
Госник
.pdf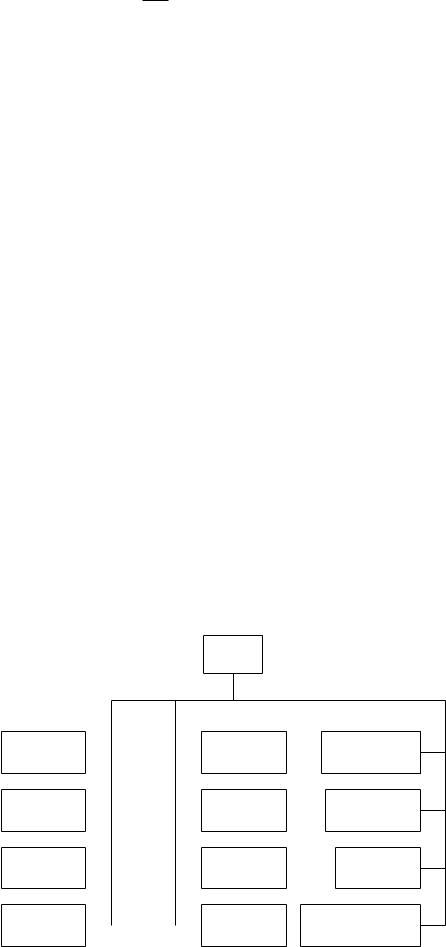
2) основное условие устойчивости:
k |
M |
|
M |
||
|
B O
;
где
M |
B |
|
восстанавливающий момент; |
|||
|
|
|
||||
|
|
|
|
|
||
M |
O |
|
|
опрокидывающий момент; |
|
|
|
|
|
|
|||
|
|
|
|
|
|
|
k |
коэффициент запаса (1,15…1,2). |
|||||
|
|
|
||||
|
|
|
|
|
M |
B |
|
|
|
|
|
|
G |
B |
|
;
где
G |
B |
|
вес ненагруженной вышки;
расстояние от оси вышки до откосов. 3) момент опрокидывания основания:
где
h |
O |
|
4)
M |
OO |
P |
(h |
B |
h |
O |
) P |
|
1 |
|
|
2 |
|
высота основания. |
|
|
|
|
|
|
|
|
|
|
|
|
|
|
|
|
|
|
момент устойчивости: |
|
|
|
|
|
|
|
||
|
M |
BO |
(G |
B |
G |
O |
) |
2 |
; |
|
|
|
|
|
|||||
|
|
|
|
|
|
|
|
|
H |
BET |
|
;
где
|
2 |
|
расстояние от центра вышки до края основания; |
||
|
|
||||
|
|
|
|
||
G |
B |
|
вес вышки; |
||
|
|
|
|
||
|
|
|
|
|
G |
O |
|
вес основания. |
|
|
||
|
|
|
7.2.2.ОСНОВНЫЕ ЭЛЕМЕНТЫ ОСНОВАНИЙ. 1) подроторные балки-выполняются из проката и снабжаются ребрами жесткости для повышения устойчивости;
2) подсвечники-платформа, состоящая из рядов двутавровых балок, соединенных промежуточными связями, на верхнюю часть укладывают деревянный сплошной настил толщиной не менее 70 мм, внутри устанавливаются трубопроводы для подачи пара, предназначенного для обогрева нижних концов бурильных труб.
3) приемные мостки и стеллажи-состоят из наклонной и горизонтальной цельносварной конструкции, горизонтальный стеллаж выполнен в виде полозьев для облегчения транспортировки трубы, длина горизонтальных стеллажей 15м, ширина
2…2,5 м, угол наклона приемного мостка
35...70 |
0 |
|
;
4)лестницы и ограждения, элементы укрытия, опорные элементы.
25.Классификация и основные параметры буровых установок. Способы передвижения. Устройство и работы движителей.
1.Классификация и основные параметры буровых установок. Способы передвижения. Устройство и работы движителей.
БУ
вышка |
|
|
|
подъемный |
компрессоры |
|
|
|
комплекс |
и оборудование |
|
|
|
|
|
пневмоситемы |
|
ротор |
|
|
|
талевая |
циркуляционная |
|
|
|
система |
система |
|
|
|
|
|||
|
|
|
|
||
вертлюг |
|
|
|
лебедка |
оборудование |
|
|
|
устья |
||
|
|
||||
|
|
|
|
|
|
буровые |
|
|
|
силовой |
измерительные и |
|
|
|
пускорегулирующие |
||
насосы |
|
|
|
привод |
|
|
|
|
|||
|
|
|
устройства |
||
|
|
|
|
|
Классификация буровых установок:
1)БУ для бурения глубоких эксплуатационных и разведочных скважин (транспортируются по частям или блокам в зависимости от дорожных условий и транспортных средств);
2)БУ для бурения неглубоких структурных и поисковых скважин ( выполняются мобильными, все оборудование смонтировано на одном шасси или нескольких самоходных платформах);
3)БУ для бурения на море.
Параметр |
БУ для эксплуатационно – |
БУ для структурно – |
|
разведочного бурения |
поискового бурения |
||
|
|||
|
|
|
|
Глубина бурения, м |
1000…15000 |
25…3000 |
|
|
|
|
|
Мощность привода, кВт |
440…4000 |
15…400 |
|
|
|
|
|
Максимально допустимая |
0,8…8 |
0,01…0,8 |
|
Нагрузка на крюк, МН |
|||
|
|
||
|
|
|
|
Диаметр скважины, м |
0,14…0,9 |
0,076…0,17 |
|
|
|
|
|
Диаметр бурильных труб, м |
0,089…0,14 |
0,043…0,089 |
|
|
|
|
Каждая категория БУ имеет несколько классов. Сравнительная оценка мощности и класса БУ – это допустимая нагрузка на крюк и номинальная глубина скважины при бурении, в расчете что конечный диаметр скважины равен 215 мм при использовании бурильных труб диаметром 114 мм с весом одного погонного метра 300 Н.
