
- •500 Engine Data
- •500.00 Main Data for GenSets
- •500.01(01H) Introduction
- •500.02(01H) Safety
- •500.05(01H) Cross Section
- •500.10(01H) Key for Engine Designation
- •500.11(01H) Designation of Cylinders
- •500.12(01H) Engine Rotation Clockwise
- •500.20(01H) Code identification for Instruments
- •500.35(01H) Data for Pressure and Tolerance
- •500.35(11H) Data for Pressure and Tolerance
- •500.40(01S) Data for Torque Moment
- •500.45(01H) Declaration of Weight
- •500.50(01H) Ordering of Spare Parts
- •500.55(01H) Service Letters
- •500.60(01H) Conversion Table
- •500.65(01H) Basic Symbols for Piping
- •501 Operation of Engine
- •501.01(01H) Operating
- •501.05(01H) Out-of Service
- •501.10(01H) Starting-up after Out of Service Periods
- •501.15(02H) Guidelines for Longterm Low-Load Operation on HFO
- •501.25(01H) Operating a Diesel Engine at Low Frequency
- •502 Engine Performance and Condition
- •502.01(01H) Engine Performance and Condition
- •502.05(01H) Condensate Amount
- •502-01.00(01H) Engine Performance Data
- •503 Trouble Tracing
- •503.01(01H) Starting Failures
- •503.01(02H) Starting Failures
- •503.02(01H) Faults in Fuel Oil System
- •503.03(01H) Disturbances during Running
- •503.04(01H) Ignition in Crankcase
- •503.06(01H) Trouble Shooting Guide for Turbine Starter
- •503.09(01H) Trouble Shooting for Cooling Water System
- •503.10(01H) Trouble Shooting for Lubricating Oil Cooler
- •504.01(01H) Lubricating Oil Specification
- •504.01(05H) Lubricating Oil Specification
- •504.03(01H) Maintenance of Lubricating Oil Condition
- •504.05(01H) Lubricating Points
- •504.06(01H) Lubricating Oil in Base Frame
- •504.06(04H) Lubricating Oil in Base Frame
- •504.20(02H) Fuel Oil Specification
- •504.20(04H) Fuel Oil Specification
- •504.25(01H) Fuel Oil Quality
- •504.26(01H) Nomogram for Determination of CCAI
- •504.26(02H) Nomogram for Determination of CCAI
- •504.27(01H) Analysis Data
- •504.30(01H) Fuel Oil Cleaning
- •504.40(01H) Fresh Water System Treatment
- •504.40(02H) Freshwater System Treatment
- •505 Cylinder Head
- •505.01(01H) Cylinder Head
- •505-01.00(01H) Dismantling of Cylinder Head
- •505-01.05(01H) Inspection of Inlet Valve, Exhaust Valve and Valve Guide
- •505-01.15(01H) Valve Rotator
- •505-01.20(01H) Replacement of Valve Guide
- •505-01.26(01H) Indicator Valve
- •505-01.30(01H) Replacement of Sleeve for Fuel Injector
- •505-01.35(01H) Replacement of Valve Seat Ring
- •505-01.40(01H) Mounting of Cylinder Head
- •505-01.45(01H) Inspection of Cylinder Head Cooling Water Space
- •50501-01H Cylinder Head
- •50502-01H Valve Spindles and Valve Gear
- •50508-01H Indicator Valve
- •50510-01H Cylinder Head, Top Cover
- •506 Piston, Connecting Rod and Cylinder Liner
- •506.01(01H) Piston, Connecting Rod and Cylinder liner
- •506-01.05(01H) Separation of Piston and Connecting Rod
- •506-01.10(01H) Piston
- •506-01.15(01H) Connecting Rod
- •506-01.25(01H) Tightening and Check of Connecting Rod Screws
- •506-01.30(01H) In-situ Inspection of Connecting Rod Big-end Bearing
- •506-01.35(01H) Inspection and Honing of Cylinder Liner
- •506-01.40(01H) Replacement of Cylinder Liner
- •50601-01H Piston and Connecting Rod
- •507 Camshaft and Camshaft Drive
