
ТМБ, част1 / Конспект / ТМБ1_Лекцiя 04_Технологiчнiсть
.pdf
4. ТЕХНОЛОГІЧНІСТЬ КОНСТРУКЦІЇ ВИРОБУ
1.Загальні поняття про технологічність виробу.
2.Види технологічності. Головні фактори, які визначають вимоги до технологічності конструкції. Оцінка технологічності.
3.Технологічний контроль креслень.
4.Загальні вимоги до технологічності конструкції заготовки, деталі та складальної оди- ниці. Якісна оцінка технологічності.
5.Кількісна оцінка технологічності. Основні правила вибору і розрахунків показників технологічності конструкції виробу.
4.1.Загальні поняття про технологічність виробу.
Перед процесом проектування чи вдосконалення технологічного процесу, конструкція виробу (складальної одиниці, деталі) повинна бути проаналізована з метою виявлення недоліків її конструкції за тими даними, які містяться у кресленнях та технічних вимогах, а також можли- вого покращення її технологічності.
Технологічність конструкції деталі – це сукупність властивостей її конструкції, які визначають пристосованість цієї деталі для досягнення оптимальних витрат ресурсів (праці, засобів, матеріалів та часу) у процесах виготовлення, експлуатації та ремонту для заданих пока- зників якості, обсягу випуску та умов виконання робіт без шкоди для її службового призначен- ня. Технологічність конструкції складальної одиниці ( вузла) – така ж сукупність, що забезпечує технологічність виробу, до складу якого ця складальна одиниця входить. Технологі- чність конструкції визначається технологічним контролем креслень та аналізом конструкції де- талі (складальної одиниці).
Відпрацювання конструкції виробу на технологічність забезпечує, залежно від його ви- ду, вирішення таких основних задач:
-зниження працеємності та собівартості виготовлення виробу;
-зниження працеємності, циклу і вартості робіт з обслуговування виробу при експлуа- тації, що включає підготовку виробу до функціонування, контроль працездатності, профілактичне технічне обслуговування, і ремонту виробу.
Комплекс робіт із зниження працеємності та собівартості виготовлення в загальному ви- падку включає:
-підвищення серійності при виготовленні за допомогою стандартизації, уніфікації і групування виробів і їх елементів за конструктивними ознаками;
-обмеження номенклатури конструкцій і застосовуваних матеріалів;
-спадковість освоєних у виробництві конструктивних рішень, що відповідають сучас- ним вимогам;
-зниження маси виробу;
-застосування високопродуктивних технологічних процесів і засобів технологічного оснащення.
Відпрацювання конструкції на технологічність виконується на всіх стадіях розроблення виробу, при технологічному оснащенні виробництва і виготовленні виробу і включає:
-забезпечення технологічності конструкції виробу при його проектуванні;
-технологічний контроль конструкторської документації;
-підготовку і внесення змін у конструкторську документацію, які забезпечують досягнення оптимальних показників технологічності.
4. Технологічність конструкції виробу
Відпрацювання конструкції виробу на технологічність проводять у такому порядку:
-добір і аналіз вихідних матеріалів для оцінки технологічності конструкції;
-уточнення обсягу випуску;
-аналіз показників технологічності виробів аналогічної конструкції;
-визначення показників виробничої й експлуатаційної технологічності;
-проведення порівняльної оцінки і розрахунок рівня технологічності конструкції роз- роблюваного виробу;
-розроблення рекомендацій по покращанню показників технологічності.
При проведенні відпрацювання конструкції виробу на технологічність враховується:
- вид виробу, ступінь його новизни, умови роботи, технічного обслуговування і ремон-
ту;
-перспективність виробу, обсяг його випуску;
-передовий досвід підприємства-розробника й інших підприємств з аналогічним виро- бництвом, нові високопродуктивні методи і процеси виготовлення відповідно до вимог станда- ртів ЄСТПВ;
-оптимальні умови конкретного виробництва при раціональному використанні наявних засобів технологічного спорядження і виробничих площ і впровадженні нових передових мето- дів і засобів виробництва, а при відсутності інформації про підприємство-розробника - передові методи і засоби виробництва;
-зв'язок розглянутих показників технологічності з іншими показниками якості виробу,
утому числі показниками призначення, надійності й ергономічності.
