
Лахтин_Матеориаловедение
.pdfконием, титаном и другими переходивши металлами превышает обычно назначаемую температуру нагрева под деформацию или закалку, поэтому после закалки и старения таких сплавов в них сохраняется нерекристаллизованная (полигонизованная) структура с высокой плотностью дислокаций, что повышает ее прочность по сравнению с рекристаллизованной структурой. Это явление получило название структурного упрочнения.
В результате структурного упрочнения значения σΒ и σ0,2 повышаются до 30—40 %. Наиболее сильно етруктурное упрочнение проявляется в прессованных полуфабрикатах (прутки, профили, трубы), поэтому это явление применительно к ним называют пресс-эффектом.
Диффузионный отжиг (гомогенизация). Этому виду отжига подвергают слитки перед обработкой давлением для устранения дендритной ликвации, которая приводит к получению неоднородного твердого раствора и выделению по границам зерен и между ветвями дендритов хрупких неравновесных эвтектических включений CuAl2, Al2CuMg (S-фаза), Mg2Si и др. (см. рис. 183,
а). В процессе гомогенизации состав кристаллитов твердого раствора выравнивается, а интерметаллиды растворяются. В процессе последующего охлаждения интерметаллиды выделяются в виде равномерно распределенных мелких вторичных включений (см. рис. 183, б). В результате пластичность литого сплава повышается, что позволяет увеличить степень обжатия при горячей обработке давлением, скорость прессования и уменьшить технологические отходы. Гомогенизация способствует получению мелкозернистой структуры в отожженных листах и уменьшает склонность к коррозии под напряжением.
Температура гомогенизации лежит в пределах 450—520 °С, а выдержка составляет 4—40 ч. Охлаждение проводят на воздухе или вместе с печью.
Рекристаллизационный отжиг. Такой отжиг заключается в нагреве деформированного сплава до температур выше температуры окончания первичной рекристаллизации; применяется для снятия наклепа и получения мелкого зерна. Температура рекристалли-зационного отжига в зависимости от состава сплава колеблется от 350 до 500 °С, выдержка 0,5—2 ч. После рекристаллизацион-ного отжига сплавов, неупрочняемых термической обработкой, скорость охлаждения выбирают произвольно. Для сплавов, упрочняемых термической обработкой, скорость охлаждения до 200— 250 °С должна быть 30 °С/ч. Отжиг в качестве промежуточной операции применяют при холодной деформации или между горячей и холодной деформациями.
Отжиг для разупрочнения сплавов, прошедших закалку и старение. Этот вид отжига проводят при 360—450 °С с выдержкой 1—2 ч. При этих температурах происходят полный распад пересыщенного твердого раствора и коагуляция упрочняющих фаз. Скорость охлаждения не должна превышать 30 °С/ч. После от-
391
жига сплав имеет низкое временное сопротивление, удовлетворительную пластичность и высокую сопротивляемость коррозии под напряжением.
4. ДЕФОРМИРУЕМЫЕ АЛЮМИНИЕВЫЕ СПЛАВЫ, УПРОЧНЯЕМЫЕ ТЕРМИЧЕСКОЙ ОБРАБОТКОЙ
Дуралюмины. Дуралюминами называют сплавы Аl—Сu—Mg, в которые дополнительно вводят марганец (см. табл. 34). Типичным дуралюмином является сплав Д1, однако вследствие сравнительно низких механических свойств производство его заметно сокращается; сплав Д1 для листов и профилей заменяется сплавом Д16. Упрочнение дуралюмина при термической обработке достигается в результате образования зон ГП сложного состава или метастабильных фаз θ и S.
Марганец повышает стойкость дуралюмина против коррозии, а присутствуя в виде дисперсных частиц фазы Τ (Al12Mn2Cu), повышает температуру рекристаллизации и улучшает механические свойства. В качестве примесей в дуралюмине присутствуют железо и кремний. Железо образует соединение Al8Fe и (Μn, Fe) Al6, кристаллизующееся в виде грубых пластин. Кроме того, железо образует соединение Al7Cu2Fe, нерастворимое в алюминии. Железо связывает медь в этом соединении, вследствие чего снижается эффект упрочнения при старении.
