
Met_OrgSynthesis
.pdf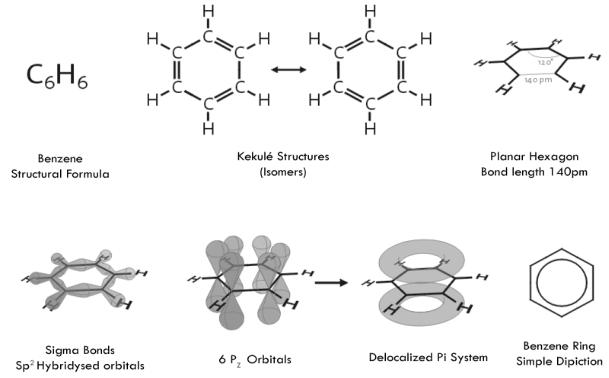
TEXT 4. BENZENE
Benzene, or benzol, is an organic chemical compound and a known carcinogen with the molecular formula C6H6. It is sometimes abbreviated Ph–H. Benzene is a colorless and highly flammable liquid with a sweet smell and a relatively high melting point. Because it is a known carcinogen, its use as an additive in gasoline is now limited, but it is an important industrial solvent and precursor in the production of drugs, plastics, synthetic rubber, and dyes. Benzene is a natural constituent of crude oil, and may be synthesized from other compounds present in petroleum. Benzene is an aromatic hydrocarbon and the second [n]-annulene ([6]-annulene), a cyclic hydrocarbon with a continuous pi bond.
Faraday first isolated and identified benzene in 1825 from the oily residue derived from the production of illuminating gas, giving it the name bicarburet of hydrogen. In 1833, Eilhard Mitscherlich produced it via the distillation of benzoic acid (from gum benzoin) and lime. Mitscherlich gave the compound the name benzin.
In 1836 the French chemist Auguste Laurent named the substance "phène"; this is the root of the word phenol, which is hydroxylated benzene, and phenyl, which is the radical formed by abstraction of a hydrogen atom from benzene.
In 1836, Charles Mansfield, working under August Wilhelm von Hofmann, isolated benzene from coal tar. Four years later, Mansfield began the first industrialscale production of benzene, based on the coal-tar method.
Gradually the sense developed among chemists that substances related to benzene formed a natural chemical family. In 1855 August Wilhelm Hofmann used the word "aromatic" to designate this family relationship, after a characteristic property of many of its members.
The various representaions of benzene:
79
Structure
Benzene represents a special problem in that, to account for all the bonds, there must be alternating double carbon bonds.
Using X-ray diffraction, researchers discovered that all of the carbon-carbon bonds in benzene are of the same length of 140 picometres (pm). The C–C bond lengths are greater than a double bond (135pm) but shorter than a single bond (147pm). This intermediate distance is explained by electron delocalization: the electrons for C–C bonding are distributed equally between each of the six carbon atoms. One representation is that the structure exists as a superposition of so-called resonance structures, rather than either form individually. This delocalisation of electrons is known as aromaticity, and gives benzene great stability. This enhanced stability is the fundamental property of aromatic molecules that differentiates them from molecules that are non-aromatic. To reflect the delocalised nature of the bonding, benzene is often depicted with a circle inside a hexagonal arrangement of carbon atoms.
Production
Until World War II, most benzene was produced as a by-product of coke production (or "coke-oven light oil") in the steel industry. However, in the 1950s, increased demand for benzene, especially from the growing plastics industry, necessitated the production of benzene from petroleum. Today, most benzene comes from the petrochemical industry, with only a small fraction being produced from coal.
Four chemical processes contribute to industrial benzene production: catalytic reforming, toluene hydrodealkylation, toluene disproportionation, and steam cracking. In the US, 50% of benzene comes from catalytic reforming and 25% from steam cracking. In Western Europe, 50% of benzene comes from steam cracking and 25% from catalytic reforming.
