
ТМБ, част1 / Конспект / ТМБ1_Лекц_я 07_Основи теорii розмiрних ланцюгiв
.pdf
7. ОСНОВИ ТЕОРІЇ РОЗМІРНИХ ЛАНЦЮГІВ ДЛЯ РІШЕННЯ ЗАДАЧ ТЕХНОЛОГІЇ МАШИНОБУДУВАННЯ
1.Основні методи досягнення точності у машинобудуванні.
2.Основні поняття та визначення теорії розмірних ланцюгів. Класифікація розмірних лан- цюгів.
3.Розмірний аналіз технологічного процесу.
4.Похибка замикальної ланки розмірного ланцюга та шляхи оптимізації її точності.
5.Основні методи досягнення точності в машинобудуванні.
6.Типовий порядок розрахунку розмірних ланцюгів.
7.1.Основні методи досягнення точності у машинобудуванні
Якість роботи кожної машини, незалежно від її конструкції та принципу дії, залежить, голо- вно, від характеру і точності з’єднань пар тертя її деталей. Якщо величини зазорів, які характери- зують ці з’єднання, у процесі роботи внаслідок спрацювання (стирання) збільшуються і виходять за допустимі межі, то машина виходить з ладу. На точність з’єднань суттєвим чином впливає точ- ність виконання окремих деталей. Досягти цієї точності можна двома принципово різними спосо- бами – методом залежного і незалежного оброблення.
Метод з а л е ж н о г о о б р о б л е н н я , чи, інакше, метод індивідуальної пригонки полягає в тому, що за виготовленою однією з деталей з’єднання виготовляють другу, без витримування при цьому певного точно визначеного розміру, але примірюючи („ приганяючи”) її в процесі роботи до вже виготовленої деталі таким чином, щоб, врешті-решт, мати з’єднання заданого характеру. Оцін- ка такого з’єднання носить суб’єктивний характер. Виготовлена раніше деталь відіграє при цьому роль калібру. Метод індивідуальної пригонки застосовується, головно, в одиничному та дрібносе- рійному виробництві.
Метод н е з а л е ж н о г о о б р о б л е н н я полягає в тому, що обидві деталі з’єднання вико- нуються незалежно одна від одної, навіть у різних місцях і в різний час. Точність виготовлених де- талей при цьому повинна бути настільки високою, щоб всі вони давали з’єднання потрібної якості без будь-якої підгонки. При цьому методі досягнення точності деталі виготовляються зазвичай на налаштованих верстатах і вимірюються за допомогою системи калібрів. Оскільки будь-яка деталь з’єднання може бути замінена іншою такою ж деталлю, то вказаний метод виготовлення називають ще м е т о д о м в з а є м о з а м і н н о с т і , що є основним методом досягнення точності в серійному і масовому видах виробництва.
При методі і н д и в і д у а л ь н о г о п і д б о р у до взятої довільно першої деталі шляхом про- би підбираються інші деталі до тих пір, поки не буде потрібної посадки. Основним недоліком цьо- го методу є, очевидно, суб’єктивність у встановленні якості посадки. Цього недоліку не має метод селекції, який основується на розсортуванні з’єднуваних деталей за допомогою спеціальних сорту- вальних калібрів на декілька розмірних груп і з’єднуванні їх між собою в межах однойменних груп. Коли закони розподілу розмірів з’єднуваних деталей однакові, то і розмірні групи з’єднуваних деталей можуть бути однаковими. Коли ж закони розподілу різні, то розмірні інтерва- ли повинні по можливості підбиратися так, щоб кількість деталей у відповідних розмірних групах була приблизно однаковою.
7. Основи теорії розмірних ланцюгів для рішення задач технології машинобудування
Для того, щоб характер посадок для розмірних груп залишався однаковим, необхідно, щоб початкові поля допусків отвору і вала 6А і бв були однакові. Коли ця умова не виконується, то ха- рактер посадок різних розмірних груп неоднаковий і різниці будуть тим більші, чим більша різни- ця між полями допусків з’єднуваних деталей та чим більша кількість розмірних груп, на які ці поля допусків розділені. При такому розміщенні полів допусків з’єднання перших двох розмірних груп дає рухомі посадки, а третя і четверта розмірні групи — відповідно посадки перехідні та нерухомі.
При с е л е к ц і й н о м у м е т о д і практичне значення має кількість деталей у відповідних розмірних групах. Чим більша різниця в кількості деталей у відповідних розмірних групах, тим бі- льша кількість деталей, які після здійснення з’єднань виявляться без відповідних пар. Це може ста- тися тоді, коли розміри з’єднуваних деталей підлягають різним законам розподілу.
