
РМАТП_Лабор_работы
.pdf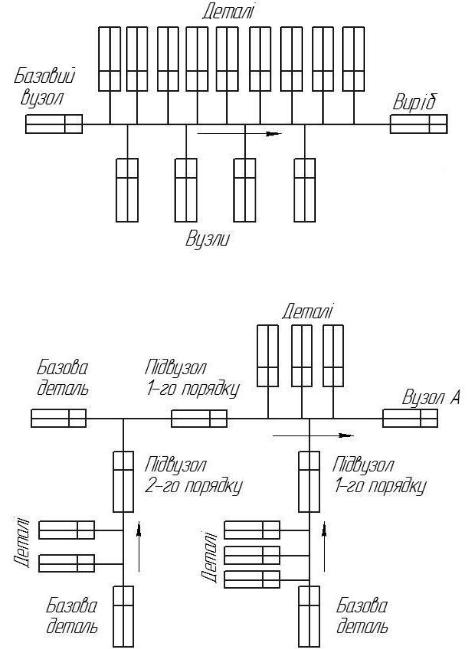
схема вузлового складання виробу, загальне складання якого показане на рисунку 3. Вузлове складання дозволяє здійснювати паралельне складання вузлів виробу, значно скорочує тривалість циклу складання машин.
Рисунок 3 – Технологічна схема загального складання виробу.
Рисунок 4 – Технологічна схема вузлового складання виробу
Технологічні схеми складання відображають структуру і послідовність (маршрут) складання виробу і його вузлів: при їх складанні встановлюють також необхідні контрольні та допоміжні операції. Ці схеми дають уявлення про технологічність конструкції виробу щодо його складання. Конструкція виробу зумовлює методи складання. При проектуванні технологічного процесу складання визначають темп (ритм, такт) загального та вузлового складання, поділяючи річний фонд робочого часу на хвилини на річну програму випуску виробів (вузлів) в штуках. Якщо темп значно пе-
10
ревершує середню тривалість характерних складальних операцій, то складання ведуть за принципами серійного виробництва. У цьому випадку на одному робочому місці періодично (партіями, серіями) збираються різні вироби або вузли.
Якщо темп близький до середньої тривалості характерних складальних операцій або менше її, то складання ведуть за принципами масового виробництва, закріплюючи за кожним робочим місцем певну складальну операцію. При малому темпі складання диференціюють, розділяючи операції. Якщо це з технологічних міркувань важко або неможливо, то операції виконують паралельно, дублюючи робочі місця. Зміст операцій складання повинний бути таким, щоб на кожному робочому місці виконувалася по можливості однорідна і технологічно закінчена робота. Це сприяє кращій спеціалізації складальників і підвищенню продуктивності їх праці.
Технологічні процеси складання можуть бути типові, групові та індивідуальні. Типові процеси створюються для різних груп з’єднань і вузлів на базі узагальнення досвіду прогресивних методів складання в масштабі галузі машинобудування. Особливістю групових процесів є їх придатність для складання кількох виробів (вузлів), які характеризуються однорідністю конструктивно-технологічних ознак. Індивідуальні процеси розробляються для складання одного конкретного виробу.
При побудові маршруту і операцій складання виявляються її організаційні форми. Складання може бути потоковим і непотоковим. Переміщення зібраного об’єкта від одного робочого місця до іншого при потоковому складанні здійснюється вручну (на верстатах, рольгангах, на візках), вантажопідйомними машинами (кранами, тельферами тощо), конвеєром, що періодично рухається, – пластинчастим конвеєром, візками, відомими по рейковому шляху замкнутим ланцюгом , а також конвеєром, що безперервно рухається.