Catalytic reforming. In catalytic reforming, a mixture of hydrocarbons with boiling points between 60–200 °C is blended with hydrogen gas and then exposed to a bifunctional platinum chloride or rhenium chloride catalyst at 500–525 °C and pressures ranging from 8–50 atm. Under these conditions, aliphatic hydrocarbons form rings and lose hydrogen to become aromatic hydrocarbons. The aromatic products of the reaction are then separated from the reaction mixture (or reformate) by extraction with any one of a number of solvents, including diethylene glycol or sulfolane, and benzene is then separated from the other aromatics by distillation. The extraction step of aromatics from the reformate is designed to produce aromatics with lowest non-aromatic components. So-called "BTX (Benzene-Toluene-Xylenes)" process consists of such extraction and distillation steps. One such widely used process from UOP was licensed to producers and called the Udex process.
Similarly to this catalytic reforming, UOP and BP commercialized a method from LPG (mainly propane and butane) to aromatics.
80
Toluene hydrodealkylation. Toluene hydrodealkylation converts toluene to benzene. In this hydrogen-intensive process, toluene is mixed with hydrogen, then passed over a chromium, molybdenum, or platinum oxide catalyst at 500–600 °C and 40–60 atm pressure. Sometimes, higher temperatures are used instead of a catalyst (at the similar reaction condition). Under these conditions, toluene undergoes dealkylation according to the chemical equation:
C6H5CH3 + H2 → C6H6 + CH4
This irreversible reaction is accompanied by an equilibrium side reaction that produces biphenyl (aka diphenyl) at higher temperature:
2 C6H6 ↔ H2 + C12H10
If the raw material stream contains much non-aromatic components (paraffins or naphthenes), those are likely decomposed to lower hydrocarbons such as methane, which increases the consumption of hydrogen.
A typical reaction yield exceeds 95%. Sometimes, xylenes and heavier aromatics are used in place of toluene, with similar efficiency.
This is often called "on-purpose" methodology to produce benzene, compared to conventional BTX (benzene-toluene-xylene) processes. The hydrodealkylation process is not economically feasible if the price gap between benzene and toluene is small (or the gap is smaller than about 15% of benzene price).
Toluene disproportionation. Where a chemical complex has similar demands for both benzene and xylene, then toluene disproportionation (TDP) may be an attractive alternative to the toluene hydrodealkylation. Broadly speaking 2 toluene molecules are reacted and the methyl groups rearranged from one toluene molecule to the other, yielding one benzene molecule and one xylene molecule.
Given that demand for para-xylene (p-xylene) substantially exceeds demand for other xylene isomers, a refinement of the TDP process called Selective TDP (STDP) may be used. In this process, the xylene stream exiting the TDP unit is approximately 90% paraxylene. In some current catalytic systems, even the benzene- to-xylenes ratio is decreased (more xylenes) when the demand of xylenes is higher.
Steam cracking. Steam cracking is the process for producing ethylene and other alkenes from aliphatic hydrocarbons. Depending on the feedstock used to produce the olefins, steam cracking can produce a benzene-rich liquid by-product called pyrolysis gasoline. Pyrolysis gasoline can be blended with other hydrocarbons as a gasoline additive, or distilled (in BTX process) to separate it into its components, including benzene.
Current uses
Benzene is used as an intermediate to make other chemicals. Its most widelyproduced derivatives include styrene, which is used to make polymers and plastics, phenol for resins and adhesives (via cumene), and cyclohexane, which is used in the manufacture of Nylon. Smaller amounts of benzene are used to make some types of rubbers, lubricants, dyes, detergents, drugs, explosives, napalm, and pesticides.
