
библиотека нефтяника / Бурение скважин / Глава 4
.pdf
Рис. 4.4. Турбобур с полым валом
Как видно из рис. 4.4, турбинные секции состоят из корпуса и полого вала, установленного внутри корпуса на четырех резинометаллических радиальных опорах. В пространстве между корпусом и полым валом установлено около 100 ступеней турбины. Концы полого вала оборудованы конус- но-шлицевыми полумуфтами, внутри которых имеются уплотнительные элементы, предотвращающие утечку бурового раствора из полости вала к турбине. При сборке турбинных секций соблюдаются заданные размеры «вылета» и «утопания» полумуфт для обеспечения необходимого положения роторов относительно статоров.
Шпиндель турбобура состоит из корпуса и полого вала, установленного внутри корпуса на резинометаллических радиальных опорах и упорно-радиальном шариковом подшипнике серии 128 000. При необходимости нижний конец корпуса шпинделя может быть оборудован стабилизатором, при этом на нижний конец вала устанавливается удлинитель, который центрируется внутри стабилизатора резинометаллической радиальной опорой.
При сборке турбинных секций предусмотрена возможность установки стабилизаторов между турбинными секциями или
между турбинной секцией и шпинделем. Для этого на нижнем переводнике турбинной секции на резьбе закрепляется стабилизатор, а на нижнем конце вала – удлинитель соответствующей длины, так, чтобы не изменять ранее отрегулированные присоединительные размеры «утопания» и «вылетов» полумуфт.
Наличие полых валов турбинных секций и шпинделя позволяет осуществлять следующие операции:
поддерживать в насадках долота перепад давлений в 6–9 МПа без дополнительного нагружения буровых насосов;
проводить замеры пространственного положения ствола скважины в непосредственной близости от долота без подъема бурильной колонны на дневную поверхность;
на основании проведенных замеров корректировать осевую нагрузку на долото для управления процессом набора, сброса или стабилизации угла искривления ствола скважины;
прокачивать через полость валов, минуя турбину, разного рода наполнители;
спускать в аварийных случаях в полость вала приборы для определения места прихвата ПО-50 по ТУ 39-020–75 и торпеды, например, ТШ-35,
91
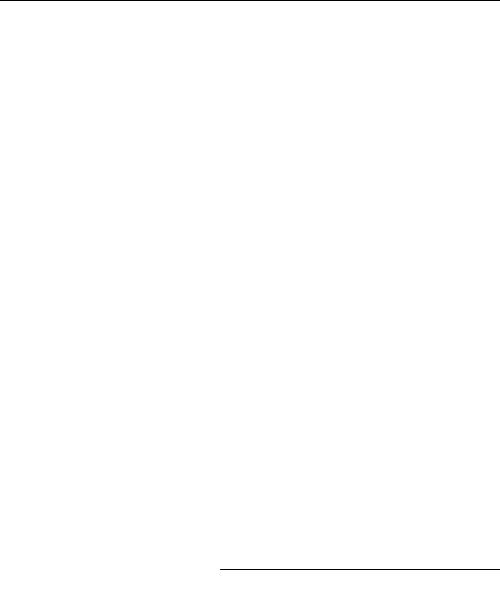
Ò à á ë è ö à 4.6
|
Число сту- |
Расход жид- |
Крутящий |
Частота |
Перепад |
Диаметр долота, |
|
Øèôð òóð- |
вращения |
||||||
пеней тур- |
кости через |
момент при |
давления, |
||||
бобура |
áèíû |
турбину, л/с |
Nmax, Í ì |
ïðè Nmax, |
ÌÏà |
ìì |
|
|
ñ–1 |
|
|||||
ÒÏÂ 240 |
552 |
30 |
2800 |
5,7 |
6,7 |
311; 295,3; 269,9 |
|
À7ÏÂ |
588 |
22 |
1600 |
4,9 |
4,9 |
215,9; 212,2 |
|
ÒÏÂ 178 |
552 |
17 |
1200 |
7,6 |
10 |
215,9; 212,2 |
Ï ð è ì å ÷ à í è å. Nmax – максимальная мощность турбобура. Плотность жидкости – 1000 кг/м3.