Для БУ предусмотрено 11 классов. Вид БУ одного и того же класса определяется рядом факторов:
1)условия бурения (местность, температура, окружающей среды, колебание ветра);
2)цель бурения (разведочное или эксплуатационное);
3)тип скважины (вертикальная или наклонная);
4)способ бурения (роторный или забойными двигателями);
5)технология бурения (как проводятся СПО);
6)геологические условия бурения;
Различные виды БУ одного класса могут иметь отличающиеся друг от друга параметры и характеристики отдельных машин и агрегатов. Параметры каждого агрегата выбирают:
1)на основе анализа результатов бурения скважин;
2)по конструкциям скважины и условиям бурения.
ОСНОВНЫЕ ТРЕБОВАНИЯ К БУ.
Технические:
1)высокий к.п.д., достаточная прочность, надежность и долговечность;
2)конструирование должно проводиться с учетом новейших достижений науки и техники;
3)параметры должны соответствовать мировым стандартам.
Эксплуатационные:
1)высокая ремонтопригодность;
2)контроль технического состояния, замена узлов и деталей. Технологические:
1)простота конструкции;
2)простота форм деталей;
3)рациональный выбор материала и способ изготовления деталей;
4)качество изготовления, шероховатость, точность;
5)максимальное использование стандартных и унифицированных деталей и узлов.
Существует три метода монтажа буровых установок: агрегатный, мелкоблочный и крупноблочный.
Агрегатный метод предусматривает индивидуальный монтаж оборудования и строительство сооружений установки с применением фундаментов однократного использования. В этом случае строят бетонные или деревянные фундаменты отдельно под каждый агрегат установки. При повторном монтаже буровую установку разбирают на агрегаты и узлы и перевозят на новую точку бурения, где вновь строят фундаменты, сооружения и монтируют оборудование.
Эти недостатки агрегатного метода приводят к низкой производительности труда и высокой себестоимости сооружения буровых. В настоящее время агрегатный метод применяют очень редко и только при монтаже буровых установок большой грузоподъемности.
Мелкоблочный метод заключается в том, что агрегаты и узлы установки монтируют не на бетонных или деревянных фундаментах, а на металлических основаниях санного типа. Количество мелких блоков определяется конструкцией установки и обычно буровая установка расчленяется на 15—20 мелких блоков. Габаритные размеры и масса мелких блоков позволяют перевозить их на универсальном транспорте или волоком, а в труднодоступных районах — вертолетами.
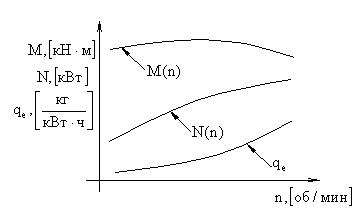
По сравнению с агрегатным методом при мелкоблочном снижается трудоемкость вышкомонтажных работ, сокращаются объемы работ по сооружению фундаментов и сроки сооружения буровых, повышается сохранность оборудования и увеличивается срок его службы, снижается объем транспортно-такелажных работ.
К недостаткам этого способа относятся:
большая расчлененность бурового оборудования на мелкие блоки, в результате чего не обеспечивается создание кинематически увязанных обособленных рабочих узлов; применение оснований санного типа, требующих большое количество тракторов для перетаскивания блоков;
ограниченные габаритные размеры оснований, не позволяющие размещать на них буровые укрытия и коммуникации. Крупноблочный метод монтажа буровых установок включает перевозку агрегатов и узлов установки крупными блоками на специальном транспорте (тяжеловозах), установку блоков на фундаменты и соединение их коммуникациями. При этом буровую установку расчленяют на два-три блока массой 60— 120 т. Крупный блок состоит из металлического основания, перевозимого на специальных транспортных средствах, и смонтированных на нем агрегатов и узлов буровой установки, кинематически связанных между собой. При перевозке таких блоков почти не нарушаются кинематические связи узлов установки и коммуникации и не демонтируются укрытия, что позволяет исключить трудоемкие работы, выполняемые при других методах монтажа (строительные, плотничные, слесарные и некоторые подсобно-вспомогательные).
По сравнению с мелкоблочным методом крупноблочный имеет следующие преимущества:
резкое сокращение числа блоков, размещение буровых укрытий на основаниях, упрощение конструкции фундаментов; снижение объема строительно-монтажных работ и сокращение сроков сооружения буровых до минимума; увеличение скорости транспортировки блоков и уменьшение числа используемых для этого тракторов; повышение срока службы оборудования и оснований благодаря их транспортировке на гусеничных тяжеловозах; экономия строительных материалов.
7.3.2.ПРИВОД С ДВИГАТЕЛЕМ ВНУТРЕННЕГО СГОРАНИЯ (ДВС).
Применяют 3…4 двигателей в групповых установках, мощность 430…790 кВт, частот вращения 1000…1600 об/мин. Соответствие двигателя заданным условиям работы определяется внешней его характеристикой и его конструкцией. Внешней
(механической) характеристикой называется зависимость мощности
q |
e |
от частоты вращения коленвала: |
|
||
|
|
N
, крутящего момента M и удельного расхода топлива
Если нарушается равновесие между моментом сопротивления исполнительного механизма и крутящим моментом двигателя, то это восстанавливается воздействием специальных регуляторов на источник энергии, которые изменяют подаваемое количество топлива и воздуха. ДВС могут работать при изменении массового соотношения воздуха и топлива в сравнительно небольшом диапазоне:
15:1-бедная смесь (15-воздух, 1-топливо); 11:1-богатая смесь.
Для подъемного комплекса рекомендуется режим, при котором ДВС развивает 80% номинальной мощности, а для привода насоса при длительном режиме-60%.
При работе на максимальных оборотах увеличивается расход топлива и сокращается ресурс. Недостатки ДВС: невозможность их запуска под нагрузкой, мощность двигателя зависит от давления, температуры и влажности окружающей среды. Преимущества: высокий к.п.д., небольшой удельный расход топлива и воды, небольшая удельная масса, приходящаяся на единицу мощности.
Потеря мощности на 1% происходит:
1)при увеличении высоты над уровнем моря на 100м;
2)при повышении температуры окружающей среды на каждые 60 С .
