
В.И.Чуешов, Л.А.Мандрыка, А.А. Сичкарь Оборудование и основы проектирования химико-фармацевтических производств
.pdf
разгрузке устанавливаются на специальные подставки и присоединяются к магистралям воздуха и распределения хладонов. В бочки поочередно по
дается изб1,почное давление до 1,2 МПа (сжатым воздухом или азотом), и хладон псрего11яется в дозировочную емкость 7, установленную на весах 6.
За количеством перегоняемых хладонов следят по весам. После этого ежа-
Рис.2.23. Принци пиальная схема приго товления смесей про пеллентов.
тый воздух подается в емl<ость 7 и смесь отrуда передавливается в одну из
/емкостей 5. Из двух емкостей 5 одна работает, другая подготавливается. Благодаря наличию двух емкостей 5 для смеси хладонов линия наполнения может работать бесперебойно. На линии приготовления хладонов парал лельно компрессору 3 установлены баллоны с азотом 2. В случае неис
правности компрессора можно подключиться к азотным баллонам. Таким образом, ликвидируется всякая возможность простоя.
При данной технологии возможны некоторые потери хладонов: в ем костях остается смесь сжатого воздуха с rазообразным хладоном, для по вторного заполнения емкостей необходимо выпускать ее в атмосферу. Чтобы избежать этих потерь, смесь перекачивают обратно из емкостей 5 и
7 в бочки 1.
Для транспортировки (подачи) пропеллентов на линию наполнения применяют два способа: 1) передавливание пропеллента из емкости, в ко торой он хранится, с помощью избыточного давления, создаваемого в ем кости либо азотом, либо нагретыми парами самих хладонов; 2) перекачи вание насосами.
Величина избыточного давления в емкостн с пропеллентом, которое создается с помощью подачи в емкость азота, зависит от давления' насы
щенного пара пропеллента. Обычно создают давление азот-а в системе в пределах 0,8-1,5 МПа в зависимости от типа пропеллента.
Наполнение и оформление аэрозольных упаковок. Комплекс технологических операций наполнения аэрозольных упаковок производит
ся на линиях наполнения, которые могут представлять собой либо серию отдельных полуавтоматов, либо автоматическое оборудование, компактно
объединенное в одну линию с помощью различных конвейеров и транс портеров. Обычно линии наполнения с помощью транспортирующих средств связаны с линиями упаковки готовой продукции.
Принципиальная схема технологической линии наполнения аэрозоль
ных упаковок представлена на рис. 2.24. Чистые баллоны поступают на приемное устройство 1 начале конвейера 2. После продувки их сжатым
воздухом 3 они по конвейерной ленте подаются на расфасовку ко1щентра та 4, заполняются и д1щ.жутся дальше к месту вакуумизации и крепления клапана 5. Подача концентрата к дозатору, где заполняются баллоны, в большинстве случаев осуществляется по трубопроводам из отделения их приготовления.
Одновременно с креплением клапанов на баллонах (герметизацией) путем обжима или закалки производится вакуумизация баллонов. Удале ние воздуха может также быть осуществлено путем введения капли ежи женного пропеллента в баллон до его герметизации. Для этого в линию встраиваются специальные устройства, герметизированные баллоны по даются к автомату наполнения 6, где под давлением в них нагнетается доза пропеллента, поступающая к линии по специал ным коммуникациям с
участка подготовки пропеллентов.
.. ..
Рис.2.24. Схема технологической линии наполнения аэрозольных упаковок (объяснение в тексте).
Заполненные баллоны испытываются на прочность и герметичность в водяной ванне 7 при температуре 45-50°С в течение 5-20 мин (в зависи мости от типа баллона). После ванны баллоны сушатся струёй теплого воздуха в сушильном туннеле 8, взвешиваются на автоматических весах 9, затем на них надеваются распылители 1О и защитные колпачки 11. На го товые баллоны наносится маркировка серии 12, после чего они поступают на упаковку 13.
Типовая планировка производственного помещения для наполнения аэрозольных упаковок со всей последовательностью технологических опе раций представлена на рис. 2.25.
•
11
Рис.2.25. Схематическое изображение технологической линии наполнения и упа ковки аэрозолей (объяснение в тексте)
60 |
61 |
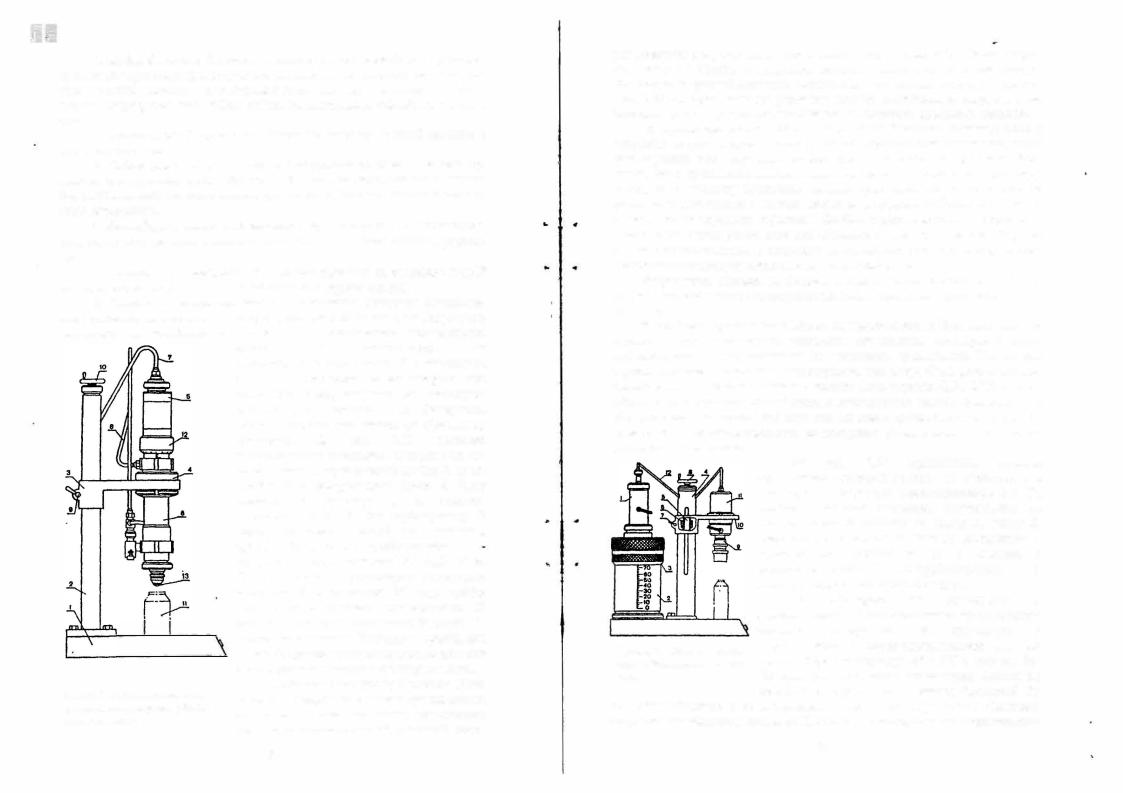
\. Мойка баллонов. Баллоны со склада руч ым способом загружают ся на ле1пу транспортера, откуда они автоматически надеваются на держа тели моечной машины I и, поступая в различные зоны машины, проходят стадии предварительной мойки, мойки, ополаскивания, обработки паром и
сушки.