ÒØ-43, ÒØ-50 ïî ÒÓ 25-04-2726–75, ÒÓ-25-04-2702–75 èëè ÒÄØ-25-1, ÒÄØ-50-2 ïî ÒÓ 39/5-137–73 è ÒÓ 39/5-138–73;
продавливать буровой раствор и выравнивать его свойства через полый вал с последующим сбросом гидромониторного узла; такая операция позволяет во много раз сократить время для проведения указанных работ.
В табл. 4.6 приведены технические характеристики турбобуров с полым валом.
Турбобур с редуктором-вставкой
Турбобуры с редуктором-вставкой типа РМ предназначены для эффективного использования шарошечных долот с маслонаполненными опорами при технологически необходимом расходе бурового раствора и уменьшенном по сравнению с другими гидравлическими двигателями перепаде дав-
лений.
Маслонаполненный редуктор-вставка (рис. 4.5) применяется в сочетании с турбинными секциями и шпинделем серийно выпускаемых турбобуров.
Редуктор-вставка устанавливается между шпинделем и турбинными секциями, имеет планетарную передачу и систему маслозащиты передачи и опор.
Планетарная передача двухрядная, зубчатая, с косозубым зацеплением Новикова. Система маслозащиты имеет уплотнения торцового типа.
Выходной вал с помощью шлицевой муфты соединен с валом шпинделя, а входной вал с помощью полумуфты – с турбинными секциями.
Редуктор-вставка является автономным узлом, который может быть заменен непосредственно на буровой. Энергетиче-
Рис. 4.5. Герметизированный маслонаполненный шпиндель
92
Ò à á ë è ö à 4.7
Òèï |
Количество |
Расход |
Крутящий момент, Н м |
|
Перепад |
||
турбинной |
турбинных |
жидкости, |
|
|
|
||
предельный |
ïðè Nmax |
давления, МПа |
|||||
секции |
секций |
ë/ñ |
|||||
|
|
||||||
|
|
|
|
||||
ЗТСША-195ТЛ |
1 |
24 |
4826 |
2413 |
|
2,7 |
|
ÇÒÑØ1-195 |
1 |
40 |
4806 |
2403 |
|
3,6 |
|
À7ÒØ |
1 |
30 |
3650 |
1825 |
|
3 |
|
Ï ð è ì å ÷ à í è å. Nmax – |
максимальная |
мощность турбобура. Плотность |
жидкости – |
||||
1000 êã/ì3. |
|
|
|
|
|
|
ские характеристики турбобура с редуктором-вставкой и разными типами турбин приведены в табл. 4.7.
Турбины современных турбобуров
Турбина турбобура является преобразователем гидравлической энергии потока жидкости в механическую энергию вращения вала.
Турбина современного турбобура является многоступенчатой, осевого типа и состоит из системы статоров и системы роторов. Как правило, система статоров связана с корпусом, а система роторов – с валом турбобура.
При постоянном значении расхода бурового раствора через турбину развиваемый ею крутящий момент определяется по формуле Эйлера
M = Qρr(C1u – C2u)z, |
(4.1) |
ãäå Q – расход жидкости; ρ – плотность жидкости; r – средний радиус турбины; Ñ1u, C2u – проекции абсолютной скорости потока жидкости, протекающего соответственно через статор и ротор, на направление окружной скорости турбины; z – число ступеней турбины.
Эффективный перепад давления на турбине определяется по формуле
ðý = ρu2z, |
(4.2) |
ãäå u – окружная скорость турбины на среднем диаметре.
Развиваемый турбиной крутящий момент зависит от режима ее работы, т.е. от частоты вращения ротора турбины. Для большинства современных турбин эта зависимость линейна и определяется уравнением
M = Mò 1− |
n |
, |
(4.3) |
|
|||
|
nx |
|
ãäå Ìò – тормозной (предельный) крутящий момент; ï – частота вращения ротора; ïõ – частота вращения ротора на холостом режиме (предельная).
