
Тема 3-3-2
.pdfТема. Физико-технологические основы электрических соединений
Качественные характеристики соединений определяются многими факторами, но во всех случаях должны быть обеспечены:
Высокая надёжность и долговечность соединения.
Минимальное омическое сопротивление в зоне контакта и его стабильность при различных климатических воздействиях.
Максимально достижимая механическая прочность.
Минимальное значение основных параметров процесса контактирования (температуры, давления, длительности выдержки и т.д.).
Возможность соединения разнообразных сочетаний материалов и типоразмеров.
Стойкость к термоциклированию.
В зоне контакта не должно образовываться материалов вызывающих деградацию соединения.
Качество соединения должно контролироваться простыми и надёжными средствами.
Экономическая эффективность и производительность процесса.
Основные методы выполнения электрических соединений обеспечиваются на основе:
пайки,
сварки,
соединения, основанные на пластической деформации контактируемых деталей,
соединения токопроводящими клеями.
Пайка – это процесс соединения металлов в твёрдом состоянии путём введения в зазор расплавленного припоя, взаимодействующего с основным металлом и образующего жидкую металлическую прослойку, кристаллизация которой приводит к образованию паяного шва. Паяные соединения очень широко применяют при монтаже электронной аппаратуры из-за низкого и стабильного электрического сопротивления, универсальности, простоты автоматизации, контроля и ремонта. Однако методу пайки присущи и существенные недостатки: высокая стоимость используемых цветных металлов и флюсов, длительное воздействие высоких температур, коррозионная активность остатков флюсов, выделение вредных веществ.
Сварка – это процесс получения неразъёмного соединения материалов под действием активирующей энергии теплового поля, деформации, ультразвуковых колебаний или их сочетаний. По сравнению с пайкой она характеризуется следующими преимуществами: более высокой механической прочностью получаемых соединений, отсутствием присадочного материала, незначительной дозированной тепловой нагрузкой, возможностью уменьшения расстояния между контактами. К недостаткам метода следует отнести: критичность при выборе сочетаний материалов, увеличение переходного сопротивления из-за образования интерметаллидов, невозможность группового контактирования соединений, сложность ремонта.
Соединения, основанные на пластической деформации контактируемых деталей,
проводов или выводов, выполняются в холодном состоянии. Под действием значительных механических усилий, приложенным к этим элементам, происходит разрушение оксидных плёнок и образование надёжного вакуум-плотного соединения. Оно характеризуется высокой механической прочностью, низкой стоимостью, легко поддаётся механизации, не создаёт помех в цепях низкого напряжения.
Соединение токопроводящими клеями и пастами в отличие от пайки и сварки не вызывает изменения структуры соединяемых материалов, так как проводится при низких температурах, упрощает конструкцию соединений и применяется в тех случаях, когда другие способы невозможны: в труднодоступных местах, при ремонтных работах и т.д. Однако
широкого распространения в серийном производстве метод не получил из-за невысокой проводимости, низкой термостойкости и надёжности соединений.
1Сварка
Процесс образования сварного соединения можно условно разделить на четыре стадии:
образование физического контакта между поверхностями материалов;
активизация контактных поверхностей;
объёмное развитие взаимодействия;
кристаллизация.
На первой стадии сближаются материалы на расстояние порядка 10…100 нм, при котором между частицами начинает проявляться физическое взаимодействие, обусловленное силами Ван-дер-Ваальса.
На второй стадии происходит образование на поверхности более твёрдого из соединяемых материалов центров, активных в химическом отношении. Активный центр упрощённо – это частицы со свободными валентностями, которые могут возникнуть при разрыве связей в кристалле, в местах образования дефектов. Для активизации поверхностей вводится дополнительная энергия: тепловая, деформации, ультразвуковая. При сварке плавлением цепная реакция растекания с выделением энергии поверхностного натяжения увеличивает площадь контакта вокруг каждой точки взаимодействия.