Кремний образует фазы MgaSi и W (AlxMg5Cu4Si4), которые растворяются в алюминии и при последующем старении упрочняют сплав. Однако упрочнение от Mg2Si и W-фаз невелико, поэтому примесь кремния, уменьшая количество основных упрочняющих фаз S и θ, способствует снижению прочности. При одновременном присутствии Fe и Si образуются химические соединения, не содержащие основных легирующих элементов (Сu
и Mg).
Железо и кремний, образуя грубые нерастворимые интерметаллические фазы, снижают трещиностойкость Κ1c, т. е. облегчают распространение трещин при действии растягивающих напряжений. По ГОСТ 4784—74 допускается содержание до 0,5 % Fe и 0,5 % Si. Снижение содержания Fe и Si до 0,1—0,3 % и меньше значительно повышает вязкость разрушения Κ1c, не изменяя величины σΒ и σ0,2. Сплав Д16ч (чистый) имеет Κ1c = 40,6, а обычный Д16 — К1с = 34,5 МПа·м1/2 (после закалки и старения).
Дуралюмин, изготовляемый в листах, для защиты от коррозии подвергают плакированию, т. е. покрытию тонким слоем алюминия высокой чистоты (не ниже 99,5 %). Толщина слоя должна составлять 4 % толщины листа. Плакирование заметно снижает прочность дуралюмина. Например, предел прочности плакированных листов из сплава Д16 составляет 440 вместо 520 МПа для остальных полуфабрикатов.
Упрочнение достигается закалкой и старением. Структура закаленного дуралюмина состоит из пересыщенного α-твердого раствора и нерастворимых соединений железа (см. рис. 183, б).
392
Дуралюмины после закалки подвергают естественному старению, так как оно обеспечивает получение более высокой коррозионной стойкости. Понижение температуры тормозит старение, а повышение ее, наоборот, увеличивает скорость процесса, но понижает пластичность, и сопротивление коррозии. Прессованные полуфабрикаты из сплавов Д1 и Д16 значительно прочнее, чем листы, вследствие пресс-эффекта. Для повышения коррозионной стойкости дуралюмин подвергают электрохимическому оксидированию (анодированию). Дуралюмины удовлетворительно обрабатываются резанием в закаленном и состаренном состояниях и плохо — в отожженном состоянии, хорошо свариваются точечной сваркой и не свариваются сваркой плавлением вследствие склонности к образованию трещин. Из сплава Д16 изготовляют обшивки, шпангоуты, стрингера и лонжероны самолетов, силовые каркасы, строительные конструкции, кузова грузовых автомобилей и т. д.
Сплавы авиаль (АВ). Эти сплавы уступают дуралюминам по прочности, но обладают лучшей пластичностью в холодном и горячем состояниях (см. табл. 34). Авиаль удовлетворительно обрабатывается резанием (после закалки и старения) и сваривается контактной и аргонодуговой сваркой. Сплав обладает высокой общей сопротивляемостью коррозии, но склонен к меж-кристаллитной коррозии.
Авиаль закаливают от 515—525 °С с охлаждением в воде, а затем подвергают естественному старению (АВТ) или искусственному при 160 °С 12 ч (АВТ1). Искусственное старение надо выполнять сразу после закалки. При увеличении перерывов между временем закалки и началом искусственного старения прочность сплава после старения уменьшается. Упрочняющей фазой в авиале является соединение Mg2Si.
Из сплава АВ изготовляют различные полуфабрикаты (листы, трубы и т. д.), используемые для элементов конструкций, несущих умеренные нагрузки, кроме того, лопасти винтов вертолетов, кованые детали двигателей, рамы, двери, для которых требуется высокая пластичность в холодном и горячем состояниях.
Высокопрочные сплавы. Предел прочности этих сплавов достигает 550—700 МПа, но при меньшей пластичности, чем у дура-люминов. Представителем высокопрочных алюминиевых сплавов является сплав В95 (см. табл. 34).
