
- •Textbook Series
- •Contents
- •1 Overview and Definitions
- •Overview
- •General Definitions
- •Glossary
- •List of Symbols
- •Greek Symbols
- •Others
- •Self-assessment Questions
- •Answers
- •2 The Atmosphere
- •Introduction
- •The Physical Properties of Air
- •Static Pressure
- •Temperature
- •Air Density
- •International Standard Atmosphere (ISA)
- •Dynamic Pressure
- •Key Facts
- •Measuring Dynamic Pressure
- •Relationships between Airspeeds
- •Airspeed
- •Errors and Corrections
- •V Speeds
- •Summary
- •Questions
- •Answers
- •3 Basic Aerodynamic Theory
- •The Principle of Continuity
- •Bernoulli’s Theorem
- •Streamlines and the Streamtube
- •Summary
- •Questions
- •Answers
- •4 Subsonic Airflow
- •Aerofoil Terminology
- •Basics about Airflow
- •Two Dimensional Airflow
- •Summary
- •Questions
- •Answers
- •5 Lift
- •Aerodynamic Force Coefficient
- •The Basic Lift Equation
- •Review:
- •The Lift Curve
- •Interpretation of the Lift Curve
- •Density Altitude
- •Aerofoil Section Lift Characteristics
- •Introduction to Drag Characteristics
- •Lift/Drag Ratio
- •Effect of Aircraft Weight on Minimum Flight Speed
- •Condition of the Surface
- •Flight at High Lift Conditions
- •Three Dimensional Airflow
- •Wing Terminology
- •Wing Tip Vortices
- •Wake Turbulence: (Ref: AIC P 072/2010)
- •Ground Effect
- •Conclusion
- •Summary
- •Answers from page 77
- •Answers from page 78
- •Questions
- •Answers
- •6 Drag
- •Introduction
- •Parasite Drag
- •Induced Drag
- •Methods of Reducing Induced Drag
- •Effect of Lift on Parasite Drag
- •Aeroplane Total Drag
- •The Effect of Aircraft Gross Weight on Total Drag
- •The Effect of Altitude on Total Drag
- •The Effect of Configuration on Total Drag
- •Speed Stability
- •Power Required (Introduction)
- •Summary
- •Questions
- •Annex C
- •Answers
- •7 Stalling
- •Introduction
- •Cause of the Stall
- •The Lift Curve
- •Stall Recovery
- •Aircraft Behaviour Close to the Stall
- •Use of Flight Controls Close to the Stall
- •Stall Recognition
- •Stall Speed
- •Stall Warning
- •Artificial Stall Warning Devices
- •Basic Stall Requirements (EASA and FAR)
- •Wing Design Characteristics
- •The Effect of Aerofoil Section
- •The Effect of Wing Planform
- •Key Facts 1
- •Super Stall (Deep Stall)
- •Factors that Affect Stall Speed
- •1g Stall Speed
- •Effect of Weight Change on Stall Speed
- •Composition and Resolution of Forces
- •Using Trigonometry to Resolve Forces
- •Lift Increase in a Level Turn
- •Effect of Load Factor on Stall Speed
- •Effect of High Lift Devices on Stall Speed
- •Effect of CG Position on Stall Speed
- •Effect of Landing Gear on the Stall Speed
- •Effect of Engine Power on Stall Speed
- •Effect of Mach Number (Compressibility) on Stall Speed
- •Effect of Wing Contamination on Stall Speed
- •Warning to the Pilot of Icing-induced Stalls
- •Stabilizer Stall Due to Ice
- •Effect of Heavy Rain on Stall Speed
- •Stall and Recovery Characteristics of Canards
- •Spinning
- •Primary Causes of a Spin
- •Phases of a Spin
- •The Effect of Mass and Balance on Spins
- •Spin Recovery
- •Special Phenomena of Stall