2. Транспортер 2 с жит для подачи баллонов от моечной машины к линии наполнения.
3. Подающий стол 3 - начало производственной линии. На него по даются чистые после мойки баллоны. Он является накопителем баллонов для выравнивания высокой производительности моющих машин с автома тами наполнения.
4.Конвейерные ленточные транспортеры 4 служат для автоматиче ской связивсех технологических операций на линии наполнения и упаков
'ки.
5.Автомат для продувки 5 служит для удаления из баллонов струёй сжатого воздуха случайно попавшей пыли или других частиц.
6.Наполнение концентратом Для наполнения баллонов концентра
том применяются автоматические дозирующие установки. Они могут быть роторного или линейного типа с различным количеством наполняющих головок в зависимости от производительности линии. В зависимости от агрегатного состояния концентрата, они могут быть предназначены для растворов, суспензий, пен, порошков и др. Дозировка, как правило, осуществляется по объемному принципу. На рис. 2.26 показана наполнительная установка, которая состоит из основания 1, вертикальной стойки 2, крон штейна 3 и дозирующего блока 4. Блок состоит из дозатора 5 и головки впрыскивания 6, 13. По трубопроводу 7 подводится сжатый воздух под дав.пением
0,4-0,5 МПа, а по трубопроводу 8 концентрат под давлением О, 1-0,15 МПа. Положение блока 4 регулируют с помощью маховика 9 и рукоятки 1О так, чтобы нижняя точка головки впрыскивания 13 была на 5 мм выше горловины баллона 11. Перед наполнением баллонов вращением лимба 12 против соответствующего деления шкалы устанавливается необходимая доза.
Рис.2.26. Установка для дози |
7. Удаление воздуха из баллонов. Если |
|
удаление воздуха из баллона производится |
||
|
||
рования концентратов (объяс |
сжиженным rазом, то линия наполнения |
|
нение в тексте) |
||
оснащается автоматической головкой, кото- |
||
|
рая дозирует одну-две капли сжиженного хладона (рис.2.27). Капля хладо на, попадая в баллон и испаряясь, вытесняет находящийся в нем воздух. Для баллона средней величины достаточно I мл сжиженного газа, что соз
дает 250 мл пара. Если для удаления воздуха используется вакуумизация баллона, то этот процесс осуществляется на автомате крепления клапана.
8. Крепление клапана. После наполнения баллонов концентратом и удаления из них воздуха производится их герметизация клапанами, кото рые вручную или полуавтоматически устанавливаются в горловины -бал лонов. Если производительность линии наполнения более 5 млн. упаковок в год, то к автомату крепления клапана пристраивается автоматическое устройство для подачи и вставки клапанов в горловины баллонов. В зави симости от конструкции горловины баллона крепление клапана осуществ ляется с помощью разжимных или обжимных цанг или закаткой. Закатка клапана осуществляется с помощью вращающихся роликов, которые при вальцовывают капсулу клапана к горловине баллона.
Закрепление клапана на баллоне является самой ответственной опе рацией, так как плохое его закрепление может привести к разгерметизации упаковки.
9. Введение пропеллента. Вслед за герметизацией баллонов они по ступают к специальным автоматическим порционным дозаторам 9, кото рые осуществляют впрыскивание под давлением пропеллента. Так же, как и установки для наполнения концентратом, они могут быть роторного или линейного типа. Рабочее давление должно быть порядка 0,7-1 МПа в зави симости от вводимого пропеллента и конструкции самого дозатора. Так как производительность автоматов для введения пропеллента не всегда со ответствует производительности предыдущих узлов линии, на линии их может быть несколько.
|
На рис. 2.27 представлен дозатор |
||||||
|
пропеллента, который состоит из дозирующего |
||||||
|
цилиндра 1 и силового пневмоцилиндра 2-3. На |
||||||
|
стойке 4 имеется механизм регулировки по |
||||||
|
высоте, который состоит из винта 5, гайки 6, |
||||||
|
рукоятки 7 и маховика 8. Головка наполнения 9 |
||||||
|
крепится |
на |
кронштейне I О |
и связана |
с |
||
|
пневмоцилиндром 11. По трубопроводам 12 к |
||||||
|
дозатору подводится сжатый воздух. |
|
|||||
|
1О. |
Проверка |
на |
прочность |
и |
||
|
герметичность. После заполнения пропеллентом |
||||||
|
баллоны |
проверяются |
на |
прочность |
и |
||
Рис.2.27. Дозатор хладо |
герметичность |
в термостатированной водяной |
|||||
ванне 1О при температуре 45 ± 5°С в течение 15- |
|||||||
нов {объяснение в тек |
|||||||
сте). |
20 мин |
(для покрытых стеклянных баллонов) |
|||||
|
или 5-10 мин (для металлических баллонов). За |
||||||
это время баллоны и их содержимое нагреваются. |
При этом в баллонах |
||||||
создается повыше}fное давление. Баллоны, не выдержавшие повышенного |
63
62

в ту или и1.1ую сторону баллоны автоматически отбраковываются.. |
|
|
дух, так как он может создать повышенное давление в упаковке либо не- |
||
13. Проверка давления |
Эта операция, в основном, осуществляется |
|
|
||
|
|
В свя1и с тем, что в качестве пропелле,пов при производстве фарма |
|||
для аэрозольных упаковок, содержащих в качестве пропеллентов сжатые |
|
|
|||
газы, наличие которых в баллоне можно проверить лишь с помощью ма |
|
|
|||
нометра. Поэтому все баллоны поступают к автоматическому устройству |
|
|
|||
13, которое определяет давление внутри баллонов и отбраковывает балло |
|
|
|||
ны, в которых отсутствует пропеллент или содержится малое его количе |
|
|
|||
ство. |
|
|
|
|
|
давления, взрываются Если баллоны прочны, но не герметичны, то при |
|
|
цевтических аэрозолей могут применяться как сжиже1111ые, так и сжатые |
||
повышенном давлении происходит выделение пропеллента, что видно по |
|
|
газы, сущссrвуют два основных метода наполнения: под давлением и при |
||
поднимающимся в воде пузырькам. Водяная ванна специально приспособ |
|
|
низких, температурах Причем, если в качестве пропеллента применяются |
||
лена для визуального контроля. Для предохранения от взрывов не выдер |
|
|
сжиженные газы, то наполнение может осуществляться обоими методами. |
||
жавших испытания баллонов ванна снабжена предохранительным колпа |
|
|
Если в качестве .пропеллента применяются сжатые газы, наполнение про |
||
ком из органического сте1<11а. |
|
|
|
изводится только первым методом. |
|
11. Сушка баллонов Для удаления воды с поверхности испытанных в |
|
|
|
||
ванне баллонов последние по конвейеру поступают в сушильный туннель с |
|
|
Напол11е1111е под давле11нем. Это наиболее распространенный в на |
||
направленными на них форсунками 11. Из форсунок на баллоны подается |
|
|
стоящее время метод наполнения. Весь процесс наполнения представлен |
||
струя теплого воздуха. |
|
|
|
на рис. 2.28. Пропеллент вводится в баллон при комнатной температуре |
|
12. Взвеишвание Сухие заполненные баллоны с помощью автомати |
|
|
под давлением через клапан или под него,(через горловину баллона). Не |
||
ческих весов 12 проходят контрольное взвешивание. При отклонении веса |
• |
посредственно перед герметизацией необходимо удалить из баллона воз |
|||
|
|
|
|
|
|
14. |
Установка распылителя и проверка качества распыления Эти |
|
|
|
|
операции осуществляются специальными автоматическими устройствами, |
