
Основы КСУ (Бормотов А) / Основы конструирования
.pdf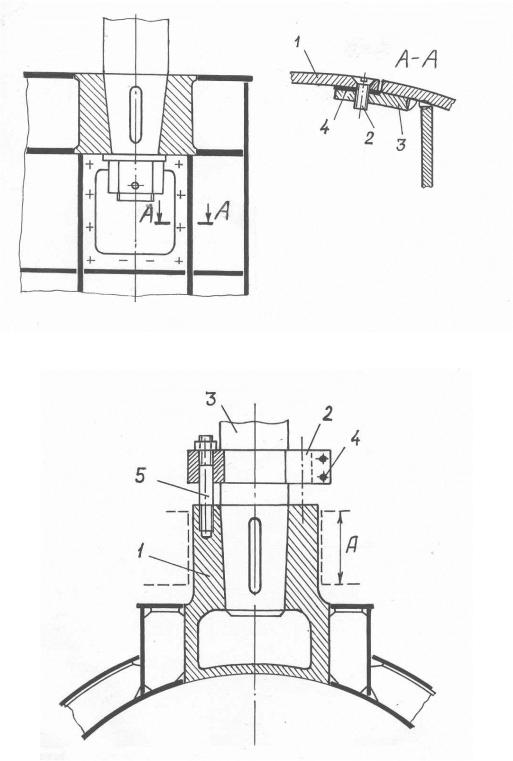
а)
б)
Рис. 4.40. Конусное соединение баллера:
а- с пером руля; б – с насадкой;
1- съемный лист; 2 – винт; 3 – планка; 4 – прокладка; 5 – шпильки;
А– место установки нижнего подшипника баллера
120
Передача крутящего момента Mкр в конусном соединении осуществляется с помощью одной, двух шпонок. Размеры сечения шпонки b h принимают по ГОСТ 23360-78 в зависимости от среднего диаметра конуса dcp (табл. 4.14), а
длину шпонки l назначают на основе проверки ее прочности на смятие [2]:
|
|
|
|
4M кр |
|
|
|
||
|
|
l |
|
|
|
. |
|
|
|
|
|
d |
cp |
h σ |
|
|
|
||
|
|
|
|
см |
|
|
|
||
Таблица 4.14. Размеры призматических шпонок |
|
||||||||
|
|
|
|
|
|
|
|
||
Диаметр вала, мм |
50…58 |
58…65 |
|
65...75 |
75...85 |
85...95 |
95...110 |
||
Шпонка b h, мм |
16 10 |
18 11 |
|
20 12 |
22 14 |
25 14 |
28 16 |
||
Глубина паза вала / |
|
|
|
|
|
|
|
|
|
ступицы, мм |
6,0/4,3 |
7,0/4,4 |
|
|
7,5/4,9 |
9,0/5,4 |
9,0/5,4 |
10,0/6,4 |
|
|
|
|
|||||||
Диаметр вала, мм |
110...130 |
130...150 |
150...170 |
170...200 |
200...230 |
230...260 |
|||
Шпонка b h, мм |
32 18 |
36 20 |
|
40 22 |
45 25 |
50 28 |
56 32 |
||
Глубина паза вала / |
11,0/7,4 |
12,0/8,4 |
|
|
13,0/9,4 |
15,0/10,4 |
17,0/11,4 |
20,0/12,4 |
|
ступицы, мм |
|
|
|
|
|
|
|
|
|
|
|
|
|
||||||
Диаметр вала, мм |
260...290 |
290...330 |
330...380 |
380...440 |
440...500 |
|
|||
Шпонка b h, мм |
63 32 |
70 36 |
|
80 40 |
90 45 |
100 50 |
|
||
Глубина паза вала / |
20,0/12,4 |
22,0/14,4 |
25,0/15,4 |
28,0/17,4 |
32,0/19,5 |
|
|||
ступицы, мм |
|
|
|
|
|
|
|
|
|
4.12.4. Опоры баллера и пера руля
Угловая скорость перекладки рулей (насадок) невелика, а условия работы достаточно суровые: повышенная влажность, большие нагрузки, сложность подвода смазки, нерегулярный контроль работы. Это определило в качестве основной разновидности опор баллеров рулей и насадок применение подшипников скольжения. Лишь во внутренних помещениях судна при устройстве надежных систем смазки используются подшипники качения.
