
спхфу Метода Расчет и проект аппаратов с мешалкой Иванов, Алферова 2016
.pdf
д) составление эскизной компоновки аппарата; е) расчет вала мешалки.
4-й этап– выполнение графической части проекта. Этап выполняется на основании эскизной компоновки корпуса и аппарата в целом, расчета и подбора конструктивных элементов корпуса и перемешивающего устройства.
5-й этап– окончательное оформление расчетно-пояснительной записки . 6-й этап – подготовка к защите и защита курсового проекта. Выполненный проект, удовлетворяющий предъявляемым к нему требованиям и подписанный руководителем, допускается к защите. Защита проекта состоит из краткого сообщения студента о проделанной работе и ответов на вопросы членов комиссии. При оценке проекта учитывается не только техническое качество проекта, но и выполнение установленных сроков проектирования, самостоятельность и творческая инициатива, проявлен-
ные при проектировании.
2. РАСЧЕТ КОРПУСА АППАРАТА
Целью расчета корпуса аппарата является определение его соответствия заданным условиям эксплуатации, обеспечивающего требуемую работоспособностьвтечениевсегосрокаслужбы.Расчетыпроводятсякакпроверочные, с использованием действующих технических рекомендаций и нормативов.
Точность выполнения расчетов не превышает трех значащих цифр, поэтому полученный результат, например, 2345678 Па целесообразно записывать в виде 2,35·106 Па или 2,35 МПа. Если первой значащей цифрой является единица, то число записывается с четырьмя значащими цифрами, например 1,473·108 Па.
1.1. Материалы корпуса аппарата
Марки сталей для изготовления обечаек, днищ и крышек аппаратов указаны в техническом задании на курсовое проектирование.
Допускаемое напряжение [σ] при расчете по предельным нагрузкам конструктивных элементов корпуса для углеродистых и низколегированных сталей определяется по выражению:
[σ]= min (σТ)nТ ;σВ(nВ),
где σт, σв – предел текучести и временное сопротивление (предел прочности) при расчетной температуре, МПа; nт, nв– коэффициенты запаса по
11
пределу текучести и по пределу прочности, которые принимаются равными соответственно 1,5 и 2,4 [31]. Для сталей, используемых в химическом аппаратостроении, допускаемые напряжения для рабочих условий, определяемые в соответствии с указанной формулой, приведены в «Методических указаниях и заданиях» в таблицах 7 и 8. Необходимые для расчетов значения модуля продольной упругости для сталей приведены в таблице 9 в «Методических указаниях и заданиях».
2.2. Расчетные параметры и нормы
2.2.1. Под условным проходом Dу понимается номинальный внутренний диаметр трубы или аппарата. Фактический внутренний диаметр в зависимости от способа изготовления трубы (аппарата) может несколько отличаться от номинального стандартного размера. Условные проходы установлены стандартом СЭВ 254–76 и имеют следующие значения (мм): 10; 15; 20; 25; 32; 40; 50; 65; 80; 100; 125; 150; 200; 250; 300; 350; 400; 500;600; 800; 1000; 1200;1400; 1600; 1800; 2000; 2200; 2400; 2600; 2800; 3000; 3200.
Внутренние диаметры корпусов цилиндрических сосудов и аппаратов, величина которых регламентирована ГОСТ 9931–85, совпадают с величинами условных проходов.
2.2.2. Расчетная температура tp используется для определения физи- ко-механических характеристик материала и допускаемых напряжений. При расчете стенок корпуса расчетная температура принимается равной температуре среды в аппарате tс.
Расчетная температура для фланцевых соединений принимается: при наличии тепловой изоляции – для фланцев равной tс, для фланцевых болтов – 0,97 tс; для фланцев без тепловой изоляции – 0,96 tс, для болтов в этом случае – 0,95 tс.
2.2.3. Под условным давлением ру следует понимать наибольшее избыточное давление при температуре среды 20 °С, при котором допустима длительная работа аппарата или трубопровода, имеющих данные размеры, обусловленные расчетом на прочность. Ряд условных давлений установлен ГОСТ 356–80 и включает следующие значения (МПа); 0,1; 0,16; 0,25; 0,40; 0,63; 1,00; 1,6; 2,50; 4,00; 6,3; 10,00; 12,5; 16,0.
Под рабочим давлением р для сосуда и аппарата принимается наибольшее внутреннее избыточное или наружное давление, возникающее при нормальном протекании процесса.
Расчетное давление рр для конструктивных элементов сосуда и аппарата – давление, при котором производится их расчет на прочность или устойчивость. Как правило, расчетное давление принимается равным рабочему давлению: рр = р.
