
Госник
.pdf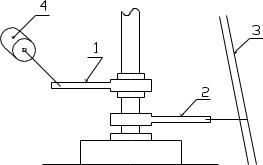
1,2 – ключи;
3 – нога вышки;
4 – раскрепитель.
Ключ АКБ устанавливают между лебедкой и ротором со стороны приводного вала.
Ключ ПКБ подвешивается на канатах, его вставляют в бурильную колонну, развинчивают трубу и возвращают на место.
14.Система автомат спуско-подъема (АСП). Состав оборудования, общие принципы эксплуатации и об-служивания.
Спуск и подъем бурильной колонны - сложный и трудоемкий процесс, зависящий от глубины скважины и числа рейсов долота. Существующие способы и оборудование для автоматизации этого процесса конструктивно сложные и дорогостоящие, поэтому они применяются при бурении скважин глубинной более 4000 м в тех случаях, когда большое число рейсов долота. При незначительном числе рейсов долота и меньшей глубине экономически целесообразнее использовать системы с частичной механизацией.
Для механизации СПО применяют механизмы в различных комбинациях, а для тяжелых условий работы - автоматические системы АСП-3М. В механизированных системах используются обычные талевые системы и СПО ведутся без совмещения по времени отдельных операций. При системах АСП-3М совмещаются операции спуска ненагруженного элеватора с отвинчиванием и уборкой свечи при спуске бурильной колонны или подачи к ротору и свинчивание свечей. Это требует применения более широких кронблока и талевого блока, а также усложняет монтаж вышки.
Комплекс механизмов АСП-3М
Применение АСП-3М значительно облегчает труд рабочих при СПО в процессе бурения глубоких скважин и ускоряет эти работы.
АСП обеспечивает:
совмещение по времени спуско-подъема колонны бурильных труб и ненагруженного элеватора с установкой свечи на подсвечник, выносом ее с подсвечника, а также с операциями по свинчиванию и развинчиванию свечи; механизацию свинчивания и развинчивания бурильных труб; механизацию установки свечей на подсвечник и вынос их к центру скважины;
автоматизацию управления элеватором при захвате и освобождении им колонны бурильных труб; механизацию закрепления колонны бурильных труб в роторе,
Для совмещения операций при подъеме и спуске колонн применяется специальная талевая система, состоящая из талевого блока, автоматического элеватора и приспособления для захвата вертлюга. Талевый блок отличается от обычного тем, что две секции шкивов раздвинуты относительно вертикальной оси и соединены траверсой, позволяющей спускать и поднимать его по свече; в это время соединение развинчивается или свинчивается ключом АКБ. Такая схема позволяет интенсифицировать работы путем совмещения во времени операции подъема и спуска загруженного и незагруженного талевого блока с операциями свинчивания и развинчивания свечи, установки ее на подсвечник и переноса с подсвечника к центру скважины.
Установка АСП-3М состоит из пульта управления, талевого блока, автоматического элеватора; пневматического роторного клинового захвата, ключа АКБ-3М2, центратора для удержания свечей в вертикальном положении, механизма захвата свечи, механизмов подъема свечи и переноса свечи.
Свечи устанавливаются на подсвечники, а верхняя их часть заводится в магазины, удерживающие свечи в определенном порядке на подсвечнике. Наверху буровой установлены кронблок с дополнительным шкивом и два приспособления для закрепления направляющих канатов центратора.
Управление механизмами АСП-3М осуществляется с поста бурильщика, на котором находятся несколько пультов: пульт бурильщика, на котором выполняются обычные операции и управление пневматическим клиновым захватом; пульт управления, откуда помощник бурильщика управляет ключом АКБ-3М2;
пульт, с которого рабочий управляет командоаппаратами электродвигателей передвижения тележки и стрелы механизма захвата свечи, а также пневматическим цилиндром механизма подъема свеч.
Тележка механизма расстановки свечей управляется автоматически с помощью сельсинно-следящей системы. Передвижение тележки и стрелы механизма захвата свечи сблокировано с движением талевого блока таким образом, что исключается возможность столкновения блока с механизмом захвата свечи.
15.Оборудование циркуляционной системы буровой установки. Функции и взаимосвязь.
Предназначена для промывки скважины путем многократной принудительной циркуляции. Замкнутая циркуляция имеет ряд преимуществ:
1)экономическая выгода благодаря сокращению расхода химических компонентов и других ценных материалов;
2)предотвращение загрязнения окружающей среды стоками бурового раствора.
