
Химическая переработка нефти
.pdfvk.com/club152685050 | vk.com/id446425943
Глава 5
ХИМИЧЕСКИЕ ПРОИЗВОДСТВА
5.1. ВВЕДЕНИЕ
Химические производства будем рассматривать как примеры реализации основных положений теории химических процессов и реакторов и химико-
технологических систем. Выбраны две группы производств: органических и неорганических продуктов. Из всей обширной гаммы органических производств выбрана химическая переработка нефти и прослежены пути получения из сложной природной смеси ряда продуктов. Основное здесь - разделение и химические превращения компонентов сложной смеси. На примере производств эталбензола и стирола показан выбор оптимального реактора. Обоснование и построение оригинальной энерготехнологической схемы продемонстрировано на примере производства стирола. Анализ тепловой эффективности сделан для производства этилена пиролизом бензинов.
Хорошо изученные процессы в производстве неорганических веществ рассмотрены с иной точки зрения: физико-химическое обоснование технологических схем, процессов и аппаратов отдельных стадий производства.
Некоторые данные о производствах приведены в описательном виде, поскольку эти производства были обсуждены в предыдущих разделах. Также с привлечением предыдущего материала может быть сделан детальный анализ процессов - например, выбор системы разделения продуктов алкилирования бензола или смеси ароматических углеводородов, образующихся при каталитическом риформинге; выбор схемы теплообмена в системе "двойное контактирование/двойная абсорбция" в производстве серной кислоты;
определение возможных путей обеспечения экологической безопасности производств и др.
Материал этой главы поможет сопоставить теоретические положения с имеющейся практикой, проверить и закрепить знания, полученные при изучении предыдущих глав.
1
vk.com/club152685050 | vk.com/id446425943
5.2. ХИМИЧЕСКАЯ ПЕРЕРАБОТКА НЕФТИ
5.2.1. Общая характеристика нефтехимического комплекса Нефти различных месторождений заметно отличаются по фракционному
составу - содержанию легких, средних и тяжелых дистиллятов. Большинство нефтей содержит 15-25% бензиновых фракций, выкипающих до 180 °С, и 45-55%
фракций, перегоняющихся до 300-350 °С.
Основные химические элементы, входящие в состав нефти - углерод (82-
87%), водород (11-14%), сера (0,1-7%), азот (0,001- 1,8%), кислород (0,5- 1%).
Общее содержание алканов (парафины) в нефтях достигает 30-50%,
циклоалканов (циклопарафины, нафтены) - от 25 до 75%. Арены (ароматические углеводороды) содержатся, как правило, в меньшем количестве по сравнению с алканами и циклоалканами (10-20%).
Соотношения между группами углеводородов придают нефтям различные свойства и оказывают влияние на выбор метода переработки нефти и номенклатуру получаемых продуктов.
Нефть является основным источником сырья для нефтеперерабатывающих заводов при получении моторных топлив, масел и мазута. Нефть и продукты ее переработки служат также сырьем для синтеза многочисленных химических продуктов: полимерных материалов, пластических масс, синтетических каучуков и волокон, спиртов, растворителей и др. В перспективе большая часть нефтепродуктов (особенно энергетических топлив) может быть замещена альтернативными энергоносителями, в то время как замена нефтяного сырья в качестве источника получения нефтехимических продуктов мало вероятна. Более того, доля нефти, используемой в нефтехимических производствах, в ближайшие годы в мире возрастет до 8% и по прогнозам в 2000 г. достигнет 20-25%. В связи с этим происходит интеграция нефтеперерабатывающей и нефтехимической промышленности и формирование нефтехимических комплексов.
