
Лахтин_Матеориаловедение
.pdf
азота (рис. 152). Твердость азотированного слоя на железе невелика ~300—350 HV. Поэтому азотированию подвергают средне-углеродистые стали, легированные Сг, Мо, V, А1, которые приобретают высокую твердость и износостойкость при азотировании. В легированной стали на поверхности образуются легированные ε- и γ'-фазы: (Fe, M)2_3N и (Fe, M)4N. Такие элементы, как Сr, Мо, V и другие, растворенные в феррите (подслой), повышают растворимость азота в α-фазе и образуют специальные нитриды MN и M2N (см. рис. 151, в).
При низких температурах азотирования в α-твердом растворе первоначально образуются сегрегации типа зон Гинье—Престона. При более высоких температурах возникают дисперсные нитриды легирующих элементов (Cr, МО, V и др.). Зоны Гинье—Престона
иобособленные выделения нитридов препятствуют движению дислокаций и тем самым повышают твердость азотированного слоя. Наиболее сильно повышают твердость А1, Сr, Мо и V. Толщину слоя легирующие элементы уменьшают.
Если главными требованиями, предъявляемыми к азотированному слою, являются высокие твердость на поверхности
иизносостойкость, то применяют сталь 38Х2МЮА, содержащую
0,35— 0,42 % С; 1,35—1,65 % Сr; 0,7—1,10 % А1 и 0,15—0,25 %
Мо, остальное Fe. Одновременное присутствие алюминия, хрома и молибдена позволяет повысить твердость азотированного слоя на поверхности до 1200 HV. Молибден, кроме того, устраняет отпускную хрупкость, которая может возникнуть при медленном охлаждении от температуры азотирования.
241
Однако алюминий придает азотированному слою повышенную хрупкость. Поэтому все шире применяют стали, легированные Сг
(1—3 %), Мо (0,2—0,4 %), V (до 1,0—1,2 %). Эти стали имеют пониженную твердость на поверхности 700—950 HV, но при прочих равных условиях большую эффективную толщину азотированного слоя (до 400—500 HV), что позволяет сократить длительность процесса. Для повышения коррозионной стойкости можно азотировать и углеродистые стали.
Износостойкость азотированной стали выше, чем износостойкость цементованной и закаленной. В азотированном слое возникают остаточные напряжения сжатия, величина которых на поверхности составляет 600—800 МПа. Это повышает предел выносливости и переносит очаг усталостного разрушения под азотированный слой. Предел выносливости гладких образцов возрастает на 30—40 %, а при наличии концентраторов напряжений (острых надрезов) — более чем на 100 %.
Технология процесса азотирования. Технологический процесс предусматривает несколько операций, приведенных ниже.
1.Предварительная термическая обработка заготовки. Эта операция состоит из закалки и высокого отпуска стали для получения повышенной прочности и вязкости в сердцевине изделия.
Отпуск проводят при высокой температуре 600—675 °С, превышающей максимальную температуру последующего азотирования и обеспечивающей получение твердости, при которой сталь можно обрабатывать резанием. Структура стали после этого отпуска — сорбит.
2.Механическая обработка деталей, а также шлифование, которое придает окончательные размеры детали.
3.Защита участков, не подлежащих азотированию, нанесением тонкого слоя (0,01—0,015 мм) олова электролитическим методом или жидкого стекла. Олово при температуре азотирования расплавляется на поверхности стали в виде тонкой не проницаемой для азота пленки.
4.Азотирование.
5.Окончательное шлифование или доводка изделия. Азотирование тонкостенных изделий сложной конфигурации
из стали 38Х2МЮА рекомендуется выполнять при 500—520 °С. Длительность процесса зависит от требуемой толщины азотированного слоя. Чем выше температура азотирования, тем ниже твердость азотированного слоя и больше толщина слоя (рис. 153). Снижение твердости азотированного слоя связано с коагуляцией нитридов легирующих элементов. Обычно при азотировании желательно иметь слой толщиной 0,3—0,6 мм. Процесс азотирования при 500—520 °С в этом случае является продолжительным и составляет 24—60 ч.
Для ускорения процесса азотирования применяют двухступенчатый процесс: сначала азотирование проводят при 500—520 °С, а затем при 540—560 °С. При двухступенчатом процессе сокра-
242

щается продолжительность процесса, при этом сохраняется
высокая твердость слоя.
В процессе насыщения азотом изменяются, но очень мало, размеры изделия вследствие увеличения объема поверхностного слоя. Деформация возрастает при повышении температуры азотирования и толщины слоя.