Циркуляционная система предназначена для выполнения следующих функций: 1) регулирование физико-механических свойств раствора;
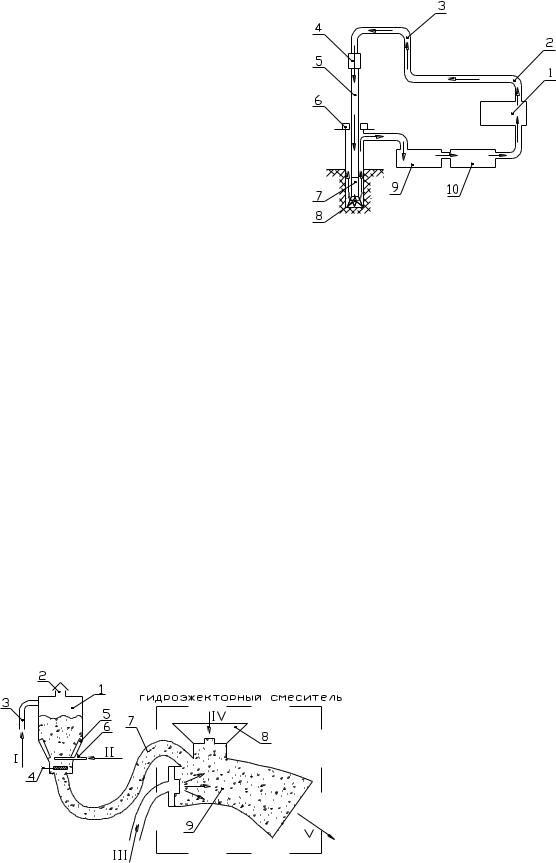
2)подвод гидравлической энергии к забойным двигателям;
3)подвод гидравлической мощности к долоту;
4)подача в буровую колонну необходимого количества раствора;
5)создание непрерывной циркуляции жидкости;
6)приготовление бурового раствора;
7)очистка бурового раствора.
Схема циркуляционной системы:
1-буровой насос;
2-нагнетательная линия;
3-стояк;
4-вертлюг;
5-буровая колонна;
6-ротор;
7-забойный двигатель;
8-долото;
9-система для очистки раствора;
10-система для приготовления раствора.
Буровые растворы должны выполнять следующие функции:
1)облегчать разрушение горной породы но не усиливать разрушение оборудования и инструмента;
2)эффективно очищать забой скважины;
3)транспортировать выбуренный шлам на дневную поверхность, удерживая его во
взвешенном состоянии и не размывая стенок скважины;
4)компенсировать избыточное пластовое давление, но не допускать поглощения раствора отдельными пластами.
5)укреплять стенки скважины в неустойчивых породах, но при этом не ухудшать проницаемость горизонта.
6)обеспечивать прокачивание буровыми растворами;
7)обладать свойством осаждать песок и шлам после выноса их из скважины;
8)смазывать и охлаждать долото и оборудование.
ОБОРУДОВАНИЕ ДЛЯ ПРИГОТОВЛЕНИЯ РАСТВОРА.
Процесс приготовления раствора состоит из трех основных операций:
1)приготовление основы раствора из воды и глины, соляро-битуумного раствора, или водо-нефтяной эмульсии;
2)добавление порошкообразных барита или гематита с целью повышения плотности;
3)обработка раствора химическими реагентами с целью регулирования и стабилизации основных его свойств . Оборудование для приготовления раствора по принципу действия делится намеханическое и гидравлическое.
БЛОК ПРИГОТОВЛЕНИЯ БУРОВОГО РАСТВОРА (БПР).
Предназначен для хранения на буровой запаса глинопорошка и приготовления из него растворов. Существуют 3 вида БПР:
БПР-100 (2 бункера для хранения по 50
БПР-70 (2 бункера для хранения по 35
БПР-50 (2 бункера для хранения по 25
М3
М3
М |
3 |
|
);
);
).
1-бункер;
2-воздушный фильтр;
3-трубопровод для подачи порошка;
4-разгрузочное устройство;
5-система аэрирования;
6-аэродорожки;
7-шланг; 8-воронка;
9-камера смешивания.
I – подача глинопорошка из цементовоза; II – подача воздуха для аэрирования;
III – подача жидкости из насоса; IV – ручная подача глинопорошка;
V –подача готового раствора в циркуляционную систему.
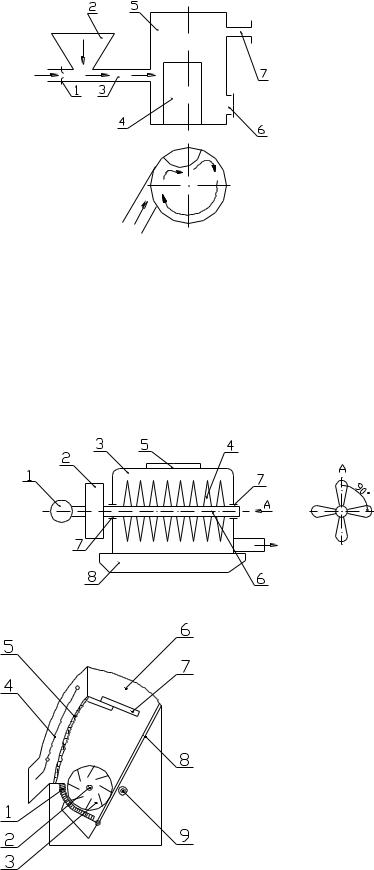
ГИДРОМЕШАЛКИ.
1-сопло;
2-воронка;
3-камера смешивания;
4-отбойник;
5-емкость;
6-люк для очистки;
7-отвод.
