
МИНИСТЕРСТВО СЕЛЬСКОГО ХОЗЯЙСТВА РФ
Федеральное государственное образовательное учреждение
высшего профессионального образования
«Пермская государственная сельскохозяйственная академия
имени академика Д.Н. Прянишникова»
Кафедра деталей машин
В.С. Новосельцев, В.Ф. Миллер, Ю.А. Барыкин
ПОДЪЕМНО-ТРАНСПОРТИРУЮЩИЕ МАШИНЫ
Учебное пособие
ПЕРМЬ
ФГОУ ВПО «Пермская ГСХА»
2010
УДК Б 21.86.001.Б 3 (075.8)
Рецензент: кандидат технических наук, доцент М.А. Трутнев
Подъемно-транспортирующие машины. Учебное пособие/ К.т.н., доцент В.С.Новосельцев (части 1.1-1.9, 2), к.т.н., доцент В.Ф.Миллер (части 1.6, 1.8), ст. преподаватель Ю.А.Барыкин (часть 3). М-во с.-х. РФ, ФГОУ ВПО «Пермская ГСХА». – Пермь: Изд-во ФГОУ ВПО «Пермская ГСХА», 2010. – 119 с.
Учебное пособие «Подъемно-транспортирующие машины» предназначено для студентов третьего, четвертого курсов инженерно- технических специальностей очной и заочной форм обучения: 110301 «Механизация сельского хозяйства», 190603 «Сервис транспортных и технологических машин и оборудования (в автомобильном транспорте)», 110304 «Технология обслуживания и ремонта машин в АПК», 280101 «Безопасность жизнедеятельности (в техносфере)».
В предлагаемом пособии изложены методические рекомендации и представлены нормативные материалы, необходимые для выполнения курсовой работы, даны примеры расчетов, выдержки из каталогов и стандартов на основные узлы и детали грузоподъемных и транспортирующих машин.
Учебное пособие рассмотрено и утверждено методической комиссией факультета технического сервиса 25. 01. 2010 г. (Протокол № 4)
© ФГОУ ВПО «Пермская ГСХА», 2010
Cодержание
Введение 4
1. Проектирование и расчет механизмов подъема
1.1. Основные характеристики грузоподъемных машин 5
1.2. Полиспасты 6
1.3. Гибкие подъемные и тяговые органы 10
1.4. Блоки, барабаны 14
1.5. Привод механизма подъема груза 15
1.6. Подбор редукторов, муфт и тормозов для механизма подъема 17
1.7. Пример расчета механизма подъема груза 22
1.8 Расчет и проектирование механизма поворота крана 27
1.9. Пример расчета механизма передвижения МК 37
2. Устройство и основы проектирования
ленточных конвейеров
2.1. Устройство и основы проектирования
ленточных конвейеров 54
2.2. Пример расчета ленточного конвейера 72
3. Пневмотранспортные установки
3.1. Устройство и основы проектирования
пневмотранспортных установок 77
3.2. Примеры расчета пневмотранспортных установок 87
Контрольные вопросы 94
Литература 96
Приложение А. Справочные материалы 97
Приложение Б. Примеры оформления чертежей 115
Введение
Развитие и совершенствование отрасли сельского хозяйства в значительной степени зависит от ее материальной базы, внедрения в проекты развития прогрессивных научно-технических достижений.
Многообразие грузов, различающихся по характеру и назначению, обуславливают применение разнообразных подъемно-транспортирующих механизмов, - грузоподъемников, лебёдок, кран-балок, ленточных конвейеров и т.д. Грузоподъемные машины все чаще включают в систему машин для комплексной механизации грузопотоков.
В связи с этим общеинженерная подготовка в сельскохозяйственных вузах заключается в изучении раздела «Подъемно-транспортирующие машины» (ПТМ). В процессе обучения студенты получают знания об особенностях процессов перегрузки грузов, подъемно-транспортирующих средствах основных типов, их характеристиках, областях применения и методах расчетов.
Изучение дисциплины «Детали машин и основы конструирования» завершается выполнением курсовой работы, в которой одним из вопросов является расчет механизмов и узлов ПТМ.
4
1. Проектирование и расчет механизмов подъема
1.1 Основные характеристики грузоподъемных машин
К основным характеристикам грузоподъемных машин относятся:
грузоподъемность, скорость перемещений и высота подъема груза, режим работы, вылет стрелы, масса машин.
Грузоподъемность машин (по ГОСТ 1575 – 87) – это масса наибольшего груза, поднимаемого специальным приспособлением. Это величина включает в себя и массу используемого грузозахватного приспособления.
Номинальная грузоподъемность подъемно-транспортных машин, т.: 0,025;0,05; 0,1; 0,125; 0,16; 0,2; 0,25; 0,32; 0,4; 0,5; 0,63; 0,8; 1,0; 1,25; 1,6; 2,0; 2,5; 3,2;4,0; 5,0; 6,3; 8,0; 10,0; 12,5; 16,0; 20,0; 25,0; 32,0; 40,0; 50,0; 63,0; 80,0; 100,0 и т. д.
Скорости рабочих движений грузоподъемных механизмов рекомендуется выбирать из рядов, установленных также по ГОСТ 1575 – 87 линейные скорости, м/с: 0,1; 0,125; 0,16; 0,2; 0,25; 0,32; 0,4; 0,5; 0,63; 0,8; 1,0; 1,25; 1,6; 2,0; 2,5; 3,2; 4,0; 5,0; 6,3; 8,0; 10,0; 12,5.
При выборе скоростей следует учитывать технологические требования, безопасность работы, тип машин, удобство управления, требуемую точность установки груза и др.
Так для перегрузки штучных грузов рекомендуются следующие скорости механизма подъема груза, м/с: подъем – 0,15; опускание – 0,10. Правилами Гостехнадзора установлены следующие режимы работы кранов: с ручным приводом – Р; с машинным приводом: легкий – Л, средний – С, тяжелый – Т. весьма тяжелый – ВТ.
Режимы
работы
с
машинным
приводом
выбирают
в
зависимости
от
коэффициента
использования
механизма
по
грузоподъемности
,коэффициентов
годового
и
суточного
использования
механизма,
коэффициента
относительной
продолжительности
включения
двигателя
механизма,
СПВ,
числа
включений
механизма
в
час,
температуры
окружающей
среды.
За
главные
показатели,
определяющие
режим
работы
механизма,
приняты
коэффициенты
использования
по
грузоподъемности
и
относительной
продолжительности
включения
ПВ
,
(1.1)
где
–
средняя
масса
груза,
поднимаемого
за
смену,
кг;
–номинальная
грузоподъемность,
кг.
, (1.2)
где–
сумма
продолжительности
работы
за
цикл,
мин;
продолжительность
цикла.
5
Режим работы электрооборудования отдельных механизмов выбирают по таблице 1.1 в зависимости от значений рассмотренных ранее коэффициентов.
Таблица 1.1 – Режим работы электрооборудования и отдельных механизмов грузоподъемных машин
Режим работы |
Коэффициент использования |
ПВ, % |
Число включений в час (среднее за смену) |
Температура окружающей среды, ºС | ||
По грузо- подъемности
|
По времени | |||||
В течение
года
|
В течение
суток
| |||||
Л |
1 0,75 0,5 0,25 0,1 |
Нерегулярная редкая работа То же |
60 |
25 | ||
0,25 0,5 1 |
0,33 0,67 1 |
15 15 25 | ||||
С |
1 0,75 0,5 0,25 0,1 |
1 0,5 0,5 1 1 |
0,67 0,33 0,67 1 1 |
15 25 25 40 60 |
120 |
25 |
Т |
1 1 0,75 0,5 0,25 |
1 1 0,75 1 1 |
0,67 0,33 0,67 1 1 |
25 40 40 40 40 |
240 |
25 |
ВТ |
1 0,75 0,5 0,25 0,7 |
1 1 1 1 1 |
1 1 1 1 1 |
60 40 60 60 60 |
300…600 |
45 25 45 45 45 |
1.2 Полиспасты
Полиспастом называют систему подвижных и неподвижных блоков огибаемых канатом.
Основной характеристикой полиспаста является – кратность полиспастной системы, т.к. она определяется как отношение числа ветвей,
участвующих
в подъеме
груза
,
к числу ветвей, наматывающихся на
барабан,
6
,
(1.3)
Кратность полиспастной системы выбирают в зависимости от грузоподъемности механизма (табл. 1.2).
Таблица 1.2 – Рекомендуемая кратность полиспастов
Сдвоенный полиспаст |
Простой полиспаст | ||
Грузоподъемность, т |
Кратность одного полиспаста m |
Грузоподъемность, т |
Кратность одного полиспаста m |
до 8 |
2 |
до 1 |
1...2 |
10...16 |
2...3 |
1,25…6,3 |
2...3 |
20...32 |
3...4 |
8...16 |
3...4 |
40...50 |
4...5 |
20...32 |
5...6 |
m=2
m=3
m=1
m=2
m=3
а
б
а – одинарные; б – сдвоенные
Рисунок 1.1 – Схема полиспастов
Натяжение тяговой ветви каната (Н), наматываемой на барабан S, может быть определено с достаточной точностью по формуле
,
(1.4)
где
,
сумма веса поднимаемого груза и крюковой
обоймы или грузозахватного устройства.
Вес крюковой обоймы выбирают в зависимости
от режима работы машины и веса поднимаемого
груза (табл. 1.3, 1.4);
m – кратность полиспастной системы определяют по схеме (рис.1.1) или по таблице 1.2;
7
Номер крюка |
Ручной привод |
Машинный привод | |
Режим Л; С |
Режим Т; ВТ | ||
1 |
0,4 |
0,32 |
0,25 |
2 |
0,5 |
0,4 |
0,32 |
3 |
0,64 |
0,5 |
0,4 |
4 |
0,8 |
0,63 |
0,5 |
5 |
1,0 |
0,8 |
0,63 |
6 |
1,25 |
1,0 |
0,8 |
7 |
1,6 |
1,25 |
1,0 |
8 |
2 |
1,6 |
1,25 |
9 |
2,5 |
2 |
1,6 |
10 |
3,2 |
2,5 |
2,0 |
11 |
4 |
3,2 |
2,5 |
12 |
5 |
4,0 |
3,2 |
13 |
6,3 |
5,0 |
4,0 |
14 |
8 |
6,3 |
5,0 |
15 |
10 |
8,0 |
6,3 |
16 |
12,5 |
10 |
8,0 |
17 |
16 |
12,5 |
10 |
18 |
20 |
16 |
12,5 |
19 |
- |
20 |
16 |
20 |
- |
25 |
20 |
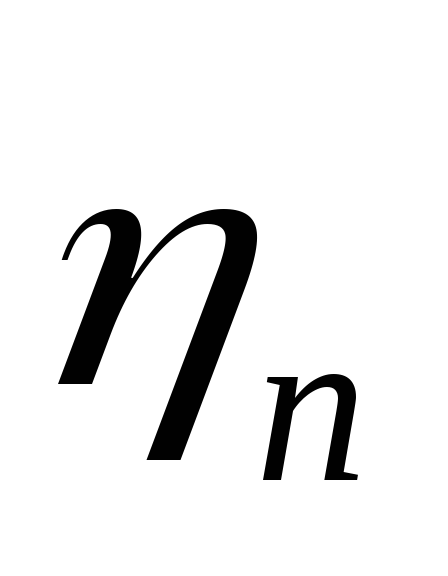
,
(1.5)
–КПД
блока, берется по таблице 1.5.