|
|
|
||
встроенными в линию наполнения. |
|
|
|
||
15. Одевание защитного колпачка. Производится на линии с помо |
|
|
|
||
щью ориентирующего автоматического приспособления 15. |
|
|
|
||
16. Маркировка Автоматическое печатное устройство 16 на боковую |
|
|
|
||
часть баллона (обычно снизу) наносит маркировочные данные (серию и |
|
|
|
||
|
|
|
|||
срок годности). Маркировка также может производиться выдавливанием |
|
|
|
||
серии на алюминиевой части клапана (капсуле). |
|
|
Рис.2 28 Схема автоматической линии наполнения (производства) аэрозолей |
||
К |
линии наполнения |
обычно пристраивается линия упаковки |
|
|
|
|
|
благоприятно воздействовать на препарат, а также способствовать разви |
|||
(рис.2 25, поз.17-20), осуществляющая: |
.. |
||||
17. Упаковку баллонов в пеналы |
|
|
тию коррозионных процессов в металлических баллонах. |
||
18. Вставку в пенаqы инструкций |
|
|
Известны четыре метода удаления воздуха из баллона. Лучший спо |
||
19 |
Вставку в пенаqьz насадок и закрытие пеналов |
|
|
соб удаления воздуха - введение капли сжиженного газа (пропеллента) |
|
20 |
Упаковку пена 1ов с баллонами в транспортную тару и ее обанде- |
|
|
Кроме того, его можно удалить с помощью вакуумного отсоса, введения |
|
рwиwн |
|
|
|
инертного газа или же через клапан, перевернув заполненный баллон и |
|
Методы наполнения аэрозольных баллонов. Под наполнением аэ |
|
|
нажав на шток клапана Последний способ не пригоден при массовом про |
||
розольных упаковок понимают весь процесс производства любых аэрозо |
|
|
изводстве. |
||
лей: от заполнения баллонов концентратом, крепления клапана, введения |
|
|
Концентрат также может содержать воздух, поэтому перед наполне |
||
пропеллента, проверки на прочность и герметичность, обеспечения всеми |
|
|
нием баллонов его необходимо удалить. Для этого рекомендуется сле |
||
комплектующими (распылителями, насадками, защитными колпачками) до |
|
|
дующий метод удалений воздуха. В концентрат перед наполнением вво |
||
оформления и упаковки готовой продукции. |
|
|
дитс.11 инертный газ (например, азот). Поток мельчайших пузырьков азота |
||
Однако, когда говорят о методах наполнения баллонов, то обычно |
|
|
инжектируют в препарат в специальном устройстве. Кислород десорбиру |
||
имеют в виду пути или способы введения в них концентрата и пропеллен |
|
|
ется вследствие разности парциальных давлений и мигрирует в пузырьки |
||
та. |
|
|
|
|
|
64 |
65 |
|

азота. После достижения статического равновесия между газом и жидко |
|
|
|
|
|
стыо поток раствора идет в резервуар. Там пузырьки азота с включенным |
|
|
|
|
|
кислородом поднимаются к поверхности и удаляются. Установка такого |
|
|
|
|
|
устройства в линию непосредственно перед наполнительным автоматом |
|
|
|
|
|
может дать определенный эффект - с помощью инжектирования азота уда |
|
|
|
|
|
ется понижать содержа ие кислорода до 2 объемных % и менее от перво |
|
|
|
|
|
начальной величины. |
|
|
|
|
|
Напол11е1111с сжижснным11 пропсллснтами. Последовательность |
|
|
|
|
|
операций при наполнении сжиженными газами зависит от выбранного |
|
|
|
|
|
способа удаления воздуха и введения пропеллента. При введении пропел |
|
|
|
|
|
лента нелосредственно через клапан наполнительная головка герметически |
|
|
|
|
|
соединяется со штоком клапана, нажимает на него, и под давлением про |
|
|
|
|
|
изводится впрыск отмеренной дозы пропеллента (рис. 2.29). Первой ос |
|
|
|
|
|
новной перацией при этом методе является введение в баллон отмеренной |
|
|
|
|
|
дозы концентрата. Затем в баллон вводится капля хладона для вытеснения |
|
|
|
|
|
воздуха из баллона. После закрепления клапана через него вводится про |
|
|
Рис 2.29. Введение пропеллен |
Рис.2.30. Автомат для наполнения |
|
пеллент. |
|
|
|
баллонов под клапан |
|
|
|
|
та в баллон под давлением: |
||
Введение пропеллента через горловину баллона (под клапан) исполь |
|
|
|
||
|
|
1 - баллон; 2 -наполнительная го |
|
||
зуется не только в тех случаях, когда клапан не приспособлен для напол |
|
|
ловка, 3 - клапан, 4 - концентрат; |
|
|
нения баллона через него, но и в обычных условиях наполнения для уве |
|
|
S-пропеллент |
|
|
личения производительности оборудования, так как скорость наполнения |
|
|
|
|
|
через клапан, имеющий отверстие с малым сечением, значительно ниже, |
|
|
|
|
|
чем при введении под клапан. При этQ способе пропеллент вводится в |
|
|
|
|
|
баллон непосредственно перед закреплением клапана. Этот способ имеет |
|
|
|
|
|
различные разновидности в зависимости от того, как соединяется баллон с |
|
|
|
|
|
наполнительной головкой. Итальянская фирма "Solfrene S.p.A" разработала |
|
|
|
|
|
наполнительную установку (рис. 2.30). Наполнение баллонов концентра |
|
|
|
|
|
том, пропеллентом и герметизация клапаном происходят в одном рабочем |
|
|
|
|
|
цикле (рис. 2.31). Наполняемый баллон при этом предварительно изолиру |
|
|
|
|
|
ется от окружающего пространства герметичным кожухом. |
|
|
|
|
|
Швейцарские и немецкие фирмы разработали варианты машин, где |
|
|
Рис. 2.31. Наполнение баллонов пропеллентом под клапан с предварительной изо |
||
изолируется не весь баллон, а только его горловина (рис. 2.32). В этом слу |
.. |
.. |
|||
|
|
ляцией баллона от окружающей среды герметичным кожухом: |
|||
чае потери пропеллента несколько меньше. Техника заполнения под кла |
|
|
|||
|
|
1 - баллон с незакрепленным клапаном, 2 - герметизация баллона от окружающей среды, 3 |
|||
пан требует в три раза меньших затрат времени, чем через клапан, увели |
|
|
- наполнение баллона и крепление клапана (а - подъем клапана цанговым устройством, б - |
||
3 |
3 |
|
|
удаление воздуха пропеллентом, в - заполнение готовой аэрозольной смесью, r - опускание |
|
чивая скорость заполнения до 500 см /с вместо 150 см /с. Однако этот спо |
|
|
|||
|
|
клапана и удаление паров пропеллента из кожуха), 4 - закрепление клапана, 5 - опускание |
|||
соб неприменим для баллонов с диаметром горловины менее 25 мм. |
|
|
|||
|
|
баллона |
|
||
Кроме описанных · способов введения |
сжиженных пропеллентов |
|
|
|
|
применяется способ их введения в два приема. При этом первоначально в |
Наполнение сжатыми пропеллентами. При использовании в каче |
|
баллон вводится смесь, состоящая из концентрата и части пропеллента в |
||
стве пропеллентов сжатых газов наполнение ими баллонов произ одится |
||
жидком виде. Испарение незначительного количества пропеллента приво |
||
под давлением через клапан. При этом методе сжатый газ не дозируют, а в |
||
дит к вытеснению из баллона воздуха, после чего баллоны герметизируют |
||
баллон вводится его такое количество, которое обесnечивает в упаковке |
||
клапанами. Остальная часть пропеллента вводится непосредственно через |
||
необ1содимое давление. Воздух из баллона может бьпь удален либо введе |
||
клапан. |
||
нием инертного газа перед герметизацией, либо введением капли хладона |
||
|
||
|
или вакуумизацией. |
66 |
67 |

Рис 2 32. 1 lа юлнение балло11а под клапан с изоляцией горло вины баллона:
1 - введс1те ко1щсн1рата; 2 - ва куумизация баллона; З - введение nроnеллента, 4 - герметизация балло11а.