81
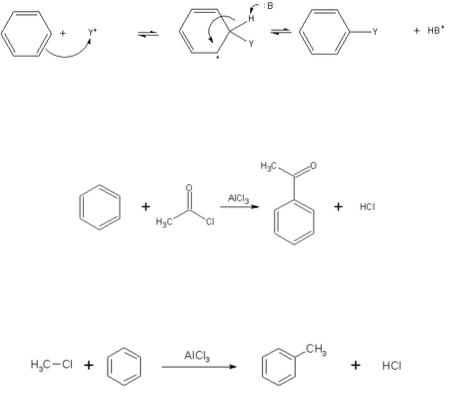
In both the US and Europe, 50% of benzene is used in the production of ethylbenzene / styrene, 20% is used in the production of cumene, and about 15% of benzene is used in the production of cyclohexane (eventually to nylon).
In laboratory research, toluene is now often used as a substitute for benzene. The solvent-properties of the two are similar but toluene is less toxic and has a wider liquid range.
Reactions
Electrophilic aromatic substitution is a general method of derivatizing benzene. Benzene is sufficiently nucleophilic that it undergoes substitution by acylium ions or alkyl carbocations to give substituted derivatives.
The Friedel-Crafts acylation is a specific example of electrophilic aromatic substitution. The reaction involves the acylation of benzene (or many other aromatic rings) with an acyl chloride using a strong Lewis acid catalyst such as aluminium chloride or iron chloride which act as a halogen carrier.
Like the Friedel-Crafts acylation, the Friedel-Crafts alkylation involves the alkylation of benzene (and many other aromatic rings) using an alkyl halide in the presence of a strong Lewis acid catalyst.
Sulfonation. The most common method involves mixing sulfuric acid with sulfate, a mixture called fuming sulfuric acid. The sulfuric acid protonates the sulfate, giving the sulfur atom a permanent, rather than resonance stabilized positive formal charge. This molecule is very electrophillic and Electrophillic Aromatic Substitution then occurs.
Nitration: Benzene undergoes nitration with nitronium ions (NO2+) as the electrophile. Thus, warming benzene at 50-55 degrees Celsius, with a combination of concentrated sulfuric and nitric acid to produce the electrophile, gives nitrobenzene.
Hydrogenation(Reduction): Benzene and derivatives convert to cyclohexane and derivatives when treated with hydrogen at 450 K and 10 atm of pressure with a finely divided nickel catalyst.
Benzene is an excellent ligand in the organometallic chemistry of low-valent metals.
82

TEXT 5. CAPROLACTAM (I)
Application. A process for the production of high-purity caprolactam from benzene and hydrogen or cyclohexane, ammonia, oleum and sulfur dioxide.
Chemical reactions.
Description. In a one-step vapor-phase hydrogenation benzene is hydrogenated to cyclohexane. The cyclohexane is oxidized with air-oxygen in the liquid phase at 150-160°C and 8-9 atmospheres pressure in the presence of a cobalt catalyst. Reaction products obtained: cyclohexanol, cyclohexanone, acids, esters and carbon oxide gases. Due to chosen reaction conditions the efficiency to cyclohexanol and cyclohexanone is in the 76% range. A caustic soda wash neutralizes all acids and saponifies most of the esters. The unreacted cyclohexane is distilled off and recycled; pure cyclohexanone is produced from the crude oxidation oil. The remainder, mainly cyclohexanol, is fed through a vapor phase dehydrogenation, thus producing cyclohexanone. The reaction mixture is recycled into the distillation section.
Hydroxylamine sulfate is produced from ammonium nitrite and sulfur dioxide. The cyclohexanone is reacted with hydroxylamine-sulfate to cyclohexanone-oxime and ammonium-sulfate byproduct. The oxime is rearranged in oleum to caprolactam according to Beckmann’s reaction.
Both the oximation and rearrangement steps proceed at efficiencies close to 100%. The aqueous crude lactam solution is neutralized and ammonium sulfate separated. Both ammonium sulfate streams are processed to fertilizer-grade crystals.
