
Лекция 4
.pdfЛекция № 4
Тема: Характеристика металлорежущих систем и
процессов в станках
Цель: Дать представления о составе, структуре и
взаимодействии основных компонентов металлорежущих систем.
План: 4.1. Определение металлорежущих систем
4.2.Станок как элемент технологической системы
4.3.Процессы в станках
4.4.Основные критерии работоспособности станка Контрольные вопросы и задания
4.1. Определение металлорежущих систем
Металлорежущие системы – станочные системы, т.е. управляемая совокупность металлорежущего и вспомогательного оборудования, предназначенная для обработки изделий.
Оборудование вспомогательное - совокупность транспортно-
накопительных и загрузочно-разгрузочных устройств, предназначенных для хранения и перемещения предметов и орудий труда, а также отходов производства (заготовки, полуфабрикаты, детали, инструменты, оснастка, стружка).
Подсистема управления - автоматическая или автоматизированная совокупность технологической системы и программно-математическое обеспечение.
Технологическая система - совокупность функционально взаимосвязанных средств технологического оснащения, предметов производства и исполнителей для выполнения в регламентированных условиях производства заданных технологического процесса либо операций.
В начало лекции
4.2. Станок как элемент технологической системы
Металлорежущие станки различаются по функциям, конструкции, уровню автоматизации, техническим параметрам, габаритам, весу и другим характеристикам, оказывающим существенное влияние па их надежность и способы ее обеспечения.
Металлорежущий станок состоит из большого количества разнородных элементов, в которых происходят сложные физико-химические процессы. На этапе изучения, расчета и обеспечения надежности станок целесообразно рассматривать как совокупность взаимосвязанных систем, различающихся видом элементов, характером нагрузок, физикой отказов, уровнем и способами обеспечения их надежности. Такими системами являются механическая, гидравлическая, пневматическая, электрическая, электронная, инструментальная.Внекоторыхслучаяхудобноделениестанканасистемыпо функциональному признаку, т. е. на двигательную, передаточную, транспортную, инструментальную, измерительную, информационную, технического диагностирования, подачи СОЖ и др.
Системы первого и второго видов принадлежат к восстанавливаемым и состоят из восстанавливаемых и невосстанавливаемых элементов. Характер производства элементов разнообразен: от массового (подшипники качения, гидравлические аппараты, режущие инструменты и др.) до единичного (шпиндели, базовые детали и др.). Сами станки и автоматические линии во многих случаях являются уникальными изделиями, что не дает возможности выделять для их испытаний представительную выборку.
Существенные различия между станками, их системами и элементами требуют использования в каждом случае наиболее подходящих методов испытаний, расчета и обеспечения надежности.
В начало лекции
4.3. Процессы в станках
Процессы в станках бывают: обратимые и необратимые.
Обратимые процессы в станке с изменением параметров станка и его компонентов в определенных пределах без тенденций прогрессивного ухудшения - пример: деформация узлов под действием давления и температуры.
Необратимые процессы - изнашивание, коррозия - постепенное ухудшение с течением времени технических характеристик станка.
Скорость протекания процессов - влияет на изменение показателей качества станка.
Быстропротекающие процессы - имеют периодичность, измеряемую долями секунд; заканчиваются в пределах цикла обработки одной детали и вновь возникают при обработке следующей заготовки - вибрация узлов, изменение силы в подвижных соединениях и др.
Быстропротекающие процессы продолжаются в течение цикла работы станка и заканчиваются с его прекращением. К ним относятся колебания нагрузок, упругие деформации, вибрации узлов, изменения сил трения и др. Быстропротекающие процессы приводят к изменениям шероховатости поверхностей и рассеиванию размеров обработанных на станке деталей.