- •High Speed Buffet (Shock Stall)
- •Answers to Questions on Page 173
- •Key Facts 2
- •Questions
- •Key Facts 1 (Completed)
- •Key Facts 2 (Completed)
- •Answers
- •8 High Lift Devices
- •Purpose of High Lift Devices
- •Take-off and Landing Speeds
- •Augmentation
- •Flaps
- •Trailing Edge Flaps
- •Plain Flap
- •Split Flap
- •Slotted and Multiple Slotted Flaps
- •The Fowler Flap
- •Comparison of Trailing Edge Flaps
- •and Stalling Angle
- •Drag
- •Lift / Drag Ratio
- •Pitching Moment
- •Centre of Pressure Movement
- •Change of Downwash
- •Overall Pitch Change
- •Aircraft Attitude with Flaps Lowered
- •Leading Edge High Lift Devices
- •Leading Edge Flaps
- •Effect of Leading Edge Flaps on Lift
- •Leading Edge Slots
- •Leading Edge Slat
- •Automatic Slots
- •Disadvantages of the Slot
- •Drag and Pitching Moment of Leading Edge Devices
- •Trailing Edge Plus Leading Edge Devices
- •Sequence of Operation
- •Asymmetry of High Lift Devices
- •Flap Load Relief System
- •Choice of Flap Setting for Take-off, Climb and Landing
- •Management of High Lift Devices
- •Flap Extension Prior to Landing
- •Questions
- •Annexes
- •Answers
- •9 Airframe Contamination
- •Introduction
- •Types of Contamination
- •Effect of Frost and Ice on the Aircraft
- •Effect on Instruments
- •Effect on Controls
- •Water Contamination
- •Airframe Aging
- •Questions
- •Answers
- •10 Stability and Control
- •Introduction
- •Static Stability
- •Aeroplane Reference Axes
- •Static Longitudinal Stability
- •Neutral Point
- •Static Margin
- •Trim and Controllability
- •Key Facts 1
- •Graphic Presentation of Static Longitudinal Stability
- •Contribution of the Component Surfaces
- •Power-off Stability
- •Effect of CG Position
- •Power Effects
- •High Lift Devices
- •Control Force Stability
- •Manoeuvre Stability
- •Stick Force Per ‘g’
- •Tailoring Control Forces
- •Longitudinal Control
- •Manoeuvring Control Requirement
- •Take-off Control Requirement
- •Landing Control Requirement
- •Dynamic Stability
- •Longitudinal Dynamic Stability
- •Long Period Oscillation (Phugoid)
- •Short Period Oscillation
- •Directional Stability and Control
- •Sideslip Angle
- •Static Directional Stability
- •Contribution of the Aeroplane Components.
- •Lateral Stability and Control
- •Static Lateral Stability
- •Contribution of the Aeroplane Components
- •Lateral Dynamic Effects
- •Spiral Divergence
- •Dutch Roll
- •Pilot Induced Oscillation (PIO)
- •High Mach Numbers
- •Mach Trim
- •Key Facts 2
- •Summary
- •Questions
- •Key Facts 1 (Completed)
- •Key Facts 2 (Completed)
- •Answers
- •11 Controls
- •Introduction
- •Hinge Moments
- •Control Balancing
- •Mass Balance
- •Longitudinal Control
- •Lateral Control
- •Speed Brakes
- •Directional Control
- •Secondary Effects of Controls
- •Trimming
- •Questions
- •Answers
- •12 Flight Mechanics
- •Introduction
- •Straight Horizontal Steady Flight
- •Tailplane and Elevator
- •Balance of Forces
- •Straight Steady Climb
- •Climb Angle
- •Effect of Weight, Altitude and Temperature.
- •Power-on Descent
- •Emergency Descent
- •Glide
- •Rate of Descent in the Glide
- •Turning