Стали, не содержащие алюминий (Cr—Mo—V-стали), азотируют при 570 °С в течение 6—10 ч, что обеспечивает достаточную толщину слоя 0,3—0,4 мм, высокую твердость (~800 HV) и износостойкость. Охлаждение после азотирования проводят вместе с печью в потоке аммиака (до 200 °С) во избежание окисления поверхности.
Получило применение азотирование при 570 °С в течение 5-10 ч в атмосфере, содержащей 50 % эндогаза и 50 % аммиака или 50 % метана и 50 % аммиака. В результате такой обработки на поверхности етали образуется тонкий карбонитридный слой (Fe, М)2-3 (N, С), обладающий меньшей хрупкостью и более высокой износостойкостью, чем чисто азотистая е-фаза. Твердость карбонитридного слоя на легированных сталях 600—1100HV. Такая обработка вильно повышает предел выносливости изделий.
Ионное азотирование. В последние годы получило применение азотирование в тлеющем разряде (ионное азотирование), которое проводят в разреженной азотсодержащей атмосфере (NH3 или N) при подключении обрабатываемых деталей к отрицательному электроду — катоду. Анодом является контейнер установки. Между катодом (деталью) и анодом возбуждается тлеющий разряд,
243

иионы газа, бомбардируя поверхность катода, нагревают ее до температуры насыщения. Процесс ионного азотирования реализуется в две стадии: первая — очистка поверхности катодным распылением; вторая — собственно насыщение.
Катодное распыление проводят в течение 5—60 мин при напряжении 1100—1400 В и низком давлении. В процессе катодного распыления температура поверхности детали не превышает 250 °С Азотирование ведут при температуре 470—580 °С, рабочем напряжении 400—1100 В, продолжительности процесса 1—24 ч.
Ионное азотирование сокращает общую длительность процесса, позволяет получить диффузионный слой регулируемого состава
истроения, незначительные деформации и обладает большой
экономичностью.
Азотирование в жидких средах (тенифер-процесс)1. Процесс проводят при температуре 570 °C в течение 0,5—3,0 ч в расплавленных цианистых солях (85 % соли, содержащие 40 % KCNO и 60 % NaCN + 15 % NO2CO3 или 55 % карбамида
(NH2)2CO и 45 % Na2CO3, через которые пропускают сухой воздух). Соли расплавляются в тигле из титана. Вследствие низкой температуры в сталь диффундирует в основном азот, образующийся при разложении цианистых солей. В результате обработки на поверхности стали возникает тонкий (7—15 мкм) карбонитридный слой (Fe, М)2-3 (N, C), обладающий высоким сопротивлением износу и не вклонный к хрупкому разрушению. Ниже карбонитридного слоя располагается слой, состоящий из твердого раствора азота в α-железе и избыточных кристаллов γ'- фазы. Общая толщина слоя 0,15—0,5 мм. Как и после газового азотирования, твердость слоя на углеродистых сталях 300—350 HV, а на легированных — 600— 1100 HV. Жидкое азотирование значительно повышает предел выносливости сталей. Достоинством процесса является незначительное изменение размеров и отсутствие коробления деталей, недостатком — токсичность и высокая стоимость цианистых солей. Этот процесс за рубежом широко применяют для обработки деталей автомобиля (коленчатых валов, шестерен и т. д.), штампов, npecс-форм и т. д.
4. ЦИАНИРОВАНИЕ
Цианированием называют процесс диффузионного насыщения поверхностного слоя стали одновременно углеродом и азотом при температуре 820—950 °С в расплавленных солях, содержащих группу NaCN.
Среднетемпературное цианирование. В этом процессе изделие нагревают до 820—860 °С в расплавленных солях, содержащих NaCN. Для получения слоя небольшой толщины (0,15—0,35 мм)
1 Тенифер (Tenifer) — от начальных слогов трех латинских слов: tenax — твердый; nitrogenium — азот; ferrum — железо.
244

процесс ведут при температуре 820—860 °С в ваннах (20— 25 % NaCN, 26—50 % NaCl и 25—50 % Na2CO3).
Продолжительность процесса обусловлена требуемой толщиной слоя и составляет 30—90 мин.
Цианистый натрий в процессе цианирования окисляется кислородом воздуха, и происходят следующие реакции:
Выделяющийся атомарный углерод и азот диффундируют в сталь. Цианированный слой, полученный при температуре 820— 860 °С, содержит 0,7 % С и 0,8—1,2 % N.
