
Лабораторна робота1
.pdfЛабораторна робота № 1
ДОПОМІЖНІ ОПЕРАЦІЇ ПРИ ВИГОТОВЛЕННІ ЛІКАРСЬКИХ ЗАСОБІВ. ВИГОТОВЛЕННЯ ТВЕРДИХ ЛІКАРСЬКИХ ЗАСОБІВ (ПОРОШКІВ). (4 год)
Мета роботи: вивчення властивостей порошкоподібних лікарських субстанцій і визначення ролі різних властивостей сипких речовин у технологіях одержання твердих лікарських форм; ознайомлення з допоміжними операціями подрібнення, просіювання та змішування, які застосовують у фармацевтичній промисловості, опанування методів ситового аналізу та складання матеріального балансу за стадіями приготування порошків, експрес-аналізу лікарського засобу.
Матеріали та обладнання: кульковий млин, сита з діаметром отворів 0,2, 0,25, 0,3, 0,5 мм; секундомір; ваги технічні; ступки з пестиками; пробірки на 10 см3, пробіркоутримувачі, штативи для пробірок; цукор, камфора, спирт етиловий, кислота борна, порошок оксиду цинку, тальк; компоненти для приготування солі карловарської штучної (див. додаток), реактиви для проведення експрес-аналізу компонентів солі карловарської штучної (додаток).
Загальні відомості Правила роботи і техніки безпеки в лабораторії. Перед початком
виконання лабораторної роботи кожен студент повинен ознайомитися з технікою безпеки у біотехнологічній лабораторії і поставити свій підпис у журналі з техніки безпеки.
Виконання лабораторних робіт проводять у чистих халатах, волосся слід підібрати. Кожен студент працює на постійному місці, виконує завдання індивідуально. На робочому місці потрібно підтримувати зразковий порядок. Особисті речі повинні зберігатися в спеціально відведеному місці.
У лабораторії забороняється вживати напої та їсти. Після закінчення роботи студент повинен упорядкувати робоче місце, руки необхідно ретельно вимити, а за потреби обробити дезінфікуючим розчином. Слід мати індивідуальний рушник або серветки для витирання.
Виготовлення складних порошків.
Порошки – тверда лікарська форма для зовнішнього та внутрішнього застосування, що складається з однієї чи декількох подрібнених речовин та має властивість сипучості. На відміну від простих, складні порошки складаються із декількох інгредієнтів.
Порошки – одна з найбільш древніх лікарських форм, що застосовувалася в медичній практиці ще за 2,5 – 3 тис. років до н. е. і не втратила значення дотепер. Порошки є компонентами майже усіх лікарських форм, так як їх основною перевагою являється зручність введення до лікарської форми та простота в зберіганні й перевезенні, більшість з них
легко подрібнюються без допоміжних засобів, змішуються до утворення однорідної консистенції. Класифікують порошки за ступенем подрібнення, що виражається розміром отворів сита, через яке повністю просіюється порошок.
До переваг порошків як лікарської форми можна віднести:
простоту приготування, точність дозування;
універсальність складу (у формі порошків можна сполучити різні за складом і властивостями лікарські речовини);
зручність зберігання і транспортування.
Недоліки порошків:
повільніша терапевтична дія порівняно з рідкими лікарськими формами;
незначний термін зберігання через велику питому поверхню (легко втрачають або поглинають воду, окиснюються тощо);
незручність прийому пахучих речовин, забарвлених і тих, що мають неприємний смак;
подразнююча дія на слизову оболонку шлунково-кишкового тракту. Вивчення різноманітних властивостей порошкоподібних лікарських
речовин (лікарських субстанцій) необхідне для подальшого вивчення технологій одержання твердих лікарських форм, зокрема таблеток, так як ці властивості визначають раціональний спосіб гранулювання та таблетування останніх.
Порошкоподібні лікарські субстанції можна охарактеризувати за такими основними властивостями – фізико-хімічні та технологічні.
Фізико-хімічні властивості.
Форма і розмір часточок. Порошкоподібні лікарські субстанції є грубодисперсними системами і складаються з часточок різних форм і розмірів. Більшість з них – кристалічні речовини. Існує 6 кристалічних систем: кубічна, гексагональна, тетрагональна, ромбічна, моноклінічна, триклінічна. Відомо, що тільки речовини, які належать до кубічної системи, пресуються в таблетки без додаткової грануляції і додавання допоміжних речовин (натрію хлорид, калію бромід).