Опорами руля или поворотной насадки на ахтерштевне или боковых кронштейнах служат штыри – подшипники скольжения с консольной осью, работающие в условиях смазки водой. Тело штыря изготавливают из качественной или легированной стали (лишь на малых судах иногда применяют стали марок Ст 4, Ст 5). Рабочую поверхность штыря длиной 1,0…1,5 его диаметра нередко снабжают износо- и коррозионно-стойкой облицовкой из бронзы, латуни, нержавеющей стали, которая напрессовывается на штырь (рис. 4.41). В
121

этом случае необходимо принять меры для исключения попадания воды между облицовкой и телом штыря, применяя различные уплотнения. На некоторых судах в качестве рубашки штыря применена наплавка бронзой с последующей механической обработкой. Конический хвостовик штыря, длиной не менее его диаметра, вставляется в бобышку, надежно приваренную к набору и обшивке пера руля. Хвостовик затягивается гайкой, которая тщательно стопорится от самоотвинчивания.
Рис. 4.41. Штыревая опора:
1 – петля ахтерштевня; 2 – петля руля; 3 – штырь; 4, 6 – уплотнения; 5 – гайка; 7 – втулка; 8 – рубашка; 9 – винт
Диаметр штыря назначают расчетом на прочность при изгибе его опорной реакцией, величина которой определяется по табл. 4.11:
|
3 |
|
, (4.47) |
d |
10R l 0,5h / σ |
||
где d |
- диаметр штыря без обли- |
цовки, мм; R - опорная реакция штыря, Н; l – длина цилиндрической части штыря, мм; h – высота втулки подшипника штыря, мм; материала штыря,
МПа.
В отверстие петли ахтерштевня вставляется втулка, материал которой можно выбрать по табл. 4.15 в зависимости от облицовки штыря. Размеры втулок назначают по рекомендациям [2, 19]. Втулки закрепляют в петле буртиками, стопорными шайбами, запрессовкой. Толщину втулки берут в пределах 10….15 % диаметра штыря (при больших диаметрах – меньшие значения процентов). Высота втулки составляет 0,7…1,3 диаметра штыря, что уточняется по величине удельного давления в подшипнике:
p |
R |
p , |
(4.48) |
|
d o h |
||||
|
|
|
где d0 - диаметр штыря с облицовкой, мм; [p] – допустимое удельное давление, указанное в табл.4.16.
122

Таблица 4.15. Втулки подшипников штырей
Материал облицовки штыря |
Материал втулки |
Штырь без облицовки |
Бронза, баббит, резина |
Бронза, латунь |
Бакаут |
Нержавеющая сталь |
Бронза, текстолит, капрон |
Таблица 4.16. Допустимые удельные давления для подшипников баллера
Материалы |
Допустимые удельные давления, Н/мм2 |
|
трущихся пар |
Смазка водой |
Смазка маслом |
Сталь по бронзе |
6,7 |
10,0 |
Сталь по баббиту |
- |
4,4 |
Сталь или бронза по бакауту |
2,4 |
- |
Сталь по пластмассе |
2,0 |
- |
Сталь по резине |
2,0 |
- |
Полимер SXL (Канада) |
12,0 |
- |
Нижняя опора баллера, размещаемая в верхней части гельмпорта и включает в себя опорный подшипник скольжения и сальниковое уплотнение, смонтированные в общем корпусе (рис. 4.42). Втулку подшипника делают бронзовой либо биметаллической (стальная втулка с наплавкой бронзой или латунью). Внутреннюю поверхность втулки снабжают канавками для подвода смазки. Размеры втулки назначают расчетом по удельному давлению с помощью выражения (4.48), в котором реакция опоры R и диаметр баллера dб уже известны по расчету прочности баллера.