Производительность 70…90 |
М |
3 |
/ час |
, объем воронки 0,175 |
|
||||
|
|
|
ГЛИНОМЕШАЛКИ.
М |
3 |
|
, объем емкости 1
М |
3 |
|
.
Производительность: комовая глина 2…4 м3/час; глинопорошок 6 м3/час. Камера смешивания до 4 м3, частота вращения 37…174 об/мин, мощность электродвигателей 2…22 кВт. По конструкции бывают одновальные и двухвальные . Вал имеет
|
90 |
0 |
|
рабочие лопасти под углом |
друг к другу, зазор между концами лопастей и стенками корпуса 30…35 мм. Преимущества: |
||
|
достаточная надежность, высокое качество выполнения операций, простота конструкции. Недостатки: малая производительность, затрудненный доступ внутрь мешалки для выполнения ремонта и очистки, заклинивание и поломка лопастей при попадании вместе с комовой глиной камней; уменьшение рабочего объема при налипании глины на стенки.
1-двигатель;
2-понижающий редуктор;
3-камера;
4-лопасть;
5-люк для засыпки глины;
6-вал;
7-подшипник;
8-рама.
ФРЕЗЕРНО-СТРУЙНЫЕ МЕЛЬНИЦЫ.
1-рифленая плита;
2-вал;
3-ротор;
4-ограждение;
5-сетка;
6-бункер;
7-выдвигающаяся плита;
8-откидная крышка;
9-штифт.
ОБОРУДОВАНИЕ ДЛЯ ОЧИСТКИ БУРОВОГО РАСТВОРА. Процесс очистки заключается в удалении из раствора частиц выбуренной породы, ила или газа. Своевременная и качественная очистка раствора повышает:
1)долговечность узлов бурового оборудования;
2)эффективность процесса бурения.
Для очистки бурового раствора применяют два вида устройств:
1)устройства для механической очистки с использованием вибросит;
2)устройства, в которых разделение твердых частиц из жидкости происходит за счет центробежных сил.
Схема расположения оборудования для очистки:
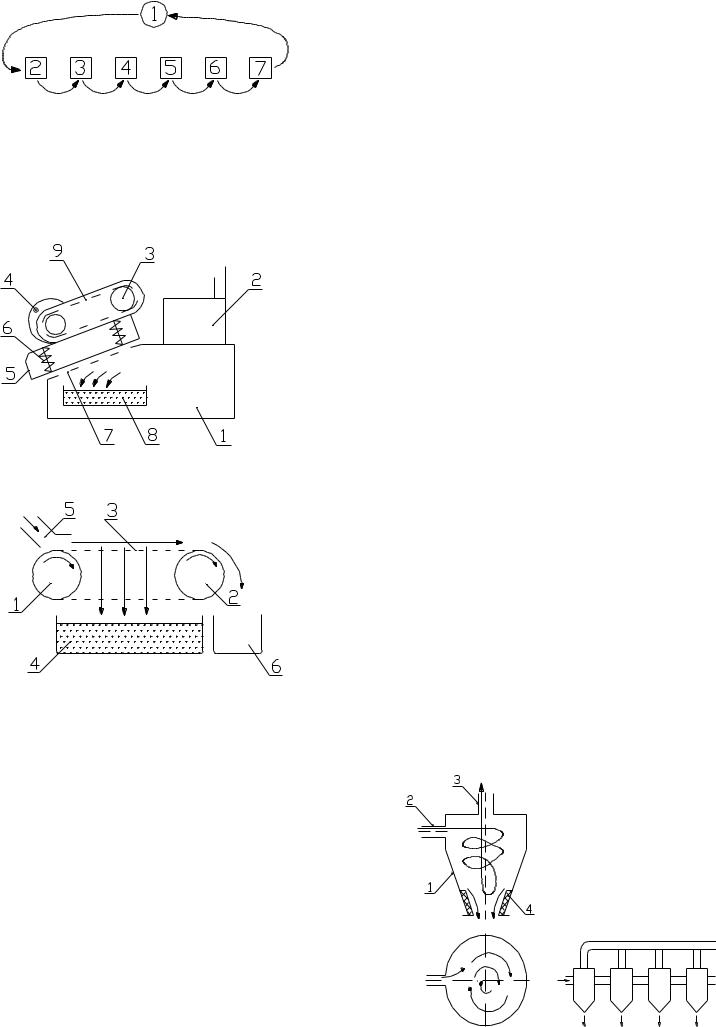
1-скважина;
2-первоначальное вибросито;
3-пескоотделитель;
4-пескоотделитель гидроциклонный;
5-илоотделитель;
6,7-сепараторы центрифуги.
