
05 семестр / Лекции и семинары / Третьяков Курс лекций по дисциплине Технология конструкционных материалов
.pdfЛекция № 10. ТЕХНОЛОГИЧЕСКИЕ ПРОЦЕССЫ МЕХАНИЧЕСКОЙ ОБРАБОТКИ ЗАГОТОВОК РЕЗАНИЕМ
В этой лекции вы ознакомитесь с кинематикой резания, узнаете о физических закономерностях механической обработки резанием, ознакомитесь с показателями, характеризующими качество обработанной поверхности.
10.1.Особенности технологических процессов механической обработки заготовок
Обработка металлов резанием представляет собой процесс срезания режущим инструментом с поверхности заготовок слоя металла в виде стружки для получения необходимой геометрической формы, а также точности размеров, взаимного положения и качества поверхностей изделий. Большинство деталей сложной формы изготавливают путем механической обработки заготовок. С помощью режущего инструмента могут быть получены разные изделия – от деталей часовых механизмов до сосудов высокого давления диаметром свыше 3 м и других крупногабаритных изделий.
Существует большое разнообразие видов механической обработки заготовок резанием. Наиболее широкое применение среди них получили точение, растачивание, сверление, фрезерование, строгание, долбление и шлифование.
Механическая обработка резанием базируется на целенаправ-
ленном, управляемом разрушении поверхностного слоя. Металл, удаляемый в процессе обработки заготовки, подвергается пластическому деформированию и разрушению. В результате этого материал, отделяемый от обрабатываемой заготовки, приобретает характерную форму, и в таком виде его принято называть стружкой.
Для разрушения поверхностного слоя необходимо сообщить режущему инструменту и заготовке относительные движения. Перемещения рабочих органов станков подразделяют на движения резания, установочные и вспомогательные.
91
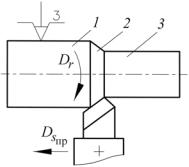
Движения, которые обеспечивают срезание с заготовки слоя металла или вызывают изменение состояния обрабатываемой поверхности, называют движениями резания. К ним относятся главное движение резания и движение подачи.
За главное движение резания (Dr) принимают движение, определяющее скорость деформирования поверхностного слоя заготовки и отделение стружки. Движение режущего инструмента или заготовки, предназначенное для того, чтобы распространить отделение слоя материала по всей обрабатываемой поверхности, принято называть движением подачи (Ds). Скорость главного движения резания обозначают v, скорость движения подачи – vs, при
этом v > vs.
Большинство принципиальных кинематических схем резания предусматривает сочетание двух движений – главного и подачи. При сложных сочетаниях трех одновременно осуществляемых движений дополнительное определяет специфику формообразования, например изготовление зубчатого колеса методом обкатки. Эти движения в совокупности определяют плоскую или пространственную траекторию результирующего перемещения точек главной режущей кромки.
Движение, обеспечивающее взаимное положение инструмента и заготовки для срезания с нее определенного слоя материала, на-
зывают установочным. К вспомогательным движениям относят транспортирование заготовки, закрепление заготовки и инструмента, быстрые перемещения рабочих органов станка.
Для любого процесса резания можно составить схему обработки, на которой показывают обрабатываемую заготовку, способ ее базирования, закрепления и положение инструмента относительно заготовки, а также движения резания (рис.
10.1). Инструмент показывают в положении, соответствующем окончанию обработки поверхности изделия. Движение подачи может быть продольным (ПР), поперечным (П), вертикальным (В), круговым (КР) и др. В процессе резания на заготовке различают обрабатываемую поверхность 1, обработанную поверхность 3 и поверхность резания 2
(см. рис. 10.1).
92
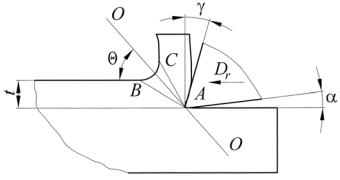
Пространственную форму детали определяют сочетанием различных поверхностей. Для облегчения механической обработки при проектировании детали стремятся использовать простые геометрические поверхности: плоские, цилиндрические, конические, шаровые и торовые.
