
Госник
.pdf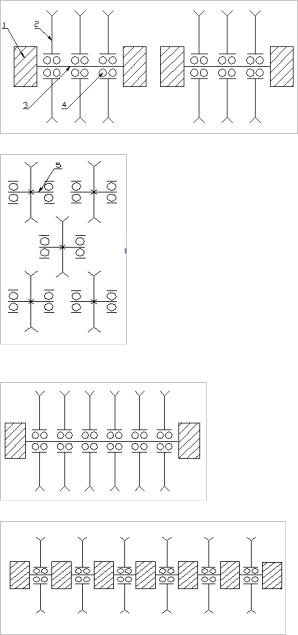
где - модуль упругости каната;
- модуль упругости проволоки;
- коэффициент (0,33…0,35 для стальной свивки).
Конструктивное удлинение каната в пределах 0,2…6% от первоначальной длины каната. Длина каната гостируется в зависимости от диаметра каната:
диаметр, мм |
25 |
28 |
32 |
35 |
38 |
|
|
|
|
|
|
длина, м |
1000 |
1200 |
1500 |
2000 |
2000 |
|
|
|
|
|
|
Шифр каната:
Канат 1-32-1600-В-ГОСТ 16853-71;
где 1 - исполнение; 32 - диаметр каната, мм;
1600 - предел прочности проволоки, МПа; В - правая крестовая свивка марки В (1600-Л-В левая крестовая). 2.КРОНБЛОК.
Кронблок-неподвижный узел талевой системы, предназначен для поддержания на весу подвижной части и груза на крюке. Устанавливается на горловине вышки. Кронблок передает вышке нагрузку от веса колонны и собственного веса талевой системы. Кронблоки состоят из двух групп шкивов, смонтированных соосно на подшипниках качения. Кронблоки различаются грузоподъемностью, числом шкивов и их диаметром. По числу осей и их креплениюразличаются:
а) соосные с промежуточными опорами осей;
б) многоосные;
в) одноосные с двумя внешними опорами;
г) одноосные многоопорные;
д) комбинированные.
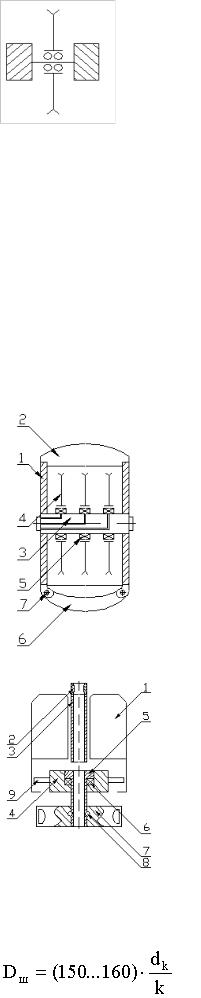
Маркировка кронблока:
У3-300;
где У-завод «Уралмаш»; 3-номер оборудования буровой установки;
300-грузоподъемность на крюке, тонн.
УКБА-7-300;
где У-завод «Уралмаш»; КБ-кронблок;
А-кронблок применим в комплексе АСП; 7-количество шкивов; 300-грузоподъемность, тонн. 3.ТАЛЕВЫЙ БЛОК.
Талевый блок является подвижной частью талевой системы. Существуют два вида талевых блоков: одноосные и соосные. В одноосном все шкивы смонтированы на одной оси, в соосном талевый блок состоит из двух блоков со шкивами, между которыми предусмотрено пространство для спуска свечи. На рисунке показан одноосный талевый блок.
1-боковая щека;
2-траверса;
3-ось с каналами для подачи смазки к подшиникам; 4-шкив; 5-подшипник; 6-серьга; 7-палец.
Двухосный талевый блок применяется в талевых системах АСП (автоматического спускаподъема). Особенности его конструкции в том, что между секциями шкивов расположен желоб с приемным конусом, который обеспечивает направление талевого блока вдоль свечи. В нижней секции вмонтированы две оси для подвески траверсы, в которой установлен стакан со скобой-подвеской.
1-секция шкивов;
2-приемный конус;
3-желоб;
4-траверса;
5-стакан;
6-подшипник;
7-скоба-подвеска;
8-палец;
9-ось.