Упрочняющими фазами в сплавах являются MgZn2, Т-фаза (Al2Mg3Zn8) и S-фаза (Al2CuMg). При увеличении содержания цинка и магния прочность сплавов повышается, а их пластичность и коррозионная стойкость понижаются. Добавки марганца и хрома улучшают коррозионную стойкость. Сплавы закаливают от 460—470 °С (с охлаждением в холодной или горячей воде) и подвергают искусственному старению при 135—145 °С 16 ч. По сравнению G дуралюмином эти сплавы обладают большой чувствительностью к концентраторам напряжений и пониженной
393
коррозионной стойкостью под напряжением. У них меньше, чем у дуралюмина, предел выносливости (σ-1) и вязкость разрушения (К1с 25 МПа·м1/2). Профили из сплава В95 значительно прочнее листов. Это результат пресс-эффекта, который обусловлен присутствием в сплаве марганца и хрома.
Сплавы обладают хорошей пластичностью в горячем состоянии и сравнительно легко деформируются в холодном состоянии после отжига. Листы из сплава В95 плакируют сплавом алюминия с 0,9—1,3 % Zn для повышения коррозионной стойкости. Сплав В95 хорошо обрабатывается резанием и сваривается точечной сваркой, его применяют в самолетостроении для нагруженных конструкций, работающих длительное время при t ≤ 100÷120 oC (обшивка, стрингеры, шпангоуты, лонжероны; силовые каркасы строительных сооружений и т. д.). Сплав В95 рекомендуется для сжатых зон конструкции и для деталей без концентраторов напряжений.
Сплавы для ковки и штамповки. Сплавы этого типа отличаются высокой пластичностью и удовлетворительными литейными свойствами, позволяющими получить качественные слитки.
Сплав АК6 (см. табл. 34) используют для деталей сложной формы и средней прочности, изготовление которых требует высокой пластичности в горячем состоянии (подмоторные рамы, фитинги, крепежные детали, крыльчатки и т. д.). Сплав АК8 рекомендуется для тяжелонагруженных штампованных деталей (подмоторные рамы, стыковые узлы, пояса лонжеронов, лопасти винтов вертолета и т. д.). Сплав АК8 менее технологичен, чем сплав АК6.
Ковку и штамповку сплавов проводят при температуре 450— 475 °С. Их подвергают закалке и старению при 150—165 °С 6— 15 ч. Упрочняющими фазами при старении являются соединения
Mg2Si, CuAl2 и ω-фаза (AlxMg5Cu5Si4). Сплавы АК6 и АК8 хорошо обрабатываются резанием и удовлетворительно свариваются контактной и аргонодуговой сваркой. Сплавы склонны к коррозии под напряжением и межкристаллитной коррозии.
Жаропрочные сплавы. Эти сплавы (см. табл. 34) используют для деталей, работающих при температуре до 300 °С (поршни, головки цилиндров, крыльчатки, лопатки и диски осевых компрессоров турбореактивных двигателей; обшивка сверхзвуковых самолетов и т. д.). Жаропрочные сплавы имеют более сложный химический состав, чем рассмотренные выше алюминиевые сплавы. Их дополнительно легируют железом, никелем и титаном.
Фазами — упрочнителями жаропрочных сплавов являются θ-
фаза (CuAl2), S-фаза (Al2CuMg), фазы Al12Mn2Cu, а также Al9FeNi и Al6Cu3Ni. При частичном распаде твердого раствора они выделяются в виде дисперсных частиц, устойчивых к коагуляции, что обеспечивает повышенную жаропрочность.
Высокая жаропрочность сплава Д20 достигается благодаря высокому содержанию меди, а также марганца и титана, замед-
394
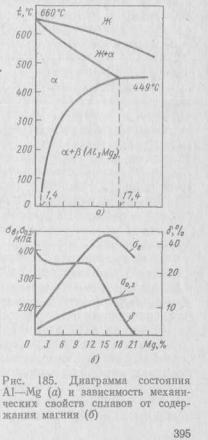
ляющих диффузионные процессы. Кроме того, титан задерживает процесс рекристаллизации. Сплавы АК4-1 закаливают при 530 °С в холодной или горячей воде и подвергают старению при
200°С
5. ДЕФОРМИРУЕМЫЕ АЛЮМИНИЕВЫЕ СПЛАВЫ, НЕ УПРОЧНЯЕМЫЕ ТЕРМИЧЕСКОЙ ОБРАБОТКОЙ
К этим сплавам относятся сплавы алюминия с марганцем или с магнием (см. табл. 35). Упрочнение сплавов достигается в результате образования твердого раствора и в меньшей степени избыточных фаз.