Таблица 1.3 – Грузоподъемность однорогих крюков (по ГОСТ 6627 – 74*)
8
Рисунок 1.2 – Эскиз крюка
Таблица 1.4 – Основные размеры крюков, мм
Номер крюка |
A |
s |
b |
h |
d |
|
|
L |
|
|
Масса, кг | ||
ТипА |
ТипБ |
не менее |
ТипА |
ТипБ | |||||||||
1 |
20 |
14 |
12 |
18 |
15 |
12 |
М12 |
65 |
80 |
30 |
20 |
0,18 |
0,2 |
2 |
22 |
16 |
13 |
21 |
15 |
12 |
М12 |
70 |
90 |
32 |
20 |
0,22 |
0,25 |
3 |
25 |
18 |
15 |
24 |
18 |
15 |
М14 |
75 |
100 |
35 |
20 |
0,35 |
0,4 |
4 |
30 |
22 |
18 |
26 |
20 |
17 |
М16 |
85 |
110 |
40 |
25 |
0,5 |
0,6 |
5 |
32 |
24 |
20 |
28 |
20 |
17 |
М16 |
90 |
120 |
45 |
25 |
0,6 |
0,7 |
6 |
36 |
26 |
22 |
32 |
25 |
20 |
М20 |
105 |
130 |
50 |
30 |
0,9 |
1 |
7 |
40 |
30 |
24 |
36 |
25 |
20 |
М20 |
110 |
140 |
35 |
30 |
1,1 |
1,2 |
8 |
45 |
33 |
26 |
40 |
30 |
25 |
М24 |
130 |
160 |
65 |
35 |
1,7 |
1,9 |
9 |
50 |
36 |
30 |
45 |
35 |
30 |
М27 |
145 |
180 |
70 |
40 |
2,6 |
2,9 |
10 |
55 |
40 |
34 |
52 |
35 |
30 |
М30 |
165 |
220 |
85 |
45 |
3,2 |
3,6 |
11 |
60 |
45 |
38 |
55 |
40 |
35 |
М33 |
180 |
300 |
90 |
50 |
4,5 |
5,7 |
12 |
65 |
50 |
40 |
65 |
45 |
40 |
М36 |
195 |
375 |
95 |
55 |
5,9 |
8,1 |
13 |
75 |
55 |
48 |
75 |
52 |
45 |
М42 |
250 |
410 |
105 |
60 |
9,6 |
12,2 |
14 |
85 |
65 |
54 |
82 |
56 |
50 |
М48 |
280 |
475 |
120 |
70 |
12,5 |
16,2 |
15 |
95 |
75 |
60 |
90 |
62 |
55 |
М52 |
310 |
520 |
135 |
75 |
18 |
23 |
16 |
110 |
85 |
65 |
100 |
63 |
60 |
М56 |
340 |
580 |
150 |
80 |
26 |
33 |
17 |
120 |
90 |
75 |
115 |
80 |
70 |
М64 |
415 |
600 |
165 |
90 |
36 |
43 |
18 |
130 |
100 |
80 |
130 |
85 |
75 |
Трап 70х80 |
440 |
630 |
180 |
95 |
47 |
56 |
19 |
150 |
115 |
90 |
150 |
95 |
85 |
Трап 80х10 |
480 |
660 |
210 |
100 |
64 |
74 |
20 |
170 |
130 |
102 |
164 |
110 |
100 |
Трап 90х12 |
535 |
730 |
230 |
115 |
95 |
110 |
9
Примечание: Тип А – короткий крюк, Тип Б – удлиненный
Таблица
1.5
–
Коэффициенты полезного действия
крюковых
полиспастов
Тип подшипников блоков |
| ||||
2 |
3 3 |
4 |
5 |
6 | |
Скольжения КПД
блока
|
0,98 |
0,96 |
0,94 |
0,92 |
0,90 |
Качения КПД
блока
|
0,99 |
0,98 |
0,97 |
0,96 |
0,95 |
1.3.Гибкие подъемные и тяговые органы
В качестве гибких тяговых органов используются стальные канаты, и пластинчатые цепи. Их выбор зависит от назначения, условий эксплуатации, режима работы и особых требований.
Канаты. Промышленность выпускает стальные проволочные канаты разных типов, различающихся конструкцией, характером и направлением свивки и размером проволок. Конструкции стальных канатов представлены на рис. 1.3.
а – одинарной свивки, б – двойной свивки из отдельных прядей, в – тройной свивки из канатов двойной свивки, г – односторонней свивки, д – крестовой свивки, е – типа ЛК-О, ж – типа ЛК-Р, з – ЛК-РО
Рисунок 1.3 – Стальные канаты
10
В канатах двойной и тройной свивки предусмотрен сердечник, который может быть органическим (ОС) из натуральных (пенька) или синтетических материалов, металлическим сердечником (МС) и асбестовым (АС).
По роду свивки проволок в прядях различают канаты следующих типов: ТК – с точечным касанием проволок между собой в прядях, ЛК – с линейным касанием проволок в прядях.
По направлению свивки различают канаты правой и левой свивок. Используется и модернизированная конструкция канатов типа ЛК, пряди которых предварительно обшиты. Долговечность этих канатов выше в 1,3...2,8 раза, а разрывное усилие больше на 10...15%.
Все канаты стандартизированы. В грузоподъемных машинах в качестве тяговых канатов при однослойной на барабан и нарезных канавках на нем широко применяются канаты типа ЛК - Р (6x19, ГОСТ 2688 - 80 проволок двух разных диаметров в верхнем слое пряди, рис. 1.3) и ЛК - РО (6x36, ГОСТ 7668 - 80, проволок одинакового и разного диаметра по отдельным слоям, рис. 1.3). Характеристики этих канатов выборочно приведены в таб. 1.6; 1.7; 1.8.
Таблица 1.6 – Размеры и параметры канатов двойной свивки типа ЛК-РО конструкции 6х 36 (1 + 7 + 7/7 + 14) +1 о.с. (по ГОСТ 7668 – 80*)
Диаметр каната dK, мм |
Расчетная площадей сечения всех проволок,
|
Масса 1000м смазанного каната, кг |
Расчетное
разрывное усилие каната
(не
менее), при
| |||
1372 (140) |
1568 (160) |
1666 (170) |
1764 (180) | |||
8,1 |
25,67 |
253,5 |
- |
- |
- |
37,85 |
9,7 |
38,82 |
383,5 |
- |
50,9 |
54,1 |
57,25 |
11,5 |
51,95 |
513 |
- |
68,15 |
72,4 |
76,65 |
13,5 |
70,55 |
696,5 |
- |
92,55 |
98,3 |
104 |
15,0 |
87,60 |
865 |
- |
114,5 |
122 |
129 |
16,5 |
105,24 |
1040 |
- |
138 |
146,5 |
155 |
18 |
125,77 |
1245 |
- |
165 |
175 |
179 |
20 |
153,98 |
1520 |
- |
202 |
214,5 |
219,5 |
22 |
185,10 |
1830 |
212 |
242,5 |
258 |
264 |
23 |
214,57 |
2120 |
246 |
281,5 |
299 |
306 |
25,5 |
252,45 |
2495 |
289,5 |
331 |
351 |
360 |
27 |
283,78 |
2800 |
325,5 |
372 |
395,5 |
405 |
29 |
325,42 |
3215 |
373,5 |
426,5 |
453,5 |
464 |
31 |
369,97 |
3655 |
424,5 |
485 |
515,5 |
528 |
33 |
420,96 |
4155 |
483 |
552 |
586,5 |
600,5 |
36,5 |
503,08 |
4965 |
577,5 |
660 |
701 |
718 |
39,5 |
615,95 |
6080 |
707 |
808 |
858,5 |
879 |
42 |
683,67 |
6750 |
784,5 |
896,5 |
953 |
975,5 |
11
Таблица 1.7 – Размеры и параметры канатов двойной свивки типа ЛК-Р конструкции 6 х19 (1 + 6 + 6/6) + 1 о.с. (по ГОСТ 2688 – 80*)
Диаметр каната dK, мм |
Расчетная площадей сечения всех проволок, мм2 |
Масса 1000м смазанного каната, кг |
Расчетное
разрывное усилие каната
| |||
|
|
|
1372(140) |
1568(160) |
1666(170) |
1764(180) |
3,8 |
5,63 |
55,1 |
- |
- |
- |
8,4 |
4,1 |
6,55 |
64,1 |
- |
- |
- |
9,75 |
4,5 |
7,55 |
73,9 |
- |
- |
- |
11,25 |
4,8 |
8,62 |
84,4 |
- |
- |
- |
12,85 |
5,1 |
9,76 |
95,5 |
- |
- |
- |
14,9 |
5,6 |
11,9 |
116,5 |
- |
- |
- |
18,2 |
6,9 |
18,05 |
176,6 |
- |
24,5 |
26,85 |
26,85 |
8,3 |
26,15 |
256 |
- |
35,55 |
37,75 |
38,95 |
9,1 |
31,18 |
305 |
- |
42,35 |
45,05 |
46,4 |
9,9 |
36,66 |
358,6 |
- |
49,85 |
52,85 |
54,44 |
11 |
47,19 |
461,6 |
- |
64,15 |
68,15 |
70,25 |
12 |
53,87 |
527 |
- |
73,25 |
77,8 |
80,2 |
13 |
61 |
596,6 |
72,55 |
82,95 |
88,1 |
90,85 |
14 |
74,4 |
728 |
88,5 |
101 |
107,5 |
110,5 |
15 |
86,28 |
844 |
102,5 |
117 |
124,5 |
128,5 |
16,5 |
104,61 |
1025 |
124 |
142 |
151 |
155,5 |
18 |
124,73 |
1220 |
148 |
169,5 |
180 |
185,5 |
19,5 |
143,61 |
1405 |
170,5 |
195 |
207,5 |
213,5 |
21 |
167,03 |
1535 |
198,5 |
227 |
241 |
248,5 |
22,5 |
188,78 |
1850 |
224,5 |
256,5 |
272,5 |
281 |
24 |
215,49 |
2110 |
256 |
293 |
311 |
320,5 |
25 |
244 |
2390 |
290 |
331,5 |
352,5 |
363 |
28 |
297,63 |
2911 |
354 |
404,5 |
430 |
443 |
30,5 |
356,72 |
3490 |
424 |
485 |
515 |
531 |
12
Таблица 1.8 – Размеры и параметры канатов двойной свивки типа ЛК-О конструкции 6х19 (1 + 9 + 9) + 1 о.с. (по ГОСТ 3077 – 80*)
Диаметр каната dK, мм |
Расчетная площадей сечения всех проволок, мм2 |
Масса 1000м смазанного каната, кг |
Расчетное
разрывное
усилие
каната
| |||
|
|
|
1372 (140) |
1568 (160) |
1666 (170) |
1764 (180) |
5,1 |
9,79 |
95,9 |
- |
- |
- |
14,95 |
5,7 |
12,20 |
119,6 |
- |
- |
- |
18,65 |
6,4 |
15,35 |
150,5 |
- |
- |
- |
22,85 |
7,8 |
22,47 |
220,5 |
- |
30,55 |
34,45 |
33,45 |
8,8 |
29,55 |
289,6 |
- |
40,15 |
42,65 |
44 |
10,5 |
39,54 |
287,5 |
- |
53,75 |
57,1 |
58,85 |
11,5 |
49,67 |
487 |
- |
67,5 |
71,75 |
73,95 |
12 |
54,07 |
530 |
- |
73,5 |
78,1 |
80,5 |
13 |
60,94 |
597,5 |
- |
82,85 |
88,05 |
90,75 |
14 |
73,36 |
719 |
- |
99,75 |
106 |
109 |
15 |
85,95 |
852,5 |
- |
118 |
125,5 |
129,5 |
16,5 |
101,68 |
996,5 |
120,5 |
138 |
146,5 |
151 |
17,5 |
117,58 |
1155 |
139,5 |
159,5 |
169,5 |
175 |
19,5 |
139,69 |
1370 |
166 |
189,5 |
201,5 |
208 |
20,5 |
150,19 |
1551 |
188 |
215 |
220,5 |
235,5 |
22 |
177,85 |
1745 |
211,5 |
241,3 |
256,5 |
264,5 |
23 |
198,67 |
1950 |
236 |
270 |
287 |
295,5 |
25,5 |
243,76 |
2390 |
290 |
331,5 |
352 |
363 |
28 |
293,48 |
2880 |
349 |
299 |
424 |
437 |
30,5 |
347,82 |
3410 |
413,5 |
473 |
502,5 |
518 |
По
правилам Гостехнадзора канаты подбираются
по разрывному усилию
,
указанному в стандарте или заводском
сертификате, исходя из соотношения
, (1.6)
где n – коэффициент запаса прочности (табл. 1.9)
Наименование канатов |
Тип провода |
Режим работы |
Коэффициент запаса прочности n |
Коэффициент пропорциональности е | |
для всех кранов, кроме стреловых |
для стреловых кранов | ||||
Грузовые и |
Ручной |
|
4 |
18 |
16 |
стреловые |
Машинный |
Л |
5 |
20 |
16 |
|
|
С |
5,5 |
25 |
18 |
|
|
Т |
6 |
30 |
20 |
|
|
ВТ |
6 |
35 |
25 |
Лебедок для |
Ручной |
|
9 |
16 |
- |
подъема людей |
Машинный |
|
9 |
25 |
- |
13
1.4 Блоки, барабаны
Блоки, применяемые в грузоподъемных машинах, бывают подвижными и неподвижными. Неподвижные, их оси закреплены, служат для изменения направления движения каната. Подвижные блоки используются в полиспастах для выигрыша в скорости или в силе.