Рішення по розбіжностях, що виникнули при відпрацюванні конструкції виробу на тех- нологічність, у залежності від виду виробу при безумовному виконанні заданих технічних ви- мог до виробу приймають у встановленому порядку.
Технологічність конструкції виробу може бути виражена показниками, що характеризу-
ють:
-технологічну раціональність конструктивних рішень;
-спадковість конструкції або придатність до використання (застосовуваність) у складі інших виробів.
Номенклатура показників технологічності для однотипних виробів з обліком їх констру- ктивних особливостей установлюється стандартами підприємства. Допускається застосування спеціальних показників технологічності. Кількість показників повинна бути мінімальною, але достатньою для оцінки технологічності конструкції виробу.
Технологічність конструкції виробу розглядають, як правило, стосовно усього виробу, з огляду на технологічність складових частин, складання, випробовувань, технічного обслугову- вання і ремонту.
Зміни конструкції виробу, необхідність внесення яких виникає в процесі серійного виро- бництва у зв'язку з поліпшенням показників технологічності, не повинні порушувати стабільно- го ходу виробничого процесу.
4.2. Види технологічності. Головні фактори, які визначають вимоги до тех- нологічності конструкції. Оцінка технологічності.
Вид технологічності визначається ознаками, які характеризують область прояву техно- логічності конструкції виробу. Залежно від області прояву технологічності конструкції виробу розрізняють такі види технологічності:
-виробничу;
-експлуатаційну.
Виробнича технологічність конструкції виробу виявляється в скороченні витрат засобів і часу на:
-конструкторську підготовку виробництва;
-технологічну підготовку виробництва;
2
4. Технологічність конструкції виробу
- процеси виготовлення, у тому числі контролю й випробувань.
Експлуатаційна технологічність конструкції виробу виявляється в скороченні витрат ча- су і засобів на технічне обслуговування і ремонт виробу.
Головними факторами, що визначають вимоги до технологічності конструкції, є:
-вид виробу,
-обсяг випуску;
-тип виробництва.
Вид виробу визначає головні конструктивні та технологічні ознаки, що обумовлюють основні вимоги до технологічності конструкції. Обсяг випуску і тип виробництва визначає сту- пінь технологічного спорядження, механізації й автоматизації технологічних процесів і спеціа- лізацію усього виробництва.
Вид оцінки технологічності характеризує метод порівняння конструктивних рішень і об- ґрунтованого вибору оптимального варіанту конструкції виробу.
Оцінка технологічності конструкції виробу може бути двох видів:
-якісною;
-кількісною.
4.3. Технологічний контроль креслень
Технологічний контроль креслень зводиться до їх ретельного вивчення. Робочі креслення оброблюваних деталей повинні містити всі необхідні дані, які давали б повну уяву про деталь, тобто усі проекції, розрізи й перетини, котрі абсолютно чітко й однозначно пояс- нюють конфігурацію деталі і можливі способи отримання заготовки. Креслення деталі повинно містити усі необхідні дані про матеріал деталі, термічне оброблення, масу тощо.
На кресленні повинні бути вказані всі розміри з необхідними відхиленнями, необхідна шорсткість оброблюваних поверхонь, допустимі відхилення від правильних геометричних форм і взаємного розташування поверхонь.
Проставлення розмірів і допусків на кресленні деталі повинне:
1)відображати вимоги, які висуваються до цієї деталі, виходячи з її службового призначення;
2)забезпечувати можливість її виготовлення простими технологічними методами. Виконання першої умови забезпечується виявленням розмірних зв’язків поверхонь дета-
лі на основі розмірного аналізу вузла, другого – правильним вибором допусків для розмірів, які входять у складальні розмірні ланцюги, завдяки правильному вибору методу досягнення точно- сті замикальної ланки.
Наприклад, попереднє проставлення розмірів вала (рис 4.1, а) виконується на основі розмірного аналізу вузла, у який входить ця деталь шляхом вибірки зі складальних розмірних ланцюгів поздовжніх розмірів, які належать валу. На рис. 4.1, б показано кінцеве проставлення розмірів деталі з числовими значеннями і граничними відхиленнями, встановленими при про- веденні розмірного аналізу вузла.
