
Технология производства стали в ОАО НЛМК
.pdf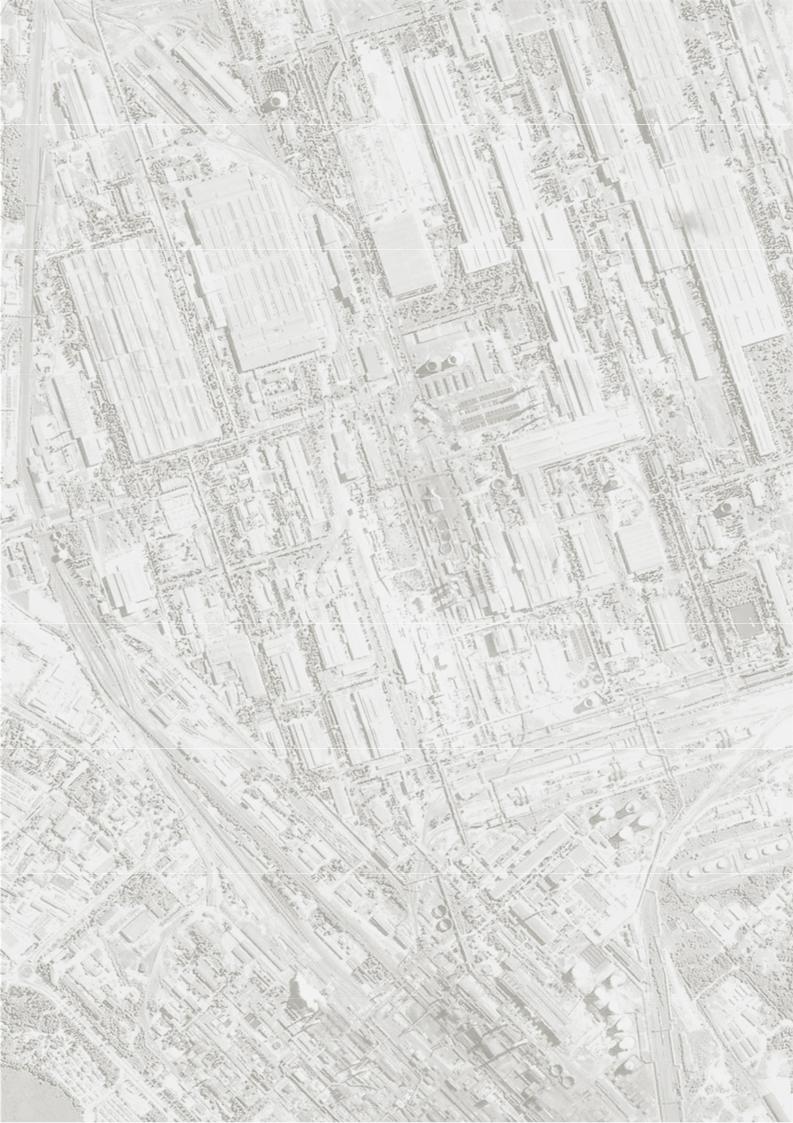
ОТКРЫТОЕ АКЦИОНЕРНОЕ ОБЩЕСТВО «НОВОЛИПЕЦКИЙ МЕТАЛЛУРГИЧЕСКИЙ КОМБИНАТ» Управление профессионального развития персонала
УТВЕРЖДАЮ
Директор по персоналу
и общим вопросам
_______________ С.П. Мельник
«____» _______________ 2013 г.