Допустимый диаметр блока, мм, огибаемого стальным канатом определяется по формуле
,
(1.7)
где е – коэффициент, зависящий от грузоподъемности машины и режима ее работы (см. табл. 1.9)
Блоки устанавливаются в основном на подшипниках качения и лишь в неответственных случаях - на подшипниках скольжения.
Барабаны изготавливаются литыми из чугуна, например, марки СЧ 15 или стали марки 25 Л (не ниже) и сварными из стали марки Ст3 сп (не ниже).
При однослойной навивке на барабан на его рабочей поверхности нарезают винтовую канавку, которая способствует правильной укладке и уменьшению износа каната.
Если кратность полиспастной системы m >3, то предполагают, что потери на барабане меньше потерь энергии в полиспасте и его размеры принимают в соответствии с требованиями Гостехнадзора.
и
тогда длина барабана
,
(1.8)
где Н – высота подъема, глубина опускания груза, м;
1,5 –витки каната на барабан на запас крепления каната на барабане;
t
–
шаг нарезки на барабане, мм,
мм.
Для определения числа оборотов барабана используют формулу
,
(1.9)
где
–
скорость
подъема груза, м/с;
–диаметр
барабана, мм.
Толщина стенки барабана определяется следующим выражением
,
(1.10)
Общие потери механизма учитываются коэффициентом полезного действия механизма
,
(1.11)
где
–
КПД полиспастной системы механизма
подъеме;
–
КПД
барабана, принимается
=
0,98;
–
КПД
редуктора, принимается
=
0,94.
14
1.5 Привод механизма подъема груза
Электрический привод. Для привода механизмов подъема используют двигатели переменного тока с короткозамкнутым ротором серии МТК (таблица 1.10) и фазным ротором (контактными кольцами) серии МТF (таблица 1.11), а также двигатели постоянного тока.
При малых мощностях можно применять асинхронные электродвигатели общепромышленной серии 4А, а также 4 АЕ со встроенным электромагнитным триодом, 4 АП с повышенным пусковым моментом и 4 АС с повышенным скольжением (таблицы приложения А.5, А.6, А.7).
Асинхронные двигатели с короткозамкнутым ротором серии МТК наиболее просты в устройстве и управлении, надежны в эксплуатации, имеют наименьшую массу, габаритные размеры и стоимость. Эти преимущества обеспечили широкое применение их при относительно небольшой частоте включений, когда не требуется электрического регулирования скорости или достаточно регулировать ее ступенчатость.
В подъемно-транспортирующих машинах двигатели серии МТК используют для привода конвейеров, тихоходных подъемников, электроталей, кран - балок и тихоходных механизмов кранов.
Таблица 1.10 – Технические характеристики крановых асинхронных двигателей с короткозамкнутым ротором серии МТК
Типоразмер электро-двигателя |
Мощность и частота вращения |
Пусковой момент, H·м
|
Макси-мальный момент, H·м
|
Махо-вой момент, кг·м |
Масса, кг | |||||||
|
|
|
|
|
|
|
| |||||
ПВ = 15% |
ПВ = 25% |
ПВ = 40% |
|
| ||||||||
МТК 011-6 |
2 |
780 |
1,7 |
835 |
1,4 |
875 |
42 |
42 |
0,08 |
47 | ||
МТК 012-6 |
3,1 |
785 |
2,7 |
835 |
2,2 |
880 |
67 |
67 |
0,11 |
53 | ||
МТК 111-6 |
4,5 |
825 |
4,1 |
850 |
3,5 |
885 |
104 |
105 |
0,18 |
70 | ||
МТК 1 12-6 |
6,5 |
845 |
5,8 |
870 |
5 |
895 |
175 |
175 |
0,26 |
80 | ||
МТК 21 1-6 |
10,5 |
800 |
9 |
840 |
7,5 |
880 |
210 |
220 |
0,44 |
ПО | ||
МТК 31 1-6 |
14 |
880 |
13 |
895 |
11 |
910 |
380 |
390 |
0,85 |
155 | ||
МТК 31 2-6 |
19,5 |
900 |
17,5 |
915 |
15 |
930 |
590 |
600 |
1,20 |
195 | ||
МТК 41 1-6 |
13 |
905 |
27 |
915 |
22 |
935 |
720 |
780 |
1,90 |
255 | ||
МТК 4 12-6 |
40 |
910 |
36 |
920 |
30 |
935 |
950 |
1000 |
2,55 |
315 | ||
МТК 31 1-8 |
10,5 |
660 |
9 |
670 |
7 |
690 |
3320 |
330 |
1,1 |
155 | ||
МТК 31 2-8 |
15 |
675 |
13 |
690 |
11 |
700 |
470 |
510 |
1,55 |
195 | ||
МТК 41 1-8 |
22 |
660 |
18 |
680 |
15 |
695 |
650 |
670 |
2,15 |
255 | ||
МТК 4 12-8 |
30 |
675 |
26 |
690 |
22 |
700 |
950 |
1000 |
3,0 |
315 |
15
Таблица 1.11 – Технические характеристики асинхронных крановых двигателе с фазовым ротором серии MTF
Типоразмер Электрод-вигателя |
Мощность и частота вращения |
Макси-мальный момент, H·м |
Маховой момент, кг·м |
Масса, кг | ||||||
|
|
|
|
|
| |||||
|
ПВ=15% |
ПВ = 25% |
ПВ = 40% |
|
|
| ||||
MTF 011-6 |
2,0 |
800 |
1,7 |
850 |
1,4 |
885 |
40 |
0,09 |
51 | |
MTF 111-6 |
4,5 |
850 |
4,1 |
870 |
3,5 |
895 |
87 |
0,12 |
76 | |
MTF 112-6 |
10,5 |
895 |
5,8 |
915 |
5 |
930 |
140 |
0,27 |
83 | |
MTF211-6 |
10,5 |
895 |
9 |
915 |
7,5 |
930 |
195 |
0,46 |
120 | |
MTF311-6 |
14 |
925 |
13 |
935 |
11 |
945 |
320 |
0,90 |
170 | |
MTF312-6 |
19,5 |
945 |
17,5 |
950 |
15 |
955 |
480 |
1,25 |
210 | |
MTF411-6 |
30 |
945 |
27 |
955 |
22 |
965 |
650 |
2,0 |
280 | |
MTF412-6 |
40 |
960 |
36 |
965 |
30 |
970 |
950 |
2,7 |
345 | |
MTF311-8 |
10,5 |
665 |
9 |
680 |
7 |
695 |
270 |
1,1 |
170 | |
MTF312-8 |
15 |
680 |
13 |
695 |
11 |
705 |
430 |
1,55 |
210 | |
MTF411-8 |
22 |
685 |
18 |
700 |
15 |
710 |
580 |
2,15 |
260 | |
MTF412-8 |
30 |
705 |
26 |
715 |
22 |
720 |
900 |
3,0 |
345 |
Асинхронные двигатели с фазовым ротором (контактными кольцами) серии МТ по сравнению с двигателями серии МТК имеют большую массу, габаритные размеры и стоимость, сложнее в устройстве и управлении. Но они позволяют регулировать скорость при подъеме (опускании) и торможении, изменять в широких пределах момент при пуске и торможении и получать требуемые ускорения, а, следовательно, и необходимую плавность пуска и торможения.
Характерная особенность двигателей с фазным ротором - возможность уменьшения пускового тока с помощью реостата при одновременном увеличении пускового момента.
В двигателях с короткозамкнутым ротором уменьшение пускового тока сопровождается снижением пускового момента, что недопустимо. В обмотках двигателей с фазным ротором меньше потери энергии при переходных процессах, чем у двигателей с короткозамкнутым ротором.
Указанные преимущества позволяют использовать двигатели серии МТ при напряженных режимах работы, характеризующихся большими скоростями, частыми пусками и остановками.
Эти двигатели устанавливают в приводе эскалаторов, механизмов большинства кранов, подъемников, экскаваторов и конвейеров.
Двигатели постоянного тока используют в случаях, когда к электроприводу предъявляются повышенные требования в отношении регулирования скорости, а также при весьма напряженных режимах работы. Их использование требует устройств, преобразующих переменный ток в постоянный, что значительно усложняет и удорожает электропривод.
16
Электродвигатели механизмов подъема рекомендуется подбирать по статической мощности, необходимой для подъема максимального груза, кВт.
, (1.12)
где
,g
= 9,81
;
–скорость
подъема
груза,
м/с;
102 – коэффициент перевода единиц (СГС в СИ);
60 – коэффициент перевода из м/мин в м/с.
Номинальную мощность выбираемого двигателя можно принимать на 10...15 % меньше статической.
1.6 Подбор редукторов, муфт и тормозов для механизмов подъема
Редукторы для грузоподъемных машин выбирают по мощности или вращающему моменту при заданном режиме с учетом обеспечения необходимого передаточного отношения и компоновки механизма.
Условное обозначение редуктора включает в себя наименование изделия (редуктор), обозначение его типоразмера, вариант сборки и формы выступающего конца тихоходного вала (К – коническая, Ц – цилиндрическая, М – в идее части зубчатой муфты), например, редуктор 42-160-200-13-22-Ц-УЗ, где 42 – тип редуктора, 160 – межосевое расстояние, 200 – передаточное число, 13 – вариант сборки, 22 – вариант расположения червячной пары, Ц – цилиндрический конец тихоходного вала, УЗ – климатическое исполнение и категория по ГОСТ 15150-69.
