
Методичка по ПКИС
.pdf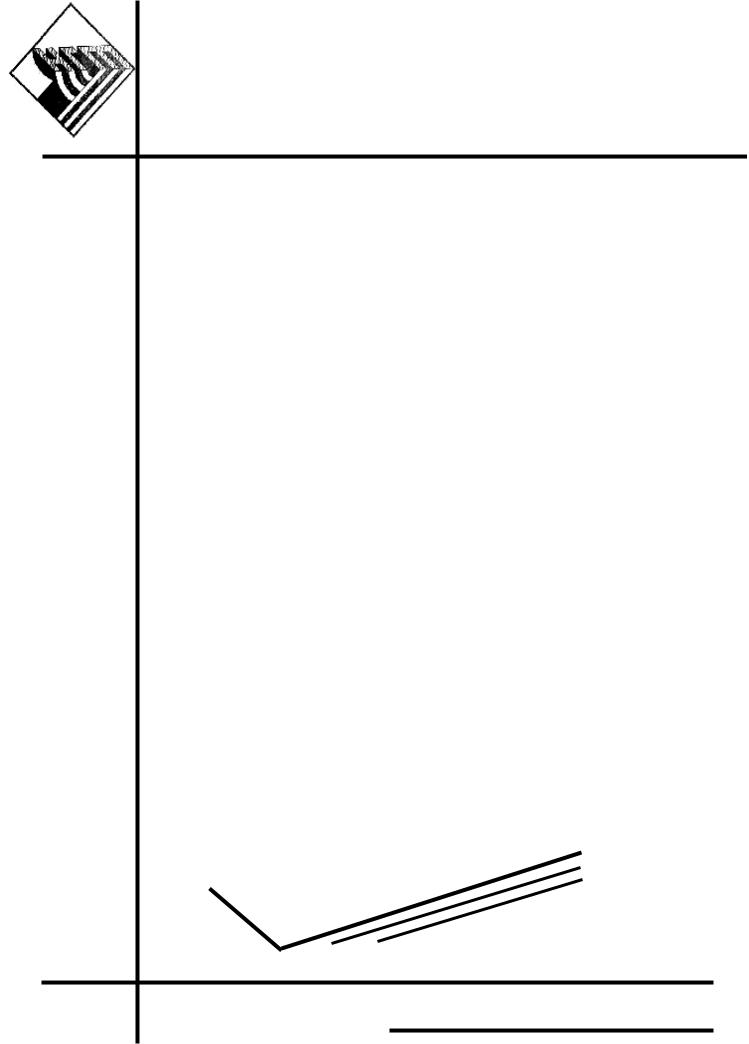
|
Федеральное агентство по образованию |
|
Арзамасский политехнический институт (филиал) |
|
Нижегородского Государственного Технического |
|
Университета им. Р.Е. Алексеева |
УКАЗАНИЯ |
"ПРОЕКТИРОВАНИЕ КОНТРОЛЬНО- |
ИЗМЕРИТЕЛЬНЫХ СРЕДСТВ" |
|
|
|
МЕТОДИЧЕСКИЕ |
Методические указания к практическим занятиям |
для всех форм обучения |
|
специальностей 150900; 151001 |
|
|
|
|
Арзамас 2009 |
PDF created with pdfFactory Pro trial version www.pdffactory.com
Федеральное агентство по образованию Арзамасский политехнический институт (филиал)
Нижегородского Государственного Технического Университета им. Р.Е. Алексеева
Кафедра "Технология машиностроения"
"Проектирование контрольно-измерительных средств"
Методические указания к практическим занятиям для всех форм обучения
специальностей 150900; 151001
Утверждено на заседании кафедры ТМ
" 19 " февраля 2009 г.
протокол № 5
Арзамас 2009
1
PDF created with pdfFactory Pro trial version www.pdffactory.com
УДК 389 001 ББК 30.10 Г 60
Печатается по решению кафедры "Технология машиностроения"
Арзамасского политехнического института НГТУ
"Проектирование контрольно-измерительных средств".