Материалы для изготовления талевых блоков: шкивы - среднеуглеродистые стали легированные хромом и марганцом, оси - Сталь40.
4.ШКИВЫ.
Шкивы у талевого блока и у кронблока имеют одинаковую форму и размеры.
На срок службы талевых канатов влияют диаметр шкива, профиль и размеры канавки. С увеличением диаметра шкива возрастает усталостная долговечность каната. Диаметр шкива определяют по формуле:
;
где диаметр каната;
запас прочности.
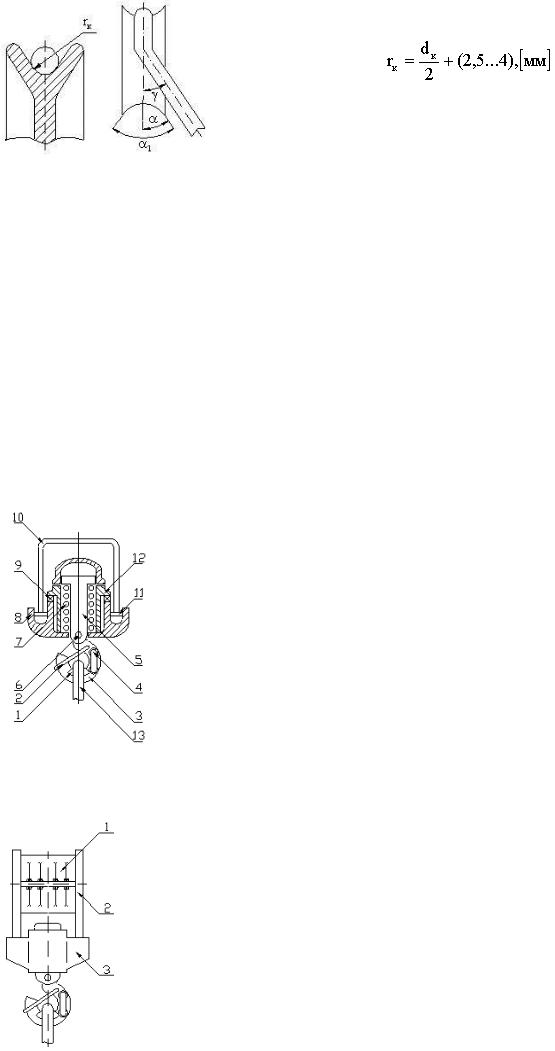
;
где радиус ложи канавки.
При увеличении радиуса канавки опорная поверхность каната уменьшается, возрастают контактные напряжения, вследствие чего уменьшается срок службы
каната. Для нормальной работы каната угол должен быть
больше угла .
Для более правильной работы угол должен быть
.
Канавка шкива подвергается поверхностной закалке на глубину не менее 3 мм, с твердостью поверхности , радиальное биение не должно превышать 2 мм, а смещение оси канавки от средней плоскости шкива не должно превышать 2 мм.
Шифр талевого блока:
ТБ-3-100; УТБА-5-300; ТБ-75-Бр; У4-300
расшифровка аналогична расшифровке шифра кронблока. 5.КРЮКИ.
Предназначены для подвешивания вертлюга и буровой колонны, для подвешивания элеватора с помощью штропов, для подвешивания и перемещения тяжелого бурового оборудования при монтажно-демонтажных работах и инструмента при бурении скважин. Крюк входит в талевую систему и является ее третьим узлом после кронблока и талевого блока. По конструкции крюки бывают: литые, кованные, пластинчатые. Лучше всего применять пластинчатые крюки, т.к. это облегчает изготовление самого крюка и повышает его надежность. Пластины для такого крюка изготавливают из легированной конструкционной стали с пределом текучести свыше 700 МПа, пластины соединяют между собой потайными заклепками. Для защиты и предохранения зева основного крюка от износа в нем закреплена защитная подушка из материала 35ХНЛ.
1-подушка;
2-подпружиненный стопор;
3-основной рог;
4-дополнительный рог;
5-ствол крюка;
6,11-ось;
7-пружина;
8-корпус;
9-подшипник;
10,13-штроп;
12-стакан.
Материал изготовления: литой крюк - 30ХНЛ; штропы - 30ХГСА, 35; корпус - 30Л, 35Л; боковые рога - 38Х2Н2МА, 40ХН.
5.1.КРЮКО-БЛОКИ.