Сальниковое уплотнение состоит из набивки и нажимной втулки, поджимаемой с помощью шпилек. Набивку выполняют из стандартных плетеных хлопчатобумажных или пеньковых шнуров квадратного сечения, пропитанных антифрикционным составом. Размер шнура – его сторону можно определить по соотношению
|
|
|
|
s 2 dб , мм, |
(4.49) |
где dб – диаметр баллера, мм.
Шнур, сечением меньше 4 4 мм и больше 28 28 мм, не применяют. Число колец набивки по высоте делают не менее четырех, но и не более шести. Основные размеры типовых подшипников, изображенных на рис. 4.42, приведены в табл. 4.17.
Верхняя опора баллера представляет собой опорно-упорный подшипник, сочетающий в себе опорный подшипник скольжения, снабженный бронзовой или биметаллической втулкой, и стандартный шарикоподшипник, опирающий-
123
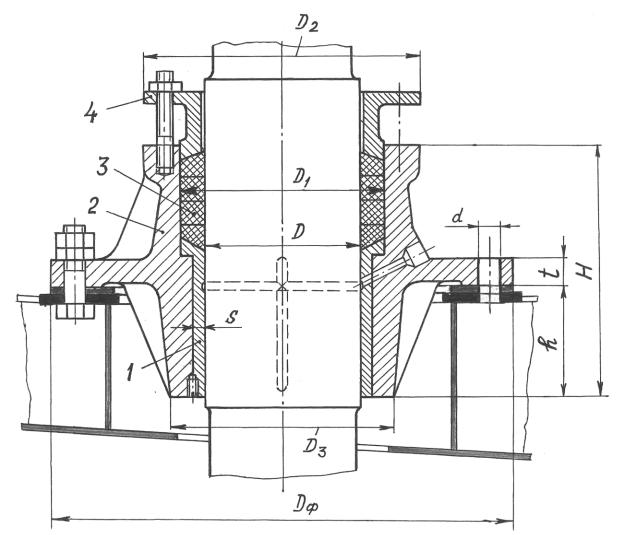
ся на корпус подшипника скольжения. Масса баллера вместе с пером руля или насадкой воспринимается шарикоподшипником благодаря установке врезного разъемного кольца (рис. 4.43) или нажимной гайки. Для смазки подшипников предусмотрена установка колпачковой или пресс-масленки. Для исключения осевого перемещения баллера вверх (при посадке судна на мель) под корпусом подшипника может устанавливаться с небольшим осевым зазором упорное кольцо.
Рис. 4.42. Нижняя опора баллера:
1 – втулка; 2 – корпус; 3 – сальниковая набивка; 4 – нажимная втулка
Размеры втулки подшипника скольжения подбирают по приведенному выше выражению (4.48), а упорный шарикоподшипник проверяют по допусти-
мой статической нагрузке: |
|
Qст n Pp Pб , |
(4.50) |
124

где n – коэффициент запаса прочности, n =4…5 - для подвесных рулей и насадок; n = 2…3 – для рулей и насадок с опорой на пятке ахтерштевня; Pp , Pб -
вес руля (насадки) и баллера.
Рис. 4.43. Верхняя опора баллера:
1 – корпус; 2 – втулка; 3 – шарикоподшипник; 4 – хомут; 5 – кольцо упорное
Вес руля и баллера должен определяться по их чертежам. При отсутствии таковых приближенно можно принять [19]
|
P 5,9F |
; P 7,7 d 2 |
l 1 , кН, |
(4.51) |
|
|
p |
p |
б |
|
|
где F |
площадь руля, м2 ; |
dб, |
l – диаметр и длина баллера, м; = 7,8 т/м3 - |
||
p |
|
|
|
|
|
плотность стали баллера.