Методические указания к практическим занятиям по дисциплине "Проекти- рование контрольно-измерительных средств" для студентов всех форм обучения специальностей 150900; 151001 / АПИ НГТУ; Сост.: Л.Н. Голышева, О.В. Бунда- кова. – Арзамас: Издательство ОО "Ассоциация ученых" г. Арзамаса, 2009. – 17 с.
В методических указаниях представлен теоретический материал по проек- тированию средств измерения и примеры расчетов специальных средств измере- ний: гладких калибров, калибров расположения, пневматических пробок, кон- трольных приспособлений.
Рис. 4. Табл. 1. Библиогр.: 13 назв.
УДК 389 001 ББК 30.10 Г 60
______________________________________________________________________
"Проектирование контрольно-измерительных средств".
Методические указания к практическим занятиям для студентов всех форм обучения специаль- ностей 150900; 151001 / АПИ НГТУ; Сост.: Л.Н. Голышева, О.В. Бундакова. – Арзамас: Изда- тельство ОО "Ассоциация ученых" г. Арзамаса, 2009. – 17 с.
Компьютерный набор и верстка О.В. Бундаковой.
Лицензия ИД №05442 от 20.07.2001 г. Подп. к печ. 10.10.2006 г. Формат 60×84 1/16.
Бумага газетная. Печать офсетная. Печ. л. Тираж 350 экз. Заказ |
. |
Издатель: ОО "Ассоциация ученых" г. Арзамаса |
|
607220, г. Арзамас Нижегородской области, ул. Калинина, 19. |
|
Участок офсетной печати: |
|
607220, г. Арзамас Нижегородской области, ул. Севастопольская, 15. |
|
©Голышева Л.Н., Бундакова О.В., 2009
©ОО "Ассоциация ученых" г. Арзамаса, 2009
©Арзамасский политехнический институт (филиал) Нижегородского государственного техниче- ского университета им. Р.Е. Алексеева, 2009
2
PDF created with pdfFactory Pro trial version www.pdffactory.com
Содержание
1.Исходные данные и этапы проектирования ……………………………. 4
2.Краткие теоретические сведения по проектированию специальных средств измерений ……………………………………………………………….... 5
2.1.Проектирование калибров расположений ……………………………. 5
2.2.Пневматические средства измерения …………………………………. 6
2.3.Проектирование контрольно-измерительных приспособлений …….. 7
3.Примеры расчета контрольно-измерительных средств ………………. 9
3.1.Проектирование специальных гладких калибров …………………… 9
3.2.Проектирование пневматических пробок …………………………… 9
3.3.Проектирование калибров расположения …………………………… 10
3.4.Проектирование контрольных приспособлений ……………………. 14 Библиографический список ……………………………………………….. 16
3
PDF created with pdfFactory Pro trial version www.pdffactory.com
1. ИСХОДНЫЕ ДАННЫЕ И ЭТАПЫ ПРОЕКТИРОВАНИЯ
Специальные контрольно-измерительные средства относятся к технологи- ческой оснастке. Это калибры, шаблоны, контрольные приспособления, кон- трольно-сортировочные автоматы, системы автоматизированного и активного контроля. Используются специальные СИ в серийном и массовом производстве с целью повышения производительности операций и получения стабильного каче- ства изделий.
Исходными данными для проектирования специальных средств измерений (СИ) служат чертеж изделия (детали) с заданными нормами точности; технологи- ческий процесс (производительность операции обработки и достигаемая точность изготовления); аналогичные конструкции СИ, применяемые для других изделий; унифицированные элементы контрольной оснастки, применяемые на данном предприятии; условия эксплуатации (внешние воздействия, срок эксплуатации, безопасность и т.д.).