После наполнения баллонов сжатыми газами обязательно должно быть измерено внутреннее давление, так как это единственный способ оп ределить наличие пропеллента в упаковке. Величину давления контроли- руют маIJометром.
Наполнение растворимыми сжатыми пропеллентами. Если сжа тый газообразный пропеллент растворим в концентрате (например, закись азота), то в этом случае наполнение баллона пропеллентом также осущест вляется через клапан, но при этом процесс должен сопровождаться энер гичным встряхиванием для лучшего поглощения пропеллента концентра том. Введение газа и встряхивание продолжаются до полного насыщения вещества и установления равновесия системы. Обычно это занимает до 20 с. Этот способ используют в основном для аэрозольной упаковки пищевых
продуктов.
Низкотемпературный метод. В литературе этот метод получил на звание "холодное наполнение" или «наполнение при низких температу раю>. Наполнение пропеллентом производится ускоренно через верхнее отверстие баллона (горловину), после чего баллон герметизируется клапа
ном.
Для сравнения основные стадии наполнения под давлением и при
низких температурах представлены на рис. 2.33 - А, Б. |
||
|
о о-. о |
|
-im-ш --,-·e- |
||
О, . |
2 |
. , 4 . , • |
Рис.2.33, А Основные стадии наполнения аэрозолей под давлением: |
||||||||
1 - мойка ба.плонов; 2 - введение препарата; 3 - удаление воздуха из балJ1она; 4 - герметиза |
||||||||
ция баллонов; 5 - введение про еллента; 6 |
|
- проверка на пр чность и герметичность |
||||||
- |
|
|
. |
|
о |
о |
|
|
/ |
uuu - -i-i- |
|||||||
г; |
|
|
/ |
э |
• |
• |
• |
U' z
Рис.2.33, Б. Основные стадии наполнения аэрозолей при низких температурах:
1 - мойка баллонов; 2 - охлаждение баллонов; З - введение препарата; 4 - введение проnеллен та; 5 - герметизация баллонов клапанами; 6 - проверка на прочность и герметичность.
|
|
При 11юкотемпературном методе баллоны хра11ятся в холодильнике с |
||||||
|
|
низкой ми11усовой температурой. Это предохраняет от резкого испарения' |
||||||
|
|
пропелле11та из заполняемого баллона. У рабочего места баллоны хранятся |
||||||
|
|
в переносных холодильных камерах и закладываются в машину непосред |
||||||
|
|
ственно перед заполнением. |
|
|
|
|
|
|
|
|
Концентрат и пропеллент охлаждаются так, чтобы избежать потерь |
||||||
|
|
при испарении. Пропеллент обычно охлаждается до температуры на 5'С |
||||||
|
|
ниже его температуры кипения и вводится в баллон за один пр"ем или |
||||||
|
|
порциями в зависимости от характера оборудования и величины баллона. |
||||||
|
|
Чтобы избежать больших потерь проnеллента (достигающих 5-15%) и уве |
||||||
|
|
личить скорость наполнения, третью и четвертую стадии объединяют. Для |
||||||
.. |
с |
этого концентрат и проnеллент смешивают и предварительно охлаждают в |
||||||
|
|
больших емкостях, а затем по передаточным линиям подают к головке на |
||||||
|
|
полнения. |
|
|
|
|
|
|
|
|
|
|
|
Из головки наполнения в баллон |
|||
|
|
Рис. 2.34. Напол- |
подается готовая смесь {рис.2.34), после |
|||||
|
|
пение баллона ох- |
чего баллон герметизируется клапаном. |
|||||
|
|
лаждеиной |
смесью |
Основным |
недостатком |
низ- |
||
|
|
концентрат |
а |
с |
котемпературного |
метода |
является |
|
|
|
пропеллент ом: |
|
образование |
льда |
на головке |
наполне- |
|
|
|
1 - баллон; 2 - на- |
||||||
|
|
ния, в результате чего ее необходимо |
||||||
|
|
полнительнЗJI голов- |
||||||
|
|
ка; 3 - готова смесь; |
периодически очищать. Кроме того, этот |
|||||
|
|
4 - клапан. |
|
|
метод не пригоден; для веществ с |
высокой вязкостью, а также для растворов, содержащих воду. Также известно, что охлаждение отрицатель но сказывается на стабильности эмульсий. Поэтому этот метод может бьrrь использован, тех случаях, когда в баллон вводятся большие количества веществ способных выдерживать низкую температуру без изменения свойств.
|
Низкотемпературный метод был распространен в США и Канаде, где |
|
такое nоложение сложилось исторически. Однако позднее достоинства |
.. |
способа наполнения под давлением заставили предпринимателей нару |
|
|
|
шить сложившуюся традицию. |
|
В СНГ и во всех развитых странах применяется исключительно метод |
|
наполнения под давлением. |
2.11. Оборудование производства экстракционных препаратов из лекарственного растительного сырья
В современном фармацевтическом производстве большое значение
имеют процессы экстракции биологически активных веществ из природно гФ сырья растительного или животного происхождения, потому что каж дый третий лекарственный препарат, используемый в медицине - это про
дукт животного или растительного происхождения.
68 |
69 |
|

Производство настоек и жидких экстрактов включает стадии из |
|
|
мельчен11я и рассева сыр,,я, экстрагирования, очистки извлечений отсrаи |
|
|
ванием 11ли фил1,трацией В производстве экстрактов густых и сухих, экс |
|
|
трактов-"011центратов, максимально очищенных препаратов к вышепере |
|
|
численным стадиям добавляются еще сгущение извлечений и сушка. |
|
|
Типы оборудов ния применяемого для измельчения и рассева сы |
|
|
рья были подробно рассмотрены ранее Специфическим оборудованием в |
|
|
этих производствах являются различные типы экстрак.оров. Все экстрак |
|
|
торы, применяемые в фармацевтическом производстве, могут быть |
клас |
|
сифицированы |
|
|
1)периодического и непрерывного действия, |
|
|
2)прямоточного, противоточного и смешанного действия; |
|
• |
,З)по способу обтекания твёрдых частиц жидкостью (с неподвиж |
|
|
ным слоем твердого материала; механическим перемешиванием; со |
|
|
взвешенным слоем. |
|
|
На предприятиях с малыми объемами производства используются |
|
|
аппараты периодического действия - мацерационные баки и перколяторы |
|
Мllцерационный бак представляет собой емкостной аппарат ци линдрической формы с плоским днищем, который оборудован ложным перфорированным дном для укладки фильтрующего материала и сырья; перемешивающим устройством; крышкой; штуцером для слива экстракта и если экстрагирование проводится с принудительной циркуляцией, то в комплект входит циркуляционный насос.