Крім перечислених методів досягнення точності з’єднань досить широке застосування ма- ють також методи досягнення точності за д о п о м о г о ю к о м п е н с а т о р і в , тобто ланок, за ра- хунок яких компенсуються неточності виконання окремих деталей з’єднання. Компенсатори мо- жуть бути рухомі або нерухомі.
Нерухомі компенсатори — це деталі, які входять в багатоелементні з’єднання і при збиранні підганяються таким чином, щоб величина сумарного зазора з’єднання знаходилася в за- даних границях. Нерухомим компенсатором може бути як спеціально введена в з’єднання деталь- компенсатор, так і одна з робочих деталей з’єднання. Основним недоліком нерухомих компенсато- рів є те, що вони в процесі збирання вимагають пригонки, що знижує продуктивність праці. Назва- ього недоліку не мають рухомі компенсатори, положення яких при збиранні вузла відповідним чи- ном регулюється. Можливість застосування такого методу досягнення точності повинна бути за- кладена вже в самій конструкції вузла. Прикладом рухомого компенсатора для досягнення потріб- ного зазора може бути рухома втулка В, показана на рис. 5. 4, а. Переміщення цієї втулки в осьо- вому напрямку та фіксація вибраного положення, наприклад штифтом III або в інший спосіб, дає змогу відрегулювати зазор 3 на потрібну величину. Приклад розв’язання цієї ж задачі за допомо- гою нерухомого компенсатора К (шайби) показаний на рис. 5. 4, б. Конструкцій нерухомих і рухо- мих компенсаторів є дуже багато. Останнім часом починають появлятися конструкції автоматично регульованих компенсаторів, які у процесі роботи з’єднання самі настроюються на потрібні роз- міри.
7.2. Основні поняття та визначення теорії розмірних ланцюгів. Класифікація розмірних ланцюгів.
У найбільш загальному випадку будь-яке з’єднання деталей можна розглядати як сукуп- ність взаємно пов’язаних між собою розмірів. Коли ці розміри зв’язані між собою так, що утворю- ють замкнений контур, визначають взаємне розташування поверхонь чи осей поверхонь однієї де- талі чи декількох деталей складального з’єднання і впливають на інший розмір, точність якого ха- рактеризує точність усього з’єднання, то таку сукупність розмірів називають р о з м і р н и м л а - н ц ю г о м . Розміри, які входять у розмірний ланцюг, називаються л а н к а м и . Розмір, який най- більш суттєво впливає на характер роботи, і в процесі механічного оброблення чи складання отри-
мується останнім, називається з а м и к а л ь н и м р о з м і р о м або з а м и к а л ь н о ю л а н к о ю .
Замикальна ланка є вихідною при постановці задачі чи отримується останньою в результаті її рі- шення. Коли при розрахунку розмірного ланцюга задаються вимоги до замикальної ланки чи вели- чини її допуску, то таку ланку називають в и х і д н о ю . Інші ланки розмірного ланцюга називають-
ся с к л а д о в и м и .
Приклади поставленої задачі: необхідно забезпечити необхідний зазор між шпонкою та шпонковим пазом (рис. 7.1, а) або валом та втулкою (рис. 7.1, б).
2
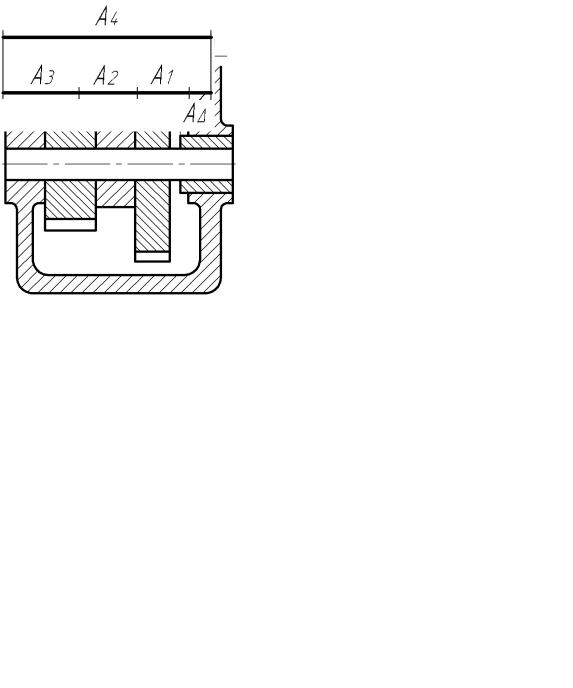
7. Основи теорії розмірних ланцюгів для рішення задач технології машинобудування
|
|
|
|
|
|
|
|
|
|
|
|
|
|
|
|
|
|
|
а) |
|
б) |
|
|
Рис. 7.1. Інженерні задачі, у яких використовуються розмірний ланцюг. |
|
||||
Складові ланки розмірного ланцюга можуть бути з б і л ь ш у в а л ь н и м и чи з м е н ш у - |
|||||
в а л ь н и м и , залежно від того, як вони впливають на замикальну ланку. Збільшувальна ланка – |
це |
||||
ланка, зі збільшенням якої збільшується також розмір замикальної ланки. Зменшувальна ланка – |
це |
ланка, зі збільшенням якої розмір замикальної ланки зменшується. Для з’єднання, зображеного на рис. 7.2 а, збільшувальним розміром є розмір А4, зменшувальними – розміри А1, А2, А3. Розмір А є замикальною ланкою.
