
05 семестр / Лекции и семинары / Третьяков Курс лекций по дисциплине Технология конструкционных материалов
.pdfкомпозитах, осуществляют путем восстановления треххлористого бора водородом. В результате химического осаждения бора на вольфрамовую нить диаметром 10…12 мкм образуются волокна, прочность которых во многом зависит от наличия локальных дефектов в виде крупных кристаллов, инородных включений, трещин, пустот и др. Производительность промышленного процесса получения волокон с заданными свойствами с увеличением температуры процесса от 980 до 1200 ºС возрастает. Повышение температуры до 1300 ºС приводит к образованию крупных кристаллов, что заметно снижает их прочность. Для повышения термостойкости волокон на их поверхность химическим осаждением наносят слой карбидов кремния или бора толщиной 2...6 мкм.
После того как был открыт легко разлагающийся летучий карбонил никеля, возникла новая отрасль металлургии – газофазная металлургия. В настоящее время эта отрасль включает наряду с карбонильным методом и галогенидные процессы.
Химическое осаждение из газовой фазы не только позволяет получать изделия сложной конфигурации, оно может стать эффективным способом соединения заготовок из тугоплавких металлов путем осаждения нужного материала в зазоре между соединяемыми элементами. Отсутствие в изделии шва и околошовной зоны с крупнозернистой структурой является основным преимуществом этого технологического процесса по сравнению со сваркой плавлением при прочих равных условиях.
Так, для соединения листовых элементов толщиной 0,15…0,5 мм используют метод химического осаждения W путем восстановления газообразного соединения WF6 водородом. При этом температура свариваемых кромок составляет 550…750 ºС, а длительность процесса 10…20 мин. Прочность полученных таким образом соединений составляет 66…96 % от прочности основного материала. Толщина осаждаемого покрытия в зоне соединения превышает толщину свариваемых кромок в 5 раз.
Известно применение никеля, образующегося при разложении карбонила никеля [Ni(CO)4], для формирования нахлесточного соединения стальных и керамических элементов конструкции.
Методы физического и химического осаждения имеют свои преимущества и недостатки. Анализ литературных данных показывает, что физическое осаждение с успехом применяется для получения тонких пленок толщиной 3…5 мкм. В том случае, когда требуются более массивные осадки, экономичнее использовать химическое осаждение, поскольку максимальная скорость образо-
41
вания сплошных пленок составляет 1525 мкм/ч, а при физическом осаждении – 255 мкм/ч.
В процессе химического осаждения достигается наибольшее рассеивание материала, поэтому можно получать равномерные покрытия (осадки) на изделиях сложной формы. Однако в этом случае подложка должна быть нагрета до температуры от 150 до 2000 ºС в зависимости от свойств осаждаемого материала.
Основной областью применения технологических процессов осаждения из парогазовой фазы являются декоративные покрытия и пленки для электроники и оптики. При физическом методе осаждения покрытия могут быть получены из всех твердых химических элементов, большинства галоидных солей и других соединений, испаряющихся без разложения. Химическое осаждение может быть применено для получения заготовок и нанесения покрытий из всех металлов, за исключением щелочных и щелочноземельных, а также из углерода, кремния, карбидов, нитридов, силицидов, боридов, оксидов и сульфидов.
Например, химическое осаждение используют для получения пленок, которые применяют в качестве функциональных слоев кремниевых микросхем (двуокиси кремния, нитрида кремния, силицида вольфрама и др.).
4.3. Химикотермическая обработка заготовок
Для упрочнения деталей машин широко применяют поверхностное легирование, которое может осуществляться в газовой среде. Химикотермическая обработка (ХТО) сводится к диффузионному насыщению поверхностного слоя заготовки неметаллами (C, N2, Si, B и др.) или металлами (Cr, Al, Zn и др.) в процессе выдержки при определенной температуре в активной газовой среде.
При ХТО одновременно протекают несколько процессов:
−образование в окружающей среде диффундирующего элемента в атомарном или ионизированном состоянии;
−адсорбция атомов (ионов) на поверхности изделия с образованием химических связей между ионами насыщающего элемента
иосновного металла (химосорбция);
−диффузия адсорбированных атомов в глубь обрабатываемой заготовки.
Толщина диффузионного слоя зависит от температуры насыщения, продолжительности процесса, характера образующегося твердого раствора (внедрения или замещения), атомно-кристалли-
42
ческого строения материала заготовки и концентрации диффундирующего элемента на поверхности. С повышением температуры, длительности процесса насыщения и концентрации диффундирующего элемента возрастает толщина легированного слоя.