Муфты применяют для соединения валов электродвигателей с быстроходными валами редукторов и тихоходных валов редукторов с барабанами. Муфты также должны компенсировать возможные смещения и перекосы осей соединяемых элементов передачи, возникающих вследствие неточности монтажа и деформации рамы.
Для этих целей широко применяют зубчатые муфты общего назначения и муфты с тормозными шкафами для соединения валов электродвигателей с быстроходными валами редукторов. Допустимый перекос валов для крановых зубчатых муфт составляет 0° 30 .
Для соединения валов часто используют втулочно-пальцевые муфты с упругими элементами в виде резиновых втулок. При использовании такой муфты для соединения вала электродвигателя с быстроходным валом редуктора одна из полумуфт выполняет функции тормозного шкива.
Муфты подбирают в зависимости от передаваемого вращающего момента и условий работы
, (1.13)
где
–
допустимый вращающий момент, который
способен передать муфта;
17
–
расчетный вращающий момент;
–коэффициент,
учитывающий степень ответственности
соединения: для механизма подъема –
1,3; передвижения –
1,2; изменения вылета стрелы и поворота
–
1,4;
–
коэффициент, учитывающий режим работы
механизма: легкий –
1,1; средний –
1,2; тяжелый –
1,3; весьма тяжелый –
1,5;
–
коэффициент условного смещения;
–
действующий номинальный момент.
Согласно
ГОСТ 5006-83 для зубчатых муфт принимают
следующие значения коэффициента
:
Угол перекоса вала |
0,25 |
0,5 |
1 |
1,5 |
|
1 |
1,25 |
1,5 |
1,75 |
Для
всех
остальных
муфт
=1.
Согласно правилам устройства и безопасной эксплуатации грузоподъемных машин для стопорения их механизмов необходимы надежные устройства, в качестве которых используют тормоза и остановы. При этом используют автоматические грузоупорные и двухколодочные тормоза.
В крановых механизмах наиболее часто применяют двухколодочные пружинные тормоза типа ТКТ с короткоходовым электромагнитом переменного тока и тормоза с электрогидравлическим толкателем (таблица 1.14).
Подбор колодочных тормозов.
Для механизмов подъема тормоз рекомендуется подбирать, исходя из условия
,
(1.14)
где
–
создаваемый
тормозной
момент,
.
Расчетный
тормозной
момент,
,
(1.15)
К – коэффициент запаса торможения выбирается из следующих значений в зависимости от режима работы механизма подъема:
Режим работы |
Р, Л |
С |
Т |
ВТ |
К |
1,5 |
1,75 |
2,0 |
2,5 |
1.6.1 Расчет дискового тормоза
В электроталях обычно устанавливаются многодисковые стопорные тормоза и дисковые грузоупорные. Принимается конструкция дискового тормоза (рисунок. 1.14. и 1.15).
18
В
этих
тормозах
давление
на
диски
трения
осуществляется
за
счет
силы
пружины,
а
в
грузоупорных
осевая
сила
создается
при
помощи
пары
винт
– гайка.
Исходя
из
конструктивных
размеров
электротали
(тали),
внутренний
диаметр
диска
выбирают
минимально
допустимым.
Наружный диаметр поверхности трения принимают из условия хорошего смазывания по соотношению
,
(1.16)
причем
≤
120 мм.
1 – подвижные диски; 2 – неподвижные диски
Рисунок.1.4 – Схема стопорного дискового тормоза электротали
Рисунок 1.5 – Схема грузоупорного дискового тормоза электротали
19
15.2. Осевое усилие, необходимое для создания тормозного момента, определяется по формуле
,
(1.17)
где
–
момент
трения
(торможения),
Н·м.
Z – число трущихся поверхностей: Z = 2 при грузоподъемности тали до 2000 Н; Z ≥ 4 при грузоподъемности свыше 2000 Н;
f – коэффициент трения (табл.1.8.4).
15.3. Определяется удельное давление на трущихся поверхностях
,
(1.18)
где [Р] – допускаемое удельное давление, Н/мм2 (табл.1.12).
При
необходимости
увязки
допускаемого
удельного
давления
[P]
и
величины
тормозного
момента
из
формулы
(1.15)
определяют
осевое
усилие
Q,
Н.
Затем
подставляют
значение
Q
в
формулу
(1.17),
из
которой
при
известных
значениях
f,
находят число трущихся поверхностей
Z.
Таблица 1.12 – Таблица коэффициентов трения и удельного давления
Материалы трущихся поверхностей |
Коэффициент трения |
Допускаемые удельные давления [Р], Н/мм2 | |||
Без смазки |
в масленой ванне |
без смазки |
в густой смазке |
в масленой ванне | |
Чугун по чугуну и по стали |
0,15 – 0,20 |
0,06 – 0,08 |
0,3 |
0,4 |
0,8 |
Бронза по стали и чугуну |
0,15 –0,20 |
0,08 – 0,011 |
0,3 |
0,4 |
0,5 |
Лента тормозная асбестовая тканая, ГОСТ ТТ 98 – 69 по металлу: Тип А Тип Б |
0,35 – 0,40 0,30 –0,35 |
0,10 – 0,12 0,09 – 0,12 |
0,3 0,3 |
0,6 0,6 |
0,8 0,8 |
Лента вальцовочная, ТУ 3027-51, по металлу |
0,42-0,48 |
0,12-0,16 |
0,6 |
1,0 |
1,2 |
15.4. Определяется суммарный ход дисков при растормаживании
20
Н= Z·Е, (1.19)
где Е – зазор между парой поверхностей трения, мм;
Е = 0,5 – при установке фрикционных обкладок на неподвижных дисках;
Е = 0,2 – при работе стальных дисков в масляной ванне.
Величина
суммарного
хода
дисков
Н
не
должна
превышать
максимального
хода
якоря
магнита
(таблица
1.13).
Если
это
условие
не
выполняется,
необходимо
увеличить
поверхность
трения
,
чтобы уменьшить
число
трущихся
поверхностей
Z.
Таблица 1.13 – Зависимость усилия и хода якоря от грузоподъемности
Грузоподъемность электротали, кН |
5 |
10 |
20 |
Максимальное усилие одного магнита, Н |
100 |
250 | |
Максимальный ход якоря, мм |
25 |
25 |
1.6.2 Проектирование металлоконструкции крана
Металлические конструкции грузоподъемных машин выполняют сварными и клепаными. Наибольшее распространение получили сварные конструкции, которые изготовляют из стальных листов, стального фасонного проката, гнутых и штампованных профилей из углеродистых и низколегированных сталей. Для металлических конструкций в основном используют сталь Ст.3 (ГОСТ 380-71), которая обладает достаточно высокими механическими свойствами, удовлетворительной ударной вязкостью и хорошими технологическими свойствами: свариваемостью и пластичностью.
Для металлоконструкций применяют листовую и профильную прокатную сталь. Профильную сталь разделяют на сортовую (полоса, квадрат, уголки) и фасонную (двутавры, швеллеры и т.д.).
Наибольшее распространение при расчете металлических конструкций получил метод допускаемых напряжений, основанный на сравнении напряжений, возникающих в элементах конструкции от действия расчетных нагрузок с допускаемыми напряжениями, т.е.
,
(1.20)
где
–
предел
текучести,
принимается
по
таблице;
n – запас прочности, принимается по таблице.
В
качестве
расчетных
нагрузок
принимается
заданная
грузоподъемность,
умноженная
на
коэффициент
динамичности
:
=1,1
– при
легком
режиме;
=1,2
–
при
среднем
режиме;
=1,3
–
при
тяжелом
режиме.
21
Допустимое напряжение при расчете металлоконструкций для стали марки Ст.3 принимается 140…160 Н/мм2.
Одной из серьезных задач при проектировании металлоконструкицй является экономия металла. Поэтому преподаватель совместно с группой, изучив различные металлические конструкции кранов по литературным источникам, дает задание студентам на разработку различных вариантов, анализ которых позволит правильно выбрать и обосновать наилучший вариант, который выносится для защиты.
1.7 Пример расчета механизма подъема груза
Выполнить
расчет
механизма
подъема
полноповоротного
крана
с
электрическим
приводом
при
следующих
исходных
данных:
грузоподъемность
100
кН,
высота
подъема
Н
=
10 м, скорость
подъема
= 0,2 м/с;
режим
работы
средний
(ПВ
=
25%). Кран
используется
для
перегрузки
грузов.
1 – двигатель, 2 – муфта, 3 – тормозное устройство, 4 – муфта,5 – редуктор,
6 – барабан, 7 – блок направляющий подвижный,8 – блок направляющий неподвижный, 9 – круговая обойма с крюком
Рисунок 1.6 – Расчетная схема механизма подъема
Основные сборочные единицы механизма подъема (см. рис. 1.6): крановая подвеска, полиспаст, барабан, редуктор, тормоз и электродвигатель. Расчет механизма подъема крана выполняется в следующем порядке.
Выбор схемы подвески.
Исходя из выбранной схемы подъема груза, определяем кратность полиспастной системы
.
Выбор крюковой подвески.
22
С учетом принятой схемы подвески груза выбираем крюковую подвеску с верхним расположением блока (см. рис. 1.6). При грузоподъемности до 10 т применяют, как правило, однорогие крюки (по ГОСТ 6627-74). Зная грузоподъемность и режим работы механизма, по таблице 1.3 выбираем крюк № 16 и таблице 1.4 его масса 33 кг.
Выбор каната.
Канат
выбирается
по
разрывному
усилию
.
Определяется усилие в канате, наматываемом на барабан:
,
где
–
КПД
полиспастной
системы,
который
определяется
в
первом
приближении
=
,
где
берется
по
таблице
1.5
=
26,13 кН.
Определяем разрывное усилие
,
где n – коэффициент запаса прочности пакета, берется по таблице 1.9
5,5∙26,13
=143,70 кН.
По
разрывному
усилию
из
таблицы
1.6 выбираем
диаметр
пакета
=
18 мм,
тип
каната
ЛК-РП
6-19, (ГОСТ
2688-80),
разрывное
усилие
169,5
кН,
=1568
МПа.
Определение размеров блоков и барабана.
Диаметр блока определяется по формуле (1.7).
,
где е – коэффициент, зависящий от грузоподъемности машины и режима ее работы, принимается по таблице 1.9.
мм.
Уточняем
значение
для
канатов
крестовой
свивки
=
25.
=
25·18 = 450 мм.
Принимаем
=
450 мм.
Определяем
- диаметр
блока
по
оси
каната
в
желобе.
450
+ l8 = 468 мм.
Берем
стандартный
размер
=
450 мм.
23
Уточняем
коэффициент
полезного
действия
полиспаста
с
учетом
подвижных
и
неподвижных
блоков,
для
этого
определяем
их
КПД,
то
есть
и
,
где К = 1,185 – коэффициент, характеризующий изгибную жесткость каната крестовой свивки типа ЛК;
μ = 0,012 – приведенный коэффициент трения в подшипниках качения;
–
диаметр
оси
блока,
определяется
по
формуле
,
где
–
изгибающий момент в опасном сечении
оси блока, Н∙м;
,
–
длина
оси
блока,
принимается
по
таблице
1.12
Таблица 1.14 – Длина ступицы блока, мм
Диаметр блока |
150 |
200 |
250 |
300 |
350 |
400 |
450 |
500 |
600 |
Длина ступицы |
40 |
50 |
50 |
50 |
60 |
70 |
100 |
120 |
150 |
м,
.