Цианирование при указанных сравнительно невысоких температурах позволяет выполнять закалку непосредственно из цианистой ванны. После закалки следует низкотемпературный отпуск (180—200 °С). Твердость цианированного слоя после термической обработки HRC 58—62. Цианированный слой по сравнению с цементованным обладает более высокой износостойкостью и эффективно повышает предел выносливости. Этот вид цианирования применяют для упрочнения мелких деталей.
Высокотемпературное цианирование. Для получения слоя большей толщины (0,5—2,0 мм) применяют высокотемпературное или глубокое цианирование при 930—950 °С в ванне, содержащей 8 % NaCN, 82 % ВаС12 и 10 % NaCl (состав ванны до расплавления). Зеркало ванны покрывают слоем графита во избежание больших потерь теплоты и угара цианистых солей. Время выдержки изделий в ванне для получения слоев указанной толщины составляет 1,5—6 ч.
При цианировании в ванне протекают следующие реакции:
Выделяющийся атомарный углерод и азот диффундируют
вжелезо. При указанных высоких температурах сталь с поверхности в большей степени насыщается углеродом (до 0,8— 1,2 %) и в меньшей — азотом (0,2—0,3 %). Строение цианированного слоя аналогично цементованному. После высокотемпературного цианирования детали охлаждают на воздухе, а затем для измельчения зерна закаливают с нагревом
всоляной ванне или печи и подвергают низкотемпературному отпуску.
Процесс цианирования по сравнению с процессом цементации требует меньшего времени для получения слоя заданной толщины,
245
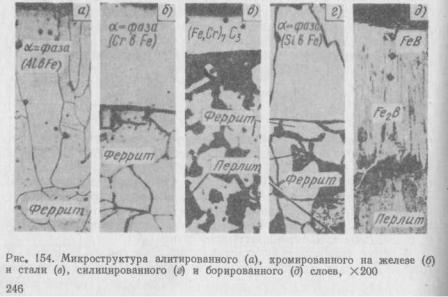
характеризуется значительно меньшими деформациями и короблением деталей сложной формы и более высоким сопротивлением износу и коррозии.
Недостатком цианирования является высокая стоимость, ядовитость цианистых солей и необходимость в связи с этим принятия специальных мер по охране труда.
5. БОРИРОВАНИЕ
Борированием называют химико-термическую обработку, заключающуюся в диффузионном насыщении поверхностного слоя стали бором при нагреве в соответствующей среде. Бориро-вание чаще выполняют при электролизе расплавленной буры (Na2B4O7). Изделие служит катодом. Температура насыщения 930—950 °С, выдержка 2—6 ч. Процесс можно вести и без электролиза в ваннах с расплавленными хлористыми солями (NaCl, ВаС12), в которые добавляют 20 % ферробора или 10 % карбида бора (В4С). Хорошие результаты получены при газовом бориро-вании. В этом случае насыщение ведут при температуре 850— 900 °С в среде диборана (В2Н6) или треххлористого бора (ВС13) в смеси сводородом.
Диффузионный слой состоит из боридов FeB (на поверхности) и Fe2B (рис. 154, д). Толщина слоя 0,1—0,2 мм. Борированный слой обладает высокой твердостью (1800—2000 HV), износостойкостью (главным образом, абразивной), коррозионной стойкостью, окалиностойкостью (до 800 °С) и теплостойкостью.
Борирование применяют для повышения износостойкости втулок грязевых нефтяных насосов, дисков пяты турбобура, вытяж-
ных, гибочных и формовочных штампов, деталей пресс-форм и машин для литья под давлением. Стойкость указанных деталей после борирования возрастает в 2—10 раз.
6. СИЛИЦИРОВАНИЕ
Насыщение поверхности стали кремнием называют си-
лицированием. Силицирование придает стали высокую коррозионную стойкость в морской воде, в азотной, серной и соляной кислотах и несколько увеличивает устойчивость против износа.
Силицированный слой (рис. 154, г) является твердым раствором кремния в α-железе. Под диффузионным слоем часто наблюдается слой перлита. Эго объясняется оттеснением углерода из диффузионного слоя вследствие пониженной растворимости его в кремнистом феррите.
Силицированный слой отличается повышенной пористостью, толщина его 300—1000 мкм. Несмотря на низкую твердость 200— 300 HV, силицированный слой обладает высокой износостойкостью после предварительной пропитки маслом при
170—200 °С.
Силицированию подвергают детали, используемые в оборудовании химической, бумажной и нефтяной промышленности (валики насосов, трубопроводы, арматура, гайки, болты и т. д.). Силицирование широко применяют для повышения сопротивления окислению при высоких температурах сплавов молибдена.