12
Если на элемент сосуда или аппарата действует гидростатическое давление, составляющее 5 % и выше от рабочего, то расчетное давление должно быть увеличено на эту величину:
Ррв = Р+ Рг;
Рг = 106 g ρж Нж,
где Ррв – расчетное внутреннее давление, МПа; Рг – гидростатическое давление, МПа; g = 9,81 – ускорение свободного падения, м/с2;
ρж – плотность жидкой среды, кг/м3, (для воды ρж = 1000 кг/м3) Нж – высота столба жидкости от верхнего уровня до нижней точки рассчитываемого элемента, м.
При расчете на прочность (по внутреннему давлению) стенки обогревающей рубашки в качестве расчетного следует принимать рабочее давление теплоносителя (пара) рп. Это же давление принимается в качестве расчетного при проверке на устойчивость части корпуса аппарата, находящейся под рубашкой.
2.2.4.Коэффициент прочности сварного шва φ , который вводят
врасчетные формулы при расчете сосудов и аппаратов, характеризует прочность сварного соединения в сравнении с прочностью основного материала. Значения этого коэффициента в зависимости от типа шва, вида сварки и длины контролируемых швов для стальных аппаратов указаны
в«Методических указаниях и заданиях» в таблице 10. (Типы швов, вид сварки, длину контролируемых швов принять по своему аппарату).
2.2.5.Прибавки к расчетным толщинам конструктивных элемен-
тов, учитываемые при расчете, определяются по формуле:
С = С1 + С2,
где С – сумма прибавок к расчетным толщинам стенок, мм; С1 – прибавка для компенсации коррозии и эрозии, мм; С2 – прибавка
для компенсации минусового допуска на стандартную толщину стального листа (см. «Методические указания и задания», таблица 11).
Таким образом, исполнительная толщина стенки S элемента аппа-
рата определяется как:
S ≥ Sr + С,
где Sr – расчетная толщина стенки, мм.
Прибавка С1 для компенсации коррозии и эрозии равна:
С1 = Пτ + Сэ,
гдеП–глубинныйпоказателькоррозии,мм/год;τ–срокслужбыаппа- рата, в годах; Сэ – прибавка для компенсации эрозии, мм.
13
Для изготовления химических аппаратов, как правило, должны использоваться металлы, для которых глубинный показатель коррозии П ≤ 0,1 мм/год. Коррозионную стойкость материалов в различных средах можно найти в справочной литературе [3].
Прибавку Сэ рекомендуется учитывать лишь при высоких окружных скоростях движения среды в аппарате (для жидких сред более 20 м/с) или при наличии в движущейся среде абразивных частиц, что в химико-фар- мацевтическом производстве встречается сравнительно редко.
Прибавка С2 учитывается лишь в тех случаях, когда её величина превышает 5 % номинальной толщины листа.
2.3.Расчёт корпуса аппарата, нагруженного внутренним давлением
2.3.1.Цилиндрическая обечайка (рис. 2, б).
Расчетная толщина стенки обечайки определяется выражением:
Sr = Ррв Д/ (2 [σ] Ррв). |
(1) |
Исполнительная толщина стенки обечайки находится из условия:
S ≥ Sr + С,
где Sr – расчетная толщина стенки обечайки, мм; S – исполнительная толщина стенки обечайки (принимается в соответствии с ГОСТ) мм; Ррв – расчетное внутреннее давление, МПа; Д – внутренний диаметр обечайки, мм; [σ] – допускаемое напряжение для материала при расчетной температуре, МПа; φ – коэффициент прочности сварного шва; С – сумма прибавок к расчетной толщине, мм.
Допускаемоевнутреннееизбыточноедавлениепоусловиюпрочности определяется как:
[Ррв] = 2[σ]φSr/(Д + Srs), |
(2) |
где Srs = S – С – толщина стенки по окончании срока эксплуатации аппарата с учётом минусового допуска на стандартную толщину листа и прибавки на коррозию.
По этим же формулам (1) и (2) рассчитывается толщина стенки обогревающей рубашки.
14
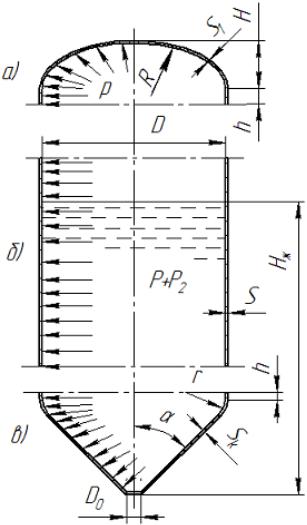
Э
Рис. 2. Расчетные схемы конструктивных элементов корпуса, нагруженного внутренним давлением:
а) эллиптическая крышка; б) цилиндрическая обечайка; в) коническое днище.