С момента образования на контактных поверхностях активных центров наступает третья стадия, при которой развивается взаимодействие соединяемых металлов как в плоскости так и в объёме зоны контакта. В плоскости контакта оно заканчивается слиянием очагов взаимодействия, что является необходимым условием возникновения прочных химических связей между материалами Процесс образования сварного соединения можно условно разделить на четыре стадии:
1.Образование физического контакта между поверхностями материалов.
2.Активизация контактных поверхностей. На этой стадии происходит образование на поверхности более твёрдого из соединяемых материалов центров, активных в химическом отношении. Для активизации поверхностей вводится дополнительная энергия: тепловая, деформации, ультразвуковая. При сварке плавлением цепная реакция растекания с выделением энергии поверхностного натяжения увеличивает площадь контакта вокруг каждой точки взаимодействия.
3.Объёмное развитие взаимодействия. С момента образования на контактных поверхностях активных центров наступает третья стадия, при которой развивается взаимодействие соединяемых металлов как в плоскости так и в объёме зоны контакта.
4.Кристаллизация. Характерной особенностью кристаллизации сварного соединения является образование зональной структуры, состоящей из ядра, переходной зоны и неизменяемой зоны основы.
Выделяют следующие виды сварки: термический, термомеханический, механический
виды.
1.Термическая сварка. К ней относятся виды сварки, осуществляемые плавлением под действием различных видов энергии:
– Электроннолучевая сварка основана на использовании теплоты, выделяемой при соударении электронов и атомов свариваемого металла, диаметр пятна нагрева 1мкм. Для охвата больших поверхностей используется сканирование лучом либо позиционирование деталей. Применяется для герметизации радиоэлектронных устройств в металлостеклянных корпусах. Преимущества: высокая производительность и время сварки 5мс, место сварки не нагревается. Недостатки – высокая стоимость оборудования
– Лазерная основана на использовании монохромного когерентного светового луча с
высокой плотностью энергии, превращение которой в теплоту вызывает оплавление

свариваемых материалов. Диаметр пятна 0,01мм. Применяется при монтаже различных элементов радиоэлектронной техники и при герметизации корпусов. Недостаток: сложность юстировки оптической системы.
–Микроплазменная сварка является разновидностью сварки плавлением. Отличительная особенность процесса – создание ионизированного потока инертного газа (смесь аргона с гелием (до 70%), с водородом (до 10—15%) или азотом). Расплавление металла происходит сжатой дугой прямого действия и потоком плотной ионизированной плазмы. Этот способ сварки применяется для герметизации корпусов приборов из ковара или никеля толщиной 0,1–0,3 мм
2. Термомеханическая сварка использует тепловую энергию и давление:
–Термокомпрессионная сварка – это сварка, которая проводится при невысоких давлениях с подогревом соединяемых деталей (рис.2). Один из соединяемых материалов (обычно вывод) при должен обладать достаточно высокой пластичностью. Является наиболее распространенным способом монтажа полупроводниковых микроприборов и интегральных микросхем в разнообразных корпусах гибкими проволочными проводниками.
При приложении температуры и давления в момент осадки в результате течения пластичного металла вдоль поверхности другого металла происходит очистка места соединения от оксидных плёнок, сближение поверхностей и образование между ними плотного контакта. После сварки за счёт развития процесса диффузии между свариваемыми материалами полученное соединение упрочняется.
Основными параметрами режима термокомпрессии являются: усилие сжатия Р, температура нагрева инструмента или соединения Т, длительность выдержки под давлением t. Температура нагрева не должна превышать температуру образования эвтектики соединяемых материалов и колеблется для различных материалов от 250 до 450оС. Длительность выдержки устанавливается в зависимости от сочетания свариваемых материалов и определяется экспериментально путём оценки прочности соединения.
Рисунок 2 – Схема термокомпрессионной сварки
Достоинства: стабильность сварочного инструмента и его высокая стойкость, малая чувствительность к изменению режима, простота контроля основных параметров процесса.
Недостатки: ограниченное число сочетаний свариваемых материалов (только пластичные), необходимость весьма тщательной подготовки соединяемых деталей.