Комбинирование нефтепереработки (первичная переработка,
каталитический крекинг, риформинг) с нефтехимическими процессами (пиролиз,
синтез мономеров, производство пластмасс и др.) значительно расширяет
2
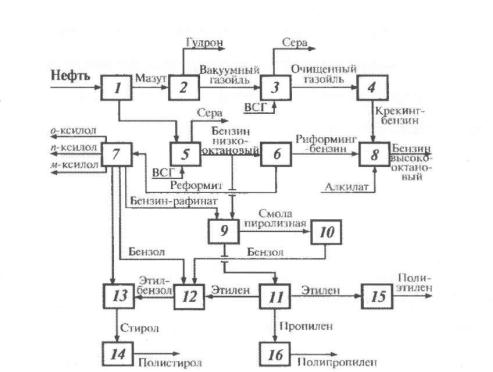
vk.com/club152685050 | vk.com/id446425943
возможности выбора оптимальных схем глубокой переработки нефти, повышает гибкость производственных систем для получения моторных топлив или нефтехимического сырья, способствует увеличению их рентабельности. В
настоящее время имеется большое число процессов и их комбинаций, которые потенциально могут обеспечить глубину переработки нефти вплоть до 100%,
Выбор структуры нефтехимического комплекса зависит
Рис. 5.7. Структура нефтехимического комплекса:
1- первичная переработка нефти (в установках АВТ); 2 - вакуумная перегонка мазута (в установках ВТ), 3 - (гидроочистка вакуумного газойля; 4
каталитический крекинг газойля; 5 - гидроочистка бензина; 6- риформинг бензина; 7 – разложение риформата, 8 - компаундирование (смешение); 9 -
пиролиз бензина; 10 - переработка пиролизной смеси; 11 - разделение газа пиролиза; 12 - алкилирование бензола; 13 - производство стирола; 14 -
производство полистирола, 15 - (производство полиэтилена; 16 - производство полипропилена; ВСГ – водородсодержащий газ
3
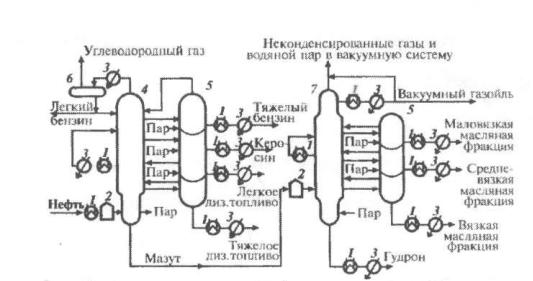
vk.com/club152685050 | vk.com/id446425943
от регионального и общего спроса на нефтепродукты, от природы нефти,
экологических факторов. Структура одного из вариантов нефтехимического комплекса показана на рис. 5.1.
5.2.2. Первичная переработка нефти Существуют первичные и вторичные методы переработки нефти.
Первичными являются процессы разделения нефти на фракции перегонкой,
вторичные процессы - это деструктивная (химическая) переработка нефти и очистка нефтепродуктов (фракции перегонки различаются интервалом температур кипения компонентов).
Рис. 5.2. Схема установки первичной перегонки нефти (АВТ топливно-
масляная):
1 - теплообменник; 2 - трубчатая печь; 3 - холодильник, конденсатор-
холодильник; 4 - атмосферная колонна; 5- отгонная колонна; 6- газосепаратор; 7-
вакуумная колонна
К первичной перегонке относят процессы атмосферной перегонки нефти и вакуумной перегонки мазута. Их назначение состоит в разделении нефти на фракции для последующей их переработки или использования как товарных
4
vk.com/club152685050 | vk.com/id446425943
продуктов. Первичную перегонку осуществляют соответственно в атмосферных трубчатых (AT) и вакуумных трубчатых (ВТ) или атмосферновакуумных трубчатых (АВТ) установках.
На установках AT осуществляют неглубокую переработку нефти с получением бензиновых, керосиновых, дизельных фракций и мазута. Установки ВТ предназначены для углубления переработки нефти. Получаемые в них из мазута газойлевые, масляные фракции и гудрон используют в качестве сырья в процессах вторичной переработки нефти для производства смазочных масел,
кокса, битума и других нефтепродуктов.
Принципиальная схема установки АВТ первичной перегонки нефти показана на рис. 5.2. Ниже приведен состав (в %) полупродуктов перегонки западносибирской нефти на установке АВТ-6 (мощность по перерабатываемому
сырью 6 млн т/год) |
|
Газ ............................... |
1,1 |
Фракции, °С: |
|
до 62 .................... ... |
. 4,1 |
62-85 ........................... |
2,4 |
85-120 ................... .. ... |
4,5 |
120-140 ...................... |
3,0 |
140-180 ........................ |
6,0 |
180 240 ........................ |
9,5 |
240-350 ..................... |
19,0 |
350-460 ...................... |
21,0 |
Гудрон ....................... |
28.4 |
Потери......................... |
1,0 |
У г л е во д о р о д н ы й газ состоит преимущественно из пропана и бутанов,
которые в растворенном виде содержатся в поступающей на переработку нефти.