125

Основные размеры типовых подшипников, изображенных на рис. 4.43, указаны в табл. 4.17.
Таблица 4.17. Размеры подшипников баллера, мм
D |
D1 |
D2 |
|
D3 |
Dф |
S |
H |
h |
t |
Болты |
|
|
|
Нижний опорный подшипник (рис. 4.42) |
|
|
|||||
230 |
295 |
400 |
330 |
670 |
15 |
360 |
170 |
40 |
8М 30 |
|
250 |
315 |
420 |
350 |
670 |
15 |
380 |
180 |
40 |
8М 30 |
|
280 |
345 |
450 |
385 |
750 |
15 |
410 |
200 |
40 |
8М 30 |
|
300 |
370 |
475 |
405 |
750 |
20 |
440 |
220 |
40 |
8М 30 |
|
380 |
465 |
570 |
490 |
1000 |
20 |
550 |
300 |
50 |
8М 42 |
|
420 |
510 |
615 |
540 |
1000 |
20 |
590 |
330 |
50 |
8М 42 |
|
450 |
540 |
645 |
580 |
1100 |
25 |
620 |
350 |
50 |
8М 42 |
|
480 |
570 |
675 |
610 |
1100 |
25 |
660 |
400 |
50 |
8М 42 |
|
|
|
Верхний опорно-упорый подшипник (рис. 4.43) |
|
|
||||||
150 |
140 |
200 |
210 |
470 |
15 |
205 |
110 |
30 |
8М 24 |
|
160 |
150 |
215 |
230 |
500 |
15 |
220 |
120 |
30 |
8М 24 |
|
190 |
180 |
250 |
250 |
570 |
15 |
255 |
150 |
30 |
8М 24 |
|
210 |
200 |
280 |
275 |
630 |
15 |
280 |
170 |
30 |
8М 30 |
|
230 |
220 |
300 |
310 |
670 |
15 |
305 |
185 |
30 |
8М 30 |
|
250 |
240 |
300 |
330 |
690 |
15 |
305 |
205 |
30 |
8М 30 |
|
300 |
280 |
350 |
400 |
810 |
20 |
365 |
240 |
40 |
8М 30 |
|
360 |
340 |
420 |
480 |
950 |
20 |
435 |
290 |
50 |
8М 42 |
Приведенные в пособии схемы и рисунки надо рассматривать лишь как учебные примеры, далеко не исчерпывающие всего многообразия реально применяющихся конструкций.
4.13. Выбор размеров деталей рулевого устройства по Правилам Речного Регистра
Правила классификации и постройки судов внутреннего плавания (часть III) Речного Регистра [17] требуют, чтобы диаметр баллера руля или насадки обосновывался расчетом при действии наибольших гидродинамических нагрузок. Вместе с этим, Правила дают возможность назначить диаметр баллера руля в районе нижнего подшипника путем упрощенного расчета:
для подвесного руля
|
|
k |
|
|
, см; |
|
||
d 4,623 |
c F v2 |
r 2 0,5h l 2 |
|
(4.52) |
||||
|
||||||||
|
|
|
p |
|
|
|
|
|
|
|
ReH |
|
|
|
|
для руля с нижней опорой на пятке ахтерштевня
126

|
|
k |
|
|
|
|
|
|
|
||
d 4,623 |
c F v2 |
|
r 2 0,029h2 , см; |
(4.53) |
|||||||
|
|||||||||||
|
|
ReH |
p |
|
|
|
|
|
|||
|
|
|
|
|
|
|
|
||||
для руля со штырями на петлях ахтерштевня |
|
||||||||||
|
|
|
|
|
|
||||||
d 4,623 |
k |
c F v2r , см, |
(4.54) |
||||||||
|
|||||||||||
|
|
|
|
|
ReH |
|
p |
|
|||
|
|
|
|
|
|
|
|
|
|
где k – коэффициент запаса прочности, принимаемый 2,0 для судов классов Р и Л и 2,5 для судов классов М и О; ReH - предел текучести материала бал-
лера, МПа; c – |
коэффициент, учитывающий удлинение руля |
λ |
: |
||
|
|
|
|
||
с 13,87 22,025 ; |
ζ - коэффициент, учитывающий влияние гребного винта (ζ |
||||
= 1,0 для рулей за винтом и ζ = 0,9 для рулей вне потока винтов); |
Fp |
- |
|||