7. ДИФФУЗИОННОЕ НАСЫЩЕНИЕ МЕТАЛЛАМИ
Поверхностное насыщение стали алюминием, хромом, цинком и другими элементами называют диффузионным насыщением металлами. Изделие, поверхность которого обогащена этими элементами, приобретает ценные свойства, к числу которых относятся высокая жаростойкость, коррозионная стойкость, повышенная износостойкость и твердость.
В зависимости от метода переноса диффузионного элемента на насыщаемую поверхность различают следующие основные способы диффузионного насыщения металлами: 1) погружение в расплавленный металл, если диффундирующий элемент имеет низкую температуру плавления (например, алюминий, цинк); 2) насыщение из расплавленных солей, содержащих диффундирующий элемент (с электролизом и без электролиза); 3) насыщение из суб-лимированной фазы путем испарения диффундирующего элемента; 4) насыщение из газовой фазы (контактным и неконтактным методом), состоящей из галогенных соединений диффундирующего элемента.
Галогенные соединения диффундирующего элемента получают путем воздействия галоидного или галоидводородного газа на этот элемент или его ферросплав: Μ + n НГ MFn + (п/2) Н2. На границе раздела газовая фаза — обрабатываемая поверхность могут протекать следующие реакции:
247
1)реакция обмена: МГn + Fe → FFn + М;
2)реакциядиссоциации: МГn МГn;
3)реакция диспропорционироваиия: МГn + Μ + МГm, где Μ — диффундирующий металл; Г — соответствующий галоид (CI, F, Br); п и т — стехиометричеекие коэффициенты (целые числа).
Металл М, образующийся в результате реакции, адсорбируется обрабатываемой поверхностью и диффундирует в глубь обрабатываемого изделия. Наиболее часто применяют контактный метод насыщения из разовой фазы. Для этого обрабатываемую деталь упаковывают в порошкообразную ереду, состоящую из ферросплава диффундирующего элемента (50—75 %), А12О3 или шамота и 0,5—5,0 % NH4G1. При высокой температуре идет реакция диссоциации NH4G1 → NH3 + HGl, при этом НС1 взаимодействует с ферросплавом, образуя галоидные еоединения диффундирующего элемента. Процеее ведут при температуре 950— 1150 °С в течение 3—12 ч.
Впоследние годы насыщение металлами (например, хромом) проводят путем испарения диффундирующего элемента в вакууме. Насыщение поверхности стального изделия двумя и большим числом компонентов (А1 и Si, Gr и Si, В и ΑΙ и др.) позволяет в большей мере изменить свойства их поверхности. Ниже дана характеристика наиболее часто применяемых процессов диффузионной металлизации.
Алитирование — насыщение поверхности стали алюминием. В
результате алитирования сталь приобретает высокую окалиностойкость (до 850—900 °С), так как в процессе нагрева на поверхности алитированных изделий образуется плотная пленка окиси алюминия А12О3, предохраняющая металл от окисления. Алитированный слой обладает также хорошим сопротивлением коррозии в атмосфере и морской воде.
Структура алитированного слоя представляет собой твердый раствор алюминия в α-железе (см. рис. 154, а). Концентрация алюминия в поверхностной части слоя составляет ~30 %. Толщина слоя 200—1000 мкм. Твердость алитированного слоя (на поверхности) до 500 HV, износостойкость низкая. Алитированию подвергают топливники газогенераторных машин, чехлы термопар, детали разливочных ковшей, клапаны и другие детали, работающие при высоких температурах.
Хромирование — насыщение поверхности етальных изделий хромом. Этот процесс обеспечивает повышенную устойчивость стали к газовой коррозии (окалиностойкость) при температуре до 800 °С, высокую коррозионную стойкость в таких средах, как вода, морская вода и азотная кислота. Хромирование сталей, содержащих свыше 0,3—0,4 % С, повышает также твердость и износостойкость.
Диффузионный слой, получаемый при хромировании технического железа, состоит из твердого раствора хрома в α- железе
248
(см. рис. 154, б). Слой, полученный при хромировании етали, содержащей 0,3 % и более углерода, состоит из карбидов хрома (CΓ, Fe)7C3 или (Cr, Fe)23C6. На рис. 154, в показана структура хромированного елоя, полученного на стали с 0,45 % С. Слой состоит из карбидов хрома (Cr, Fe)7C3. Под елоем карбидов находится переходный слой с высоким содержанием углерода (0,8 %). Такие слои образуются в результате диффузии углерода из внутренних слоев к поверхности навстречу хрому. Углерод обладает большей скоростью диффузии, чем хром, поэтому для образования карбидного елоя используется не весь углерод и под карбидным слоем находится переходный слой с высоким содержанием углерода. Карбидный слой обладает высокой твердостью. Твердость слоя, полученного хромированием железа, 250—300 HV, а хромированием стали — 1200—1300 HV.
