
1381-metallurgicheskie-pod-emno-transportnye-mashiny-konveyery-2mb
.pdf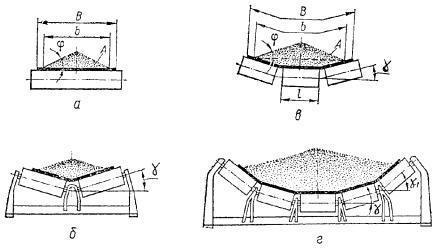
Рис. 4.4. Типы роликовых опор:
а– однороликовая; б – двухроликовая; в – трехроликовая;
г– пятироликовая
Однороликовые опоры обычно применяются для перемещения насыпных или штучных грузов при небольшой производительно- сти конвейера, двухроликовые – в передвижных конвейерах лег- кого типа, пятироликовые – для высокопроизводительных кон- вейеров с широкой лентой. Повышение производительности кон- вейера при использовании желобчатой формы ленты достигается в результате увеличения площади сечения транспортируемого насыпного груза.
Конструкция ролика приведена на рис. 4.5. Корпус 1 ролика изготовляется преимущественно из стальных труб диаметром 63…245 мм, реже – литым. Диаметр ролика выбирается в соот- ветствии с данными табл. 4.3 в зависимости от ширины ленты и плотности транспортируемого груза, а его длина принимается на 100…200 мм больше ширины ленты. Корпус ролика с вкладыша- ми 2 устанавливается на неподвижной оси 3 с помощью подшип- ников качения 5, которые защищены от попадания в них загряз- нений с наружной стороны лабиринтным уплотнением 4. Ось 3 ролика закрепляется на неподвижных кронштейнах, соединенных с металлоконструкцией конвейера.
20