Форму часточок встановлюють за співвідношенням їх середніх розмірів (довжини частинок до середньої ширини). При цьому частинки умовно поділяють на 3 основні групи: видовжені – співвідношення довжини до ширини більш ніж 3:1; пластинчасті – довжина перевищує ширину і товщину, але не більше ніж у 3 рази; рівнодіаметричні – мають кулеподібну, багатогранну форму, близьку до ізодіаметричної. Зазвичай, порошки, які мають паличкоподібну форму, характеризуються дрібнодисперсністю, добрим ущільненням і достатньою пористістю (анальгін, норсульфазол, акрихін тощо). Порошки з рівнодіаметричною формою часточок – крупнодисперсні, з низьким ступенем ущільнення, малопористі (лактоза, гексаметилентетрамін, салол). Чим складніша поверхня часточок порошку, тим краще ущільнення і менша сипкість, і навпаки.
Змочуваність порошкоподібних лікарських речовин – їх здатність взаємодіяти з різними рідинами, у тому числі з водою. Практичне значення змочуваності полягає в легкопроникності води в таблетку, яка одержана шляхом пресування добрезмочуваних водою речовин, що прискорює розпадання таблетки.
Гігроскопічність. Якщо субстанція сильно гігроскопічна, то порошкоподібна маса підготовлена для таблетування, почне поглинати пари з повітря і розпливатися в цій волозі. Для запобігання даного явища використовують допоміжні речовини – вологостимулятори.
Кристалізаційна вода. Молекули кристалізаційної води визначають механічні (міцність, пластичність) і термічні (відношення до температури повітряного середовища) властивості кристалізаційної речовини і впливають на її поведінку під тиском. Явище «цементування таблеток» тісно пов’язане з наявністю кристалізаційної води в субстанціях.
Технологічні властивості.
Фракційний (гранулометричний) склад – розподілення часточок порошку за розміром (фракціями), певним чином впливає на ступінь сипкості, та відповідно, на ритмічну роботу таблетмашин, стабільність маси одержуваних таблеток, точність дозування лікарських речовин, а також на якісні характеристики таблеток (зовнішній вигляд, розпадання, міцність).
Дослідження фракційного складу фармацевтичних порошків, які призначені для виробництва таблеток, показали – більшість з них містять переважно дрібну фракцію (менше 0,2 мм) і тому володіють поганою сипкістю, тому погано дозуються за об’ємом при таблетуванні. Фракційний склад порошків можна змінювати за допомогою направленого гранулювання, яке дозволяє одержати більш крупні гранули, що будуть краще пресуватися.
Насипна (об’ємна) щільність – маса одиниці об’єму вільно насипаного порошкоподібного матеріалу. Насипна щільність залежить від форми, розміру, щільності часточок порошку (гранул), їх вологості. За значенням насипної щільності можна прогнозувати об’єм матричного гнізда таблетувального пресу.
Однак найбільш важливими технологічними властивостями є сипкість, пресуємість та ковзна здатність порошкоподібного матеріалу.
Сипкість – здатність порошкоподібної маси висипатися із завантажувальної воронки під дією сили власного тяжіння та забезпечувати рівномірне заповнення матричного гнізда. Матеріал, який має погану сипкість у воронці, прилипає до її стінок, що порушує ритм його надходження до матриці. Це призводить до того, що необхідна маса і щільність окремих таблеток будуть суттєво відрізнятися. Сипкість розраховується за формулою:
Vc |
|
m |
|
|
|||
t 20 |
|||
|
|
де Vc – сипкість, кг/с; m – масса наважки, кг;
t – тривалість досліду, с;
20 – час утрясання, с.
Сипкість порошків може бути використана при виборі технології таблетування. Порошкоподібні суміші, які містять 80 – 100% дрібної фракції (розмір часточок менше 0,2 мм), погано дозуються, тому необхідно проводити направлене укрупнення часточок таких мас, тобто гранулювання. Якщо дрібної фракції міститься до 15%, можливе використання методу прямого пресування.
Пресуємість порошку – це здатність його часточок до когезії та адгезії під тиском. При цьому часточки порошку ніби склеюються, злипаються, зчіплюються між собою з утворенням однорідного твердого тіла. Пресуємість може бути визначена за здатністю таблетки до стискання. Чим вища міцність таблетки, тим краща пресуємість маси для таблетування.