Потокове складання при нерухомому об'єкті здійснюється на розташованих в лінію нерухомих стендах. Кожен складальник (бригада складальників) виконує свою операцію, переходячи послідовно від одного стенду до іншого. Таке складання доцільно застосовувати в серійному виробництві при значному темпі, особливо для складання важких машин, переміщення яких важко забезпечити. При потоковому складанні повинно бути забезпечено безперебійне, ув'язане з темпом складання постачання складальної лінії взаємозамінними деталями і вузлами: слюсарно-припасовувальні роботи можуть бути допущені лише в тому випадку, якщо вони пов'язані з темпом складання. Якщо потрібна висока точність, то деталі, що сполучаються підбирають одну до одної (селективне складання) або проводиться їх індивідуальне припасування. В цьому випадку деталі, що сполучаються надходять на складання спареними. Потокове складання скорочує цикл виробництва і міжопераційні заділи деталей, підвищує спеціалізацію складальників, збільшує можливості механізації і автоматизації виробництва і зменшує трудомісткість виробів.
11
Механізація складання направлена на часткову або повну заміну ручної праці оператора машинним шляхом оснащення робочих місць електричним, пневматичним або гідравлічним інструментом і пристроями. Автоматизація має на меті передачу складальним машинам і їх комплексам функції керування процесами складання. Механізація і автоматизація процесів може бути одиничною і комплексною.
Непотокове складання застосовується в одиничному і дрібносерійному виробництві.
При проектуванні технологічного процесу складання встановлюють об'єкти, методи і засоби технічного контролю для визначення відповідності точності форми і розмірів, відносного положення та руху елементів виробу заданим технічним умовам. Перевірці підлягають: взаємне положення елементів виробу, якість виконаних з'єднань (сила і момент затяжки різьбових з'єднань, якість припасування поверхонь, що стикуються тощо), правильність постановки та наявність деталей в з'єднаннях, маса вузлів і виробу в цілому, врівноваженість обертових частин виробу і т. п.
Основні напрями підвищення продуктивності складання – механізація і автоматизація, усунення припасовувальних робіт, зменшення кількості найменувань деталей і вузлів машини, нормалізація та уніфікація кріпильних і деяких деталей виробу, зменшення кількості багатоланкових розмірних ланцюгів.
Зміст роботи
При виконанні лабораторної роботи необхідно ознайомитись з конструкцією вузла-представника, виконати креслення цього вузла та виконати всі потрібні види, щоб конструкція виробу була зрозуміла, зробити специфікацію усіх деталей які входять у цей вузол, скласти схему складання та маршрут складання.
Порядок виконання роботи
1Ознайомитися з правилами складання механізмів у машинобудуванні (виконується при підготовці до лабораторної роботи за даними з літературних джерел).
2Робоче місце – стенд з вузлом представником.
Спочатку потрібно ознайомитися конструктивними елементами редуктора, визначити тип редуктора, призначення, описати принцип роботи вузла. Розібрати редуктор на складальні одиниці чи вузли.
3 Зробити креслення вузла з усіма потрібними видами та перетинами, щоб конструкція вузла була зрозуміла (приклад представлений в додатку Б).
4 Скласти специфікацію складальних одиниць редуктора.
12
5 Ознайомившись з конструкцією та принципом роботи скласти схему складання згідно з правилами оформлення схем складання (виконується при підготовці до лабораторної за даними з літературних джерел).
6 Зробити маршрут складання.
Обробка й аналіз результатів роботи
1 Виконуючи складання редуктора проаналізувати тип складання.
2 Зняти усі потрібні розміри для креслення.
3 Обґрунтувати вузол редуктора у якому є розмірний ланцюг, що є замикаючою ланкою та як досягається точність складання .
Зміст звіту
1Назва, мета і опис вузла представника.
2Креслення вузла представника.
3Специфікація.
4Схема складання.
5Маршрут складання.
6Висновки
Контрольні запитання
1 Що називається складанням?
2 У чому полягає різниця організації складальних операцій у одиничному та масовому виробництві?
3 За якими принципами будується схема складання.
4 Перерахувати методи досягнення точності при складанні?
5 У чому полягає метод неповної взаємозамінності?
Лабораторна робота № 3
Дослідження методів досягнення точності при складанні вузлів, виявлення та розв’язання конструкторських розмірних ланцюгів
Мета роботи – ознайомитися з основними методами досягнення точності при складанні вузлів деталей машин, навчитися виявляти та вирішувати конструкторські розмірні ланцюги.
