
Верстка 4 Пособие для Сталевара КЦ-1
.pdfТема 1. Система повышения эффективности производства в ОАО
«НЛМК»
Одним из важнейших показателей деятельности предприятия является качество продукции. Улучшение качества определяет выживаемость и конкурентоспособность предприятия в условиях рынка, темпы технического прогресса, внедрения инноваций, рост эффективности производства, экономию всех видов ресурсов, используемых на предприятии.
Система повышения эффективности производства предусматривает смещение акцентов от контроля качества продукции к контролю качества процесса, от аудитов технологии к стабилизации технологического процесса производственным персоналом, от принципа «чинить, когда сломается» к выявлению истиной причины поломки и разработке мер по ее устранению.
Целью системы повышения эффективности производства является достижение стабильного качества выпускаемой продукции, снижение ее себестоимости, стабилизация технологии на всех этапах производства.
В основе системы повышения эффективности производства положен метод шести сигм. Метод «Шесть сигм» в основанном применяется в уже действующем технологическом процессе, его задача улучшать показатели уже действующего процесса. Он не создает новый вид продукции, не определяет новые потребности клиентов. Он совершенствует, то, что уже существует. Поэтому с полной уверенностью можно говорить, что «Шесть сигм» - это составная часть TQM (тотального менеджмента качества).
Суть данного метода - систематизированная совокупность инструментов, позволяющих:
-выявлять потенциальные дефекты, которые могут возникнуть при применении продукции или оказании услуг;
-определять причины их появления;
-вырабатывать действия по устранению этих причин.
Целью методологии |
«Шесть сигм» является сокращение отклонений |
в ходе производственного |
процесса и его совершенствование путем |
реализации так называемого проекта совершенствования «Шесть сигм», который распадается на последовательность шагов DMAIC (define, measure, analyze, improve, control): определение, измерение, анализ, совершенствование и контроль.
На этапе «определения» (define) ставятся цели и определяются рамки проекта, выявляются проблемы, которые должны быть решены для
достижения определенного уровня отклонений. Цели |
могут различаться |
на разных уровнях организации — так, например, |
на уровне высшего |
руководства это может быть большая отдача от инвестиций или завоевание большей доли рынка. На уровне операций целью может быть увеличение объемов выпуска какого-либо цеха. На проектном уровне — снижение количества брака или увеличение эффективности отдельного процесса.
На этапе «измерения» (measure) происходит сбор информации о текущем состоянии процесса производства для получения данных, характеризующих
81
базовый уровень показателей работы, и выявления участков, требующих наибольшего внимания. На этом этапе также определяются метрики, позволяющие оценить степень приближения к намеченным целям.
На этапе «анализа» (analyze) выявляются основные причины возникновения проблем в обеспечении качества, после чего правильность выбора этих причин проверяется при помощи специальных инструментов анализа данных.
На этапе «совершенствования» (improve) внедряются решения, ориентированные на устранение основных причин тех проблем, которые были определены на этапе анализа. В число таких решений могут входить средства управления проектами и другие инструменты управления и планирования.
Цель этапа «контроля» (control) — оценка и мониторинг результатов предшествующих этапов. На данном этапе улучшения подкрепляются модификацией системы стимулов и поощрений, наборов правил, процедур, систем MRP, бюджетов, инструкций для персонала и других рычагов управления. Для гарантии корректности документации можно обеспечить, например, ее соответствие спецификации ISO 9000.
«Шесть Сигм (Six Sigma)» - это целевой показатель, соответствующий уровню максимально возможного совершенства в удовлетворении требований потребителей, т.е. это полученный методом статистических расчетов плановый показатель операционной деятельности, при котором на миллион операций или «возможностей» приходится не более 3,4 отклонений (дефектов). Само название системы определяется в разбросе статистических замеров равных + 6 σ, где σ (сигма) – стандартное отклонение.