10.2. Физические закономерности механической обработки резанием
Механическая обработка является сложным процессом взаимодействия режущей части инструмента и заготовки, заключающимся в упругопластическом деформировании в зоне резания, тепловыделении и изнашивании инструмента. Процесс резания заготовки резцом можно упрощенно представить в виде схемы
(рис. 10.2).
Рис. 10.2. Зона деформации при превращении срезаемого слоя в стружку:
θ – угол сдвига; γ – передний угол инструмента; α – задний угол
Сложное упруго-напряженное состояние металла приводит к пластической деформации, а рост ее – к сдвиговым деформациям, которые происходят в зоне стружкообразования АВС, причем деформации начинаются по плоскости АВ и заканчиваются по плоскости АС, в которой образуется стружка. Далее процесс повторяется и образуется следующий элемент стружки. Принято считать, что сдвиговые деформации происходят по плоскости ОО, которую называют условной плоскостью сдвига или скалывания. Она располагается под углом θ ≈ 30º.
93

Схема напряженного состояния объема металла, расположенного на условной плоскости сдвига, и эпюры изменения касательных и нормальных напряжений вдоль указанной линии изображены на рис. 10.3. Независимо от свойств обрабатываемого материала, переднего угла инструмента γ (см. рис. 10.2), толщины срезаемого слоя и скорости резания касательные напряжения τ вдоль условной плоскости сдвига имеют постоянное значение. Нормальные напряжения σу, сохраняя постоянство знака, увеличиваются при приближении к лезвию (см. рис. 10.3).
Рис. 10.3. Схема напряженного состояния на условной плоскости сдвига:
γ – передний угол; δ – угол режущего клина; α – задний угол; t – толщина срезаемого слоя (глубина резания); θ – угол сдвига
Срезаемые стружки имеют различную форму, зависящую от свойств материала обрабатываемой заготовки, толщины срезаемого слоя, геометрических параметров режущего инструмента, режима резания и других факторов. Все стружки по внешнему виду и строению разделяют на четыре основных типа: сливная, суставчатая, элементная и надлома (рис. 10.4).
94
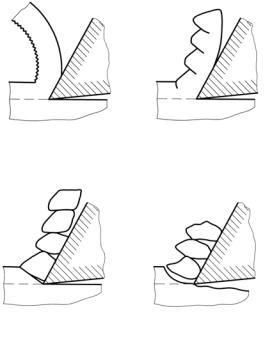
аб
вг
Рис. 10.4. Типы стружек, образующихся при резании пластичных и хрупких материалов:
а – сливная; б – суставчатая; в – элементная; г – надлома
Сливная стружка образуется при резании пластичных материалов и представляет собой сплошную ленту с гладкой прирезцовой стороной. Суставчатая cтружка, образующаяся при обработке металлов средней твердости, представляет собой ленту, на внешней стороне которой присутствуют ярко выраженные зазубрины. Элементная стружка состоит из отдельных элементов приблизительно одинаковой формы, не связанных друг с другом. Стружка надлома образуется при резании хрупких металлов и состоит из отдельных, не связанных между собой элементов различной формы и размеров. При этом поверхность сдвига может располагаться ниже поверхности резания, в результате чего последняя покрыта следами выломанных из нее клочков стружки.
Тип стружки влияет на износ режущего инструмента, шероховатость обработанной поверхности и силу резания. Чтобы перевести стружку из одного состояния в другое, например, суставчатую
95
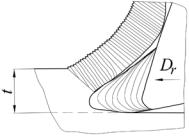
стружку в элементную, в конструкциию режущего инструмента вводят стружколомательные устройства, порожки и разделительные канавки. Иногда применяют прерывистый процесс резания или вибрационное резание металлов.
Обработке резанием большинства конструкционных материалов при определенных условиях сопутствует явление, называемое наростообразованием. Под наростом понимают клиновидную область материала обрабатываемой заготовки, расположенную у лезвия инструмента перед ее передней поверхностью (рис.
10.5).
Образование нароста объясняется тем, что геометрическая форма инструмента не идеальна для обтекания ее металлом. При некоторых условиях обработки силы трения между передней поверхностью
инструмента и частицами срезаемого слоя становятся больше сил внутреннего сцепления. Поэтому при определенных температурах и давлениях, обусловленных параметрами процесса резания, материал заготовки прочно удерживается силами адгезии на передней поверхности инструмента.