При идеальной отчистке раствора из него должны быть удалены твердые частицы размером более 1 мкм; частиц вибросита > 150 мкм; размер частиц гидроциклона > 40 мкм; гидроциклонные илоотделители очищают до 90% частиц > 25 мкм; центрифуги > 10 мкм ВИБРОСИТА Оборудование первой (грубой) ступени отчистки. Потеря растворов неутяжеленного не более 0,2%,
утяжеленных растворов – 0,1%. Качество отчистки зависит от типа и состояния вибрирующей сетки, которая выполняется из |
|
нержавеющей стали, диаметр проволоки 0,13…0,33 мм. Размер ячеек: квадратное 0.16, 0.2, 0.25, 0.9, 1.6, 2, прямоугольное 1 |
|
2.3, 1
5 мм.
1-рама;
2-желоб;
3-двигатель;
4-вал с эксцентриком;
5-вибрирующая рама;
6-пружинный амортизатор;
7-сетка;
8-емкость для сбора отчищенного раствора; 9-клиноременная передача.
Пропускная способность до 60 л/сек, частота вибрации сетки 1600…2000 кол/мин, наклон сетки 12…18 градусов.
1,2-вал барабана;
3-бесконечная сетка;
4-емкость для сбора отчищенного раствора;
5-желоб;
6-емкость для сбора шлама.
СИТОКОНВЕЕР. Достоинства:
1)простота конструкции;
2)отсутствие потребления электроэнергии;
3)повышенная долговечность сетки. Недостатки:
повышенная потеря раствора вследствие промывки сетки водой. ГИДРОЦИКЛОНЫ. Оборудование второй ступени отчистки. Принцип действия инертно-гравитационный.
1-конусообразный корпус;
2-трубопровод;
3-отвод для отчищенного раствора;
4-резиновая насадка.
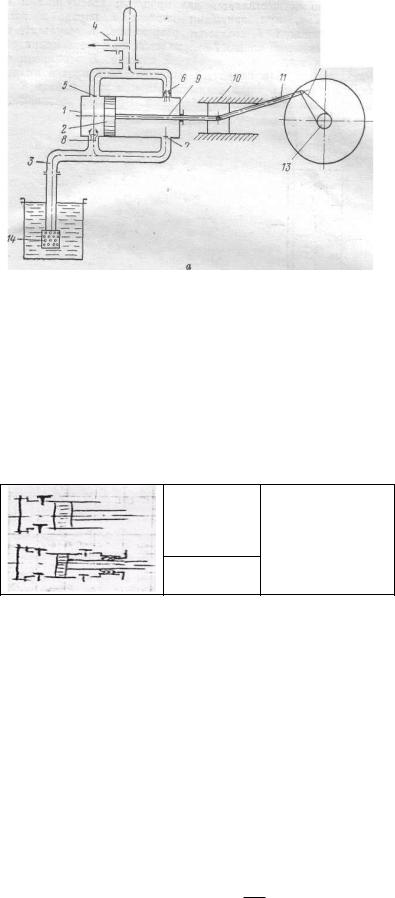
16. Назначение, условия работы и классификация буровых насосов. Современные конструкции.
БН предназначен для нагнетания бур.раствора в скважину.
Требования к БН: 1 возможность регулирования подачи в пределах, обеспечивающих эффективность промывки; 2 - мощность БН должна быть достаточной для промывки скв. и работы забойного двигателя; 3 - обеспечение минимально возможных инерционных нагрузок и пульсаций давления; 4 - долговечность узлов и деталей; 5 - защита элементов приводной части от промывочной жидкости и грязи; 6- удобство в обслуживании и возможность быстрой замены изнашиваемых деталей; 7 - возможность транспортирования и перемещения в собранном виде; 8 - экономичность и безопасность в работе.
Поршневой насос двойного действия:
1 — цилиндр; 2— поршень; 3— всасывающий 4 - нагнетательный трубопровод; 5, 6-нагнетательныеклапкны; 7,8-всасывающие клапаны;9-шток; 10-крейцкопф;11 — шатун, 12 — кривошип; 13 — кривошипный-вал; 14-фильтр
Классификация БН:
1)по приводной мощности: а) малой мощности до 200 кВт: б) средней 200 – 400 кВт: в) большой свыше 400 кВт;
2)по принципу действия при вытеснении жидкости: а) одностороннего (простого) действия; б) двухстороннего (двойного)
действия; по числу цилиндров насоса: а)двухцилиндровые;б) трехцилиндровые.
В качестве буровых насосов применяются горизонтальные, поршневые насосы с двумя цилиндрами двойного действия (дуплексы) и тремя цилиндрами простого действия (триплексы).
Поршни бывают цельными и сборными.
Простого действия Поршень
триплекса=1/2
поршня дуплекса
Двойного
действия
Угол м/у эксцентриком у дуплекса 900, а у триплекса 1200. Преимущества 3-х цил. Перед 2-х цил.
1.Лучшая гидр. хар-ка, обусловленная меньшей неравномерностью подачи.
2.Проще конструкция гидравлической части (отсутствуют уплотнения штока и пара клапанов).
3.Меньше масса насоса (у насосов большой мощности)
Недостатки:1-более сложная конструкция приводной части.2-увеличивается ск-ть перемещения поршня => а) повышается износ трущихся деталей, б) ухудшение гидр. хар-ки. 3 - необходимость установки подпорного насоса. 4 - необходимость смазывания поверхностей поршня и цилиндра (требует установки масляного насоса)
17.Расчет и выбор рабочих и конструктивных параметров бурового насоса. Регулирование режима рабо-ты.