Тепловая энергия, потребляемая одним ДВС составляет 40…60 МДж/ч при к.п.д., равном 0,25…0,35%, а часовой расход топлива 220…300 г / кВт ч 7.3.3.ЭЛЕКТРОПРИВОД.
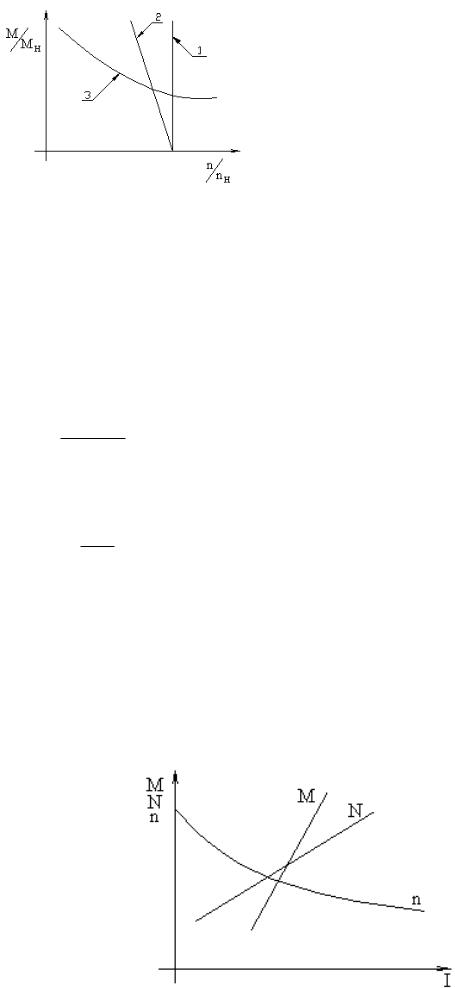
Первоначально применяли асинхронные электродвигатели переменного трехфазного тока с фазным или короткозамкнутым ротором, в последствии стали применять синхронные электродвигатели. Электродвигатели постоянного тока применяют при бурении скважин более 6 тыс.м. Механическая характеристика электродвигателя:
Линия 1-абсолютно жеская характеристика, т.е. частота вращения при уменьшении момента остается постоянной (синхронный двигатель);
Линия 2-жесткая характеристика, с увеличением момента частота вращения уменьшается незначительно (асинхронный двигатель переменного тока и двигатель постоянного тока независимого возбуждения);
Линия 3-гибкая характеристика, при большом изменении момента значительно меняется частота вращения (двигатель постоянного тока с последовательным возбуждением).
Бывает естественная характеристика, в ней частота вращения и момент изменяются до определенного момента автоматически без действия внешних регуляторов. Искусственная характеристика-когда естественная характеристика изменяется при помощи регулирующих устройств.
В асинхронных двигателях:
где
где
S
n |
H |
|
|
100 S |
; |
||||||
|
|
|
|
|
|
|
|
|
скольжение: |
|
|
|
|
|
|
|
|
|
S |
(n |
C |
n |
H |
) |
||
|
|
|
|
|
|
|||
|
|
|
|
|
|
|
||
|
|
|
|
n |
C |
|
|
|
|
|
|
|
|
|
|
|
|
|
номинальная частота вращения; |
|
|
|
|
|
|
|
|
|
|
|
|
|
|
;
n |
C |
|
синхронная частота вращения:
n |
|
|
60 f |
|
C |
z |
|||
|
|
|||
|
|
|
;
где f частота тока;
z число пар полюсов.
Асинхронные электродвигатели с фазным ротором улучшают только пусковае характеристики привода, но не могут работать в приводах главных исполнительных механизмов.
Недостатки синхронного двигателя: невозможность работы параллельно двух двигателей на один вал, что снижает надежность системы и увеличивает динамические нагрузки на трансмиссию.
Электродвигатели постоянного тока обладают гибкой характеристикой, обеспечивающей глубокое и плавное регулирование частоты вращения и момента, а также плавность разгона при пусках и торможения при остановках.
Характеристики двигателя постоянного тока зависят от способов возбуждения (параллельное, последовательное, комбинированное).
Преимущества асинхронных двигателей:
1)простота конструкции;
2)надежность в эксплуатации;
3)сравнительно низкая стоимость.
Внешняя характеристика электродвигателя:
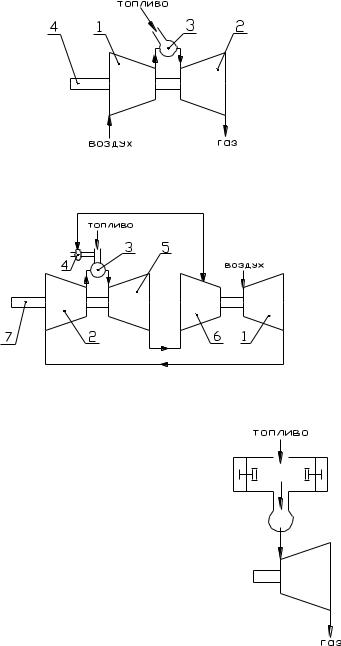
8.ГАЗОТУРБИННЫЕ УСТАНОВКИ (ГТУ).
ГТУ делятся на одновальные, двухвальные и комбинированные и при этом обладают преимуществами:
1)хорошей приемистостью;
2)хорошей надежностью;
3)высокой естественной приспособляемостью. 8.1.ОДНОВАЛЬНЫЕ ГТУ.
Вних компрессор и турбина смонтированы на одном валу:
1-компрессор;
2-турбина;
3-камера сгорания;
4-вал турбины.
При увеличении внешней нагрузки снижается частота и количество газа, питающего турбину, в результате уменьшается мощность и крутящий момент двигателя.
8.2.ДВУХВАЛЬНЫЕ ГТУ.
1,2-компрессоры низкого и высокого давления соответственно; 3-камера сгорания; 4-регенератор;
5-турбина высокого давления;
6-турбина низкого давления;
7-вал турбины.
