределе ния, ограниченной наименьшим и наибольшим допустимыми (без ремонта) значениями размеров (износов):
Здесь Х1 и Х2 - наименьший и наибольший допустимый без ремонта раз мер (износ) детали; X - среднее арифметическое значение размера (износа) де
тали; σ - среднее квадратическое отклонение размера (износа). |
|
|
Pг |
=Ф(z2)-Ф(z1). |
(4.7) |
С целью нахождения характеристик рассеивания размера (износа) в пар тии деталей строят практическую кривую распределения. Для этого измеряют размер X всех деталей партии. Износ каждой детали вычисляют по зависимо стям:
для наружных поверхностей (валов) |
|
|
||
|
|
И = ХВН-Х; |
|
(4.8) |
для внутренних поверхностей (отверстий) |
|
|
||
|
|
И = |
Х-Хон, |
(4.9) |
где |
Хвн и Хон |
- номинальный размер нового (неизношенного) вала и отвер |
||
стия соответственно. |
|
|
||
|
Затем определяют величину рассеивания износа со |
|
||
|
|
ω = Xmax -Xmin или ω = Иmax |
-Иmin , |
|
где |
Хmax, Хmin - максимальный и минимальный размеры изношенных дета |
|||
лей в партии; |
Иmax, Иmin- максимальный и минимальный износ деталей в |
партии.
Полученную величину ω делят на несколько равных интервалов, затем определяют частость попадания размеров в интервал Хi
где mi - количество размеров, попавших в i-й интервал.
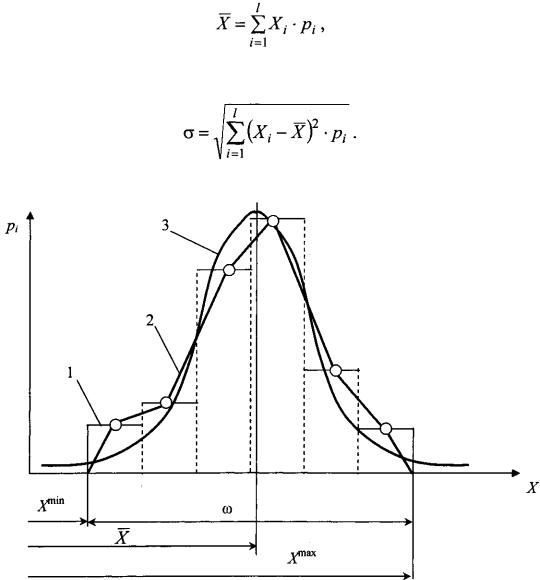
18
По результатам измерений и расчетов составляют таблицы по форме табл. П 2.3 и П 2.4, затем гистограмму и практическую кривую распределения (см. рис.) [4.2].
Основными характеристиками кривой распределения являются:
- среднее арифметическое значение размеров изношенных деталей, которое можно рассчитать по зависимости
(4.11)
где Xt - среднее значение размеров в i-м интервале; l - число интервалов;
- выборочное среднее квадратическое отклонение размеров в партии деталей а
(4.12)
Рис. Гистограмма (1), практическая (2) и теоретическая (3) кривые распределения размера изношенных деталей
На график практической кривой наносится также теоретическая кривая распределения (например Гаусса). Оценку точности совпадения кривых можно провести при помощи критериев согласия, например, критерия Пирсона [4.3].
19
4.3.Содержание работы
Впроцессе выполнения работы необходимо оценить корреляционную связь между контролируемыми параметрами партии деталей ремонтного фонда
исделать заключение относительно возможности сокращения числа контроли руемых параметров. Используя методы математической статистики, необходи мо оценить величину рассеивания одного из размеров партии деталей, постро ить гистограмму и практическую кривую распределения, подобрать близкую к последней кривую нормального распределения и определить коэффициенты годности и восстановления деталей.
4.4.Средства технологического оснащения
-Микрометры МК-25 и МК-50 со стойками.
-Партия деталей ремонтного фонда объемом 25 - 50 штук.
4.5.Порядок выполнения работы
-Измеряют с помощью микрометра несколько размеров у всех деталей партии и, сравнивая результаты измерений с допустимыми без ремонта разме рами, заполняют таблицу по форме табл. П 2.1 приложения.
-По формуле (4.1) рассчитывают число коэффициентов корреляции.
-Используя зависимости (4.2) - (4.4), находят коэффициенты корреляции по каждой паре параметров, результаты заносят в таблицу по форме табл. П 2.2 приложения.
-Отмечают параметры, между которыми существует тесная корреляци онная связь.
-Измеряют с помощью микрометра один из размеров у всех деталей пар тии, результаты измерений заносят в таблицу по форме табл. П 2.3 приложения.
-Находят величину рассеивания со размеров (износа) деталей партии и, приняв число интервалов l, рассчитывают величину интервала АХ = со / £.
-Производят разбивку деталей по интервалам согласно табл. П 2.3.
-По зависимости (4.10) рассчитывают частость /?,; используя данные табл. П 2.4, строят гистограмму и практическую кривую распределения разме ра.
-По зависимостям (4.11) и (4.12) находят среднее арифметическое значе ние и среднее квадратическое отклонение размеров деталей; промежуточные вычисления заносят в табл. П 2.5.
-Строят теоретическую кривую нормального распределения и оценивают точность ее совпадения с практической кривой, используя методику, изложен ную в учебном пособии [4.2].
-Ориентируясь на наименьший и наибольший допустимый без ремонта размеры детали, определяют аргументы функции Лапласа z\ и zi\ из приложе ния [4.2] находят значения функции Лапласа Ф{г{) и Ф(г2) и по формуле (4.7) определяют вероятность появления годной детали Рг. Коэффициент годности Кг