- •Flight with Asymmetric Thrust
- •Summary of Minimum Control Speeds
- •Questions
- •Answers
- •13 High Speed Flight
- •Introduction
- •Speed of Sound
- •Mach Number
- •Effect on Mach Number of Climbing at a Constant IAS
- •Variation of TAS with Altitude at a Constant Mach Number
- •Influence of Temperature on Mach Number at a Constant Flight Level and IAS
- •Subdivisions of Aerodynamic Flow
- •Propagation of Pressure Waves
- •Normal Shock Waves
- •Critical Mach Number
- •Pressure Distribution at Transonic Mach Numbers
- •Properties of a Normal Shock Wave
- •Oblique Shock Waves
- •Effects of Shock Wave Formation
- •Buffet
- •Factors Which Affect the Buffet Boundaries
- •The Buffet Margin
- •Use of the Buffet Onset Chart
- •Delaying or Reducing the Effects of Compressibility
- •Aerodynamic Heating
- •Mach Angle
- •Mach Cone
- •Area (Zone) of Influence
- •Bow Wave
- •Expansion Waves
- •Sonic Bang
- •Methods of Improving Control at Transonic Speeds
- •Questions
- •Answers
- •14 Limitations
- •Operating Limit Speeds
- •Loads and Safety Factors
- •Loads on the Structure
- •Load Factor
- •Boundary
- •Design Manoeuvring Speed, V
- •Effect of Altitude on V
- •Effect of Aircraft Weight on V
- •Design Cruising Speed V
- •Design Dive Speed V
- •Negative Load Factors
- •The Negative Stall
- •Manoeuvre Boundaries
- •Operational Speed Limits
- •Gust Loads
- •Effect of a Vertical Gust on the Load Factor
- •Effect of the Gust on Stalling
- •Operational Rough-air Speed (V
- •Landing Gear Speed Limitations
- •Flap Speed Limit
- •Aeroelasticity (Aeroelastic Coupling)
- •Flutter
- •Control Surface Flutter
- •Aileron Reversal
- •Questions
- •Answers
- •15 Windshear
- •Introduction (Ref: AIC 84/2008)
- •Microburst
- •Windshear Encounter during Approach
- •Effects of Windshear
- •“Typical” Recovery from Windshear
- •Windshear Reporting
- •Visual Clues
- •Conclusions
- •Questions
- •Answers
- •16 Propellers
- •Introduction
- •Definitions
- •Aerodynamic Forces on the Propeller
- •Thrust
- •Centrifugal Twisting Moment (CTM)
- •Propeller Efficiency
- •Variable Pitch Propellers
- •Power Absorption
- •Moments and Forces Generated by a Propeller
- •Effect of Atmospheric Conditions
- •Questions
- •Answers
- •17 Revision Questions
- •Questions
- •Answers
- •Explanations to Specimen Questions
- •Specimen Examination Paper
- •Answers to Specimen Exam Paper
- •Explanations to Specimen Exam Paper
- •18 Index
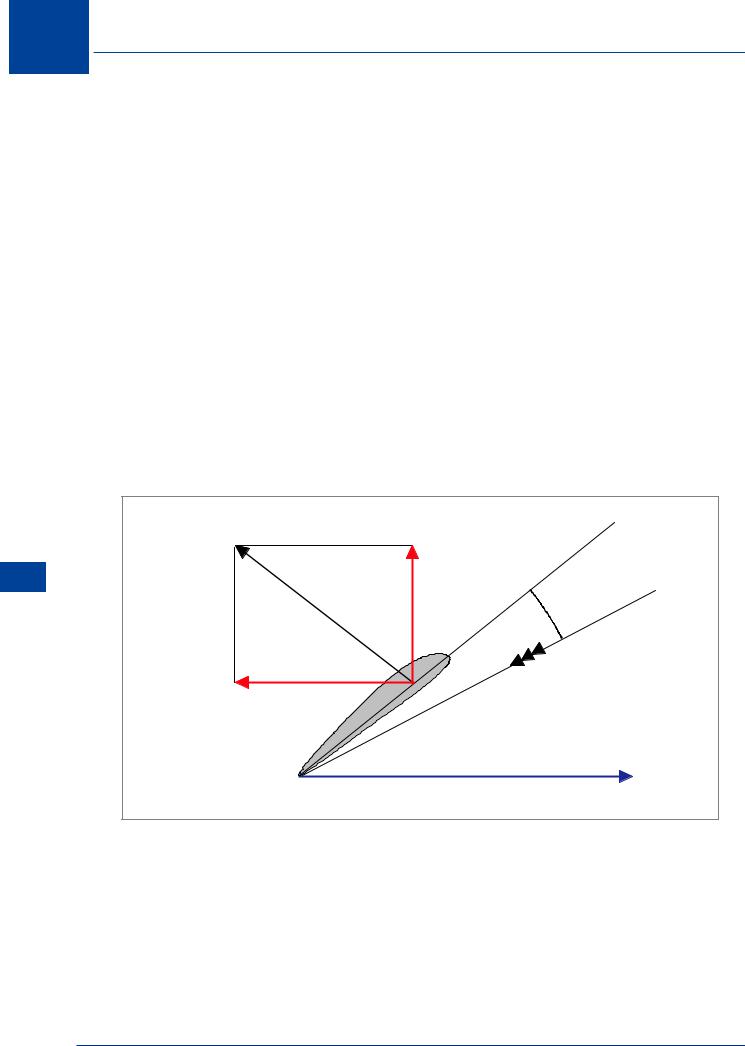
16 Propellers
Aerodynamic Forces on the Propeller
Propellers 16
A propeller blade has an aerofoil section, and when moving through the air at an angle of attack it will generate aerodynamic forces in the same way as a wing. The shape of the section will generate a pressure differential between the two surfaces. The surface which has the greater pressure is called the “pressure face” or “thrust face”. When the propeller is giving forward thrust, the thrust face is the rear, (flat) surface. The pressure differential will generate an aerodynamic force, the total reaction, which may be resolved into two components, thrust and propeller torque.