Проставлення розмірів і допусків на робочих кресленнях деталей (формування розмір- них зв’язків поверхонь) вимагає диференційованого підходу, який виражається рядом основних правил, наведених нижче.
1.На кресленні обов’язково повинні проставлятися розміри з’єднань і розміри, які входять у розмірні ланцюги. Інші розміри проставляють, виходячи з умови забезпечення мож- ливості виготовлення (див. рис. 4.1).
2.Проставлення на кресленнях розмірів деталей повинне забезпечувати отримання най- коротших складальних розмірних ланцюгів вузла, у яких кількість складових ланок рівна кіль- кості з’єднуваних деталей.
3.Кількість розмірів на кресленні повинна бути достатньою для виготовлення і контро- лю деталі. Для кожної деталі існує цілком визначена кількість розмірів, які складають її повну
3
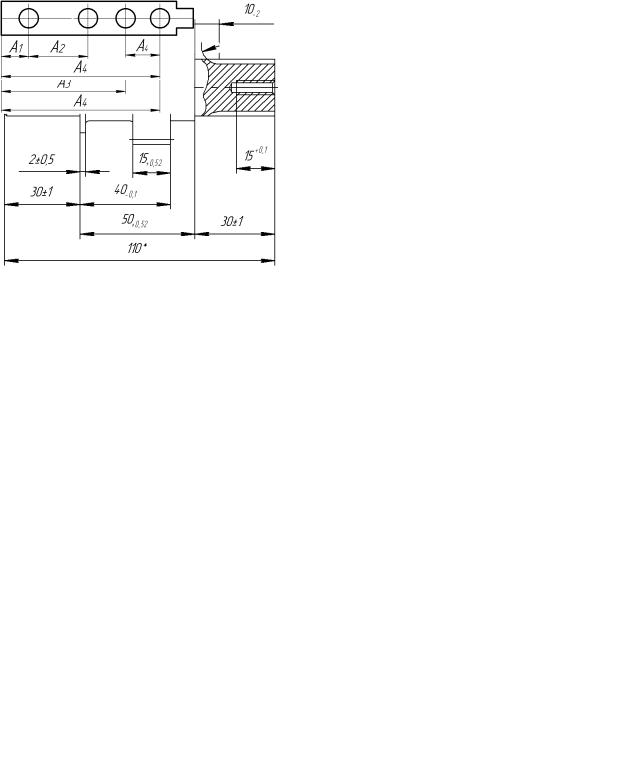
4. Технологічність конструкції виробу
повну розмірну характеристику. Можна по-різному змінювати проставлення розмірів, але їх не- обхідна кількість для конкретної деталі є постійною.
|
|
|
|
|
|
а) |
|
б) |
Рис. 4.1. Оптимізація проставлення поздовжніх розмірів деталі типу „ вал”.
4.Кожен розмір слід наводити на кресленні лише один раз.
5.Ланцюг розмірів на кресленні деталі не повинен бути замкненим. Розміри на кресленні складають подетальний розмірний ланцюг. Складові розміри цього ланцюга отриму- ють на визначених технологічних переходах (операціях). Замикальний розмір визначається у результаті виконання усіх технологічних переходів. У цьому розмірі накопичуються похибки складових розмірів, які виникають при виготовленні деталі. Тому замикальним розміром виби- рають найменш відповідальний розмір деталі, який на кресленні не проставляють, і подеталь- ний розмірний ланцюг залишається незамкненим. Якщо замикальною ланкою є габаритний розмір, то його показують на кресленні як довідковий (див. рис. 4.1, б, розмір 110* мм). Довід- кові розміри при виготовленні деталі не контролюють.
6.Проставлення розмірів повинне бути таким, щоб при виготовленні деталі найточніший її розмір мав найменшу накопичену похибку. Для цього застосовують ланцюго- вий, координатний і комбінований методи проставлення.