Перколяторы - это емкостные аппараты, которые могут быть ци линдрической или конической формы, с паровой рубашкой или без неё, с опрокидывающимся днищем (рис. 2.35, 2.36). В нижней части перколятора
Рис 2 35 Перколяторы-экстракторы |
Рис 2 36 Перколятор-экстрактор |
1 - ло>1,.ное днище, 2 - фильтрую- |
1 - корпус, 2 - паровая рубашка, 3 - ло>1,. |
щнй материал |
ное дно (решетка), 4 - откидное днище, 5 |
|
- противовес, 6 - штуцер подачи экстра- |
|
гента, 7 - штуцер слива готового экстра - |
|
та, 8 - болты. |
имеется ложное днище в виде перфорированной решётки , которая монти руется между фланцами откидного днища. На решётку укладывают слой фильтрующего материала и сырьё. Экстрагент подают через штуцер в
верхней части аппарата, а экстракт отводят через штуцер в днище Перко ляторы цини11дрической формы более удобны при выгрузке отра601ашюrо
сырья, за10 в конических перколяторах обеспечивается более равномерный процесс зкстраrирования.
Для изготовления мацерационных баков и nерколяторов использу ют высоколегированную сталь, алюминий, боросиликатное стекло, иногда
луженую медь Основным недостатком указанных аппаратов является об разование застойных зон вблизи точек соприкосновения частиц. Стнако в малотоннажных производствах фитопрепаратов широко используют бата
реи из таких экстракторов. |
|
|
Из аппаратов непрерывного действия с механическим перемешива |
нием в |
производстве получили распространение экстракторы шнекового |
типа и барабанного типа.
Шиековый экстрактор (рис. 2.37) представляет собой горизон тальный желоб 1, внутри которого вращается горизонтальный вал 2. На валу укреплены спиральные лопщ:ти 3, и крестовины 4. Сырьё поступает в экстрактор через штуцер 5,
- |
а |
экстрагент |
через штуцер |
||||
|
6. |
Сырьё |
|
и экстрагент |
|||
|
движутся |
|
прямотоком. |
||||
|
Спиральные |
|
лопасти |
||||
|
перемещают |
сырьё вдоль |
|||||
|
желоба. |
На |
лопастях |
||||
|
смонтированы |
скребки |
|||||
|
7,которые приподнимают и |
||||||
|
сбрасывают частицы сырья, |
||||||
|
и |
таким |
образом |
||||
|
перемешивают его в верти- |
||||||
|
кальном |
плоскости. |
с |
||||
|
целью |
интенсификации |
|||||
11 |
процесса экстрагирования в |
||||||
экстрактор |
через |
сопло 8 |
|||||
|
|||||||
Рис 2 37 Шнековый экстрактор |
может подаваться |
острый |
|||||
пар. Для |
улучшения |
кон |
|||||
|
такта между сырьем и экстрагентом, последний постоянно перемешивает ся при помощи козырьков 9, приваренных к корпусу аппарата. Э"стракт выводится ю аппарата через сливной штуцер, а отработанное сырье отво дится посредством наклонного элеватора 1О. Стенки ковшей элеватора 11 выполнены в виде сит, через которые из отработанного сырья удаляется экстракт, который выводится из аппарата через шrуцер 12. Эти аппараты надежны и высокопроизводительны, но громоздки, энергоемки и металла-
емки.
Другой разновидностью этих аппаратов является вертuкlt!lьный шнековый экстрактор (рис. 2.38). Он состоит из загрузочной колонны 1, экстракционной колонны 3 и соединяющего шнека 2. Загрузочная и
70 |
71 |

1
'i"
экстракционная колонны представляют собой вертикальные цилиндры, внутри
которых вращаются шнековые валь1.
Между этими цилиндрами расположен горизонтальный шнековый вал, при по мощи которого, сырье из загрузочной колонны передается в экстракционную. Сырье подается в загрузочную колонну сверху и шнеком перемещается по ко
лонне вниз, а далее поступает в экстрак ционную колонну, где шнек перемещает
его вверх. Здесь отработанное сырье отжимается от экстрагента '1 выталкива ется из колонны. Свежий экстрагент непрерывно подается в верхнюю часть экстракционной колонны, где встреча- ется с сырьем обедненным по экстрак-
тивным веществам. По мере продвижения вниз по колонне экстрагент из влекает из сырья действующие вещества. Далее экстрагент перемещается в загрузочную колонну и по мере продвижения верх насыщается экстрак тивными веществами и в виде вытяжки удаляется из колонны. Этот экс трактор работает по принципу противотока.
В производстве фитопрепаратов работают экстракторы и других конструкций: дисковые, барабанные (рис. 2.39), пру:нсинно-лопастиые.
4 |
12 10 S |
3 11 |
|
|
Рис. 2.39. Барабанный экстрактор:
1 - горизонтальный цилиндрический барабан; 2 - передняя крышка; З - задняя крышка; 4 - штуцер для ввода сырья; 5 - бандаж; 6 - опорный. ролик; 7 - зубчатая передача; 8 - червяч ный редуктор; 9 - электродвигатель; 1 О - лопасти; 11 - штуцер для отвода вытяжки и шро та; 12 - тепловая изоляция.