Thrust
A component at right angles to the plane of rotation. The thrust force will vary along the length of each blade, reducing at the tip where the pressures equalize and towards the root where the rotational velocity is low. Thrust will cause a bending moment on each blade, tending to bend the tip forward. (Equal and opposite reaction to “throwing” air backwards).
Torque (Propeller)
Torque is the equal and opposite reaction to the propeller being rotated, which generates a turning moment about the aircraft longitudinal axis. Propeller torque also gives a bending moment to the blades, but in the opposite direction to the plane of rotation.
TOTAL |
THRUST |
REACTION |
ANGLE OF
ATTACK
TORQUE
PLANE OF ROTATION
Figure 16.7 Thrust & torque
506
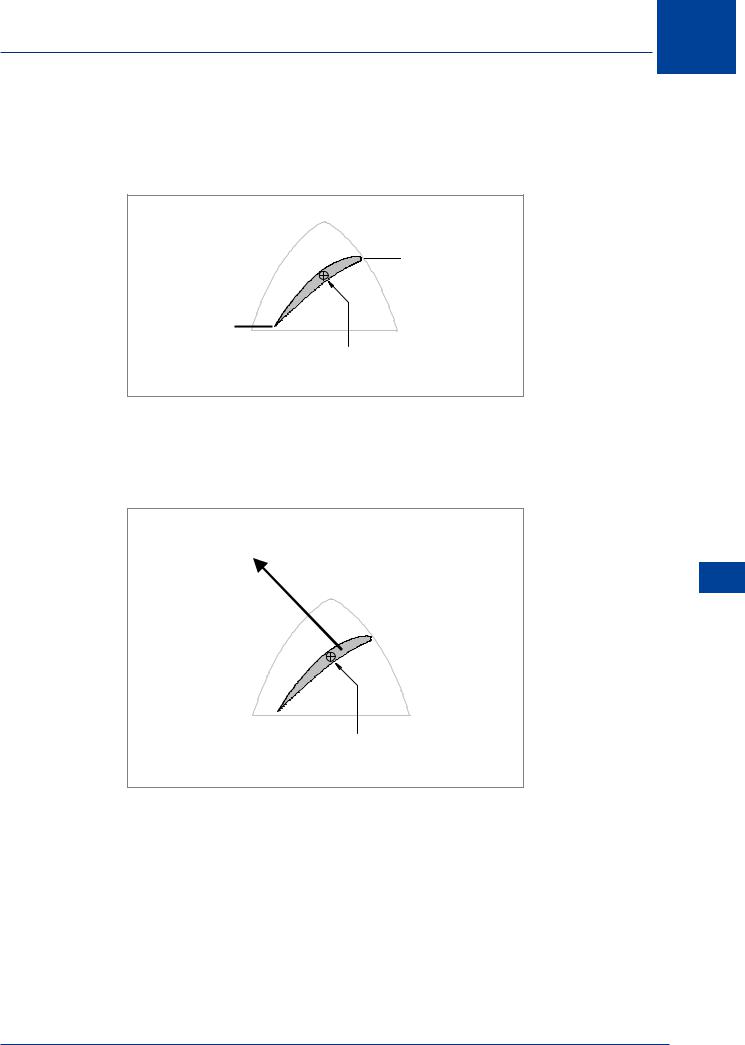
Propellers 16
Centrifugal Twisting Moment (CTM)
Components ‘A’ and ‘B’, of the centrifugal force acting on the blade, produce a moment around the pitch change axis which tends to ‘fine’ the blade off.
A
B
PITCH
CHANGE
AXIS
Figure 16.8 Centrifugal turning moment (CTM)
AerodynamicTwisting Moment (ATM)
Because the blade CP is in front of the pitch change axis, aerodynamic force generates a moment around the pitch change axis acting in the direction of coarse pitch.
TOTAL
REACTION
Propellers 16
PITCH
CHANGE
AXIS
Figure 16.9 Aerodynamic twisting moment (ATM)
The ATM partially offsets the CTM during normal engine operations, but the CTM is dominant. However, when the propeller is windmilling, the ATM acts in the same direction as the CTM (see Figure 16.15) and will reinforce it.