В процессе обработки резанием размеры и форма нароста непрерывно меняются в результате действия сил трения между сходящей стружкой и внешней поверхностью нароста. Эксперименты показывают, что частицы нароста постоянно уносятся стружкой, увлекаются обрабатываемой поверхностью заготовки, иногда нарост целиком срывается с передней поверхности инструмента и тут же вновь образуется. Нарост существенно влияет на процесс резания и качество обработанной поверхности заготовки, так как при его наличии меняются условия стружкообразования.
Положительное влияние нароста состоит в том, что при его наличии форма лезвия инструмента изменяется таким образом, что сила резания уменьшается. При определенных скоростях резания нарост уменьшает износ режущего инструмента по передней и задней поверхностям. Кроме того, нарост улучшает теплоотвод от режущего инструмента.
Отрицательное влияние нароста состоит в том, что он увеличивает шероховатость обработанной поверхности. При периодичес-
96

ком разрушении вершины нароста на поверхности заготовки образуются надрывы и борозды, а часть нароста внедряется в обработанную поверхность (рис. 10.6). Вследствие нестабильности нароста изменяются размеры обрабатываемой поверхности, которая получается волнистой. Нарост изменяет передний угол инструмента и, как следствие, меняется сила резания, что вызывает вибрацию узлов станка и инструмента, а это, в свою очередь, ухудшает
качество обработанной поверхности. |
|
Наростообразование зависит от |
|
физико-механических свойств об- |
|
рабатываемых заготовок, скорости |
|
резания, геометрических парамет- |
|
ров режущего инструмента и дру- |
|
гих факторов. Наиболее интенсивно |
|
нарост образуется при обработке |
|
пластичных металлов при скоро- |
|
стях резания 0,3…0,5 м/с. При ско- |
|
ростях резания до 0,2 м/с и свыше |
Рис. 10.6. Разрушение вершины |
1 м/с нарост на режущем инстру- |
нароста и образование неровно- |
менте практически не образуется. |
сти на поверхности резания |
Таким образом, нарост оказы- |
|
вает благоприятное воздействие при черновой обработке, когда возникают большие силы резания, срезается толстый слой металла и выделяется большое количество теплоты. Однако нарост вреден при чистовой обработке, например, при протягивании, нарезании резьбы, развертывании, так как приводит к снижению качества обрабатываемой поверхности.
10.3. Качество обработанной поверхности
Качество обработанной поверхности определяется ее шероховатостью и состоянием материала поверхностного слоя. Шероховатостью поверхности называют совокупность неровностей с относительно малыми шагами. Состояние материала поверхностного слоя характеризуется его упрочнением (наклепом), микроструктурой, величиной и знаком остаточных напряжений и глубиной их залегания.
На высоту неровностей влияют геометрические параметры режущего инструмента, режим резания, механические свойства обрабатываемого и инструментального материалов, а также условия трения на контактных поверхностях инструмента. При
97
уменьшении подачи (толщины срезаемого слоя) высота неровностей уменьшается. Глубина резания (ширина срезаемого слоя) не оказывает значительного влияния на шероховатость поверхности. Влияние скорости резания на высоту неровностей проявляется по-разному, в зависимости от того, склонен или нет обрабатываемый материал к наростообразованию. Если материал не склонен к наростообразованию, то по мере увеличения скорости резания высота неровностей непрерывно уменьшается. Это связано с уменьшением объема пластической деформации и коэффициента трения. При образовании нароста шероховатость находится в прямой зависимости от высоты нароста. Поэтому для получения низкой шероховатости поверхности необходимо проводить обработку со скоростями резания, соответствующими минимальной высоте нароста.
Использование смазочно-охлаждающих технологических сред позволяет в большинстве случаев уменьшить высоту неровностей. При этом по мере увеличения скорости резания действие смазоч- но-охлаждающей жидкости ослабевает. Это связано как с уменьшением времени физико-химического воздействия жидкости, так и с затруднением проникновения ее на переднюю поверхность инструмента.
Физико-механические свойства поверхностного слоя во многом определяют эксплуатационные свойства деталей машин. Важнейшими показателями состояния поверхностного слоя являются величина, знак и глубина залегания остаточных напряжений, степень наклепа и толщина упрочненного слоя.