Пособие для обучения вновь принятого персонала
Технология производства стали в ОАО «НЛМК»
Липецк
2013
|
СОДЕРЖАНИЕ |
|
ВСТУПЛЕНИЕ |
3 |
|
1 |
АГЛОМЕРАЦИОННОЕ ПРОИЗВОДСТВО |
8 |
2 |
КОКСОХИМИЧЕСКОЕ ПРОИЗВОДСТВО |
10 |
3 |
ДОМЕННОЕ ПРОИЗВОДСТВО |
12 |
4 |
СТАЛЕПЛАВИЛЬНОЕ ПРОИЗВОДСТВО |
16 |
5 |
ПРОКАТНОЕ ПРОИЗВОДСТВО |
20 |
|
5.1 Производство горячего проката |
20 |
|
5.2 Производство холоднокатаного проката |
22 |
|
5.2.1 Производство холодного проката и покрытий |
23 |
|
5.2.2 Производство трансформаторной стали |
24 |
|
5.2.3 Производство динамной стали |
26 |
6 |
РЕМОНТНОЕ ПРОИЗВОДСТВО |
28 |
7 |
ЭНЕРГЕТИЧЕСКОЕ ПРОИЗВОДСТВО |
28 |
ГЛОССАРИЙ |
30 |
2
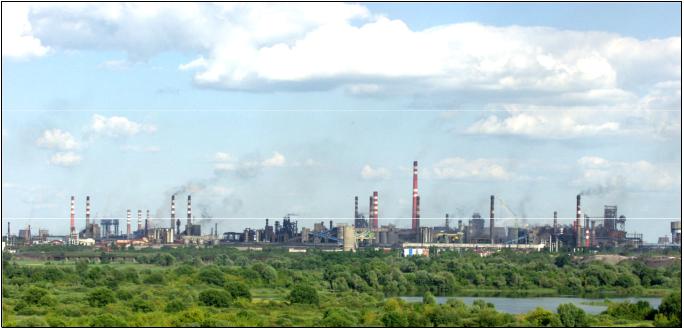
ВСТУПЛЕНИЕ
ОАО «НЛМК» является предприятием с полным металлургическим циклом, содержащим все производства, необходимые для получения из железорудного сырья конечного металлургического продукта – проката без покрытий и с покрытиями.
Общая технологическая схема производства комбината включает: агломерационное, коксохимическое, доменное, сталеплавильное и прокатное производства. Нормальное функционирование основных производств осуществляют вспомогательные подразделения: Энергетическое производство, Ремонтное производство, Центр технического обслуживания и ремонтов, Огнеупорный цех, Ферросплавный цех, Копровый цех, Цех по переработке металлургических шлаков и другие.
Агломерационное и коксохимическое производства (АГП и КХП) являются производителями основных компонентов для доменного производства – агломерата и кокса.
Доменное производство предназначено для получения чугуна, который является не только полуфабрикатом для сталеплавильного производства, но и товарной продукцией первого передела.
Сталь, получаемая в сталеплавильном производстве при продувке жидкого чугуна и металлолома кислородом, разливается в непрерывнолитые заготовки (слябы), которые в дальнейшем используются для производства проката, а также являются товарной продукцией второго передела.
Прокатное производство представлено Производством горячего проката (ПГП), Производством холодного проката и покрытий (ПХПП), Производством трансформаторной стали (ПТС) и Производством динамной стали (ПДС).
Сталь, прокатанная на стане 2000 ПГП (горячекатаный прокат), является товарной продукцией НЛМК третьего передела и служит заготовкой в производстве холоднокатаного проката в ПХПП, ПТС, ПДС.
На комбинате освоены технологии, позволяющие производить холоднокатаный углеродистый прокат без покрытий, с цинковым и полимерным покрытиями, а также прокат электротехнических сталей, что значительно увеличивает стоимость товарной продукции Компании. Холоднокатаный прокат является металлургической продукцией НЛМК с наиболее высокой добавленной стоимостью.