Встановлено, що для речовин з міцністю таблеток:
вище 7 кг/см – застосовують чисті розчинники для процесу грануляції; якщо це крупнодисперсні порошки з гарною сипкістю, то застосовують технологію прямого пресування;
4 – 7 кг/см – достатнім є застосування звичайних зв’язуючих речовин;
1 – 4 кг/см – необхідним є застосування високоефективних зв’язуючих речовин.
Зазвичай допоміжними речовинами при виготовленні порошків лікарських речовин є розріджувачі, які застосовуються у випадку порошкування отрутних і сильнодіючих препаратів, що прописуються в дуже малих дозах, і розчинники – частіше концентровані розчини етилового спирту чи ефіру. Як правило, в якості розріджувача використовується молочний цукор (лактоза) і бурячний цукор (сахароза).
Цукор молочний (Saccharum lactis) – кристалічний білого кольору порошок без запаху, слабко солодкого смаку, добре розчинний у воді. Лактоза поряд із сахарозою (звичайним цукром) є дисахаридом, що зустрічається в природі у вільному стані. Зазвичай лактоза міститься в молоці (4 – 5%), із сироватки якого вона і може бути отримана. Відмінною рисою лактози, порівняно із сахарозою, є незначна гігроскопічність, що робить особливо зручною застосування лактози при розведенні порошків лікарських
речовин, виписаних у малих кількостях. У цьому відношенні досить вдалою виявилася щільність лактози 1,52 г/см3, що мало відрізняється від щільності ряду лікарських речовин, наприклад багатьох алкалоїдів і глікозидів. Однак варто мати на увазі, що індиферентність лактози дуже відносна – ця допоміжна речовина може вступати в різного виду взаємодії як з іншими допоміжними речовинами ліків, так і з діючими інгредієнтами. Наслідком подібного роду взаємодій може бути зміна активності лікарської речовини, частіше, зміна процесів її абсорбції.
Цукор бурячний (Saccharum) – білі тверді шматки дрібнокристалічної будови, безбарвні кристали чи білий мікрокристалічний порошок без запаху, із солодким смаком. Легко розчиняється у воді, утворює розчин нейтральної реакції; нерозчинний в абсолютному спирті, бензолі й хлороформі. Гігроскопічний. Одержують з цукрового очерету і цукрового буряка.
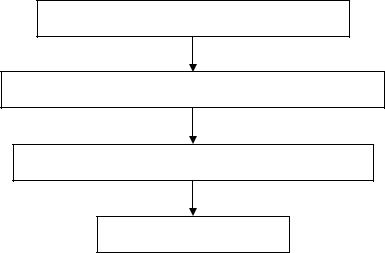
Подрібнення вихідних речовин
Розділення часточок порошку за розмірами
Змішування окремих компонентів
Фасування і пакування
Рис.1.1. Блок – схема одержання порошків
Підготування лікарських та допоміжних речовин. Лікарські і допоміжні речовини повинні відповідати нормативно-технічній документації, ГОСТам та ДСТУ і потрапляти на виробництво на подрібнення у просіяному стані. Якщо вихідні матеріали не відповідають вимогам до фракційного складу, їх подрібнюють.
Операції, способи, машини для подрібнення. Подрібнення (Pulveratio)
– це процес зменшення розміру часток твердих матеріалів способом механічного впливу, який призводить до збільшення питомої поверхні речовини, що подрібнюється. Подрібнення лікарських речовин має важливе значення при виготовленні порошків. Як правило, тонкоподрібнені речовини володіють більшим терапевтичним ефектом – швидше і повніше всмоктуються, а нерозчинні речовини краще адсорбуються слизовими оболонками і володіють кращим терапевтичним ефектом. Подрібнення має велике значення також для оптимального змішування і точного дозування. При подрібненні розмір часток лікарських речовин вирівнюється, після чого вони легко і добре змішуються і не розшаровуються при дозуванні.
Подрібнення може бути як допоміжним (забезпечення розчинності, екстракції, сушіння, грануляції) так і основним процесом (для одержання порошків, зборів, присипок). Вибір методу подрібнення залежить як від природи речовини, що подрібнюється, так і від необхідної тонкості одержуваного порошку. Подрібнення досягається за допомогою різних механічних зусиль: роздавлювання, розколювання, удару, стирання, різання. У застосовуваних методах подрібнення ці зусилля зазвичай поєднуються. Так, наприклад, подрібнення в ступці характеризується поєднанням стирання з роздавлюванням, а розмелювання в дисковому млинку «ексцєльсіорі» пов’язане з розриванням і стиранням тощо. Для подрібнення твердих речовин краще поєднувати удар з роздавлюванням (кристалічні солі); для в’язких матеріалів – розтирання з розриванням; для ламких – розколювання і розтирання.