Совокупность зависимостей крутящего момента, перепада давления, мощности и коэффициента полезного действия (КПД) от частоты вращения называется энергетической характеристикой турбины. Энергетическая характеристика приведена на рис. 4.6. Как видно из графиков, характеристика турбины турбобура – сериесная. Однако это не означает, что работа турбобура может осуществляться на всех режимах от холостого до тормозного. Известно, что при увеличении осевой нагрузки частота вращения вала турбобура вначале уменьшается, затем турбобур начинает неустойчиво работать, а потом резко останавливается – «срывается».
«Срыв» турбобура объясняется многими факторами, основными из ко-
93
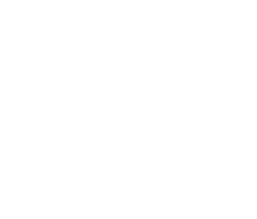
Рис. 4.6. Энергетическая характеристика турбины турбобура:
Ì – крутящий момент; Ìò – тормозной момент; N – мощность; Ný – максимальная мощность; ð – перепад давления; n – частота вращения; ný, nõ, nî – частота вращения соответственно на экстремальном, холостом и оптимальном режимах; η – КПД; η0 – максимальный КПД
торых являются нелинейный рост момента сопротивления на долоте и в пяте турбобура при увеличении осевой нагрузки и снижении частоты вращения, низкочастотные колебания момента сопротивления из-за вибраций и неравномерностей подачи бурильного инструмента, перемежаемость разбуриваемых горных пород по твердости. Все эти факторы приводят к тому, что устойчивая работа турбобура возможна только с определенным, как правило, не менее чем двукратным запасом крутящего момента, т.е. на режимах, располагающихся правее от режима максимальной мощности.
Эти режимы в большинстве случаев характеризуются также и максимальным значением механической скорости проходки. Поэтому условно режим максимальной мощности можно считать рабочим режимом турбобура.
Следует отметить, что, чем глубже забой скважины, чем больше искривлен ее ствол, чем более моментоемкое долото используется при бурении, чем выше вибрации бурильного инструмента и чем больше перемежаемость горных пород, тем ближе к холостому режиму должен приближаться рекомендуемый рабочий режим турбобура и тем ниже должна быть холостая частота его вращения.
Для расчета характеристики турбины могут использоваться преобразованные формулы, определяющие крутящий момент, и перепад давления на режиме максимальной мощности:
M = 2π Qρr2n z; |
(4.4) |
|||
p = 4π2ρr 2 |
rz |
, |
(4.5) |
|
η |
||||
|
|
|
ãäå ð – перепад давления на турбине; η – максимальный КПД.
При пересчете параметров характеристики турбины на другие значе- ния расхода, плотности жидкости и числа ее ступеней следует пользоваться выражениями
n Q; |
M Q2; p Q2; N Q3; |
ηinv Q; |
|
|||
ninv ρ; |
M ρ; |
p ρ; |
N ρ; |
ηinv ρ; |
(4.6) |
|
ηinv z; |
M z; |
p z; |
N z; |
ηinv |
z, |
|
ãäå N – мощность турбины.