|
|
|
|
|
|
|
|
|
а) |
|
б) |
Рис. 7.2. Розмірний ланцюг: а) схема з’єднання; б) схема розмірного ланцюга.
Взаємне розташування деталей складальних з’єднань чи розташування складальних елемен- тів виробів, а також окремих поверхонь деталей визначається лінійними і кутовими розмірами, що встановлюють відстані між відповідними поверхнями чи осями окремих деталей або складальних елементів, які утворюють замкнуті розмірні ланцюги.
Вихідна ланка РЛ визначає точність розмірів складових ланок. Щодо вихідної ланки визна- чаються допуски і граничні відхилення розмірів складових ланок.
У процесі обробки заготовки чи в процесі складання з’єднання вихідна ланка стає замика- льною, тому що в цьому випадку вона остаточно формується в останню чергу, замикаючи розмір-
3
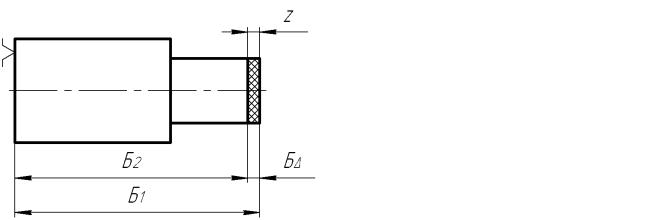
7. Основи теорії розмірних ланцюгів для рішення задач технології машинобудування
ний ланцюг. На робочих кресленнях деталей розмір замикальної (вихідної) ланки звичайно не вказується. У складальних РЛ замикальною ланкою можуть бути зазор, лінійний чи кутовий розміри, точність яких обумовлюється в технічних умовах. У технологічних РЛ замикальною ланкою часто є розмір припуску на обробку заготовки чи той конструкторський розмір, що при обробці заміняється технологічними розмірами і виходить у результаті виконання останніх.
Складова ланка РЛ, із збільшенням якого замикальна ланка збільшується, називається збі- льшувальною, а ланка, із збільшенням якого замикальна ланка зменшується - зменшувальною.
Компенсувальна ланка – складова ланка РЛ, із зміною розміру якої досягається потрібна точність.
Конструкторський РЛ визначає відстані чи відносні повороти між поверхнями чи осями поверхонь деталей у виробі. При розробці технологічних процесів складання конструкторські роз- мірні ланцюги часто називаються складальними.
Технологічний РЛ визначає відстані між поверхнями виробу при виконанні операцій обро- бки чи складання, при настроюванні верстата чи розрахунку міжопераційних розмірів і припусків. Приклади технологічних РЛ: на рис. 7.1 технологічний РЛ визначає необхідні віддалі при складан- ні; на рис. 7.2 – при механічному обробленні; на рис. 7.3 – визначає значення необхідного припус- ку.
|
|
|
|
|
|
|
|
|
|
|
|
Рис. 7.2. Розмірний ланцюг, який визначає |
Рис. 7.3. Розмірний ланцюг, який визначає |
||
необхідні віддалі при механічному обробленні. |
значення необхідного припуску. |
Вимірювальний РЛ – РЛ, який виникає при визначенні віддалей (розмірів), відносних пово- ротів між поверхнями чи їх осями або твірними поверхнями виробів.
У залежності від розташування розмірів РЛ поділяються на: лінійні (позначаються як або
), як складаються з взаємно паралельних лінійних розмірів, що позначаються
прописними літерами кирилиці; кутові, ланками яких є кутові розміри ( або
), які по- значаються малими грецькими літерами (за винятком літер α, δ, ξ, λ, ω) і плоскі, ланки яких розта- шовані в одній чи декількох паралельних площинах; просторові РЛ, ланки яких знаходяться в не- паралельних площинах.