15
2.3.2. Эллиптическое днище (крышка) (Рис.2, а)
Для стандартных эллиптических днищ и крышек высота соответственно эллиптической части днища (без учета цилиндрической отбортовки) Нэ = 0,25Д, радиус кривизны в вершине днища R = Д.
Расчетная толщина стенки днища вычисляется по формуле:
S1r = Ррв R/(2φ[σ] 0,5 Ррв).
Исполнительная толщина находится из условия:
S1 ≥ S1r + С.
Допускаемое внутреннее избыточное давление определяется из условия прочности:
[Рв] = 2[σ]φS1r/(0,5 S1r + R).
По этим же формулам рассчитывается толщина стенки днища обогревающей рубашки.
2.3.3. Коническое днище (Рис.2, в).
Длястандартныхднищ(радиустороидальногопереходаr=0,15Д)при α = 60о расчетная толщина конической части днища принимается равной:
Sкr = (Дк /cos α)Ррв /(2φ[σ]Ррв )
Sк ≥ Sкr + С.
где Sкr – расчетная толщина конической части днища, мм; Sк – исполнительная толщина стенки днища, мм; Дк ≈ 0,8Д – расчетный диаметр конического днища, мм.
Допускаемое внутреннее избыточное давление находят из условия
Ррв = 2φ[σ](Sк r – С)/(Sк r – С + Дк /cos α).
2.4.Расчет корпуса аппарата, нагруженного наружным давлением
2.4.1.Цилиндрическая обечайка (Рис. 3)
Расчетная и исполнительная толщина стенки цилиндрической обечайки могут быть определены по выражениям:
Ser =1,122 Д0,6 (РрнlP / E)0,4 , |
(3) |
Sе ≥ Sеr + С. |
(4) |
16
Допускаемое наружное давление [Pн] определяется по выражению:
[Р |
[Рσ] [PЕ] |
(5) |
||
] = ———————, |
|
|||
н |
([P |
]2 + [P |
]2)0,5 |
|
|
σ |
Е |
|
|
где[Pσ]–допускаемоедавлениеизусловияпрочности,рассчитываемое по формуле:
[Рσ] = 2[σ]Ser /(Д + Se r ), |
(6) |
а [PЕ] – допускаемое давление из условия устойчивости определяется как:
[PЕ] = 0,75Е(Д /lP )(Ser / Д)2,5 . |
(7) |
В приведенных формулах (3) – (7) использованы следующие обозначения:
Sеr – расчетная толщина стенкицилиндрическойобечайки из условия устойчивости, мм;
SЕ – исполнительная толщина стенки обечайки, мм; Pрн – расчетное наружное давление, МПа;
Е– модуль продольной упругости для материала обечайки при расчетной температуре, МПа;
lр – расчетная длина гладкой (неподкрепленной кольцами) цилиндрической обечайки, определяемая по схеме на рис.3.
Для аппарата с эллиптическим днищем lP = lц + h + HЭ / 3,
для аппарата с коническим днищем – lР = lц +h+r sin α,
где h – величина отбортовки (цилиндрический участок у штамповочного днища), принимаем равной 25 мм.
17
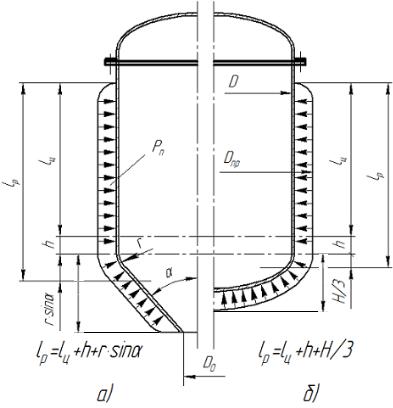
6
6 |
Н |
Н
r = 0,15D |
lц |
= Н2 – Н3 – Н6, |
α = 600 |
где |
Н3 – см. табл. 5 |
|
из «Методическихуказаний и заданий» |
Рис. 3. Схема к определению расчетной длины обечайки lр при расчете на устойчивость элементов аппарата, находящихся под обогревающей рубашкой:
а) с коническим; б) с эллиптическим днищем.
2.4.2. Эллиптическое днище (Рис. 3)
Толщина стенки днища (крышки) приближенно определяется по выражению:
S1er = 3,03KэR(Ррн / Е)0,5 ,
S1e ≥ S1er +C
18
Здесь Кэ – коэффициент формы днища, принимаемый равным 0,9. Допускаемое наружное давление [Рн] следует рассчитывать по форму-
ле (5), где допускаемое давление из условия прочности определяется как:
[Pн] = 2[σ]S1еr/(R + S1еr),
а допускаемое давление из условия устойчивости равно: [PЕ] = 0,108Е[S1еr/Кэ R]2.