–Диффузионная сварка применяется для сварки разнородных материалов, основана на диффузии материалов под действием давления и температуры. Производится в вакууме или водороде. Применяться в производстве микросхем для сварки термокомпенсаторов кристаллов
ина других операциях
–Сварка давлением с косвенным нагревом (СКИН) в отличие от термокомпрессии проводится инструментом, который импульсно нагревается проходящим по нему током (рис. 3).
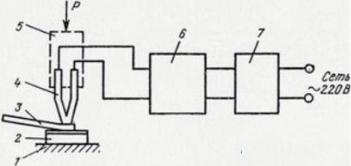
В следствии кратковременности процесса нагрева металлический проводник в месте контакта нагревается до более высоких температур, чем при термокомпрессии.
Применяется в интегральных микросхемах, которые не допускают общего разогрева, можно сваривать золотые, алюминиевые и медные проводники диаметром 20–100 мкм с разнообразными пленками, напыленными на диэлектрические или полупроводниковые подложки, этот метод позволяет приваривать проводники из относительно малопластичных металлов к тонким плёнкам на керамических подложках.
Рисунок 3 – Схема сварки давлением с косвенным нагревом, где 1 – рабочий столик; 2 – подложка или полупроводниковый кристалл; 3 – проводник; 4 – V-образный инструмент (пуансон); 5 — сварочная головка для создания давления; 6 – источник питания; 7 – реле времени
3. Механическая сварка использует механическую энергию и давление:
–Холодная сварка осуществляется за счет пластической деформации свариваемых деталей под действием давления без дополнительного подогрева. Для получения высококачественного сварного соединения при холодной сварке необходимо обеспечить точную сборку и чистоту свариваемых поверхностей и необходимую степень деформации, зависящую от соединяемых металлов. В микроэлектронике этот способ применяется для герметизации металлостеклянных корпусов приборов.
–Ультразвуковая сварка выполняется за счёт возбуждения в свариваемых деталях упругих колебаний УЗ-частоты при одновременном создании определённого давления. Для УЗмикросварки используют оборудование с частотами 22, 44, 66, 88 кГц. При УЗ-сварке температура нагрева непосредственно в зоне контакта не превышает 30…50% от температуры плавления соединяемых материалов, что позволяет использовать этот метод для соединения чувствительных к нагреву материалов.
Свариваемые материалы предварительно сжимаются с силой. В зону контакта с помощью волновода вводится ультразвуковые колебания с частотой от 15 до 170 кГц, которые разрушают оксидную пленку. Происходит атомарный обмен в поверхностном слое под действием колебательного движения.
Основным элементом установок УЗ-сварки является инструмент, форма и размер рабочей части которого имеют важное значение для получения качественных соединений.
–Односторонняя контактная сварка распространенный способ соединения различных электронных компонентов (рис.4).
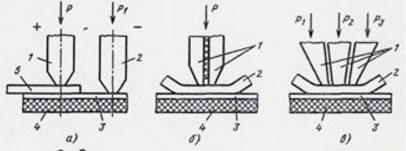
Рисунок 4 – Схемы односторонней контактной сварки:
a ) односторонняя точечная сварка, где 1 – электрод для сжатия спариваемых деталей и подвода тока к проволоке; 2 – электрод для подвода тока к шине печатной платы; 3 – контактная площадка или шина печатной платы; 4 – диэлектрическое основание печатной платы; 5 – привариваемая проволока или лента; б) и в) односторонняя сварка соответственно сдвоенным электродом (с параллельными зазорами) и строенным электродом трех-фазным током (1 – электроды; 2 – приеариваемый проводник; 3 – тонкая металлическая пленка; 4 – диэлектрическая подложка)
При односторонней точечной контактной сварке (рис. 4 а) один электрод прижимает проволоку или ленту к контактной площадке, а второй электрод служит для подвода сварочного тока к контактной площадке. Этот способ применяют для сварки весьма тонких проводников (круглых и плоских) с относительно толстым материалом и для сварки проводников с электроосажденными пленками толщиной около 20 мкм.