3
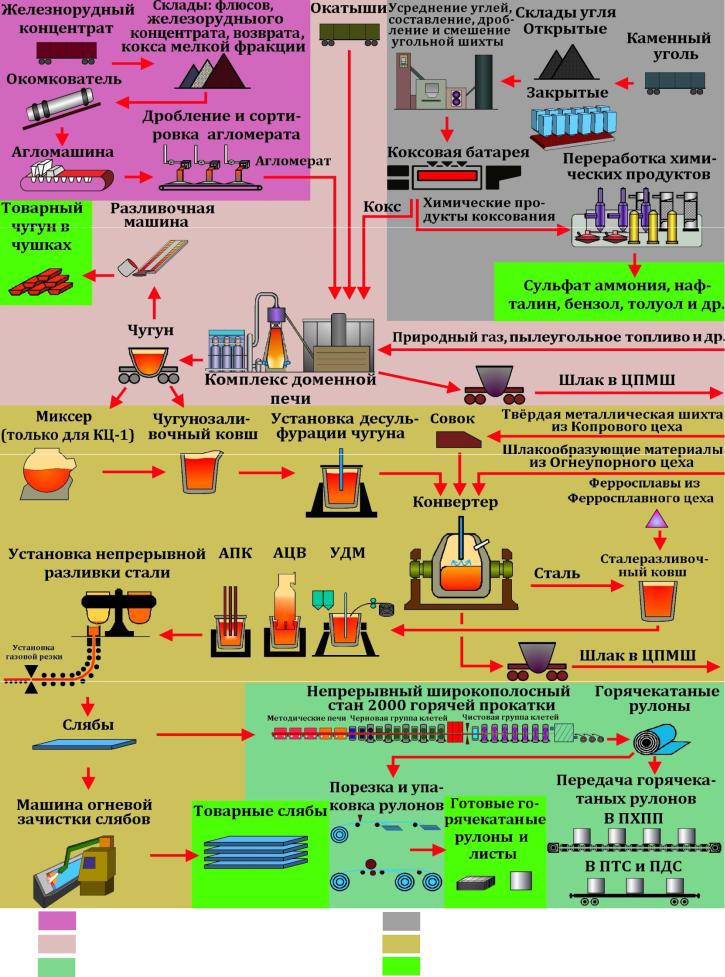
Общая схема
– Агломерационное производство |
– Коксохимическое производство |
– Доменное производство |
– Сталеплавильное производство |
– Производство горячего проката |
– Готовая продукция |
4
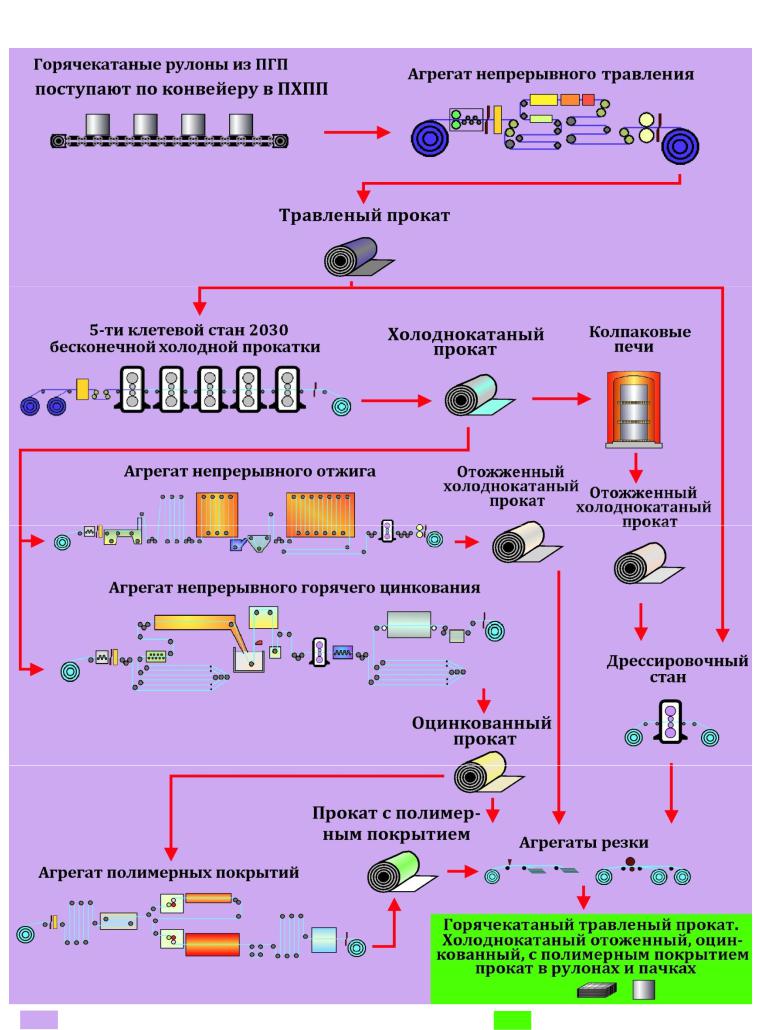
производства ОАО «НЛМК»
– Производство холодного проката и покрытий |
– Готовая продукция |
5
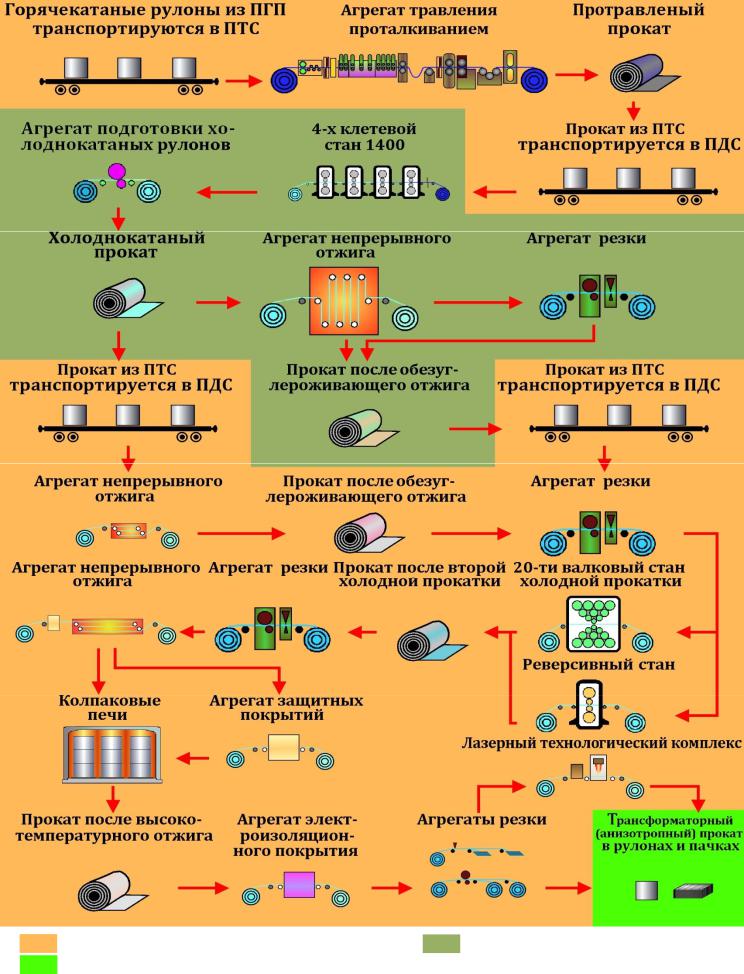
Общая схема