Скорость диффузии атомов насыщающего элемента, образующего с металлом заготовки твердые растворы внедрения, значительно выше, чем при образовании твердого раствора замещения. Диффузия элементов протекает интенсивнее в решетке α -железа, чем в более плотно упакованной решетке γ -железа.
К ХТО в газовой фазе относят процессы цементации, нитроцементации, азотирования и диффузионного насыщения металлами (Al, Cr, Zn и др.) или смесями компонентов (Al и Si, Cr и Si, B и Al и др.).
Вопросы для самоконтроля
1.Назовите основные виды осаждения материалов из парогазовой фазы, перечислите их основные характеристики и области применения.
2.Какой вид осаждения материала целесообразно применять для получения сопла ракетного двигателя из вольфрама?
3.Перечислите основные процессы, относящиеся к газофазной металлургии. Какие процессы применяют для соединения изделий из тугоплавких металлов?
4.Какие процессы протекают одновременно при химикотермической обработке заготовок?
5.Сформулируйте условия, необходимые для химического осаждения материала при нанесении покрытий на заготовки и формирования пленок.
43
Лекция № 5. ПОЛУЧЕНИЕ ЗАГОТОВОК
ИИХ ОБРАБОТКА В ЖИДКОЙ ФАЗЕ
Вэтой лекции рассмотрены научные основы технологических процессов получения заготовок в жидкой фазе, а также причины образования дефектов при кристаллизации и охлаждении. Вы ознакомитесь с основными закономерностями получения заготовок методами литья, сварки плавлением, процессами наплавки, газотермическогонанесенияпокрытий иэлектроэрозионной обработки.
5.1.Основные фазы кристаллизации
Получение заготовок в жидком состоянии предполагает, как правило, расплавление основного и (или) присадочного материала; заполнение специально подготовленной формы или зазора между соединяемымиэлементамиикристаллизациюжидкойметаллическойфазы.
Формирование большинства свойств заготовки определяется первичной кристаллизацией. Для получения слитков, отливок, сварных и паяных швов с требуемой структурой нужно уметь управлять процессом кристаллизации. Это возможно только на основе знания законов кристаллизации, понимания тех явлений, которые происходят в металле или сплаве в процессе его затвердевания.
Согласно общей теории кристаллизации, процесс затвердевания определяется двумя факторами:
−скоростью возникновения центров (зародышей) кристаллизации в единице объема жидкой фазы;
−скоростью роста зародышей кристаллизации.
Наблюдение за кристаллизацией слитков, отливок и сварных швов подтвердило достоверность гипотезы о направленной последовательной кристаллизации. Согласно этой гипотезе, затвердевание начинается на поверхности соприкосновения со стенками формы или сварочной ванны и развивается от периферии к тепловому центру.
При изготовлении слитков и отливок источником образования зародышей чаще всего являются твердые частицы (неметалличе-
44
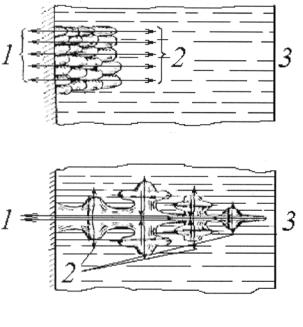
ские включения, оксиды, тугоплавкие металлы и т. д.), которые всегда присутствуют в расплаве. Чем больше примесей, тем больше центров кристаллизации, меньше размеры кристаллитов и выше механические свойства. Для получения мелкозернистой структуры в жидкий металл вводят примеси (модификаторы), которые, практически не изменяя химический состав сплава, улучшают механические свойства заготовок.
Наибольшее влияние на процесс кристаллизации металла и сплава оказывают теплоемкость, скрытая теплота плавления, температурныйинтервалкристаллизацииистепеньпереохлаждениярасплава.
Чистые металлы, как правило, кристаллизуются в дендритностолбчатую структуру (рис. 5.1, а), а сплавы – в дендритноравноосную (рис. 5.1, б). При этом чем больше температурный интервал кристаллизации сплава, тем резче проявляется дендритноравноосная структура.
а
б
Рис. 5.1. Схема направления отвода и роста кристаллитов:
а– длячистого металла; б– для сплавовсширокиминтерваломкристаллизации: 1 – направления отвода теплоты; 2 – направления роста кристаллитов;
3 – тепловой центр
45
Разный характер кристаллического строения металлов и сплавов объясняется тем, что состав жидкого металла постоянен и не изменяется с уменьшением температуры. Доступ жидкого металла к поверхности кристаллизации неограничен, и рост кристаллитов происходит преимущественно в направлении, противоположном направлению отвода теплоты, поэтому образуется плотная денд- ритно-столбчатая структура. Аналогичная схема кристаллизации реализуется при затвердевании химических соединений.