Для присоединения круглых и плоских выводов навесных элементов к тонким пленкам на хрупких подложках и к печатному монтажу применяют контактную сварку сдвоенным электродом (рис. 4, б) и сварку строенным электродом трехфазным током (рис. 4, в) применяется в технологии электрического монтажа. Сварку осуществляют инструментом-электродом, изготовленным из вольфрама или молибдена в виде двух токопроводящих частей, разделённых зазором 0,02…0,25 мм в зависимости от толщины или диаметра привариваемых выводов. Зазор между электродами оказывает значительное влияние на глубину проникновения тока и на термическую нагрузку печатного проводника в месте соединения с диэлектриком.
2 Электрическое соединение методом накрутки
Накрутка – это процесс создания электрического соединения путём навивки под натягом определённого числа витков одножильного провода на штыревой вывод с острыми кромками. Под действием приложенного усилия происходит разрушение оксидных плёнок на соединяемых поверхностях и врезание острых граней вывода в провод. Образовавшееся газонепроницаемое соединение удерживается благодаря упругим напряжениям, возникшим в этих элементах. Концентрация напряжений в зоне контакта и среднее давление порядка 15…20 Мпа обуславливают взаимную диффузию металлов, что способствует повышению надёжности соединения.
При монтаже накруткой применяют три вида соединений (рис.5):
немодифицированное (накрутка неизолированным проводом);
модифицированное (кроме витков оголённого провода на выводе имеется 1…2 витка провода в изоляции, которая демпфирует воздействие знакопеременных нагрузок на элементы контакта и уменьшает усталостные напряжения);
бандажное. В бандажном соединении соединяемый элемент (провод, вывод, шина и пр.) располагается вдоль широкой поверхности гранёного вывода и на них накручивается несколько витков бандажной проволоки (не менее восьми).
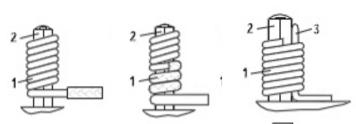
Накрутка может производится с помощью пистолета для накрутки (50-80 соединений в
час).
а) б) в)
Рисунок 5 – Монтаж методом накрутки: а) немодифицированное; б) модифицированное; в) бандажное; 1 – проводник; 2 – вывод; 3– бандажируемый элемент
3 Соединение проводящими клеями
Электропроводящие клеи (контактолы) применяют при создании монтажных соединений в тех случаях, когда другие методы оказываются неэффективными: в труднодоступных местах, при ремонте ПП, при низкой термостойкости компонентов.
Клеепроводящие композиции изготовляют на основе эпоксидных смол холодного и горячего отверждения. В качестве наполнителя используют мелкодисперсный порошок золота, серебра, палладия, никеля, меди, алюминия.
Свойства электропроводящих клеев зависит не только от типа наполнителя, но и от его концентрации. Необходимым условием получения максимальной электропроводности контактолов является формирование в объёме композиции из частичек наполнителя цепочных структур. Увеличение количества наполнителя увеличивает проводимость, но одновременно ухудшаются механические свойства соединения. В связи с этим разработан способ искусственной ориентации металлических частиц никеля под действием магнитного поля, что позволяет увеличить электропроводность в 5 – 10 раз при значительно меньшей концентрацией наполнителя.
4 Пайка
Общие сведения. Пайка представляет собой распространенный способ монтажа компонентов в производстве радиоэлектронных узлов.
1.Получить чистые металлические поверхности у соединяемых деталей (удалить загрязнения и пленки окислов) с помощью технологического флюса;
2.Нагреть припой выше точки плавления;
3.Обеспечить вытеснение флюса с помощью наступающего припоя;
4.Обеспечить растекание жидкого припоя по металлической поверхности;
5.Обеспечить диффузию атомов из твердой металлической фазы в жидкий припой и наоборот – образование сплавных зон.
Среди припоев в радиоэлектронике наиболее широкое распространение получили припои на основе композиции олова и свинца (ПОС). Сплав имеет особую точку, называемую точкой эвтектики. В этой точке температура кристаллизации припоя составляет 183 °С, что значительно ниже точек плавления Sn и Pb (232 °С и 327 °С).
