
- •Степень очистки
- •Фильтрация
- •Аэрация
- •Сорбция
- •Дегазация
- •Таблица 2
- •Показатели
- •Цели водопользования
- •Показатели
- •Цели водопользования
- •Таблица 5
- •Вещество
- •Таблица 6
- •Гидрохимическая характеристика водного объекта
- •Определяем коэффициент диффузии:
- •Таблица15
- •Состав сточных вод гальванического цеха
- •После электрообработки маслоэмульсионных стоков осадок из отстойника подается в шламонакопитель, где он может находиться до 15 суток. Отношение диаметра шламонакопителя к высоте конической части принимаем D/H= 1,5.
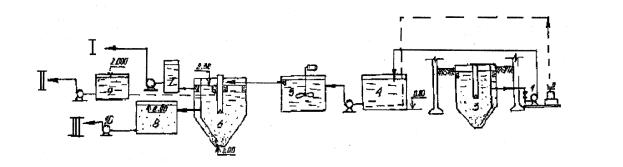
Рис. 14. Технологическая схема обработки осадка вермикулита. 1 – насос подачи шлама; 2
– воздуходувка; 3 – шламонакопитель; 4 – резервуар – усреднитель; 5 – механический смеситель; 6 – отстойник; 7 – емкость для иловой воды; 8 – емкость для сбора осадка; 9 - емкость для сбора масла; 10 – насос для подачи осадка на обезвоживание. I – на фильтры; II – на утилизацию; III – на вакуум-фильтры.
На рис. 13. и рис. 14. представлены схемы кондиционирования осадка раствором H2SO4 (рис. 13) и обработка вермикулитом (рис. 14).
Принцип работы установки электрокоагуляционной обработки осадка:
Маслосодержащий осадок забирается из шламонакопителя сифонным трубопроводом и подводится к всасывающему патрубку насоса, которым подается в резервуар-усреднитель, где усредняется по замасленности, удельному содержанию осадка в единице объема и по расходу; из резервуар-усредни- теля с помощью насосов-дозаторов подается в напорный электрокоагулятор, где происходит насыщение осадка коагулирующими ионами алюминия для увеличения его сорбционной способности.
Обработанный осадок поступает в контактную камеру для улучшения процесса хлопьеобразования.
После прохождения контактной камеры осадок поступает в отстойник, откуда подается в резервуар для сбора осадка и далее с помощью насосов-до- заторов в трубопровод перед поступлением маслоэмульсионных сточных вод на электрокоагуляционную обработку.
Технологический расчет установки электрокоагуляционной обработки осадка Шламонакопитель
После электрообработки маслоэмульсионных стоков осадок из отстойника подается в шламонакопитель, где он может находиться до 15 суток. Отношение диаметра шламонакопителя к высоте конической части принимаем D/H= 1,5.
Площадь поперечного сечения:
F=β∙Qчас∙n/3,6∙vp∙N,
где n – расчетное количество суток; β – коэффициент для учета объемного ис-
97

пользования отстойника, для D/H=1,5; β=1,5; N – количество шламонакопителей; vp – расчетная скорость движения осадка, vp=0,6 мм/с.
F=1,5∙1,5∙15/3,6∙0,6∙1=15,6 м2
Диаметр шламонакопителя:
D = |
|
4F |
= |
|
4 × 15,6 |
= 4,5м |
|
π |
|
3,14 |
|||
|
|
|
|
|
Принимаем трубопровод для отвода осадка диаметром 200 мм.
При угле наклона стен к горизонтали 50° высота конической части шламонакопителя:
hк=D/2∙tg(90-50)=4,5/2∙0,64=2,7 м
Объем уплотненного осадка:
Wуп=Qчас∙94/98=1,5∙94/98=1,4 м3
Усреднитель
Расход и концентрация нефтепродуктов в осадке производственных сточных вод колеблются в течение суток в широких пределах, поэтому для обеспечения нормальной работы установки необходимо усреднение осадка по замасленности, удельному содержанию осадка в единице объема и по расходу в регулирующих емкостях – усреднителях.
При расчетах усреднителя принимаем расчетный период усреднения 8 часов. Ориентировочный объем усреднителя в соответствии с принятым периодом усреднения составит:
V=Qсут∙T/τ,
где τ – число часов работы усреднителя, τ=16 ч; Т – период усреднения, Т=8ч.
V=24∙8/16=12 м3.
Число камер усреднителя должно быть не менее двух. Принимаем две камеры усреднителя объемом 6 м3 каждая с высотой усреднителя Н=1 м.
Ширина коридора:
В=2∙Н=2∙1=2 м.
Тогда длина усреднителя:
L=V/B∙H=6/2∙1=3 м
98
Усреднитель заглублен в землю и осадок поступает в него самотеком. Перемешивание осадка производится подачей сжатого воздуха через перфорированные пластмассовые трубы – барбатеры с отверстиями диаметром 5 мм и шагом оси отверстий 30–60 мм. Трубы укладываются по дну резервуара вдоль его стенок на подставках высотой 600 мм.
Диаметр барбатеров принимаем 75 мм.
Необходимое количество воздуха, подаваемое в усреднитель:
Q = n∙L∙qуд,
где n – число барбатеров в камере усреднителя, n=1 шт; L – длина барбатера, L=3 м; qуд – удельная интенсивность аэрации, qуд=5 – 12 м3/ч на 1 м барбатера.
Принимаем qуд=5 м3/ч. Тогда:
Q=1∙3∙5=15 м3/ч=0,25 м3/мин.
Для двух камер усреднителя расход воздуха составит 30 м3/ч.
Напорный электрокоагулятор
После усреднителя осадок подается на обработку в электрокоагулятор с растворимыми алюминиевыми электродами. Электрокоагуляторы представляют собой напорные пластинчатые электролизеры вертикального типа.
Оптимальными параметрами процесса являются:
∙доза алюминия DAl=40 мг/л;
∙напряжение на электродах 15 В;
∙оптимальная плотность тока i=160 А/м2;
∙выход алюминия по току η=70%.
На основании этих данных рассчитываем производственную установку электрокоагулятора.
Часовой расход алюминия GAl, который необходимо ввести в обрабатываемую воду:
GAl=DAl∙Qч,
где DAl – доза алюминия, DAl=40 мг/л; Qч – часовой расход осадка, Qч=1,5 м3/ч.
GAl=40∙1,5=60 г/ч
Сила тока I, обеспечивающая растворение алюминия:
I=GAl∙100/k∙η,
где GAl – часовой расход алюминия; k – электрохимический эквивалент алюминия, k=0,3356 г/А∙ч; η – выход алюминия по току
99
I=60∙100/0,3356∙70=255 А
Принимаем 3 выпрямителя по 100 А.
Рабочая поверхность анода S определяется, исходя из оптимальной плотности тока:
S=I / i=255/160=1,6 м2
Необходимая толщина анодов δ определяется с учетом их износа на 80% и срока эксплуатации:
δ=Qсут∙DAl∙nсут/0,4∙γ∙S∙106,
гдеQсут – суточный расход осадка, м3/сут ; nсут – расчетная продолжительность работы одного пакета электродов, сут; γ – удельный вес анодного материала, т/м3; S – рабочая поверхность анода, м2.
δ=24∙40∙12/0,4∙2,69∙1,6∙106=0,006 м=6 мм
Толщину катода принимаем также 6 мм.
Размеры одной пластины электрода принимаются в соответствии с конструкцией электролизера:
fэл=0,42∙1,85=0,78 м2
Общее количество анодов:
nа=S/fэл=1,6/0,78=2 шт.
Общее количество электродов:
n=2∙na+1=2∙2+1=5
В аппарате, в соответствии с конструкцией, общее количество электродов 17, из них 9 анодов и 8 катодов. Принимаем 1 аппарат.