Рассматривая плотность нормального распределения, где среднее значение – это пик плотности распределения, а стандартное отклонение определяется как расстояние между средним значением и точкой перегиба кривой.
Свойство нормального распределения: если для процесса установлены некоторые контрольные пределы, за которые выход результатов процесса считается нежелательным событием, то чем больше сигм процесса умещается между средним значением и ближайшим контрольным пределом, тем меньше дефектов имеет процесс, что наглядно видно на картинке (Рис. 54).
Уровень работы процесса определяется количеством сигм, укладывающихся в заданный интервал. Чем меньше значение стандартного отклонения, тем стабильнее и лучше результат (при условии, что среднее значении близко к целевому значению).
82
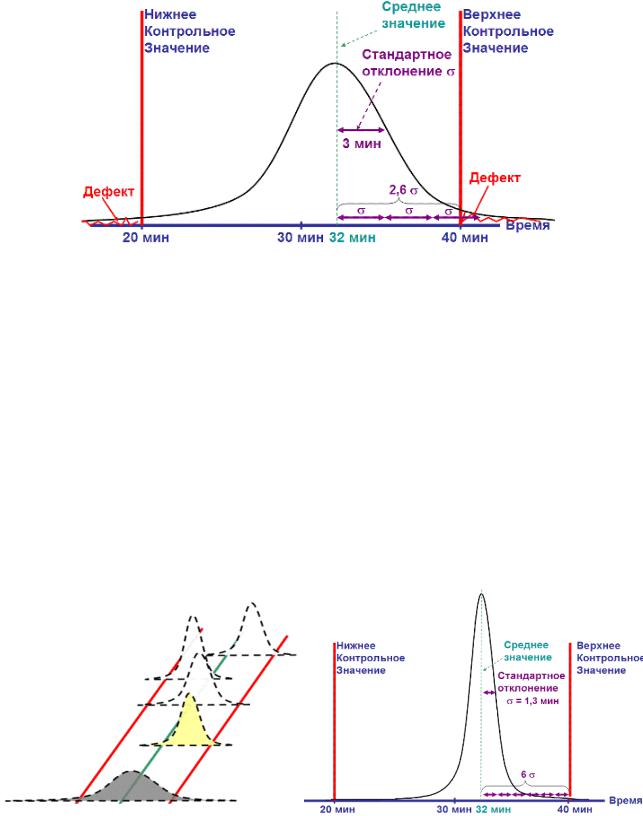
Рис. 75 Чем больше сигм процесса укладывается между средним значением и ближайшим контрольным пределом, тем меньше дефектов имеет процесс.
Процесс работает на уровне 2,6 сигм.
Из статистического обоснования известно, что при уровне процесса 4,5 сигм, из миллиона единиц продукции дефектов будет не более 3,4, и то условие выполняется для стабильных процессов. В настоящих же условиях, поведение процессов может меняться со временем года, времени суток и т.д. (Рис. 55).
Основываясь на эмпирических данных, исследователи пришли к выводу, что отклонения процесса, вызванные его естественной нестабильностью, дают отклонения качества в 1,5 сигм. Таким образом, если целевой уровень качества составляет 4,5 сигма (3,4 дефекта на миллион возможностей), то с учетом перестраховки 1,5 сигма на отклонения, необходимо обеспечить уровень качества 6 сигм (Рис. 56).