Независимость валов позволяет изменять характеристику ГТУ в широких пределах. 8.3.КОМБИНИРОВАННЫЕ (СМЕШАННЫЕ) ГТУ.
Недостаток ГТУ: обладает низким к.п.д.
26. Типовые схемы фонтанной арматуры. Состав оборудования фонтанной арматуры, характеристика каждого из них. Расчеты, связанные с конструированием фонтанной арматуры.
Фонтанный или газлифтный подъемник на поверхности стыкуется с фонтанной арматурой, монтируемой на колонной головке скважины. Фонтанная арматура выполняет несколько функций, главные из которых: удержание на весу колонны НКТ, спущенной в скважину, а при двухрядном подъемнике-двух колонн, герметизация затрубных пространств и их взаимная изоляция, обеспечение возможности регулирования режима работы скважины в заданных пределах, непрерывности ее работы и исследования скважины путем измерения параметров ее работы как внутри самой скважины, так и на поверхности.
Стандартом предусмотрено несколько схем, составляющих, как видно, две группы арматур—на базе использования тройников и на базе крестовин.
Трубная головка наиболее характерного типа, используемая в фонтанных арматурах, состоит из корпуса-крестовика 1 с двумя боковыми отводами и фланцами для крепления запорных устройств, трубодержателя 4, переводника 10 для подвески НКТ, уплотнения 2 с грундбуксой 3, втулкой 9 и стопорными винтами 6. Трубные головки изготовливаются согласно требованиям АРI 6А для рабочих давлений от 14 до 105 МПа.
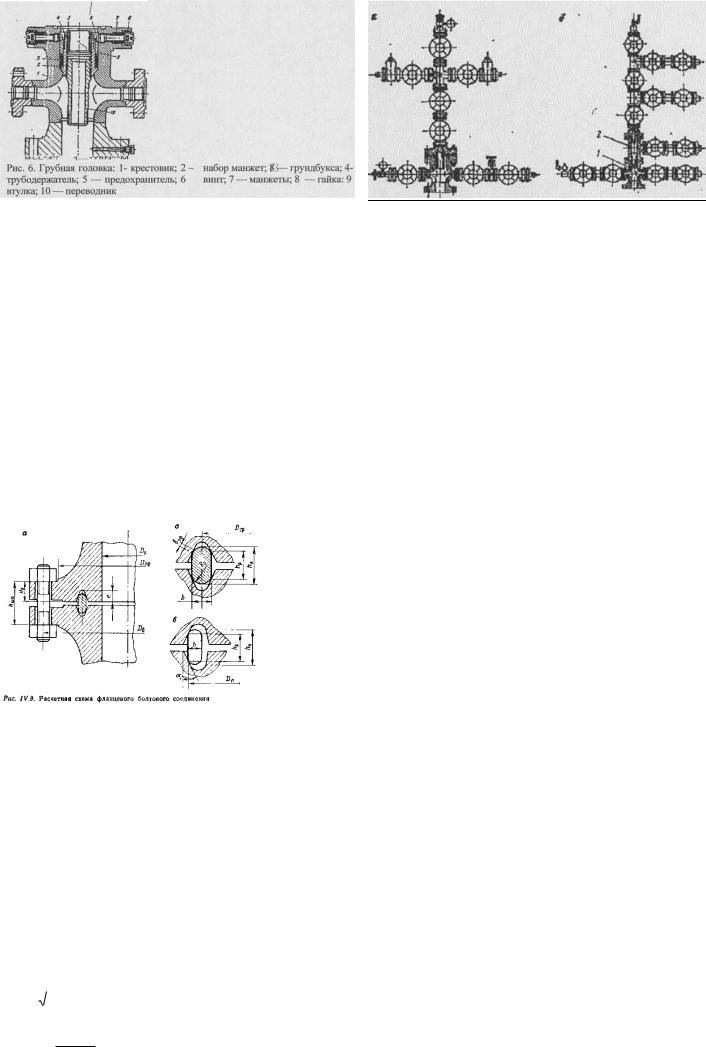
Крестовая арматура для скважин, не содержащих абразив, с проходным (условным) отверстием 50 мм, рассчитана на рабочее давление 70 МПа. Елка арматуры имеет два сменных штуцера, что позволяет быстро их заменять. Арматура рассчитана как на однорядный, так и на двухрядный подъемник, в последнем случае используется другая трубная головка.
Тройниковая арматура Трубная головка, кроме крестовины, имеет тройник, что позволяет нести два ряда НКТ.
Как видно, на арматуре, рассчитанной на большое давление, на боковых отводах установлено не по одной, а по две задвижки. Это обусловлено большей надежностью примененных задвижек при одновременном обеспечении возможности их смены на работающей скважине, т е. без ее остановки. В связи с широким применением клапанов-отсекателей пласта и целого ряда приборов для измерений внутри работающей скважины, диаметры которых значительны.
Арматура надежна при эксплуатации в особо сложных условиях:
В средах, содержащих H2S и CО2 до 25% по объему каждого, примеси нефти, ингибиторы коррозии и др.
При рабочих давлениях от 2000 до 15 000 psi (14–105 МПа);
В различных климатических зонах с температурой окружающей среды от — 60 до + 60 0С.
Существуют несколько способов стыка элементов фонтанной арматуры. Наиболее распространенный — фланцевый с креплением болтами или шпильками. К недостаткам таких соединений относятся их значительная металлоемкость, большое число болтов (шпилек) и необходимость стабильности крепления каждого из них, а также чувствительность соединения к эффекту релаксации. Фланцевые соединения обусловили необходимость сварки литой части заготовок корпусов тройников и крестовин со штамповками, что усложняет изготовление и приводит к увеличению объема работ по механической обработке.
При фланцевых соединениях методика расчета зависит от способа соединения фланцев: шпильками или хомутами. В обоих случаях рассчитывают размеры фланцев и уплотнительной прокладки, но в первом случае рассчитываются шпильки, а во втором — хомут и стягивающие его болты. В обоих случаях определяют усилия предварительной затяжки уплотнительной прокладки. Осевое усилие при, соединении фланцев шпильками, равно сумме усилий затяжки шпилек, а при хомутовом соединении — результирующей от усилий обжима наружных конических поверхностей фланцев внутренними коническими поверхностями хомута.