где α – угол угла охвата канатом блока, принимается α = 90º.
,
,
где
2 и
3 – степени,
равные
числу
подвижных
и
неподвижных
блоков
по
схеме,
представленной
на
рисунке
1.2. Уточняем
усилие
натяжения
каната
и
разрывное
усилие
.
кН,
=5,5∙30,588=168,236
кН.
24
По
таблице
1.6 диаметр
каната
=
18 мм
Окончательно
выбираем
канат
типа
ЛК-Р
6x19 (по
ГОСТ
2688-80) со
следующими
параметрами:
= 18 мм,
= 169,15 кН,
= 1569 МПа
(160 кгс/
мм2).
Длина барабана определяем по формуле (1.8)
мм,
при
мм.
Принимаем
=
0,6 м
Определяем толщину стенки барабана
δ
=
+
(6...10) мм
= 0,02∙450
+ 8 = 17 мм.
Определяем число оборотов барабана по формуле (1.9)
об/с.
Выбор электродвигателя проводится по формуле (1.12)
Вт
= 2,554 кВт.
при
.
По
таблице
1.11 при
ПВ
= 25% выбираем
двигатель
с
фазовым
ротором
серии
MTF012-6.
Характеристики
двигателя:
= 2,7 кВт;
= 840
;
маховый
момент
ротора
;
=
57 Н∙м;
масса
= 58 кг.
Выбор редуктора.
Редуктор выбирается по передаточному числу и вращающему моменту на тихоходном валу. Расчетное передаточное число редуктора
.
Вращающий момент на тихоходном валу редуктора равен моменту на барабане
кН·м.
По
таблице
1.13 по
и
выбираем
редуктор
Ц2-400
цилиндрический
горизонтальный
двухступенчатый
редуктор
типа
Ц2.
Передаточное
число
редуктора
= 25, отличается
от
расчетного
на
,
что не превышает допустимого, т. е. 4%; момент на тихоходном валу
=
9 кН∙м,
т. е. больше расчетного значения.
25
Выбор тормоза.
Тормоз устанавливают на быстроходном валу привода. Расчетный тормозной момент определяется по формуле (1.15)
,
Н·м.
По
таблице 1.16 выбираем колодочный тормоз
ТКТ-300 с тормозным шкивом 300 мм, развивающий
тормозной момент
=500 Н∙м
(при ПВ= = 25%).
Таблица 1.15– Технические характеристики цилиндрических горизонтальных двухступенчатых редукторов типа Ц2
Типораз-мер редуктора
|
Передаточное число
|
Вращающий момент на тихоходном валу , кН∙м, при режиме работы | ||||||||
Л |
С |
Т |
ВТ | |||||||
И
частоте
вращения,
| ||||||||||
600 |
960 |
600 |
960 |
600 |
960 |
600 |
960 | |||
Ц2-250 |
10; 12,5; |
3,5 |
2,8 |
2,5 |
1,8 |
1,5 |
1,1 |
1 |
0,9 | |
|
16; 20; |
3,8 |
3,3 |
2,7 |
2,6 |
1,5 |
1,3 |
1,0 |
0,9 | |
|
25; 31,6; |
3,8 |
3,3 |
2,7 |
2,6 |
1,5 |
1,3 |
1,2 |
1 | |
|
40; 50 |
4 |
3,8 |
2,8 |
2,7 |
1,5 |
1,3 |
1,2 |
0,9 | |
Ц2-300 |
10; 12,5; |
5 |
4 |
4,4 |
3,5 |
2,3 |
2,0 |
1,4 |
1,4 | |
|
16; 20; |
5,8 |
5,0 |
4,6 |
3,8 |
2,3 |
2,1 |
1,4 |
1,4 | |
|
25; 31,5; |
5,8 |
5,0 |
4,3 |
4,3 |
2,7 |
2,5 |
1,8 |
1,6 | |
|
40; 50 |
6 |
5,4 |
4,4 |
4,3 |
2,5 |
2,3 |
1,8 |
1,6 | |
Ц2-350 |
10; 12,5; |
8 |
7,1 |
6 |
5,6 |
3,5 |
2,8 |
2,2 |
2,1 | |
|
16; 20; |
9 |
7,3 |
6,8 |
5,6 |
3,5 |
3 |
2,2 |
1,9 | |
|
25; 31,6; |
9,5 |
8,2 |
6,5 |
6,3 |
4,1 |
3,3 |
2,7 |
2,2 | |
|
40; 50 |
9,5 |
8,5 |
6,7 |
6,3 |
3,7 |
3,3 |
2,7 |
2,2 | |
Ц2-400 |
10; 12,5; |
14 |
11,2 |
8,2 |
6,2 |
5,3 |
3,8 |
4,1 |
4,1 | |
|
16; 20; |
18 |
14 |
11,5 |
8,2 |
6,5 |
4,8 |
4,4 |
3,7 | |
|
25; 31,6; |
18,5 |
16,5 |
11,5 |
9 |
6 |
4,3 |
4,4 |
4,4 | |
|
40; 50 |
18,5 |
17 |
11,5 |
9 |
6 |
4,6 |
5 |
4,4 | |
Ц2-500 |
10; 12,5; |
28 |
24 |
18 |
16 |
11,2 |
9 |
7,3 |
7,3 | |
|
16; 20; |
31,5 |
24,3 |
21,2 |
17,5 |
11,2 |
9 |
7,3 |
6,5 | |
|
25; 31,6; |
31,5 |
30 |
21,2 |
20 |
13,2 |
7 |
7,3 |
6,5 | |
|
40; 50 |
31,5 |
30 |
21,2 |
20 |
13,2 |
10,6 |
7,3 |
6,5 |
26
Таблица 1.16 – Тормоза колодочные короткоходовые типа ТКТ
Тип |
Тормоз-ной момент |
Удельное давление на колодка, МПа |
Отход колодок, мм |
Момент магнита, Н·м |
Ход штока, мм |
Тип магнита |
Масса тор-моза, кг |
Размеры | ||||
|
|
а |
b |
| ||||||||
ТКТ-100 |
20 |
0,12 |
0,4...0,6 |
5,5 |
2...3 |
МО 100Б |
12 |
100 |
70 |
100 |
170 |
22 |
ТКТ-200/ 100 |
40 |
0,04 |
0,4...0,6 |
5,5 |
2...3 |
МО 10Б |
25 |
200 |
90 |
170 |
305 |
22 |
ТКТ 200 |
160 |
0,18 |
0,5...0,8 |
40 |
2,5...3,8 |
МО 200Б |
37 |
200 |
90 |
170 |
305 |
40 |
ТКТ-300/ 200 |
240 |
0,07 |
0,5...0,8 |
40 |
2,5...3,8 |
МО 200Б |
68 |
300 |
140 |
240 |
430 |
40 |
ТКТ - 300 |
500 |
0,16 |
0,7...1 |
100 |
3...4,4 |
МО 300Б |
92 |
300 |
140 |
240 |
430 |
46 |
Расчет окончен.
1.8 Расчет и проектирование механизма поворота крана
Главный конструктор в зависимости от типа крана и его назначения предлагает конструкторам проработать несколько вариантов механизма крана, при этом могут быть разработаны различные механизмы поворота, кинематические схемы, опорные устройства крана их конструктивное исполнение и расположение.
В зависимости от места расположения привода механизма поворота крана, их подразделяют на механизмы с приводом, расположенным на поворотной или неподвижной части кран и вне крановой конструкции.
Механизмы поворота у поворотных кранов служат для вращения металлоконструкции и груза.
Принципиальное отличие работы механизмов поворота от рассмотренных выше механизмов подъема и передвижения заключается в том, что при повороте отсутствует поступательно движущиеся массы – имеются только вращающие массы.
Существует два основных типа поворотных кранов:
а) краны с поворотной колонной (с переменным вылетом, рис. 1.6; с постоянным вылетом, рис. 1.7);
б) краны с неподвижной колонной (с переменным вылетом, рис. 1.8 и с постоянным вылетом конструкции, как на рис. 1.7, но без тележки (рис. 1.6).
Из атласов по ПТМ принимают вес металлоконструкции крана Gм или из табл. 1.17 для рис. 1.6; 1.18 для рис. 1.7 и 1.19 для рис. 1.8.
27
Таблица 1.17 – Вес металлоконструкции крана, указанного на рисунке 1.6
Грузоподъемность Q, Н |
Вылет стрелы l, м |
Вес тележки Gт, Н |
Вес металлоконструкции Gм , Н |
50000 |
4,5 7,5 |
4500 4500 |
30000 30000 |
75000 |
4,5 7,5 |
5500 5500 |
38000 45000 |
Таблица 1.18 – Вес металлоконструкции крана, указанного на рисунке 1.7
Грузоподъемность Q, Н |
Вылет стрелы l, м |
Вес тележки Gт, Н |
50000 |
4,5 7,5 |
20000 25000 |
75000 |
4,5 7,5 |
28000 37000 |
Таблица 1.19 – Вес металлоконструкции крана, указанного на рисунке 1.8
Грузоподъемность Q, Н |
Вылет стрелы l, м |
Вес тележки Gт, Н |
Вес металлоконструкции Gм , Н |
15000 |
4 7 |
3500 |
15000 25000 |
50000 |
4 7 |
4500 |
30000 50000 |
75000 |
4 7 |
5500 |
40000 60000 |
Рисунок 1.6 – Схема крана с поворотной колонной и переменным вылетом
28
Рисунок 1.7 – Схема крана с поворотной колонной и постоянным вылетом
Рисунок 1.8 – Схема крана с неподвижной колонной и переменным вылетом
29
1.8.1 Последовательность расчета механизма поворота
1. Определяется нагрузка от противовеса (Н)
,
(1.21)
где l – вылет стрелы, м;
–расстояние
от оси вращения до центра тяжести
противовеса, м;
,
(1.22)
2. Определяются усилия, действующие в опорах поворотной части крана:
вертикальное усилие
,
(1.23)
горизонтальное усилие
,
(1.24)
3. Определяются диаметры цапф верхней и нижней опоры, мм (рисунок 1.9; 1.10; 1.11; 1.12)
,
(1.25)
где Н – горизонтальная опорная реакция, Н;
h – расстояние между опорами, мм;
–допускаемое
напряжение на изгиб, МПа;
=
80…100 МПа – для стали 40 или 50.
4. Определяется длинна втулки из условия невыдавливания смазки (если опора на подшипниках скольжения)
,
(1.26)
где
–
диаметр цапфы, мм;
[Р] –допускаемое давление, МПа;
[Р] = 8…12 МПа – для бронзовых втулок;
[Р] = 12…16 МПа – для чугунных и стальных втулок.
5. Определяется диаметр неподвижной колонны у нижней опоры, мм (рисунок 1.12)
,
(1.27)
где
Q,
,
– действующие нагрузки, Н;
l,
,
– плечи приложения действующих нагрузок,
мм;
30
–допускаемое
напряжения для материала колонны, МПа;
=
80…100 МПа – для колонны, изготовленной
из материала сталь 50.
Рисунок 1.9 – Верхняя опора крана с поворотной колонной
Рисунок 1.10 – Нижняя опора крана с поворотной колонной
31
Рисунок 1.11 – Верхняя опора крана с неподвижной колонной
1 – корпус катков; 2 – каток; 3 – ось катка
Рисунок 1.12 – Нижняя опора крана с неподвижной колонной
6. Определяется длина катка из условия не выдавливания смазки
,
(1.28)
где Н – горизонтальная опорная реакция, Н;
d – диаметр оси катка, мм;
[Р] – допускаемое удельное давление
2α – угол между двумя смежными катками (рисунок 1.12), обычно α =30°.