|
|
Хорошо 1арскомсндовали себя з,,стрш:торы, сиаб:,,сеииые РПА. В этом |
||||||||||||||||
|
|
случае оl:уществляется процесс многократ11ой циркуляции сырья и экстра |
||||||||||||||||
|
|
гента при rюмощи РПА. При этом происходит механическое измельчение |
||||||||||||||||
|
|
частиц сырья, а вся смесь подвергается воздействию пульсации и турбули |
||||||||||||||||
|
|
зации. В технологической схеме РПА устанавливается ниже днища экс |
||||||||||||||||
|
|
трактора. Сырье загружается на ложное днище экстрактора и заливается |
||||||||||||||||
|
|
экстрагентом. В РПА жидкая фаза из экстрактора поступает через штуце |
||||||||||||||||
|
|
ры, а сырье·посредством шнека. Из РПА пульпа измельченного сыt1Ья по |
||||||||||||||||
|
|
дается сверху в экстрактор с мешалкой. Экстрагирование с использовани |
||||||||||||||||
|
|
ем РПА применяется в производстве масла облепихи, настоек календулы и |
||||||||||||||||
|
|
валерианы. Время экстрагирования в этих установках сокращается в 1,5-2 |
||||||||||||||||
.. |
• |
раза, а выход БАБ увеличивается. В таких экстр кторах в качестве экстра |
||||||||||||||||
|
||||||||||||||||||
|
|
гентов можно использовать органические вещества: дихлорэтан, хлори |
||||||||||||||||
|
|
стый метилен, а также минеральные и растительные масла. |
|
|
|
|
|
|||||||||||
|
|
|
Аппараты с взвешенным слоем также позволяют интенсифициро |
|||||||||||||||
|
|
вать процесс экстрагирования. |
Аппарат колонного типа с псевдоожижен |
|||||||||||||||
|
|
ным слоем (рис. 2.40), отличаясь простотой устройства и небольшой мае- |
||||||||||||||||
|
|
сой, позволяет значительно ускорить течение процесса с одно1:1ременным |
||||||||||||||||
|
|
|
|
|
s |
увеличением |
степени |
извлечения |
БАВ. |
В |
||||||||
|
|
|
|
|
аппарат снизу непрерывно подается экстрагент, |
|||||||||||||
|
|
|
|
|
|
|||||||||||||
|
|
|
4 |
|
|
который |
|
проходит |
|
через |
|
отверстия |
||||||
|
|
|
|
|
|
распределительной решетки и далее сквозь слой |
||||||||||||
|
|
|
|
|
|
мелко раздробленного сырья с такой скоростью, |
||||||||||||
|
|
|
|
|
|
что |
частицы |
находятся |
|
в |
состоянии |
|||||||
|
|
|
|
|
|
псевдоожижения. |
Экстракт отводится из верхней |
|||||||||||
|
|
|
|
|
|
расширенной части аппарата через кольцевой |
||||||||||||
|
|
|
|
|
|
желоб и штуцер. |
Свежее сырье подается через |
|||||||||||
|
|
|
|
|
|
загрузочную |
трубу непосредственно в |
кипящий |
||||||||||
|
|
|
|
|
|
слой, |
а |
отработанное сырье выводится из |
||||||||||
|
|
|
|
|
|
аппарата |
через |
штуцер |
в |
нижней |
части. |
|||||||
.. |
|
|
|
|
|
Перспективным |
направлением |
в |
создании |
|||||||||
|
|
|
|
|
|
|||||||||||||
|
|
Рис. |
|
|
нный |
оборудования фитохимических производств яв |
||||||||||||
|
|
|
|
ляется применение физических процессов гид |
||||||||||||||
|
|
2.40. |
Коло |
|
|
|
|
|
|
|
|
|
|
|
|
|
||
|
|
экстрактор |
с |
пс евдо |
родинамической кавитации, |
вибрации, |
фильтра |
|||||||||||
|
|
ожиженным |
(кипящим) |
|||||||||||||||
|
|
ции через мембраны, псевдоожижения э"страк |
||||||||||||||||
|
|
слоем: |
|
|
||||||||||||||
|
|
|
|
ционной |
системы |
за счет кипения |
экстрагента |
|||||||||||
|
|
1 - колонна; 2 - штуцер |
||||||||||||||||
|
|
для ввода свежего экстра |
под вакуу |
|
|
|
|
|
|
|
|
|
|
|||||
|
|
гента; 3 - распределитель |
|
|
мом. |
|
|
|
|
|
|
|
|
|
||||
|
|
|
Гидродинамическая |
кавитация |
позво |
|||||||||||||
|
|
ная решетка; |
4 - |
кольце |
ляет |
интенсифицировать процесс массопереда |
||||||||||||
|
|
вой желоб; 5 - штуцер для |
||||||||||||||||
|
|
чи. Этот способ заключается в том, |
что измель- |
|||||||||||||||
|
|
отвода вытяжки; 6 - шту |
||||||||||||||||
|
|
|
|
|
|
|
|
|
|
|
|
|
|
|
||||
|
|
цер для отвода шрота; 7 - |
ченное растительное сырье укладывается в экс |
|||||||||||||||
|
|
Зf,Грузочная труба Аf!Я рас- |
трактор в |
пакетах из фильтрующего |
материала, |
а |
||||||||||||
|
|
|
|
|
|
|
|
|
|
|
|
|
|
|
||||
|
|
тительноrо сырья |
|
рециркуляцию экстрагента проводят при помо |
||||||||||||||
|
|
|
|
|
|
|||||||||||||
|
|
щи насоса через так называемые кавитационные генераторы |
(гидродина |
|||||||||||||||
|
|
мический, ультр вуковой, импульсно-вихревой, |
электромагнитный). По- |
72 |
73 |

ложителы1ым в этом способе является то, что для реализации,этих процес сов можно использовать имеющееся экстракционное оборудование, а так же отсутствие в экстракторах механических перемешивающих устройств, Перспективным является и<;лользование вибрацио1111ых м11огофутщио ш111ы1ых шm11р11тов, позволяющих в едином рабочем объеме проводить несколько технолоrичес1_5их процессов: растворение,. кристаллизацию, упа ривание, фильтрацию, очистку экстрактов от остаточного количества экст рагента; кондуктивную сушку и измельчение в виброкипящем слое. Ос новным преимуществом данных аппаратов являются:- отсутствие переме шивающих устройств в рабочем объеме; отсутствие газового теплоносите ля; полная герметизация рабочего объема, за счет чего потери продукта
сокращаются до минимума; сокращение времени технологического про цесса; эк шоrическая чистота; низкий уровень энергозатрат.
Полученные изв)lечения в фитохимическом производстве· подвер гаются концентрированию. Широкое применение нашли прямоточный
роторный испаритель, циркуляционный вакуум-выпарной аппарат «Simax» и пенный испаритель, потому что они характеризуются ках высокоэффек тивные, надежные, малоэнерrоемкие и удобные в обслуживании.
Роториый прямоточный испаритель (рис. 2.41) состоит из верти |
||
|
кального цилиндрического корпуса I с паровой |
|
|
рубашкой 2. В центре аппарата расположен ро |
|
|
тор 3, который представляет собой вертикаль |
|
Выт |
ный вал с зз,крепленными на нем скребками 4. |
|
Вытяжка, поступающая на сгущение (концен |
||
|
||
|
трирование) подается через штуцер 5 в верхнюю |
|
|
часть аппара:rа в ра,спределительное кольцо 6, из |
|
|
которого вьщ:кает в виде многочисленных стру |
|
|
ек, которь1е стекают на скребки. Скребки раз |
|
|
брызгивают вытяжку на стенки аппарата, по ко |
|
|
торым она сtекает тонкой пленкой. Стенки ап |
|
|
парата обогреваются и за счет этого тепла идет |
|
|
испарение экстрагента из вытяжки. Ко центри |
|
|
рованная (сгущенная) вытяжка скребками сни- |
|
Рис. 2.41. Роторный |
мается со стенок и сбрасывается в кон11чекую |
|
прямоточный испарите:Л1. |
камеру внизу испарителя, из которой она через |
штуцер 7 отводится из аппарата. Роторныii ис паритель работает и под вакуумом, и под атмосферным давлением.