Калибрами можно контролировать детали, начиная с 6-го квалитета. Ши- роко калибры применяются в массовом и крупносерийном производствах. Они применяются для того, чтобы определить выходит ли величина контролируемого размера за нижнее или верхнее допустимое значение допуска или находится меж- ду двумя допустимыми пределами отклонений.
По виду контролируемых параметров калибры различают: гладкие; резьбо- вые; шлицевые; для контроля длины, уступов, глубин и высот; для взаимного рас- положения поверхностей и др.
По числу единовременно контролируемых параметров делят на элементные и комплексные.
По условиям оценки годности деталей делят на нормальные и предельные. Предельные калибры определяют размеры деталей по lim и делят их на 3
группы: годные, брак из-за перехода за верхнюю границу износа и брак из-за пе- рехода за нижнюю границу износа. Предельные калибры изготовляют попарно ПР и НЕ.
Проектируются специальные СИ в основном в конструкторском отделе по технологической оснастке при главном технологе, а изготавливаются и инстру- ментальном цехе предприятия (фирмы).
На каждое специальное СИ разрабатывается техническое задание на про- ектирование, содержание и объем которого зависят от сложности СИ.
Техническое задание включает следующие разделы:
−наименование СИ и область применения (рабочие, лабораторные или эта- лоны, стационарные или переносные, подлежат или нет Государственному метро- логическому контролю и надзору (ГМКН), операционный или приемочный кон- троль и так далее);
−основание для разработки и технико-экономическое обоснование (наличие отечественных и зарубежных аналогов, нецелесообразность их использования,
снижение себестоимости операций контроля и повышение качества изделий и так далее);
4
PDF created with pdfFactory Pro trial version www.pdffactory.com

−используемые источники (научно-исследовательские работы, патентные изыскания, образцы, макеты, каталоги и паспорта известных аналогов СИ и так далее);
−технические условия на проектируемое СИ (метрологические и эксплуа- тационные характеристики, показатели качества, условия эксплуатации и так да- лее);
−этапы и сроки проектирования и изготовления (эскизный проект, техни- ческий и рабочий, технологические документы, метрологическая экспертиза, из- готовление опытного и серийного образцов и так далее);
−перечень документов на метрологическое обеспечение СИ (методика вы- полнения измерения, методика испытаний и аттестации с указанием ответствен- ной организации и необходимого оборудования и СИ для испытаний, методика периодической поверки или калибровки и так далее);
−перечень эксплуатационных документов (паспорт, инструкция по экс-
плуатации; для СИ, подлежащих экспорту, документы должны быть пе- реведены на несколько иностранных языков).
Вся техническая документация на специальные СИ подвергается обя- зательно метрологической проработке и метрологической экспертизе.
Этапы проектирования в виде эскизного, технического и рабочего проектов предусматриваются для СИ, используемых в автоматическом режиме контроля, для экспорта, для утверждения типа СИ. В машиностроительном про- изводстве получили широкое распространение простейшие СИ (калибры, шаб- лоны) и контрольные приспособления, для которых может выполняться рабочий проект.
2. КРАТКИЕ ТЕОРЕТИЧЕСКИЕ СВЕДЕНИЯ ПО ПРОЕКТИРОВАНИЮ
СПЕЦИАЛЬНЫХ СРЕДСТВ ИЗМЕРЕНИЙ
2.1. ПРОЕКТИРОВАНИЕ КАЛИБРОВ РАСПОЛОЖЕНИЯ
Калибры расположения проектируются в том случае, если допуск распо- ложения поверхностей детали задан как зависимый м . Зависимыми допусками могут быть следующие допуски расположения: позиционный, соосности, сим- метричности, пересечения осей и перпендикулярности, а также некоторые до- пуски формы – прямолинейность оси цилиндрической поверхности и плоскост- ность плоскости симметрии призматической детали.
Зависимый допуск – переменный допуск, его минимальное значение указы- вается в чертеже и его допускается превышать за счёт изменения размеров рас- сматриваемых элементов, но так, чтобы их линейные размеры не выходили за пределы предписанных допусков.