Представляют собой совмещенную конструкцию талевого блока и крюка. Преимущество: высота крюко-блока меньше суммарной высоты талевого блока и крюка, что позволяет уменьшить высоту вышки. Недостаток: крюко-блок тяжелее, чем
крюк, и им труднее манипулировать при спуско-подъемных операциях.
1-талевый блок;
2-боковая щека;
3-крюк.
8. Буровая лебедка: назначение и параметры, классификация, кинематика и динамика.
Назначение:
Буровые лебедки - это основной механизм буровой установки, он предназначен для проведени следующих операций:
1)спуска и подъема бурильных и обсадных труб;
2)удержания колонны на весу;
3)передачи вращения ротору;
4)свинчивания и развинчивания труб;
5)производства вспомогательных работ по подтаскиванию на буровую инструмента, оборудования, труб и т.д.;
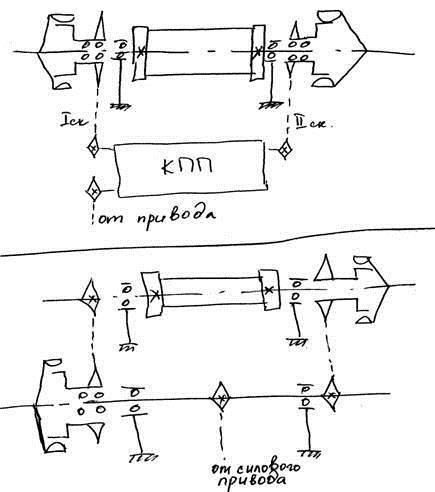
6)для подъема собранной вышки в вертикальное положение.
Основные узлы лебедки:
1)подъемные и трансмиссионные валы;
2)КПП (коробка перемены передач);
3)тормозная система, состоящая из основного и вспомогательного тормозов.
Классификация лебедок:
1)по мощности от 200 до 3000 кВт;
2)по числу скоростей подъема 2,3,4,6 скоростные;
3)используемый привод: со ступенчатым, непрерывноступенчатым, бесступенчатым изменением скорости подъема;
4)по типу двигателя: электродвигатели переменного тока, электродвигатели постоянного тока, двигатели внутреннего сгорания;
5)по числу валов: одновальные, двухвальные, трехвальные;
6)по схеме включения быстроходной передачи: а) независимая быстрая скорость; б) зависимая быстрая скорость.
7)по способу управления подачей долота: с ручным или автоматическим управлением.
8)В зависимости от используемого привода различают буровые лебедки:
-со ступенчатым,
-непрерывно-ступенчатым
-бесступенчатым изменением скоростей подъема.
По числу скоростей, передаваемых ротору, и кинематической схеме передач, установленных между лебедкой и ротором.
По способу управления подачей долота различают буровые лебедки с ручным и автоматическим управлением, осуществляемым посредством регулятора подачи долота.
Кинематика
Задача кинематики - определение скоростей и ускорений подъемного механизма. При этом заданными являются высота подъема, кинематическая схема и размеры звеньев подъемного механизма, частота вращения и характеристика используемого двигателя.
При спуско-подъемных операциях высота подъема h несколько превышает длину бурильной свечи l, т. е. H . Это обусловлено возможностью установки бурильной колонны на клинья либо элеватор. При спуске бурильная колонна приподнимается для освобождения клиньев либо элеватора, поэтому перемещения при спусках и подъемах бурильных свечей примерно одинаковые.
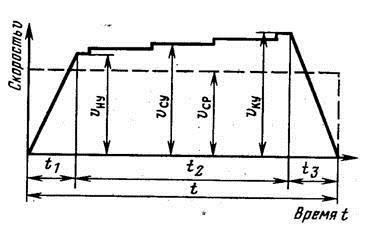
Изменения скорости за время подъема и спуска одной свечи изображаются тахограммой. Для подъемных механизмов характерна трехпериодная тахограмма подъема, имеющая трапецеидальную форму (рис. Х1.9)
Рис. Х1-.9. Тахограмма подъема
Динамика
Динамические нагрузки в подъемном механизме буровой установки возникают при СПО вследствие действия ускорения или замедления, а также упругих колебаний создавемых во время переходных процессов.