Флюс является материалом, под воздействием которого происходит быстрое и совершенное смачивание металлической поверхности соединяемых деталей расплавленным припоем благодаря влиянию сил поверхностного натяжения. Кроме того, флюс обладает свойством растворения и удаления окисных слоев на контактируемых металлах и защиты очищенной поверхности от нового окисления. Остатки флюса должны легко удаляться, быть не изменять электрические параметры исходного материала и не вызывать коррозии. Распространены флюсы на основе органических кислот из смол хвойных пород деревьев (канифоль). Известно и большое количество синтетических материалов.
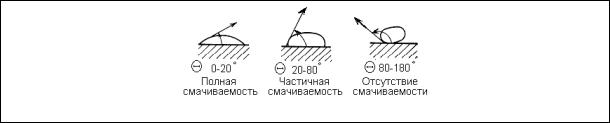
Рисунок 6 – Качество смачивания
Смачивание, как решающий фактор процесса пайки, может улучшаться посредством поверхностно-активных веществ флюсов. Качество смачивания можно определить по краевому углу смачивания (рис. 6). Уменьшение поверхностного натяжения припоя в расплавленном состоянии приводит к уменьшению угла смачивания. Именно в процессе смачивания создаются условия (наряду с высокой температурой) для создания диффузионных сплавных зон на границах раздела припоя и соединяемых металлов, которые определяют прочностные характеристики паяного соединения. Зачастую прочность диффузионных сплавных зон превышает прочность соединяемых металлов.
Впоследнее время набирает силу движение за исключение свинца как токсичного металла из электронных сборок. В поисках сплавов на замену традиционной композиции SnPb исследовано большое количество материалов, однако абсолютно равноценной замены пока не найдено. ПОС обладает практически оптимальными свойствами для РЭА: хорошей смачиваемостью, прочностью, пластичностью, удобной точкой плавления, коррозионной стойкостью, усталостной прочностью, и, наконец, стоимостью.
Появление на ПП поверхностно монтируемых компонентов существенно изменило технологию пайки. Пайка волной припоя была внедрена в середине прошлого века и до настоящего времени является единственным групповым методом пайки компонентов, устанавливаемых в отверстия ПП. Она выполняется чаще всего погружением обратной стороны платы с выступающими выводами в ванну с припоем. Для пайки плат со смешанным монтажом (компоненты, монтируемые в отверстия с одной стороны платы и простые, монтируемые на поверхность с другой) был разработан метод пайки двойной волной припоя.
Для пайки поверхностно монтируемых компонентов была разработана технология оплавления дозированного припоя. Методами трафаретной печати припой в виде пасты наносится на контактные площадки ПП, затем на него устанавливаются компоненты. В ряде случаев припойную пасту просушивают после нанесения с целью удаления из ее состава летучих ингредиентов или предотвращения смещения компонентов непосредственно перед пайкой. Оплавление припоя и получение паяных соединений происходит в нагревательном устройстве.
В1973 г. появилась пайка в парогазовой фазе (ПГФ), когда фирма DuPont разработала и запатентовала специальные жидкие материалы, имеющие температуру кипения 215 °С. С 1983 г. основным конкурентом пайки в ПГФ стала пайка расплавлением дозированного припоя с помощью инфракрасного нагрева (ИК-пайка). Примерно с этого же времени развивается пайка
вконвекционных печах. В Японии пайка компонентов, устанавливаемых на поверхность недорогих плат с низкой плотностью монтажа, производится с применением нагретого инструмента. Для чувствительных к тепловому воздействию и сложных микросборок с поверхностным монтажом ведущими японскими компаниями была разработана лазерная пайка. Ведущие поставщики сборочно-монтажного оборудования обычно включают установки для пайки в состав выпускаемых производственных линий.
Групповые методы пайки
Современные методы групповой пайки в производстве РЭА классифицируются по источникам тепловой энергии, являющимся главным фактором при формировании паяных соединений (рис.7).