– Производство трансформаторной стали |
– Производство динамной стали |
– Готовая продукция |
|
6
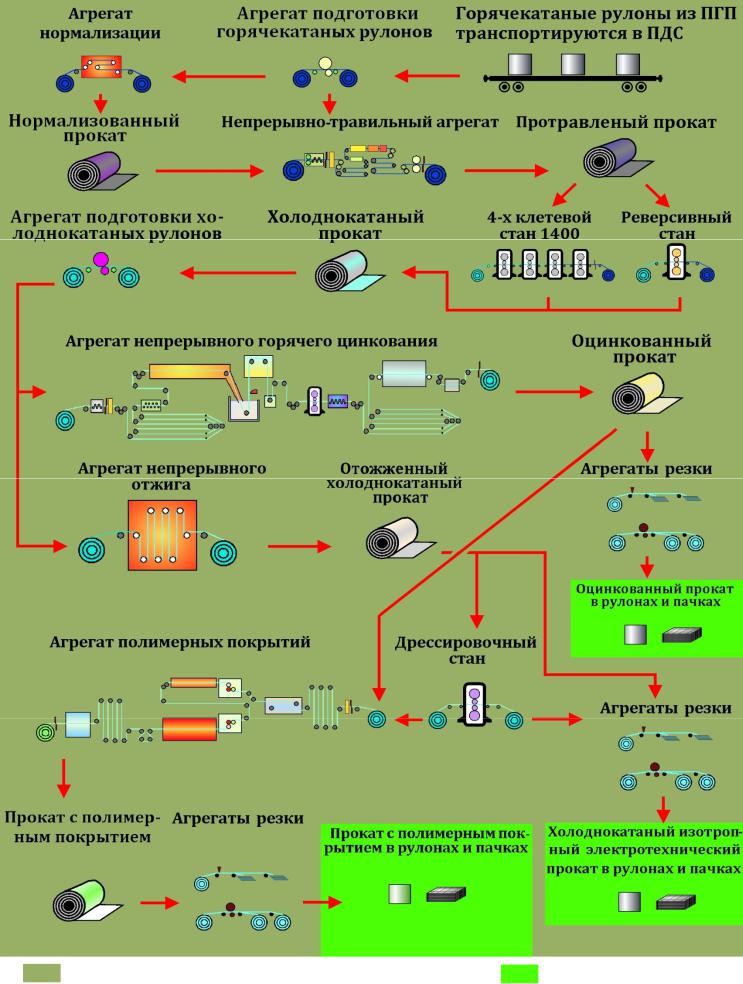
производства ОАО «НЛМК»
– Производство динамной стали |
– Готовая продукция |
7
1 АГЛОМЕРАЦИОННОЕ ПРОИЗВОДСТВО
Задачей агломерационного производства является получение высококачественного, равного по крупности агломерата, являющегося сырьём для доменной печи в процессе выплавки чугуна.