1)суммарная мощность насоса:
|
|
N |
Q |
C |
|
|
C |
|
|
где |
QC |
суммарная подача; |
|
|
|
|
|
pH давление нагнетания.
2) полезная мощность одного насоса:
pH
;
NH NC z ;
где z – число применяемых насосов.

3) мощность двигателей ,которые приводят в действие насос:
N |
|
|
N |
|
|
H |
|
||
|
|
|
|
|
|
Д |
|
|
|
|
|
|
|
|
|
|
|
H |
; |
|
|
|
|
4) наибольший крутящий момент, развиваемый двигателем:
M |
k |
Д |
М |
Д |
u |
ДН |
P |
|
|
|
где k Д коэффициент перегрузки двигателя;
Д
;
МД
uДК
|
номинальный крутящий момент; |
|
передаточное отношение от двигателя к приводному валу насоса;
|
Д |
|
к.п.д. двигателя. |
|
|
||
|
|
|
РАСЧЕТ ШТОКА. Штоки насосов одностороннего действия расчитываются на сжатие и продольную прочность, двухстороннего действия дополнительно расчитываются на растяжение.
1) усилие растяжения без учета сил трения:
Р |
р |
(F |
РАСТ |
МАХ |
|
f
)
;
где F и f – площади поршня и штока соответственно. 2) усилие сжатия без учета сил трения:
|
P |
|
р |
МАХ |
F |
|
|
|
|
|
|
|
|
|
|
|
|
|
|
|||
|
CЖ |
|
|
|
|
|
|
|
|
|
|
|
|
|
|
|
|
|
|
|||
3) усилие растяжения с учетом сил трения: |
d |
|
|
|
|
|
|
|
|
|
|
|
||||||||||
|
|
|
|
|
|
|
|
D |
|
|
|
|
|
|
|
|
|
|
|
|||
|
|
|
|
|
|
|
|
2 |
|
|
|
2 |
|
|
|
|
|
|
|
|
|
|
P |
|
|
p |
|
|
|
( |
|
|
|
|
D |
1 |
k |
C |
d |
2 |
) |
||||
PACT |
|
|
MAX |
|
|
4 |
|
|
|
|
|
|
|
|
||||||||
|
|
|
|
|
|
|
|
|
|
|
|
|
|
|
|
|
|
|
|
|
||
4) усилие сжатия с учетом сил трения: |
|
|
|
|
|
|
|
|
|
|
|
|
|
|
|
|
||||||
|
|
|
|
|
|
D |
2 |
|
|
|
|
|
|
|
|
|
|
|
|
|
|
|
P |
р |
|
|
|
( |
D |
|
k |
|
d |
|
|
) |
|
|
|
|
|||||
МАХ |
|
1 |
C |
2 |
|
|
|
|
||||||||||||||
СЖ |
|
|
|
4 |
|
|
|
|
|
|
|
|
|
|
|
|||||||
|
|
|
|
|
|
|
|
|
|
|
|
|
|
|
|
|
|
|
|
|
где
1 |
и |
2 |
-длины уплотнения поршня и сальника соответственно; |
|
|
коэффициент трения между резиной и металлом, уплотнением поршня и штока; |
|||
|
|
k |
|
|
|
|
|
|
|
C |
|
коэффициент среднего давления уплотнения на шток. |
|||||
|
|
||||||
5) напряжение сжатия: |
|
|
|
|
|
||
|
|
CЖ |
|
РСЖ |
|||
|
|
|
f |
|
|||
|
|
|
|
|
|
||
6) напряжение растяжения: |
|
|
|
|
|
||
|
|
|
|
|
P |
||
|
|
|
|
PACT |
|||
|
|
|
|
|
|
||
|
|
|
PACT |
|
|
f |
|
|
|
|
|
|
|
РАСЧЕТ ПРИВОДНОЙ ЧАСТИ. Усилие сжатия, действующее вдоль оси шатуна:
T |
|
P |
|
C |
|
||
|
|
|
|
C |
|
cos |
|
|
|
; |
|
|
|
|
где угол наклона шатуна в процессе работы;
P |
|
C |
нагрузка сжатия. |
|
РАСЧЕТ ШТОКОВ НА ПРОДОЛЬНУЮ ПРОЧНОСТЬ. 1) гибкость штока:
|
Ш |
|
105 |
|
iMIN |
||||
|
; |
где Ш длина штока;
iMIN минимальный радиус действия штока:
iMIN |
|
|
I |
|
||
|
|
|
|
|||
f ; |
||||||
|
|
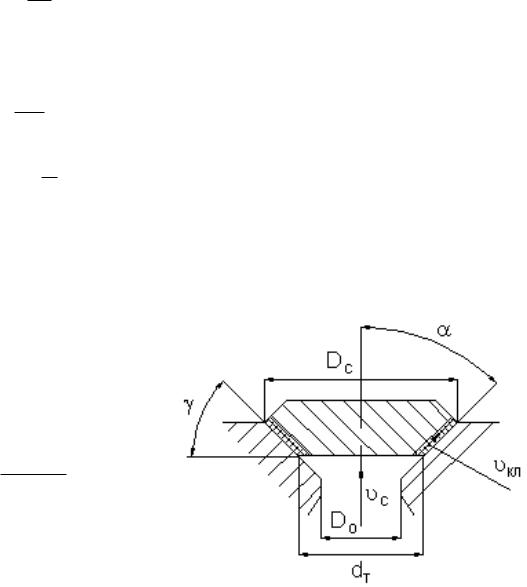
где |
f |
площадь штока; |
I |
|
|
момент инерции: |
|
|
|
|
|
|
|
|
|
d |
|
|
|
|
|
|
|
|
|
4 |
|
|
|
|
|
|
I |
|
64 |
|
|
|
|
|
|
|
|
|
|
|
2) критическая сила сжатия штока: |
|
|
|
Е I |
|
|
|||
|
|
|
|
2 |
|
|
|||
|
|
|
|
|
|
|
|
|
|
|
|
Р |
|
|
|
2 |
|
; |
|