Коефіцієнт, що характеризує ступінь впливу розміру і відхилення складового ланки на роз- мір, а також відхилення замикальної ланки, називається передавальним відношенням ξ. Для лан- цюгів з непаралельними ланками передавальні відносини змінюються в межах: 0 ≤ ξ ≤ 1 - для збі- льшувальних ланок і −1 ≤ ξ ≤ 0 - для зменшувальних складових ланок.
Для плоских лінійних ланцюгів з паралельними ланками передавальні відносини рівні: ξ = +1 - для збільшувальних і ξ = -1 - для зменшувальних ланок.
4
7. Основи теорії розмірних ланцюгів для рішення задач технології машинобудування
7.3. Розмірний аналіз технологічного процесу.
Головна задача розмірного аналізу технологічного процесу - правильне та обґрунтоване ви- значення проміжних та остаточних розмірів і допусків на них. Особливо цього потребують промі- жні розміри, що зв’язують протилежні поверхні. Визначення припусків на такі поверхні розрахун- ково-аналітичним або табличним методом дуже ускладнене. В той же час робота на налагоджених верстатах потребує детальної пророблення всіх проміжних розмірів з тим, щоб на заключних опе- раціях (переходах) автоматично забезпечувались остаточні розміри. Правильне розв’язання цієї задачі забезпечує розмірний аналіз технологічного процесу, який складається з ряду етапів. Роз- глянемо ці етапи детальніше.
7.3.1. Розробка розмірної схеми технологічного процесу.
Розмірну схему технологічного процесу складають і оформляють так. Креслять ескіз деталі. Для тіл обертання достатньо однієї проекції. Для корпусних деталей можуть знадобитися дві або навіть три проекції залежно від розташування розмірів довжин. Над деталлю вказують розміри до- вжин з допусками, задані конструктором. Для зручності складання розмірних ланцюгів конструк- торські розміри позначають буквою Аі. На ескіз деталі умовно наносять припуски zm. Всі поверхні деталі нумерують зліва направо. Через нумеровані поверхні проводять вертикальні лінії. Між вер- тикальними лініями знизу вгору вказують технологічні розміри, які отримують при виконанні ко- жного технологічного переходу. Технологічні розміри позначають буквою Sk. Розміри заготовки позначають буквою Зr. Справа від розмірної схеми для кожної операції складають технологічні розмірні ланцюги.
7.3.2. Виявлення технологічних розмірних ланцюгів.
Якщо технологічний розмір збігається з конструкторським, то отримують дволанковий роз- мірний ланцюг.
Замикаючі ланки на всіх схемах розмірних ланцюгів беруть у квадратні дужки. Виявлення розмірних ланцюг за розмірною схемою починають з останньої операції, тобто за схемою згори вниз. У такій же послідовності розраховують розмірні ланцюги. При цьому необхідно, щоб у кож- ному новому ланцюгу був невідомим тільки один розмір. Спираючись на схеми розмірних ланцю- гів, визначають типи ланок та складають вихідні рівняння, а потім їх розраховують. Виявлення технологічних розмірних ланцюгів за розмірною схемою ТП в ряді випадків може виявитись дуже трудомістким, оскільки технологічні розмірні ланцюги часто є зв’язаними. Тому при їх побудові необхідно, щоб у кожному розмірному ланцюгу був лише один конструкторський розмір чи один розмір припуску, який є замикаючою ланкою технологічного розмірного ланцюга. Складнощі ви- явлення технологічних розмірних ланцюгів за розмірною схемою пояснюються тим, що вони ви- ступають на схемах не явно, а у прихованому вигляді. Виявлення технологічних розмірних ланцю- гів можна значно спростити і полегшити, скориставшись теорією графів.
7.3.3. Виявлення технологічних розмірних ланцюгів за допомогою графів.
Теорія графів - одна з математичних дисциплін, яка вивчає складні структури і системи, що складаються з багатьох елементів і зв’язків між ними. Деталь у процесі її виготовлення можна роз- глядати як геометричну структуру, яка складається з багатьох поверхонь та зв’язків (розмірів) між ними. Тому таку структуру доцільно вивчати за допомогою графів.