В процессе подъема динамические нагрузки зависят от пусковых св-в двигателей и упругости ситстемы, включающей силовые передачи, лебедку, талевый канат, вышку и колонну поднимаемых труб. При спуске зависят от снижения скорости, регулируемой вспомогательным и основным тормозами лебедки, а также от упругости талевого каната, вышки и колонны спускаемых труб.
9.Расчет рабочих параметров буровых лебедок и нагрузок, действующих на узлы.
Косновным параметрам буровых лебедок относятся мощность, скорости подъема, тяговое усилие, длина и диаметр барабана лебедки.
Мощность лебедки определяется полезной мощностью на ее барабане, которая должна быть достаточной для выполнения спуско-подъемных операций и аварийных работ при бурении и креплении скважин заданной конструкции. Оптимальная мощность буровой лебедки определяется из условий подъема наиболее тяжелой бурильной колонны для заданной глубины бурения с расчетной скоростью 0,4—0,5 м/с:
Nб = (Gб.к +Gт)*vр / т.с
где Nб —мощность на барабане лебедки, кВт; Gб.к —вес бурильной колонны, кН; Gт —вес подвижных частей талевого механизма, кН; vр —расчетная скорость подъема крюка, м/с; т.с — к.п.д. талевого механизма.
Мощность лебедки уточняется после выбора двигателей и силовых передач ее привода:
Nб = Nдв* тр,
где Nдв—мощность, получаемая от вала двигателя, кВт; тр— к.п.д. трансмиссии (от вала двигателя до барабана лебедки). Максимальная скорость подъема ограничивается безопасностью управления процессом подъема и предельной скоростью ходовой струны, при которой обеспечивается нормальная навивка каната на барабан лебедки.
Учитывая известную зависимость скорости ходовой струны от скорости подъема крюках = кр iт.с, максимальную скорость подъема выбирают из следующих условий:
для талевых механизмов с кратностью оснастки iт.с≤10 (υкр)max=2 м/с;
для талевых механизмов с кратностью оснастки iт.с>10
(υкр)max=20/ iт.с м/с.
Величина минимальной скорости подъема принимается в установленных практикой бурения пределах: (υкр)min=0,1÷0,2 м/с.
Диаметр барабана лебедки выбирают в зависимости от диаметра талевого каната
Dб=(23÷26)dk.
Диаметр конечного слоя навивки каната на барабан
Dk=Dб+α(2K-1).
где α=0,93—коэффициент, учитывающий уменьшение диаметра навивки вследствие смещения каната в промежутки между витками нижнего слоя.
Средний диаметр навивки
Dср=Dк+D1)/2,
где D1=Dб+dк—диаметр 1-го слоя навивки каната на барабан.
Длина барабана выбирается с таким расчетом, чтобы при заданном его диаметре обеспечить навивку каната в три-четыре слоя. Расчеты на прочность деталей и узлов лебедки выполняются по тяговому усилию, возникающему при допускаемой нагрузке на крюке, с учетом веса подвижных частей талевого механизма, кратности оснастки и потерь на трение при подъеме.
10. Тормозная система буровых лебедок.
ЛЕНТОЧНЫЙ ТОРМОЗ.
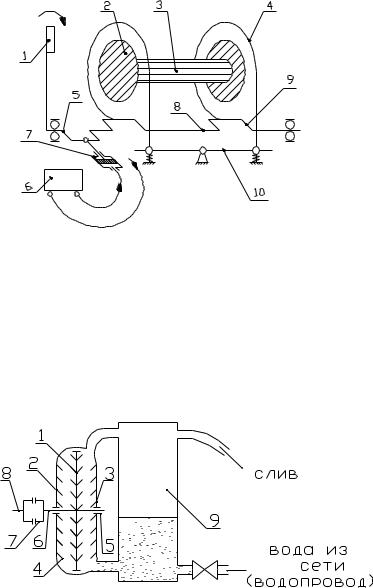
Требования к ленточному тормозу:
1)тормозной момент должен обеспечивать надежное удержание в неподвижном состоянии колонны труб;
2)привод тормоза должен обеспечивать плавное регулирование тормозного момента и мягкую посадку колонны на стол ротора;
1-рукоять тормоза;
2-тормозные шкивы;
3-барабан;
4-тормозные ленты с фрикционными накладками; 5,9-шейки коленвала;
6-регулятор управления;
7-тормозной цилиндр;
8-коленвал;
10-балансир.