|
|
КР |
|
|
|
|
|
|
|
|
|
|
|
|
Ш |
|
|
|
|
|
|
|
|
|
|
|
|
|
|
где |
Е |
модуль упругости материала штока |
|
|
|
|
|||
|
|
|
|
|
3) коэффициент запаса прочности:
.
если
n PKP P
СЖ ;
105 |
|
KP |
335 0,6 |
(для углеродистых сталей); |
, то |
|
|
|
KP 470 2,3 (для сталей с содержанием никеля 5%)
n |
|
KP |
|
||
|
|
|
|
|
|
|
СЖ |
При расчете составных штоков к длине штока добавляется эквивалентная длина штока-ползуна (контршток):
|
|
|
|
( |
d |
|
Э |
ШП |
d |
||||
|
|
|
||||
|
|
|
|
|
||
|
|
|
|
|
1 |
где |
|
ШП |
|
длина штока-ползуна; |
|
|
|||
|
|
|
|
d |
|
|
диаметр штока; |
||
d |
диаметр штока-ползуна. |
|
1 |
||
|
Тогда расчетная длина:
) |
2 |
|
;
|
Р |
|
Ш |
|
Э |
|
|
|
РАСЧЕТ КЛАПАНОВ.
Основные размеры клапанов зависят от подачи и числа двойных ходов поршня. Высота подъема клапана определяется скоростью потока жидкости в клапанном отверстии.
1)критерий, определяющий степень опасности возникновения стука:
|
|
|
D |
|
2 |
D |
|
2 |
|
k |
|
|
k |
|
0 |
|
|
||
|
|
|
|
|
|
||||
|
|
|
|
|
|
|
|
||
|
CT |
|
D |
|
2 |
cos |
|
|
|
|
|
|
0 |
|
; |
||||
|
|
|
|
|
|
|
|
||
|
|
|
|
|
|
|
|
|
|
D |
|
|
|
где |
k |
|
|
диаметр клапана; |
|
|
|
||
|
D0 |
|
диаметр отверстия в седле; |
|
|
|
|
||
|
угол наклона посадочной поверхности клапана |
|||
|
|
|||
|
|
(30…60 градусов). |
|
k |
0,5 |
|
k |
CT |
0,4 |
|
При |
CT |
|
для воды и |
|
|
для вязких растворов |
|
|
|
|
|
|
|||
стук отсутствует. |
|
|
|
|
|
||
2) сила, действующая на тарель закрытого клапана: |
PK |
|
p |
|
D 2 |
||
H |
|
|
K |
|
||
|
|
|
|
|||
|
|
|
4 |
; |
||
где pH давление на выходе или давление нагнетания |
||||||
3) момент изгиба тарели клапана: |
|
|
|
|
|
|
M |
|
p |
d |
2 |
(3 ) |
|
H |
T |
|
||||
|
|
|
|
|
||
T |
|
|
64 |
|
|
|
|
|
|
; |

где
4)
d |
|
|
||
T |
|
|
диаметр тарели по минимальному контуру; |
|
|
|
|||
коэффициент Пуассона или модуль упругости. |
||||
|
|
максимальное напряжение изгиба тарели при опрессовке:
|
|
|
6 M |
T |
|
|
|
|
|||
|
|
|
|
|
|
|
ИЗГ |
|
|
2 |
|
|
|
|
|
|
|
|
|
|
T |
|
|
где |
|
Т |
|
толщина тарели |
|
|
|||
|
|
|
|
Запас прочности:
;
S |
|
|
|
T |
3 |
|
|
||||
|
|
|
|
|
|
|
T |
|
|
|
|
|
|
|
|
|
|
|
|
|
ИЗГ |
|
5) сила гидродинамического воздействия:
где
где
PГ Q ( C КЛ sin ) ;
Q |
|
|
|
|
|
|
||
|
|
расход жидкости через клапан: |
|
|
|
|||
|
|
|
Q |
C |
F |
|
F |
|
|
|
|
|
C |
КЛ |
КЛ |
||
|
|
|
|
|
|
|
|
; |
|
С |
|
скорость течения жидкости через сечение; |
|
||||
|
|
|
||||||
|
|
|
|
КЛ скорость истечения через клапан;
F |
|
|
|
|
||
C |
|
|
площадь сечения седла; |
|||
|
|
|
||||
F |
|
|
|
|
||
КЛ |
|
|
|
площадь общего суммарного сечения зазора; |
||
|
|
|||||
|
|
отклонения потока жидкости; |
||||
|
угол |
|||||
плотность жидкости. |
||||||
|
|
6) высота подъема клапана определяется из условия безударной посадки тарели на седло клапана:
hMAX
n
1200...1300
;
где
hMAX
допускаемая высота подъема клапана;
n частота ходов поршня.