507
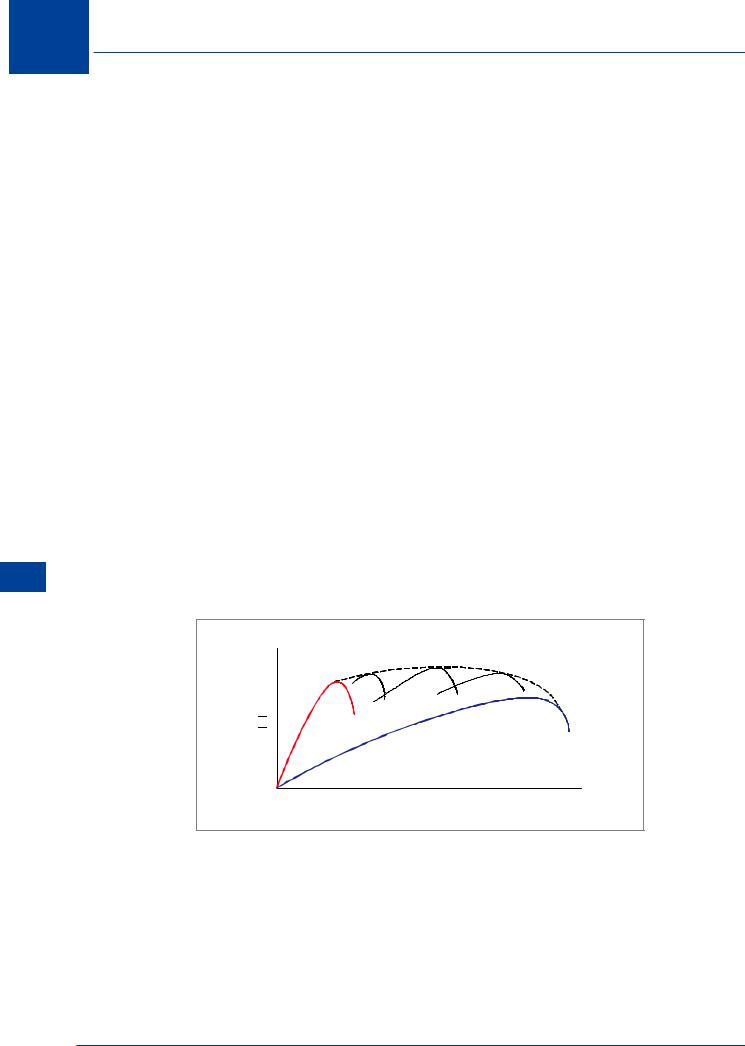
16 Propellers
Propeller Efficiency
Propellers 16
The efficiency of the propeller can be measured from the ratio, Power out / Power in. The power extracted (out) from a propeller, “Thrust Power”, is the product of Force (Thrust) × Velocity (TAS). The power into the propeller, “Shaft Power” is engine torque (Force) × Rotational Velocity (RPM). The efficiency of the propeller can be expressed as:
Thrust Power Propeller Efficiency = Shaft Power
Variation of Propeller Efficiency with Speed
Figure 16.5 illustrated that for a fixed pitch propeller, increasing TAS at a constant RPM reduces the blade angle of attack. This will decrease thrust. The effect of this on propeller efficiency is as follows:
•At some high forward speed the blade will be close to zero lift angle of attack and thrust, and therefore Thrust Power, will be zero. From the above ‘equation’ it can be seen that propeller efficiency will also be zero.
•There will be only one speed at which a fixed pitch propeller is operating at its most efficient angle of attack and where the propeller efficiency will be maximum, Figure 16.10.
•As TAS is decreased, thrust will increase because blade angle of attack is increased. Thrust is very large, but the TAS is low so propeller efficiency will be low. Thus no useful work is being done when the aircraft is, for instance, held against the brakes at full power prior to take-off. The efficiency of a fixed pitch propeller varies with forward speed.
If blade angle can be varied as TAS and/or RPM is changed, the propeller will remain efficient over a much wider range of aircraft operating conditions, as illustrated in Figure 16.10.
100 %
FINE |
COARSE |
PITCH |
|
|
PITCH |
AIRCRAFT FORWARD SPEED
Figure 16.10 Efficiency improved by varying blade angle
508

Propellers 16
Variable Pitch Propellers
Adjustable pitch propellers
These are propellers which can have their pitch adjusted on the ground by mechanically resetting the blades in the hub. In flight they act as fixed pitch propellers.
