
05 семестр / К экзамену-зачёту / Ответы на экзаменационные вопросы / отвыеты на вопросы / практика2
.pdfПасты – паста ГОИ, алмазные пасты. Для ускорения притирки ее начинают с крупнозернистых порошков, а для получения необходимой шероховатости заканчивают мелкозернистыми порошками.
Сущность притирки заключается в том, что очень мелкими зернами абразивного материала, расположенными между поверхностью инструмента
(притира) и обрабатываемой поверхностью, с последней срезают мельчайшие неровности, и она приобретает требумую точность размеров и шероховатость.
Притиры изготавливают из материалов менее твердых, чем обрабатываемые детали, например, из чугуна, меди, латуни, древесины и др. Абразивные зерна шаржируют притир и при относительном движении притира по обрабатываемой поверхности осуществляют обработку. Форма притиров должна соответствовать форме обрабатываемой поверхности.
Абразивные материалы используют в виде порошков или паст. Порошки – наждак,
корунд, карбид кремния, окись хрома и др. Пасты – паста ГОИ, алмазные пасты.
Припуск на притирку обычносоставляет 0,01 -0,02 мм.
Приработка
Аналогична притирке, только вместо притира используют сопрягаемую деталь и ее применяют, когда необходимо обеспечить соединение деталей с органическими растворителями и дистиллированной водой.
Механическая обработка деталей
Характерной особенностью сборки многих оптических приборов является необходимость дополнительной механической обработки деталей непосредственно в сборочном цехе.
Наиболее распространенные виды дополнительной обработки следующие:
сверление, развертывание, зенковка, нарезание резьбы под винты, шпильки и др.,
растачивание точных посадочных отверстий и подрезка торцов в заданный размер,
притирка деталей и шабрение плоскостей и направляющих.
Притирка и приработка
Притиркой называют обработку поверхности детали абразивными порошками или пастами с целью получения разъемных и подвижных соединений, к которым предъявляются дополнительные требования по обеспечению плавности хода при отсутствии зазором порядка 1-2 мкм.
Притирку и приработку производят вручную или на токарных станках с помощью специальных приспособлений для закрепления деталей.
После обработки необходимо весьма тщательно промыть детали, чтобы удалить с поверхности абразивные зерна.
Шабрение
Процесс шабрения заключается в соскабливании тонких слоев металла для получения точной и ровной поверхности детали, т.е. прямолинейности и плоскостности.
Инструментом для шабрения служит шабер.
Процесс шабрения делят на две стадии.
Первая стадия – выравнивание обрабатываемой поверхности. Берут поверочную плиту, смазанную тонким слоем краски (сажа, синька разведенная в масле) и накладывают на нее деталь, которую перемещают в разных направлениях.
Выступающие места поверхности детали окрашиваются, и их соскабливают шабером. Это продолжается до тех пор, пока вся обрабатываемая поверхность не будет равномерно покрываться пятнами краски.
На второй стадии обеспечивают необходимую точность поверхности, для чего крупные пятна краски шабрением разбивают на более мелкие.
Точность шабрения определяют по числу точек контакта детали и плиты,
приходящихся на поверхность квадрата 25 х 25 мм. Чем точнее шабрение, тем большее число точек приходится на единицу поверхности.
Для герметичного соединения двух плоскостей количество точек контакта должно быть не менее пяти на участке 25 х 25 мм. Чтобы обеспечить прямолинейность и плавность хода соединения типа «ласточкин хвост», рабочие поверхности детали должны быть пришабрены с точностью 10 -12 точек контакта.
Шабрение дает возможность получать правильную плоскость с отклонением до 0,005 мм. Припуск на шабрение не должен превышать 0,1 мм.