Ширина электролизера:
В=b+2∙a=0,42+2∙0,01=0,44 м,
где b – ширина электрода, м; а – расстояние от электродов до корпуса электролизера, м.
100
Длина электролизера:
L=n¢∙d+9∙(n¢-1)∙l+2∙a=17∙0,006+(17-1)∙0,015+2∙0,01=0,36
где l – расстояние между электродами, м; n¢ – количество электродов в аппарате, шт; d – толщина электрода, м.
Высота электролизера:
Н=hэл+а1+а2=1,85+0,15+0,25=2,25 м,
где а1 – расстояние от электрода до дна, м; а2 – расстояние от электрода до поверхности воды, м; hэл – высота электрода, м.
Строительная высота:
Нстр=Н+0,175=2,25+0,175=2,43 м
Объем осадка в электролизере равен разности между внутренним объемом электролизера Wвн и объемом электродов Wэ:
Wос=Wвн – Wэ=(2,43∙0,36∙0,44)-(17∙0,42∙1,85∙,006)=0,31м
Время пребывания осадка в аппарате t:
t=Wос/Qчас=0,31/1,5=0,2 ч
Скорость движения осадка в электролизере:
v=H/t=2,25/0,2=11,25 м/ч
Потребляемая мощность:
Е=I∙U=255∙15=3825Вт=3,8 кВт
Удельный расход электроэнергии:
W=I∙U/Qчас=3,8/1,5=2,4 кВт×ч/м3
Рассчитываем количество выделяющегося водорода на катодах для проектирования вентиляции:
W=g∙c∙I∙(273+T)/273
где γ – выход водорода по току (0,9-0,95); с – объемный электрохимический эквивалент водорода, равный 0,00042 м3/(А∙ч); Т – температура осадка, °С; I –
101
необходимая сила тока, пропускаемая через электролизер.
W=0,9∙0,00042∙255∙(273+20)/273=0,103 м3/ч
В осадке растворяется водорода:
Wp=21,4∙(273+T)∙Q/(273∙103)
где Q – расход осадка, м3/ч; 21,4 – растворимость водорода в 1 м3 осадка при Т=0°С и атмосферном давлении, л.
Wp=21,4∙(273+20)∙1,5/(273∙103)=0,034 м3/ч
В производственном помещении выделяется водорода:
Wвыд=W-Wp=0,103-0,034=0,069 м3,
что составляет 0,03 об.% < 0,04 об.% , т.е. автономное вытяжное устройство для электролизера не нужно.
В производственном помещении предусматривается общевытяжная вентиляция.
Контактная камера
Контактная камера служит для улучшения процесса хлопьеобразования и рассчитывается на время пребывания в ней осадка 10 мин.
Объем камеры в соответствии с временем контакта:
V=Qсут/τ∙T,
где Qсут – суточный расход осадка, м3/сут; τ – число часов работы контактной камеры, τ=16 ч; Т – период контакта, Т=0,17 ч
V=24/16∙0,17=1 м3
Принимаем одну контактную камеру с размерами в плане 1х1х1 м. Перемешивание осадка производится с помощью барбатера сжатым
воздухом через перфорированные трубы d=75 мм с отверстиями d=5 мм, которые располагаются по его длине через 30÷60 мм.
Необходимое количество воздуха, подаваемого в контактную камеру:
Qвозд=n∙L∙qуд,
где n – число барбатеров в контактной камере, n=1; L – длина барбатера, L=1 м; qуд – удельная интенсивность аэрации, принимаем 3 м3/ч∙м2
102

Qвозд=1∙1∙3=3 м3/ч
Необходимое количество воздуха для подачи в резервуар усреднитель и контактную камеру:
Qобщ=Qуср+Qконт=30+3=33 м3/ч
Подбираем воздуходувку марки ВК-1,5, имеющую следующие характе-
ристики: |
|
– объем подаваемого воздуха, м3/ч |
90 |
– давление нагнетания, МПа |
0,05-0,16 |
– частота вращения, об/мин |
1500 |
– мощность электродвигателя, кВт |
5,5 |
– длина, мм |
1250 |
– ширина, мм |
1320 |
– высота, мм |
1020 |
Вертикальный отстойник
В технологической схеме электрообработки осадка предусматривается вертикальный отстойник, т.к. установка имеет производительность 24 м3/сут и работа сооружений не круглосуточная.
Отношение диаметра вертикального отстойника к высоте зоны осаждения принимаем D/H=1,5.
Площадь поперечного сечения зоны осаждения отстойника:
F=β∙Qчас/3,6∙vp∙N,
где Qчас – часовой расход осадка, м3/час; vр – расчетная скорость восходящего потока воды, vp=0,6 мм/с; N – расчетное количество отстойников; β – коэффициент для учета объемного использования отстойника при D/H=1,5; β=1,5
F=1,5∙1,5/3,6∙0,6∙1=1 м2
Диаметр отстойника:
D = |
|
F × 4 |
= |
|
1 |
× 4 |
= 1,1м |
|
π |
|
π |
|
|||
|
|
|
|
|
|
Принимаем диаметр отстойника 2 м.
Принимаем трубопровод для сбора осадка d=200 мм. Тогда высота конической части (осадочной) отстойника при угле наклона стен к горизонтали 50° составит:
hк=(D-d)/2∙tg(90-50)=(2-0,2)/2∙0,84=0,8 м
Объем конической осадочной части:
103
Wос=π/3∙hк[(D/2)2+(d/2)2+D/2∙d/2]=3,14/3∙0,8[(2/2)2+(0,2/2)2+2/2∙0,2/2]==0,4 м3
Период действия между сбросами осадка:
Т=Wос∙N∙δ/Qчас∙(Сср-m),
где Wос – объем конической осадочной части, м3; N – количество отстойников; δ – концентрация уплотненного осадка, г/м2, при концентрации взвешенных веществ Сср=400-1000 мг/л; δ=50 000;
Сср – 590 мг/л
где m – содержание загрязнений на выходе из отстойника, m= 40 мг/л.
Т=0,4∙1∙50 000/1,5∙(590-40)=22,4 ч ≈ 1 сут.
fкж=qсек/0,6=0,025/0,6=0,04 м²
Для сбора воды устраивается периферийный желоб. Расчетная скорость движения воды в желобе v0= 0,6 м/с.
Принимаем желоб с поперечным сечением 0,2х0,2.
При диаметре отверстия d0=20 мм его площадь составляет fо=0,000314 м2 количество отверстий:
n0=0,04/0,000314=10 шт.
Периметр стенки кольцевого желоба Р=4,14 м, шаг отверстий:
l0=Р/n0=4,14/10=400 мм.
Резервуар для сбора осадка
Из отстойника осадок подается на хранение в специальную емкость, откуда часть его поступает на рециркуляцию для очистки маслоэмульсионных сточных вод, а часть – на механическое обезвоживание.
Объем резервуара определяется исходя из времени хранения осадка, его расхода и необходимой дозы для рециркуляции при очистке МЭС (Dос=0,5
г/л).
Объем резервуара:
V=qчас∙Т/8
где qчас – часовой расход осадка, м3/час; Т – время хранения осадка в резервуаре, ч.
104
V=1,4∙16/8=28 м3
Принимаем высоту резервуара для сбора осадка 1,5 м, тогда его длина L=5 м, а ширина В=4 м.
Вакуум-фильтр
Осадки производственных сточных вод в данном случае не требуют предварительной обработки их перед механическим обезвоживанием, т.к. состоят в основном из коагулированных гидроокисей металла (Аl).
Расчет вакуум-фильтра производится по сухому веществу:
Мсух=Wупл∙(100-Вл)∙gос/100
где Вл = 94% – влажность уплотненного осадка; gос = 1,1 т/м3 – объемный вес осадка; Wупл – 40% от общего объема осадка (не подаваемого на рециркуляцию).