Граф - це фігура, яка складається із точок і ліній, що з’єднують ці точки. Точки називаються вершинами, а лінії, що їх з’єднують, - дугами чи ребрами графа, Ребро вважається орієнтованим, якщо на ньому є стрілка, що вказує, з якої вершини воно виходить і в яку вершину входить. Якщо такої стрілки на ребрі немає, то воно вважається неорієнтованим. Граф є орієнтованим чи неорієн- тованим залежно від назви ребер. Якщо пару вершин з’єднати кількома ребрами, то такі ребра на- зиваються кратними. Послідовність ребер, в якій два сусідніх ребра мають спільну вершину, на- зивається маршрутом. Якщо початок і кінець маршруту знаходяться в одній вершині, то такий ма- ршрут називається циклічним. Якщо в кожному маршруті кожне ребро зустрічається один раз, то такий маршрут називається ланцюгом. Як що ланцюг замкнений, тобто починається і закінчується
5
7. Основи теорії розмірних ланцюгів для рішення задач технології машинобудування
в одній вершині, його називають циклом. Коли кожну вершину можна з’єднати з будь-якою іншою вершинок деяким ланцюгом, то граф є зв’язковим.
Якщо вважати поверхні заготовки і деталі за вершини, зв’язки між ними (розміри) - за реб- ра, то креслення деталі з конструкторськими і технологічними розмірами можна представити у ви- гляді двох дерев. Дерево з конструкторськими розмірами і розмірами припусків на обробку нази- вається вихідним, а дерево з технологічними розмірами - похідним або технологічним. Якщо тепер обидва дерева сумістити, то такий суміщений граф дає змогу в закодованій формі представити геометричну структуру технологічного процесу обробки деталі. В такому графі всі розмірні зв’язки та технологічні розмірні ланцюги з неявних перетворюються на явні. З’являється можли- вість, не звертаючись до креслення, а використовуючи лише ту інформацію, яку несе граф, прово- дити всі необхідні дослідження і розрахунки. Будь-який замкнений .контур на суміщеному графі, що складається з ребер вихідного та технологічного дерева, створює технологічний розмірний ла- нцюг. У ньому ребро вихідного дерева є замикальною ланкою, а ребра технологічного дерева - складовими ланками. В термінології теорії графів розмірний ланцюг - це шлях у похідному дереві, що заданий ребром вихідного дерева. Для того, щоб вказати шлях, слід перерахувати ребра, за якими треба йти. Якщо відома-довжина ребер (розміри, допуски) похідного дерева в даному лан- цюгу, то можна знайти і довжину шляху, тобто розмір чи допуск замикальної ланки. Кожний роз- мірний ланцюг створює цикл. У будь-якому розмірному ланцюгу одне ребро повинно бути ребром вихідного дерева (конструкторський розмір чи припуск), а інші— ребрами похідного дерева, тобто технологічними розмірами. Найкоротшим є цикл, який складається з двох ребер. Йому відповідає дволанковий розмірний ланцюг, в якому ребро вихідного дерева (конструкторський розмір) є за- микальною ланкою, а ребро похідного дерева (технологічний розмір) — складовою ланкою.
Для побудови графа розмірних ланцюгів необхідно попередньо побудувати розмірну схему технологічного процесу. Спочатку будують похідне, потім вихідне дерево, і після цього дерева су- міщають. Цим отримується граф технологічних розмірних ланцюгів. Вершини (поверхні) позна- чають кружечками, всередині вказують номери. Ребра похідного дерева зображають прямими ліні- ями зі стрілками на кінці, що показують, в яку вершину вони входять. Ребра вихідного дерева зо- бражають у вигляді дуг, коли вони є конструкторськими розмірами, або у вигляді хвилястих ліній, коли вони є розмірами припусків.
При побудові похідного дерева коренем вибирають вершину (поверхню), до якої за розмір- ною схемою процесу не підходить жодна стрілка. Цю вершину слід викреслити у вигляді подвій- ного кружка і провести з неї ті ребра, що дотикаються до неї своїми неорієнтованими кінцями. На орієнтованих кінцях цих ребер слід вказати кружечками вершини (поверхні), в які вони впирають- ся своїми стрілками. На цьому побудова похідного дерева закінчується.
Аналогічно будують вихідне дерево . Його ребра можна не орієнтувати, тому при побудові можна вибирати коренем будь-яку вершину (поверхню) на кресленні готової деталі. Порядок роз- ташування вершин на вихідному дереві повинен бути таким самим як і на похідному. Дуги озна- чають конструкторські розміри, а хвилясті лінії - розміри припусків. Оскільки ребра вихідного де- рева не орієнтовані, то вони вказують лише на те, які вершини дерева зв’язані між собою констру- кторськими розмірами чи розмірами припусків.
Після побудови кожного дерева перевіряють правильність його побудови за такими ознака-
ми:
1.Кількість вершин у кожного дерева повинно дорівнювати кількості поверхонь на розмір- ній схемі технологічного процесу.
2.Кількість ребер у кожного дерева повинно бути однаковим і дорівнювати кількості вер- шин, зменшеному на одиницю.