Two pitch propellers
These are propellers which have a fine and coarse pitch setting which can be selected in flight. Fine pitch can be selected for take-off, climb and landing and coarse pitch for cruise. They will usually also have a feathered position.
(Variable pitch) Constant speed propellers
Modern aircraft have propellers which are controlled automatically to vary their pitch (blade angle) so as to maintain a selected RPM. A variable pitch propeller permits high efficiency to be obtained over a wider range of TAS, giving improved take-off and climb performance and cruising fuel consumption.
Constant Speed Propeller
OPEN |
INCR |
|
MIXTURE |
THROTTLE |
RPM |
CLOSE |
DECR |
Figure 16.11
Figure 16.11 illustrates a ‘typical’ set of engine and propeller controls for a small piston engine aircraft with a variable pitch propeller. Throttle, prop’ and mixture are shown in the take-off (all forward) position.
“Pulling back” on the prop’ control will decrease RPM.
“Pushing forward” on the prop’ control will increase RPM.
NB: A reasonable analogy is to think of the prop’ control as an infinitely variable “gear change”.
Forward (increase RPM) is first gear.
Back (decrease RPM) is fifth gear.
Propellers 16
509
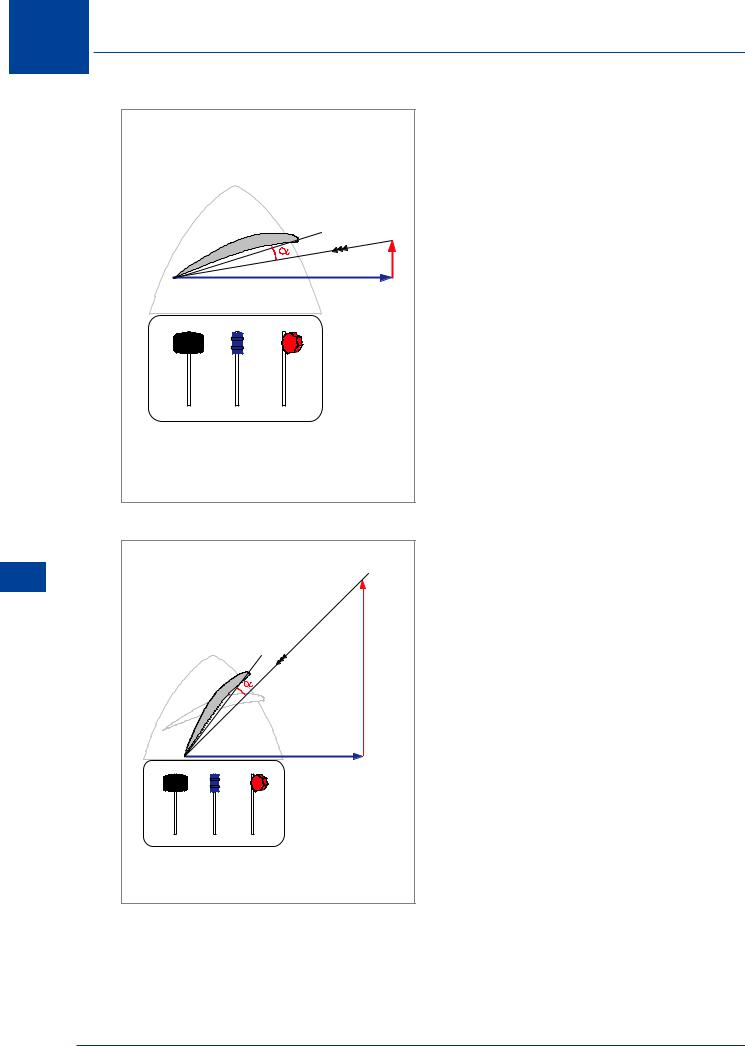
16 Propellers |
|
|
|
|
Figure 16.12 shows conditions during the |
||
FINE PITCH |
early stages of the take-off roll. |
The RPM |
|
( "small" blade angle ) |
is set to maximum and the TAS is low. The |
||
angle of attack is optimum and maximum |
|||
|
|||
|
available efficiency is obtained. As the aircraft |
||
|
continues to accelerate, the TAS will increase, |
||
|
which decreases the angle of attack of the |
||
|
blades. Less thrust will be generated and less |
||
|
propeller torque. This gives less resistance for |
||
|
the engine to overcome and RPM would tend |
||
|
to increase. The constant speed unit (CSU) |
||
|
senses the RPM increase and increases pitch to |
||
|
maintain the blade angle of attack constant. |
||
AT THE START OF THE |
|
|
|
TAKE - OFF ROLL. |
|
|
|
LOW FORWARD SPEED, |
|
|
|
HIGH RPM |
|
|
|
Figure 16.12 Low TAS, high RPM |
|
|
Propellers 16
TAS |
COARSE PITCH |
( "large" blade angle ) |
RPM |
HIGH FORWARD SPEED, |
HIGH RPM |
Figure 16.13 High TAS, high RPM
Figure 16.13 shows the conditions at high forward speed in level flight. As the TAS increased, the CSU continually increased the blade angle (coarsened the pitch) to maintain a constant blade angle of attack.