Мсух=8,96∙(100-94)∙1,1/100=0,59 т/сут
Требуемая площадь вакуум-фильтра:
F=Мсух∙1000/Т∙к
где Т – число часов работы в сутки; к=20 кг/м2×ч – нагрузка на 1 м2 поверхности вакуум-фильтра
F=0,59∙1000/16∙20=1,8 м2
Принимаем 1 вакуум-фильтр марки БОУ-5-1,75. Его технические характеристики:
Площадь поверхности фильтрования, м2 |
5 |
Диаметр барабана, мм |
1762 |
Длина барабана, мм |
960 |
Число оборотов, об/мин |
0,13-2 |
Объем жидкости в корыте, л |
1300 |
Мощность электродвигателя привода, кВт, барабана |
1,1 |
Габаритные размеры, мм |
2680х2410х2650 |
Масса: фильтра с приводами, кг |
4990 |
Наиболее тяжелого монтируемого узла(барабана), кг |
2645 |
Производительность вакуум-насосов:
Wв.н.=N∙n∙0,5=1,1∙1∙0,5=0,55 м3/мин
105
Расход сжатого воздуха:
Wсж.в.=N∙0,1∙n=1,1∙0,1∙1=0,11 м3/мин
Количество осадка (кека) после вакуум-фильтрации, м3/мин:
Vкека=Vуп∙(100-Wуп)/(100-Wкека),
где Wуп – влажность уплотненного осадка, Wуп=78-80%
Vкека=8,96∙(100-94)/(100-80)=2,7 м3/сут
Составление технологических схем очистки воды и обработки осадка промпредприятий
На основании результатов проведенных экспериментальных исследований на натурных маслоэмульсионных стоках завода и модельных стоках, составленных на базе используемых заводами эмульсолов, разработана технологическая схема очистки охлаждающей жидкости (рис. 15). Очистные сооружения предназначены для сбора отработанной эмульсии и промывных щелочных вод, разрушения эмульсии, очистки стоков, сбора и обработки первичного и вторичного маслосодержащего осадков.
Всостав очистных сооружений входят: 2 резервуара для приема эмульсии (прямоугольные с пирамидальным дном α=570, W=15 м3); 2 резервуара для приема щелочной промывной воды и вод второй промывки (W=18 м3); 2 резервуара для приема стоков 3 и 4 промывки (W=18 м3); 2 резервуара для хранения очищенной воды( W=18 м3); 2 напорных пластинчатых электролизера первой ступени (Q=5 м3/ч); отстойник (вертикальный цилиндрический D=2 м, W=11 м3 с коническим дном α=450 ); 2 напорных пластинчатых электролизера второй ступени (Q=5 м3/ч); флотатор заводского изготовления (Q=5 м3/ч ); напорный фильтр доочистки ФОВ-1,0-6 с зернистой загрузкой; баки для хранения кислоты и щелочи (W=1×2 м3); 2 бака для сбора пены( W=0,85 м3); резервуар для обработки первичного осадка, W=15 м3); 2 резервуара для обработки вторичного осадка в щелочном и кислотном режиме( W=15 м3); резервуар для раствора регенерированного коагулянта (W=2×2=4 м3); бак для хранения флокулянта (W=0,25 м3); бак раствора щелочи (W=0,8 м3); 2 ванны для электролиза раствора (W=1×2=2 м3); 3 резервуара для извлечения ионов меди из очищенной от эмульсии воды и вод травления (W=18 м3).
Всистеме обработки осадка предусмотрены бак для хранения маслоотходов W=1 м3 и эмалированный реактор W=1,3 м3 с мешалкой, W=1,6 м3 для утилизации маслоотходов.
Два насоса марки Х-50-32-125/2-К Q=8 м3/ч, Н=18 м с электродвигателем 4А9012 N=3 кВт, n=2900 об/мин предназначены для подачи предвари-
тельно разрушенной и подкисленной эмульсии на очистку в электролизеры первой ступени.
106
Насос химический, консольный, двухступенчатый, установленный в комплекте флотатора, служит для насыщения воды воздухом, а также для промывки фильтров, трубопроводов и емкостей, марки Х-8/60–2–А, Q=8 м3/ч, Н=60 м с электродвигателем 4А160С2 N=15 кВт, n=2900 об/мин.
Насос пековой марки П 12,5/12,5 Q=12,5 м3/ч, Н=12,5 м с электродвигателем 4А1100С4 N=3 кВт, n=1450 об/мин служит для перекачки жидких шламов.
Комплект вихревых насосов с корпусом из чугуна марки ВК 2/26, Q=7,2 м3/ч, Н=26 м и три насоса ВК 1/16, Q=3,6 м3/ч, Н=16 м предназначены для перекачки растворов, осадка и дренажных вод.
Три насоса вихревых с корпусом из нержавеющей стали ВК 1/16 НЖ Q=3,6 м3/ч, Н=16 м предназначены для перекачки кислых растворов и осадков.
Насосы–дозаторы НД 2,5–16/63–14А установлены для дозировки кислоты и флокулянтов. Насос-дозатор НД 2,5-40/25К–14А-для перекачки щелочи.
Источником питания электролизеров служат реверсивные выпрямительные агрегаты ТВР 1−1600/24 Т−09 ХЛЧ, на ток 1600 А, U=12-24 В в количестве 4-х штук.
Описание работы установки для очистки МЭС и обработки осадка.
Отработанные мыло-маслянные и синтетические эмульсии поступают в приемный резервуар 1, состоящий из 2 емкостей V=15 м3 каждая, где происходит раскисление до рН=4.
Вода от первой промывки раствором щелочи централизованной системы или нейтрализационные растворы поступают в резервуар 2, состоящий из емкости V=18 м3, где раскисляется кислотой до рН=4.
Пена из резервуара 1 и 2 отводится в резервуар для ее сбора, там раскисляется до рН=2 и разделяется на масло, эмульсию и жидкие отходы. Промывные воды 2, 3, 4 промывок централизованной системы подаются в емкости 3, 4, 5, V=18 м3 каждая, емкости 1 и 2 выполнены из нержавеющей стали, емкости 3, 4, 5 из черного металла. Первично обработанная эмульсия и промывные растворы в смеси 1:1 насосом подаются на напорные электролизеры пластинчатого типа первой ступени (один рабочий и один резервный) с рабочей площадью анодов Fан=11,8 м2, корпус которых выполнен из нержавеющей стали. После электролизера жидкость подщелачивается до рН=7–7,5, смешивается в трубчатом смесителе и поступает в камеру хлопьеобразования, встроенную в вертикальный отстойник D=2 м. Перед камерой хлопьеобразования осуществляется ввод флокулянта, в качестве которого может быть использован полиакриламид или активированная кремниевая кислота.
Осветленная вода из отстойника самотечно поступает на вторую ступень электрокоагуляции. Принято два напорных электролизера с рабочей площадью анодов 11,8 м2 (один рабочий и один резервный) с корпусом из черного металла.
107
После электролизера второй ступени жидкость поступает в камеру хлопьеобразования напорного флотатора. Затем обработанная вода проходит две камеры флотации и направляется в сборный лоток, откуда насосом перекачивается на доочистку на напорные фильтры с зернистой загрузкой из дробленого керамзита с эквивалентным диаметром 1–1,2 мм.
Очищенная вода собирается и хранится в двух резервуарах чистой воды и резервуарах 3 и 4 промывки V=18 м3 каждый.
Из резервуара чистой воды вода насосом подается на технические нужды и для промывки фильтров. Загрязненная вода от промывки фильтров отводится в резервуар 2.