площадь пера руля, м2; v - расчетная скорость хода судна в грузу, км/ч; |
r – от- |
стояние точки приложения условной расчетной нагрузки от оси баллера, м;
определяемое по выражению r b 1
p 3
|
3 |
|
F |
|
2 |
|
|
|
|
|
|
||||
|
|
|
1 |
|
|
|
a ; bр – ширина пера руля, м; hр |
|
|
|
|||||
|
2 |
|
F |
|
|
|
|
|
|
|
p |
|
|
|
|
|
|
|
|
|
|
|
– высота пера руля, м; F |
- площадь балансирной части руля, м2; a – отстоя- |
1 |
ние оси вращения от передней кромки руля на уровне центра тяжести его площади, м; l – расстояние между верхним торцем руля и нижней опорой баллера, м.
Условная расчетная реакция нижней опоры баллера должна приниматься не менее определенной по выражениям:
для подвесного руля
R 0,01c F v |
2 |
|
|
|
/ f |
, кН, |
(4.55) |
|
|
0,5h l f |
|||||
p |
|
|
p |
|
|
|
|
где f – расстояние между опорами баллера, м; |
|
|
|
|
|||
для руля с нижней опорой на пятке ахтерштевня |
|
|
|
||||
R 0,0054c F v2 |
, кН, |
|
(4.56) |
||||
|
|
|
p |
|
|
|
|
где обозначения величин указаны выше. |
|
|
|
|
|
|
|
Толщина обшивки пустотелого руля должна приниматься не менее |
|
||||||
t kd 3, мм, |
|
|
|
(4.57) |
где d – диаметр баллера, мм, рассчитанный по выражениям (4.52)…(4.54); k – коэффициент, равный 0,025 – для судов класса М, 0,020 – для судов класса О, 0,015 – для судов классов Р и Л.
127
Толщина листов пластинчатого руля должна быть не менее tп k'd 4 , мм, где коэффициент k'принимают для судов перечисленных выше классов соответственно: 0,080; 0,055; 0,030.
Толщина листов наружной обшивки насадки и ее стабилизатора должна приниматься не менее tн=t+1, мм, если t определена по (4.57). Толщина внутренней обшивки насадки назначается на 25% больше толщины наружной обшивки, а средний пояс этой обшивки рекомендуется делать из нержавеющей стали толщиной вдвое больше толщины внутренней обшивки.
В любом случае толщина листов пера руля или насадки не должна быть меньше толщины обшивки корпуса в корме судна.
Соединение руля или насадки с баллером должно выполняться с помощью горизонтальных фланцев. В отдельных случаях, одобренных [17], допускается конусное соединение. Во фланцевом соединении суммарная площадь всех болтов или шпилек должна быть не менее
F= 0,3dб2 ,
где dб – диаметр баллера в нижнем подшипнике.
В конусном соединении длина конуса должна быть не менее полутора диаметров баллера, а конусность – не более 1:10. По образующей конуса необходимо установить шпонку, размеры которой определяются расчетом прочности.
Опорами баллера служат подшипники скольжения, высота втулки которых должна быть не менее
h = 10R/pdб, см,
где R – реакция опоры, кН, определяемая по выражениям (4.55) и (4.56); dб – диаметр баллера в опоре, см; p – допустимое удельное давление, МПа, для материала втулки подшипника, принимаемое по табл. 4.15.
Высота опорной поверхности втулки должна быть не менее h = 0,8 dб.