При ланцюговому методі розміри проставляють послідовно (ланцюгом) (рис. 4.2, а). При такому проставленні похибка отримання кожного розміру не залежить від похибок отри- мання попередніх розмірів, що є основною перевагою цього методу. Тому його застосовують при проставленні розмірів на міжосьових розмірах, ступінчастих деталях тощо.
|
|
|
|
|
|
|
|
|
|
|
|
|
|
|
а) |
|
б) |
|
в) |
Рис. 4.2. Схеми розмірних ланцюгів, побудованих з використанням різних методів проставлення розмірів.
При координатному методі розміри проставляють від однієї бази (рис. 4.2, б). Тому точність будь-якого з координатних розмірів не залежить від точності виконання інших розмі- рів. Цим методом користуються, якщо необхідно точно розташувати елементи деталі відносно бази. Недоліком цього методу є деяке збільшення похибки між суміжними елементами деталі.
4

4. Технологічність конструкції виробу
Комбінований метод проставлення розмірів є поєднанням ланцюгового і координат- ного методів (рис. 4.2, в). Його використовують для зменшення похибки відповідальних розмі- рів.
7.При проставленні розмірів необхідно враховувати технологію оброблення деталі, зок- рема призначення і використання технологічних баз. У цьому контексті слід пам’ятати і про те, що зміна характеру виробництва (наприклад, заміна універсального металорізального устат- кування на спеціальне з автоматичним отриманням заданого розміру) у більшості випадків та- кож викликає зміну технологічних баз.
8.На кресленні розміри повинні бути проставлені так, щоб вони безпосередньо отримувалися в процесі оброблення деталі без зміни технологічних баз і перерахунку допусків. При будь-якій початково заданій на кресленні системі розмірів у процесі розроблення техноло- гічного процесу чи його здійсненні бази проставлення розмірів можуть змінюватися відповідно до прийнятого методу оброблення деталі і технологічних баз. Проте за необхідності збереження заданих на кресленні допусків це завжди призводить до зменшення допусків на оброблення. Технологічнішим у цьому випадку є проставлення розмірів, яке передбачає умови виконання технологічного процесу і тим самим усуває необхідність оброблення деталі по суттєво зменше- них технологічним допусках.
9.Розміри, які визначають віддалі між необроблюваними поверхнями, повинні замика- тися між собою, утворюючи окремі подетальні ланцюги, які не містять інших розмірів.
Для деталей, які містять необроблювані поверхні, розрізняють дві системи розмірів: ви- хідної заготовки (сукупність розмірів, які зв’язують необроблювані поверхні), і деталі (сукуп- ність розмірів, які зв’язують оброблювані поверхні). У зв’язку з цим розміри, які визначають геометричні параметри таких деталей, можуть зв’язувати:
1)дві необроблювані поверхні;
2)дві оброблювані поверхні;
3)оброблювану поверхню з необроблюваною.
Розміри першого виду утворюють систему розмірів вихідної заготовки, другого – систе- му розмірів деталі, третього – координують обидві системи одна відносно одної. Побудова ко- жної з вказаних систем підпорядковується загальним принципам проставлення розмірів. При проставленні розмірів третього виду необхідно також враховувати послідовність різних стадій виготовлення деталі.
Системи розмірів необроблюваних і оброблюваних розмірів повинні зв’язуватися одним розміром по кожній координатній осі. Зв’язувати окремими розмірами оброблювану і необроблювану поверхні допускається лише у тому ви- падку, коли останню планується використовувати як технологічну базу.
Приклад 4.1. Проаналізувати різні варіанти проставлення розмірів на кресленні литої деталі, показаної на рис. 4.3.
Проставлення розмірів на рис. 4.3, а невірне, оскільки віддаль між оброблюваними поверх- нями, зв’язаними з необроблюваними сумою розмірів 15; 175 і 10 мм, у цьому випадку колива- ється у широких межах через коливання розмірів необроблюваних поверхонь. Така ж помилка допущена на рис 4.3, б, де віддаль між оброблюваними поверхнями задана сумою розмірів 185 і 15 мм.
При проставленні розмірів відповідно до рис. 4.3, в, віддаль між оброблюваними поверхнями (200 мм) витримується у межах допуску на механічне оброблення. Помилка полягає у тому, що необроблювані поверхні зв’язані з суміжними оброблюваними (розміри 15 і 10 мм). Витримати таку координацію практичну неможливо. Положення необроблюваних поверхонь коливається у межах точності лиття, а з ним коливається і віддаль до оброблюваних поверхонь.