Рис. 4.5. Конструкция конвейерного ролика: а – легкого типа; б – тяжелого типа
|
|
|
|
|
Таблица 4.3 |
|
Рекомендации по выбору диаметра ролика |
||||
|
|
|
|
|
|
Диаметр |
|
Ширина |
Плотность |
Рекомендуемая |
|
ролика, мм |
|
ленты, мм |
груза, т/м3 |
скорость ленты, м/с |
|
89 |
|
400, 500, |
650 |
1,6 |
2,0 |
|
|
|
|
|
|
|
|
800 |
|
1,6 |
1,6 |
|
|
|
|
|
|
108 |
|
400, 500, |
650 |
2,0 |
2,5 |
|
|
|
|
|
|
|
|
800, 1000, |
1200 |
1,6 |
2,5 |
|
|
|
|
|
|
133 |
|
800, 1000, |
1200 |
2,0 |
2,5 |
|
|
|
|
|
|
159 |
|
800, 1000, |
1200 |
3,5 |
4,0 |
|
|
|
|
|
|
|
|
1400,1600, 2000 |
3,5 |
3,2 |
|
|
|
|
|
|
|
194, 219, 245 |
|
800, 1000, |
1400 |
3,5 |
4,0 |
|
|
|
|
|
|
|
|
1600, 2000 |
4,0 |
6,3 |
|
|
|
|
|
|
|
В зависимости от несущей нагрузки различают ролики легкого и тя- желого типа. Ролики легкого типа устанавливают на шариковых под- шипниках, тяжелого типа – на конических. Основные параметры роли- ков для ленточных конвейеров регламентированы ГОСТ 22646–77.
Шаг роликов рабочей ветви lрр выбирается по табл. 4.4 в зависи- мости от ширины ленты и плотности груза. В местах загрузки рас- стояние lрр уменьшают до 0,5 м.
21
|
|
|
|
|
Таблица 4.4 |
Расстояние lрр между роликоопорами рабочей ветви конвейера |
|||||
|
|
|
|
|
|
Ширина ленты, |
Расстояние lрр, м в зависимости от плотности |
||||
мм |
|
транспортируемого груза, т/м3 |
|
||
|
Менее 0,8 |
0,8…1,6 |
1,6…2,0 |
2,0…2,5 |
Более 2,5 |
|
|
|
|
|
|
400 |
1,5 |
1,4 |
1,4 |
1,3 |
1,2 |
500 |
1,5 |
1,4 |
1,4 |
1,3 |
1,2 |
650 |
1,4 |
1,3 |
1,3 |
1,2 |
1,2 |
800 |
1,4 |
1,3 |
1,3 |
1,2 |
1,1 |
1000 |
1,3 |
1,2 |
1,2 |
1,1 |
1,1 |
1200 |
1,3 |
1,2 |
1,2 |
1,1 |
1,1 |
1400 |
1,3 |
1,2 |
1,2 |
1,1 |
1,1 |
1600 |
1,3 |
1,2 |
1,2 |
1,1 |
1,1 |
2000 |
1,3 |
1,2 |
1,1 |
1,0 |
1,0 |
Шаг роликов холостой ветви lрх принимается в два раза бóльшим,
т.е. lрх = 2 lрр.
Условная линейная (погонная) плотность роликов (кг/м) для рабо-
чей и холостой ветвей ленты равна соответственно
ρрр = mрр / lрр, ρрх = mрх / lрх, |
(4.4) |
где mрр и mрх – массы роликов (кг) рабочей и холостой ветвей соот- ветственно, определяемые по каталогам заводов- изготовителей.
При отсутствии табличных данных массу роликов можно оценить по следующим эмпирическим формулам:
mрр ≈ 220 В; mрх ≈ 130 (В – 0,2), |
(4.5) |
где В – ширина ленты, м.
Усредненные значения погонного веса роликов qpp = ρрр g и qpх = = ρрх g для конвейеров общего назначения приведены в табл. 4.2.
Провисание ленты между опорами увеличивает угол наклона лен- ты при ее набегании на поддерживающий ролик, что приводит к ссыпанию груза, а также к возрастанию ударных нагрузок на ролик при транспортировке штучных или крупнокусковых грузов. Поэтому провисание ленты необходимо ограничивать.
Максимальная стрела провисания ленты (м) имеет место на уча- стке с минимальным натяжением Fmin (Н) посередине между опорами и определяется по формуле
22
ymax = (qг + qл) lрр2 / (8 Fmin),
где qг и qл – линейные силы тяжести груза и ленты соответствен- но, Н/м.
Отсюда необходимое минимальное натяжение ленты
Fmin = (qг + qл) lрр2 / (8 ymax).
Натяжение Fmin должно быть таким, чтобы провисание ленты не превышало следующей величины:
[ymax] = (0,018…0,030) lрр.
Для конвейеров металлургических предприятий, работающих в тяжелых условиях, принимается меньшее значение [ymax] = 0,018 lрр.
Следовательно, для конвейеров металлургических предприятий минимальное натяжение ленты должно удовлетворять следующему условию:
Fmin ≥ 7 (qг + qл) lрр. |
(4.6) |
Линейная (погонная) сила тяжести насыпного груза qг (Н/м) свя-
зана с его линейной (погонной) массой ρL (кг/м) зависимостью
qг = ρL g ≈ 10 ρL. |
(4.7) |
Аналогично находится нагрузка от собственного веса ленты и других элементов конвейера.
Для предотвращения смещения ленты от продольной оси конвей- ера применяют центрирующие роликоопоры, устанавливаемые через каждые 8–9 неподвижных роликоопор.
Центрирующая желобчатая роликоопора (рис. 4.6, а) имеет обычную трехроликовую опору 1, установленную на раме 3, ко- торая в определенных пределах может поворачиваться на верти- кальной оси 4. К поворотной раме 3 с обеих сторон прикреплены рычаги 5, на концах которых установлены ролики 2. При смеще- нии влево (рис. 4.6, б) лента своей кромкой нажимает на ролик 2 и поворачивает раму с роликоопорой на некоторый угол по от- ношению к продольной оси конвейера. При перекосе роликоопо- ры на поверхности ленты возникает восстанавливающее усилие, стремящееся возвратить ленту в исходное положение. После того как лента возвратится в исходное «центральное» положение, ро- ликоопора под действием самой ленты автоматически устанавли- вается в нормальное положение.
23

Рис. 4.6. Центрирующие роликоопоры для верхней ветви ленты: а – конструкция; б – схема поворота при сдвиге ленты в левую сторону для нереверсивного конвейера; в – конструкция для реверсивного конвейера
На конвейере с реверсивным движением ленты (рис. 4.6, в) ролики 2 устанавливаются по оси центрирующей опоры; они воздействуют через рычаг 6 и прижим 7 на боковой ролик 1, притормаживая его. Это обу- словливает поворот роликоопоры для центрирования ленты.
Для снижения динамических нагрузок и защиты ленты от разру- шения в местах загрузки применяются амортизирующие роликоопо- ры, в которых ударные нагрузки гасятся с помощью пружин или ре- зиновых элементов.
24

4.4. Привод ленточных конвейеров
Привод ленточного конвейера (рис. 4.7) состоит из электродвига- теля 1, редуктора 3, приводного барабана 5 и муфт 2, 4. Конвейерная лента приводится в движение посредством трения между лентой и приводным барабаном. Для увеличения угла обхвата барабана лен- той применяется специальный отклоняющий барабан. Привод уста- навливается на раме.
Рис. 4.7. Схема привода ленточного конвейера:
1 – двигатель; 2,4 – муфты; 3 – редуктор; 5 – приводной барабан
Приводной и натяжной барабаны обычно устанавливаются на противоположных концах ленточного конвейера, а в местах измене- ния направления размещаются отклоняющие барабаны (см. рис. 4.1).
По числу приводных барабанов различаются приводы одно-, двух- и многобарабанные (рис. 4.8); по числу двигателей – одно-, двух- и многодвигательные (рис. 4.9). Наиболее простым и распро- страненным является однобарабанный привод с одним или двумя двигателями. Однако в тяжело нагруженных конвейерах большой длины силы сопротивления движению ленты достигают значитель- ных величин и для их преодоления необходимо создавать очень большое натяжение тягового элемента (ленты). Это приводит к су- щественному увеличению массы и стоимости ленты, привода и дру- гих элементов конвейера. Поэтому применение однобарабанного привода в этом случае становится экономически невыгодным, а ино- гда и невозможным.
25