Пример расчета
Требуется подобрать размеры основных деталей рулевого устройства речного судна класса О. Конструктивная схема крепления руля соответствует схеме рис. 35, г, а расчетная схема балки баллер-рудерпис – второй схеме табл.
4.11.
Исходные данные. Максимальное значение рулевой силы P=174 кН. Максимальное значение гидродинамического момента Mmax = 60кНм. Радиус рум-
128
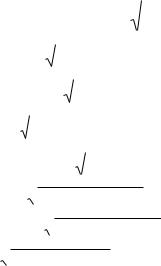
пеля рулевой машины r = 0,4 м. Расстояния между опорами баллера ( в соответствии с обозначениями табл. 4.11): h = 1,61 м, a = 0,30 м, b = 1,25 м, c=0,95 м.
Расчет прочности баллера
1. |
Расчетное значение крутящего момента на баллере |
||||||||||||||||
|
Mб = 1,2 Mmax = 1,2∙60 = 72 кН·м. |
||||||||||||||||
2. |
Окружное усилие рулевого привода |
|
|
|
|
|
|
|
|
|
|
|
|
||||
|
T0 = Mб /r = 72/0,4 = 180 кН. |
||||||||||||||||
3. |
Значения реакций опор баллера (табл. 4.11): |
|
|
|
|
||||||||||||
|
R1 = P(a+b+c+0,5h)/(b+c)+T0 c/(b+c)= |
||||||||||||||||
|
= 174(0,3+1,25+0,95+0,81)/2,20+180·0,95/2,20 = 340 кН; |
||||||||||||||||
|
R2 = T0 b/(b+c) -P(a+0,5h)/(b+c)= |
||||||||||||||||
|
= 180 1,25/2020-174(0,30+0,81)/2,20 = 14 кН. |
||||||||||||||||
4. |
Значения изгибающих |
моментов |
баллера |
в характерных сечениях |
|||||||||||||
(табл. 4.11): |
|
|
|
|
|
|
|
|
|
|
|
|
|
|
|
|
|
|
M0 = Ph/2 = 174∙1,61/ 2 = 140 кНм; |
||||||||||||||||
|
M1= P (a + h/2) = 174(0,30 + 1,61/2) = 192 кН·м; |
||||||||||||||||
|
MT = – R2 c = – 14∙0,95 = – 13,3 кН·м. |
||||||||||||||||
|
|
|
|
|
|
|
|
|
|
|
|
|
|
|
|
||
5. |
Значения приведенных моментов M |
np |
|
|
|
M 2 |
0,75M 2 : |
||||||||||
|
|
|
|
|
|
|
|
|
|
|
из |
|
|
кр |
|||
|
|
|
|
|
|
|
|
|
|
|
|||||||
у верхнего торца руля Mпр |
= 1402 0,75 722 |
= 153 кН·м, |
|||||||||||||||
|
|
|
|
|
|
|
|
||||||||||
у нижней опоры баллера Mпр = 1922 0,75 722 |
= 202 кН·м, |
||||||||||||||||
|
|
|
|
|
|
|
|||||||||||
у ступицы румпеля Mпр = 13,32 0,75 722 |
|
|
= 64 кН·м. |
||||||||||||||
|
|
|
|
|
|
|
|
|
|
||||||||
6. |
Размеры баллера по сечениям d 3 10M |
np |
/ : |
|
|
|
|
||||||||||
|
|
|
|
|
|
|
|
|
|
|
|
|
|
|
|
|
у верхнего торца руля d1 ≥310 153000 /141 = 22,2 см,
у нижней опоры баллера d2 ≥310 202000 /141= 24,3 см,
у ступицы румпеля d3 ≥ 310 64000 /141 = 16,6 см.
В расчете принято [σ] = 0,45 ReH = 0,45∙314 = 141 МПа в соответствии с табл. 4.10 для стали 35 ГОСТ 1050-88.
Диаметр баллера у верхней опоры можно назначить по допустимому давлению опорного подшипника скольжения (сталь по бронзе), приняв высоту
129