510
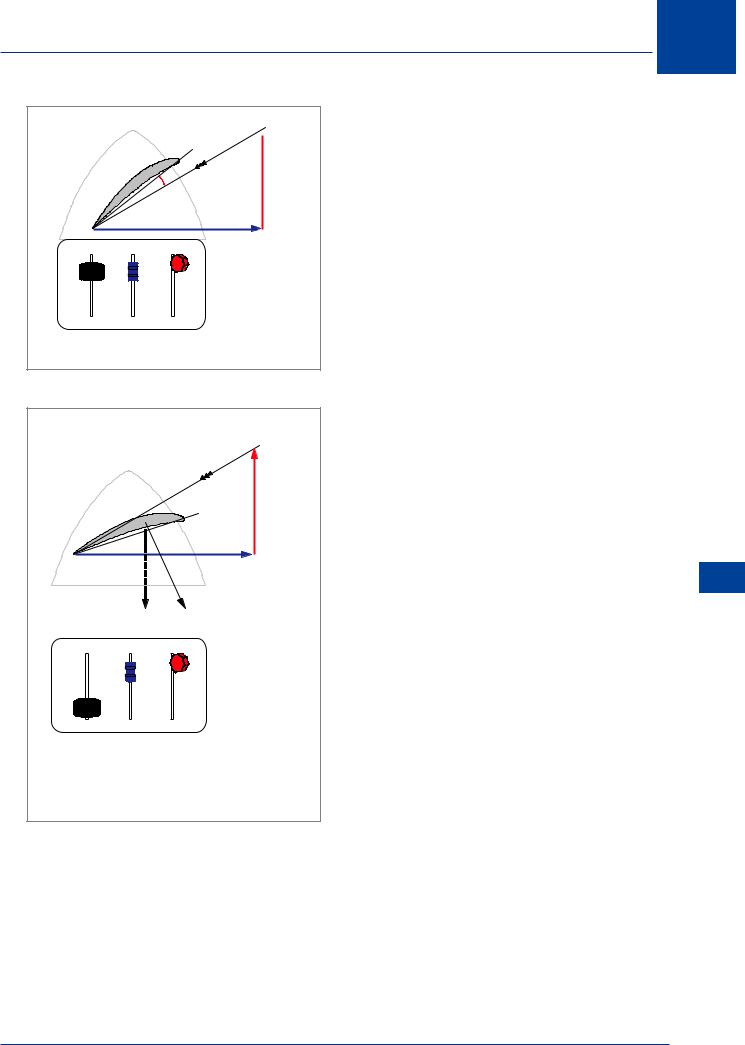
Propellers 16
TAS
RPM
CRUISE SETTING
Figure 16.14
FINE PITCH
( "small" blade angle ) |
TAS |
TORQUE
RPM
TOTAL
DRAG REACTION
STEADY GLIDE,
THROTTLE CLOSED,
NO SHAFT POWER,
PROPELLER WINDMILLING.
Figure 16.15 Windmilling
Figure 16.14 shows conditions when the engine and prop’ have been set for cruise conditions. Optimum throttle and RPM settings are listed in the aircraft Flight Manual. The recommended procedure is to reduce the throttle first, then RPM.
Whatever configuration into which the aircraft is placed, climb, descent or bank, the CSU will adjust the blade angle (prop’ pitch) to maintain the RPM which has been set. At least it will try to maintain constant RPM. There are exceptions, which will be discussed.
Windmilling
If a loss of engine torque occurs (the throttle is closed or the engine fails), the prop’ will “fine off” in an attempt to maintain the set RPM.