Сплав АМц представляет α-твердый раствор марганца в алюминии, в котором также имеются в небольшом количестве частицы соединения А16Мп. Сплавы типа АМГ В равновесном состоянии после охлаждения двухфазные α + β (Al3Mg2) (рис. 185, α). Однако вследствие высокой устойчивости твердого раствора и малой скорости диффузии магния в алюминии, даже после медленного охлаждения, они не содержат избыточных фаз и состоят только
из α-твердого раствора. Магний сильно повышает прочность сплавов
(см. рис. 185, б). До 12—14 % Mg
пластичность изменяется мало, а затем резко падает. Сплавы А1—Mg добавочно легируют марганцем (см. табл. 35), который, образуя дисперсные частицы А16Мn, упрочняет сплав и способствует измельчению зерна. Эффект от закалки и старения сплавов АМг и АМц невелик, и их применяют в отожженном состоянии. Отжиг сплавов АМц и АМг2 проводят при 350—410 °С, сплава АМг3 — при 270—280 °С и сплава МАМг5 — при 310—335 °С,
охлаждение на воздухе. Повышение прочности при
некотором уменьшении пластичности изделий простой формы (листы, плиты) достигается нагартовкой (см. табл. 35). Упрочнение, создаваемое нагартовкой, снимается в зоне сварки.
Сплавы легко обрабатываются давлением (штамповка, гибка и т. д.), хорошо свариваются и обладают высокой коррозионной стойкостью. Обработка резанием
затруднена. Сплавы применяют для сварных и клепаных элементов конструкций, испытывающих небольшие нагрузки и требующие высокого сопротивления коррозии. Например, сплавы АМц, АМг2, АМг3 нашли применение при изготовлении емкостей для жидкости (баки для бензина), трубопроводов, палубных надстроек, морских и речных судов, в строительстве (витражи, перегородки, двери, оконные рамы и т. д.)
Для средненагруженных деталей и конструкций используют сплавы АМг5 и АМг6 (рамы и кузова вагонов, подвесные нагруженные потолки, перегородки здания и переборки судов, лифты, узлы подъемных кранов, корпуса и мачты судов и др.).
6. ЛИТЕЙНЫЕАЛЮМИНИЕВЫЕСПЛАВЫ
Сплавы для фасонного литья должны обладать высокой жидкотекучестью, сравнительно небольшой усадкой, малой склонностью к образованию горячих трещин и пористости в сочетании с хорошими механическими свойствами, сопротивлением коррозии и др.
Высокими литейными свойствами обладают сплавы, содержащие в своей структуре эвтектику. Эвтектика образуется во многих сплавах, в которых содержание легирующих элементов больше предельной растворимости в алюминии. В связи с этим содержание легирующих элементов в литейных сплавах выше, чем в деформируемых. Чаще применяют сплавы А1—Si, ΑΙ—Сu, ΑΙ— Mg (табл. 36), которые дополнительно легируют небольшим количеством меди и магния (А1—Si), марганца, никеля, хрома (А1— Сu). Для измельчения зерна, а следовательно, улучшения механических свойств в сплавы вводят модифицирующие добавки: Ti, Zr, В, V И др. Состав и механические свойства некоторых литейных сплавов алюминия приведены в табл. 36.
Многие отливки из алюминиевых сплавов подвергают термической обработке. В зависимости от характера отливки и условий ее работы используют один из видов термической обработки, приведенных ниже.
1.Искусственное старение (условное обозначение Т1) при (175
±5) °С в течение 5—20 ч без предварительной закалки. При литье многих сплавов (АЛ4, АЛ5, АЛЗ) в сырую песчаную форму или в кокиль происходит частичная закалка, поэтому старение повышает прочность и улучшает обработку резанием.
2.Отжиг (Т2) при 300 °С в течение 5—10 ч. Охлаждение при отжиге проводят на воздухе. Отжиг применяют для снятия литейных напряжений, а также остаточных напряжений, вызванных механической обработкой. ОТЖИР несколько повышает пластичность.