Твердый осадок из емкостей 1 и 2 взмучивается и насосом перекачивается в резервуар для обработки твердого осадка, где раскисляется кислотой до рН=2 и разделяется на масло, эмульсию, жидкие и нерастворимые отходы. Масло из резервуаров обработки пены и твердых отходов собирается в емкость для сбора масла. Эмульсии перекачиваются в резервуар 1, жидкие отходы отводятся на утилизацию.
Маслосодержащий осадок из отстойника и флотатора перекачивается в резервуар V=15 м3, где обрабатывается раствором NаОН до рН=11 и разделяется на регенерированный раствор и осадок. Регенерированный раствор коагулянта в виде NаАlО2 отводится в резервуар и повторно используется путем дозированного ввода его перед первой ступенью электрокоагуляции. Осадок перекачивается в резервуар V=15 м3 для второй ступени обработки раствором серной кислоты до рН=1,5–2. Выделившееся масло собирается в резервуар для сбора масла, шлам направляется на захоронение, раствор, содержащий сульфат меди, на обработку в гальванические ванны. Все баки для приема и обработки эмульсии, осадка и пены выполняются из нержавеющей стали, а также баки для хранения флокулянта и расходные баки кислоты и щелочи при флотаторе выполняются из нержавеющей стали. Из черного металла выполнены резервуары промывной воды 3 и 4 промывки, РЧВ, вертикальный отстойник, электролизер второй ступени и флотатор.
На рис. 15. представлена технологическая схема очистки отработанной смазочно-охлаждающей жидкости (СОЖ).
На рис. 16 представлена технологическая схема регенерации смазочноохлаждающей жидкости (СОЖ).
108
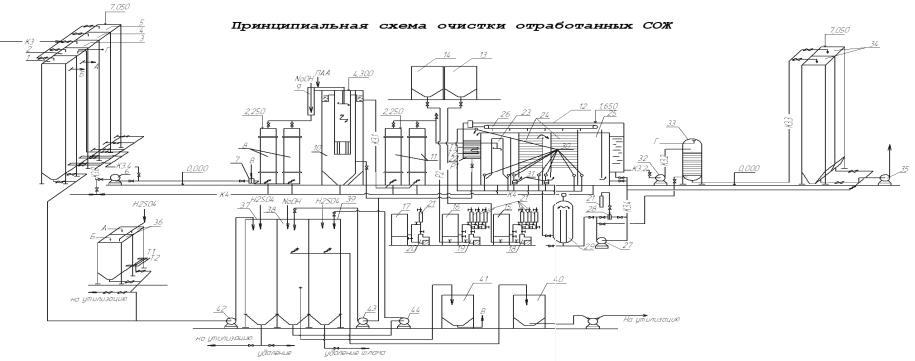
Рис. 15 – Резервуар приема эмульсии; 2,3,4,5 – резервуары приема вод 1 – ой, 2 – ой,3 – ой, 4 – ой промывки; 6 - насосы подачи стоков на очистку; 7 - эжектор для ввода регенерированного раствора коагулянта; 8,11 – электролизеры 1 – ой и 2 – ой ступени; 9 – трубчатый смеситель; 10 – вертикальный отстойник; 12 – флотатор напорный; 13 – бак хранения кислоты, 14 – бак хранения щелочи; 15 – расходный бак кислоты; 16 - расходный бак щелочи; 17 – расходный бак флокулянта; 18 – насос дозатор кислоты; 19 – насос дозатор щелочи; 20 – насос дозатор флокулянта; 21 – расходомеры-ротаметры; 22 – сборный карман для флотирования отходов; 23 – смесительная камера; 24 – флотационные камеры; 25 – отстойная камера; 26 – скребковый механизм; 27 – рециркуляционный насос; 28 – водовоздушный эжектор; 29 – напорный бак; 30 – распределительный трубы; 31 – диафрагмы; 32 – насос подкачки; 33 – напорный фильтр доочистки; 34 – РЧВ; 35
– насосы технической воды; 36 – резервуары для сбора пенного продукта; 37 – резервуар для обработки осадков из резервуаров 1 и 2; 38, 39 – резервуар для обработки маслосодержащих жидких отходов 1 и 2 ступени; 40 – резервуар для сбора масла; 41 – резервуар для сбора раствора регенерированного коагулянта; 42 – насос для перекачки осадков из резервуаров 1 и 2; 43,44 – насосы для жидких маслосодержащих отходов 1 – ой и 2 – ой ступени;К3 – трубопровод подачи отработанных эмульсий и растворов; К3.0 – трубопровод подачи стоков на очистку; К3.1, К3.2 – трубопровод стоков после 1-ой и 2-ой ступени очистки; К3.3 – трубопровод очищенной воды; К3.4 – трубопровод рециркуляции; К4 – трубопровод опорожнения; Р1,Р2 – трубопроводы кислоты и щелочи; Т1,Т2 – теплопровод подающий и обратный
109
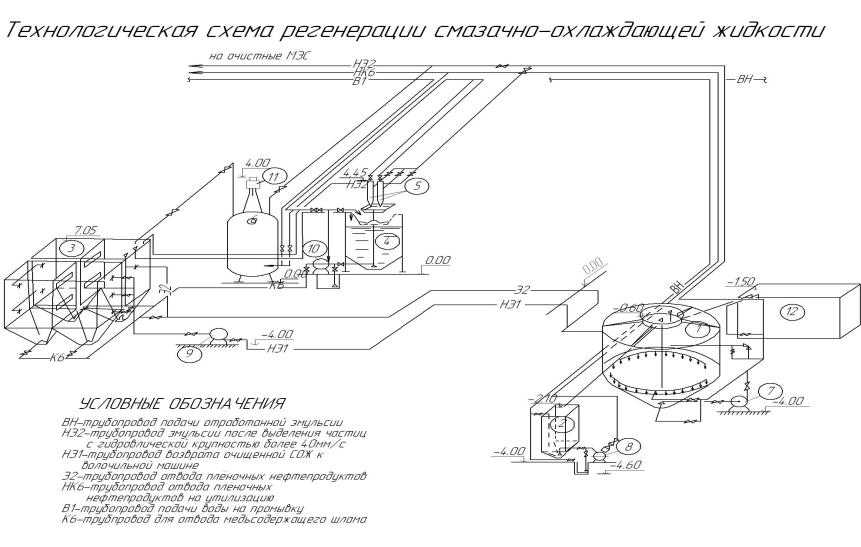
Рис.16. 1−резервуар для сбора эмульсии; 2−бак для сбора плавающих веществ; 3−расходный резервуар эмульсии; 4−резервуар для сбора шлама; 5−гидроциклон; 6−фильтр с плавающей загрузкой; 7−насос центробежный консольный; 8.9.10−насосы вихревые самовсасывающие; 11 – мотор – редуктор мешалки фильтра; 12−запасной резервуар для сбора пленочных масел.
110
Описание работы схемы
Отработанная эмульсия от волочильных машин по самотечному трубопроводу 200мм поступает в сборный резервуар 1, откуда насосом 7 забирается из конической сети и направляется на регенерацию. Продукты разрушения эмульсии в виде пленочных масел выплывают на поверхность и периодически с поднятием уровня эмульсии в баке за маслосборной воронкой, отводятся в сборный бак 2. Маслоотходы из сборного бака 2 и дренажные замасленные воды перекачиваются насосом 3 на очистные сооружения МЭС. При переполнении бака 1, через трубопровод перелива эмульсия отводится в существующий бак W=35 м³. Для предотвращения выпадения и накапливания осадка в конусной части бака X, от напорного трубопровода насоса 7 предусмотрены отводы к системам принудительного смыва осадка со стенок конуса и система взмучивания осадка бака 1. При повышении давления в напорном трубопроводе более 6,00 атм. эмульсия возвращается в приемный резервуар через предохранительный клапан в систему смыва осадка. Избытки эмульсии могут быть пропущены в существующий резервуар объемом 35м3. Для разжижения масла в бак 2 добавляется раствор щелочи. Перемешивание раствора в баке 2 и взмучивание осадка в дренажном приямке предусматривается сжатым воздухом.