Рис. 76 Изменение процессов в |
Рис. 77 Уровень качества 6 сигм |
|
течение времени |
||
|
В рамках данной концепции принята следующая классификация организаций по критерию воспроизводимости (Таб.12)
83
Классификация организаций по критерию воспроизводимости
|
|
|
Таблица 12 |
Влияние воспроизводимости процессов на конкурентоспособность организаций |
|||
Расстояние между центром |
Число дефектов |
Стоимость |
Уровень конкуренто- |
распределения и границей допуска |
на миллион |
низкого качества |
способности |
6 сигм |
3,4 |
< 10% от ОП |
Мировой класс |
5 сигм |
233 |
10-15% от ОП |
|
4 сигмы |
6210 |
15-20% от ОП |
Средняя по отрасли |
3 сигмы |
66807 |
20-30% от ОП |
|
2 сигмы |
308537 |
30-40% от ОП |
Неконкурентоспособна |
1 сигма |
690000 |
|
|
Примечание: ОП - объем продаж |
|
Опираясь на метод «шести сигм» система повышения эффективности производства в ОАО «НЛМК» устанавливает порядок осуществления оперативной корректировки процессов производственным персоналом путем устранения «грубых» отклонений процесса от его нормального состояния. Эта процедура осуществляется с помощью отслеживания контрольных карт. Выход контролируемого параметра за контрольные границы, является сигналом производственному персоналу для определения причины и принятия корректирующего действия.
Контролируемыми характеристиками являются ключевые показатели эффективности предприятия (конечное качество продукции, себестоимость и т.д.), а также характеристики, способные на них повлиять, закрепленные за производственным подразделением в соответствии с утвержденной областью ключевых показателей эффективности (КПЭ) предприятия.
Источником информации для построения контрольной карты являются данные, содержащиеся в информационных системах ОАО «НЛМК», а также результаты испытаний, анализов, замеров и т.д. хранящиеся на бумажных или электронных носителях.
В процессе определения условий проведения анализа выбираются:
агрегат, для которого будет проводиться анализ;
источник информации для выбранной характеристики;
состав сортаментных подгрупп, по которым должны рассчитываться контрольные границы;
состав групп анализа, по которым будет проводиться анализ;
правила исключения из анализа «опытных» плавок, плавок с пометкой «несоответствующая продукция», обработанных не по действующей технологии и прочие условия;
вид контрольной карты;
способ заполнения карты (автоматический или ручной).
Контрольная карта заполняется производственным персоналом (оператором) вручную (в случае, если сбор информации по контролируемому параметру осуществляется один раз в смену и реже) или отсутствует
84
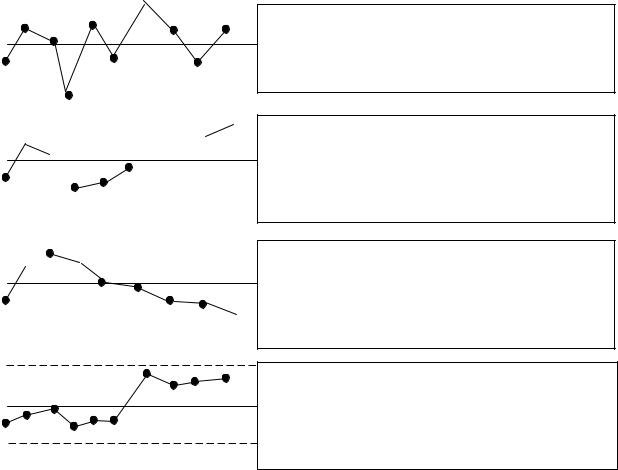
техническая возможность реализовать построение контрольной карты в автоматическом режиме.
По каждой вводимой контрольной карте или группе контрольных карт, вводимых по конкретному производственному подразделению, а также в случае изменения контрольных границ для уже существующей контрольной карты, издается распоряжение вице-президента по перспективному развитию и экологии, определяющее регламент (периодичность) и устанавливающее обязанности персонала по проведению процедуры заполнения и анализа контрольных карт.
Таким образом, каждый контролируемый процесс закрепляется за конкретным производственным персоналом.
По мере поступления информации об отслеживаемой характеристике по формулам, представленным на бланке контрольной карты, персонал производственного подразделения осуществляет расчет значений точек, наносимых на карты - среднего значения для каждой подгруппы, размаха подгруппы, скользящего размаха между индивидуальными значениями и т.д. – в зависимости от вида контрольных карт. Точки, нанесенные на контрольные карты, соединяют линиями.