Циркуляционный вакуум-выпарной ttnnapain ((Simax>> (рис. 2.42)
также может работать под вакуумом и· под атмосферным. давлением. Со ставные части аппарата изготовлены из боросиликатноrо стекла, поэтому все стадии процесса можно контролировать визуально. Вытяжка, которая подлежит концентрированию, закачивается в колбу-приемник l при по мощи вакуума через штуцер 2 до уровня верхнего края спиралей калори фера 3. В калорифер через патрубок 4 подается rреющий пар, а конденсат из калорифера вr:.1водится по патрубку 5. В зоне калорифера происходит
••
•
••
..
|
быстрое вскипание вытяжки. Она |
||||||
|
переходит |
в |
|
состояние |
|||
|
парожидкостной |
смеси, |
|
которая |
|||
|
через узкую горловину 6 вы |
||||||
|
брасывается в колбу-расширитель 7. |
||||||
|
Здесь |
происходит |
интенсивная |
||||
|
циркуляция парожидкостной смеси с |
||||||
|
образованием |
хорошо |
|
рювитой |
|||
|
поверхности |
испарения. |
Пары |
||||
|
экстрагента поднимаются вверх и по |
||||||
|
трубе 8 поступают в холодильник |
||||||
|
конденсатор |
9, |
|
|
который |
||
Рис. 2.42. Схема циркуляционного ва |
представля·етсобой змеевик. JЗ каче |
||||||
стве хладагента используется холод |
|||||||
куум-выпарного аппарата фирмы «Си- |
|||||||
ная вода. Сконденсировавшиеся па |
|||||||
макс» |
|||||||
|
ры экстрагента стекают в колбу |
||||||
приемник I О, из которой экстрагент выводится через штуцер 11 |
|
после то |
го, как в системе устанавливается атмосферное давление. Неисцарившаяся вытяжка из колбы-расширителя по зазору 12 между циркуляционной тру бой 13 и стенками аппарата спускается в колбу-приемник. И процес.с упа ривания повторяется. Упариваемая вытяжка циркулирует в системе до тех пор, пока не будет получен заданный конечный объем вытяжки.
Пенный испаритель (рис. 2.43) широко применяется для концен- трирования водных извлечений, по скольку его· конструкция не преду сматривает конденсацию вторичного пара. Установка состоит из рабочей емкости 1, в которую загружается ис ходная вытяжка. Посредством насоса 2 вытяжка через патрубок 3 подается на распределительное устройство 4 в испарительную камеру 5. В камере размещена система горизонтальных трубок 6, по которым проходит. греющий пар. Вытяжка из распреде лительного устройства орошает по верхность разогретых трубок, распре
Рис. 2.43. Схема п нноrо испарителя |
деляясь по их поверхности тонким |
|
слоем. При этом она мгновенно вски |
||
|
пает и пенится, образуя большую поверхность испарения. Чтобы ускорить
процесс испарен1:1я В,!Iаги через испарительную камеру при помощи венти ляrора пропускается воздух, который уносит с собой испарившуюся влагу.
Аппарат удобен и надежен в эксплуатации, высокоэффективен и характе ризуется малой энергоемкостью.
74 |
75 |

В 11роизводстве многих лекарственных препаратов выделение их из растворов 11ысу1111ша1111см, является заключительной стадией получения готового продукта, поэтому условия проведения данной операции в боль
шой мере влияют на качество препаратов. Высушивание очищенных вы тяжек может проводиться как без предварительного концентрирования растворов, так и с предварительным концентрированием. В первом случае сушка осуществляется в распыл11тельных сушилках и в сушилках со слоем
инертных кипящих тел.
В рltсnылительиых cyuutЛкax жидкая вытяжка распыляется в виде мелкодисперсных капель в рабочей камере. Навстречу падающим каплям в нижней части рабочей камеры подается rарячий воздух с температурой
150-200°С. Влага испаряется, а высушенный продукт с температурой 50600С падает в приемник сушилки и выгружается.
Уста11овка по обе1воживанию водных растворов и экстрактов в кипящем слое инертной насадки производительностью 80 кг/ч по испа ряемой влаге (рис. 2.44) была разработана Санкт-Петербургским НПО
Рис. 2.44. Схема промышленной установки для обезвоживания растворов и экстрак тов в слое инертных кипящих тел:
1 - аппарат кнп.ящего слоя; 2 - паровой калорифер; 3 - элсктрокалорнфер: 4, 5 - высокона порные вентнл.яторы; 6- циклоны; 7 - ткане11Ые фильтры; 8, 9 - резервуары для хранения раствора и воды; 1 О - насос-дозатор; 11 - ц ентробежный насос; 12 - возд) шный фильтр; 13 - фильтр тон -ой очистки; 14 -возду:-.ораспределнтельная решетка; 15 - форсунка; 16-..сбор ник готового продукта; 17, 18-системы воздуховодов, 19инертные тела.
«Прогресс». Одним из преи:¼уществ этих аппаратов является полифунк циональность, т.е. вьiполнение в одном аппарате нескольких операций: выпаривания, сушки, измеJ.Jьчения, просеивания, для каж.: .ой из которых требуется технологический аппарат. Кроме этого, сушка растворов в ки пящем слое позволяет получить мелкодисперсный порошок. Обезвожива ние растворов происходит следующим образом. В аппарат плотно загру жают инертные тела (фторопластовые цилиндрики), а в сборник исходного раствора заливают подлежащий обезвоживанию раствор (зкстракт) и всю систему герметизируют. Предварительно очищенный воздух подается вен тилятором в паровой калорифер и далее в секции электрокалорифера, в ре
зультате чего разогревается до температуры l 10-I45°C (в зависимости от препарата). После нагрева инертных тел до температуры порядка I00°C
|
|
вклю< асн;я насос-дозатор, который из сборника подает раствор в механи |
||||||
|
|
ческую форсунку. Форсунка расположена внутри слоя инертных тел на |
||||||
|
|
высоте 300 мм от решетки. Механическая форсунка с тангенциальным за |
||||||
|
|
вихритслсм обеспечивает тонкое и равномерное распыление. |
Раствор, вы |
|||||
|
|
ходя из форсунки, орошает нагретые инертные тела. При этом влага испа |
||||||
|
|
ряется, а обезвоженный готовый продукт покрывает тонким слоем инерт |
||||||
|
|
ные тела. В результате соударения тел, пленка готового продукта разруша |
||||||
|
|
ется, частички осаждаются, а поток воздуха вместе с частицами го'rового |
||||||
|
|
продукта поступает в батарею циклонов и далее в рукавный фильтр. Воз |
||||||
|
|
дух нагнетается двумя вентиляторами, каждый из которых преодолевает |
||||||
|
|
половину сопротивления тракта, поэтому вся система трубопроводов, по |
||||||
• |
• |
которым проходит высушенное вещесtво, находится под разрежением, |
||||||
|
|
благодаря чему предотвращается выброс пыли· в рабочее помещение. В |
||||||
|
|
цилиндрической части аппарата на расстоянии 550-бSОмм от воздухорас |
||||||
|
|
пределительного устройства установлены два ролика, на которые натянуто |
||||||
|
|
по семь струн из стальной проволоки диаметром 1 |
мм. Струны способст |
|||||
|
|
вуют ускоренному обновлению поверхности инертных тел, то есть интен |
||||||
|
|
сифицируют процесс отделения высушенного продукта. |
|
|||||
|
|
|
В случае предварительной концентрации растворов (экстрактов) |
|||||