- •507.01(01H) Camshaft and Camshaft Drive
- •507-01.00(01H) Check of Camshaft and Camshaft Drive
- •507-01.05(01H) Inspection and Replacement of Camshaft Bearing
- •507-01.20(01H) Adjustment of Camshaft
- •50701-01H Intermediate Wheel
- •50705-01H Camshaft and Camshaft Bearing
- •50705-07H Camshaft and Camshaft Bearing
- •508-01.00(01S) Inspection of Valve Roller Guides
- •50801-01H Roller Guide and Push Rods
- •509.01(01H) Control and Safety Systems
- •509.05(01H) Instruments and Automatics
- •509.10(02H) Lambda Controller
- •509.35(01H) Starting Box
- •509-01.05(01H) Functional Test and Adjustment of Overspeed Trip
- •509-05.00(01S) Adjustment and Test of ON/OFF Pressostate
- •509-05.01(01S) Adjustment and Test of ON/OFF Thermostate
- •50903-01H Overspeed Device
- •50905-03H Prelubricating Oil Alarm (LAL 25)
- •50905-04H Instrument Panel
- •50907-02H Thermometer
- •50908-01H Pick-up
- •50910-01H Lambda Controller
- •50935-01H Starting Box
- •510 Crankshaft and Main Bearings
- •510.01(01H) Crankshaft and Main Bearings
- •510-01.00(05H) Checking of Main Bearings Alignment (Autolog)
- •510-01.05(01H) Inspection of Main Bearing Shells
- •510-01.10(01H) Inspection of Guide Bearing Shells
- •51001-01H Crankshaft
- •51002-02H Resilient Gear Wheel
- •51003-02H Flywheel with Gear Rim
- •511S Engine Frame and Base Frame
- •511.01(01H) Engine Frame and Base Frame
- •511-01.00(01H) Functional Test of Crankcase Safety Relief Valves
- •51101-02H Frame with Main Bearings
- •51102-02H Mounting of Pumps
- •51106-02H Covers on Frame
- •51106-03S Covers on Frame
- •512 Turbocharger System
- •512.01(01H) Turbocharger System
- •512-01.00(01H) Overhaul of Charging Air Cooler
- •512-15.00(01H) Water Washing of Turbine Side
- •51202-01S Exhaust Pipe Arrangement
- •51203-03H Turbocharging Arrangement
- •513 Compressed Air System
- •513.01(01S) Compressed Air System
- •513.01.30(01H) Overhaul, Test and Inspection of Turbine Starter
- •513-01.40(01H) Main Starting Valve
- •513-01.90(01H) Check of Compressed Air Piping System
- •51309-01H Turbine Starter
- •51310-01H Main Starting Valve
- •51314-01S Starting Valve
- •51315-03H Main Stop Valve
- •51316-03H Air Strainer
- •51319-02H Safety Valve
- •51320-01H ON-OFF Valve for Jet System
- •51321-01H Air Filter
- •514 Fuel Oil System
- •514.01(01H) Internal Fuel Oil System
- •514-01.05(01H) Fuel Injection Pump and Fuel Injection Pipe
- •514-01.10(02H) Fuel Injection Valve
- •514-01.15(01H) Fuel Oil Split Filter
- •514-01.90(01H) Check of Fuel Oil Piping System
- •514-05.01(01H) Adjustment of The Maximum Combustion Pressure
- •51401-01H Fuel Injection Pump
- •51402-01H Fuel Injection Valve
- •51403-01H Fuel Oil Filter Duplex
- •51404-01H Fuel Injection Pipe
- •51430-01H Pipes on Cylinder Section
- •515 Lubricating Oil System
- •515.01(01H) Internal Lubricating Oil System
- •515.06(01H) Lubricating Oil Cooler
- •515-01.00(01H) Lubricating Oil Pump, Engine Driven
- •515-01.10(01H) Lubricating Oil Filter
- •515-01.20(01H) Lubricating Oil, Thermostatic Valve
- •515-01.90(01H) Check of Lubricating Oil Piping System
- •515-06.00(02H) Lubricating Oil Cooler
- •51501-03H Lubricating Oil Pump (Gear Driven)
- •51502-01H Lubricating Oil Filter (Type A)