Зависимые допуски расположения назначают в тех случаях, когда необхо- димо обеспечить собираемость деталей, сопрягающихся одновременно по не- скольким поверхностям.
Калибры расположения являются нормальными (проходными), изделие счи- тается годным, если калибр соединяется по всем контролируемым по- верхностям. Контроль допусков расположения производится после того, как уста-
5
PDF created with pdfFactory Pro trial version www.pdffactory.com
новлена годность действительных размеров (диаметры отверстий, валов, ширина паза и так далее) контролируемой детали. Калибр расположения представляет собой контрдеталь, собираемую с контролируемой.
Расчет исполнительных размеров калибров расположения производится по ГОСТ 16085-80, в котором дана методика проектирования и примеры ее исполь- зования.
Применение таблиц стандарта предусмотрено только для позиционных до- пусков. Если допуски расположения поверхностей изделия заданы другими ви- дами допусков или координатным способом, то необходимо выполнить перевод заданного допуска в позиционный.
Допуски на изготовление (Н; Н0), износ (W; W0) и расположение (Тpk) уста- навливаются для каждого измерительного элемента калибра в зависимости от по- зиционного допуска у детали. С индексом ноль обозначены допуски базового элемента. У калибра допуск расположения задается как независимый, контроль его выполняется универсальными СИ.
Допуски на изготовление и износ элементов калибра смещаются в сторону поля допуска расположения детали на величину F – это основное отклонение, со- ответствующее проходному пределу размера нового калибра (максимум мате- риала). Допуски на изготовление калибра задаются односторонние "в тело" ка- либра (для наружных поверхностей "в минус", а для внутренних "в плюс"). Ка- либры расположения изготавливаются как цельные, так и сборные.
Для резьбовых измерительных элементов калибров отклонения и допуски относятся к среднему диаметру резьбы. Допуски на остальные размеры резьбовых
элементов калибров расположения определяются для поэлементных проходных резьбовых калибров по ГОСТ 24997-81.
Рабочие поверхности калибра расположения должны быть выполнены из инструментальной стали, закалены до HRC 58...62 и обработаны до шероховато- сти Ra = 0,4. Допуск формы цилиндрической поверхности 20…30% от допуска на изготовление элемента калибра (H или Н0): Tф = 0,2 ... 0,3 Н (Н0). Допуски на рас- положение измерительных элементов калибров могут быть указаны в виде пози- ционных допусков или координатным способом. Если в детали использованы другие виды допусков расположения (соосность, пересечение осей), то для калиб- ра должен назначаться такой же вид допуска.
2.2. ПНЕВМАТИЧЕСКИЕ СРЕДСТВА ИЗМЕРЕНИЯ
Пневматические средства измерения имеют высокую точность, позволяют выполнять дистанционные измерения в труднодоступных и опасных местах.
Достоинством пневматического метода контроля является простота конст- рукции прибора и измерительной оснастки, работа бесконтактным методом, воз- можность автоматизации процесса и создания многомерных устройств.
В пневматических приборах происходит преобразование изменения размера (зазора между деталью и соплом) в изменение давления или скорости потока воз- духа. Расход сжатого воздуха G зависит от давления Р и площади F проходного сечения клапана (сопла), а F определяется величиной зазора S.
6
PDF created with pdfFactory Pro trial version www.pdffactory.com
Для работы пневматических приборов необходима воздушная сеть с опре- деленным давлением воздуха. Принято подразделять давление на сетевое Р1 = 0,32...0,6 МПа, рабочее Р2, подводимое к прибору через узел подготовки воздуха, измерительное Р – это переменное давление, зависящее от расхода воздуха: Р = (0,6 ...0,9) Р2.
Воздух для пневматических приборов должен соответствовать требованиям ГОСТ 17433-80, он не должен содержать капель влаги, масла и твердых частиц размером более 0,5 мкм.