На рис. 4.3, г помилка посилюється тим, що товщина горизонтальної стінки (задана безпосе- редньо розміром 5 мм) визначається висотою внутрішньої порожнини, яка задана відносно обро- блюваної нижньої поверхні (розмір 185 мм). Таким чином вводиться ще одне джерело похибки, і товщина стінки коливатиметься у широких межах.
5
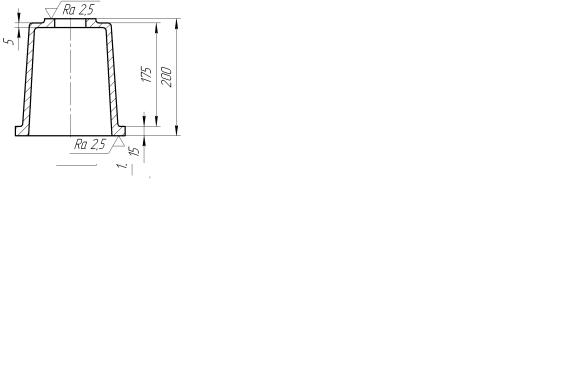
4. Технологічність конструкції виробу
При проставленні розмірів відповідно до рис.4.3, д, положення нижньої оброблюваної пове- рхні задано двома розмірами від необроблюваної поверхні (розміри 190 і 15 мм). Витримати таку координацію, як й у випадку, наведеному на рис. 4.3, в, практично неможливо.
Рис. 4.3, е відповідає правильному проставенню розмірів. У цьому випадку чорновою базою вибрано необроблювану поверхню фланця. З нею розміром 15 мм зв’язана технологічна база. З останньою розміром 200 мм зв’язана оброблювана верхня поверхня, яка в свою чергу координу- ється від бази заготовки (розмір 175 мм) і від верхньої поверхні (товщина верхньої стінки – роз- мір 5 мм). Віддаль між верхніми оброблюваними і необроблюваними поверхнями стає замикаль- ною ланкою розмірного ланцюга і служить компенсатором відхилень розташування поверхонь, отримуваних на заготівельній операції.
|
|
|
|
|
|
|
|
|
|
|
|
|
|
|
|
|
|
|
а) |
|
|
б) |
|
|
в) |
|
|
|
|
|
|
|
|
|
|
|
|
|
|
|
|
|
|
|
|
|
|
|
|
|
|
|
|
г) |
д) |
е) |
Рис. 4.3. Схеми проставлення розмірів, які визначають віддалі між необроблюваними поверхнями.
4.4. Загальні вимоги до технологічності конструкції заготовки, деталі та складальної одиниці. Якісна оцінка технологічності.
Якісна оцінка технологічності узагальнено характеризує технологічність конструк- ції виробу вимогам, які забезпечують його технологічність під час отримання заготовки, меха- нічного оброблення та складання на підставі досвіду виконавця i проводиться як попередня. Якісна порівняльна оцінка варіантів конструкції припустима на всіх стадіях проектування, коли здійснюється вибір кращого конструктивного рішення і не потрібно кількісного визначення ступеня розходження технологічності порівнюваних варіантів.
Якісна оцінка базується на інженерно-візуальних методах. Вона виконується на основі знань, кваліфікації та досвіду інженера-технолога та визначається такими показниками: добре- погано, припустимо-неприпустимо тощо.
Якісна оцінка технологічності конструкції виробу полягає у перевірці відповідності його конструкції вимогам, які забезпечують технологічність під час заготівельних процесів, механіч- ного оброблення та складання. При цьому доцільно використовувати рекомендації щодо техно- логічності конструкції виробів, окремих деталей і заготовок, наведені у довідковій літературі,
наприклад, [7 (т. 5), 8 (т. 2), 10 тощо].
Вимоги, які забезпечують технологічність конструкції заготовки, отриманої різними способами лиття, листового чи об’ємного штампування тощо, відрізняються змістом i обсягом.