- •51502-02H Lubricating Oil Filter (Suppl. for Plate 51502-01H)
- •51504-01H Prelubricating Pump
- •51506-01H Lubricating Oil Cooler
- •51525-01H Hand Wing Pump
- •51530-01H Lubricating Oil Separator
- •516 Cooling Water System
- •516.01(01H) Cooling Water System
- •516.04(01H) Cooling Water Thermostatic Valve
- •516-01.90(01H) Check of Cooling Water System
- •516.04-00(01H) Cooling Water, Thermostatic Valve
- •51604-01H Cooling Water Thermostatic Valve
- •51610-01H High Temperature Fresh Water Pump
- •51625-01H Pipes on Cylinder Head
- •51635-01H Preheater - Fresh Water
- •517 Special Equipment
- •518 Driven Machinery
- •519 Specific Plant Information
- •519.03(01S) Resilient Mounting of Generating Sets
- •519-03.00(01S) Fitting Instructions for Resilient Mounting of GenSets
- •519-03.00(02S) Fitting Instructions for Resilient Mounting of GenSets
- •519-03.00(03S) Fitting Instructions for Resilient Mounting of GenSets
- •519-03.05(01S) Replacement of Conicals
- •519-03.10(01S) Replacement of Conicals
- •520 Tools
- •520.01(01H) Introduction to Spare Part Plates for Tools
- •520-01.05(01H) Application of Hydraulic Tools
- •520-01.10(01H) Maintenance of Hydraulic Tools
- •520-01.15(01H) Tightening with Torque Spanner

Index
Page 1 (1)
Piston, Connecting Rod and Cylinder Liner |
506 |
|
|
|
L23/30H |
Description |
|
Piston, Connecting Rod and Cylinder liner ................................................................... |
506.01(01H) |
Working Card |
|
Dismounting of Piston and Connecting Red ........................................................... |
506-01.00 (01H) |
Separation of Piston and Connecting Rod .............................................................. |
506-01.05 (01H) |
Piston ....................................................................................................................... |
506-01.10 (01H) |
Connecting Rod ....................................................................................................... |
506-01.15 (01H) |
Criteria for Replacement of Connecting Rod Big-end and Main Bearing Shells ..... |
506-01.16 (01H) |
Mouthing of Piston and Connecting Rod ................................................................. |
506-01.20 (01H) |
Tightening and Check of Connecting Rod Screws .................................................. |
506-01.25 (01H) |
In-situ Inspection of Connecting Rod Big-end Bearing ........................................... |
506-01.30 (01H) |
Inspection and Honing of Cylinder Liner ................................................................. |
506-01.35 (01H) |
Replacement of Cylinder Liner ................................................................................ |
506-01.40 (01H) |
Grinding of Seal Face on Cylinder Liner and Cylinder Head .................................. |
506-01.45 (01H) |
Dismounting of Piston and Cylinder Liner at Low Overhaul Heights ........................ |
506-01.50 (01H) |
Plates |
|
Piston and Connecting Rod ............................................................................................. |
50601-01H |
Piston and Connecting Rod ............................................................................................. |