Агломерат представляет собой окускованный спечённый рудный концентрат, полученный в процессе агломерации. Процесс агломерации заключается в укрупнении исходного сырья (получении кусков агломерата) путём спекания его с твёрдым топливом при температуре 1300 -1600 °С, с целью придания формы и свойств, необходимых для оптимальной и устойчивой работы доменной печи.
Исходным сырьём для производства агломерата являются железорудные концентраты (продукт обогащения на горно-обогатительном комбинате железной руды), мелкая железная руда, специальные добавки – флюсы (известняк, доломит), металлосодержащие отходы металлургического производства (шлам, пыль, окалина и др.), возврат (отсеянный мелкий агломерат, возвращаемый для повторного спекания). Твёрдым топливом для процесса агломерации служит кокс мелких фракций.
Процесс производства агломерата состоит из следующих операций: подготовка шихты (смеси компонентов исходного сырья и твёрдого топлива), спекание подготовленной шихты на агломерационных машинах, обработка спёкшегося агломерата.
Подготовка шихты включает в себя: дозирование (для поддержания заданного соотношения и количества между компонентами шихты), смешивание, увлажнение и окомкование (для получения однородной смеси всех компонентов шихты с высокой газопроницаемостью в процессе спекания).
Процесс спекания подготовленной шихты (агломерации) осуществляется в агломерационных машинах, представляющих собой замкнутый конвейер, состоящий из спекательных тележек (паллет) с днищами в виде колосниковой решётки, движущихся по направляющим рельсам. При прохождении паллеты под питателем на неё укладывается подготовленная шихта. В загруженной паллете, при её прохождении под газовыми горелками зажигательного горна, начинается горение твёрдого топлива, содержащегося в поверхностной зоне спекаемого слоя шихты, при этом фронт горения распространяется сверху вниз.
Движущиеся паллеты последовательно проходят под вакуум-камерами, предназначенными для просасывания через спекаемую шихту воздуха, необходимого для горения твёрдого топлива и удаления продуктов сгорания. Воздух просасывается сквозь слой шихты благодаря действию специальных вакуумных устройств – эксгаустеров. В процессе спекания непрерывно увеличивается высота слоя готового агломерата и уменьшается высота слоя неспечённой шихты.
Последующая обработка спёкшегося агломерата заключается в его дроблении и сортировке с удалением из него возврата, вновь используемого в качестве компонента шихты.
Отсортированный агломерат требуемой фракции поступает в доменные цеха. В состав агломерационного производства ОАО «НЛМК» входят шихтоподготовительный и два агломерационных цеха, в каждом из которых находятся по две
агломерационные машины.