В зависимости от величины рабочего давления различают приборы низкого давления Р2 ≤ 0,1 МПа и приборы высокого давления Р2 > 0,1 МПа.
Расход воздуха измеряют с помощью манометров или ротаметров. Мано- метры реагируют на изменение давления. Ротаметры реагируют на изменение скорости воздушного потока. В качестве чувствительного элемента используются жидкость (приборы типа Солекс), трубка Бурдона, мембрана, сильфон, конусная трубка с поплавком. Величина конусности стеклянной трубки 7 зависит от типа поплавка (легкий или тяжелый). Конусность трубки обычно 1:400 или 1:1000, вес поплавка может быть 0,25; 0,5 или 0,8 г.
Высота подъема поплавка определяется размером измеряемого зазора. Чем больше зазор, тем больше скорость протекания воздуха, тем выше поднимается поплавок. Можно производить градуировку шкалы в долях измеряемой величины, а можно устанавливать ограничительные флажки в положениях поплавка, соот- ветствующих предельным размерам.
Повышение чувствительности прибора может быть достигнуто за счет уве- личения диаметра измерительного сопла или рабочего давления, а также за счет уменьшения веса поплавка и конусности трубки.
2.3. ПРОЕКТИРОВАНИЕ КОНТРОЛЬНО-ИЗМЕРИТЕЛЬНЫХ
ПРИСПОСОБЛЕНИЙ
Контрольные приспособления предназначены для контроля деталей формы, измерение которых невозможно универсальными средствами. Обычно
они используются в серийном и массовом производстве для контроля допусков формы и взаимного расположения поверхностей.
Требования к контрольным приспособлениям: обеспечение оптимальной производительности операций контроля. Приспособления должны быть удобны в эксплуатации, технологичны в изготовлении, износоустойчивы и экономически целесообразны. Экономическая целесообразность внедрения специального кон- трольного приспособления оценивается повышением качества изделий и умень- шением брака, повышением производительности контрольных операций, сниже- нием требований и квалификации контролеров.
Так же, как и станочные приспособления, контрольные могут собираться из унифицированных элементов и узлов.
Основные элементы контрольных приспособлений:
−базирующие элементы для установки детали (это призмы, оправки, центры
ит.д.);
7
PDF created with pdfFactory Pro trial version www.pdffactory.com
−зажимные устройства для закрепления выбранного положения детали (струбцины, эксцентриковые, винтовые или байонетные зажимы и т.п.);
−измерительные элементы (индикаторы, датчики, световые табло и т.п.);
−вспомогательные устройства для крепления измерительных элементов;
−подвижные элементы для перемещения и поворота детали или измери- тельного элемента в процессе контроля (часто поворот детали производят вруч- ную);
−корпус приспособления.
Конструкция и габариты приспособления определяются формой и раз- мерами контролируемой детали.
Приспособления бывают стационарные и переносные (для крупногабарит- ных деталей).
По числу контролируемых параметров приспособления могут быть одно- мерные и многомерные, а по количеству одновременно контролируемых деталей
– одноместные и многоместные.
Технические требования на контрольные приспособления должны со- держать следующие требования:
1)контролируемый параметр и величину допускаемого отклонения для него;
2)метрологические характеристики измерительного прибора (условное обо- значение по ГОСТ, цена деления, диапазон измерения и др.);
3)методы измерения и настройки, допускаемую погрешность настройки (для концевых мер длины (КМД) класс точности и состав блока, для установочной де- тали требования к точности ее размеров);
4)допуски на взаимное расположение базовых и измерительных элементов (параллельность, перпендикулярность, соосность, симметричность и др);
5)для быстро изнашиваемых элементов (наконечников, направляющих, оп- равок) предусмотреть термообработку и задать твердость – HRC, указать допус- тимую величину износа;
6)указать тип смазки и ее периодичность для трущихся подвижных эле- ментов;
7)проверить плавность и легкость взаимодействия подвижных элементов (толчки и заедания недопустимы);
8)требования к внешнему виду (покрытие, масса, габаритные размеры);
9)спецификации на оригинальные, стандартные и покупные детали;
10)сроки поверок или калибровок;
11)если используется пневмо- или гидрозажим, то необходимо указать: вид рабочей среды, рабочее давление, длину рабочего хода, диаметр цилиндра, усиле- ние зажима, испытать на герметичность при давлении в 1,5...2 раза выше рабочего (утечки недопустимы);
12)вращающиеся от электродвигателя детали приспособления должны быть защищены кожухами;
13)предусмотреть рым-болты для подъема и транспортирования приспо- собления;
14)магнитные приспособления должны быть полностью водонепроницаемы;
15)электропроводка должна быть безопасной и иметь заземление.