Загальні відомості
Необхідна точність складання виробів досягається одним з п'яти методів: повної взаємозамінності, неповної взаємозамінності, групової взаємозамінності, регулюванням, припасування.
13
Метод повної взаємозамінності – при цьому методі необхідна точ-
ність складання досягається шляхом з'єднання деталей без їх вибору, підбору або зміни розмірів. Застосування методу повної взаємозамінності доцільно при складанні з'єднань, що складаються з невеликої кількості деталей, тому що збільшення числа деталей вимагає обробки сполучених поверхонь з меншими допусками, що не завжди технічно досяжно та економічно доцільно.
Метод неповної взаємозамінності – метод, при якому необхідна то-
чність складання досягається не у всіх з'єднань при сполученні деталей без їх вибору, підбору або модифікації розмірів, а у заздалегідь певної їх частини, тобто обумовлений відсоток (або частки відсотка) з'єднань не відповідає вимогам точності складання і вимагає розбирання і повторного складання. Якщо додаткові витрати на виконання розбірно-складальних робіт менше витрат на виготовлення деталей, що сполучаються з більш вузькими допусками, які забезпечують отримання необхідної точності складання у всіх з'єднань, то метод неповної взаємозамінності доцільний в цьому даному конкретному випадку.
Метод групової взаємозамінності – метод, при якому необхідна то-
чність складання досягається шляхом з'єднання деталей, що відносяться до однієї з розмірних груп, на які вони вже розсортовані. Цей метод іноді називають селективним. В межах кожної групи необхідна точність складання досягається методом повної взаємозамінності. Даний метод надає високу точність складання, однак він пов'язаний з додатковою операцією сортування деталей на розмірні групи, потребою зберігання запасів деталей всіх розмірних груп і неможливістю використання частини деталей, коли деталі, що сполучаються нерівномірно розподіляються по розмірним групам.
Метод регулювання – при цьому методі необхідна точність складання виходить шляхом модифікації розміру однієї з деталей (або групи деталей) сполуки, що називається компенсатором, без зняття шару матеріалу.
Метод припасування – метод, при якому необхідна точність складання досягається шляхом зміни розміру компенсатора зі зняттям шару матеріалу.
Метод розмірних ланцюгів виявляється дуже зручним для вирішення багатьох конструкторських і технологічних задач, пов'язаних з питаннями точності.
Конструкторський розмірний ланцюг визначає відстані між окре-
мими поверхнями та осями поверхонь виробів або їх поворот. Такі ланцюга також називають складальними.
Найбільш важливим є визначення замикаючих ланок розмірного ланцюга, оскільки вони остаточно формуються і замикають розмірний ланцюг. Замикаюча ланка може являти собою технологічний допуск, який порівнюють з конструкторським допуском. В результаті такого порівняння можна з усією визначеністю сказати про якість виготовленої деталі або зібраної машини. Технологічний допуск повинен бути менше або, в край-
14

ньому випадку, дорівнює конструкторському допуску. Якщо ця умова не дотримується, необхідно змінити (або продовжити) технологічний процес виготовлення деталей.
У розрахунках за допомогою розмірних ланцюгів необхідно прийняти деякі правила. Складова ланка розмірного ланцюга, з подовженням яко-
го замикає ланку збільшується, називають збільшуючою і познача-
ють Ai . Складова ланка розмірної ланцюга, зі збільшенням якого зами-
кає ланку зменшується, називають зменшуючою і позначають Аi . Для ви-
готовленої деталі або машини, що складається складають відповідні схеми із зображенням відрізків у вигляді збільшують і зменшують ланок. Зазвичай розмірну ланцюг будують від однієї з поверхонь (осі), що обмежують замикає ланку. У ланцюг повинні входити тільки ті складові ланки, які беруть участь у вирішенні поставленого завдання, тобто в проведенні розрахунку. Складові ланки повинні доходити до другої поверхні (осі), що обмежує замикає ланку. Ланцюг неодмінно треба замкнути.