3.До кожної вершини похідного дерева, крім кореневої, повинна підходити лише одна стрі- лка орієнтованої ребра, а до кореневої вершини - жодної.
4.Дерева не повинні мати замкнених контурів та розривів.
6
7. Основи теорії розмірних ланцюгів для рішення задач технології машинобудування
Після перевірки правильності побудови дерев їх суміщають так, щоб вершини з однаковими порядковими номерами збігалися. На практиці два дерева окремо не будують, а роблять так: спо- чатку будують похідне дерево, а потім на ньому ж — вихідне, в результаті чого замикання дерев відбувається саме по собі. При побудові дерев вершини слід розташовувати так, щоб при їх сумі- щенні не перетинались ребра. Суміщений граф похідного та вихідного дерев і буде графом техно- логічних розмірних ланцюгів.
Разом з виявленням технологічних розмірних ланцюгів потрібно за графом визначити також знаки складових ланок за таким правилом. Замикаючій ланці присвоюють знак «—» і, починаючи з цієї ланки, обходять замкнений контур у певному напрямі. Оскільки ребро замикаючої ланки зв’язує дві вершини, з яких одна має менший, а друга — більший порядковий номер, то обхід лан- цюга починають із вершини з меншим номером. Якщо в напрямі обходу наступне ребро ланцюга буде з’єднувати вершину з меншим порядковим номером і вершину з більшим номером, то ребру присвоюють знак «+», якщо ж ребро з’єднує вершину з більшим номером і вершину з меншим но- мером, то йому присвоюють знак «—». Одночасно з визначенням знаків розмірного ланцюга скла- дають розрахункові рівняння з умови, що алгебраїчна сума всіх ланок розмірного ланцюга, вклю- чаючи замикаючу, дорівнює нулю. Потім ці рівняння перебудовують у вихідні, тобто складені від- носно замикаючої ланки. В початковому (вихідному) рівнянні (в правій частині) ланки, що мають знак «+», є збільшувальними, а ті, що мають знак мінус, -зменшувальними. Виявлення і розрахунок технологічних ланцюгів за графом розпочинають з дволанкових ланцюгів, а потім у такій послідо- вності, щоб у кожному ланцюгу була лише одна невідома за величиною ланка, а інші ланки були б визначені в розрахунках попередніх розмірних ланцюгів. Для виконання цієї умови слід починати виявлення і розрахунок розмірних ланцюгів у послідовності, зворотній до виконання операцій та переходів, тобто починати з останньої операції й останнього переходу і закінчувати першим пере- ходом чи розміром заготовки.
Граф технологічних розмірних ланцюгів не лише полегшує виявлення ланцюгів, але й дає змогу виявити помилки в технології чи кресленні. Наприклад, якщо при складанні похідного чи вихідного дерева виявиться розрив між вершинами або з’явиться замкнений контур, то це вказує в першому випадку на відсутність потрібних розмірів у прийнятій технології, а в другому — на на- явність зайвих розмірів.
7.4. Похибка замикальної ланки розмірного ланцюга та шляхи оптимізації її то- чності.
При встановленні похибки замикальної ланки РЛ, розрізняють два випадки:
1)визначення похибки при виготовленні однієї деталі чи виробу;
2)визначення похибки при виготовленні партії деталей чи виробів.
Для першого випадку для плоских РЛ з паралельними ланками похибка ЗЛ:
m
Ω = Ω1 + Ω2 + ... + Ωm = ∑Ωi ;
i=1
для кутових РЛ (сума похибок проекцій):
m
Ω = Ω1 cos α1 + Ω2 cos α 2 + ... + Ωm cos α m = ∑Ωi cos αi
i=1
Для другого випадку для визначення похибки ЗЛ РЛ правильніше говорити е про похибку, а про поле розсіювання ЗЛ. Для знаходження залежності між полем розсіювання і значенням ЗЛ ко- ристуються повним диференціалом. Враховуючи, що ЗЛ – функція складових ланок:
A = f (A1 , A 2 , ..., Am-1 )
7
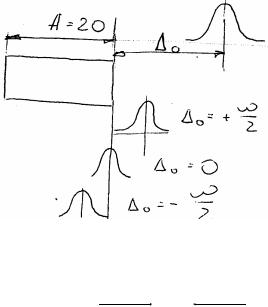
7. Основи теорії розмірних ланцюгів для рішення задач технології машинобудування
dA = |
∂A |
dA1 + |
∂A |
dA 2 + ... + |
∂A |
dAm−1 |
|
∂A1 |
∂A2 |
∂Am−1 |
|||||
|
|
|
|
Замінивши диференціал приростами, які представляють собою відповідні поля розсіювання, отримаємо:
ωA = |
∂A |
|
ωA1 + |
∂A |
|
ωA 2 + ... + |
∂A |
|
ωAm−1 |
||||||
∂A1 |
∂A2 |
|
∂Am−1 |
||||||||||||
або |
|
|
|
|
|
m−1 |
|
∂A |
|
|
|
|
|
||
|
|
|
|
|
ωA |
|
|
ωAi |
|
|
|
||||
|
|
|
|
|
|
|
|
|
|
||||||
|
|
|
|
|
= ∑ |
|
∂Ai |
|
|
|
|
||||
|
|
∂A |
|
i=1 |
|
|
|
|
|
|
|||||
У цих рівняннях значення |
- передавальні відношення (коефіцієнти приведення). Вони |
||||||||||||||
|
∂Ai |
показують вплив величини поля розсіювання кожної складової ланки на величину поля розсіюван- ня ЗЛ.