Шабрение в основном применяют в условиях единичного и мелкосерийного производства в следующих случаях:
для герметизации соединений двух плоскостей (если требуется);
для обеспечения прямолинейности движения, плавности хода без люфта;
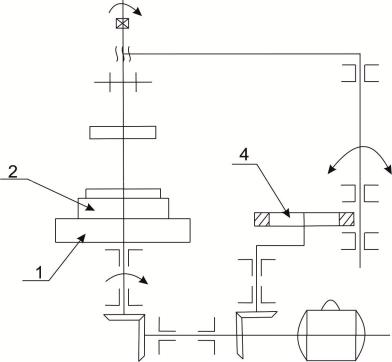
для обеспечения положения контрольных установочных площадок приборов под уровень. Шабрение в этом случае производится после юстировки прибора.
декоративное шабрение.
Схема механической притирки 1 – притир; 2 – притираемая деталь; 4 – кулиса.
Ручная притирка – процесс трудоемкий и малопроизводительный, поэтому операции притирки необходимо всемерно механизировать.
Одна из конструкций притирочных станков показана на рис. . Плоские поверхности притираются при вращающемся притире 1 и маятниковом движении детали 2, причем одно и то же зерно не проходит по одному и тому же месту детали дважды.
При притирке обязательно применяют машинное масло, керосин, скипидар и другие смазывающие жидкости.
Припуск на притирку обычно составляет 0,01 – 0,02 мм.
Смазка механических узлов
На поверхности механических деталей в процессе сборки наносят различные смазки. Трущиеся поверхности покрывают смазками, обеспечивающими плавность хода подвижных соединений. Внутренние нетрущиеся поверхности прибора,
расположенные вблизи оптических деталей, протирают специальными смазками,
предотвращающими осыпку частиц отделочных покрытий др. инородных материалов. И, наконец, антикоррозионные смазки.
Смазки для оптических приборов должны не загустевать и не вытекать из соединений в пределах рабочих температур прибора; не высыхать и сохранять свойства в течение длительного времени (1 – 2 года), не вызывать налетов на оптических деталях и не разбрызгиваться при ударах и вибрациях прибора и т.д.
В зависимости от вида и вязкости различают смазки твердые, консистентные и масла (жидкие).
Консистентная смазка ГОИ-54П состоит из церезина, масла МВП и масла костного. Она предназначена для смазывания трущихся поверхностей механических соединений, близко расположенных к оптическим деталям и имеющих зазоры от 5
до 50 мкм.
Для смазывания механических соединений, работающих при больших нагрузках (например, червячные и фрикционные передачи), рекомендуются церезино-графитовые смазки типа БВН-1, содержащие от 3 до 35% коллоидно-
графитового препарата С-1 с частицами до 4 мкм.
При сборке объективов фотоаппаратов для смазывания окулярной резьбы применяют смазку М3-5, выдерживающую температуру от -15 до +50°С.
Смазки ОКБ-122-7 и ЦИАТИМ-202 применяют при сборке шарикоподшипников и узлов трения, удаленных от оптических деталей (-70 до
+120°С).
Смазка «Орион» (церезин, масло авиационное, воск пчелиный) применяется для предохранения от осыпки.
При сборке узлов типа часовых механизмов (автоспуски, мосты замедления фотоаппаратуры) для смазывания зубчатых колес, трибок применяют часовое масло
МЗП-6. Для смазывания осей лепестков центральных затворов фотообъективов использую масло веретенное марки АУ.
Для консервации металлических деталей при длительном хранении применяют пушечную смазку ПВК или ГОИ-54П. Эти смазки имеют хорошие защитные свойства.
Наносят смазки на поверхности металлических деталей при помощи шпателя
(деревянной лопаточки), щетки, кисточки или салфетки, смоченной в масле.
Герметизация приборов
Многие приборы работают в различных климатических условиях (жара,
холод, дождь, снег, морская вода и т.д.). Проникновение внутрь прибора влаги,
пыли, паров приводит к образованию налетов на оптических деталях, коррозии металлических деталей.