32
Диаметр
катка
,
мм.
Если
,
необходимо сделать перерасчет,
предварительно увеличив
.
Длину оси катка l1
рекомендуют принимать: l1=
l
+ (20…30) мм.
7. Проверяется ось катка на изгиб
,
(1.29)
8. По диаметрам цапф колонны подбираются подшипники. При этом по вертикальному усилию «V» рассчитывается и выбирается упорный шарикоподшипник, а по горизонтальному усилию «Н» – радиальный подшипник.
9. Определяется статистический момент сопротивления повороту (момент при установившемся режиме работы) относительно оси поворота крана (момент трения), Н·м
=
ТВ
+ ТН
, (1.30)
где ТВ –момент трения в верхней опоре, Н·м;
ТН – момент трения в нижней опоре, Н·м;
9.1. Для крана с поворотной колонной момент трения в верхней опоре
,
(1.31)
9.2. При сплошной пяте момент трения в нижней опоре
,
(1.32)
9.3. Для крана с неподвижной колонной при сплошной пяте момент трения в верхней опоре
,
(1.33)
9.4. При установке оси катков с эксцентриситетом для регулирования положения катков относительно колонны и компенсаций изготовления корпуса катков момент трения в нижней опоре
,
(1.34)
где
– сопротивление передвижению катков,
Н
,
(1.35)
Примечание. При наличии кольцевой пяты момент трения от вертикального усилия V определяется по формуле
,
(1.36)
где dН, dВ – соответственно наружный и внутренний диаметры кольцевой пяты, м.
33
Если в пяте имеется упорный подшипник, тогда момент трения будет равен
,
(1.37)
где d0 – диаметр цапфы, м.
f – коэффициент трения в подшипниках: f = 0,08…0,1 – для подшипников скольжения; f = 0,013…0,2 – для подшипников качения;
µ – коэффициент трения качения катка, м;
Д – диаметр катка, м;
d – диаметр оси катка, м;
–диаметр
колонны, м (см. рисунок 1.12);
dЦ – диаметр цапфы опоры крана, м (см. рисунок 1.11).
10. Статическая мощность (кВт), необходимая для поворота крана при работе с номинальным грузом, определяется по формуле
,
(1.38)
где
–
статистический момент сопротивления
повороту относительно оси вращения,
Н·м;
n
–
частота вращения крана,
;
η – общий КПД механизма поворота;
=
0,68…0,70 – для червячного редуктора;
=
0,80…0,82 –для зубчатых колес.
11.
По полученной статической мощности
выбирается электродвигатель (см.
приложение А.5, А.6, А.7). Выписываются
технические данные выбранного
электродвигателя:
–номинальная
мощность, кВт;
–частота
вращения вала двигателя,
;
маховой
момент ротора двигателя,
;
–коэффициент
допускаемой нагрузки/ кратность
максимального момента
к номинальному моменту
при ПВ = 25%
,
(1.39)
12. Определяется общее передаточное число привода механизма поворота
,
(1.40)
которое разбивается на ряд передаточных чисел (редуктора, открытой конической пары и открытой цилиндрической пары)
34
,
(1.41)
где
n
– число вращения крана,
;
–передаточное
число редукторов;
–передаточное
число конической пары;
–передаточное
число цилиндрической пары.
Так как обычно простые поворотные краны имеют небольшую частоту вращения, то передаточное число привода механизма поворота получается весьма большим, поэтому главный конструктор должен уделить особое внимание правильной его разбивке на ряд передач. В этом случае рекомендуется разработать несколько вариантов, и после их глубокого анализа выбрать наилучший с учетом компоновки механизма привода и крана, его расположение на кране эстетических, экономических и других факторов. В приводе механизма поворота могут быть использованы различные типы редукторов: червячные, цилиндрически – конические и другие.
Поэтому прежде чем перейти компоновке привода механизма поворота, рекомендуется подробное изучение конструкций приводов по литературным источникам.
13. Для поворотных кранов, имеющих противовесы, пусковой момент определяется по формуле
,
(1.42)
где
–
статистический момент сопротивления,
Н·м,
приведенный к валу двигателя
,
(1.43)
β – коэффициент, учитывающий влияние вращающихся масс передаточного механизма; β = 1,1…1,2.
–маховой
момент ротора электродвигателя, Н·м2;
–маховой
момент муфты, Н·м2;
–время
пуска
(разгона),
=
2…5 с;
частота
вращения вала двигателя,
;
Q – грузоподъемность крана, Н;
–нагрузка
от противовеса, Н, определяется по
формуле (1.21);
–расстояние
от оси вращения до центра тяжести стрелы,
м;
35
–расстояние
от оси вращения до центра тяжести
противовеса, м;
U0 – общее передаточное число привода механизма поворота;
η – общий КПД привода механизма поворота.
В связи с тем, что момент сопротивления повороту от сил трения в несколько раз (от 3 до 10) меньше моментов от сил инерции, то при расчетах возможны случаи, когда действительный коэффициент перегрузки двигателя больше допускаемого, т.е. ψ > [ψ]. В этом случае выбор двигателя следует приводить не по мощности, определенной по формуле (1.38), а по мощности, определенной по формуле
,
(1.44)
где
n
– чистота вращения крана,
;
ψ – коэффициент перегрузки двигателя при пуске, принимаемый для крановых двигателей переменного тока ψ = 2,5…3,4.
14. Затем, после выбора редуктора, производится расчет открытых зубчатых передач и выбор муфт.
15. Расчет тормоза.
Для механизмов поворота величина тормозного момента (Н·м) определяется по формуле
,
(1.45)
где
– время торможения, с;
,
(1.46)
где–
путь торможения или угол поворота, рад.:
–для
легкого режима работы;
–для
среднего режима работы;
–для
тяжелого режима работы.
Остальные элементы, входящие в данную формулу, определяются как и в предыдущих формулах.
При величине тормозного момента выбирается тормоз типа ТКТ по таблице 1.16. Выбранный тормоз должен быть отрегулирован на величину тормозного момента.
36
1.9 Пример расчета механизма передвижения МК
Рассчитать
механизм передвижения мостового
однобалочного крана (кран-балки)
грузоподъемноcтью Q
= 1 т. Пролет крана
=10,5
м, скорость передвижения v
= 0,6 м/с, высота подъема H
= 6м; режим работы средний; управление с
пола. Кран работает в мастерской по
ремонту сельскохозяйственной техники.
Мостовые однобалочные краны грузоподъемностью 1…5 трегламентированы ГОСТ 2045-89* (см. табл.1.20 и рис.1.15).
В соответствии с прототипом выбираем кинематическую схему однобалочного мостового крана (кран-балки) с электрической талью, согласно ГОСТ 22584-96 по грузоподъемности 1 т выбираем электроталь ТЭ 100-521 (см. табл.1.21 и рис.1.16).
Расчет механизма передвижения крана проводим в следующем порядке.
Определяем
размеры ходовых колес по формуле
.
Максимальную нагрузку на колесо вычисляем при одном из крайних положений электротали (см. рис. 1.13).
По
ГОСТ 22584-96 (см. табл. 1.21) принимаем массу
тали
200
кг = 0,2 т (ее вес
кН)
и длинуL
= 700 мм. Массу крана с электроталью
выбираем приближенно по прототипу (см.
табл. 1.20):
=
2т. Тогда вес крана
кН.
Ориентировочно принимаем
=L
= 0,7 м.
Для
определения нагрузки
составим уравнения статики (рис. 1.13)
;
,
Рисунок 1.13 – Мостовой однобалочный кран с электрической талью
37
Откуда
,
кН.
При
общем числе ходовых колес
=
4 нагрузка приходится на те два колеса
крана, вблизи которых расположена
тележка. Тогда
=R/2
= 20/2 = 10 кН = 10000 Н.
Следовательно
мм.
Согласно
ГОСТ 3569-74 (см. табл. 1.22 и рис.1.17) выбираем
крановое двухребордное колесо диаметром
мм.
Диаметр цапфы
мм.
Принимаем
мм.
Для
изготовления колес используем сталь
45, способ термообработки – нормализация
(НВ=200). Колесо имеет цилиндрическую
рабочую поверхность и катится по плоскому
рельсу. При
200мм
принимаем плоский рельс прямоугольного
сечения, выбирая размерa
по условию: а
< В.
При
200
мм ширина поверхности каченияВ
=
50 мм. Принимаем а
= 40мм. Рабочая поверхность контакта
b = а – 2∙r = 40 – 2∙9=22 мм.
Коэффициент влияния скорости
=1
+ 0,2∙v
=1
+ 0,2∙0,6 = 1,12.
Для
стальных колес коэффициент пропорциональности
=190.
Предварительно выбранные ходовые колеса проверяем по контактным напряжениям.
При линейном контакте
МПа.
Поскольку
допустимые контактные напряжения для
стального нормализованного колеса
=
450…500МПа, то условие прочности выполняется.
2.Определяем
статическое сопротивление передвижению
крана по формуле. Поскольку кран работает
в помещении, то сопротивление от ветровой
нагрузки
не учитываем, т.е.
.
Сопротивление от сил трения в ходовых частях крана
.
38
По
таблице 1.23 принимаем μ
= 0,3 мм, а по таблице 1.24 для колес на
подшипниках качения f
= 0,015,
=1,5.
Тогда
кН
= 304 Н.
Сопротивление движению от возможного уклона пути
Н
= 45 кН.
Значения расчетного уклона α указаны в лекции.
Таким
образом, получаем
=
304 + 45 = 349 Н.
Сила инерции при поступательном движении крана
Н,
где
время
пуска, с,
Q
и
– массы соответственно груза и крана,
кг.
Усилие, необходимое для передвижения крана в период пуска (разгона)
Н.
3.Подбираем электродвигатель по требуемой мощности
Вт
= 0,334 кВт.
Предварительно
принимаем η
= 0,85 и
=1,65
(для асинхронных двигателей с повышенным
скольжением).
По
таблице A.7
приложения выбираем асинхронный
электродвигатель переменного тока с
повышенным скольжением 4АС71А6УЗ с
параметрами: номинальная мощность
кВт;
номинальная частота вращения
;
маховой
момент ротора
;
;
.
Диаметр валаd
= 19 мм.
Номинальный момент на валу двигателя
Н∙м.
Статический момент
Н∙м.
4.
Подбираем муфту с тормозным шкивом для
установки тормоза. В выбранной схеме
механизма передвижения муфта с тормозным
шкивом установлена между редуктором и
электродвигателем. В соответствии с
рекомендациями по таблице 1.25 и рис.1.18
подбираем упругую втулочно-пальцевую
муфту с наибольшим диаметром расточки
под вал 22 мм и наибольшим передаваемым
моментом
=32 Н∙м.
39
Проверяем
условие подбора
.
Для муфты
2,1∙4,16
= 8,7 Н∙м. Момент инерции тормозного шкива
муфты
.
Маховой момент
.
Подобранный двигатель проверяем по условиям пуска. Время пуска
c.
Общий маховой момент
,
.
Относительное
время пуска принимаем по графику (см.
рис.1.14 б) в зависимости от коэффициента
α
=.
Посколькуα
= 2,17/4,16 = 0,52, то
=
1 (рис. 1.14).