3.Закалка и естественное старение (ТЗ, Т4). Температура закалки 510—520 °С для еплавов АЛ1, АЛ7 и 535—545 °С для
396

сплавов АЛ4, АЛ9, АЛ19 и др. Так как после закалки отливки выдерживают достаточно длительное время при нормальной температуре, режим (ТЗ) практически соответствует закалке и естественному старению (Т4).
4.Закалка и кратковременное (2—3 ч) искусственное старение обычно при 150—175 °С (Т5). При данной температуре и продолжительности процесс старения полностью не заканчивается, поэтому после такой обработки отливки приобретают высокую прочность при сохранении повышенной пластичности.
5.Закалка и полное искусственное старение (Т6) при 200 °С 3—5 ч. Старение при повышенной температуре по сравнению
397
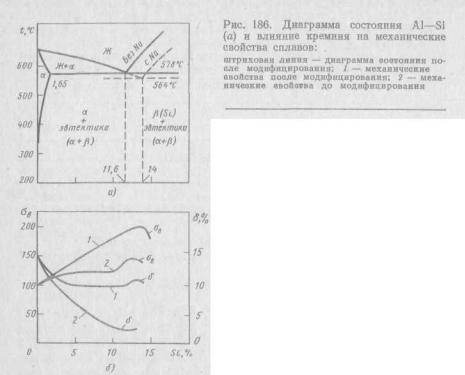
с режимом Т5 придает наибольшую прочность, но пластичность снижает. Закалка и стабилизирующий отпуск (Т7) при 230 °С для сплавов АЛ9, АЛ5, АЛ1 и при 250 °С для сплава АЛ 19 в течение 3—10 ч. Этот вид обработки используют для стабилизации структуры и объемных изменений отливки при сохранении достаточной прочности. Закалка и смягчающий отпуск (Т8) при 240—260 °С в течение 3—5 ч. Высокая температура отпуска заметно снижает прочность, но повышает пластичность и стабильность размеров.
Сплавы Al—Si. Эти сплавы (см. табл. 36), получившие название силумины, близки по составу к эвтектическому сплаву (рис. 186, а) и потому отличаются высокими литейными свойствами, а отливки — большой плотностью.
Наиболее распространен сплав, содержащий 10—13 % Si (АЛ2), обладающий высокой коррозионной стойкостью. Сплав АЛ2 содержит в структуре эвтектику α + β и нередко первичные кристаллы кремния (см. рис. 187, а). Кремний при затвердении эвтектики выделяется в виде грубых кристаллов игольчатой формы, которые играют роль внутренних надрезов в пластичном α-твердом растворе. Такая структура обладает низкими механическими свойствами (см. рис. 186).
Для измельчения структуры эвтектики и устранения избыточных кристаллов кремния силумины модифицируют натрием (0,05—0,08 %) путем присадки к расплаву смеси солей 67 % NaF и 33 % NaCl. В присутствии натрия происходит смещение линий диаграммы состояния (см. рис. 186, а) и заэвтектический (эвтектический) сплав АЛ2 (11—13 % Si) становится доэвтектическим. В этом случае в структуре сплава вместо избыточного кремния появляются кристаллы α-раствора (рис. 187, б). Эвтектика приобретает более тонкое строение и состоит из мелких кристаллов β-(Si) и α-твердого раствора. В процессе затвердевания кристаллы
398
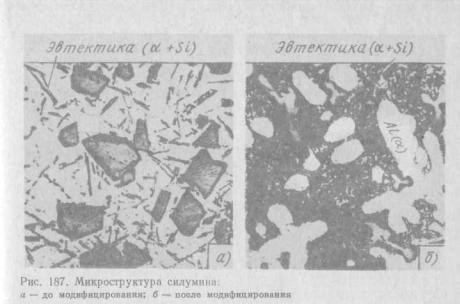
кремния обволакиваются пленкой силицида натрия Na2Si, которая затрудняет их рост. Такие изменения структуры улучшают механические свойства сплава (см. рис. 186, б). Сплав АЛ2 не подвергают упрочняющей термической обработке. Доэвтекти-ческие сплавы АЛ4 и АЛ9 (см. табл. 36), дополнительно легированные магнием, могут упрочняться кроме модифицирования термической обработкой. Упрочняющей фазой служит Mg2Si. При одновременном введении магния и меди могут образоваться фазы CuAl2 и W(AlxMg5Cu4Si4).