Підлягають подрібненню продукти тонкого органічного синтезу, рослинні та тваринні матеріали, неорганічні матеріали. Залежно від

призначення речовини подрібнюють до певного ступеня (середнього, тонкого тощо). Вибір машини для подрібнення визначається фізико-хімічними властивостями вихідних матеріалів та кінцевим розміром часток порошку. У фармацевтичній промисловості широко використовують валки, ексцельсіори, дисмембратори, молоткові та барабанні млини. Для попереднього подрібнення до середніх розмірів крупнокристалічних матеріалів (NaCl, цукор) застосовують молоткові млини, до дрібного та тонкого – дисмембратори та кулькові млини. Для надтонкого подрібнення з метою досягнення однорідності змішування лікарських речовин з малим дозуванням використовують газоструминні млини.
В тому випадку коли операція подрібнення є основним процесом вона складається з кількох послідовних стадій, а саме: подрібнення, ситовий аналіз та змішування компонентів. Результати подрібнення оцінюють за ступенем подрібнення – це відношення середнього початкового розміру шматка матеріалу до його середнього розміру в поперечнику після подрібнення:
іd n d k
де, i – індекс подрібнення; dn – середній розмір часточок до подрібнення; dk – середній розмір часточок після подрібнення.
Залежно від ступеня подрібнення і розрізняють наступні види подрібнення: крупне (2 – 6), середнє (6 – 10), дрібне (10 – 50), тонке (50 – 100), надтонке (100 – 10000; 1 – 100 нм). Надтонке подрібнення призводить до одержання колоїдних частинок.
У фармацевтичній практиці використовують дві групи речовин, які необхідно подрібнювати:
1.Аморфні (amorpfus – безформенні)– переохолоджені рідини – скло, смоли, полімери, характеризуються ізотропією властивостей, тобто фізичні властивості даної речовини (пружність, теплопровідність, міцність тощо) розповсюджуються однаково у всіх напрямках. Це означає, що при подрібненні аморфне тіло буде розпадатися у різних непередбачуваних напрямках (неправильний злам). Вцілому сили зчеплення між елементарними часточками аморфних тіл незначні і аморфні речовини легко подрібнюються (а, якщо аморфне тіло охолодити, то воно буде утворювати псевдокристалічну структуру і стане більш крихким, відповідно, подрібнювати його буде легше).
2.Кристалічні речовини характеризуються наявністю кристалічної структури. Кристали можуть відрізнятися як за формою (існує 14 кристалографічних типів ґраток), так і за характером взаємодії між частинками (атомні, молекулярні, іонні ґратки). Кристалічні тіла, на відміну від аморфних, відрізняються анізотропією властивостей – фізичні властивості кристала розповсюджуються неоднаково у всіх напрямках. Перш за все це стосується механічної міцності кристала: кристали легко розколюються за певними площинами. Тому мета подрібнення кристалічних речовин – зруйнування кристалічної ґратки, переведення тіла у дрібнодисперсний стан.
Для того щоб швидко і з найменшими затратами енергії подрібнити кристалічну речовину, необхідно знати будову і тип кристалічної ґратки речовини, що подрібнюється.
До основних задач подрібнення належать:
зменшення відстані між елементарними частинками і збільшення питомої поверхні речовини;
одержання речовин з дещо зміненими властивостями, в тому числі фізико-хімічними.
Оскільки після подрібнення утворюються часточки різних розмірів, їх необхідно фракціонувати на ситах.
Операції просіювання твердих матеріалів. Подрібнені матеріали переважно неоднорідні за величиною часток, тому для достатньо точного визначення розміру цих частинок існують різні методи (повітряна сепарація, гідравлічна класифікація, ситова класифікація). Ситова класифікація – розділення матеріалу на фракції за допомогою сит – основний метод визначення розміру часточок, що використовується у фармацевтичній промисловості.
Просіювання (culbatio). Подрібнені лікарські засоби необхідно просіювати крізь визначені сита. Мета цієї операції – одержання продукту з однаковим розміром часток, що досягається за допомогою ситового аналізу. Просіювання регламентується спеціальною статтею ДФ XI «Визначення подрібнення порошків і сита».