Вобоих случаях прокладка может занимать относительно граней проточек два положения. В первом случае она еще при сборке касается внутренних и наружных поверхностей проточек, а уплотняется в результате упругой деформации прокладки и зон контакта фланцев. Во втором положение прокладки зависит от затяжки шпилек. При сборке она контактирует с внешней поверхностью верхнего фланца и фаской нижнего, а при последующем обжиме фланцами ее положение и размер меняются, она уменьшается в пределах упругой деформации. Указанием на упор прокладки о внутреннюю поверхность проточки служит резкий скачок в осевом усилии — при затяжке шпилек хомута.
Поставляемая заводами арматура в основном изготовляется с прокладками, выполненными по второй схеме.
Вметодике расчета для второго способа установки прокладки она рассматривается как элемент толстостенного сосуда, находящегося под внешним давлением р0. Тогда эквивалентное напряжение в зоне внутренней поверхности можно определить из формулы
|
экв |
|
2 |
2 |
|
Z |
|
|
|
|
Z |
|
|
|
где — окружное и z осевое напряжения.
2r 2
p0 rн2 н rв2
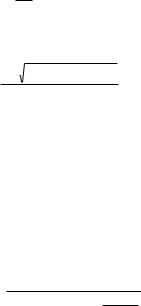
|
|
|
P |
|
|
|
z |
||
|
|
|
|
|
|
z |
|
f |
|
|
|
|
пр |
|
|
|
|
|
где rн и rв—радиусы прокладки (наружной и внутренней);
Рг—осевое усилие; fnp—площадь сечения прокладки, перпендикулярная к ее оси. Подставляя, получим
|
|
|
P |
|
3P |
2 |
4 |
2 |
(r |
2 |
r |
2 |
) |
2 |
|
|
|
|
|
|
|
экв |
|||||||
p |
|
|
z |
|
z |
|
|
н |
в |
|
||||
0 |
|
|
|
|
|
|
2 |
|
|
|
|
|
||
|
|
|
|
|
|
4 r |
|
|
|
|
|
|||
|
|
|
|
|
|
|
|
|
|
|
|
|
||
|
|
|
|
|
|
|
|
н |
|
|
|
|
|
Осевое усилие и внешнее давление связаны уравнением: 2Pz tg 1 p0 DП hр
где Dn— диаметр цилиндра в плоскости касания прокладки и фланца: Dn=2rн - 2R0( I—sin 1), hР=hП—0,22Ro — рабочая высота прокладки.
Примем, что максимальное р0 должно быть таким, при котором экв т материала прокладки. В таком случае становится возможным заменить экв на т с одновременной корректировкой уравнения введением в него коэффициента запаса
прочности, обычно принимаемого 2.5 для фланца и 2,25 для прокладки; тогда экв = т/n
Для определения усилия затяжки необходимо учесть силы трения, возникающие на контакте прокладка—фланцы. С учетом их усилие затяжки будет:
|
|
|
|
|
D |
|
h |
|
(r |
2 |
r |
2 |
) |
|
|
|
||
|
|
|
|
|
П |
Р |
|
|
|
ЭКВ |
|
|||||||
P |
|
|
|
|
|
|
Н |
|
В |
|
|
|||||||
ЗАТ |
|
|
|
2 |
|
|
|
|
|
|
|
|
|
|
|
|
cos( |
) |
|
2 |
2r |
tg ( |
) h |
|
D |
|
1 |
|
1 |
|
|||||||
|
|
|
Р |
П |
|
|||||||||||||
|
|
Н |
1 |
|
|
|
|
|
|
|
|
cos( |
) |
|||||
|
|
|
|
|
|
|
|
|
|
|
|
|
|
|
|
|||
|
|
|
|
|
|
|
|
|
|
|
|
|
|
|
|
|
1 |
|
Когда угол 1 |
имеет большие значения, осевые напряжения малы, поэтому их можно не учитывать. Обозначив |
|||||||||||||||||||
получим упрощенную формулу для определения усилия затяжки: |
P |
0,25 D |
|
h (1 k |
2 |
) ctg |
|
|||||||||||||
|
|
|
||||||||||||||||||
ЗАТ |
|
П |
Р |
|
Т |
1 |
||||||||||||||
|
|
|
|
|
|
|
|
|
|
|
|
|
|
|
|
|||||
Усилия, действующие при работе фланцевого соединения, определяются по формуле: |
|
|||||||||||||||||||
P |
Р |
|
Р |
|
(F |
А |
) р |
|
, где |
F |
D |
|
/ 4 |
|
|
|
|
|
|
|
|
|
|
|
|
|
|
|
|
|
|
|
|||||||||
|
|
|
|
0 |
|
П |
|
|
|
|
|
|
|
|
||||||
ЗАТ |
|
ДАВЛ |
ЗАТ |
0 |
0 |
|
РАБ |
|
|
|
|
|
|
|
|
|
|
|||
|
|
|
|
|
|
|
|
|
|
|
|
|
|
k
rВ
/ rН
,
Эта формула соответствует положению
Величины |
А |
0,5 D |
h |
f (k)ctg |
, |
f (k) 2k |
2 |
/(1 |
|
|
|
|
|||||
|
|
|
|
|
||||
|
0 |
|
П Р |
1 |
|
|
|
|
прокладки, контактирующей в результате затяжки с обеими поверхностями канавки.
k |
2 |
) |
|
где —коэффициент Пуассона.
При использовании арматуры с фланцевыми соединениями старых типов уплотнение прокладок происходит по первому способу. Поэтому практический интерес представляет расчет фланцевого соединения по схеме (см. рис. IV.9, б). Методика этого расчета проще.