Остаточные напряжения, возникающие в поверхностном слое, и его наклеп являются следствием воздействия, создаваемого силами резания и нагрева материала обрабатываемой заготовки, вызывающего структурные превращения. При резании лезвийным инструментом (точении, фрезеровании, сверлении и т. п.) остаточные напряжения образуются главным образом под действием силового контакта, а температура имеет вторичное значение. При высокотемпературном режиме (шлифовании) остаточные напряжения образуются вследствие высокой температуры поверхностного слоя и всегда являются растягивающими.
Наличие в поверхностном слое растягивающих напряжений значительно ухудшает усталостную прочность детали. В том случае, когда остаточные напряжения превосходят предел прочности материала обрабатываемой заготовки, образуются поверхностные трещины. Величина и глубина залегания остаточных напряжений
98
зависят от скорости резания, подачи (толщины срезаемого слоя), геометрических параметров инструмента и степени его износа.
В зависимости от физико-механических свойств материала обрабатываемой заготовки и режима резания глубина наклепанного слоя составляет от нескольких миллиметров при черновой обработке до сотых и тысячных долей миллиметра при чистовой. Неравномерная релаксация остаточных напряжений искажает геометрическую форму обработанных поверхностей, снижает точность их взаимного расположения и размеров.
Следовательно, окончательную обработку поверхностей заготовок следует вести таким образом, чтобы остаточные напряжения отсутствовали или были минимальными. Для получения в поверхностном слое напряжений сжатия можно рекомендовать обработку поверхностным пластическим деформированием.
Вопросы для самоконтроля
1.Какие виды механической обработки резанием реализуют при изготовлении деталей машин? Укажите технологические особенности процессов механической обработки резанием.
2.Назовите движения резания, обеспечивающие срезание с заготовки слоя металла. Какое движение называют установочным?
3.Сформулируйте физические основы стружкообразования при резании. Какие факторы влияют на тип стружки?
4.Объясните механизм наростообразования на режущей кромке инструмента и влияние нароста на качество обрабатываемой поверхности заготовки.
5.Назовите причины упрочнения поверхности заготовок в процессе резания. Какое влияние оказывает упрочнение на качество детали?
6.Какие основные факторы механической обработки резанием определяют качество поверхностного слоя деталей машин?
99
Лекция № 11. ВЛИЯНИЕ НА КАЧЕСТВО ИЗДЕЛИЯ СИЛОВОГО ВЗАИМОДЕЙСТВИЯ ИНСТРУМЕНТА И ЗАГОТОВКИ
Эта лекция посвящена изучению влияния сил, возникающих в процессе резания, деформации заготовки и тепловых явлений на качество изделий. Вы ознакомитесь с сущностью процессов изнашивания лезвийных режущих инструментов.
11.1. Силы, возникающие в процессе резания
Процесс резания характеризуется силовым воздействием инструмента на заготовку, в результате чего в зоне их контакта происходит деформирование, а также разрушение поверхностного слоя заготовки – снятие стружки. Деформирование и срезание с заготовки слоя металла происходит под действием внешней силы R, приложенной со стороны инструмента к обрабатываемой заготовке. Направление вектора силы совпадает с вектором скорости резания v. Работа, затрачиваемая на деформирование и разрушение материала заготовки, расходуется на упругую и пластическую деформации металла, его разрушение, а также на преодоление сил трения инструмента о заготовку и стружку.
Заготовку закрепляют для уравновешивания силового воздействия со стороны инструмента, т. е. прикладывают к ней силы со стороны приспособления. В результате образуется замкнутая система, состоящая из станка, приспособления, заготовки и инструмента. На рис. 11.1 показанасхема действиясилприобработке цилиндрической заготовки. Значение силы резания и ее положение в пространстве зависят от физико-механических свойств материала обрабатываемой заготовки, толщины снимаемого слоя, скорости резания, подачи, геометрическихразмероврежущейчастиинструментаидругихфакторов.
Для удобства расчетов используют не равнодействующую силу резания R, а ее составляющие, действующие по трем взаимно перпендикулярным направлениям – координатным осям металлорежущего станка.
100