Средненагруженные детали из сплава АЛ4 подвергают только искусственному старению (Т1), а крупные нагруженные детали (корпуса компрессоров, картеры и блоки цилиндров двигателей и т. д.) — закалке и искусственному старению (Т6). Отливки из сплава АЛ9, требующие повышенной пластичности, подвергают закалке (Т4), а для повышения прочности — закалке и старению (Т6). Когда важна высокая пластичность и стабильность размеров, после закалки проводят отпуск при 250 °С в течение 3— 5 ч.
Сплавы Аl—Si сравнительно легко обрабатываются резанием. Заварку дефектов можно производить газовой и аргонодуговой сваркой.
Сплавы Аl—Cu. Эти сплавы (АЛ7, АЛ19) после термической обработки имеют высокие механические свойства при нормальной и повышенных температурах и хорошо обрабатываются резанием. Литейные свойства сплавов низкие (большая усадка, склонность к образованию горячих трещин и т. д.). Сплав АЛ7 используют для отливки небольших деталей простой формы (арматура, кронштейн и т. д.). Сплав склонен к хрупкому разрушению вслед-
399
ствие выделения по границам зерен грубых частиц CuAl2 и Al7Cu2Fe (см. рис. 183, а) поэтому его применяют в закаленном состоянии (Т4), когда эти соединения переведены в твердый раствор. Если от отливок требуется повышенная прочность, то их после закалки подвергают искусственному старению при 150 °С 2—4 ч (Т5).
В сплаве АЛ19 кроме CuAl2 образуются фазы Al12Mn2Cu и Al3Ti, располагающиеся по границам зерен твердого раствора.
Присутствие в твердом растворе марганца и образование по границам интерметаллидных фаз повышает жаропрочность сплава. Титан измельчает зерно.
Упрочнение сплава достигается закалкой и старением при 175 °С 3—5 ч (Т5, Т6). Сплавы Аl—Сu малоустойчивы против коррозии, поэтому отливки обычно анодируют.
Сплавы Аl—Mg. Сплавы алюминия с магнием (см. табл. 36) имеют низкие литейные свойства, так как не содержат эвтектики. Характерной особенностью этих сплавов является хорошая коррозионная стойкость, повышенные механические свойства и обрабатываемость резанием. Добавление к сплаву (9,5—11,5 % Мо) модифицирующих присадок (Ti, Zr) улучшает механические свойства, а бериллия — уменьшает окисляемость расплава, что позволяет вести плавку без защитных флюсов.
Сплавы АЛ8 и АЛ27 предназначены для отливок, работающих во влажной атмосфере, например в судостроении и авиации. Структура сплавов (см. рис. 185, а) состоит из α-твердого раствора и грубых включений частиц Al3Mg2, которые располагаются по границам зерен, охрупчивая сплав. В связи с этим сплавы АЛ8 и АЛ27 применяют после закалки от 430 °С с охлаждением в масле (40—50 °С) и выдерживают при температуре закалки в течение 12—20 ч, что обеспечивает растворение частиц Al3Mg2 в α-твердом растворе и получение после закалки однородного твердого раствора. Добавление к сплавам Аl—Mg до 1,5 % Si (сплавы АЛ13, АЛ22) улучшает литейные свойства в результате образования тройной эвтектики. Сплавы применяют в судостроении и авиации.
Жаропрочные сплавы. Наибольшее применение получил сплав АЛ1, из которого изготовляют поршни, головки цилиндров и другие детали, работающие при температуре 275— 300 °С. Структура литого сплава АЛ1 состоит из α-твердого раствора, содержащего Cu, Mg и Ni и избыточных фаз Al2CuMg и Al6Cu3Ni. Отливки применяют после закалки и кратковременного старения при 175 °С (Т5); поршни подвергают закалке и старению при 200 °C (Т7). При закалке S- фаза растворяется в α-твердом растворе.
Более жаропрочны сплавы АЛЗЗ и АЛ19. Ниже приведена длительная прочность жаропрочных алюминиевых сплавов:
Сплав ..................................... |
АЛ7 |
АЛ1 |
АЛ19 |
АЛЗЗ |
σ300100МПа................................. |
30 |
45 |
65 |
90 |
400