Поле розсіювання може зміщуватися відносно розрахункової (номінальної) величини. Для того, щоб це зміщення врахувати, вводиться поняття координати середини поля розсіювання, яка позначається як o ( o A1 - для ланки А1) і є віддалю від номіналу до середини поля розсіювання.
Рис. 7.4. Поле розсіювання ЗЛ.
Координата середини поля розсіювання ЗЛ завжди дорівнює алгебраїчній сумі координат середин полів розсіювання складових ланок:
n |
|
|
|
|
m−1 |
ωAi |
o A = ∑ o ωAi − |
∑ o |
|||||
i=1 |
|
∂A |
|
|
i=n+1 |
|
m−1 |
|
|
ωAi , можна зробити висновок, що підвищити |
|||
|
|
|||||
Проаналізувавши формулу ωA = ∑ |
|
∂Ai |
|
|||
i=1 |
|
|
|
|
|
точність ЗЛ можна за рахунок:
1)зменшення полів розсіювання складових ланок ωAi ;
2)зменшення кількості складових ланок РЛ (зменшення m);
3) зменшення величини передавальних відношень |
∂A |
кожної складової ланки. |
∂Ai |
8
7. Основи теорії розмірних ланцюгів для рішення задач технології машинобудування
7.5. Основні методи досягнення точності в машинобудуванні.
Якість роботи кожної машини, яким б не були її конструкція і принцип дії, залежить, голо- вним чином, від характеру і точності з’єднань її пар тертя. Якщо величини зазорів, що характери- зують ці з’єднання, у процесі роботи внаслідок спрацювання (стирання) збільшуються і виходять за допустимі межі, то машина виходить із ладу.
Відновлення працездатності машини - це відновлення зазорів тертьових частин до їх перві- сного стану.
Точність виконання окремих деталей, з яких складається машина, має суттєве значення, оскільки від неї залежить точність з’єднань. Досягти цієї точності можна двома принципово різни-
ми способами - методом залежного оброблення, або методом незалежного оброблення.
Метод залежного оброблення (або інакше метод індивідуальної пригонки) полягає в тому, що за виготовленою наперед однією з деталей з’єднання виготовляють іншу деталь, не додержую- чись при цьому якогось точно визначеного розміру, але примірюючи її в процесі роботи до вигото- вленої раніше деталі так, щоб, врешті-решт, мати з’єднання потрібного характеру. Оцінка такого з’єднання носить суб’єктивний характер. Виготовлена раніше деталь відіграє при цьому роль нор- мального калібру.. Коли деталі великі та важкі, і використовувати раніше виготовлену деталь в ро- лі калібру неможливо, метод індивідуальної пригонки здійснюється так: вимірюють точно посадо- чний розмір виготовленої раніше деталі, і його значення записують на окремому бланку (формуля- рі). Другу деталь виконують таким чином, щоб вона разом з першою дала з’єднання потрібного характеру. Цей метод часто ще називають методом роботи «за формуляром».
Метод незалежної обробки полягає в тому, що обидві деталі з’єднання виконуються неза- лежно одна від іншої, звичайно, навіть у різних місцях і в різний час. Точність виконаних деталей мусить при цьому бути такою високою, щоб попри все давати з’єднання потрібної якості без будь- якої підгонки. При цьому методі досягнення точності деталі виготовляються, звичайно, на настро- єних верстатах і вимірюються за допомогою системи калібрів. Оскільки при цьому будь-яка деталь з’єднання може бути замінена іншою такою ж деталлю, то такий метод виготовлення називається методом взаємозамінності, що є основним методом досягнення точності в серійному і масовому видах виробництва, тоді як метод індивідуальної пригонки застосовується, головним чином, в оди- ничному та дрібносерійному виробництві.