Several extensive purification steps including extractions and final vacuum distillation are used to purify the crude lactam thus producing extremely pure caprolactam at a constant quality level. In the purification section only minor mechanical losses occur.
Special Features: Process is extremely simple to operate and requires 2 shift foremen and 9 shift operators for the complete plant. Use of regular chemical equipment ensures low capital investment and guarantees low maintenance cost. The process is continuous and in one stream up to high capacities.
Consumption figures per ton of caprolactam: |
|
|
|||
Benzene |
kg |
1,018 |
Oleum |
kg |
1,340 |
Hydrogen |
kg |
85 |
Steam |
kg |
14,200 |
Sulfur dioxide |
kg |
1,350 |
Electric power |
kwh |
465 |
Ammonia |
kg |
1,510 |
Export sulfate |
kg |
4,450 |
83
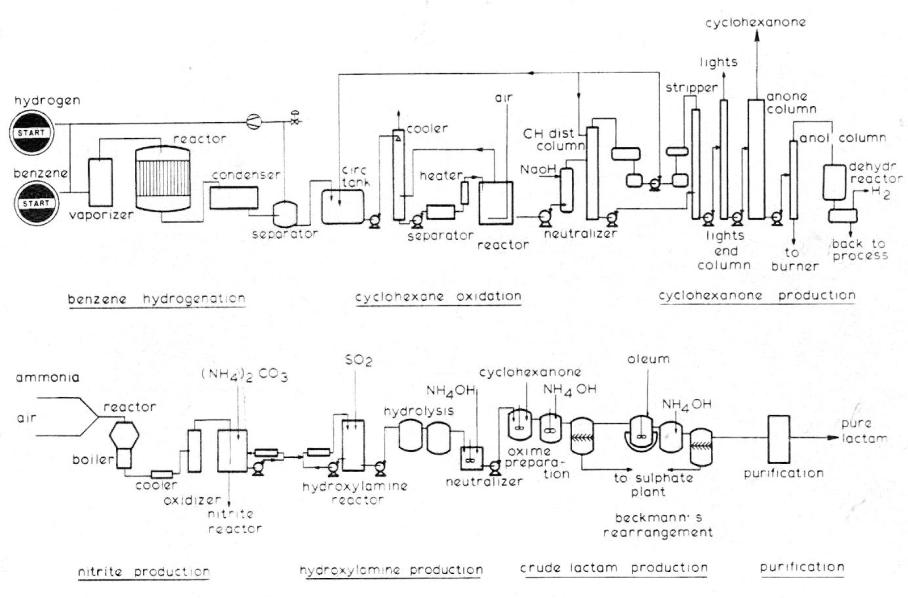
Fig. 7. Caprolactam (I) production scheme
84
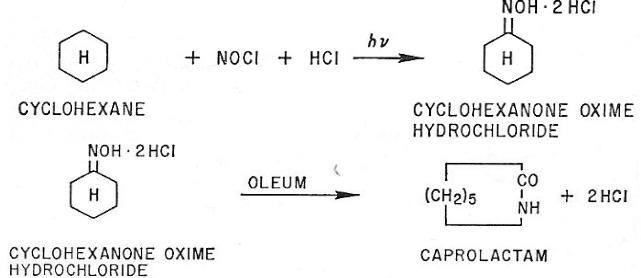
TEXT 6. CAPROLACTAM (II)
Application. A photochemical process for the manufacture of caprolactam from cyclohexane, ammonia, oleum and hydrogen chloride. The products arc fibergrade caprolactam and fertilizer-grade ammonium sulfate crystal.
Description. This is called PNC process which has come from “PhotoNitrosation of Cyclohexane.”
Nitrosyl Chloride. According to following equations, nitrosyl chloride is produced from ammonia.