6
4. Технологічність конструкції виробу
Нижче наведено деякі з основних рекомендацій для заготовок, отриманих литтям, штампуван- ням i куванням.
Литі заготовки з чавуну та сталі повинні відповідати таким вимогам:
1)форма заготовки повинна мати конфігурацію, наближену до деталі, високу розмірну точність, мінімальні припуски на механічне оброблення, малу шорсткість поверхонь;
2)конструкція заготовки повинна мати просту зовнішню форму: без гострих кутів i заокруглень, високих ребер i виступів, а також мінімальну кількість внутрішніх порожнин;
3)виливок по можливості повинен передбачати мінімальне механічне оброблення, мати відповідні технологічні ухили для забезпечення виймання модельного комплекту з форми; стін- ки повинні бути оптимальної товщини залежно від обраного способу лиття; товщина усіх сті- нок повинна бути однаковою без різких переходів від тонких частин до товстих.
Основні вимоги до заготовок, отриманих штампуванням та куванням:
1)заготовки не повинні мати різких переходів у поперечних перетинах; площа поперечних перетинів по довжині деталі не повинна змінюватися більше трьох разів;
2)виступи та ребра не повинні розміщуватися близько один від одного;
3)бобишки, в яких повинні свердлитися отвори, для забезпечення мінімальної товщини стінки повинні бути овальними у напрямі зміщення отворів;
4)на деталях з двома i більше бобишками, у яких важко визначити напрям зміщення, ді- аметри бобишок повинні бути такими, щоб одержати максимально допустимий розмір стінки.
5)штамповані заготовки повинні мати відповідні ухили для забезпечення виймання їх зі штампів; значення ухилів для зовнішніх поверхонь приймаються 1:10 – 1:7, для внутрішніх – 1:7 – 1:5 ( при підвищеній точності заготовки значення ухилу приймають меншими).
Загальними вимогами до технологічності конструкції деталі є такі:
1)конструкція деталі повинна складатися зі стандартних й уніфікованих конструкційних елементів;
2)фізико-хімічні та механічні властивості матеріалу деталі, її форма та розміри, а також параметри її точності та шорсткості повинні відповідати вимогам технології виготовлення;
3)деталь повинна мати просту і правильну геометричну форму, що полегшує її базування в процесі механічного оброблення, а також спрощує процес отримання заготовки;
4)деталь повинна бути виготовлена зі стандартної чи уніфікованої заготовки;
5)показники базових поверхонь (точність та шорсткість) деталі повинні забезпечувати точність встановлення, оброблення та контролю;
6)конструкція деталі повинна забезпечувати можливість застосування типових технологічних процесів її виготовлення;
7)деталь повинна мати стандартні базові поверхні для початкового та подальшого обро-
блення;
8)оброблення поверхонь деталі за можливості повинно забезпечуватися напрохід і допускати застосування високопродуктивного устаткування;
9)конструкція деталі повинна дозволяти використання граничних калібрів для контролю поверхонь та не вимагати застосування унікальних вимірювальних пристроїв та інструментів.
На рисунку 4.4 наведено нетехнологічні рішення конструкції елементів деталей. Вісь отвору 2 деталі, наведеної на рис. 2.4 а, є не перпендикулярною до поверхні, що зумовлює не- обхідність проектування та виготовлення спеціального пристрою для свердлення. На рис. 4.4 в отвір більш високої точності (7-й квалітет) спроектований як глухий, що не дає змоги обробля- ти його на прохід, а також використати прогресивні методи оброблення, наприклад, протягу- вання. У цьому випадку доцільніше точніший отвір зробити наскрізним.
7

4. Технологічність конструкції виробу
|
|
|
|
|
|
|
|
|
|
|
|
|
|
|
а) |
|
б) |
|
в) |
Рис. 4.4. Приклади нетехнологічних рішень елементів деталей.
Вимоги щодо забезпечення технологічності конструкції деталей, які підлягають механі- чному обробленню, залежать від типу деталі та її геометричної форми. Нижче наведено загаль- ні рекомендації для проведення аналізу технологічності окремих класифікаційних груп деталей.