3) тормоз должен растормаживаться одновременно с включением привода лебедки;
4)конструкция должна обеспечить легкость в управлении, удобство в обслуживании и исключить самопроизвольное расторможение и торможение;
5)температура во фрикционной паре не должна превышать допустимую.
6.2.ВСПОМОГАТЕЛЬНЫЙ ТОРМОЗ. Принцип действия основан на поглощении части энергии, освобождающейся при спуске колонны, в результате чего на долю ленточного томоза остается только остановка колонны. Вспомогательный
тормоз должен иметь возможность регулирования тормозного момента в зависимости от веса спускаемой колонны, и автоматически отключаться или значительно уменьшать свой тормозной момент при подъеме колонны. 6.3.ГИДРОДИНАМИЧЕСКИЙ ТОРМОЗ
1-ротор;
2,3-статор, выполненный в виде крышек; 4-направляющие лопатки; 5-подшипник; 6-вал; 7-муфта;
8-подъемный вал лебедки;
9-холодильник.
При правильном выборе объема воды, залитой в систему, можно установить оптимальную скорость спуска колонны в каждом конкретном случае. Чем меньше скорость спуска, тем меньший тормозной момент развивает гидродинамический тормоз. Тормозной момент зависит от диаметра и частоты вращения ротора, регулируется уровнем наполнения жидкости в тормозе. Тормозной момент пропорционален диаметру ротора в пятой степени. Температура воды в тормозе не должна превышать
90 |
0 |
С |
|
||
|
|
, чтобы исключить эффект кавитации. Толщина лопаток от 12 до 25 мм. Основные преимущества гидродинамического |
тормоза: простота конструкции, надежность в работе. Недостатки: незначительный тормозной момент при малой частоте вращения, невозможность автоматического регулирования тормозного усилия по мере увеличения веса колонны. Тормоза этой конструкции применяются в установках грузоподъемностью более 500 кН.
Основные параметры: 1) тормозной момент:
M |
т |
M |
у |
M |
тр |
M |
мех |
|
|
|
|
;
а)
М |
у |
|
|
|
момент, создаваемый жидкостью, циркулирующей в тормозе:
М у |
|
Q g D |
А |
|
|
2 |
; |
||||
|
|
где Q масса жидкости;плотность жидкости;
g ускорение свободного падения;
DА активный диаметр ротора.
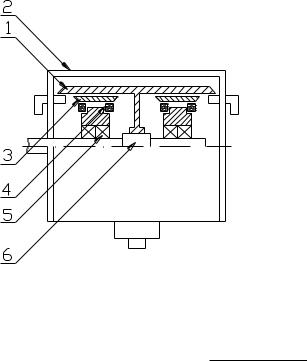
б)
М |
тр |
|
|
|
момент трения воды о поверхность ротора:
|
|
|
|
|
М |
тр |
|
|
|
|
|
|
|
где |
n |
частота вращения ротора. |
||||
|
|
|||||
в) |
M |
мех |
|
момент, создаваемый |
||
|
|
|||||
|
|
|
|
учитывается:
1,2 D |
5 |
n |
2 |
|
A |
; |
|||
|
|
|||
|
|
|
механическими потерями, обычно не
М |
мех |
0 |
|
|
2) тормозной момент можно рассчитать по другой формуле:
М |
т |
|
|
|
(D |
5 |
|
м |
Н |
|||
|
|
D |
|
5 |
) |
В |
|
||
|
|
|
n |
2 |
|
т |
||
|
;
где
3)
|
м |
|
коэффициент гидравлического момента; |
|
|
|
|||
|
|
|
||
DН наибольший активный диаметр ротора; |
||||
D |
В |
|
диаметр, до которого доходит уровень воды |
|
|
|
|
||
|
|
|
|
мощность торможения:
при вращении.