Сита бувають металеві, виготовлені штампуванням металевого листа, і тканинні, виготовлені з шовкових (ДСТ 4403-77), капронових (ОСТ 17-46-82)
іметалевих (ДСТ 214-83) ниток. Розрізняють сита відкриті, що представляють собою порожні циліндри, виготовлені з металу чи дерева, дно яких затягнуте відповідною тканиною з визначеною величиною отворів; і закриті, що складаються з власне сита, приймача, у який надходить просіяний матеріал, і кришки, що захищає його від розпилення.
При необережному користуванні у сит, виготовлених із шовку, розташування ниток може змінюватися, внаслідок чого одержують порошок з різним розміром часток. Номер шовкового сита вказує, яка кількість отворів припадає на 1 см. Номер металевого дротяного сита відповідає розміру отворів сита в міліметрах. Номер пробивних сит із круглими отворами відповідає діаметру отвору в міліметрах, помноженому на 10. Номер сита з довгастими отворами відповідає ширині отвору в міліметрах, помноженому на 10.
Необхідно дотримуватися умови, щоб речовини, що подрібнюються, не взаємодіяли з матеріалом сита і не змінювали свого складу.
Результат просіювання прямо залежить від тиску, під яким проходить порошок, від величини отворів сита, а також від тривалості і сили, з якими проводиться просіювання. Тому при просіюванні необхідно враховувати вплив зазначених факторів і проводити цей процес не дуже швидко, ретельно перемішуючи порошок.
Для одержання порошків, вільних від дрібніших часточок, вдаються до методу «подвійного просіювання», який полягає в тому, що від дрібнішого порошку звільняються просіюванням через наступне густіше сито.
При просіюванні зручно користуватися віброситом. Сита бувають обертові, коливальні та вібраційні. Вібраційні сита є найбільш продуктивними за рахунок вібруючого руху сітки та більшої частоти коливань.
В результаті простого просіювання (через одне сито), вихідний матеріал поділяється на дві фракції: 1) просів (нижній продукт) – матеріал, що пройшов крізь сито; 2) відсів (верхній продукт) – матеріал, що не пройшов крізь сито і залишився зверху на ситі.
Проведення ситового аналізу. Фракційний склад. Лікарські препарати, як хіміко-фармацевтичні, так і порошки рослинного походження, мають різну ступінь дисперсності. Визначення фракційного складу порошків проводять шляхом просіювання речовини певної маси через стандартний набір сит (4 сита з діаметром отворів 0,5; 0,3; 0,2; 0,1 мм). Набір герметично закритий кожухом. Просіювання проводять на віброустановці з частотою 340 – 360 коливань/хв або вручну протягом 5 хв. Порошкоподібна маса складається із 2
– 4 фракцій.
Подрібнені і просіяні вихідні матеріали змішують у змішувачах. Операції змішування. Змішування (mixtio) – це процес, у результаті
якого досягається однорідність, тобто однакове співвідношення складових часток у будь-якій частині одержуваної суміші. Процес змішування – основна операція при виготовленні складних порошків. При недостатньо ретельному змішуванні інгредієнтів окремі дози порошку, одержувані при наступному його дозуванні, можуть містити різну кількість лікарських речовин. Це може несприятливо відбитися на лікувальній дії лікарського препарату, а при використанні сильнодіючих і отруйних лікарських речовин
– навіть призвести до отруєння.
Спосіб і порядок змішування порошків залежить від вагового співвідношення прописаних інгредієнтів та їх фізико-хімічних властивостей (агрегатний стан, вологопоглинання тощо). Залежно від зазначених факторів рекомендовані дуже важливі практичні положення, яких варто дотримуватись при змішуванні порошків.
Основні з них такі:
1. Лікарські речовини складного порошку, виписані в рівних чи приблизно рівних кількостях (співвідношення в масі не перевищує 1:5). У цьому випадку можливі два варіанти змішування:
якщо фізико-хімічні властивості лікарських речовин приблизно однакові, то їх змішують з урахуванням величини втрат при розтиранні.
якщо фізико-хімічні властивості лікарських речовин різні, то змішування і подрібнення починають із крупнокристалічної речовини, а потім до неї додають дрібнокристалічні.
2. Аморфні речовини (тальк, магнію оксид, крохмаль та ін.) змішують з порошковою масою без додаткового подрібнення.
3. Речовини, що легко розпилюються, додають в останню чергу і змішують обережно.
Складання матеріального балансу за стадіями (подрібнення, просіювання). Розрахунок виходу (η), втрат (ε) та витратного коефіцієнту(Квитр). При виробництві готових лікарських засобів кількість готового продукту, з урахуванням побічних продуктів і відходів, завжди менша кількості вихідних матеріалів. Пояснюється це наявними на кожному виробництві матеріальними втратами, яких тим більше, чим менш досконалий технологічний процес.