Для корпусних деталей визначають:
1)чи допускає конструкція оброблення площин напрохід і що заважає такому виду об-
роблення;
2)чи є можливість одночасного оброблення отворів на багатошпиндельних верстатах з урахуванням відстаней між осями цих отворів;
3)як форма отворів та взаємне їх розташування дозволяє оброблювати ці отвори: на- прохід з одного установу чи з двох боків;
4)чи є вільний доступ інструменту до оброблюваних поверхонь;
5)чи потрібне оброблення торців маточин з внутрішніх сторін виливка і чи можна усунути таке оброблення;
6)чи є глухі отвори і чи можна їх замінити наскрізними;
7)чи наявні оброблювані площини, котрі розташовані не під прямим кутом, і чи можна їх замінити площинами, розташованими паралельно чи перпендикулярно одна до одної;
8)чи наявні отвори, котрі розташовані не під прямим кутом до площини входу і виходу,
ічи можлива зміна цих елементів;
9)чи достатня жорсткість деталі, чи не обмежує вона режими різання;
10)чи наявні в конструкції деталі достатні за розмірами і відстанями базові поверхні; якщо ні, то яким чином слід вибрати допоміжні бази;
11)чи нема в конструкції внутрішньої різі великого діаметру і чи можливо замінити її іншими конструктивними елементами;
12)наскільки простий спосіб отримання заготовки (виливка), чи правильно вибрані елементи конструкції, які обумовлюють виготовлення заготовки;
Для валів вказують:
1)чи можна обробити поверхні прохідними різцями;
2)чи зменшуються до кінців діаметральні розміри шийок вала;
3)чи можна зменшити діаметр великих фланців чи буртів або виключити їх взагалі, і як це вплине на коефіцієнт використання металу;
4)чи можна замінити закриті шпонкові канавки відкритими, котрі набагато продуктивніше обробляються дисковими фрезами;
5)чи мають поперечні канавки форму і розміри, придатні для оброблення на гідрокопіювальних верстатах;
6)чи допускає жорсткість вала отримання високої точності оброблення (жорсткість вала вважається недостатньою, якщо для отримання точності 6÷9 квалітетів співвідношення йо- го довжини l до діаметру d понад 10÷12; для валів, виготовлених за нижчими квалітетами, це співвідношення може бути рівне 15; при багатоінструментному обробленні це співвідношення слід зменшити до 10);
При аналізі технологічності конструкції деталей, які містять елементи типу зубчастих вінців слід визначити можливість високопродуктивних методів формоутворення зубчастого ві- нця із застосуванням пластичного деформування в нагрітому і холодному стані. Конструкція таких елементів повинна характеризуватися ознаками:
8
4. Технологічність конструкції виробу
1)простою формою центрального отвору зубчастого колеса, оскільки складні отвори значно ускладнюють оброблення, викликаючи необхідність застосування револьверних верста- тів і напівавтоматів;
2)простою конфігурацією зовнішнього контуру зубчастого колеса (найбільш технологічними є зубчасті колеса пласкої форми без виступаючих маточин);
3)симетричним розташуванням перемички між маточиною і вінцем для зубчастих коліс, які підлягають термічному обробленню, як відносно вінця, так і відносно маточини; по- рушення цієї умови приводить до значних односторонніх викривлень при термічному оброб- ленні;
4)правильною формою і розмірами канавок для виходу інструментів;
5)можливістю багатоінструментного оброблення залежно від співвідношення діаметрів вінців і відстаней між ними.
Подібним чином проводиться аналіз технологічності і для інших деталей, які мають ана- логічні елементи конструкції.
Основні ознаки технологічності складальних одиниць.
Стосовно будови складальної одиниці:
1)складальна одиниця повинна поділятися на раціональну кількість складових частин;
2)конструкція повинна передбачати компонування зі стандартних, стандартизованих чи уніфікованих елементів;
3)конструкція складальної одиниці повинна мати базову частину, зручну для встанов- лення на робочому місці складання;
4)види, будова і розташування з’єднань повинні забезпечувати механізацію та автома- тизацію складальних робіт;
5)компонування складальної одиниці та її складових частих повинна передбачати зручний доступ до місць, які вимагають контролю, регулювання та інших робіт.