2NH3 + 3O2 → N2O3 + 3H2O
2H2S04 + N2O3 → 2HNOSO4 + H2O
HNOSO4 + HCl → NOGl + H2S04
Cyclohexanone Oxime Hydrochloride. Special corrosion-resistant materials are employed for the hydrogen chloride and nitrosyl chloride gas circulation system including the photoreaction vessels. A large number of mercury lamps having 60 kw of capacity are immersed in the reaction mixture of photoreaction vessels. The electric power required for the photo reaction has been reduced to less than 1.4 kwh per pound of the oxime produced. Cyclohexanone oxime hydrochloride obtained by the photochemical reaction from cyclohexane is separated as a heavy oil at the bottom of the reaction vessel. Then it is directly supplied to the Beckmann rearrangement step.
The crude lactam solution in sulfuric acid after the rearrangement is continuously fed to neutralizer where the aqueous solution containing caprolactam and ammonium sulfate is obtained by ammonia neutralization. Through several purification steps including vacuum distillation, fibre-grade purified caprolactam is produced. Less than 0.92 pound of cyclohexane is consumed per pound of caprolactam produced. On the other hand, fertilizer-grade ammonium sulfate crystal is recovered from the ammonium sulfate aqueous solution. Less than 2.3 pounds of ammonium sulfate is recovered per pound of caprolactam produced.
85
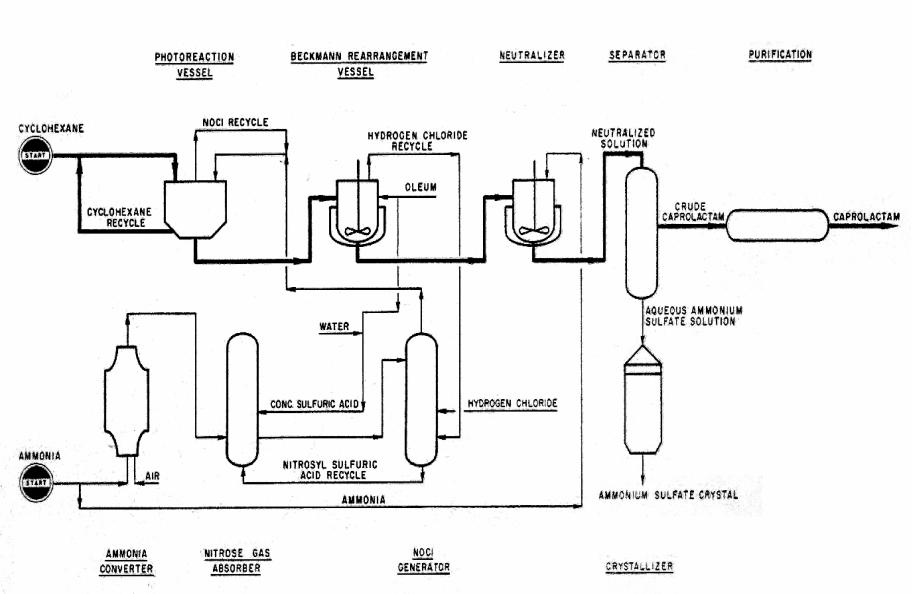
Fig.8. Caprolactam (II) production scheme
86
TEXT 7. ACRYLATES
Application. A process for the synthesis of acrylic acid, from acetylene, carbon monoxide, and water plus alcohol for production of acrylic esters.
Description. The synthesis proceeds on the basis of the following equation: CH = CH + CO + H2O → CH2 = CHCOOH + 52.5 Kcal
The reaction takes place in a liquid phase at 225° С and 100 atm. in the presence of contact salts. The solvent used is tetrahydrofuran. The heat insulated cylindrical reaction furnace has a small gas buffer at the top and contains a vertical, concentrically arranged tube by which an internal liquid circulation is effected. The components are fed to the contact furnace in two forms: in a gaseous form at the bottom and in solution at the top. The acetylene is, for reasons of safety, supplied to the reactor in the form of a gas solution in the tetrahydrofurane, which is produced in a saturator under pressure. The acetylene which is not converted in the synthesis, is recovered and after a water wash mixed with fresh carbon monoxide, again supplied to the synthesis in gaseous form. The catalyzer enters the furnace in solute form.