Герметизацию оптических приборов осуществляют двумя способами: путем введения в конструкцию прибора различного рода прокладок, сальников,
уплотнителей или применением уплотнительных замазок, которыми заполняют стыки. Уплотнительные замазки бывают трех видов: мягкие, полутвердые, твердые.
В состав мягких замазок входят церезин, канифоль, масло МВП, петролатум, воск.
Мягкие замазки работают в интервале температур ±60°С и применяются для уплотнения зазоров более 0,5 мм, заливки резьбы, постановки защитных стекол.
Замазка полутвердая содержит церезин, канифоль, вазелин, битум, масло трансформаторное, каолин, которые, находясь в в определенном весовом соотношении, обеспечивают хорошее качество уплотнения в интервале температур
±60°С.
Замазка твердая состоит из церезина, канифоли, озокерита, воска, битума,
масла МС-14 и рубрикса. Сохраняет свои свойства в интервале температур от -60 до
+70°С и применяется в приборах, предназначенных для работы в тропиках.
Кроме этих замазок применяют специальные уплотнители, например, «Герметик УТ-34», который хорошо выдерживает температурные перепады от -60
до +100°С, вибрационные и ударные нагрузки.
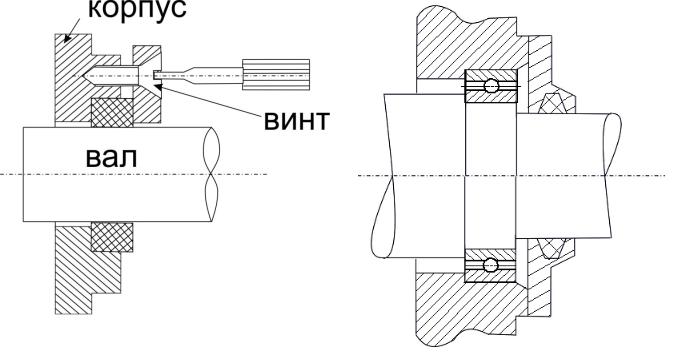
Технологический процесс герметизации узлов включает следующие операции:
обезжиривание поверхностей деталей, нанесение слоя замазки на сопрягаемые детали, плотное прижатие деталей крепежными элементами (винтами, болтами) и
удаление остатков.
Сборка уплотнений
Уплотнения, герметизирующие выходы вращающихся валов в конструкциях многих приборов, выполнены в виде войлочного пальца, зажатого в выточке корпуса крышкой (рис. 1,а). Толщина войлочного пальца должна быть больше глубины выточки, Кольцо, надетое на вал, вводят в выточку при помощи плоской выколотки. После этого закрепляют винтами крышку.
Другой распространенный вид войлочного или фетрового уплотнения показан на (рис.1,б). В этом случае кольцо вводят в коническую выточку крышки. Вручную на это требуется много времени, к тому же сборочная единица нередко получается некачественной – кольцо перекашивается, образуются складки и т.п. В серийном и массовом производстве пользуются приспособлениями, устанавливаемыми на прессе.
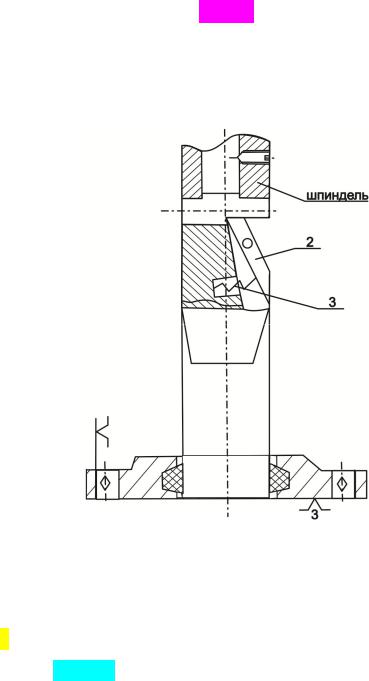
Рис. 1, а |
Рис. 1, а |
Второй операцией является окончательная заправка кольца в выточку и обрезка лишнего материала. Эту операцию выполняют на сверлильном станке, в
шпиндель которого вставляют оправку 1 (рис.2) с ножом 2, отжимаемым пружиной
3. Благодаря конусу оправки при ее опускании и вращении войлочное кольцо войдет в выточку, а излишки войлока будут срезаны.