|
|
|
|
|
|
n |
3 |
5 |
|
|
5 |
|
|
|
|
|
|
|
|
|
|
|
|
|
|
N |
т |
M |
т |
|
|
|
(D |
Н |
D |
В |
|
); |
|
|
м |
|
30 |
|
|
|
|
||||
|
|
|
|
|
|
|
|
|
|
|
|
Гидродинамические тормоза всегда работают совместно с ленточными, при этом ленточные тормоза получают ряд преимуществ:
1)облегчение работы ленточного тормоза и бурильщика (гидравлический тормоз поглощает 85% энергии спуска колонны);
2)уменьшается истирание тормозных колодок и рабочих поверхностей тормозных шкивов;
3)снижаются динамические нагрузки и улучшаются условия эксплуатации талевого каната и всего подъемного комплекса. 6.4.ЭЛЕКТРИЧЕСКИЕ ТОРМОЗА По сравнению с механическими и гидродинамическими эти тормоза обладают удобствами
управления, устойчивым режимом работы, легкостью и плавностью перехода из одного режима на другой или полного отключения. Применяют электродинамические тормоза, порошковые электротормоза и электрические генераторы постоянного тока. Возбуждение этих тормозов осуществляется от независимых генераторов постоянного тока, тормозной момент регулируется изменением возбуждения генератора или величины сопротивления в цепи статора возбудителя.
6.5.ЭЛЕКТРОДИНАМИЧЕСКИЙ ТОРМОЗ.Данный тормоз работает в режиме динамического торможения.
1-ротор Т-образный;
2-корпус;
3-статор;
4-обмотка возбуждения;
5-подшипник;
6-вал.
Управляя плотностью магнитного потока можно изменять момент торможения в широких пределах. При возбуждении электромагнитов, расположенных в статоре, при вращении ротора в нем возникает ЭДС, препятствующая его вращению, за счет чего создается момент торможения:
|
|
|
D |
|
2 |
|
|
|
|
М |
|
|
А |
|
В |
З |
|||
|
|
|
|
|
|||||
|
|
|
|
|
|
|
|||
|
т |
|
|
|
|
2 |
|
|
|
|
|
|
|
|
|
|
|
|
где DА активный диаметр ротора;
В удельная сила сцепления в зазоре;
З длина всех активных зазоров.
6.6.ПОРОШКОВЫЙ ЭЛЕКТРОТОРМОЗ
;
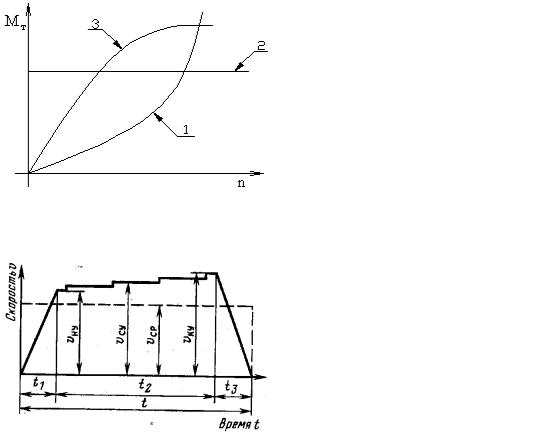
Отличается от электродинамического тормоза тем, что воздушный зазор между статором и ротором заполнен ферромагнитным порошком, который повышает магнитную проницаемость зазора в результате чего повышается величина тормозного момента. В таком тормозе тормозной момент почти не зависит от частоты вращения. Недостаток: износ и истирание порошка, необходимость уплотнения его специальными магнитными сальниками. Данным томозом можно тормозить барабан до полного торможения. Магнитный порошок засыпают во внутреннюю полость через специальное отверстие, частицы диаметром 40…200 мКм.
Тормозной момент:
где
М |
|
2 R |
2 |
B |
|
т |
|
; |
|||
|
|
|
|
||
|
|
|
|
|
|
|
|
|
|
|
напряжение сдвига при заданной величине индукции в зазоре; R средний радиус ротора;
длина всех активных зазоров;
B ширина всех активных зазоров.
Тормозной момент зависит от тока возбуждения и электрической системы и может плавно изменяться от нуля до максимума. Тормозной момент выбирается из следующего условия:
1) для электродинамического тормоза:
|
|
|
|
Мт Мст ; |
где |
М |
ст |
|
статический момент вращения от веса наиболее тяжелой колонны труб. |
|
|
|||
|
|
|
||
2) для |
|
порошкового электротормоза: |
||
|
|
|
|
Мт Мст Мин ; |
где |
М |
ин |
|
вращающий момент от действия инерционных сил при наибольшей массе |
|
|
колонны и угловом замедлении.