Рисунок 7 – Групповые методы пайки
Ниже описаны наиболее применяемые методы пайки.
Пайка волной припоя применяется только для пайки компонентов в отверстиях плат (традиционная технология), хотя некоторые изготовители утверждают, что с ее помощью можно производить пайку поверхностно монтируемых компонентов с несложной конструкцией корпусов, устанавливаемых на одной из сторон ПП.
Платы, установленные на транспортере, подвергаются предварительному нагреву, исключающему тепловой удар на этапе пайки. Затем плата проходит над волной припоя (рис.8а). Сама волна, ее форма и динамические характеристики являются наиболее важными параметрами оборудования для пайки. С помощью сопла можно менять форму волны.
Некоторые установки для пайки оборудуются дешунтирующим воздушным ножом, который обеспечивает уменьшение количества перемычек припоя. Нож располагается сразу же за участком прохождения волны припоя и включается в работу, когда припой находится еще в расплавленном состоянии на ПП. Узкий поток нагретого воздуха, движущийся с высокой скоростью, уносит с собой излишки припоя, тем самым, разрушая перемычки и способствуя удалению излишков припоя.
Когда появились ПП, с обратной стороны которых устанавливались поверхностные компоненты, их пайка производилась волной припоя. При этом возникло множество проблем, а именно: непропаи и отсутствие галтелей припоя из-за эффекта затенения другими компонентами, преграждающими доступ волны припоя к соответствующим контактным площадкам, а также наличие полостей с захваченными газообразными продуктами разложения флюса, мешающих доступу припоя. Потребовалось изменить технологический процесс пайки волной, внедрив вторую волну припоя (рис. 8 б). Первая волна делается турбулентной и узкой, исходит из сопла под большим давлением. Турбулентность и высокое давление потока припоя исключает формирование полостей с газообразными продуктами разложения флюса. Однако турбулентная волна все же образует перемычки припоя, которые разрушаются второй, более пологой волной с малой скоростью истечения. Вторая волна устраняет перемычки припоя, а также завершает формирование галтелей. Для обеспечения эффективности пайки параметры каждой волны должны быть регулируемыми, волны должны иметь отдельные насосы, сопла и блоки управления.
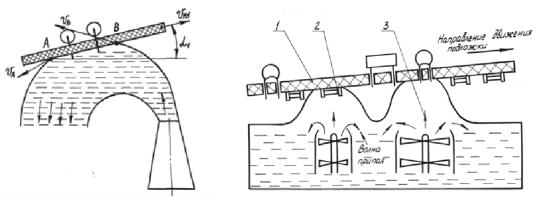
а) |
б) |
Рисунок 8 – Пайка волной припоя: а) одной волной, б) двумя волнами |
|
Пайка двойной волной припоя применяется в настоящее время для одного типа ПП: с традиционными компонентами на лицевой стороне и простыми компонентами (чипами и транзисторами) на обратной. Некоторые компоненты (даже пассивные) могут быть повреждены при погружении в припой во время пайки. Поэтому важно учитывать их термостойкость и принимать меры предосторожности: применять поверхностно монтируемые ИС, не чувствительные к тепловому воздействию; снизить скорость транспортера; проектировать ПП таким образом, чтобы исключить эффект затенения. При высокой плотности монтажа с помощью данного метода практически невозможно пропаять поверхностно монтируемые компоненты с четырехсторонней разводкой выводов.
Пайка в парогазовой среде (ПГФ) с расплавлением дозированного припоя применима только к сборкам с поверхностным монтажом (рис.9).
Процесс начинается с нанесения способом трафаретной печати припойной пасты на контактные площадки коммутационной платы. Затем на поверхность платы устанавливаются компоненты. В ряде случаев припойную пасту просушивают после нанесения, с целью удаления из ее состава летучих ингредиентов или предотвращения смещения компонентов непосредственно перед пайкой.
После этого плата разогревается до температуры расплавления.
В результате образуется паяное соединение между контактной площадкой платы и выводом компонента.
Такая техника пайки применима к коммутационным платам без монтируемых в отверстия компонентов, т. е. с набором только поверхностно монтируемых компонентов любых типов.