Металлорежущий станок является упругой системой. При нагружении силами его механические элементы деформируются; а при снятии нагрузок их форма и размеры полностью восстанавливаются. Способность элементов сопротивляться появлению упругих деформаций (отжатий) под действием нагрузки называется жесткостью. Жесткость узла зависит от деформации всех его деталей, а деталь может получить одновременно несколько деформаций разного характера: тела (шпинделя, станины и др.) и поверхностей. Жесткость - важнейшая составляющая качества станков. Она в значительной мере определяет точность и производительность процессов обработки.
Переменность сил резания, в основном являющаяся результатом колебаний припуска и физико-механических свойств обрабатываемого материала, приводит к рассеиванию точности обработки.
В станке могут возникать колебания (вибрации). Вибрации ухудшают шероховатость поверхностей обрабатываемых деталей, вызывают рассеивание размеров и поломки режущих инструментов, снижают долговечность станка. Под действием внешней периодической силы, которая обусловлена прерывистостью процесса резания и дисбалансом вращающихся частей, возникают вынужденные колебания.
Процессысреднейскорости - протекают за времянепрерывной работы станка(час,мин.)- приводяткизменениюначальныхпараметров- (обратимые процессы - изменение температурных полей станка и температуры окружающей среды; необратимые - изнашивание режущего инструмента).
Процессы средней скорости продолжаются в течение периода бесподналадочной работы, т. е. в течение нескольких минут или часов. К ним относятся изменения температуры станка, износ режущего инструмента.
Станокнагреваетсязасчеттеплообразованияприработеегомеханизмов и в зоне резания, а также от внешних источников. На отвод тепла влияют суточные и годовые колебания температуры в цехе. В результате изменения температуры детали станка — станина, корпус, столы, ходовые винты, планшайбы, шпиндели — деформируются. При этом изменяются линейные размеры, геометрическая форма и положение деталей.
Нагрев станка до температуры, при которой тепловые деформации его деталей становятся заметными и начинают влиять на его работоспособность, длится 1-8 ч после включения станка. В большинстве случаев температурные деформации узлов и деталей станков приводят к дополнительным погрешностям обработки. Это происходит, например, в том случае, когда деталь обрабатывается на автоматизированном станке и ее размеры определяются упорами, кулачками или копирами, которые настраиваются в начале смены на холодном станке. На рис. 4.1 показана температурная деформация стойки плоскошлифовальиого станка, вызванная неравномерным нагревом ее потоком тепла из шпиндельной бабки. В результате этой
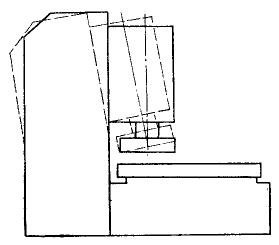
деформации возникает не параллельность торцов изделия, достигающая 0,010— 0,012 мм на 100 мм его длины.
Рисунок 4.1 – Температурная деформация стойки плоскошлифовального станка
Нагрев станка сопровождается также следующими нежелательными явлениями: уменьшением вязкости масла в гидроприводе и соответствующим увеличением утечек, изменением длительности цикла, а иногда и полным его нарушением. Изменения температуры приводят и к изменениям вязкости смазочных масел, а, следовательно, условий смазки и трения. Температурные деформации деталей станка и изменения вязкости масла относятся к обратимым процессам.
Процессы, характеризующиеся средними скоростями, вследствие переменности условий, при которых они развиваются, являются случайными.
Медленнопротекающиепроцессыразвиваютсясначалаэксплуатации станка, но их результаты становятся ощутимыми за периоды работы между ремонтами станка. К ним относятся изнашивание основных деталей, перераспределение внутренних напряжений и вызываемое этим коробление ответственных деталей, коррозия, старение пластмасс, резины, рабочей жидкости, смазочных масел, электронной аппаратуры и др.
