
- •ПРЕДИСЛОВИЕ
- •1. МАТЕРИАЛЫ ТИПОВОЙ РЕАКЦИОННОЙ АППАРАТУРЫ
- •2. ЗАЩИТНЫЕ ПОКРЫТИЯ
- •3. ВЫБОР МАТЕРИАЛОВ ДЛЯ АППАРАТУРЫ
- •4. КОНСТРУКТИВНЫЕ УЗЛЫ
- •4.1. Элементы поверхности теплообмена вертикальных котлов
- •4.2. Гарнитура реакционных аппаратов
- •4.3. Арматура химических установок
- •4.4. Перемешивающие устройства
- •2.2. Аппараты для разделения неоднородных систем
- •2.3. Дробилки и мельницы
- •2.4. Сушилки
- •2.5. Смесители для твердых сыпучих тел
- •Рекомендуемая литература
- •Оглавление
2.3.Дробилки и мельницы
Вхимико-технологических процессах измельчение (диспергирование) твердой фазы производится с целью:
-уменьшения размеров кусков твердых материалов (исходное горно-химическое сырье, обжиг и др.);
-раскрытия зерен чистых включений, входящих в состав сростков перед процес- сами механического обогащения продуктов;
-увеличения свободной наружной поверхности зерен твердого материала перед операциями растворения, экстрагирования, химического взаимодействия, и т.д.
Взависимости от размеров исходного и измельченного материала различа- ют несколько классов измельчения (табл. 6).
Для характеристики измельченного материала используют линейную сте- пень измельчения i = dн /dк; объемную степень измельчения i’ = d3н /d3к; удель- ную поверхность, фракционный (гранулометрический состав), характеристику по верхнему (—d) и нижнему (+d) пределу.
Взависимости от физико-химических свойств материалов существуют че- тыре основных метода измельчения: раздавливанием, раскалыванием, истирани- ем и ударом.
Таблица 6
Классы измельчения
Классизмельчения |
Размер кусков, мм |
|
|
исходных |
полученных |
Дробление: |
|
|
крупное |
1000 |
250 |
среднее |
250 |
20 |
мелкое |
20 |
1-5 |
Помол: |
1-5 |
0,1-0,04 |
грубый |
||
средний |
0,1-0,04 |
0,015-0,005 |
тонкий |
0,1-0,04 |
0,005-0,001 |
коллоидный |
<0,1 |
< 0,001 |
Для крупного и среднего дробления используются щековые, конусные и зубовалковые дробилки. Измельчение в этих дробилках происходит в основ- ном за счет раскалывания и размалывания. Эти аппараты позволяют получить измельченный материал с размером частиц до 20 мм.
Измельчающие машины истирающе-раздавливающего действия - это бегу- ны, гладкие валки. Измельченный материал имеет размер частиц до 40 мкм и ни- же. Для получения более тонкодисперсного материала используются мельницы - барабанные (шаровые, стержневые) и газоструйные. Измельчение материала происходит за счет удара и истирания.
Высокая степень измельчения не может быть получена в одном аппарате или в нескольких аппаратах одной конструкции. Процесс измельчения чаще все- го является процессом многостадийным, и каждой стадии измельчения отвечает своя оптимальная степень измельчения.
88
На практике установлено, что в аппаратах доля крупного и среднего дробле- ния (при кусках более 50 мм), степень измельчения (i) составляет 2-3, для мелкого дробления (от 50 до 5 мм) i = 3-5. При более тонком измельчении i = 6-8. Зная тре- буемую степень измельчения, с учетом указанных конкретных степеней измель- чения, можно определить число стадий процесса измельчения.
Все технологические схемы измельчения должны быть построены так, что- бы сократить степень возможного переизмельчения продукта.
Во-первых, желательно сразу, до начала процесса, удалить из исходного сырья ту его часть, которая представляет собой уже готовый продукт, т.е. все зерна целевой фракции, и уже переизмельченные зерна. Это сократит количест- во измельчаемого сырья и предотвратит неоправданные расходы энергии на пе-
реизмельчение целевого продукта и на бессмысленное дальнейшее измельчение уже переизмельченной фракции. Для этого целесообразно прибегнуть к предва- рительной классификации исходного материала по крупности частиц, на измель- чение должен поступать, по возможности, только недоизмельченный продукт.
Во-вторых, режим измельчения должен быть построен так, чтобы измель- ченный материал не задерживался на длительный срок в измельчительных уста- новках. Тогда полученный продукт не будет доизмельчаться и переизмельчать- ся.
Однако сокращение времени пребывания частиц в измельчающем устрой-
стве делает более вероятным прохождение недоизмельченных частиц через весь аппарат без требуемой степени измельчения. Поэтому из аппарата может выхо- дить продукт со значительным содержанием недоизмельченной фракции. В этом случае на выходе из аппарата необходимо поставить классифицирующее уст- ройство, отделяющее готовый продукт от недоизмельченной фракции. Выде- ленная недо-измельченная фракция будет поступать на повторное измельчение.
Выбор той или иной схемы измельчения (аппаратов для измельчения) зави- сит от следующих факторов:
§физико-химических свойств измельчаемого материала (твердость, хрупкость, налипание, сыпучесть, насыпной вес и др.);
§размера частиц исходного материала;
§степени измельчения;
§степени использования полезного объема измельчительных установок;
§данных по производительности рекомендуемых измельчителей и др.