Критерии проявления особых причин
LSC
_ X
LIC
LSC _
X
LIC
LSC _
X
LIC
2 – Наблюдается нестабильность. 2 точки вышли за пределы контроля. Необходимо выяснить причины, вызвавшие эти отклонения, чтобы уменьшить нестабильность.
3a – Серия из 6 последовательных точек (увеличение). Вероятно, имело место изменение технологического процесса. Необходимо предупредить ответственных и/или отрегулировать процесс.
3б – Серия из 6 последовательных точек (уменьшение). Вероятно, имело место изменение технологического процесса. Необходимо предупредить ответственных и/или отрегулировать процесс.
LSC |
_ |
X |
LIC |
9 – Зафиксировано резкое отклонение. В технологическом процессе произошло изменение. Необходимо установить причину и предупредить об этом ответственных и/или пересмотреть контрольные границы
Рис. 78 Интерпретация карт
85
Анализ контрольной карты производственным персоналом, разработка корректирующих/предупреждающих действий заключается в следующем:
регулярный анализ контрольной карты в ИС СПЭП (в случае автоматического заполнения) или заполнение бланков контрольных карт (в случае ручного заполнения);
выявление причин нестабильности процесса (поломка оборудования, приход нового сотрудника, новая партия сырья, грубое нарушение технологии и т.д.) в соответствии с критериями проявления особых причин настоящего стандарта предприятия;
оперативное устранение причин (если возможно) или разработка корректирующих/предупреждающих действий и определение ответственных за их выполнение;
ввод информации по всем выявленным несоответствиям, их причинам и предпринятым действиям в ИС СПЭП не позднее 5-ти суток с момента выявления отклонения (или фиксирование причин
на бланке, в случае заполнения вручную).
Для каждого случая нарушения контрольной границы (красной точки) в систему вводится результат анализа причины возникновения этого нарушения.
Регулярно в соответствии с графиком проводится цеховое совещание по качеству, на котором рассматриваются результаты контроля процесса производственным персоналом и обсуждаются разработанные мероприятия. По итогам каждого совещания персонал цеха/производства выпускает протокол и заполняет форму инициатив по повышению экономической эффективности производственного процесса в рамках СПЭП.
Ежемесячно на совещании по качеству металлопродукции, проводимому директором по направлению в соответствии с графиком, анализируется эффективность принятых мер в предыдущих периодах, оценивается выполнение начальником цеха/производства ключевых показателей и рассматриваются нерешенные вопросы, включенные в протокол цехового совещания по качеству.
Тема 2. Контрольные карты, применяемые в рамках СПЭП
в ОАО «НЛМК»
Перечень контрольных карт ИС СПЭП, контролируемых сталеваром конвертера КЦ-1:
КЦ-1. Конвертеры. Длительность выпуска металла из конвертера [ОСП04]; КЦ-1. Конвертеры. Основность конвертерного шлака (1 замер) [ОСП04]; КЦ-1. Конвертеры. Наличие химподогрева на УДМ [ОСП04];