Метод пайки в парогазовой фазе является разновидностью пайки расплавлением дозированного припоя, в ходе которой пары специальной жидкости конденсируются на коммутационной плате, отдавая скрытую теплоту парообразования открытым участкам микросборки. При этом припойная паста расплавляется и образует галтель между выводом компонента и контактной площадкой платы.
Когда температура платы достигает температуры жидкости, процесс конденсации прекращается, тем самым заканчивается и нагрев пасты.
Повышение температуры платы от ее начальной температуры до температуры расплавления припоя осуществляется очень быстро и не поддается регулированию. Поэтому необходим предварительный подогрев платы с компонентами для уменьшения термических напряжений в компонентах и местах их контактов с платой. Температура расплавления припоя также не регулируется и равна температуре кипения используемой при пайке жидкости. Такой жидкостью является инертный фторуглерод (например, FC-70).
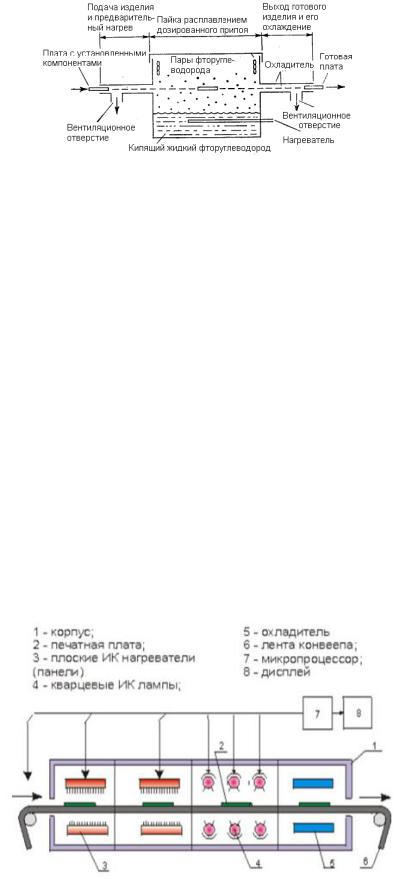
Рисунок 9 – Пайка в ПГФ Пайка инфракрасным нагревом (ИК-пайка) аналогична пайке в ПГФ, за исключением
того, что нагрев платы с компонентами производится не парами жидкости, а ИК-излучением (рис.9.10). Основным механизмом передачи тепла, используемым в установках пайки с ИКнагревом, является излучение. В отличие от пайки в ПГФ, в процессе пайки с ИК-излучением скорость нагрева регулируется изменением мощности каждого излучателя и скорости движения транспортера с ПП. Поэтому термические напряжения в компонентах и платах могут быть снижены посредством постепенного нагрева сборок.
Инфракрасные печи применяются при изготовлении несложных плат. Обусловлено это тем, что инфракрасный тип нагрева имеет ряд отрицательных эффектов. Наиболее существенно влияют на работу следующие:
–количество энергии излучения, поглощаемой компонентами и платами, зависит от поглощающей способности материалов, из которых они изготовлены. Поэтому нагрев осуществляется неравномерно в пределах монтируемого устройства;
–высокие элементы могут закрывать более низкие, создавая «тень», где высока вероятность непропая;
–некоторые элементы корпусом могут закрывать свои собственные выводы.
В некоторых установках для пайки с ИК-нагревом вместо ламп ИК-излучения применяются панельные излучающие системы. Излучение такой системы не нагревает непосредственно компоненты на сборке, а поглощается технологической средой (воздух или газ), которая в свою очередь передает тепло на ПП за счет конвекции. Этот способ пайки устраняет ряд недостатков, присущих пайке с ИК-нагревом, таких, как неравномерный прогрев отдельных частей сборки и невозможность пайки компонентов в корпусах, непрозрачных для ИК-излучения. Панельные излучатели обеспечивают намного меньшую скорость нагрева, чем традиционные источники ИК-излучения.
Рисунок 10 – Схема инфракрасной пайки