Так как среднечасовое потребление эмульсии волочильными машинами составляет 15–20 м³/час, а объем регулирующих емкостей равен 18 м3, система оборота эмульсии в среднем равна 7 г/час. При этом постоянная работа регенерационной установки становится необязательной. Крупные включения медной стружки могут быть успешно выделены путем отстаивания в расходном резервуаре 3, а медная пыль и продукты разложения эмульсии могут выделяться периодически по мере их накопления в системе.
Таким образом, эмульсия, поступающая по напорному трубопроводу Д125мм на участок регенерации, может приниматься по трем вариантам.
I вариант: Работа сооружений в режиме очистки эмульсии.
Эмульсия поступает на 2 гидроциклона (5) работающих параллельно, где при производительности 3 м3/час выделяются частицы включений с гидравлической крупностью более 40 мм/с. Затем проходят напорный фильтр с плавающей загрузкой ФПЗ (б), где очищаются от пленочных нефтепродуктов и тонкой металлической меди. Механически очищенная эмульсия поступает в расходный резервуар (3), откуда насосами (9) по напорному трубопроводу Д125мм подается к волочильным машинам.
Шлам от гидроциклонов (6) отводится в сетчатый контейнер резервуара для сбора шлама (4). В контейнере задерживается частицы размером более 0,5мм и в том числе медная стружка, в резервуаре (4) сохранится часть моющего раствора или специально вводятся раствор каустической соды. Насосом (10) создается рециркуляция раствора в баке (4) для отмывки от масла сетчатого контейнера и медной стружки задержанной им. Тем же раствором периодически промываются гидроциклоны (5) для отмывки их внутренней поверх-
111
ности шламового патрубка от возможных отложений масла. Взмучивание такого осадка осевшего в призматическом днище резервуара (1) предусматривается сжатым воздухом.
Регенерация фильтра ФПЗ предусматривается моющим раствором каустической соды, для отмывки загрузки промывным раствором предусмотрена мешалка (II) с электроприводом и редуктором. Промывная вода от Фильтра насосом (10) перекачивается на очистные сооружения МЭС. Контейнер с отмытой медной стружкой вынимается из резервуара (4) с помощью тали, подается на отметку + 0,00, где выгружается и очищается. Промывка фильтрующей загрузки осуществляется с помощью насоса (14), а загрязненная промывная вода поступает в приемные баки от куда насосом подачи отправляется на очистку (очистные сооружения).
II вариант: Работа сооружений в режиме циркуляции рабочей эмульсии.
Эмульсия, минуя гидроциклон и фильтр, подается сразу в расходный резервуар (3), который выполнен из двух последовательно соединенных емкостей и состоит из 4х секций обеспечивающих каскадное движение эмульсии через него. Общее расчетное время пребывания эмульсии в резервуаре до 1 часа, обеспечивает возможность введения крупных включений, в том числе медной стружки, а также всплывание пленочных масел в первой и второй секции резервуара. В периоды
остановки системы подачи СОЖ (в ночное время, выходные и праздничные дни) в резервуаре возможно глубокое оседание (разделение) тонкого осадка и пленочных масел. Перед запуском системы в работу необходимо насосом (10) откачать осадок из бункеров резервуара (3) в резервуар шлама (4) с подачей осадка через сетчатый контейнер. Плавающие масла из резервуара (3) через переливную воронку самотечно отводится в резервуар
(4).
III вариант: Работа сооружений регенерации эмульсий в режиме с байпасом.
По этому варианту 20–50 % эмульсии подается в один из гидроциклонов и очищается (вариант I), остальная эмульсия направляется в расходной резервуар (вариант II). Вследствие высокой оборачиваемости эмульсия пройдет очистку 2–4 раза в сутки без перегрузки системы реконструкции.
Оптимальное соотношение подачи эмульсии на регенерацию и рециркуляцию устанавливается в процессе эксплуатации.
На рис. 18 показана технологическая схема локальной установки гальванокоагуляционной обработки хромсодержащих сточных вод.
112
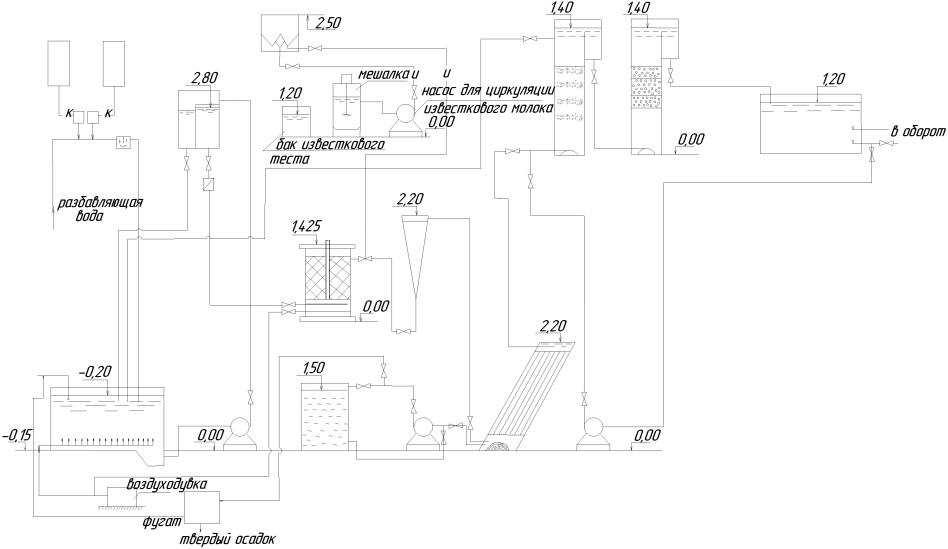
Рис. 17. Технологическая схема локальной установки гальванокоагуляционной обработки хромсодержащих сточных вод.
113
Описание технологической схемы локальной установки производительностью 5 м3/сут для гальванокоагуляционной очистки хромсодержащих промышленных стоков.
Основные элементы установки: отстойник (тонкослойный), гальванокоагуляторы, резервуар-усреднитель, фильтры с плавающей загрузкой и сорбционные фильтры. Из расходного бака−усреднителя насосом ВКС-16 в стоки подаются в регулирующий бак, избыток расхода через переливную трубку возвращается в расходный бак. Из регулирующего бака через расходомер УВ вода поступает в гальванокоагуляторы, где образуются ионы железа, при растворении стружки, за счет образования гальванической пары, после этого вода поступает в камеру хлопьеобразования, перед входом в которую устроен суженный участок для ввода щелочного реагента (для корректировки рН). Из камеры хлопьеобразования вода подаётся на отстойник, затем поступает на первую ступень фильтрации через плавающую, пенополистирольную загрузку, после чего на сорбционные фильтры. Очищенная жидкость отводится в резервуар чистой воды. Сточные воды перед поступлением в гальванокоагуляторы подкисляются раствором H2SO4 до рH=2. Перед камерой хлопьеобразования проводится подщелачивание до рН=7,8.
МОДУЛЬ 4 «Комплексное использование различных методов в схемах очистки промышленных сточных вод и обработки осадка»
Восьмое практическое занятие Составление схемы компактно блочной установки – 0,084(3 час)
На основании результатов эксперимента разработана технологическая схема установки для очистки сточных вод, содержащих трудноокисляемые органические вещества представленная на рис.18, где осуществлено комплексное использование различных методов.