В этом случае усилие Рзат определяют по допустимому давлению предварительного обжима q прокладки:
Р |
D b |
q |
, где Dcp—средний диаметр прокладки; Ьэф—эффективная ширина прокладки. |
|
|||
ЗАТ |
СР ЭФ |
|
|
Допустимое давление для сталей марок сталь 20 принимается равным 120—130 МПа, для сталей, предназначенных для работы в коррозионных средах, марок 1Х18Н9—170—175 МПа Приведенный выше метод расчета шпилек предназначен для эксплуатации фланцевого соединения при отсутствии резких
колебаний температур продукции и окружающей среды и при симметричном и равномерном распределении усилий по шпилькам.
27. Оборудование газлифтных скважин. Типы газлифтных установок. Пусковые и рабочие газлифтные клапаны, принцип их действия.
При газлифтном способе эксплуатации нефтяных скважин подъем жидкости происходит за счет энергии газа, нагнетаемого под давлением с поверхности в колонну подъемных труб. Наиболее рациональной технологической схемой эксплуатации скважин является замкнутый газлифтный цикл, при котором нагнетаемый в газлифтные скважины газ многократно используется для подъема жидкости из скважин. При этой схеме в состав промыслового газлифтного комплекса входят: компрессорная станция, трубопроводы подачи газа по промыслу, газораспределительные батареи, сепараторы, газоочистители и скважинное газлифтное оборудование.
В состав оборудования для эксплуатации скважин газлифтным способом входят: колонна насосно-компрессорных труб с рабочими и пусковыми клапанами, пакер, клапан-отсекатель, ингибиторный клапан, клапан аварийного глушения, разъединитель и прочие устройства, наличие которых обусловлено особенностями технологического режима эксплуатации скважин и характером пласта. Устье газлифтной скважины оборудуется колонной головкой и устьевой арматурой, позволяющими герметизировать межтрубное пространство, подвешивать одну или несколько колонн насосно-компрессорных труб, подводить в скважину газ, отводить продукцию пласта в промысловую сеть.
Для оборудования устья газлифтной скважины используется фонтанная арматура.
Для оборудования насосно-компрессорных труб различного вида клапанами в колонну труб встраивают скважинные камеры. Скважинные камеры предназначены для посадки газлифтных или ингибиторных клапанов, глухих или циркуляционных пробок при эксплуатации нефтяных скважин фонтанным или газлифтным способом.
Устанавливают газлифтные клапаны в скважинных камерах специальным инструментом, спускаемым на проволоке гидравлической лебедкой. Эксцентричность камеры обеспечивает при установленном клапане сохранение свободного проходного
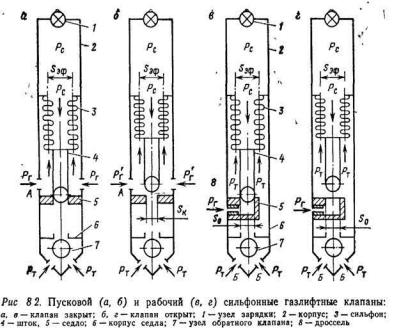
сечения, равного проходному сечению НКТ. Это позволяет выполнять необходимые работы в скважине без извлечения насоснокомпрессорных труб.
Скважинные камеры состоят из наконечников, рубашки и кармана. Рубашку изготавливают из специальных овальных труб. Для уплотнения клапанов в кармане предусмотрены посадочные поверхности. В кармане камеры имеются перепускные отверстия, через которые газ поступает к газлифтному клапану и, открывая его, газирует жидкость в подъемных трубах. При ремонтнопрофилактических работах в карман может быть установлена циркуляционная пробка, а при необходимости заглушить перепускные отверстия - глухая пробка.
Установка камер значительно облегчает и ускоряет спуск скважин и подъем оборудования.
Скважинная камера имеет приварные наконечники и карманы для установки клапанов. Сварка в месте подсоединения наконечников ослабляет прочность скважинной камеры, особенно при работе в агрессивных средах. Поэтому конструкторами принята и вторая технология изготовления скважинных камер, в которой наконечники и рубашка выполняются из цельных труб, без сварки. В этом случае приваривают только карман для установки клапана.
Диаметральные размеры скважинных камер определяются диаметром колонны насосно-компрессорных труб, в которую они встраиваются, и диаметром клапанов.
Длина камеры обусловлена длиной клапана и технологическими особенностями его установки в карман Последнюю задачу разработчик решает при графическом оформлении камеры с учетом размеров клапана и инструмента для его посадки. Рассмотрим несколько подробнее пусковой сильфонный газлифтный клапан, имеющий характерные для всех клапанов элементы.
Газлифтные клапаны Г, управляемые давлением газа, состоят из устройства для зарядки, сильфонной камеры, пары шток-седло, обратного клапана и устройства фиксации клапана в скважинной камере. Сильфонную камеру заряжают азотом через золотник, установленный во ввернутом заряднике. Давление в сильфонной камере клапана регулируют через зарядник на специальном приспособлении стенда СИ-32.
Сильфонная камера-герметичный сварной сосуд высокого давления, основным рабочим органом которого служит металлический многослойный сильфон, являющийся чувствительным элементом клапана. Роль запорного устройства выполняет пара шток-седло. Газ к клапану поступает через отверстие, сообщающееся с затрубным пространством через окна кармана скважинной камеры. Отверстие расположено между двумя комплектами манжет, благодаря чему создается герметичный канал для поступления газа, нагнетаемого из затрубного пространства.
Обратный клапан предназначен для предотвращения перетока жидкости из подъемных труб в затрубное пространство скважины.
Газлифтные клапаны Г по назначению делятся на пусковые и рабочие.
Управляющим давлением для пусковых клапанов (см. рис. 82, а и б) является давление газа, нагнетаемого в затрубное пространство скважины. При их работе газ через отверстие Л проникает в полость, где воздействуя на эффективную площадь сильфона, сжимает его, в результате чего шток поднимается и газ, открывая обратный клапан, поступает в подъемные трубы, аэрируя жидкость в них.
Нагнетаемый газ снижает уровень жидкости в кольцевом пространстве ниже первого клапана. При этом через отверстие клапана газ поступает в подъемные трубы, уровень жидкости постепенно повышается. По мере эксплуатации уровень жидкости в кольцевом пространстве снижается, и обнажается второй клапан.