Медленно протекающие процессы приводят к прогрессивному ухудшению технических характеристик станков, называемому физическим
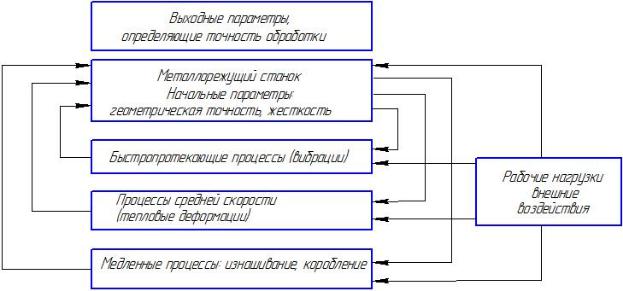
старением. Скорость старения определяется как первоначальным качеством станка, так и качеством обслуживания.
На работоспособность станка наиболее сильно влияет изнашивание его деталей. Изнашивание - это процесс постепенного изменения размеров тела при трении, проявляющийся в отделении с поверхности трения материала и (или) его остаточной деформации. Результатом изнашивания является износ.
Преимущественное влияние износа на ухудшение эксплуатационных свойств станков можно объяснить большим количеством трущихся поверхностей, многие из которых трудно или невозможно защитить от пыли, стружки, смазочно-охлаждающей -жидкости. Он приводит к потери точности элементов, участвующих в образовании формы обрабатываемой детали, понижениюпрочностидеталейвследствиеуменьшенияихсечений,снижению коэффициента полезного действия гидроагрегатов и увеличеню утечек в гидроаппаратах.
Рисунок 4.2 - Влияние процессов на начальные параметры
Взаимодействие процессов сложно и имеет обратные связи, когда изменение начальных параметров станка влияют на характеристики протекающих процессов.
Например, тепловая деформация отдельных звеньев станка может исказить взаимное положение его узлов и повлиять на точность обработки, но
и привести к повышенным нагрузкам и, как следствие, к более интенсивному тепловыделению в станках.
Для обеспечения работоспособности:
1)иметь заданные начальные характеристики;
2)создать такую конструкцию, которая имела бы высокую сопротивляемость по отношению к воздействию различных процессов, изменяющих его выходные параметры.
В начало лекции
4.4. Основные критерии работоспособности станка
К основным критериям работоспособности станка относятся:
1.Геометрическая и кинематическая точность.
2.Статическая жесткость.
3.Виброустойчивость.
4.Теплостойкость (сопротивление температурных деформаций).
5.Износостойкость.
6.Коррозионная стойкость.
7.Сопротивление усталости.
8.Сопротивление короблению.
Первые пять критериев – это основные. Остальные распределяются следующим образом: 1, 2 - связаны с начальными параметрами станка.
3- быстропротекаемые процессы.
4- средняя скорость.
5- медленные процессы.
6, 7, 8 - тоже относятся к медленно протекающим, но они характерны для специальных деталей и условий работы станка.
Коррозионнаястойкость относится к внешним воздействиям и связана с недопустимыми методами эксплуатации, транспортирования и хранения станка. Коррозия появляется под действием СОЖ при плохом её составе.
Сопротивление усталости характерно для работы кинематических пар (подшипники и направляющие качения, зубчатые передачи).
Коробление характерно для станин и круглых корпусных деталей. Выводы: Современные станочные системы рассматриваются как
комплекс программно-управляемого металлорежущего и вспомогательного оборудования. Использование модульного принципа делает это оборудование быстропереналаживаемым, легко адаптируемым к новой номенклатуре обрабатываемых изделий. Основной же целевой функцией конструктора является создание минимальной области состояния и уменьшение скорости ее роста.
В начало лекции
Контрольные вопросы и задания
1.Понятие металлорежущие системы.
2.Назовите основные процессы, присутствующие в станках.
3.Что входит в понятие «Быстропротекающий процесс».
4.Критерии работоспособности станка.
Литература 1. Кочергин А.И. основы надежности металлорежущих
станков:/Учеб.пособиедлявузовпоспец.0501«Технологиямашиностроения, металлорежущие станки и инструменты» -2-е изд., перераб. и доп.-Минск.
Выш. школа, 1982. -175 с., ил.
В начало лекции