Процесс очистки сточных вод осуществляется следующим образом: сточная жидкость поступает в резервуар-усреднитель (1), пройдя грубую решетку (2), насосом (3) подается на очистку в электролизер-коагулятор (4) первой ступени, содержащий алюминиевые (5) и графитовые (6) электроды, из которого поступает на виброфильтр (13) для первичного отделения осадка, затем, пройдя электрокоагулятор (7) второй ступени с растворимыми анодами, дочищается и обеззараживается в фильтрах (8,9,10,11) первой, второй, третьей и четвертой ступени, которые загружены на первой (8) и третьей (10)- дробленым керамзитом, второй (9) и четвертой (11) – активированным углем; глубокая очистка и обеззараживание стоков осуществляется путем озонирования в теле фильтра второй (9) и четвертой (11) ступени, озон подается из озонатора (14). Задержанный виброфильтром (13) осадок уплотняется на вибро-
114
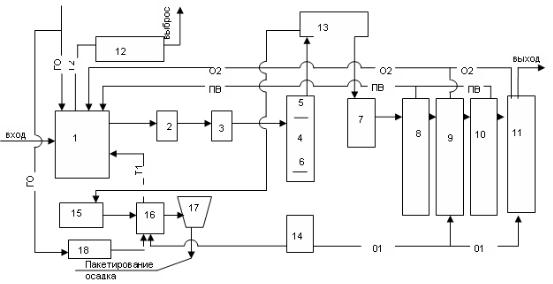
уплотнителе (15) и подается в барабанную сушилку-дробилку (16),высушивается с помощью электрокалорифера (18) и отводится на пакетирование (17).
Рис.18. Технологическая схема очистки сточных вод, содержащих трудноокисляемые органические загрязнения 1- резервуар-усреднитель, 2 – решетка, 3 – насос, 4 – электрокоагулятор 1 ступени, 5 - электрокоагулятор первой ступени, содержащий алюминиевые электроды, 6 - электрокоагулятор первой ступени, содержащий графитовые электроды, 7 - электрокоагулятор второй ступени с растворимыми анодами, 8,9,10,11 - фильтры первой, второй, третьей и четвертой ступени, 12 – вентилятор,13 – виброфильтр, 14 - озонатор, 15
– виброуплотнитель, 16 - барабанная сушилка-дробилка, 17 – пакетирование, 18 – электрокалорифер
Расчет установки для очистки сточных вод содержащих трудноокисляемые органические вещества Резервуар – усреднитель
При необходимости усреднения состава и расхода сточных вод надлежит предусматривать усреднители. Принимаем барботажный тип усреднителя с учетом характера концентраций загрязняющих веществ, а также вида и количества взвешенных веществ. Число секций усреднителя необходимо принимать не менее двух, причем обе рабочие. В усреднителях с барботированием при наличии в стоках легколетучих ядовитых веществ следует предусматривать покрытия и вентиляторную систему.
Объем резервуара – усреднителя, м3
W = |
Q × 1,8 |
× T = |
6 × 1,8 |
× 24 = 10,8м3 |
|
24 |
|
24 |
|
где T – количество часов в смену, T = 24 ч, Q – расход, Q = 6 м3/сут Высота усреднителя, м
Принимаем конструктивно H = 1,5 м Ширина усреднителя, м
115
B = 2 × H = 2 × 1,5 = 3 м
Длина усреднителя, м
L = |
W |
= |
10,8 |
= 2,4 м |
|
B × H |
3× 1,5 |
||||
|
|
|
Удельный расход воздуха, м/с
υ д = k × u 0,5
где k – коэффициент, зависящий от вида частиц, для структурной части k = 6; u = 0,3 – хлопьевидный осадок υ ä = 6∙0,30,5=3,3 мм/с = 0,0033 м/с
qуд = υ 2д / 6,25× д × H
где υ ä – скорость, υ ä = 0,0033 м/с;
qуд = (0,0033)2/6,25∙9,81∙1,5 = 15,7 м3/2∙м
Длина барбатера, м
L6 = L – 0,2 = 2,4 – 0,2 = 2,2 м
Общий расход воздуха, м3/ мин
Q = N∙Lб∙qуд
где N – число барботеров, N = 1
Q = 1∙2,2∙15,7=34,54 м3/ч = 0,57 м3/мин
По полученному расходу воздуха подбираем воздуходувку: Марка машины BK15.
Объем всасываемого воздуха 1,5 м3/мин = 90 м3/ч Давление нагнетания 0,05 – 0,18 МПа Частота вращения 1500 об/мин Мощность электродвигателя 5,5 кВт Размеры агрегата (с воздухосборниками)
Длина 1250 мм; ширина 1320 мм; высота 1020 мм
Виброфильтр
Данный фильтр служит для удаления из воды плавающих и взвешенных примесей.
116

Общая площадь фильтрации
F = |
Qсут |
Tυ pH - 3,6 × n × w × t1 - n × t2 × υ pH |
где T = 8 ч – время работы станции, υ pH = 10/25 л/с ; м2 – скорость фильтрования при нормальном режиме; n = 1 – число промывок фильтра за сутки; w = 14 л/(с∙м2) – интенсивность промывки; t2 = 0,33 ч – простой фильтра в связи с промывкой; t1 = 6 мин продолжительность промывки
F = |
|
|
10,8 |
= 0,185 |
м2 |
|
8 |
× 10 |
- 3,6 × 1× 14 × 0,1 - 1× 0,33 × 20 |
||||
|
|
|
Число фильтров
N = 12 F = 12
0,185 = 0,215
Принимаем 1 фильтр Площадь сетки фильтра
f = |
F |
= |
0,185 |
= 0,185 м2 |
||||
|
1 |
|||||||
|
N |
|
|
|
|
|
||
Потери напора при промывке фильтра |
|
|
|
|
|
|||
|
h = |
ε × C o× |
p × υ |
c |
2 |
|
|
|
|
2 |
|
|
|
|
|||
|
|
|
|
|
|
|
|
|
гдеε = f (Re c ) – коэффициент потерь, υ c = |
υ 1 |
– скорость движения воды в |
||||||
|
||||||||
|
|
|
|
|
A |
ячейках сетки. Для сетки № 0071 Ao = 31,4%, a = 0,055 мм, N=800 – проволок на 12 м.
Характерный линейный размер в числе Рейнольдса для сетки №0071
L = |
A |
= |
31,4 |
= 0,14 |
|
|
|||
c |
2π N |
|
2 × 3,14 × 35,6 |
|
|
|
|
Число Рейнольдса для температуры воды 10oC (ν = 1,31 сСт при 1 сСт = 11 м3/с)
Rec = |
υ 1 × Cc |
= |
10 × 0,14 |
|
= 0,34 4 |
|
A × ν |
31,4 × 1,31 |
|||||
|
|
|
117

При Rec = 0,34 |
ε Co = |
6,4 |
= 18,8 |
|
|
|
|
|
|
|
0,34 |
|
|
|
|
|
|
|
|||
|
|
|
|
|
|
|
|
|
|
|
|
|
h = 18,8 × |
102 |
( |
0,03 |
) |
2 |
= 8,4 |
мм |
|
|
|
2 |
0,314 |
|
||||||
|
|
|
|
|
|
|
|
|
Электрокоагулятор
Электрокоагуляторы с алюминиевыми пластинчатыми электродами следует применять для очистки сточных вод.