50601-02H |
Cylinder Liner and Water Guide Jacket ........................................................................... |
50610-01H |
Cylinder Liner and Water Guide Jacket ........................................................................... |
50610-02H |
08028-0D/H5250/94.08.12
97.05-ES0U
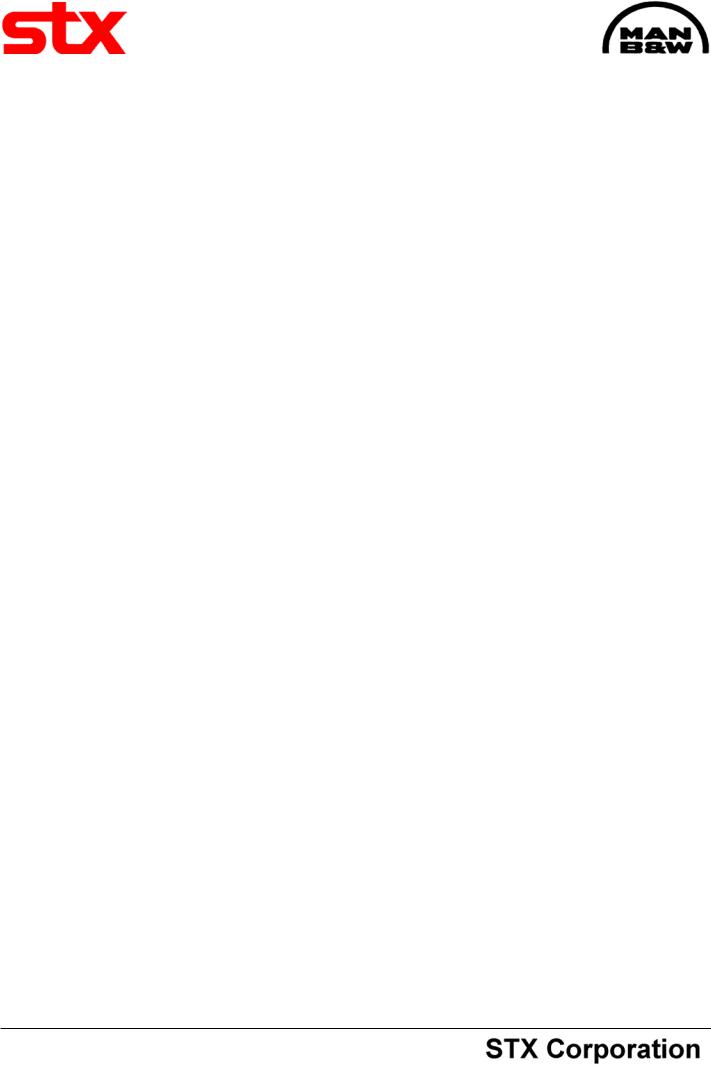
Description |
Piston, Connecting Rod and Cylinder Liner |
506.01 |
Page 1 (1) |
Edition 01H |
|
|
|
|
|
|
|
|
|
L23/30H |
Piston |
Connecting Rod |
|
The piston, which is oil-cooled and of the monobloc type made of nodular cast iron, is equipped with 3 compression rings and 1 scraper ring.
By use of a combination of compression rings with different barrel-shaped profiles and chrome-plated running surface on all rings, the piston ring pack is optimized for maximum sealing effect and minimum wear rate.
The piston has a cooling oil space close to the piston crown and the piston ring zone. The heat transport, and thus the cooling effect are based on the shaker effect arising during the piston movement. Oil from the engine's lubricating oil system is used as cooling oil.
The piston is provided with a turned edge at the top due to the flame ring mounted in the cylinder liner.
Piston Pin
The piston pin is fully floating which means that it can turn freely in the pin bosses of the piston as well as in the connecting rod bush. The piston pin is turned in place upwords in axial direction by two circlips (seeger rings).
08028-0D/H5250/94.08.12
The connecting rod is die-forged. The big-end has an inclined joint in order to facilitate the piston and connecting rod assembly to be withdrawn up through the cylinder liner. The joint faces on the connecting rod and the bearing cap are serrated to ensure precise location and to prevent relative movement of the parts.
The big-end bearing is of the trimetal type, i.e. steel shells lined with tin-aluminium or lead-bronze coated with a running layer. Designed as plain type or rillentype. The bearing shells are of the precision type and are therefore to be fitted without scraping or any other kind of adaption.
The small-end bearing is of the trimetal type and is pressed into the connecting rod.
Cylinder Liner
The cylinder liner is made of fine-grained, pearlite cast iron and is fitted in a bore in the engine frame. Replaceable cast iron sealing rings are fitted between the liner and the cylinder head and between the liner and the frame. The liner is clamped by the cylinder head and is guided by a bore at the bottom of the cooling water space of the engine frame. The liner can thus expand freely downwards, when heated during the running of the engine. Sealing for the cooling water is obtained by means of silicone rubber rings which are fitted in grooves machined in the liner.
The cylinder liner is of the socalled "stepped cylinder" type, provided with flame ring inserted in the top of the liner.
96.19 - ES0U

Working Card |
Dismounting of Piston and Connecting Rod |
506-01.00 |
Page 1 (3) |
Edition 01H |
|
|
|
|
|
|
|
08028-0D/H5250/94.08.12
L23/30H
Safety precautions:
Stopped engine
Shut-off starting air
Shut-off cooling water
Shut-off fuel oil
Shut-off cooling oil
Stopped lub. oil circul.