З метою оцінювання ступеню досконалості технологічного процесу та порівняння ефективності його проведення на різних виробництвах складають матеріальний баланс.
Матеріальний баланс – співвідношення між кількістю вихідної сировини, матеріалів, напівпродуктів і проміжної продукції (С1), використаних у виробництві, та кількістю фактично отриманої готової продукції (С2), побічних продуктів (С3), відходів або викидів (С4) і втрат (С5), тобто порівняння теоретично можливого й практично отриманого виходу готової продукції.
Це положення можна виразити рівнянням матеріального балансу:
С1 С2 С3 С4 С5
У випадку якщо відходи й побічні продукти виробництва відсутні, рівняння матеріального балансу набуде більш спрощеного вигляду:
С1 С2 С5
Матеріальний баланс складають як за окремими стадіями чи технологічними операціями, так і до всього технологічного процесу в цілому. Він може охоплювати всі матеріали (загальний, сумарний баланс) або кожен окремий компонент.
Матеріальні втрати при виробництві лікарських препаратів мають різне походження, внаслідок чого їх поділяють на кілька груп:
1)механічні, найчастіше зустрічаються при відсутності або недостатній механізації переміщення матеріалів, що переробляють (виливання рідини, розпил, утрушування, бій тощо);
2)фізико-хімічні, що спостерігаються у випадку проведення технологічного процесу без врахування фізико-хімічних властивостей лікарських речовин (неповнота екстрагування діючих речовин з лікарської рослинної сировини, втрата легколетких розчинників при фільтрації, втрата ефірного масла при випарюванні тощо);
3)хімічні, що спостерігаються в результаті недотримання або неправильного вибору параметрів проведення хімічних реакцій (синтезу).
Матеріальний баланс має велике практичне значення, так як відображає ступінь досконалості технологічного процесу. Чим він повніше складений, тим детальніше вивчена технологія даного препарату; чим менше в балансі різного роду втрат, тим точніше здійснюється процес виробництва. Навпаки, чим більше в балансі матеріальних втрат, тим менш освоєна технологія даного препарату й тим більше в ній різного роду невідповідностей.
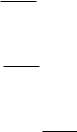
Матеріальний баланс лежить в основі регламенту виробництва, дає змогу оцінити правильність організації технологічного процесу, порівняти ефективність його проведення на різних виробництвах, що випускають однойменну продукцію.
Завдання на виконання
1.Ознайомитись з правилами роботи і техніки безпеки в технологічній лабораторії.
2.Завдання. Подрібнити на кульковому млині наважку цукру або рослинного матеріалу. Просіяти цукор чи рослинну сировину через сита з діаметром отворів 0,2; 0,25; 0,3 та 0,5 мм. Зважити окремо кожну фракцію, відділити готовий продукт, відсів та просів, вирахувати втрати. Скласти матеріальний баланс за стадіями подрібнення, просіювання та загальний баланс з урахуванням відходів. Знайти вихід (η), втрати (ε) та витратний
коефіцієнт (Квитр).
Приготування. Відібрати наважку цукру чи рослинного матеріалу масою 100 г, використовуючи технічні терези. Зразок подрібнити на кульковому млині протягом декількох секунд (залежно від завдання викладача). Тривалість подрібнення занотувати в зошит. Одержаний помел просіяти крізь сита діаметром отворів 0,2; 0,25; 0,3 та 0,5 мм. Окремо зважити просів і відсів після кожного сита. Скласти матеріальний баланс за стадіями подрібнення та просіювання та загальний матеріальний баланс з урахуванням втрат.
Приклад розрахунку. При подрібненні 100,0 г кислоти борної на кульковому млині одержали 98,0 г подрібненого продукту. Після просіювання одержали просів у кількості 78,0 г і відсів 16,6 г. Скласти матеріальний баланс за стадіями подрібнення, просіювання та загальний баланс з урахуванням відходів. Знайти вихід (η), втрати (ε) та витратний
коефіцієнт (Квитр).
а). Рівняння матеріального балансу на стадії подрібнення:
100,0 98,0 2,0
Вихід:
10098,0,0 100 % 98,0%
Втрати:
1002,0,0 100 % 2,0%
Витратний коефіцієнт:
100 ,0 К витр 98,0 1,020
б). Рівняння матеріального балансу на стадії просіювання:
98,0 78,0 16,6 3,4