8
PDF created with pdfFactory Pro trial version www.pdffactory.com
Конструкции приспособлений должны быть прочными и жесткими при ми- нимальной массе и габаритах, должны удовлетворять требованиям эргономики и эстетичности, быть просты и удобны в эксплуатации, а также технологичны в из- готовлении и ремонте, обеспечивать требуемую точность измерения.
3.ПРИМЕРЫ РАСЧЕТА КОНТРОЛЬНО-ИЗМЕРИТЕЛЬНЫХ СРЕДСТВ
3.1.ПРОЕКТИРОВАНИЕ СПЕЦИАЛЬНЫХ ГЛАДКИХ КАЛИБРОВ
При проектировании специальных гладких калибров для контроля отвер- стий и валов используют ГОСТ 24853-81, где приведены формулы для определе- ния предельных размеров калибров-пробок, калибров-скоб и контрольных ка- либров: калибры-пробки Р-ПР и Р-НЕ – для контроля отверстий; калибры-скобы Р-ПР и Р-НЕ – для контроля валов.
Калибры-пробки легко проконтролировать универсальными измеритель- ными средствами. Для контроля калибров-скоб стандартом предусмотрены кон- трольные калибры:
К-ПР – для контроля Р-ПР; К-НЕ – для контроля Р-НЕ;
К-И – для контроля Р-ПРизн.
При вычерчивании калибров необходимо на чертежах проставить не пре- дельные размеры, а исполнительные, которые определяются по следующим пра- вилам:
− за исполнительный размер калибра-пробки проходной и непроходной сто- роны принимают наибольший размер калибра с минусовым допуском на изго- товление: (Р-ПРmax)-H, (Р-НЕmax)-H (Н – допуск на изготовление калибров-пробок);
− за исполнительный размер калибра-скобы проходной и непроходной сто- роны принимают наименьший размер калибра с плюсовым допуском на изготов- ление: (Р-ПРmin)+H1; (Р-НЕmin)+H1 (Н1 – допуск на изготовление калибров-скоб);
− за исполнительный размер контрольного калибра принимают наименьший размер контрольного калибра (проходного, непроходного и изношенного) с ми-
нусовым допуском на изготовление: (К-ПРmax)-Hp; (К-НЕmax)-Hp; (К-Иmax)-Hp (Нp – допуск на изготовление контрольного калибра).
3.2. ПРОЕКТИРОВАНИЕ ПНЕВМАТИЧЕСКИХ ПРОБОК
Для проектирования пневмопробок используют ГОСТ 14864-78.
Для контроля сквозных отверстий (тип С) применяют пневмопробки, ука- занные в чертеже 1 ГОСТ 14864-78, а для контроля (тип Г) глухих отверстий – пневмопробки чертежа 2.
Основные размеры ручек пробок должны соответствовать приведенным на чертеже 11 и в таблице 9 по ГОСТ 14864-78.
При проектировании пневмопробок выбираем тип ее: манометрического типа высокого давления, пневматические длинномеры низкого давления.
Для контроля сквозного отверстия 18 Н9 спроектировать пневмопробку манометрического типа высокого давления.
9
PDF created with pdfFactory Pro trial version www.pdffactory.com