На рисунке представлена характерстика тормозов.
1-гидродинамический тормоз;
2-порошковый электротормоз;
3-электродинамический тормоз.
11. Тахограмма подъема бурильного инструмента. Определение машинного времени.
Изменения скорости за время подъема и спуска одной свечи изображаются тахограммой. Для подъемных механизмов характерна трехпериодная тахограмма подъема, имеющая трапецеидальную форму (рис. Х1.9)
Рис. Х1-.9. Тахограмма подъема Рассмотрим подробнее процесс движения талевой системы при СПО для
определения действительной скорости крюка.
Подъем крюка под нагрузкой при помощи лебедки происходит при извлечении колонны из скважины, а без нагрузки - при ее опускании.
Каждый цикл подъема (рис.1) или спуска колонны на длину свечи может состоять из двух или трех периодов: периода разгона tр, в течение которого крюк увеличивает скорость движения; периода установившейся скорости движения tу и периода замедления движения tт до полной остановки. В некоторых случаях период установившегося движения может быть очень
небольшим или отсутствовать кривая (2).
Действительная средняя механическая скорость крюка при подъеме или спуске на длину свечи с учетом разгона и торможения определяется по формуле: υК СР П = h/(tp+tу+tT);
Здесь h – длина хода крюка, м (при расчетах можно принимать h = а*Lc, где Lс—длина свечи, а =1,01÷1,02 –коэффициент, учитывающий отношение хода крюка к длине свечи).
На графиках (рис.1) показаны по два случая подъема и спуска нагруженного крюка. Кривая 1 соответствует большой мощности на крюке и максимальной скорости подъема крюка υк мах п и кривая 2 – недостаточной мощности на крюке при неправильно выбранной максимальной скорости его подъема υ’к мах п но большей, чем скорость υк мах п в первом случае (рис.1). Из этих

диаграмм видно, что во втором случае, вследствие более медленного разгона, время разгона tрп’ и общее время подъема tп’ крюка на длину свечи больше, чем время tрп и tп, достигаемое в первом случае.
Рис 1 Диаграмма (тахограмма) подъема колонны на длину свечи с различными скоростями Действительная механическая скорость крюка при подъеме зависит от длины каната,
наматываемого на первый и последний ряды барабана, и от интенсивности разгона. Она может отличаться от скорости, определенной по среднему ряду навивки каната, на 3 - 8 %. При практических расчетах этой ошибкой можно пренебречь.
Период установившейся скорости движения tу=tп – tрп – tтп, где tп – машинное время подъема колонны на длину свечи, с; tрп – время разгона крюка при подъеме, с; tтп – время торможения при подъеме, с.
Средняя механическая скорость подъема всегда меньше скорости, обеспечиваемой при полной (номинальной) частоте вращения двигателя, из-за невозможности мгновенного пуска и торможения буровой лебедки.
12. Механизация спуско-подъемных операций (СПО). Оборудование и инструмент для СПО.
Буровая установка снабжается комплексом механизмов и инструмента для захвата, подъема, удерживания на весу или на столе ротора бурильной или обсадной колонны при свинчивании и развинчивании труб, извлекаемых или спускаемых в скважину, а также для свинчивания и развинчивания бурильных и обсадных труб при спуско-подъемных операциях. Эти операции осуществляются при помощи элеваторов, клиновых захватов, предохранительных поясов, механических, машинных и круговых ключей.
В практике бурения скважин используются два способа захвата и подвешивания бурильных и обсадных колонн: за заплечик - уступ замка или за тело трубы - за счет ее обжатия.
Элеваторы бывают: корпусные, створчатые, автоматические.
Корпусной элеватор:
1 – корпус;
2 – стопорное устройство;
3 – предохранительная планка;
4 – рукоять;
5 – створка;
6 – пружинная защелка.
Данный элеватор выполняется из стали 40 грузоподъемностью до 120 тонн, и из стали 40 ХН грузоподъемностью более 120 тонн.
Шифр:
ЭК-4’’ 120;
где ЭК – элеватор кованный; 4’’ – диаметр проходного отверстия в дюймах;
40 – материал; 120 – грузоподъемность, т.
Створчатый элеватор:
1,2 – створки элеватора;
3– ось, соединяющая створки;
4– проушины для штропы;
5– ручки;
6 – пружинное стопорное устройство.