За допомогою розмірних ланцюгів вирішують, як правило, два завдання. По-перше, за заданими параметрами замикаючого ланки визначають параметри складових ланок. Це означає, що за граничним відхиленням і допуском замикаючого ланки розраховують допуски і граничні відхилення розмірів складових ланок. По-друге, за відомими параметрами складових ланок знаходять параметри останнього у ланки. Це означає, що за відомими номінальним розмірами, їх граничним відхиленням розраховують номінальний розмір замикаючого ланки, а також його допуск.
Відхилення розмірів ланок розраховують також двома методами. Перший називають "максимум - мінімум". В цьому випадку в розрахунках враховують максимальні або мінімальні значення відхилень, які завжди вказують на робочих кресленнях або в технічних умовах. Такий метод істотно спрощує розрахунок, але його точність у цьому випадку може виявитися порівняно низькою, так як враховується граничне, а не фактичне відхилення від номінального значення. Другий метод називають імовірнісним. Він враховує не граничні, а найбільш ймовірні відхилення на основі законів розсіювання розмірів. Цей метод виявляється більш трудомістким, але більш точним.
Рішення прямої задачі методом неповної взаємозамінності виконується наступним шляхом.
Допуски складових ланок визначаються з основного рівняння точності розмірного ланцюга (5) є:
|
n |
|
|
m n 1 |
|
|
|
|
2 |
2 |
2 |
2 |
2 |
2 |
|
TA t |
TAci |
ci |
ci |
TAi |
i |
i . |
(5) |
|
i 1 |
|
|
i 1 |
|
|
|
15
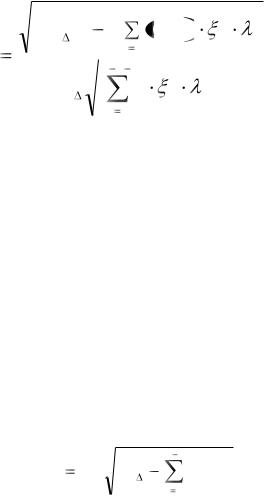
де ТАсі – попередньо заданий допуск стандартної складаючої ланки розмірного ланцюга;
n – число складових ланок розмірного ланцюга;
λі. – відносне середнє квадратичне відхилення і-ї складальної ланки розмірного ланцюга;
ξсі та λсі – передаточне відношення та відносне середнє квадратичне відхилення складової ланки розмірного ланцюга з попередньо заданими допусками;
t – коефіцієнт ризику для замикаючої ланки.
Якщо номінальні розміри складових ланок розмірного ланцюга мають суттєві розбіги, то, використовується метод рівних квалітетів, з формули (6) визначають середній квалітет складових ланок для цього враховують коефіцієнт а:
|
|
|
n |
|
2 |
|
|
|
|
|
(ТА )2 |
t2 |
ТА |
2 |
2 |
|
|
||
|
|
і |
1 |
сі |
|
сі |
сі |
|
|
а |
|
|
|
|
|
|
|
||
|
|
|
|
|
|
. |
(6) |
||
m n 1 |
|
|
|
||||||
|
|
|
|
|
|||||
|
t |
|
і2 |
2 |
2 |
|
|
|
|
|
|
|
і |
сі |
сі |
|
|
|
|
|
|
і 1 |
|
|
|
|
|
|
|
де ТА – допуск замикаючої ланки розмірного ланцюга, ТАсі – допуски на ланки стандартних виробів, і – одиниця допуску.
Дані для вирішення взяти з таблиці В2.
За кількістю одиниць допуску а знаходять квалітет. Якщо отримане з розрахунку число а точно збігається з табличним і відповідає 11–12-му квалітету, то на всі ланки ланцюга призначаються допуски з цього квалітету.
Однак найчастіше отримане з розрахунку число а не збігається точно з табличним. В цьому випадку беруть найближчим до нього з таблиці В1. Якщо число а приблизно відповідає 11–12-му квалітету і вище, то з цього квалітету призначаються допуски на всі складові ланки ланцюга, крім одного, яке називають регулюючим ланкою. Допуск регулюючої ланки
|
1 |
|
m 2 |
|
|
TAp |
TA2 |
ki2TAi2 . |
(7) |
||
|
|||||
k p |
|||||
|
|
i 1 |
|
Граничні відхилення для всіх ланок, крім регулюючого, зазвичай призначають як для основних валів і отворів, що аналогічно посадкам h і Н, або симетричні в плюс-мінус в залежності від типу поверхонь, до яких відносяться згадані ланки-розміри.