Первый клапан при этом закрывается, и аэризация происходит через второй клапан.
Число клапанов зависит от давления газа в скважине и ее глубины. Закрываются клапаны последовательно по мере снижения уровня в кольцевом пространстве скважины в момент, когда перепад между давлениями в кольцевом пространстве и в подъемной колонне, действующий на клапан, достигает заданного.
Понижение уровня в затрубном пространстве продолжается до глубины расположения нижнего (рабочего) клапана, через который поступает газ при заданном технологическом режиме работы скважины, при этом верхние (пусковые) клапаны закрыты. Они используются только в период пуска скважины.
28. Типоразмеры и конструкции штанговых насосов. Группы посадки плунжера в цилиндре.
Насосы по своей конструкции делятся на две основные группы: невставные (трубные) и вставные. В каждой из этих групп имеются различные типы насосов, отличающиеся конструктивными особенностями, устройством отдельных узлов. Невставные насосы характерны тем, что цилиндр насоса спускается на насосно-компрессорных трубах, а его плунжер в сборе со всасывающим и нагнетательным клапанами — на штангах. Поднимают невставной насос из скважины также в два приема: сначала извлекаются штанги с плунжером и клапанами, а затем трубы с цилиндром.
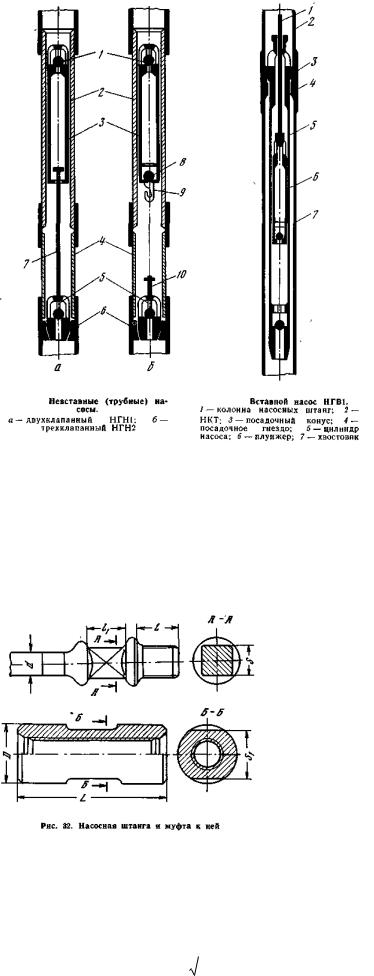
Вставной насос спускают в скважину в собранном виде (цилиндр насоса вместе с плунжером) на штангах и' извлекают его на поверхность также в собранном виде. Спущенный в со
бранном виде вставной насос закрепляют в скважине при помощи специального замкового приспособления, заранее спускаемого в скважину на трубах.
Невставные (трубные) насосы подразделяются на два типа: двухклапанные НГН1 и трехклапанные НГН2 (насосы глубинные невставные первого и второго типов соответственно). Эти насосы имеют три основных узла: 1) цилиндр с седлом конуса всасывающего клапана; 2) плунжер с нагнетательными клапанами (одним или двумя); 3) всасывающий клапан с захватным приспособлением.
Вставные насосы НГВ (насос глубинный вставной) с опорой, расположенной в верхней его части, НГВ1 имеют три основных узла: цилиндр, плунжер и замковая опора цилиндра.
Глубинные насосы с металлическими плунжерами всех типоразмеров изготовляют с зазорами трех величин между плунжером и цилиндром, что характеризует степень пригонки или посадку плунжера в цилиндре насоса.
В зависимости от величины зазора между плунжером и цилиндром насосы подразделяются на три группы посадки: I
— с тугой посадкой (минимальный зазор); II — со средней
посадкой; III группа— со слабой посадкой (максимальный зазор).
Зазоры (в мм) между плунжером и цилиндром для глубинных насосов всех типоразмеров следующие: для насосов I группы -
0,02…0,07; II группы - 0,07…0,12; III группы - 0,12…0,17.
Группы посадок устанавливает потребитель при передаче заводу заказов на изготовление насосов.
При высокой температуре и большой вязкости нефти нужно применять насос со слабой пригонкой и, наоборот, при низкой температуре и малой вязкости нефти — с тугой пригонкой.
29. Конструкция и размеры насосных штанг и муфт к ним. Материалы и методы упрочнения насосных штанг и муфт. Расчет и конструирование штанговой колонны.
Насосные штанги выпускают в соответствии с ГОСТ 13877—68 диаметрами 12, 16, 19, 22 и 25 мм и средней длиной 8 м. Для подбора длины колонны 'штанг при посадке плунжера выпускают также короткие штанги длиной от 1 до 3 м тех же диаметров.
Часто в скважину спускают ступенчатые колонны, состоящие из штанг нескольких диаметров. Для соединения штанг разных диаметров, например, 16 и 19 мм, 19 и 22 мм, 22 и 25 мм, изготовляют переводные муфты ГОСТ 13877—68 рекомендует для изготовления штанг стали марок 40
(углеродистая), 20НМ (никель-молибденовая) и ЗОХМА хромистомарганцовистая).
Для повышения механических свойств стали и достижения равнопрочности штанг по всей длине их подвергают различным видам термической обработки: нормализации (нагрев до определенной температуры с последующим охлаждением на воздухе), сорбитизации, состоящей из трех операций —
нормализации, закалки и отпуска. Для упрочнения штанг поверхность их закаливается токами высокой частоты или наклепывается дробью.
РАСЧЁТ КОЛОННЫ ШТАНГ Колонна штанг рассчитывается с учетом переменных нагрузок действующих на штанги в течение каждого качания, не по мак-
симальному напряжению, вычисленному исходя из статических условий прочности, а по методике, предложенной А. С. Вирновским, согласно которой в качестве расчетного принимается «приведенное» напряжение, учитывающее циклический
|
|
|
характер работы штанг: ПР MAX A |
где пр — приведенное напряжение в опасном сечении колонны штанг; max — |
максимальное напряжение в опасном сечении за цикл; ; a — амплитуда напряжения в опасном сечении за цикл.