Рис. 4.8. Схемы конвейеров с различными видами приводов: а – однобарабанным; б – двухбарабанным; в – трехбарабанным
Одним из вариантов решения этой проблемы является разде- ление длинного конвейера на несколько коротких конвейеров, расположенных последовательно. Однако при этом возникает необходимость передачи груза с одного конвейера на другой, что требует установки дополнительных разгрузочных, загрузочных и очистительных устройств, а в ряде случаев и недопустимо. Наи- более целесообразным решением считается применение много- барабанного привода, т.е. установка по длине конвейера не- скольких согласованно работающих приводных устройств с ин- дивидуальными электродвигателями (рис. 4.9, д). В этом случае вся трасса конвейера разбивается на отдельные участки по числу установленных приводных устройств и каждый привод воспри- нимает нагрузку только от «своего» участка трассы. Такая сис- тема значительно снижает натяжение ленты.
26

Рис. 4.9. Схемы расположения приводов конвейеров: а – однодвигательного; б – двухдвигательного;
в, г – трехдвигательного; д – многодвигательного с прямолинейными промежуточными приводами; П – привод; Д – двигатель
Барабаны изготовляют сварными из стали Ст3 или литыми из се- рого чугуна (рис. 4.10). Для улучшения условий сцепления ленты с приводным барабаном его футеруют (облицовывают) резиной или другим фрикционным материалом (см. рис. 4.10, в).
При выборе диаметра барабана следует учитывать два взаимоисклю- чающих требования. С одной стороны, желательно иметь барабан ми- нимального диаметра с целью снижения габаритов и массы конвейера; с другой стороны, с уменьшением диаметра барабана ухудшаются усло- вия работы ленты – в ней растут напряжения изгиба.
27

Рис. 4.10. Барабаны для конвейеров с резинотканевой лентой: а – приводной; б – хвостовой и отклоняющий; в – футерованный резиной; г – вариант крепления облицовки к барабану
Диаметр приводного барабана Dбп (мм) определяют, исходя из усло- вия обеспечения достаточной долговечности резинотканевой конвейер- ной ленты, в зависимости от прочности ткани σр и числа прокладок z:
28

Dбп = KD z, |
(4.8) |
где KD – коэффициент диаметра барабана, принимается в зависимо- сти от прочности ткани σр (табл. 4.5).
|
|
|
|
|
|
Таблица 4.5 |
|
|
Зависимость КD от σp |
|
|
||
|
|
|
|
|
|
|
σр, |
65 |
100 |
150 |
200 |
300 |
400 |
Н/мм |
|
|
|
|
|
|
KD, мм |
125...140 |
140...160 |
160...170 |
170...180 |
180...190 |
190...200 |
Большие значения KD берут для лент большей ширины, например, для прокладок из полиамидных нитей с прочностью σр = 150 Н/мм принимают KD = 160 при ширине ленты B = 650 мм и KD = 170 при
B = 3000 мм.
При использовании резинотросовых лент диаметр приводного ба- рабана (мм) вычисляется по формуле
Dбп = 500 dтр,
где dтр – диаметр троса, мм.
Диаметры натяжного Dбн и отклоняющего Dбо барабанов прини- маются соответственно равными
Dбн = 0,7 Dбп; Dбо = 0,5 Dбп. |
(4.9) |
Полученные значения диаметров барабанов округляются до бли- жайших стандартных значений в соответствии с ГОСТ 22644–77: 160, 250, 315, 400, 500, 630, 800, 1000, 1250, 1400, 1600, 2000 и 2500 мм.
Длина барабана Lб берется на 100...200 мм больше ширины ленты В. Выбранный диаметр приводного барабана Dбп (мм) проверяют по
давлению ленты на поверхность барабана рл (МПа):
|
рл = 360 (Fcб + Fнб) / (α π Dσп В) ≤ [рл], |
(4.10) |
|
где Fcб и Fнб |
– натяжение сбегающей с барабана и набегающей на |
||
|
|
барабан ветвей ленты соответственно при устано- |
|
α |
|
вившемся режиме, Н; |
|
– угол обхвата барабана лентой, град; |
|
||
B |
– |
ширина ленты, мм; |
|
[рл] |
– |
допускаемое давление, принимаемое равным |
|
|
|
0,2…0,3 МПа для резинотканевой ленты и |
|
|
|
0,35…0,55 МПа для резинотросовой ленты. |
|
29