2.4.3. Коническое днище с тороидальным переходом (Рис. З, а)
Толщина стенки конического днища в первом приближении определяется по формуле:
Sкer =1,122 Дке0,6 (Ррнlкр /Е)0,4
S1кer ≥ Sкer +С,
где Дke – эффективный диаметр конического днища, равный
Дкe = 0,5(Д + Д0 )/cos α.
Расчетная длина находится из выражения: lкр = 0,5(Д – Д0 )/sin α. В последних двух выражениях Д0 – диаметр отверстия в нижней части
конического днища.
Допускаемое наружное давление [Рн] определяется по формуле (5), где допускаемое давление из условия прочности находят по выражению:
[Рσ] = 2[σ]Sкеr/(Sкеr + Д / cosα),
а допускаемое давление из условия устойчивости определяется как: [PЕ] = 0,75Е(Дке/lкр)(Sкеr/ Дке)2,5 .
2.5. Фланцевые соединения
Фланцы к химическим аппаратам и штуцерам выбирают по соответствующим государственным или отраслевым стандартам [29; 35; 38–40] с учетом условного прохода, условного давления и расчетной температуры.
Для стальных цилиндрическихсварных сосудов и аппаратовнаиболее употребительны плоские приварные фланцы и фланцы приварные встык. В таблице 4 приведены рекомендации к применению фланцев обоих типов в зависимости от диаметра аппарата и условного внутреннего давления (рекомендуемые сочетания помечены знаком +).
19
|
|
|
|
|
|
|
|
|
|
|
|
Таблица 4 |
|
|
Типы и пределы применения фланцев |
|
|
|
|||||||||
Внутренний |
|
Фланцы плоские |
|
|
|
|
|
|
|
|
|||
|
|
приварные |
|
|
Фланцы приварные встык |
|
|||||||
диаметр |
|
|
|
|
|
||||||||
|
|
|
|
|
|
|
|
|
|
|
|
|
|
|
|
|
|
|
Условное давление, МПа |
|
|
|
|||||
аппарата |
|
|
|
|
|
|
|
|
|||||
|
|
|
|
|
|
|
|
|
|
|
|
|
|
|
0,3 |
|
0,63 |
1,0 |
|
1,6 |
0,6 |
1,0 |
1,6 |
|
2,5 |
4,0 |
6,3 |
400 – 1600 |
+ |
|
+ |
+ |
|
+ |
|
+ |
+ |
|
+ |
+ |
+ |
1600 – 2000 |
+ |
|
+ |
+ |
|
+ |
|
+ |
+ |
|
+ |
|
|
2000 – 3200 |
+ |
|
+ |
+ |
|
|
|
+ |
+ |
|
|
|
|
|
|
|
|
|
|
|
|
|
|
|
|
|
|
3200 – 4000 |
+ |
|
|
|
|
|
+ |
+ |
|
|
|
|
|
|
|
|
|
|
|
|
|
|
|
|
|
|
|
Фланцы могут иметь различные исполнения уплотнительных поверхностей. Гладкая уплотнительная поверхность (рис. 4 в «Методических указаниях и заданиях», исполнение 1) применяется при внутреннем давлении до 0,63 МПа, фланцы с выступом-впадиной (рис. 5 в «Методических указаниях и заданиях», исполнение 1, 2) используется при давлении 0,63 – 1,6 МПа, с шипом-пазом (рис. 4 в «Методических указаниях и заданиях», исполнение 2, 3, (рис. 5 в «Методических указаниях и заданиях», исполнение 3, 4) при давлении от 1,6 до 6,3 МПа. Кроме того, тип уплотнительной поверхности фланца определяется и материалом прокладки. При использовании прокладок из пластических масс – полихлорвинила, фторопласта, полиэтилена рекомендуется применять уплотнительную поверхность «шип-паз». Во фланцевых соединениях с гладкой уплотнительной поверхностью «выступ-впадина» применение пластмассовых прокладок не допускается.
Обозначения нормализованных размеров фланцев приведены в «Методических указаниях и заданиях», на рис. 4 и 5, а численные величины этих размеров – в таблицах 14 и 15.
В качестве материалов для изготовления фланцев используются, стали обыкновенного качества, например, ВСт3, углеродистые качественные стали 20, 25, 30, 35, легированные стали 09Г2С, 10Г2,15ХМ, 10Г2,Х- 18Н10Т, 12Х18Н10Т, 15Х5М и другие, обеспечивающие установленное качество фланцевых соединений.
Фланцы, подобранные по государственному или отраслевому стандарту, имеют размеры, полностью обеспечивающие прочность и плотность соединения, и не нуждаются в проверочном расчете.
Для соединения фланцев наиболее часто применяют либо болты, либо шпильки. Болты используются при давлении в аппарате менее 1,6 МПа. При больших давлениях, а так же при рабочих температурах выше 400 ºС применяют шпильки.
20