В соответствии с данными эксперимента:
1.Доза алюминия Дал = 25 мг/л
2.Напряжение на электродах U = 12 В
3.Плотность тока ч = 60 мг/л
4.Выпад алюминия по току г = 100%
Часовой расход Al, который необходимо ввести в обрабатываемую воду:
δ al = Дal × Qч = 25× 1,8 = 45 г / ч
Сила тока, обеспечивающая растворение AL:
У = δKal × 100n = 0,33545 × 100100 = 134,3 A
где K=0,335 – электромагнитный эквивалент
Рабочая поверхность анодов определяется из условий оптимальной плотности тока
f = |
У |
= |
134 ,3 |
= 2,24 м2 |
|
г |
|
60 |
|
Необходимая толщина анодов:
δ = |
Qсут × Д АС × nсут |
= |
10,8 × 25 × 45 |
|
= 0,005 |
м = 5 мм |
||
0,4α |
буга × fa × 106 |
0,4 × 2,69 × 2,24 × |
106 |
|||||
|
|
|
|
где nсут = расчетная продолжительность; α буга – удельный все анодного материала, т/м3
Расход Al в год, при условии изменения полярности электродных пластин
QAl = δ al × t × 1,2 = 45 × 2190 × 1,2 = 118,26 кг
где t – число рабочих часов в год. Принимаем размеры пластин электрода: 0,25x1,19; fэл = 0,2975 м2
118

Общее количество анодов
na = |
fa |
= |
2,24 |
= 8 шт |
|
0,2975 |
|||
|
fэл |
|
Общее количество электродов
n=2∙na+1=2∙8+1=17 шт
В аппарате в соответствии с разработанной конструкцией общее количество электродов 9 из них 5 анодов и 4 катода, следовательно количество аппаратов:
nап = 179 = 2 шт
Принимаем 2 аппарата Ширина электролизера
В=b+2a=0,15+2∙0,016=0,182 м
где b – ширина электрода; a – расстояние между электродом и корпусом электролизера Длина электролизера
L = n × δ + (n - 1)l + 2a = 9 × 0,005 + (9 + 1) × 0,01 + 2 × 0,016 = 0,177 м
где l – расстояние между электродными пластинами. Высота электролизера
H = hэл + а1 + а2 = 1,89 + 0,005 + 0,005 = 1,9 м
где а1 – расстояние от электрода до дна; а2 – расстояние от электрода до поверхности воды; hэл – 1,89 – высота электродной пластины
Объем воды в электролизере
Wb¢ = (H × L × B) - (n × fэл × 0,006) = (1,9 × 0,177 × 0,182) - (9 × 0,2835 × 0,005) = 0,048 м3
Время пребывания воды в электролизере
|
w′ |
|
× |
n |
an |
|
0,048× 2 |
|
|
τ = |
b |
|
|
= |
0,68 |
= 0,14 |
ч |
||
|
|
ч |
|
||||||
|
|
Q |
|
|
|
|
|||
|
|
|
|
|
|
|
|
|
Скорость потока воды в электролизере
υ = Мч = 0,141,9 = 13,5 м / ч
119
Требуемая мощность Е = Y ∙ U
Е = 134,3 ∙ 12 = 1,6 кВт
где U – напряжение (12–24 В) Удельный расход электроэнергии
W = |
JU = |
1,6 |
= 2,37 |
кВт × ч |
|
0,68 |
м3 |
||||
|
Qч |
|
Каркасно – засыпной напорный фильтр
Определение площади фильтра,
F = |
Qсут |
T × υ p.H . - 3,6n(w1 × t1 + w2t2 + w3t3 ) - n × t4 × υ p.H |
где Qсут – производительность фильтра (полезная) в м3/сутки; T – продолжительность работы станции в течение суток в ч; υ p.H . – расчетная скорость фильтрования в м/ч; n – число промывок фильтра в сутки; w1 и t1 – интенсивность в л/сек ∙м2 и продолжительность в ч первоначального взрыхления фильтрующей загрузки; w2 и t2 – интенсивность подачи воды в л/сек· ∙м2 и продолжительность в ч водовоздушной промывки; w3 и t3 – интенсивность в л/сек ·∙м 2 и продолжительность отмывки в ч; t4 – продолжительность простоя фильтра из – за промывки в ч
F = |
|
|
|
|
10,8 |
= 0,146 м2 |
|
8 |
× 10 |
- 3,6 × 1× (8 × 0,017 |
+ |
4 × 0,083 + 8 × 0,034 ) - 1× 0,33 × 10 |
|||
|
|
т.к. F = 0,146 м2, то Дф = 0,21 м
Расчет распределительной системы фильтра: Напорный вертикальный фильтр имеет D = 0,21 м.
Площадь песчаной загрузки фильтра f = 0,146 м2 (в плане). Интенсивность промывки w = 8 л/сек ∙ м2. Общий расход воды на промывке на один фильтр:
дпр = 0,146 × 8 = 1,168 л / сек = 0,0012 м3 / сек
Диаметр стального коллектора распределительной системы напорного фильтра при скорости входа в него промывной воды υ кол = 1,07 м / с будет акол = 20 мм (рекомендуемая скорость 1 – 1,2 м/с).
Режим промывки напорных фильтров следующий: взрыхление загрузки (с интенсивностью 6 – 8 л/с∙м2) 1 мин; водовоздушная промывка (3 – 4 л/сек ∙м2 воды и 20 – 25 л/с ∙м2 воздуха) 5 мин; отмывка водой (6 – 8 л/с∙м2) 2 мин.
120
Отвод промывной воды с напорного фильтра производится при помощи водосборной воронки, D воронки должен быть dв = (0,2/0,25)D, где D – диаметр фильтра. Принимаем dв = 0,042 мм.
Контактно – сорбционный фильтр
Исходные данные:
1.Производительность qw = 10,8 м3/сут = 0,45 м3/ч 2.Начальная величина ХПК (Сеп) = 240/400 мг/л 3.Конечная величина ХПК (Сех) = 50 мг/л
4.Изотерма адсорбции соответствует уравнению Фрейндлиха: аsb в мг/г
с; аsbmin = 253 Cex1/2
5.Линейная скорость относительно стен адсорбера υ 10 м/ч; 6.Ориентировочная продолжительность работы установки до проскока
tадсор = 24 ч
7.Уголь AT – 3, его кажущаяся плотность адsbкаж = 0,9, насыпная адsbнас = 0,45
8.Высота слоя угля на одном адсорбере Hads = 1,5 м. 9.Заданная степень исчерпания емкости сорбента Кsb = 0,7 10.Диаметр адсорбера D = 0,25 м
Максимальная сорбционная емкость asbmax в соответствии с изотермой, мг/г;
asbmax = 253 Cen1/ 2 = 253 × 0,31/ 2 = 138,6 мг / г
Общая площадь одновременно и параллельно работающих адсорберов, м2:
F = qw |
= |
10,8 |
= 0,045 м2 |
|
|
||||
ads |
υ |
|
24 × 10 |
|
|
|
|
Количество параллельно и одновременно работающих линий адсорберов при D=0,25 м:
Nadsb = |
Fads |
= |
0,045 |
= 0,92 =1 |
|
fадс |
3,14 × 0,252 |
||||
|
|
|
Принимаем к работе один сорбционный фильтр при скорости фильтрации 10
м/ч.