В эвтектике при постоянной температуре кристаллизуются одновременно несколько фаз, причем одна из них создает «скелет» кристаллита, а другие отлагаются в междуосных пространствах этого скелета.
При затвердевании сплавов с широким температурным интервалом кристаллизации создаются благоприятные условия для роста не только главных, но и вторичных ветвей дендритов. При этом кристаллит тем более разветвлен, чем шире интервал кристаллизации.
Питание дендритов при охлаждении сплавов с широким интервалом кристаллизации затруднено, так как оставшегося жидкого металла между ветвями дендритов недостаточно для компенсации усадки. При этом чем шире температурный интервал кристаллизации, тем хуже питание дендритов и ниже плотность литой структуры заготовки.
Кристаллизация под давлением (жидкая штамповка или точечная сварка) является одним из прогрессивных технологических процессов, позволяющих получить плотную макроструктуру заготовок с высокими свойствами. В результате воздействия давления на кристаллизующийся расплав происходит:
−уменьшение размера кристаллитов;
−равномерное распределение неметаллических включений;
−увеличение однородности за счет уменьшения степени развития ликвационных процессов;
−изменение состава и характера распределения фаз;
−повышение физико-механических свойств заготовок.
5.2.Причины образования дефектов при кристаллизации
иохлаждении заготовок
Одной их основных особенностей процесса кристаллизации металлов и сплавов является усадка, которая протекает в слитках, отливках, сварных и паяных швах при затвердевании и последую-
46
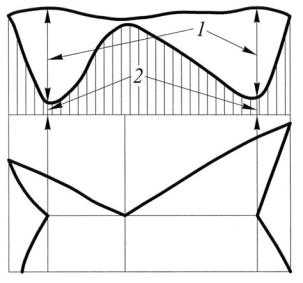
щем охлаждении. Изменение объема заготовки зависит от ее свойств, температуры и скорости охлаждения.
Подавляющее большинство металлов и сплавов плавятся с увеличением объема и кристаллизуются с его уменьшением. Некоторые материалы (серый чугун, висмут, сурьма и др.) плавятся с уменьшением объема и кристаллизуются с его увеличением. Объемная усадка материала слагается из усадки в жидком состоянии, в момент кристаллизации и в твердом состоянии.
Расплавы имеют различный характер распределения усадки по объему. Так, у технически чистых металлов, сплавов эвтектического типа и химических соединений объемная усадка проявляется в основном в виде концентрированных усадочных раковин. Сплавы, кристаллизующиеся в интервале температур, характеризуются наличием усадочной (рассеянной) пористости и усадочных рако-
вин. При этом чем больше температурный интервал, тем рассеянней объемная усадка и меньше усадочная раковина (рис. 5.2).
Рис. 5.2. Характер зависимости между составом сплавов и распределением объемной усадки в виде пор:
1 – объем рассеянных пор; 2 – объем усадочных раковин
Охлаждение и кристаллизация жидкого металла происходят последовательно с поверхности вовнутрь заготовки. В результате
47
неравномерного охлаждения в изделии возникают термические напряжения, причем чем меньше разница в температурах отдельных слоев, тем ниже их уровень. Поэтому для получения заготовок (отливок сварных конструкций) с высокими механическими свойствами и минимальными термическими напряжениями необходимо обеспечивать высокую скорость кристаллизации жидкого металла с последующим медленным охлаждением изделия до температуры окружающей среды.
Напряжения в заготовках возникают также в результате сопротивления инструмента (литейной формы, стержня, сварочного приспособления) свободной усадке металла при их изготовлении. Чем меньше податливость формы или выше жесткость закрепления свариваемых элементов, тем меньше фактическая линейная усадка металла и выше уровень напряжений в получаемых изделиях.
При изготовлении заготовок из легированных и высокоуглеродистых сталей методами литья и сварки плавлением, как правило, возникают объемные структурные напряжения. Объясняется это тем, что при охлаждении изменяется структура металла (размеры и взаимное расположение зерен), что сопровождается изменением объема металла и вызывает внутренние напряжения. Уровень этих напряжений возрастает с увеличением скорости охлаждения заготовок. При получении отливок и сварных конструкций из низколегированных и низкоуглеродистых незакаливающихся сталей структурные напряжения малы и возникают редко.
В том случае, если значение суммарных напряжений на какомлибо участке заготовки превышает предел прочности материала, образуются трещины. Искажение геометрической формы изделий без разрушения (коробление) происходит в тех случаях, когда значение напряжений превышает предел текучести, но ниже предела прочности материала заготовки.