7) площадь проходного сечения у горловины конического седла при полном открытии:
f |
d |
h |
MAX |
sin |
ПР |
КЛ |
|
|
РЕГУЛИРОВАНИЕ БУРОВЫХ НАСОСОВ Регулирование может производиться:
1)изменением подачи и давления нагнетания применением сменных цилиндровых втулок;
2)изменением числа двойных ходов поршня в минуту :
а) применением сменных шкивов. Недостатки такого способа:
-ступенчатое изменение скоростей и невозможность регулирования на ходу;
-трудоемкость работ при замене шкива и необходимость его регулировки;
-снижение долговечности ремней в результате уменьшения диаметра шкива.
б) изменение скорости вращения электродвигателя, применяются дополнительные системы:
-генератор-двигатель;
-каскад Кремера;
-вентильный каскад.
1 – асинхронный или синхронный двигатель, работающий от сети; 2 – генератор постоянного тока;
3 – приводной двигатель;
4 – шкив
18. Элементы обвязки бурового насоса: назначение, особенности конструкции.
Сетка (фильтр), устанавливаемая на конце всасывающего трубопровода, предназначена для предохранения насоса от попадания в него посторонних предметов (щепок, тряпок и др.). Суммарная площадь всех отверстий приемной сетки должна в 3—4 раза превышать площадь поперечного сечения всасывающей трубы. Целесообразно для приемной линии применять резиновый рукав диаметром 250 мм. Это устраняет передачу вибраций от насоса, предупреждает расстройство герметичности соединений и сокращает время монтажных работ.
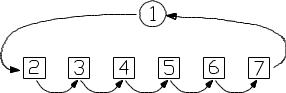
Нагнетательный трубопровод предназначается для подачи промывочного раствора от насоса к стояку в буровой вышке. Нагнетательный трубопровод должен быть прямым, герметичным и доступным для осмотра. Сваривается трубопровод из бурильных труб диаметром 168, 141 и 114 мм.
Воздушные колпаки и компенсаторы. Как уже говорилось ранее, неравномерность движения поршня приводит к пульсации потока, к резким колебаниям давления, что в свою очередь вызывает вибрацию насоса напорных трубопроводов, разрыв сварных швов, буровых рукавов и других элементов. Для смягчения толчков применяются воздушные колпаки, устанавливаемые на тройнике нагнетательного блока насоса. В начале работы насоса воздух, заполняющий колпак, под давлением жидкости сжимается до объема, соответствующего рабочему давлению, образуя воздушную подушку. При каждом толчке жидкости происходит дополнительное сжатие подушки и в колпак поступает дополнительное количество жидкости.
При замедлении движения поршня давление несколько снижается и сжатый воздух, расширяясь, выталкивает часть жид-|кости в напорный трубопровод. Таким образом, подача жидкости, а следовательно, и давление становятся более равномерными. Компенсатор — весьма ответственный узел в схеме обвязки буровых насосов и должен отвечать правилам котлонадзора. Компенсатор устанавливают на специальный фундамент, по одному-два на каждый насос. Нижнее отверстие служит для слива раствора, верхнее — для прочистки компенсатора. Давление воздуха на компенсаторе контролируется манометром, устанавливаемым на высоте 2400 мм.
Стояки, соединяющие напорную линию насосов с буровым шлангом, изготовляются из 114или 168-лш. бурильных труб и устанавливаются непосредственно у буровой вышки, по одному или по два на одной буровой. Для соединения бурового шланга со стояком в верхней его части имеется отвод с фланцем.
Непосредственное соприкосновение промывочной жидкости со сжатым воздухом приводит к постепенному поглощению раствором воздуха, находящегося в компенсаторах, и к уменьшению воздушной подушки.
Буровые насосы снабжаются предохранительными клапанами двух типов: диафрагменными и гвоздевыми. Предохранительные клапаны устанавливаются на отводе от нагнетательного патрубка.