КЦ-1. Конвертеры. Содержание FeO в конвертерном шлаке (1 замер) [ОСП04]; КЦ-1. Конвертеры. Температура металла на повалке (1 замер) [ОСП04]; КЦ-1. Конвертеры. Окисленность металла на УДМ (1 замер) [ОСП04]; КЦ-1. Конвертеры. Температура после усреднительной продувки [ОСП04];
86
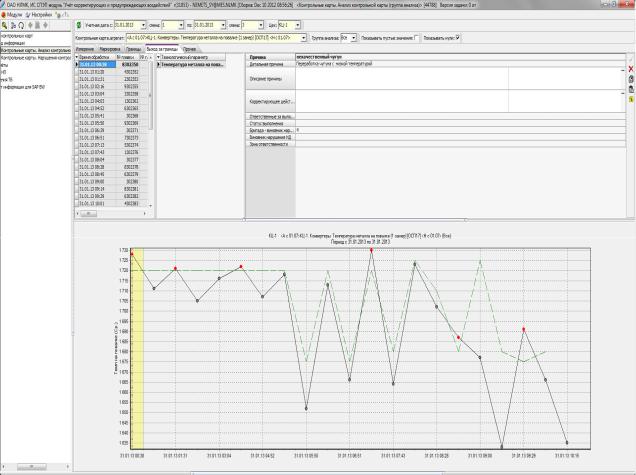
Пример контрольной карты в ИС СПЭП
Рис. 79 КЦ-1. Конвертеры. Температура металла на повалке (1 замер) [ОСП17]
Действия сталевара в рамках СПЭП:
-ежесуточный анализ контрольных карт в ИС СПЭП (в случае автоматического заполнения) или заполнение бланков контрольных карт (в случае ручного заполнения);
-выявление детальных причин нестабильности контролируемой характеристики (случаев выпада за контрольные границы) в ИС СПЭП;
-оперативное устранение причин нестабильности контролируемой характеристики (если возможно) или разработка корректирующих действий, направленных на устранение причин нестабильности;
-ввод информации по причинам, детальным причинам нестабильности контролируемых характеристик и предпринятым корректирующим действиям
вИС СПЭП не позднее 3-х суток с момента выявления нестабильности (выпада за контрольные границы) или фиксирование причин на бланке, в случае заполнения вручную.
87
Тема 3. Альтернативные системы повышения эффективности
производства
88
Перечень нормативных документов, требования которых должен выполнять сталевар конвертера
№ |
Наименование документа |
Шифр |
|
п./п. |
|||
|
|
||
1 |
2 |
3 |
|
1 |
Правила внутреннего трудового распорядка |
- |
|
работников ОАО «НЛМК» |
|||
|
|
||
|
Положение о системе управления охраной |
|
|
2 |
труда и промышленной безопасностью ОАО |
ПСУОТиПБ 05757665-НЛМК |
|
|
«НЛМК» |
|
|
3 |
Инструкция по охране труда для работников |
ИОТ 000-004 |
|
комбината (общая) |
|||
|
|
||
4 |
Положение о применении бирочной системы в |
ПСУОТиПБ 6.2-01 |
|
подразделениях ОАО «НЛМК» |
|||
|
|
||
|
Положение о применении нарядов-допусков |
|
|
5 |
при производстве работ повышенной |
ПСУОТиПБ 5.8-01 |
|
|
опасности |
|
|
|
Инструкция по охране труда для сталевара и |
|
|
6 |
подручного сталевара конвертера участка |
ИОТ 006 - 002 |
|
|
подготовки производства и выплавки стали |
|
|
7 |
Перечень опасностей и рисков КЦ-1 |
- |
|
|
Технологическая инструкция «Производство |
|
|
8 |
непрерывнолитых слябов из конвертерной |
ТИ 05757665-КЦ1-01 |
|
|
стали |
|
|
|
Технологическая инструкция «Производство |
|
|
9 |
непрерывнолитых слябов из электротехничес- |
ТИ 05757665-КЦ1-05 |
|
|
кой стали» |
|
|
10 |
Производственно-техническая инструкция |
ПТИ 006-002-037 |
|
сталевару конвертера |
|||
|
Инструкция по эксплуатации конвертера |
|
|
11 |
вертикального с комбинированным дутьем |
ИЭ 05757665-06-059 |
|
|
емкостью 160 т |
|
|
|
Технологическая инструкции «Изготовление и |
|
|
12 |
эксплуатация кислородно-конвертерных |
ТИ 05757665-КЦ1-КЦ2-15 |
|
|
фурм» |
|
|
13 |