Взаємозамінність деталей при незалежному методі виробництва може бути повною або не- повною. Повну взаємозамінність маємо тоді, коли всі пари чи групи деталей, що утворюють з’єднання, можна довільно комбінувати одні з іншими, і всі вони дають при цьому потрібні посад- ки. При неповній взаємозамінності деяка кількість пар чи груп деталей дає посадки, допуски яких виходять за допустимі межі. Повна взаємозамінність здійснюється тим легше, чим менш точним може бути з’єднання, тобто, чим меншою має бути точність виготовлення деталей.
При дуже високій точності з’єднань повна взаємозамінність стає економічно невигідною, тому що собівартість виготовлення деталей дуже зростає з підвищенням їх точності.
При дуже високій точності з’єднань (наприклад, при з’єднанні поршневого пальця з порш- нем двигуна внутрішнього згоряння) економічнішою є робота за методом неповної взаємозамінно- сті, тобто виготовляти деталі з меншою точністю, ніж цього вимагала б повна взаємозамінність, але зате підбирати в деяких межах деталі одні до інших. При неповній взаємозамінності потрібної точності можна досягти двома способами: методом індивідуального підбору або методом селекції. Обидва методи основуються на тому, що деталі з’єднань з’єднуються з собою не довільно, а по відповідних інтервалах поля розсіювання, тобто менші деталі з меншими і більші з більшими.
При методі індивідуального підбору до взятої довільно першої деталі шляхом проби підби- раються інші деталі до тих пір, поки не буде потрібної посадки. Основним недоліком цього методу є, очевидно, суб’єктивність у встановленні якості посадки. Цього недоліку не має метод селекції, який основується на розсортуванні з’єднуваних деталей за допомогою спеціальних сортувальних калібрів на декілька розмірних груп і з’єднуванні їх між собою в межах однойменних груп (рис.
9
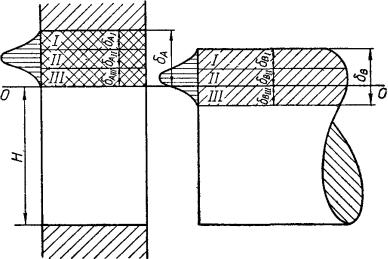
7. Основи теорії розмірних ланцюгів для рішення задач технології машинобудування
7.5). Коли закони розподілу розмірів з’єднуваних деталей однакові, то і розмірні групи з’єднуваних деталей можуть бути однаковими. Коли ж закони розподілу різні, то розмірні інтервали повинні по можливості підбиратися так, щоб кількість деталей у відповідних розмірних групах була приблиз- но однаковою.
Для того, щоб характер посадок для розмірних груп залишався однаковим, необхідно, щоб початкові поля допусків отвору і вала були однакові. Коли ця умова не виконується, то характер посадок різних розмірних груп неоднаковий і різниці будуть тим більші, чим більша різниця між полями допусків з’єднуваних деталей та чим більша кількість розмірних груп, на які ці поля допу- сків розділені.
Рис. 7.5. Розсортування деталей на розмірні групи при забезпеченні потрібної якості з’єд- нань методом селекції.
Крім перерахованих методів досягнення точності з’єднань досить широке застосування ма- ють також методи досягнення точності за допомогою компенсаторів, тобто ланок, за рахунок яких компенсуються неточності виконання окремих деталей з’єднання. Компенсатори можуть бути ру- хомими чи нерухомими.
Нерухомі компенсатори – це деталі, які входять в багатоелементні з’єднання і при складан- ні підганяються таким чином, щоб величина сумарного зазору з’єднання знаходилася в заданих границях. Нерухомим компенсатором може бути як спеціально введена в з’єднання деталь- компенсатор, так і одна з робочих деталей з’єднання. Основним недоліком нерухомих компенсато- рів є те, що вони в процесі збирання вимагають пригонки, що знижує продуктивність праці. Назва- ного недоліку не мають рухомі компенсатори, положення яких при складанні вузла відповідним чином регулюється. Можливість застосування такого методу досягнення точності повинна бути закладена вже в самій конструкції вузла. Конструкцій нерухомих і рухомих компенсаторів є дуже багато. Останнім часом починають появлятися конструкції автоматично регульованих компенсато- рів, які у процесі роботи з’єднання самі настроюються на потрібні розміри.
7.6. Типовий порядок розрахунку розмірних ланцюгів.
Теорія розмірних ланцюгів дуже широко застосовується у машинобудуванні, зокрема при визначенні точності деталей і вузлів у процесі їх проектування, виготовлення, складання та конт- ролю. Тому теорією розмірного аналізу повинні досконало володіти як конструктори, так і техно- логи.
10