94

Ò à á ë è ö à 4.8
|
Диаметр |
Расход |
Тормоз- |
Частота |
Перепад давления, |
Макси- |
|
|
вращения |
ÌÏà |
|||||
Тип турбины |
турбобу- |
раствора, |
íîé ìî- |
холостого |
|
|
мальный |
|
макси- |
||||||
|
ðà, ìì |
ë/ñ |
ìåíò, Í ì |
õîäà, ñ–1 |
рабочий |
мальный |
ÊÏÄ, % |
30/16,5-240 |
240 |
40 |
24,58 |
17,3 |
0,0262 |
0,0262 |
63,8 |
À9Ê5Ñà |
240 |
40 |
22,02 |
14,0 |
0,0252 |
0,0324 |
40,4 |
26/16,5-196 |
195 |
28 |
8,07 |
13,9 |
0,0113 |
0,0113 |
55,3 |
À7Í4Ñ |
195 |
28 |
12,59 |
18,5 |
0,0287 |
0,0363 |
40,5 |
24/18-195ÒË |
195 |
28 |
4,74 |
8,2 |
0,0048 |
0,0048 |
47,4 |
24/18-195ÒÏÊ |
195 |
28 |
5,63 |
8,1 |
0,0057 |
0,0057 |
42,3 |
À7Ï3 |
195 |
28 |
16,77 |
18,3 |
0,0320 |
0,0363 |
38,2 |
À7Ï36Ê |
195 |
28 |
17,69 |
19,8 |
0,0259 |
0,0296 |
52,8 |
21/16,5-195ÀÒË |
195 |
28 |
16,32 |
23,2 |
0,0263 |
0,0341 |
70,6 |
ÒÄ-195ÀÒË |
195 |
28 |
16,92 |
29,2 |
0,0395 |
0,0433 |
65,6 |
Ò195Ê |
195 |
28 |
9,50 |
13,8 |
0,0139 |
0,0139 |
50,8 |
28/16-172 |
172 |
24 |
8,22 |
20,5 |
0,0239 |
0,0239 |
44,2 |
À6Ê3Ñ |
164 |
20 |
6,22 |
18,1 |
0,0194 |
0,0232 |
39,8 |
П р и м е ч а н и е. Количество ступеней – 1. Плотность бурового раствора – 1000 кг/м3 (техническая вода).
Турбины турбобуров изготавливают из малолегированной стали преимущественно цельнолитыми в земляные формы и составными, когда лопаточный венец выплавляется точным литьем по моделям. Выпускаются также лопаточные венцы, изготовленные из пластмассы. Стойкость пластмассовых венцов, как правило, намного ниже стойкости стальных.
Характеристики турбин определяются экспериментально при испытаниях на специальном турбинном стенде. В табл. 4.8 даны основные параметры стендовых энергетических характеристик серийных и некоторых опытных турбин турбобуров, выпускаемых промышленностью.
Проектирование характеристики турбобура
Для эффективного применения турбобура необходимо правильно спроектировать его энергетическую характеристику. При этом следует руководствоваться следующими общими положениями.
1.Надежный контроль за режимом работы турбобура в процессе бурения возможен при режиме, когда механическая скорость проходки максимальная. Как правило, этот режим совпадает с экстремальным режимом работы турбобура или располагается в непосредственной близости в правой зоне кривой мощности. Таким образом, все расчеты характеристики турбобура имеет смысл вести для экстремального режима работы или режимов, близких к нему.
2.Следует помнить, что при недоиспользовании крутящего момента турбобура долота отрабатываются на излишне высоких частотах вращения. Это приводит к недобору проходки за рейс долота, и поэтому запас крутящего момента не должен быть излишне большим.
3.При турбинном бурении гидравлическая мощность, которую можно сработать в гидромониторных насадках долота, всегда намного меньше той, которую можно использовать при роторном способе бурения. Поэтому турбинное бурение предпочтительнее применять в разрезах, сложенных достаточно крепкими породами.
При бурении в мягких и пластичных породах необходимо в первую очередь думать об очистке вооружения долота, что обеспечивается пра-
95
вильным и несимметричным расположением промывочных каналов долота. Вполне удовлетворительная очистка вооружения шарошек достигается при сработке в долоте перепада давления в 5 МПа.
4.При турбинном бурении целесообразно использовать осевые нагрузки на долото, составляющие 60–80 % тех, которые имеются при роторном способе бурения аналогичных разрезов.
5.Использование одной и той же энергетической характеристики турбобура в разных по буримости разрезах, например, в кварцитах и мягких глинистых сланцах, заведомо ставит турбинный способ бурения в невыгодные условия. Поэтому тип сборки турбобура в каждом конкретном случае должен соответствовать физико-механическим свойствам проходимых пород, гидравлической программе бурения и возможностям применяемого бурового оборудования. Формирование необходимой характеристики осуществляется за счет использования рационального соотношения турбин и решеток ГТ.
Проектирование характеристики турбобура следует начинать с определения так называемого «удельного» крутящего момента на долоте ò, выражающего функциональную связь между осевой нагрузкой на долото и крутящим моментом, необходимым для вращения долота:
m = M/G, |
(4.7) |
ãäå ò – удельный момент, м; Ì – крутящий момент, Н м; G – осевая нагрузка на долото, Н.