Максимальная доза активного угля, г/л (кг/м3):
Dmax = |
Cen − Cex |
= |
300 − 50 |
= 4,42 кг / м2 |
|
|
|||
sb |
asbmin |
|
253× (0,05)1/ 2 |
|
|
|
|
Доза активного угля, выгружаемого из адсорбера, г/л (кг/м3):
121
Dsb = |
Cen − Cex |
= |
300 - 50 |
= |
2,58 кг / м |
3 |
|
Ksb × asbmax |
0,7 |
× 138,6 |
|
||||
|
|
|
|
|
Ориентировочная высота загрузки, обеспечивающая очистку, м:
op |
|
Dsbmax × qw × tadsop |
|
4,42 × 0,45× 24 |
|
|
||
H2 |
= |
|
= |
|
|
= 2,357 |
м |
|
Fads × адsbHac |
0,045 |
× 450 |
||||||
|
|
|
|
|
Ориентировочная высота загрузки, выгружаемая из адсорбента, м:
H1op = |
Dsb × qw × tadsop |
= |
2,58 × 0,45 × 24 |
= 1,376 м |
|
Fads × адsbHac |
0,045 × 450 |
||||
|
|
|
Высота слоя отработанного адсорбента, выгружаемого из адсорбера, принимается равной загрузке одного адсорбера H = 1,5 м
Продолжительность работы адсорбера до исчерпания емкости, ч:
t2ads = |
2 × C |
|
× K |
|
× H ε (amax |
+ C |
|
) |
= |
2 × 0,3× 1,5 × 0,5(138,6 + 0,3) |
= 63,14 |
ч |
||
|
en |
|
sb |
1 |
sb |
|
en |
|
11× |
0,32 |
||||
|
|
|
|
|
υ C 2en |
|
|
|
|
|
|
|
Произведем расчет объема загрузки одного адсорбера, м3:
Wsb = fads × H ads |
= 3,14 × |
0,252 |
× 1,5 = 0,29 м2 |
|
|
4 |
|
Сухой массы угля в адсорбере, кг:
psb = wsb × адsbhac = 0,29 × 450 = 130,5 кг
При перезагрузке адсорбера затраты угля составят:
Ssb = |
Wsbo |
= |
130,5 |
= 2 кг / ч = 0,002 т / ч |
|
t2ads |
63,14 |
||||
|
|
|
что соответствует дозе угля, г/л:
Dsb = |
Ssb |
= |
0,002 |
= 0,004 |
г / л |
|
qw |
0,45 |
|||||
|
|
|
|
Очищенная вода с необходимой и достаточной степенью очистки поступает в резервуар чистой воды (РЧВ). Объем РЧВ = 10,8 м3. Объем РЧВ обеспечивает объем воды для промывки фильтра Qпром = 1,2 л/с, которая осуществляется через 24 часа. Отвод очищенной воды из резервуара чистой воды осуществляется с поверхности воды через переливную трубу, снабженную
122
приемной воронкой dу = 200 мм, установленной на отметке 0,35 м, трубопроводом очищенной воды dу = 100 мм.
Библиографический список
1.Яковлев С.В. Водоотведение и очистка сточных вод / С.В. Яковлев, Я.А. Карелин, Ю.М. Ласков, В.И. Калицун. // М.: Стройиздат, 1996.
2.Яковлев С.В. Водоотводящие системы промышленных предприятий / С.В. Яковлев, Я.А. Карелин, Ю.М. Ласков, Ю.В. Воронов. // М.: Стройиздат, 1990.
3.СНиП 2.04.03.-85. Канализация. Наружные сети и сооружения // М.
1986.
4.Справочное пособие к СНиП 2.04.03.– 85. Проектирование сооружений для очистки сточных вод // М.: Стройиздат. 1990.
5.Укрупненные нормы водопотребления и водоотведения для различных отраслей промышленности // М.: Стройиздат, 1982
6.Санитарные правила и нормы охраны поверхностных вод от загрязнений (СанПиН 4630-88) // М.: Минздрав СССР, 1988
7.Правила приема производственных сточных вод в систему канализации населенных пунктов МЖКХ РСФСР. // М.: 1989
8.Правила пользования системами коммунального водоснабжения и канализации в Российской Федерации. // М.: Минстрой РФ, 1995.
123
9.Ласков Ю.М. Примеры расчетов канализационных сооружений/ Ю.М. Ласков, Ю.В. Воронов, В.И. Калицун. // М.: Стройиздат, 1987.
10.Жуков А.И. Канализация промышленных предприятий/ А.И. Жуков, Л.И. Демидов, И.Д. Родзиллер. // М.: Стройиздат, 1987.
11.Алферова Л.А. Замкнутые системы водного хозяйства / Л.А Алферова, Нечаев А.П.. // М.: Стройиздат, 1984.
12.Яковлев С.В. Технология электрохимической очистки воды/ С.В. Яковлев, О.Г. Красноборолько, В.И. Рогов. // Л.: Стройиздат, 1987.
13.Жуков А.И. Методы очистки производственных сточных вод / А.И. Жуков, Н.А. Мангайт, Н.Д. Родзиллер. // М.: Стройиздат, 1976 – 208с.
14.Халтурина Т.И. Водоотводящие системы промышленных предприятий: Тексты лекций. // Красноярск: КрасГАСА.1997. – 145с.
15.Халтурина Т.А. Водоотводящие системы промышленных предприятий: Учеб. пособие // Красноярск: КрасГАСА.2001. – 74с.
16.Справочник проектировщика. Канализация населенных мест и промышленных предприятий. // М.: Стройиздат, 1981. – 639 с.
17.Ласкорин Б.Н. Безотходная технология в промышленности / Б.Н. Ласкорин, Б.В. Громов, А.П.Цыганеков и др., // М.: Стройиздат, 1986
18.Яковлев С.В. Обработка и утилизвция осадков производственных сточных вод / С.В. Яковлев, П.С.Волков, Ю.В. Воронов, В.П. Волков // М.: Химия, 1999
19.Соколов Л.И. Ресурсосберегающие технологии в системах водного хозяйства промышленных предприятий. Учебное пособие./ Л.И. Соколов // М:, АСВ, 1997
20.Иванов В.Г. Водоотводящие системы промышленных предприятий. Конспект лекций / В.Г Иванов, Н.А. Черников // С–Петербург 2007г. 239 с.
21.Халтурина Т.И. Водоподготовка. Расчет станций водоочистки для хозяйственно-питьевых целей: учебное пособие с грифом Мин. образ. / Т.И. Халтурина // Красноярск: КрасГАСА. 2006. – 355 с.
22.Халтурина Т.И. Проектирование и расчет очистных сооружений промышленных предприятий. Метод. указания / Т.И. Халтурина, Б.Ф Турутин. // Красноярск: КИСИ, 1987 46 с.
124
ОГЛАВЛЕНИЕ |
|
ВВЕДЕНИЕ |
3 |
МОДУЛЬ 1 «Водное хозяйство и водоотведение |
|
промышленных предприятий» |
3 |
Первое практическое занятие |
|
Составление балансовых схем водоотведения промышленных |
|
предприятий. Обоснование технологической схемы очистки |
|
производственных сточных вод. Определение необходимой |
3 |
степени очистки сточных вод |
|
МОДУЛЬ 2. «Методы и сооружения для очистки |
|
промышленных сточных вод» |
16 |
Второе практическое занятие |
|
Классификация процессов и методов механической очистки. |
24 |
Расчет решетки, песколовки и нефтеловушки |
|
Третье практическое занятие |
|
Расчет камер хлопьеобразования. Расчет отстойников. Расчет фильтров. Расчет усреднителя
125
Нейтрализация, основные виды химических реакций, |
34 |
используемых для нейтрализации сточных вод. Расчет усреднителя |
|
Четвертое практическое занятие |
|
Расчет флотационной установки |
54 |
Расчет аппаратов электрокоагуляционной очистки |
|
Пятое практическое занятие |
|
Расчет ионообменной установки |
67 |
Расчет фильтра смешанного действия |
|
Шестое практическое занятие |
|
Расчет сооружений биохимической очистки. Технологические |
87 |
схемы сооружений |
|
МОДУЛЬ 3 «Методы и сооружения для обработк |
|
и утилизации осадков промышленных сточных вод» |
96 |
Седьмое практическое занятие |
|
Технологический расчет установки электрокоагуляционной |
|
обработки осадка. Составление технологических схем |
|
кондиционирования осадков. Составление технологических схем |
96 |
очистки воды и обработки осадка промпредприятий |
|
МОДУЛЬ 4 «Комплексное использование различных |
|
методов в схемах очистки промышленных сточных |
|
вод и обработки осадка» |
116 |
Восьмое практическое занятие |
116 |
Составление схемы компактно блочной установки |
|
Библиографический список |
126 |
126