Description:
Dismounting of piston and connecting rod assembly, for inspection and/or overhaul.
Starting position: |
|
Cylinder head has been dismounted |
|
from engine |
505-01.00 |
Crankcase open. |
|
Related procedure: |
|
Separation of piston and connecting |
|
rod |
506-01.05 |
Inspection and honing of cylinder |
|
liner |
506-01.35 |
Manpower: |
|
|
|
Working time |
: |
1 |
hour |
Capacity |
: |
2 |
men |
Data: |
|
|
|
Data for pressure and tolerance |
(Page 500.35) |
Data for torque moment |
(Page 500.40) |
Declaration of weight |
(Page 500.45) |
Special tools: |
|
|
Plate no |
Item no |
Note |
52006 |
021 |
|
52006 |
033 |
|
52006 |
094 |
2 pieces |
52006 |
224 |
|
52006 |
273 |
80-360 Nm |
52010 |
011 |
|
Tool combination for dismounting of connecting rod screw, see working card 520-01.20.
Hand tools:
Threaded pin M12.
Open-end spanner 24 mm.
Wire.
Scraper or similar.
Small adjustable spanner.
Replacement and wearing parts:
Plate no |
Item no |
Qty/ |
96.20 - ES0S

506-01.00 |
Dismounting of Piston and Connecting Rod |
Working Card |
Edition 01H |
Page 2 (3) |
|
|
|
|
|
|
|
L23/30H
Preparations before Dismounting
1) Clean the upper part of the cylinder. If not, the piston may get stuck during removal in the carbon deposited in this area.
a)Turn the piston to the buttom.
b)Place a used piston ring on top of the piston.
c)Mount the tube (for holding down the cylinder liner during the piston withdrawal) on one of the cylinder head studs, screw on the nut and tighten it slightly.
d)Turn the piston in top, in order to push the flame ring out of the cylinder by means of the piston ring.
Info: It is the used piston ring which pushes the flame ring out of the cylinder.
2)Remove the gangway, if any installed, in order to improve the access conditions.
3)Turn the crankshaft to bring the crank throw concerned into a position of approx. 50 degrees before TDC.
This position is identifiable by the connecting rod shaft being very close to the cylinder liner shirt, see fig. 1.
4)Clean the threaded hole in the piston top, and mount the eye screw.
5)Mount the tube (for holding down the cylinder liner during the piston withdrawal) on one of the cylinder head studs, screw on the nut and tighten it slightly.
6)Attach a wire rope to the eye bolt by means of a shackle, hook the wire on to a tackle and pull the wire rope tight.
Note! If minor adjustments of the crank throw position appear necessary for access to the connecting rod screws, the wire rope must be slackened before turning of the crankshaft and tightened up again in the new crank throw position.
08028-0D/H5250/94.08.12
Fig 1. Mounting of tools (placing). |
Fig 2. Removal of bearing cap. |
96.20 - ES0S

Working Card |
Dismounting of Piston and Connecting Rod |
506-01.00 |
||
Page 3 (3) |
Edition 01H |
|||
|
|
|
|
|
|
|
|
|
|
|
|
|
|
L23/30H |
|
|
|
|
|
|
|
|
|
|
Fig 3. Removal of upper big-end bearing shell.
Dismounting of Bearing Cap
7)Unload the connecting rod screws and unscrew one of the upper screws.
8)Mount the guide pin for the bearing cap in one of the threaded holes and fit a screwdriver or similar in the hole in the guide pin, and unscrew the screws.
Fig 4. Lift of piston and connecting rod assembly.
08028-0D/H5250/94.08.12
Note! The purpose of the guide pin is to prevent any damage of crank journal, joint faces or bearing surface to occur during dismounting of the bearing cap, and to facilitate easy handling when removing the bearing cap from the crankcase.
9)Remove the screwdriver from the guide pin, and dismount the bearing cap by sliding it along the guide pin, see fig 2.
10)Remove the guide pin from the connecting rod.
Dismounting of Upper Big-end Bearing Shell
11)Pull the piston and connecting rod assembly upwards and remove the upper big-end bearing shell, see fig 3.
12) Lift the piston and connecting rod assembly up through the cylinder liner and out of the engine, see fig 4.
96.20 - ES0S