Хромирование используют для деталей паросилового оборудования, пароводяной арматуры, клапанов, вентилей, патрубков, а также деталей, работающих на износ в агрессивных средах.
Вопросы для самопроверки
1. Чем отличается химико-термическая обработка от термической обработки стали?
2.Насыщение железа проводится при температуре 1000 °С в течение 6 ч углеродом и хромом. В каком случае будет больше толщина слоя и почему?
3.Что понимают под термином «эффективная толщина слоя»?
4.В каких случаях применяют цементацию, нитроцементацию и азотирование?
5.Какое строение (структуру) имеет цементованный и азотированный слой? Увяжите строение слоя с диаграммой состояния Fe—Fe3C и Fe—Ν.
6.Укажите преимущества газовой цементации перед цементацией в твердом карбюризаторе.
7.Нужно получить диффузионный слой толщиной 1,5 мм и твердостью 60 HRC. Какой процесс обеспечит эти требования? Опишите технологию принятого процесса.
8.При каких температурах проводится процесс цементации? Почему?
9.Какая термическая обработка и зачем проводится после цементации
инитроцементации?
10.Какова структура цементованного слоя после термической обработки?
11.В каких случаях применяют нитроцементацию?
12.Каково основное преимущество эндотермической атмосферы для цементации (нитроцементации)?
13.Когда будут больше толщина и твердость азотированного слоя после азотирования при 520 °С 24 ч или при 600 °С 24 ч?
ГЛ А В А ХШ. ПОВЕРХНОСТНАЯ ПЛАСТИЧЕСКАЯ
ДЕФОРМАЦИЯ
Повышение долговечности деталей машин методом поверхностного пластического деформирования (ППД) или поверхностного наклепа широко используется в промышленности для повышения сопротивляемости малоцикловой и многоцикловой усталости деталей машин. На рис. 155 приведены схемы различных методов ППД. Поверхностное упрочнение достигается (ГОСТ 18296— 72): 1) дробеструйным наклепом за счет кинетической энергии потока
249
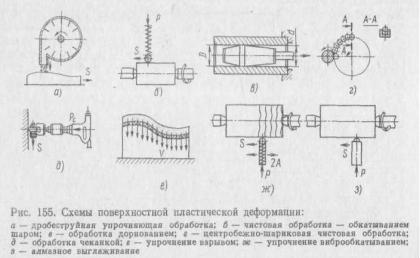
чугунной или стальной дроби; поток дроби на обрабатываемую поверхность направляется или скоростным потоком воздуха, или роторным дробеметом (рис. 155, а); 2) центробежно-шариковым наклепом за счет кинетической энергии стальных шариков (роликов), расположенных на периферии вращающего диска; при вращении диска под действием центробежной силы шарики отбрасываются к периферии обода, взаимодействуют с обрабатываемой поверхностью и отбрасываются в глубь гнезда; 3) накатыванием стальным шариком или роликом (60 HRC) (рис. 155, б); передача нагрузки на ролик может быть с жестким или упругим контактом между инструментом и обрабатываемой поверхностью (разновидности этих способов — накатывание вибрирующим роликом, раскатывание отверстий роликами и др.); 4) алмазным выглаживанием оправкой с впаенным в рабочей части алмазом (рис. 155, з); оно позволяет получать блестящую поверхность с малой шероховатостью.
Толщина деформированного слоя зависит от приложенной силы Ρ и предела текучести σ0,2: x = √Ρ/(2σ0,2); средние контактные нагрузки для низкоуглеродистых сталей 1600—1800 МПа, среднеуглеродистых 1800—1900 МПа и высокоуглеродистых 2700—3000 МПа. При обкатке шарами диаметром 10—20 мм подача составляет 0,1—0,2 мм/об при скорости обкатывания 50— 100 м/мин. При алмазном выглаживании сила выглаживания 50— 350 Н, подача 0,02—0,1 мм/об и скорость 20—200 м/мин. Радиус рабочей части алмаза при обработке мягких материалов (низко-углеродистая сталь, цветные сплавы) равен 2—3 мм и твердых материалов (58—64 HRC)— 0,5—1,5 мм.
При обкатывании и выглаживании в зоне контакта повышается температура до 350 °С и выше. Температура нагрева не должна превышать температуру рекристаллизации, снимающей эффект
250