|
|
сушку проводят в вакуум сушмьных шкафах. Сгущенная вытяжка тон |
||||||
|
|
ким слоем наносится на противни, которые помещаются в сушильный |
||||||
|
|
шкаф. Сушку проводят под вакуумом (0.07-0.08 МПа). В процессе сушки |
||||||
|
|
объем продукта увеличивается в несколько десятков раз. Эту рыхлую и |
||||||
|
|
легкую массу в виде коржей размалывают в шаровой мельнице. Высуши |
||||||
|
|
вание проводят так же в барабант,,х вакуум-сушмках. Сгущенная вы |
||||||
|
|
тяжка подается потоко между барабанами, которые вращаются навстречу |
||||||
|
|
друг другу. Барабаны ,обогреваются изнутри. На поверхности барабанов |
||||||
|
|
образуется тонкая корочка продукта, которая затем размалывается. |
||||||
|
|
|
Из жидкого состояния высушивание может проводиться в субли |
|||||
|
|
|
|
|
мационных (лиофмьных, молекуляр |
|||
|
|
|
|
|
ных) |
су111мках. |
Процесс сублимации |
|
• |
|
|
|
|
используется в тех случаях, когда пре |
|||
|
|
|
|
|
||||
|
|
|
|
|
параты термолабильны. Процесс суб |
|||
... |
|
|
|
|
лимационной сушки состоит из трех |
|||
|
|
|
|
|
фаз: предварительного замораживания, |
|||
|
|
|
|
|
сублимации льда; удаление образовав |
|||
|
|
|
|
|
||||
|
|
|
|
|
шегося пара при температуре выше |
|||
|
|
|
|
|
0°С. Типовая схема установки для суб |
|||
|
|
|
|
|
лимационной сушки приведена на рис. |
|||
|
|
|
|
|
2.45. Установка состоит из сублимаци |
|||
|
|
|
|
|
онной камеры 1, конденсатора 2, кото |
|||
|
|
|
|
|
рый охлаждается холодильной маши |
|||
|
|
|
|
|
ной 3 и 4, двухступенчатого вакуум |
|||
|
|
Рис. 2.45. Схема установки для |
насоса 7 и диффузионного насоса 8. |
|||||
|
|
сублимационной сушки |
Все |
аппараты |
установки |
соединены |
76 |
77 |
|

между собою клапанами и оборудованы регулирующими устройствами для поддержания на заданном уровне температуры и вакуума.
Флаконы или ампулы, заполненные раствором лекарственного 11ре парата, в специальных кассетах устанавливают на nолке 9 сублимационной камеры. Здесь происходит замораживание растворов до температуры от -
20°С ДО -70°С. Внутри полок проходит два ряда трубок, по одним из них подается хладоагент, а по другим горячая вода из теплообменника нагревателя 6. Хладоагент охлаждается в холодильной машине. В сублн мационtюй камере при помощи диффузионного насоса создается глубокий вакуум (до 0.013 Па). Из камеры при помощи двухступенчатого вакуум насоса откачиваются водяные пары, которые затем поступают в трубы конденсатора-вымораживателя. В межтрубном пространстве конденсатора циркулирует хладоаrент. Конденсатор включается в циркуляционный кон тур с испарителем холодильной машины и соединен с вакуум-насосом 5, который откачивает неконденсирующиеся пары и воздух. В трубках кон денсатора происходит замораживание водяных паров. Как правило работа ет два конденсатора: один на размораживание, а другой на замораживание.
2.12. Оборудование производства фармацевтических препаратов на основе микробиологического синтеза
Основное направление микробиологического синтеза - использова |
|||
ние клеток микроорганизмов для производства ферментов, антибиотиков, |
|||
витаминов, алкалоидов, аминокислот, органических кислот, полисахари |
|||
дов. Процессы, протекающие в аппаратуре для микробиологического син |
|||
теза, отличаются повышенной сложностью, потому что в |
биохимическом |
||
|
е |
организмы, реакция которых на |
изменение сре |
синтезе участвуют живы |
|||
ды обитания непредсказуема. |
|
||
На стадии основного процесса ферментации используют специаль |
|||
ные аппараты - ферментаторы. В этих аппаратах идет выращивание био |
|||
массы и получение ее метаболитов в аэробны условиях. Основным пара |
|||
метром, который характеризует эффективность аэробных процессов, явля |
|||
ется поверхность контакта газа с жидкостью. В зависимости от способа |
|||
создания этой поверхности газо:нсидкостные фер.11ентаторы подразде |
|||
ляются щ, три группы: |
эрлифтные; с механическим диспергированием |
||
газа и струйные. В зрлифтных ферментаторах поверхность контакта фаз |
|||
образуется при введении газа через газораспределительное устройство в |
|||
слой циркулирующей жидкости. В ферментаторах с механическим дис |
|||
пергированием газа |
перемешивание вводимого в аппарат газа с культу |
||
ральной жидкостью |
производится специальными устройствами. В струй |
||
ных ферментаторах |
производится эжекция газа струями |
культуральной |
|
жидкости, которая при помощи системы насадоК' распределяете.я по сече- |
|||
нию аппарата. |
|
|
|
Фер.11е11пштор1,1 с зрлифт11ы.11 тtтом пере.111еu1uщ11111н применя ются для работы с большими объе 1ами и когда в качестве газовой фазы используется воздух. Эти ферментаторы характеризуются высокои'"'жс плуатационной надежностью, поскольку в их конструкции нет подвижных элементов, требующих специальных узлов герметизации (сальники, торце вые уплотнения), в них можно размещать теплообменные устройства с nо верхностыо большой площади и при этом не нарушаются условия цирку ляции жидкости. К ферментаторам такого типа относятся аппаратьt с кю ветными аэраторами; с эрлифтнымн трубами; с желобчатыми барботерами
Фермеитатор с юоветиы.ми юpamopttмu (или зрлифтиыми тру баJ11и) представлен на рис. 2.46. Он представляет собой цилиндрическую
• емкость 3 с плоским днищем и конической крышкой. Внутри емкости раз мещены кюветы 4. Количество кювет может быть от трех до восьми. Двойные стенки кювет служат в качестве теплообменных элементов. Ох лаждающая вода вводится в полости между стенками через штуцер А. Воздух в ферментатор подается по центральной трубе 2, а по трубам 6 по ступает в барботеры 7. Барботер представляет низкую коробку, между ци линдрической стенкой которой и нижней крышкой имеется узкая кольце вая щель для выхода воздуха. Питательная среда и засевной материал че рез штуцер Б подаются в бачок I и далее по трубам 5 поступают в коробку барботера 7. Воздух при выходе из барботера поднимается вверх, увлекая за собой в кюветы питательную среду, смешанную с циркулирующей культуральной жидкостью. На выходе из ферментатора воздух проходит через сепаратор 8, где из него удаляются капельки жидкости. Биомасса выходит из ферментатора через штуцер В. Каждая из кювет работает как затопленный эрлифт. При подаче воздуха в ней образуется газожидкостная
смесь, rазосодержание в которой больше, чем газосодержание в биомассе в межкюветном пространстве аппарата. Вследствие этого в зоне кювет про
исходит циркуляция суспензии, которая препятствует осаждению твердой
фазы.
Фер.111е11татор с зрлифтными трубами (рис. 2.47). Чтобы избе-
•
А
Рис. 2.46. Ферментатор с кюветными |
Рис. 2.47. Ферментатор с эрлифтными |
аэраторами |
трубами |
78 |
79 |
|