Измельчители можно разделить на следующие основные группы:
1)раскалывающего и разламывающего действия;
2)раздавливающего действия;
3)истирающе-раздавливающего действия;
4)ударного действия;
5)ударно-истирающего действия;
6)коллоидные измельчители.
Воснову предлагаемой классификации измельчителей положен главный способ, которым в нем измельчается материал.
Измельчители раскалывающего и разламывающего действия:
89
-щековые дробилки;
-конусные дробилки;
-зубовалковые дробилки.
Измельчители раздавливающего действия:
-гладковалковые дробилки;
-ролико-кольцевые мельницы:
-горизонтальные;
-вертикальные.
Измельчители истирающе-раздавливающего действия:
-жерновые мельницы;
-бегуны;
-катково-тарельчатые мельницы;
-шаро-кольцевые мельницы;
-бисерные мельницы.
Измельчители ударного действия:
-молотковые мельницы;
-дезинтеграторы и дисмембраторы;
-центробежные мельницы;
-барабанные мельницы;
-газоструйные мельницы.
Измельчители ударно-истирающего действия:
-вибрационные мельницы;
-планетарные мельницы;
-гироскопические мельницы. Коллоидные мельницы:
-конусные;
-бильные (кавитационные);
-виброкавитационные;
-реактроны.
На рис. 61 показаны шаровые мельницы периодического действия, приме- няемые при перетире паст с металлическими шарами и броней (а) и с керамиче- скими шарами и футеровкой (б).
Особенности мельниц: гладкая поверхность футеровки барабана, наличие
рубашки у мельниц со стальными шарами и установка решетки с отверстиями малых размеров над разгрузочным патрубком для задержания мелющих тел и образующихся при их раскалывании кусков.
При получении пигментных суспензий белых и светлых колеров, а также, когда недопустим примол металла, применяют мельницы с шарами и футеровкой из керамики (фарфора, ультрафарфора, стеатита, уралита и др.). В остальных случаях используют мельницы со стальными шарами. Футеровка мельниц со стальными шарами состоит не из отдельных плит (рис. 61, а), а из съемной ци- линдрической обечайки из листовой стали, вставляемой в корпус мельницы.
Шаровые мельницы периодического действия для диспергирования пигмен- тов в связующих выпускаются емкостью от 0,1 до 8 м3.
90
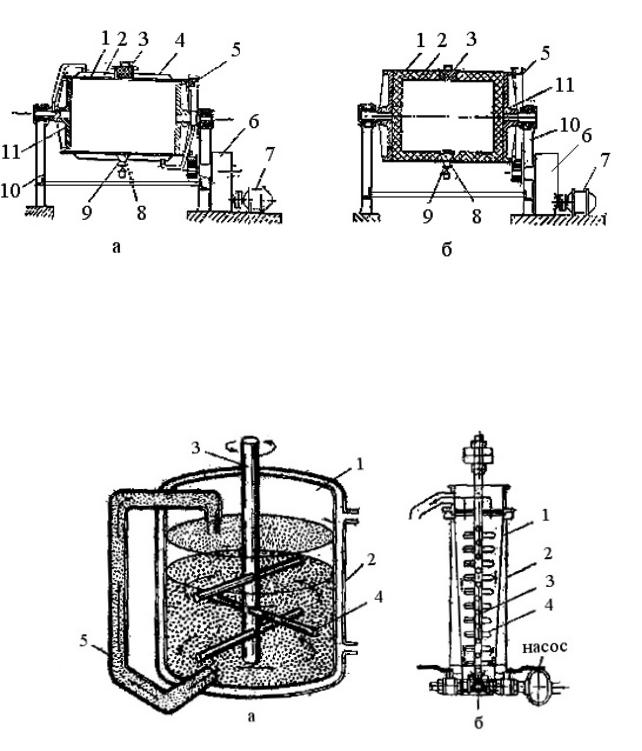
Рис. 61. Шаровые мельницы со стальными (а) и керамическими шарами (б):
1 – корпус; 2 – футеровка; 3 – загрузочный люк; 4 – рубашка; 5 – зубчатый венец; 6 – редуктор; 7 – электродвигатель; 8 – решетка; 9 – разгрузочный патрубок; 10 – стойка; 11 – днище.
Шаровые мельницы с мешалкой, известные под названием Атриторы, вы- пускаются периодического (рис.62,а) и непрерывного действия (рис. 62,б).
Рис. 62. Шаровые мельницы (атриторы) периодического (а) и непрерывного действия (б) с ме- шалками: 1 – корпус; 2 – рубашка; 3 – вал; 4 – лопасти; 5 – циркуляционная труба.
В корпусе мельницы, заполненного шарами, вращается вал с лопастями, рас- положенными по спирали под углом 60 – 90о друг к другу. Длина лопастей со- ставляет ~0,8 радиуса цилиндрического корпуса. При вращении мешалки созда- ется интенсивное движение шаров вокруг движущихся лопастей, а также их ко- лебательное движение при прохождении последних через слой шаров.
На рис. 62, а показана конструкция мельницы периодического действия. Ло- пасти мешалки чаще всего круглые. Скорость вращения мешалки в зависимости
91