Стосовно технологічного процесу складання:
1)складальні операції повинні виконуватися по можливості без складного технологіч- ного оснащення;
2)складальна операція повинна виконуватися за незмінного базування базової деталі;
3)технологічні та вимірювальні бази повинні по можливості бути суміщеними;
4)можливість використання типових технологічних процесів.
Стосовно точності і методу складання:
1)точність розташування складових частин виробу повинна бути обґрунтованою і вза- ємопов’язаною з точністю виготовлення деталей і складових частин виробу;
2)вибір методу складання для заданого типу виробництва необхідно здійснювати на основі розрахунку й аналізу розмірних ланцюгів за методом максимуму-мінімуму чи ймовірні- сним методом;
3)у конструкції деталей необхідно передбачати елементи, які забезпечували б задану точність відносного розташування складових елементів (центрувальних, компенсувальних, фік- сувальних тощо).
Окрім аналізу конструкції деталі на технологічність необхідно провести ще й відпрацю- вання її на технологічність, яке полягає в тому, що у конструкцію деталі вносять зміни, котрі дають можливість зменшити собівартість її виготовлення. Якщо таких змін не можна зробити, то визначають елементи, котрі виконано у різних нетехнологічних варіантах, обов’язково вка- зуючи, чому ці варіанти є нетехнологічними.
9
4. Технологічність конструкції виробу
4.5. Кількісна оцінка технологічності. Основні правила вибору і розрахунків показників технологічності конструкції виробу.
Кількісна оцінка технологічності конструкції виробу виражається показником, чи- сельне значення якого характеризує ступінь задоволення вимог до технологічності конструкції. Кількісна оцінка базується на визначенні відношення значень досягнутих показників до базо- вих. При цьому за базові беруть показники машин, які є кращими світовими представниками такого виду продукції. Номенклатуру загальних показників технологічності конструкції виробів наведена в таблиці 4.2.
Ціль кількісної оцінки технологічності розроблюваної конструкції виробу – забезпечення ефективного відпрацювання виробу на технологічність при зниженні витрат часу і засобів на її розробку, технологічну підготовку виробництва, виготовлення, експлуатацію і ремонт.
Показники технологічності проектованої конструкції визначають у таких випадках:
-для порівняльної оцінки варіантів конструкції в процесі проектування виробу;
-для визначення рівня технологічності конструкції виробу;
-для накопичення статистичних даних по виробах-представниках із метою наступного використання при визначенні базових показників і в процесі розробки виробів;
-для побудови математичних моделей із метою прогнозування технічного розвитку конструкцій виробів.
Основними показниками технологічності конструкції виробу є:
-працеємність;
-собівартість;
-матеріалоємність;
-енергоємність.
Працеємність виготовлення (ремонту) виробу виражається сумою нормо-годин, ви- трачених на технологічні процеси виготовлення (ремонт) всіх його складових частин i складан- ня. Рівень технологічності конструкції щодо працеємності визначають за формулою
Kп / є = |
По |
, |
(4.1) |
|
|||
|
П |
|
|
|
б |
|
де По, Пб – очікувана (проектна) i базова працеємність працеємності виготовлення (ремонту) виробу відповідно, нормо-годин.
Собівартість – сумарне (за всіма складовими частинами виробу) значення витрат на матеріали, заробітну плату виробничих робітників з нарахуваннями i накладними витратами. Собівартість є узагальнювальним показником якості виробу. Рівень технологічності конструкції за собівартістю:
Kс / в = |
Со |
, |
(4.2) |
|
|||
|
С |
|
|
|
б |
|
де Сo i Сб – очікувана (проектна) i базова собівартості виготовлення виробу, грн.
Матеріалоємність характеризує кількість матеріалу, витраченого на виготовлення ви- робу одиниці маси. На практиці часто використовують матеріалоємність як відношення маси виробу до одного з основних технічних його параметрів (наприклад, потужності).
Енергоємність характеризує кількість паливно-енергетичних ресурсів, які витрачають- ся на виготовлення виробу, наприклад, кВт, кал. Рівні технологічності виробу за матеріалоємні- стю й енергоємністю визначаються аналогічно до рівнів технологічності з працеємності та собі- вартості.
10