Пропан-бутановую фракцию используют для производства индивидуальных
5
vk.com/club152685050 | vk.com/id446425943
углеводородов на газофракционирующих установках в качестве бытового топлива.
Бе н з и н о вы е ф р а кц и и ( 6 2 - 1 8 0 ° C ) служат сырьем во вторичных процессах изомеризации, каталитического риформинга с целью производства индивидуальных ароматических углеводородов (бензола, толуола, ксилолов),
высокооктановых компонентов автомобильных и авиационных бензинов; их применяют в качестве сырья пиролиза при получении этилена.
К е р о с и н о в ы е фракции (120-240 °С) используются как топливо для реактивных двигателей в виде осветленного керосина и для производства лаков и красок (уайт-спирит),
Д и з е л ь н ы е ф р а кц и и (1 4 0 -340 °С) служат дизельным топливом и сырьем для получения жидких парафинов депарафинизацией.
М а з у т - остаток атмосферной перегонки нефти - используется как котельное топливо и в качестве сырья во вторичных процессах переработки
(каталитический крекинг, гидрокрекинг).
Г уд р о н - остаток вакуумной переработки мазута - подвергается деасфальтизации, коксованию с целью углубления переработки нефти и используется в производстве битума.
В последнее время нефть перерабатывается на комбинированных установках, сочетающих процессы первичной перегонки нефти с термическими и каталитическими процессами. Комбинированные установки требуют меньших капиталовложений, чем раздельные установки эквивалентной мощности. Они экономичнее и по эксплуатационным затратам, так как более рационально используют тепло потоков и вследствие этого расходуют меньше первичного тепла, воды и электроэнергии. В отечественных установках ЛК-6У комбинируется перегонка нефти с гидроочисткой, каталитическим риформингом я газофракционированием. Мощность этих установок по переработке нефти составляет 6 млн т/год.
5.2.3. Каталитический риформинг углеводородов
6
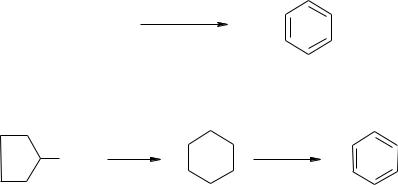
vk.com/club152685050 | vk.com/id446425943
Основные цели каталитического риформинга углеводородов в
нефтехимическом комплексе следующие:
1) превращение низкооктановых бензиновых фракций в катализат -
высокооктановые компоненты бензина;
2) превращение бензиновых фракций в катализах, из которого выделяют ароматические углеводороды - бензол, толуол, этилбеизол, изомеры ксилола.
Каталитический риформинг проводят в среде водорода при высоких температурах
(480 -530 °С), сравнительно низких давлениях (2-4 МПа) и с применением специальных катализаторов. В процессе образуется избыточное количество водорода, которое выводится в виде водородсодержащего газа (до 80% Н2) и
используется для процессов гидрирования.
Каталитический риформинг - сложный химический процесс, в котором
протекают реакции, приводящие к образованию ароматических углеводородов:
дегидрирование шестичленных нафтенов применением специальных катализаторов. В процессе образуется
избыточное количество водорода, которое выводится в виде водородсодержащего газа (до 80% Н2) и используется для процессов гидрирования.
Каталитический риформинг - сложный химический процесс, в котором
протекают реакции, приводящие к образованию ароматических углеводородов:
дегидрирование шестичленных нафтенов
n-C H |
+ |
4 H |
|
6 14 |
|
||
|
|
2 |
|
дегидроизомеризация пятичленных нафтенов |
|
|
|
CH3 |
|
+ |
3 H2 |
дегидроциклизация (ароматизация) парафинов |
|
|
|
7
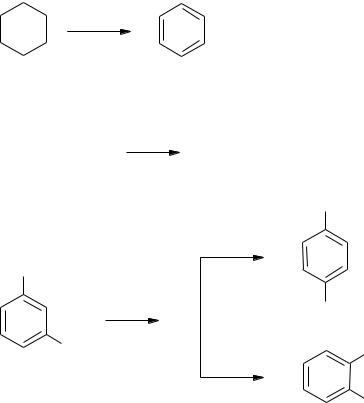
vk.com/club152685050 | vk.com/id446425943
+ |
3 H |
|
2 |
изомеризация парафинов и ароматических углеводородов
н-C H |
изо-С Н |
; |
||
6 |
14 |
6 |
14 |
|
CH3
CH3
|
CH |
|
3 |
CH |
CH |
3 |
3 |
|
|
|
CH |
|
3 |
Основные реакции каталитического риформинга - дегидрирование нафтенов и дегидроциклизация парафинов - протекают со значительным тепловым эффектом. Теплота дегидрирования метилциклогексана в толуол при рабочей температуре 800 К составляет 2212 кДж/кг, а дегидрирования н-гептана в толуол
2539 кДж/кг.