а – для двигателей с фазовым ротором (контактными кольцами)
б – для двигателей с короткозамкнутым ротором
Рисунок
1.14 –Зависимости относительного времени
пуска
от
величиныα
Ускорение в период пуска определяем по формуле
,
что удовлетворяет условию.
6.Проверяем запас сцепления приводных колес с рельсами по условию пуска при максимальном моменте двигателя без груза
40
Статическое сопротивление передвижению крана в установившемся режиме без груза
,
кН
= 232,5 Н.
Ускорение
при пуске без груза
Время
пуска без груза
.
Общий маховой момент крана, приведенный к валу двигателя без учета груза
,
.
Момент сопротивления, приведенный к валу двигателя при установившемся движении крана без груза
Н∙м.
Передаточное
число механизма
.
Поскольку частота вращения приводных
колес
,
то u = 920/57,3 = 16.
По графику на рисунке 1.14 при
α
==1,71/4,16
= 0,41,
получаем
=1.
Тогда время пуска
с.
Ускорение при пуске
.
Суммарная нагрузка на приводные колеса без учета груза
Н.
Коэффициент
сцепления ходового колеса с рельсом
для кранов, работающих в помещении,
=
0,15.
Запас сцепления
41
,
что больше минимально допустимого значения 1,2.
Следовательно, запас сцепления обеспечен.
7.Подбираем
редуктор по передаточному числу и
максимальному вращающему моменту на
тихоходном валу
,
определяемому по максимальному моменту
на валу двигателя
Н∙м,
Н∙м.
В соответствии со схемой механизма передвижения крана выбираем горизонтальный цилиндрический редуктор типа Ц2У (см. табл.А.10).
При
частоте вращения n
= 1000и
среднем режиме работы ближайшее значение
вращающего момента на тихоходном валу
0,25кН∙м
= 250Н∙м, что больше расчетного
.
Передаточное число
=16.
Типоразмер выбранного редуктора Ц2У-100.
8.Выбираем
тормоз по условию
≥
и устанавливаем его на валу электродвигателя.
Расчетный тормозной момент при передвижении крана без груза
.
Сопротивление движению от уклона
кН
= 30 Н.
Сопротивление от сил трения в ходовых частях крана
кН
= 135 Н.
Общий маховой момент
,
.
Время торможения
c.
Максимально допустимое ускорение
,
.
42
Число
приводных колес
=
2. Коэффициент сцепления
=
0,15. Запас сцепления
=1,2.
Фактическая скорость передвижения крана
м/с.
т.е. совпадает с заданным (исходным) значением.
Расчетный тормозной момент
Н∙м.
По
таблицам 1.26, 1.27, 1.28 рис.1.19 выбираем тормоз
ТКТ-100 с номинальным тормозным моментом
Н∙м,
максимально приближенным к расчетному
значению
.
Подобранный тормоз проверяем по условиям торможения при работе крана с грузом.
Проверка по времени торможения
Маховой момент масс
,
.
Статический момент сопротивления движению при торможении
.
Сопротивление движению при торможении
.
Сопротивление от сил трения
кН
= 202,5 Н.
Сопротивление от уклона
кН
= 45 Н.
Следовательно,
=
202,5 – 45 = 157,5 Н.
Тогда статический момент сопротивления
Н∙м,
а время торможения
43
с,
что
меньше допустимого
6…8 с.
Проверка по замедлению при торможении
,
что
меньше максимально допустимого значения
для кранов, работающих в помещении,
.
Следовательно, условия торможения выполняются.
9.Определяем тормозной путь по формуле
м.
По
нормам Госгортехнадзора при числе
приводных колес, равном половине общего
числа ходовых колес и при
=
0,15
м.
а – полет до 10,5 м; б – полет до 13,5…28,5 м
Рисунок 1.15 – Схемы мостового однобалочного крана типа 1, исполнение А
44
Таблица 1.20 – Технические характеристики мостовых однобалочных кранов (по ГОСТ 22045-89)
Грузо- подъем ность, т |
Пролет, м |
Масса крана, т |
Грузо- подъем- ность, м |
Пролет, м |
Масса крана, т | ||
Испол- нение А |
Испол- нение Б |
Испол-нение А |
Испол-нение Б | ||||
1 |
4,5 |
1,45 |
1,80 |
3,2 |
4,5 |
1,76 |
2,12 |
|
7,5 |
1,70 |
1,95 |
|
7,5 |
2,05 |
2,36 |
|
10,5 |
2,05 |
2,40 |
|
10,5 |
2,60 |
2,95 |
|
(13,5) |
2,70 |
3,05 |
|
16,5 |
3,60 |
3,95 |
|
16,5 |
3,02 |
3,40 |
|
22,5 |
5,05 |
5,41 |
|
(19,5) |
4,07 |
4,45 |
|
28,5 |
7,05 |
7,45 |
|
22,5 |
4,30 |
4,70 |
5 |
4,5 |
2,07 |
2,46 |
2 |
4,5 |
1,55 |
1,90 |
|
7,5 |
2,47 |
2,85 |
|
7,5 |
1,80 |
2,10 |
|
10,5 |
2,95 |
3,29 |
|
10,5 |
2,15 |
2,35 |
|
16,5 |
4,28 |
4,64 |
|
16,5 |
3,20 |
3,50 |
|
22,5 |
6,20 |
6,57 |
|
22,5 |
4,40 |
4,80 |
|
28,5 |
8,45 |
8,83 |
Примечания:
1.Краны выпускают с высотой подъема груза, м: 6; 12; 18.
2.Скорости передвижения кранов, м/мин: исполнение А-25 и 40; исполнение Б - 40 и 63.
3.Значения пролетов, указанные в скобках, применять не рекомендуется.
4.Пример условного обозначения крана типа 1 исполнения А грузоподъемностью 2 т с пролетом 10,5 м и высотой подъема 6м для работы при напряжении трехфазного тока 220 В: кран 1А2-10,5-6-220 ГОСТ 22045-89*Е.
а – исполнение 5; б – исполнение 9
Рисунок 1.16 – Общий вид электроталей
45
Таблица 1.21 – Технические характеристики электрических талей (по ГОСТ 22584-96)
Обозначениетали |
Грузо-подъ-ем- ность, т |
Вы-сота подъ-ема, м |
Размеры, мм (см. рис. 1.16) |
Масса, кг | ||||||||
В |
b |
|
H |
h |
L |
|
| |||||
Не более |
| |||||||||||
ТЭ 025-511 |
0,25 |
6 |
210 |
570 |
110 |
550 |
|
640 |
640 |
5500 |
60 | |
ТЭ 050-521 |
0,5 |
12 |
390 |
450 |
250 |
780 |
20 |
725 |
725 |
11700 |
85..115 | |
ТЭ 050-531 |
0,5 |
18 |
|
|
|
|
|
915 |
915 |
17700 |
85..115 | |
ТЭ 100-511 |
|
6 |
|
|
|
|
|
655 |
655 |
5900 |
140..185 | |
ТЭ 100-521 |
1 |
12 |
330 |
325 |
160 |
855 |
20 |
870 |
870 |
11900 |
160..205 | |
ТЭ 100-531 |
|
18 |
|
|
|
|
|
1085 |
1085 |
17900 |
170..220 | |
ТЭ 500-911 |
|
6 |
|
|
|
|
|
1000 |
1250 |
6500 |
510..615 | |
ТЭ 500-921 |
5 |
12 |
500 |
360 |
250 |
1250 |
25 |
1200 |
1470 |
12500 |
570..660 | |
ТЭ 500-931 |
|
18 |
|
|
|
|
|
1410 |
1700 |
18500 |
550..655 |
Рисунок 1.17 – Эскиз крановых колес
46
Таблица 1.22 – Основные размеры крановых колес, мм (рис.1.17)
D |
|
d |
|
|
B |
|
L |
s |
r |
Мас-са, кг |
200 |
230 |
50 |
80 |
175 |
50 |
80 |
80 |
18 |
18 |
20 |
250 |
290 |
55 |
85 |
220 |
70 |
110 |
110 |
18 |
18 |
30 |
320 |
360 |
70 |
120 |
275 |
80 |
120 |
120 |
20 |
20 |
50 |
400 |
450 |
95 |
150 |
350 |
80..100 |
130..150 |
120;130 |
25 |
25 |
90 |
500 |
550 |
110;115 |
170;175 |
440 |
90..100 |
150 |
135;150 |
35 |
35 |
140 |
560 |
600 |
100;150 |
230;310 |
500 |
90 |
130 |
180 |
35 |
20 |
200 |
630 |
680 |
135 |
200 |
530 |
90..130 |
140..180 |
150 |
35..40 |
40 |
250 |
710 |
770 |
135;145 |
200 |
640 |
100..150 |
150..200 |
150;160 |
35..60 |
40 |
410 |
710 |
770 |
175 |
200 |
640 |
100..150 |
150..200 |
160;190 |
35..60 |
40 |
410 |
710 |
770 |
180 |
200 |
640 |
100..150 |
150..200 |
200 |
35..60 |
40 |
410 |
710 |
770 |
200 |
290 |
640 |
100..150 |
150..200 |
200 |
35..60 |
40 |
410 |
800 |
880 |
155 |
240 |
720 |
100..170 |
150..250 |
150;160;170 |
35..70 |
40 |
640 |
800 |
880 |
165 |
240 |
720 |
100..170 |
150..250 |
160;170 |
35..70 |
40 |
640 |
800 |
880 |
200;220 |
360 |
720 |
100..170 |
150..250 |
200;230 |
35..70 |
40 |
640 |
900 |
980 |
175;190 |
280 |
820 |
120..150 |
190..210 |
170;190 |
45 |
40 |
640 |
1000 |
1080 |
220 |
340 |
880 |
170 |
250 |
230 |
70 |
40 |
890 |
200 |
230 |
50 |
80 |
175 |
65 |
80 |
80 |
18 |
18 |
12 |
250 |
290 |
60 |
85 |
215 |
70 |
90 |
90 |
18 |
18 |
20 |
320 |
360 |
65 |
95 |
285 |
80 |
100 |
100 |
18 |
20 |
31 |
320 |
360 |
85 |
145 |
285 |
80 |
100 |
100 |
18 |
20 |
31 |
400 |
450 |
85 |
130 |
360 |
105 |
130 |
130 |
22 |
20 |
61 |
400 |
450 |
95 |
145 |
360 |
105 |
130 |
110 |
22 |
20 |
61 |
500 |
550 |
105 |
155 |
442 |
125 |
150 |
150 |
28 |
30 |
113 |
Примечания:
Размеры шпоночного паза - по ГОСТ 23360-78. Для неприводных колес допускается бесшпоночное соединение.
Колеса следует изготовлять из стали марки 75 или 65Г по ГОСТ 14959-79. Допускается выполнять колеса диаметром 710…1000мм для кранов легкого, среднего и тяжелого режимов работы из сталей по ГОСТ 10791-89 (соответственно работы механизмов режимам по ГОСТ 25835-90).
Предельные отклонения диаметров D по h 11.
Для обеспечения требуемой твердости поверхности качения и реборд НВ = 300…350 глубина термообработки должна быть, мм, не менее:15- при D = 200…250 мм; 20-при D = 320…500 мм; 30-при D = 560…710 мм; 40- при D = 800…1000 мм.
Пример условного обозначения кранового двухребордного колеса диаметром D = 400мм и шириной поверхности качения В = 100 мм: колесо К2Р-400х100; кранового одноребордного колеса диаметром D = 400 мм: Колесо К1Р-400.