The inerts are cast off by continuously withdrawing some gas from overhead of the furnace, which is freed from nontransformed acetylene by means of a pressure wash in a separate high pressure vessel. The remainder of the gas is flared.
In this synthesis, an 18% solution of acrylic acid in tetrahydrofurane is produced. The furnace product is continuously drawn off the overflow pipe overhead and passed into a degasser column. The resulting degassed product is separated by distillation in tetrahydrofurane and acrylic acid.
The acrylic acid flows off at the sump of the column over a tube evaporator. Since the raw acrylic acid received in this process still contains some dimers, it is distilled. This acrylic acid received as a distillate flows directly to esterification, and the diacrylic acid that is recovered in the bottom is split thermally to acrylic acid.
A small quantity of acetaldehyde develops in the synthesis, which is concentrated in the return gas stream, where it is washed out with water, together with tetrahydrofurane. Tetrahydrofurane and acetaldehyde are separated in a small column.
The acrylic ester is produced in a continuous installation by means of esterification of acrylic acid with the respective alcohol. In the case of ethyl acrylate and methyl acrylate an alcohol surplus of about 100% is applied. For this reason, a separation of ester and unreacted alcohol is required, which takes place in a water wash column. In the case of butyl acrylate, only a slight excess of butanol is necessary. The alcohol/water mixtures that are formed in the wash column are separated by distillation. For stabilization of the acrylic acid and the acrylic ester during the synthesis and storage, stabilizers in solute form are added at various points.
Operating Conditions. Major operating conditions are described above.
87
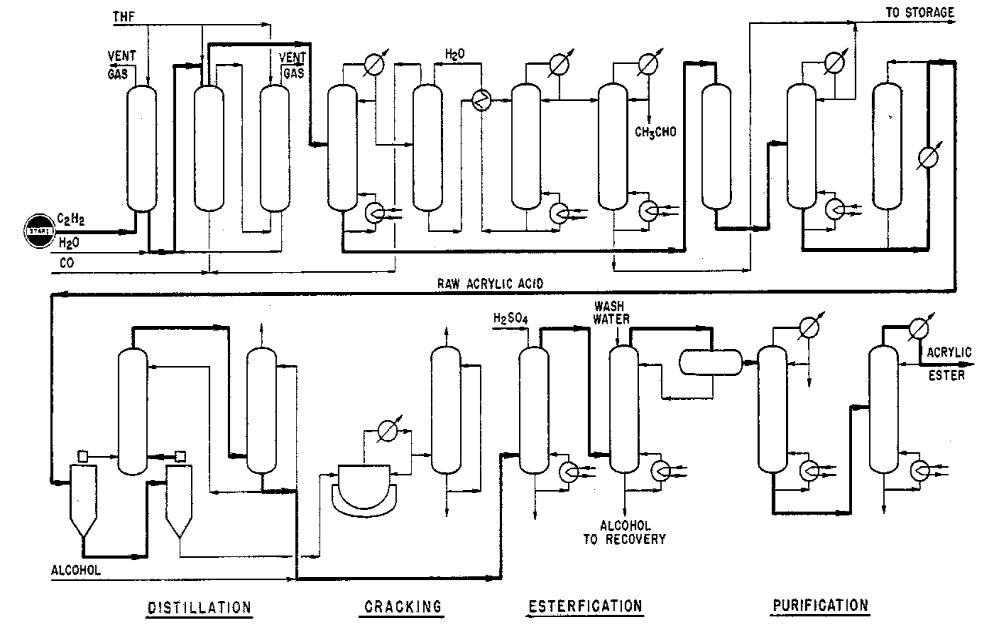
Fig. 9. Acrylic acid synthesis scheme
88