Удельные моменты для различных районов бурения и типоразмеров долот определены в результате испытаний турбобуров и электробуров и приводятся во многих источниках.
После определения ò находят потребный крутящий момент турбобура на экстремальном режиме
M = mG. |
(4.8) |
При этом нагрузку на долото G выбирают, исходя из типоразмера долота, физико-механических свойств разбуриваемых пород и других факторов.
Зная значение Ì, можно определить тормозной момент турбобура:
Ìò = 2Ì. |
(4.9) |
Расход бурового раствора определяют, исходя из возможностей насосной группы буровой установки и имеющегося бурильного инструмента. На рис. 4.7 показаны совмещенные характеристики бурового насоса (1) и гидравлического тракта «манифольд – бурильная колонна с долотом – скважина» (2) без учета турбобура. Гидравлическая характеристика насоса строится по паспортным данным, а для манифольда, бурильной колонны, долота и кольцевого пространства скважины определяется расчетным путем или экспериментально.
Точка пересечения кривых 1 è 2 определяет предельные возможности данного бурового насоса. Расход бурового раствора Qmax, соответствующий этой точке, является предельным (не оптимальным) при бурении данной скважины роторным способом. Для создания необходимой эффективной характеристики турбобура рекомендуется использовать значения расхода Q, составляющие 60–80 % Qmax. Выбранное значение Q в большинстве слу- чаев не должно превышать 0,07 л/с на 1 см2 площади забоя скважины.
96
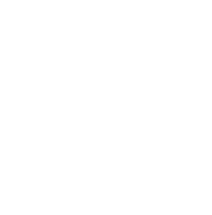
Рис. 4.7. Совмещенные гидравлические характеристики бурового насоса (1) и гидравлического тракта «манифольд – бурильная колонна с долотом – скважина» (2)
Если в распоряжении проектировщика не имеется специальных типов турбин, то они выбираются из серийных, выпускаемых машиностроительными заводами. Пересчет параметров характеристики турбобура со стендовых данных производится по формулам (4.6).
При практических расчетах допускается не учитывать потери крутящего момента турбобура в шпинделе и в радиальных опорах секций, так как серийный турбобур обычно работает в зоне, близкой к разгрузке осевой опоры, где эти потери не очень значительны.
Потери давления в проточных каналах турбобура (без учета турбины) при расходе воды, равном 20 л/с, для турбобуров диаметром 164 и 172 мм составляют 0,7 МПа; для турбобуров диаметром 195 мм – 0,4 МПа и для турбобуров диаметром 240 мм – 0,2 МПа.
Работа турбобура считается устойчивой до тех пор, пока обеспечивается как минимум двойной запас тормозного момента по сравнению с рабочим, хотя этот вопрос изучен в недостаточной степени. Регулирование рабочей частоты вращения осуществляется изложенными выше способами. Расчеты ведутся по формулам (4.1)–(4.7).
Конечная цель расчетов заключается в определении числа ступеней турбины и ступеней ГТ (если это необходимо), обеспечивающих необходимые значения крутящего момента и частоты вращения при заданных расходах и плотности бурового раствора. Разумеется, это число должно округляться для того, чтобы соответствовать целому количеству турбинных секций.
Расчет характеристики турбобура целесообразно вести для нескольких вариантов использования имеющихся турбин и ступеней ГТ. Затем выбирается тот вариант, который обеспечивает заданные параметры характеристики при меньшем перепаде давления на турбобуре, или тот, который дает возможность обходиться меньшим числом турбинных секций.
4.1.2. ВИНТОВЫЕ ЗАБОЙНЫЕ ДВИГАТЕЛИ
История создания винтовых забойных двигателей
Начиная с 40-х годов в б. СССР основным техническим средством для бурения нефтяных и газовых скважин являлся многоступенчатый турбобур.
97
Широкое распространение турбинного способа бурения обеспечило ускоренное разбуривание нефтегазоносных площадей Урало-Поволжья и Западной Сибири и, тем самым, позволило получать высокие темпы роста добычи нефти и газа.