К числу наиболее распространенных дефектов, возникающих в отливках и сварных соединениях, относятся горячие и холодные трещины.
Горячие трещины в заготовках возникают в процессе кристаллизации и усадки металла при температуре, близкой к температуре солидуса. Эти трещины проходят по границам кристаллитов и имеют окисленную поверхность. Склонность сплавов к образованию горячих трещин увеличивается при наличии в металле неметаллических включений, газов (водорода, кислорода), серы и других примесей. Кроме того, к образованию горячих
48
трещин ведут резкие переходы от тонкой части заготовки к толстой, острые углы, выступающие части и т.д. Высокая температура заливки жидкого металла в форму или сварочной ванны способствует увеличению размеров кристаллитов и увеличивает перепад температур в отдельных частях заготовки, что повышает вероятность образования этих дефектов.
Холодные трещины возникают в области упругих деформаций, когда сплав полностью затвердел. Тонкие части заготовки охлаждаются и сокращаются быстрее, чем толстые. При этом в них возникают растягивающие напряжения, которые вызывают появление трещин. Холодные трещины чаще всего образуются в тонкостенных заготовках сложной конфигурации. Вероятность образования этих дефектов тем выше, чем значительнее усадка сплава при пониженных температурах, ниже его теплопроводность и выше упругие свойства. Опасность образования трещин в заготовках усиливается при наличии в сплаве вредных примесей (например, фосфора в сталях).
Металлы и сплавы в жидком состоянии участвуют в химическом взаимодействии с окружающей средой, сущность которого состоит в окислении металла, насыщении водородом и азотом, что приводит к снижению механических свойств и образованию газовой пористости. Химическое взаимодействие ограничивают уменьшением температуры жидкого металла и времени пребывания при высоких температурах. Кроме того, предварительно просушивают литейные формы, сварочные флюсы и применяют защитные среды (инертные газы, вакуум и др.) при нагреве, кристаллизации и остывании заготовок.
В процессе охлаждения жидкого металла выделяются газы, так как растворимость их выше в жидком состоянии, чем в твердом. При затвердевании металла растущие кристаллиты препятствуют свободному выделению пузырьков газа, поэтому значительная их часть может остаться в отливке или сварном шве, образуя газовую пористость. Сплавы с широким интервалом кристаллизации при значительном газонасыщении затвердевают с увеличением объема заготовки.
Для большинства сплавов характерна различная растворимость элементов в жидкой и твердой фазах. Процесс кристаллизации таких расплавов характеризуется ликвацией, т. е. неоднородностью химического состава в различных участках слитков, отливок и сварных швов. В сплавах различают внутрикристаллическую (микроскопическую) и зональную (макроскопическую) виды лик-
49
вации. Более подробно процесс образования ликвации рассматривается в дисциплине «Материаловедение».
5.3.Получение заготовок методами литья и сварки плавлением
При литье заготовок на процесс затвердевания и образования кристаллической структуры существенно влияет температура заливки металла в форму и скорость охлаждения отливки.
Низкие температуры заливки металла, как правило, приводят к образованию мелкозернистой структуры, а высокие вызывают получение крупных кристаллитов в заготовках.
Низкие скорости охлаждения отливки способствуют получению крупных дендритно-равноосных кристаллитов. С увеличением скорости охлаждения появляются зоны столбчатых кристаллитов. При очень большой скорости охлаждения расплава получается сплошная мелкая столбчатая структура большой плотности, для которой характерны высокие механические свойства.
Особенностью отливок, изготовленных с кристаллизацией под давлением (жидкая штамповка), является отсутствие прибылей и литниковых систем. При этом усадка заготовок определяется свойствами сплава, схемой прессования, давлением и временем выдержки отливки под нагрузкой. Увеличение давления и времени прессования способствуют уменьшению усадки отливки.
При сварке плавлением в результате расплавления кромок соединяемых элементов и присадочного материала образуется сварочная ванна. Этот процесс является разновидностью литья заготовок в металлическую форму, поэтому кристаллизация шва в значительной степени напоминает формирование отливок. Однако условия кристаллизациисварочной ванны имеютследующиеотличия:
−металл шва кристаллизуется со средней скоростью, равной скорости перемещения сварочной ванны;
−условия кристаллизации шва связаны с формой подвижного температурного поля;
−наличие «готовых» центров кристаллизации на стенках соединяемых элементов и др.
Размеры столбчатых кристаллитов зависят от способа и режимов сварки. Увеличение длительности существования сварочной ванны при высоких температурах, например, в случае электрошлаковой сварки, вызывает заметное увеличение размеров кристаллитов в зоне шва и зоне термического влияния.
50