Инструкция по эксплуатации «Шлаковоз |
ИЭ 05757665-006-062 |
|
самоходный» |
|||
14 |
Инструкция по эксплуатации «Установка |
ИЭ 05757665-006-082 |
|
локального торкретирования» |
|||
|
Инструкция по режиму работы и безопасному |
|
|
15 |
обслуживанию сосудов, работающих под |
ИЭ 05757665-006-115 |
|
|
давлением |
|
|
16 |
Инструкция по эксплуатации «Комплекс |
ИЭ 05757665-006-097 |
|
оборудования отсечки шлака» |
|||
|
Инструкция по эксплуатации «Машина для |
|
|
17 |
бурения футеровки сталевыпускного |
ИЭ 05757665-006-130 |
|
|
отверстия конвертора» |
|
|
18 |
Инструкция по эксплуатации «Приспособле- |
ИЭ 05757665-006-153 |
|
ние для очистки горловины конвертора» |
89
1 |
2 |
3 |
|
Инструкция по эксплуатации «Лазерный |
|
19 |
сканер «Lacam-M» по определению |
ИЭ 05757665-006-194 |
остаточной толщины рабочего слоя |
||
|
конвертора, емкостью 160тонн» |
|
20 |
КПТО Завалка металлолома в конвертер |
КПТО 006-002-18771-0001-2010 |
21 |
КПТО Заливка чугуна в конвертер |
КПТО 006-002-18771-0003-2010 |
22 |
КПТО Замер температуры и окисленности |
КПТО 006-002-18771-0005-2010 |
металла после продувки и плавки |
||
23 |
КПТО Отбор пробы металла после продувки |
КПТО 006-002-18771-0007-2010 |
плавки, ее обработка и отправка |
||
24 |
КПТО Отдача ферросплавов на раскисление и |
КПТО 006-002-18771-0009-2010 |
легирование при выпуске металла |
||
25 |
КПТО Измерение НЗ |
КПТО 006-002-18771-0011-2011 |
26 |
КПТО Наладка и калибровка технологи- |
КПТО 006-002-18771-0012-2011 |
ческого оборудования |
||
27 |
КПТО Подварка футеровки конвертера |
КПТО 006-002-18771-0013-2011 |
огнеупорными материалами |
||
|
КПТО Перегрузка торкрет-массы из |
|
28 |
приемных бункеров в расходные системы |
КПТО 006-002-18771-0014-2011 |
|
факельного торкретирования |
|
29 |
КПТО Получение и доставка ферросплавов и |
КПТО 006-002-18771-0015-2011 |
раскислителей на плавку |
||
30 |
КПТО Факельное торкретирование футеров- |
КПТО 006-002-18771-0016-2011 |
ки конвертера |
||
31 |
КПТО Удаление настылей с кислородной |
КПТО 006-002-18771-0017-2011 |
фурмы |
||
32 |
КПТО Удаление настылей с горловины |
КПТО 006-002-18771-0018-2011 |
конвертера |
||
33 |
КПТО Выпуск металла из конвертера |
КПТО 006-002-18771-0019-2011 |
34 |
КПТО Горячий ремонт сталевыпускного |
КПТО 006-002-18771-0024-2011 |
отверстия |
Список рекомендуемой литературы
1.Кривченко Ю.С., Низяев Г.И., Шершевер М.А. Сталеплавильщик конвертерного производства. - М.: Металлургия, 1991.
2.Кривченко Ю.С., Низяев Г.И., Шершевер М.А. Сталевар конвертерного цеха. - М.: Металлургия, 1985.
3.Кудрин В.Н. Теория технологии производства стали. – М.: Мир, 2003.
4.Чиграй И.Д. Подручный сталевара конвертера. – М. Металлургия,
1987.
5.Соколов Г.А. Производство стали. - М.: Металлургия, 1982.
6.Чертов А.Д. Современный кислородно-конвертерный процесс. – ОАО
«НЛМК»,2010.
7.Якушев М.А. Справочник конверторщика. – Челябинск: Металлургия,
1990
90