The relative airflow will impinge on the front surface of the blade and generate drag and “negative propeller torque”. The propeller will now drive the engine, as shown in Figure 16.15.
The drag generated by a windmilling propeller is very high.
Propellers 16
511
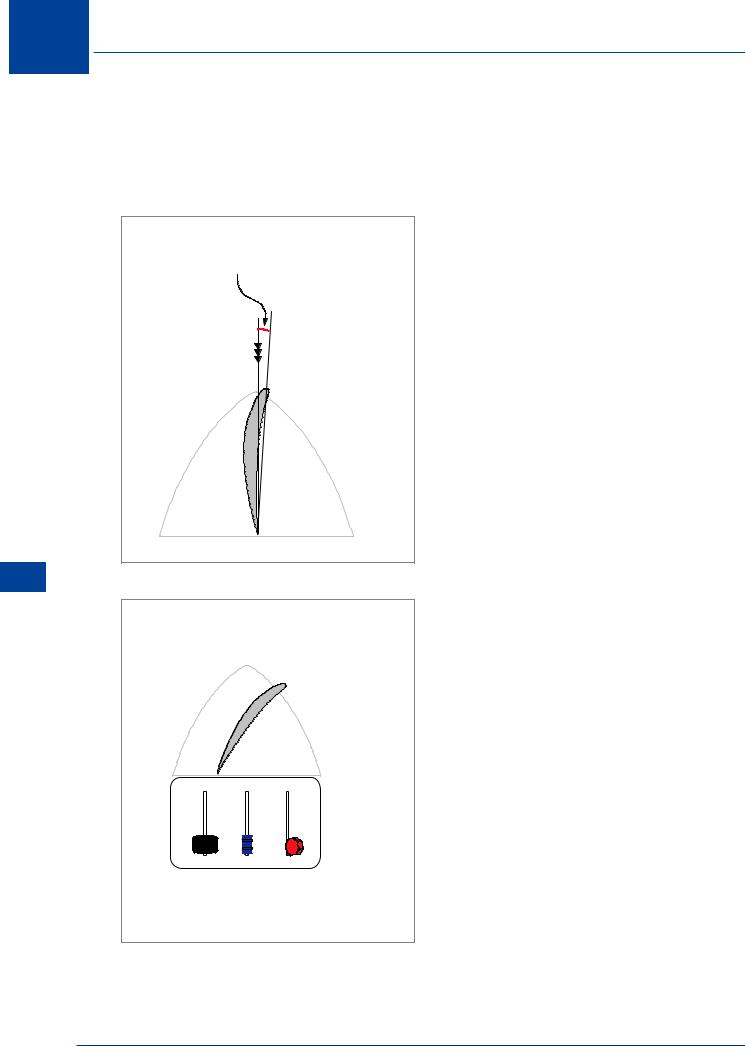
16
Propellers 16
Propellers
Feathering
Following an engine failure on a twin engine aeroplane the increased drag from the windmilling propeller will seriously degrade climb performance, limit range and add to the yawing moment caused by the failed engine which will affect controllability. Also, by continuing to turn a badly damaged engine, eventual seizure of the engine or an engine fire might result.
ZERO LIFT
ANGLE OF ATTACK
By turning the blades to their zero lift angle of attack, no propeller torque is generated and the propeller will stop, reducing drag to a minimum, as shown in Figure 16.16. This will improve climb performance because the ability to climb is dependent on excess thrust after balancing aerodynamic drag.
Windmilling drag is one of the “ingredients” of the yawing moment from a failed engine. Feathering the propeller of a failed engine will also reduce the yawing moment and consequently, VMC.
Figure 16.16 Feathered
COARSE PITCH
( "large" blade angle )
STEADY GLIDE, THROTTLE CLOSED
PROP' LEVER "PULLED BACK"
A single-engine aeroplane fitted with a constant speed propeller does not have a “feathering” capability, as such. However, following engine failure, drag can be reduced to a minimum by “pulling” the RPM (prop) control to the fully coarse position, as shown in Figure 16.17.
In a steady glide with no shaft power from the engine (throttle closed), if the propeller pitch is increased by pulling back the prop’ lever, the aircraft Lift/Drag ratio will increase. This will decrease the rate of descent. The RPM would decrease because of the reduction in negative propeller torque.
The opposite will be true if the propeller pitch is decreased.
Figure 16.17
512