Основные реакции ароматизации в процессе риформиига сопровождаются изомеризацией и гидрокрекингом углеводородов. Теплота реакций изомеризации невелика, а гидрокрекинг про текает с выделением тепла, которое частично компенсирует эндотермический эффект основных реакций риформинга.
Реакции ароматизации являются высокотемпературными. Температура процесса риформиига зависит от применяемого катализатора и достигает 740-800
К.
Исходя из термодинамики, в процессе риформинга повышение давления препятствует ароматизации сырья. Однако высокое давление водорода оказывается необходимым для насыщения непредельных углеводородов в
8
vk.com/club152685050 | vk.com/id446425943
побочных реакциях крекинга. В случае низкого парциального давления водорода на поверхности катализатора происходит уплотнение ненасыщенных углеводородов с образованием кокса. Повышенное давление и избыток водорода в процессе препятствуют коксообразованию. Высокое парциальное давление водорода достигается циркуляцией водородсодержащего газа, получаемого в ходе риформинга.
Мольные соотношения циркулирующего водородсодержащего газа и жидкофазного углеводородного сырья находятся в пределах от 6:1 до 10:1.
Увеличение содержания водорода за счет повышения кратности циркуляции повышает расход энергии на компримирование циркулирующего газа и расход топлива в трубчатой печи для подогрева этого газа. Оптимальная концентрация водорода в циркулирующем газе составляет 80 90% (об.),
В каталитическом риформинге применяют гетерогенные бифункциональные катализаторы. Эти катализаторы содержат металлы (платину,
платину и рений, платину и иридий), которые катализируют реакции дегидрирования и гидрирования. Носителем катализаторов служит промотированный галогенами оксид алюминия, обладающий кислотными свойствами и катализирующий реакции изомеризации и крекинга углеводородов.
На катализаторах риформинга протекают также реакции дегидроциклизации парафиновых углеводородов. В отечественной промышленности используют алюмоплатиновые катализаторы АП-56 и АП-64, которые содержат соответственно 0,65% и 0,64% платины, нанесенной на γ-А12О3.
Каталитический риформинг, основные реакции которого эндотермические,
осуществляют в адиабатических реакторах. Реакторный блок промышленных установок риформинга обычно состоит из трех или четырех последовательно работающих реакторов с промежуточным подогревом парогазовой смеси в печи.
Технологическая схема установки риформинга представлена на рис. 5.3.
9
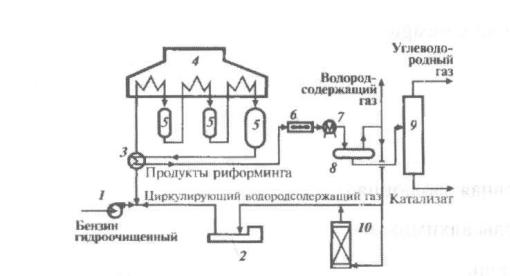
vk.com/club152685050 | vk.com/id446425943
Рис. 5.3 Схема установки каталитического риформинга:
1 - сырьевой насос; 2- циркуляционный компресcop; 4 - теплообменник; 4-
многокамерная трубчатая печь; 5 - реакторы: 6 - воздушный холодильник; 7 -
водяной холодильник; 8 – сепаратор; 9 - стабилизационная колонна; 10 –
адсорбер-осушитель
Работа установки характеризуется следующими показателями:
Катализатор………………………………………………АП-64
Температура на входе в реактор, °С……………………480
Перепад температуры в реакторе, град…………………60
Давление, МПА……………………………………………..3,5
Объемная скорость, ч-−1……………………………………1,5
Кратность циркуляции……………………………………1800
Содержание нафтенов и сырье, % (мас.)………………….36
Выход катализата, % (мас.)…………………………………77
Содержание ароматических углеводородов
в катализате, % (мас.) |
64 |
10