47
Таблица 1.23 – Значения коэффициента μ, мм
Тип рельса |
Диаметры ходовых колес, мм | |||
160…300 |
400…500 |
600…700 |
800 | |
С плоской головкой |
0,3 |
0,5 |
0,6 |
0,7 |
С выпуклой головкой |
0,4 |
0,6 |
0,8 |
1,0 |
Таблица
1.24 – Значения коэффициентов f
и
Тип подшипника |
f |
Тип механизма |
|
Скольжения: открытого типа буксы с жидкой смазкой |
0,1
0,08 |
Крановые тележки с кабельным токоподводом |
2,0 |
Качения: Шариковые и роликовые конические |
0,015 0,02 |
Крановые мосты на катках: с цилиндрическим ободом с коническим ободом При отсутствии ребер |
1,5 1,2 1,0…1,1 |
Рисунок 1.18 – Эскиз упругих втулочно-пальцевых муфт с тормозным шкивом
48
Таблица 1.25 – Характеристики и размеры упругих втулочно-пальцевых муфт с тормозным шкивом (рис.1.18)
Т, Н∙м |
|
n, |
Расчетный момент инерции муфты, |
Размеры, мм |
Масса, кг | |||||
|
d |
|
В |
L | ||||||
тормозного шкива |
Полу-муфты | |||||||||
32 |
25 |
6300 5600 4750 |
0,009 0,008 0,01 |
100 |
18 22 28 |
18 |
75 |
42 |
85 94 104 102 104 104 115 123 125 145 165 145 |
3 |
130 |
4000 |
0,012 |
30 | |||||||
55 |
100 |
5600 4750 4000 4750 |
0,053 0,062 0,057 0,135 |
160 |
22 28 30 28 |
22 25 28
25 |
75 |
42 |
5 | |
7 | ||||||||||
130 |
200 |
95 |
9 11 12 10 | |||||||
250 |
4000 |
0,152 |
30 |
165 |
11 | |||||
240 |
32 25 32 |
55
|
196 |
16 17 21 20 28 | ||||||
130 |
32 | |||||||||
226
| ||||||||||
240 | ||||||||||
38 40 42 48 |
35 | |||||||||
3350 |
0,21 0,256 | |||||||||
450 |
42 48 55 45 50 55 60 | |||||||||
700 |
3000 |
0,0345 |
145
| |||||||
50 | ||||||||||
450 |
800 |
0,707 0,939 0,952 1,105 |
300 | |||||||
700 | ||||||||||
2650 |
60 |
29 | ||||||||
1,132 | ||||||||||
1100 |
65 |
286 |
39 | |||||||
65 |
38 | |||||||||
4000 |
1500 |
1700 |
5,614 |
400 |
90 |
80 |
185 |
85 |
350 |
111 |
49
Таблица 1.26 – Технические характеристики колодочных тормозов типа ТКТ
Типоразмер тормоза |
Тормозной момент, Н∙м |
Диаметр тормозного шкива, мм |
Ширина тормозного шкива, мм |
Отход колодки, мм | ||||||||
ПВ=25% |
ПВ=40% |
ПВ=100% |
Номи-наль-ный |
Наи- боль -ший | ||||||||
ТКТ-100 |
20 |
20 |
10 |
100 |
75 |
0,4 |
0,6 | |||||
ТКТ-200/100 |
40 |
40 |
22 |
200 |
95 |
0,4 |
0,6 | |||||
ТКТ-200 |
160 |
160 |
80 |
200 |
95 |
0,5 |
0,8 | |||||
ТКТ-300/200 |
240 |
240 |
120 |
300 |
145 |
0,5 |
0,8 | |||||
Типоразмер тормоза |
Электромагнит |
Масса тормоза, кг |
| |||||||||
Тип |
Момент якоря номинальный, Н∙м |
Потребляемая мощность, Вт |
| |||||||||
ТКТ-100 |
МО-100Б |
5,5 |
140 |
12 |
| |||||||
ТКТ-200/100 |
МО-100Б |
5,5 |
140 |
25 |
| |||||||
ТКТ-200 |
МО-200Б |
40,0 |
450 |
37 |
| |||||||
ТКТ-300/200 |
МО-200Б |
40,0 |
450 |
68 |
|
Таблица 1.27 – Значения установочной длины пружины тормозов типа ТКТ в зависимости от тормозного момента (для ПВ=25%)
Типоразмер тормоза |
Тормозной момент, Н∙м |
Длина главной пружины, мм, при токе |
Типоразмер тормоза |
Тормозной момент, Н∙м |
Длина главной пружины, мм, при токе | ||
пере-менном |
посто-янном |
пере- менном |
посто-янном | ||||
ТКТ-100 |
10 |
49 |
51 |
ТКТ-200 |
140 |
93,5 |
97 |
15 |
46,5 |
47,5 |
160 |
88,5 |
92,5 | ||
20 |
43 |
44,5 |
ТКТ-300/200 |
180 |
203 |
205,5 | |
ТКТ-200/100 |
25 |
124 |
125 |
200 |
201 |
203 | |
30 |
122,5 |
123,5 |
220 |
197,5 |
201 | ||
35 |
121 |
122 |
240 |
196,5 |
199 | ||
40 |
110 |
121 |
ТКТ-300 |
300 |
|
193,05 | |
ТКТ-200 |
60 |
112,5 |
116,5 |
350 |
|
187,5 | |
80 |
108 |
112 |
400 |
|
182 | ||
100 |
103 |
107 |
450 |
|
176,5 | ||
120 |
98 |
102 |
|
|
|
50
Таблица 1.28 – Основные размеры колодочных тормозов типа ТКТ, мм (рис.1.19)
Типоразмер тормоза |
D |
B |
|
|
|
L |
|
|
|
H |
s |
d |
δ |
h |
ТКТ-100 |
100 |
130 |
70 |
110 |
40 |
421 |
150 |
250 |
120 |
292 |
6 |
13 |
4 |
100 |
ТКТ-200/100 |
200 |
130 |
90 |
175 |
60 |
566 |
265 |
430 |
180 |
432 |
8 |
17 |
6 |
170 |
ТКТ-200 |
200 |
177 |
90 |
175 |
60 |
681 |
265 |
430 |
212 |
480 |
8 |
17 |
6 |
170 |
ТКТ-300/200 |
300 |
177 |
140 |
250 |
80 |
808 |
390 |
540 |
270 |
620 |
12 |
21 |
8 |
240 |
1, 5 – вертикальные рычаги; 2 – скоба; 3 – короткоходовой электромагнит;
4 – якорь; 6 – болт; 7 – пружина; 8 – шток; 9 – вспомогательная пружина;
10 – основание; 11 – колодки
Рисунок 1.19 – Колодочных тормозов типа ТКТ с электромагнитом
51
Таблица 1.29 – Варианты задач по курсовой работе на тему ”Расчёт механизма передвижения мостового однобалочного крана”
Исходные данные |
Варианты | |||||||||||||||||||||||
1 |
2 |
3 |
4 |
5 |
6 |
7 |
8 |
9 |
10 |
11 |
12 | |||||||||||||
Грузо- подъемность, Q, т |
1,0 |
1,2 |
1,3 |
1,4 |
1,5 |
1,6 |
1,7 |
1,8 |
1,9 |
2,0 |
2,0 |
1,2 | ||||||||||||
Пролет
крана,
|
10,0 |
10,1 |
10,2 |
10,3 |
10,4 |
10,5 |
10,6 |
10,7 |
10,8 |
10,9 |
11,0 |
11,2 | ||||||||||||
Скорость передвижения крана, v, м/с |
0,41 |
0,42 |
0,43 |
0,44 |
0,45 |
0,46 |
0,47 |
0,48 |
0,49 |
0,50 |
0,51 |
0,52 | ||||||||||||
Высота подъема груза, Н, м |
6,0 |
6,0 |
6,0 |
6,0 |
6,0 |
12,0 |
12,0 |
12,0 |
12,0 |
12,0 |
18,0 |
18,0 | ||||||||||||
Режим работы |
Средний режим работы | |||||||||||||||||||||||
Управление движением мостового крана: для всех вариантов с пола | ||||||||||||||||||||||||
Исходные данные |
Варианты | |||||||||||||||||||||||
13 |
14 |
15 |
16 |
17 |
18 |
19 |
20 |
21 |
22 |
23 |
24 |
25 | ||||||||||||
Грузо- подъемность, Q, т |
1,3 |
1,1 |
1,4 |
1,5 |
1,5 |
1,6 |
1,6 |
1,7 |
1,7 |
1,8 |
1,9 |
1,9 |
2,0 | |||||||||||
Пролет
крана,
|
11,4 |
11,3 |
11,5 |
11,6 |
11,7 |
11,8 |
11,9 |
12,0 |
10,9 |
10,8 |
10,7 |
10,6 |
10,5 | |||||||||||
Скорость передвижения крана, v, м/с |
0,53 |
0,54 |
0,55 |
0,56 |
0,57 |
0,58 |
0,59 |
0,60 |
0,51 |
0,52 |
0,53 |
0,54 |
0,55 | |||||||||||
Высота подъема груза, Н, м |
18,0 |
18,0 |
18,0 |
6,0 |
6,0 |
6,0 |
6,0 |
6,0 |
12,0 |
12,0 |
12,0 |
12,0 |
12,0 | |||||||||||
Режим работы |
Средний режим работы | |||||||||||||||||||||||
Управление движением мостового крана: для всех вариантов с пола |
52
Таблица 1.30 – Варианты задач по курсовой работе на тему ”Расчёт механизма подъема груза”
Исход-ные данные |
Варианты | ||||||||||||||||||||||||
1 |
2 |
3 |
4 |
5 |
6 |
7 |
8 |
9 |
10 |
11 |
12 |
13 | |||||||||||||
Грузо-подъем-ность, кН |
70 |
75 |
80 |
125 |
120 |
115 |
110 |
105 |
100 |
85 |
90 |
95 |
71 | ||||||||||||
Скорость подъема груза, м/с |
0,24 |
0,23 |
0,22 |
0,21 |
0,20 |
0,18 |
0,19 |
0,20 |
0,21 |
0,22 |
0,23 |
0,24 |
0,21 | ||||||||||||
Высота подъема груза, м |
18 |
12 |
6 |
6 |
12 |
18 |
6 |
18 |
12 |
18 |
12 |
6 |
6 | ||||||||||||
Режим работы |
Средний режим работы | ||||||||||||||||||||||||
Время разгона двигателя до набора номинальных оборотов для среднего режима работы 2…2,5 с | |||||||||||||||||||||||||
Исход-ные данные |
Варианты | ||||||||||||||||||||||||
14 |
15 |
16 |
17 |
18 |
19 |
20 |
21 |
22 |
23 |
24 |
25 |
26 | |||||||||||||
Грузо-подъем-ность, кН |
72 |
81 |
82 |
83 |
84 |
91 |
92 |
93 |
94 |
101 |
102 |
103 |
104 | ||||||||||||
Скорость подъема груза, м/с |
0,17 |
0,18 |
0,19 |
0,20 |
0,22 |
0,23 |
0,24 |
0,21 |
0,19 |
0,18 |
0,17 |
0,23 |
0,25 | ||||||||||||
Высота подъема груза, м |
12 |
12 |
12 |
18 |
18 |
18 |
6 |
6 |
6 |
12 |
18 |
6 |
12 | ||||||||||||
Режим работы |
Средний режим работы | ||||||||||||||||||||||||
Время разгона двигателя до набора номинальных оборотов для среднего режима работы 2…2,5 с |
53