8
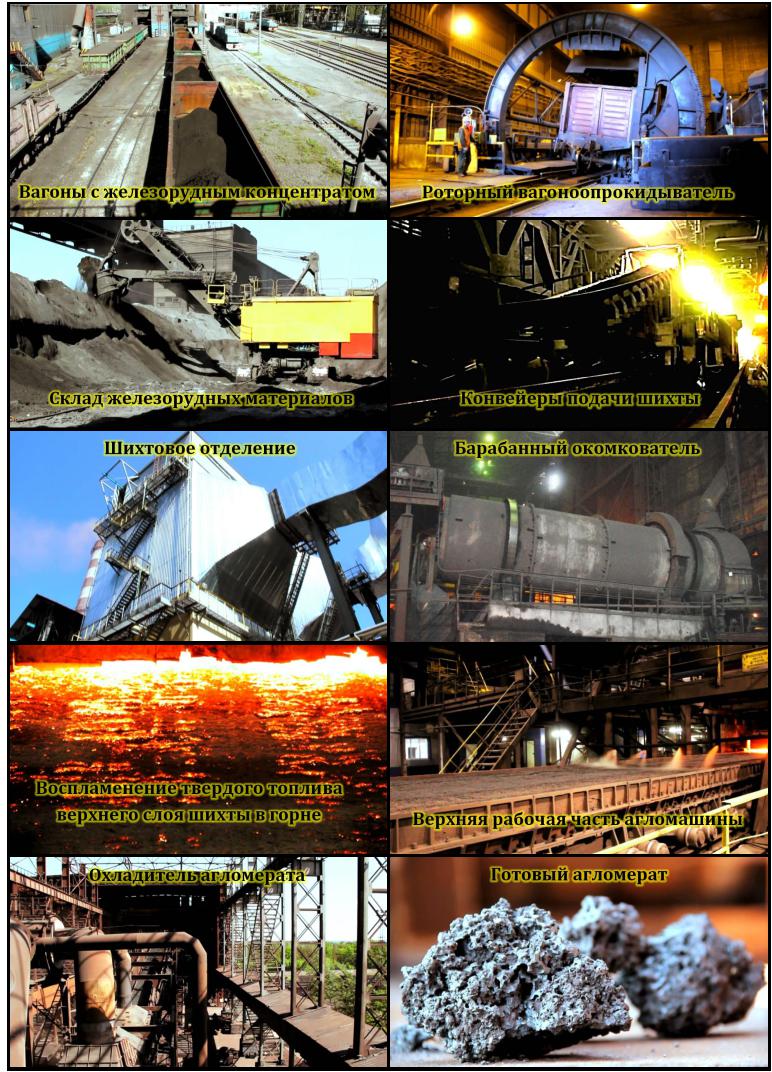
2 КОКСОХИМИЧЕСКОЕ ПРОИЗВОДСТВО
Задачей коксохимического производства является получение кокса с требуемыми свойствами, а также попутных химических продуктов, образующихся в процессе производства кокса.
Являясь топливом в доменной печи при производстве чугуна, кокс должен обладать следующими свойствами: быть прочным (не истираться при транспортировании и выдерживать большие нагрузки в самой доменной печи), пористым (не препятствовать прохождению газов, движущихся в доменной печи), достаточно чистым (содержать как можно меньше золы и серы).
Исходным сырьём для получения кокса являются особые сорта каменных углей, называемых коксующимися.
Кокс, получают в процессе коксования. Коксование заключается в нагреве смеси каменных углей (угольной шихты) в коксовых печах до температуры 900-1100°С без доступа воздуха, в результате чего образуется твёрдый остаток – кокс, а также попутные химические продукты коксования.
Процесс производства кокса состоит из следующих операций: подготовка угольной шихты, коксование угольной шихты с образованием кокса, тушение кокса, улавливание и переработка выделяющихся химических продуктов, сортировка кокса.
Подготовка угольной шихты включает в себя приём, складирование и усреднение углей, составление, дробление и смешение угольной шихты.
Коксование угольной шихты с образованием кокса осуществляется в коксовых батареях (параллельно располагающихся коксовых печах, объединённых в батареи для уменьшения потери тепла), в которые шихта загружается специальным устройством через люки, находящиеся на самом верху батареи. Процесс коксования в каждой печи периодический, при этом наличие в коксовой батарее ряда параллельно работающих печей обеспечивает непрерывность работы всей батареи. В процессе коксования, длительность которого составляет около пятнадцати часов, содержание в коксе вредных примесей (золы и серы) сводится к минимуму. Когда процесс коксования в одной из печей заканчивается, штанга коксовыталкивателя батареи медленно выдвигает «коксовый пирог» - пласт раскалённого кокса в равномерно движущийся вагон, предназначаемый для приёма, перемещения кокса под башню для его тушения и передачи к месту выгрузки.
Дальнейшая обработка выданного из печи раскалённого кокса заключается в его тушении водой (мокрый способ) или газом-охладителем (сухой способ) с последующей сортировкой на разные по крупности фракции.
Отсортированный кокс требуемой фракции поступает в доменные цеха. Попутные химические продукты коксования улавливаются для последующей
переработки. Получаемая продукция (сульфат аммония, нафталин, бензол, толуол и др.) используется в различных отраслях промышленности и сельского хозяйства. Очищенный коксовый газ применяют в металлургических печах в качестве топлива.
В состав коксохимического производства ОАО «НЛМК» входят: углеподготовительный цех, коксовый цех, цех улавливания химических продуктов.
10