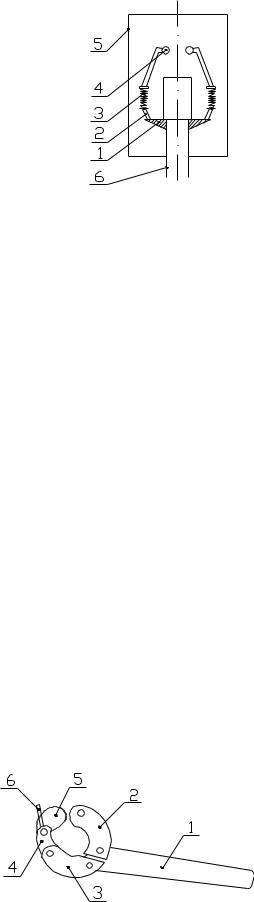
Шифр:
ЭЛ – 4’’
где ЭЛ – элеватор литой; 4’’ – диаметр проходного отверстия в дюймах.
Автоматический элеватор:
1 – клинья;
2 – система рычагов;
3 – пружина;
4 – ролики;
5 – корпус;
6 – свеча.
Шифр: ЭА – автоматический элеватор.
Клиновые захваты. При спуско-подъемных работах и наращивании труб для захвата и подвешивания колонн применяют автоматические клиновые и роторные захваты и ручные клинья.
Клинья поднимаются штоками, в нижней части соединенных бугельным кольцом, с помощью которого они поднимаются или опускаются. Подъем клиньев осуществляется на такую высоту, чтобы они раскрывались и через них свободно прошел замок. Управление клиновым захватом осуществляется сжатым воздухом под давлением 0,6 - 1 Мн/м2 с пульта бурильщика.
По окончании спуско-подъемных операций клинья захвата убирают, а на их место устанавливают в ротор вкладыши ведущей штанги.
Клинья роторные и пояса. Роторные клинья применяют для подвешивания бурильного инструмента на роторе. Они закладываются в конусное отверстие между трубой и вкладышами ротора. Наиболее распространены трехзвенные и многозвенные клинья, в которых корпусы шарнирно соединены.
Корпуса клиновых захватов допускают за счет смены собачек применения клиньев, предназначенных для бурильных труб двухтрех смежных размеров.
13. Инструмент для свинчивания и развинчивания бурильных труб.
Устройства для свинчивания предназначены для захвата бурильных труб и замков одного или нескольких размеров. К ним относятся: механические ключи, приспособления и механизмы для свинчивания и раскрепления резьбовых соединений. В процессе бурения иногда используют комбинированные колонны из труб нескольких диаметров, поэтому смена ключа во время спуска или подъема ее нежелательна, так как занимает много времени.
Крепление и раскрепление осуществляется верхней и нижней частями механических ключей или двумя машинными ключами и пневмораскрепителем. Механические и машинные ключи для облегчения работы с ними подвешиваются в буровой на противовесах. Механизированные ключи с автоматическим захватом, укрепляемые на колонне или шарнирах, выполняются так, чтобы их можно было убирать от оси скважины для того, чтобы не мешать работам во время бурения и других операций.
Процесс свинчивания состоит из:
1)самого свинчивания труб резьбы;
2)докрепления резьбового соединения.
Для предварительного свинчивания труб диаметром 102…140 мм необходим момент 100…500
Н
м
. Для укрепления момент
составляет 1…2
кН м
для труб диаметром 73…102 мм и 2…3
кН м
для труб диаметром 102..140 мм. Чтобы избежать порчу
резьбы частота вращения должна быть не более 60 об/мин и момент не более 0,8…1,2
кН м
. Для раскрепления замков момент
может составлять 10…50 кН м , а иногда до 100 кН м . Ключи могут производить более 100 тыс. свинчиваний и развинчиваний без ремонта. Для докрепления и раскрепления бурильных труб используются машинные ключи. В частности используют ключ УМК (универсальный машинный ключ). В комплекте используют два таких ключа, которые устанавливают на подвесках. Ключ четырехзвенный.
1 – рычаг;
2,3,4,5 – челюсти;
6 – защелка.
Материал изготовления – 40ХЛ; материал пальцев – 40Х.