MAX |
СР А |
где |
|
СР |
MAX |
MIN |
A |
|
MAX MIN |
|
2 |
2 |
|||||||
|
|
|
|
|
|
|
|
В формулах min — минимальное напряжение за цикл (минимальным будет напряжение при ходе штанг вниз).
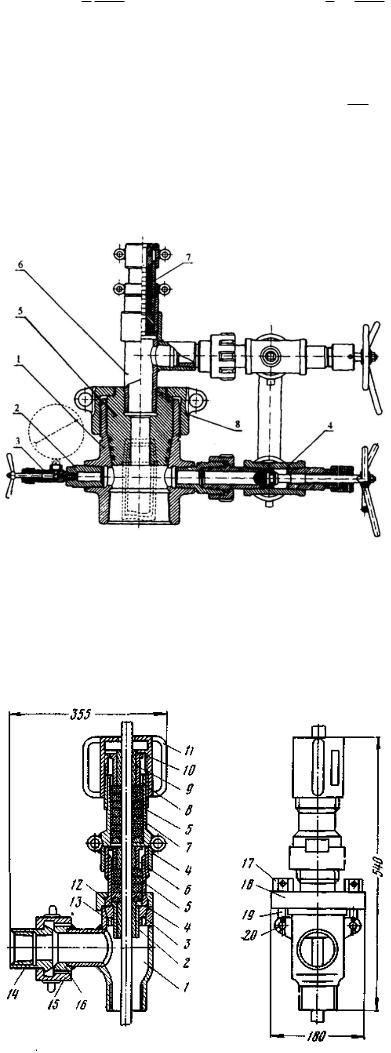
|
|
1 |
D |
2 |
|
|
||
|
|
gL |
|
|
|
ПЛ |
1 gL |
|
|
|
|
|
|
|
|
|
|
|
СР |
2 d |
2 |
1 |
||||
|
|
|
ШТ |
|
|
|
|
|
1 |
a |
D |
2 |
L m gL |
|
2 |
s |
|
|
|
|
|
|
|
||||||
|
|
|
ПЛ |
|
|
|
|||||
|
|
|
|
|
|
|
|
|
|
||
|
A |
|
2 |
0 |
d |
2 |
1 |
2g |
|||
|
|
|
|
ШТ |
|
||||||
|
|
|
|
|
|
|
|
|
|
где ср и а — напряжение в Па; и p1 — плотность жидкости и металла штанг в кг/м3; g — ускорение силы тяжести (g— 9,81 м/с2); L — глубина спуска насоса в м; D и d — диаметр плунжера и штанг в любой, но одинаковой размерности (мм); а0 — коэффициент, имеющий размерность плотности, принимаемый равным 1150 кг/м3; т — средний кинематический коэффициент,
равный 1,05…1,2; — угловая скорость кривошипа (
|
n |
|
30 |
||
|
где n — число качаний в минуту); s — длина хода сальникового
штока в м.
При подборе группы прочности стали для штанг руководствуются следующими нормами допускаемых приведенных напряжений:для углеродистых штанг (сталь 40) — 7 МПа);для тех же штанг с уплотненной поверхностью — 80 МПа для легированных сталей с соответствующей термообработкой — 90…110 Мпа.
30. Устьевая арматура скважин, эксплуатирующихся штанговыми насосными установками. Конструк-ции и предъявляемые к ним требования.
Устьевая арматура скважины, эксплуатируемой УШГН, кроме функций выполняемых при всех способах добычи должна обеспечить герметичность перемещающегося в ней возвратнопоступательно полированного штока. Последний является механической связью между колонной штанг и головкой балансира СК. На рис. 5.6 приведена одна из конструкций арматуры [ 12], применяющейся на промыслах.
Рис. 5.6. Устьевая арматура:
1 - колонная головка; 2 - затрубный ниппель; 3 - вентиль манометра; 4 - затрубный патрубок с вентилем; 5 - трубная головка; 6 - торйник; 7 - сальник; 8 - гайка.
Для подвески насосных труб, вывода продукции скважины в выкидную линию, герметизации устья, а также для отбора газа из затрубного пространства, на устье скважины устанавливают специальное оборудование. Это оборудование состоит из планшайбы и тройника-сальника. Известно много конструкций устьевого оборудования
насосных скважин, изготовляемых как на заводах, так и в мастерских НГДУ. Наиболее известной конструкцией долгое время было оборудование СГН, созданное в АзИНМАШе более 20 лет тому назад. В этой конструкции планшайба с подвешенными на ней трубами устанавливается на колонный фланец. В верхнюю муфту труб ввинчивают тройник для отвода нефти. Выше тройника для его герметизации и пропуска сальникового штока устанавливают сальник, набивку которого уплотняют сверху крышкой.
В связи с широким внедрением напорных систем сбора нефти и газа появилась необходимость применять на устье глубиннонасосных скважин оборудование, работающее при повышенных давлениях. С этой целью применяют устьевые сальники с самоустанавливающимися головками (СУСГ1, и СУСГ2).
Устьевой сальник СУСГ2.
1 - тройник; 2, 6, 8 - нижняя, промежуточная (средняя) и верхняя втулки; 3 - шаровая головка; 4 - нижний и верхний манжетодержатели; 5 - нижняя и верхняя сальниковые набивки; 7 -корпус сальника; 9 - вкладыши; 10 - крышка корпуса; 11 - ручка; 12 - уплотнительное кольцо; 13 - стопор; 14 -ниппель; 15 - накидная гайка; 16 - наконечник; 17гайка; 18 - крышка; 19 - откидной болт; 20 - палец Сальник СУСГ2 с двойным уплотнением (рис. 37) состоит из
двух основных узлов: самоустанавливающейся шаровой головки и тройника. В шаровой головке помещены нижняя и промежуточная (средняя) втулки, нижний манжетодержатель и нижняя сальниковая набивка. В корпусе сальника, навинченном на головку, помещены верхний манжетодержатель, верхняя сальниковая набивка и верхняя втулка (грундбукса). Сальниковую набивку