Корпус диафрагменного предохранительного клапана укрепляется на тройнике напорного трубопровода. Преимущества описываемой конструкции клапана перед другими заключаются в следующем:
1)диафрагма легко устанавливается и снимается без отсоединения отводной трубы;
2)благодаря удобному расположению посадочных поверхностей под диафрагму перед установкой ее можно проверить состояние этих поверхностей;
3)при замене диафрагмы не приходится снимать тяжелые детали с клапана.
Запорная арматура. В схему обвязки буровых насосов входит запорная арматура различных типов.
Задвижка на всасывающем трубопроводе устанавливается только в тех случаях, когда установка насоса произведена «под залив». Задвижки на нагнетательной линии устанавливают преимущественно сварные, высокого давления, которые в настоящее время выпускают с приспособлением, позволяющим определить положение задвижки.
Контрольная задвижка устанавливается на выкидной линии, которая направлена в приемную емкость. Открывается задвижка перед пуском насоса. После этого постепенным перекрытием контрольной задвижки промывочную жидкость направляют в скважину.
19. Состав и схема расположения оборудования для очистки промывочной жидкости. Устройство и принцип работы гидроциклона.
Процесс очистки заключается в удалении из раствора частиц выбуренной породы, ила или газа. Своевременная и качественная очистка раствора повышает:
3)долговечность узлов бурового оборудования;
4)эффективность процесса бурения.
Для очистки бурового раствора применяют два вида устройств:
3)устройства для механической очистки с использованием вибросит;
4)устройства, в которых разделение твердых частиц из жидкости происходит за счет центробежных сил. Схема расположения оборудования для очистки:
1-скважина;
2-первоначальное вибросито;
3-пескоотделитель;
4-пескоотделитель гидроциклонный;
5-илоотделитель;
6,7-сепараторы центрифуги.
При идеальной отчистке раствора из него должны быть удалены твердые частицы размером более 1 мкм; частиц вибросита > 150 мкм; размер частиц гидроциклона > 40 мкм; гидроциклонные илоотделители очищают до 90% частиц > 25 мкм; центрифуги > 10 мкм.
ВИБРОСИТА Оборудование первой (грубой) ступени отчистки. Потеря растворов неутяжеленного не более 0,2%, утяжеленных растворов – 0,1%. Качество отчистки зависит от типа и состояния вибрирующей сетки, которая выполняется из нержавеющей стали, диаметр проволоки 0,13…0,33 мм. Размер ячеек: квадратное 0.16, 0.2, 0.25, 0.9, 1.6, 2, прямоугольное 1 2.3, 1 5 мм.
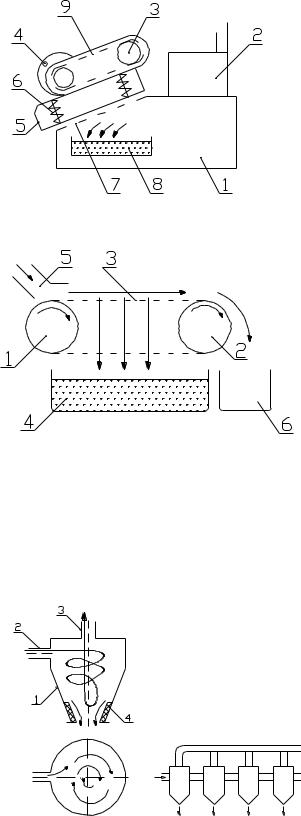
1-рама;
2-желоб;
3-двигатель;
4-вал с эксцентриком;
5-вибрирующая рама;
6-пружинный амортизатор;
7-сетка; 8-емкость для сбора отчищенного раствора;
9-клиноременная передача.
Пропускная способность до 60 л/сек, частота вибрации сетки 1600…2000 кол/мин, наклон сетки 12…18 градусов.
СИТОКОНВЕЕР.
1,2-вал барабана;
3-бесконечная сетка;
4-емкость для сбора отчищенного раствора;
5-желоб;
6-емкость для сбора шлама.
Достоинства:
4)простота конструкции;
5)отсутствие потребления электроэнергии;
6)повышенная долговечность сетки. Недостатки:
повышенная потеря раствора вследствие промывки сетки водой.
ГИДРОЦИКЛОНЫ.
Оборудование второй ступени отчистки. Принцип действия инертно-гравитационный.
1-конусообразный корпус;
2-трубопровод;
3-отвод для отчищенного раствора;
4-резиновая насадка.
Естественный и механический способы не обеспечивают хорошей степени очистки от выбуренной породы высококачественных растворов. Для очистки таких промывочных жидкостей используют гидроциклонные установки.
Гидроциклон (рис) состоит из стального сосуда, верхняя часть которого имеет цилиндрическую, а нижняя - коническую формы. Раствор под давлением 0,15—0,3 Мн/м2 поступает по тангенциальному вводу в гидроциклон и приобретает вращательное движение вокруг вертикальной оси. Под действием центробежной силы тяжелые частицы отбрасываются к стенке гидроциклона, опускаются в нижнюю часть конуса и выходят наружу через выпускной патрубок, а очищенный раствор с более легкими частицами направляется к оси циклона и подается во всасывающую линию бурового насоса.