Однако с увеличением средних глубин скважин и по мере совершенствования породоразрушающего инструмента и технологии роторного способа бурения в отечественной нефтяной промышленности с каждым годом росла тенденция отставания проходки за рейс долота – показателя, определяющего технико-экономические показатели бурения.
Несмотря на определенные усовершенствования техники и технологии турбинного бурения показатели работы долот на протяжении ряда лет улучшались весьма незначительно. Хотя в 70-е годы началось разбуривание месторождений Западной Сибири, отличающихся благоприятными условиями бурения (мягкие породы, относительно неглубокие скважины), средняя проходка за рейс по эксплуатационному бурению существенно отставала от аналогичного показателя в нефтяной промышленности США (в 3– 4 раза). Так, в 1981–1982 гг. средняя проходка за долбление в США составила 350 м, в то время как в б. СССР этот показатель не превышал 90 м.
Серьезное отставание в проходке за долбление было связано с тем, что в те годы отечественная практика бурения базировалась на высокоскоростном режиме бурения с применением многоступенчатых безредукторных турбобуров, характеристики которых не позволяли получать частоты вращения менее 400–500 об/мин с обеспечением необходимых крутящих моментов и приемлемого уровня давления насосов, и как следствие эффективно использовать революционные усовершенствования шарошечных долот (с прецизионными маслонаполненными опорами и твердосплавным вооружением). В связи с этим перед специалистами и организаторами бурения в нашей стране встал вопрос о создании техники для низкооборотного бурения.
Перед советской нефтяной промышленностью встала дилемма: либо переходить к роторному бурению, либо создать низкооборотный забойный двигатель.
К этому времени в б. СССР имелись определенные успехи роторного бурения глубоких скважин в ряде районов (Северный Кавказ, Западная Украина и др.). Однако технически, экономически и психологически нефтяная промышленность не была готова к развитию роторного бурения. За многие годы государственной поддержки турбинного бурения существенно отстала от мирового уровня техника роторного бурения: не имелось бурильных труб и буровых установок высокого технического уровня.
Переход на роторный способ бурения в основных регионах страны снизил бы темпы развития отрасли, так как промышленность не располагала необходимыми средствами для строительства новых заводов и эксплуатационных баз или закупки за рубежом новых технологий.
Таким образом определился доминирующий способ бурения на базе низкооборотных забойных двигателей.
Решение проблемы создания забойного гидравлического двигателя с характеристиками, отвечающими требованиям новых конструкций долот, было найдено в переходе от динамических машин, каким являются турбобуры, к объемным.
Первым работоспособным, нашедшим промышленное применение,
98

оказался гидродвигатель, представляющий собой обращенный насос Муано1, относящийся к планетарно-роторному типу гидромашин.
Работы по созданию опытных образцов винтовых забойных двигателей (ВЗД) начались в США и б. СССР в середине 60-х годов.
Американские специалисты фирмы «Smith Tool» разработали ВЗД (на западе их называют РDМ – positive displacement motors) для наклонно направленного бурения как альтернативу турбобурам, а в нашей стране, родине турбинного бурения – они служат техническим средством для привода низкооборотных долот.
Многолетние поисковые научно-исследовательские работы во ВНИИБТ по совершенствованию забойных гидравлических двигателей привели в 1966 г. к появлению предложенного М.Т. Гусманом, С.С. Никомаровым, Н.Д. Деркачем, Ю.В. Захаровым и В.Н. Меньшениным нового типа ВЗД, рабочие органы которого впервые в мировой практике выполнены на базе многозаходного винтового героторного механизма, исполняющего функцию планетарного редуктора.
Âпоследующие годы во ВНИИБТ и его Пермском филиале Д.Ф. Балденко, Ю.В. Вадецким, М.Т. Гусманом, Ю.В. Захаровым, А.М. Кочневым,
Ñ.Ñ.Никомаровым и другими исследователями были созданы основы теории рабочего процесса, конструирования и технологии изготовления, разработана технология бурения винтовыми двигателями.
Âрезультате многолетнего опыта бурения с использованием гидравли- ческих забойных двигателей (турбобуров и ВЗД) сложился комплекс технических требований к современному забойному двигателю.