Рис.2
Поверхность колец должна быть чистой, без ворса, утолщений и выемок.
Линии обреза должны быть ровными, без надрезов и рваных мест. В некоторых случаях фетровые кольца пропитывают в смеси: 75% технического глицерина, 20%
натриевого мыла и 5 % учатого графита.
Для предотвращения просачивания жидкостей или газов по выходящим наружу валам применяют сальниковые уплотнения. Герметичность соединения проверяют следующими способами:
1)Путем нагнетания воздуха в прибор и погружения его в воду. Место течи устанавливается по воздушным пузырькам, выходящим из незагерметизированных мест.
2)Путем нагнетания воздуха в прибор и смачивания швов мыльной водой. Место течи устанавливается по мыльным пузырькам.
3)Путем создания избыточного давления в приборе и определения спада давления по манометру.
Сборка замкнутых конструктивных цепей
При сборке реализуется базирование ЗКЦ (точнее ее РЭц), т.е. придание определенного положения в пространстве относительно других цепей. Оно осуществляется через присоединение базового элемента КБД цепи к монтажной основе более крупной сборочной единицы (узел, функциональное устройство,
прибор), в которую входит присоединяемая цепь. Как отмечалось КБД ЗКЦ всегда неподвижна, поэтому указанное присоединение сопровождается закреплением КБД цепи на монтажной основе. Схема сборки зависит от схемы базирования ЗКЦ на монтажной основе. В оптических приборах применяется в основном следующие типы монтажных основ: цилиндрические трубы; платы, получаемые обработкой резанием из пластин, а также штамповкой, литые металлические или пластмассовые корпуса сложных форм; литые станины.
Типовым для ОП является базирование цепей, имеющих КБД цилиндрической формы (трубу), на МО, представляющий собой стенку корпуса (рис. 3.6., а) или цилиндрическую трубу (рис. 3.6.,б).
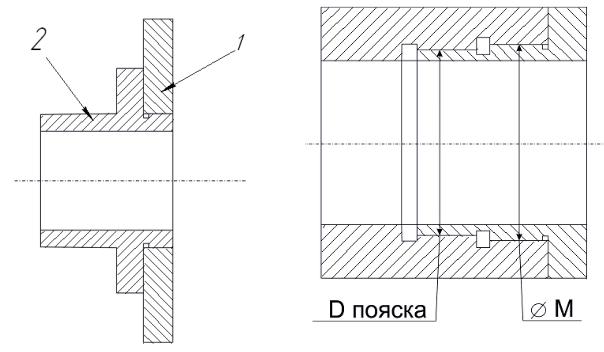
а) б)
Рис. 3.6. Базирование КБД цилиндрической формы: 1 – монтажная основа, 2 – КБД присоединяемой ЗКЦ
Надежное базирование достигается с помощью фланца (круглой или прямоугольной формы) и узкого цилиндрического центрирующего пояска(рис.3.6.,а).
Фланец является парой класса P3 , а поясок – парой P2, вместе они ограничивают пять степеней свободы КБД, а крепление фланца к стенке корпуса не лишает ее шестой.
Для обеспечения высокой точности базирования конструктор должен заказать высокую точность диаметров контактирующих поверхностей и плоскостей, кроме того ужесточить точность их взаимного расположения.
Следует иметь в виду, что резьба центрирует неточно, поэтому как средство центрирования она применяется в «грубых» оптических устройствах. Для более точной установки трубы КБД на ней делается цилиндрический центрирующий поясок (рис. 3.6.,б).
Другим весьма распространенным в ОП является базирование ЗКЦ на плоскости
(стенках корпусов, платах и т.д.) с помощью несущих кронштейнов. Такое