1. Характеристики двигателя должны обеспечивать:
высокий уровень крутящего момента (3 кН м и более для долот диаметром 215–243 мм);
частоту вращения выходного вала в диапазоне 100–200 об/мин для шарошечных долот и 500–800 об/мин для алмазных долот;
высокий КПД двигателя для эффективного использования гидравличе- ской мощности насосов;
пропорциональную зависимость между расходом бурового раствора и частотой вращения, а также между крутящим моментом и перепадом давления с целью эффективного управления режимом бурения.
2. Рабочие элементы и другие узлы двигателя должны быть износо- и термостойкими, что позволяет использовать буровой раствор любой плотности и вязкости, в том числе с содержанием тампонирующих материалов.
3. Конструктивная компоновка двигателя и проектные запасы прочности его узлов должны обеспечить:
стойкость двигателя, достаточную для стабильной работы с современными шарошечными и алмазными долотами;
возможность искривления корпуса двигателя при наклонно направленном бурении;
возможность установки на корпусе двигателя опорно-центрирующих элементов при проводке наклонно направленных и горизонтальных скважин.
4. Диаметральные и осевые размеры двигателя должны обеспечивать:
1 R. Moineau (1887–1948) – французский инженер, изобретатель одновинтовых гидравлических и пневматических машин.
99
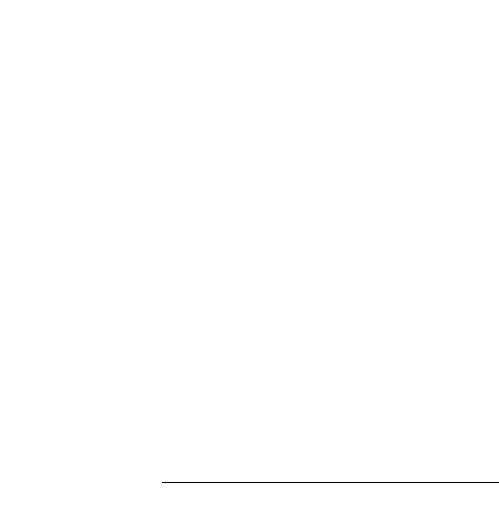
проведение буровых работ долотами различного диаметра, включая малогабаритные;
эффективную проводку наклонно направленных и горизонтальных скважин;
использование стандартного ловильного инструмента.
Анализ конструкций и характеристик забойных гидравлических двигателей различного типа показывает, что ни один из них не отвечает в полной мере всем перечисленным требованиям; в большей степени указанным требованиям соответствуют ВЗД с многозаходными рабочими элементами.
Принцип действия ВЗД
Винтовые двигатели относятся к объемным роторным гидравлическим машинам.
Согласно общей теории винтовых роторных гидравлических машин элементами рабочих органов (РО) являются:
1)статор двигателя с полостями, примыкающими по концам к камерам высокого и низкого давления;
2)ротор-винт, носящий название ведущего, через который крутящий момент передается исполнительному механизму;
3)замыкатели-винты, носящие название ведомых, назначение которых уплотнять двигатель, т.е. препятствовать перетеканию жидкости из камеры высокого давления в камеру низкого давления.
В одновинтовых гидромашинах используются механизмы, в которых замыкатель образуется лишь двумя деталями, находящимися в постоянном взаимодействии, – статором и ротором.
Упрощенная схема двигателя показана на рис. 4.8.
При циркуляции жидкости через РО в результате действия перепада давления на роторе двигателя вырабатывается крутящий момент, причем винтовые поверхности РО взаимно замыкаясь, разобщают область высокого давления и область низкого давления. Следовательно, по принципу действия винтовые двигатели аналогичны поршневым, у которых имеется винтообразный поршень, непрерывно перемещающийся в цилиндре вдоль оси двигателя.
Для создания в РО двигателя полостей, теоретически разобщенных от областей высокого и
Рис. 4.8. Упрощенная схема двигателя:
1 – корпус, 2 – ротор; 3 – âàë; 4, 5 – осевой и радиальный подшипники; 6 – долото
100