Для визначення граничних відхилень регулюючого ланки необхідно попередньо обчислити координату середини поля допуску цієї ланки. Як-
16
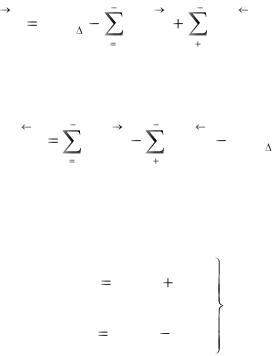
що регулююча ланка є збільшувальною, то координату середини поля допуску цієї ланки визначаємо за формулою
n 1 |
|
m 1 |
|
EC A p ECA |
EC Ai |
EC Ai . |
(8) |
i 1 |
|
n 1 |
|
Якщо регулююча ланка є зменшувальною, то
n 1 |
|
m 2 |
|
EC A p |
EC Ai |
EC Ai ECA . |
(9) |
i 1 |
|
n 1 |
|
Як регулююча ланка може бути прийнята будь-яка складова ланка. Граничні відхилення регулюючої ланки:
ESA |
ECA |
|
TAр |
, |
|
|
|
|
|
|
|||
p |
p |
2 |
|
|
|
|
|
|
|
|
|
||
|
|
. |
(10) |
|||
EIA |
ECA |
TAp |
. |
|
||
|
|
|||||
p |
p |
2 |
|
|
|
|
|
|
|
|
|
Якщо число а вказує на 7–9-й квалітет, то слід використовувати метод припасування або метод регулювання.
Порядок виконання роботи
1 Із складального креслення, яке було зроблено у попередній роботі потрібно виділити вузол та виявити конструкційний розмірний ланцюг.
Потрібно визначити замикаючу ланку, складові ланки та розставити усі потрібні розміри та допуски на складові ланки.
2 Визначивши метод досягнення точності який характерне складанню у серійному виробництві розрахувати розмірний ланцюг.
3 На підставі розрахунків зробити висновки про отримані значення квалітетів та допусків, чи всі допуски на лінійні розміри адекватні та можуть виконуватись економічно доцільно на верстатах у серійному виробництві.
Зміст звіту
1Найменування і мета роботи.
2Креслення вузла складання.
3Схема розмірного ланцюга.
4Розрахунок розмірного ланцюга, розрахункові дані занести до таблиці В4.
5Висновки.
17
Контрольні запитання
1Що називається розмірним ланцюгом?
2Як поділяються розмірні ланцюги за видами?
3Які існують методи досягнення точності при складанні?
4Що таке метод неповної взаємозамінності?
5За яким алгоритмом розраховуються розмірні ланцюги?
Лабораторна робота № 4
Виявлення та розв’язання технологічних розмірних ланцюгів 2-го роду при умові обробки на верстаті з ЧПК
Мета роботи – навчитися розраховувати технологічні розмірні ланцюги 2-го роду якщо деталі оброблюються на верстатах з ЧПК.
Загальні вказівки
Технологічні розмірні ланцюги – забезпечують необхідну відстань або відносний поворот поверхонь виробу в процесі їх виготовлення.
Технологічні розмірні ланцюги бувають першого і другого роду.
До технологічних ланцюгів другого роду відносяться розмірні ланцюги, що зв'язують окремі операції, переходи (ланцюги першого роду). Для того, щоб виявити технологічний ланцюг другого роду, необхідно проаналізувати весь технологічний процес виготовлення деталі: від операції, на якій закінчується рішення поставленої задачі, до початку технологічного процесу.
Перерахунки розмірів і допусків проводять тоді, коли необхідно змінювати вимірювальну базу, тобто приймати іншу поверхню, лінію або точку, від яких проводиться зміна розмірів, що визначають положення обробленої поверхні.
Перерахунок розмірів і допусків застосовують, коли необхідно повністю відмовитися від системи розмірів, запропонованих на робочому кресленні. Так, на рисунку 5 (розміри які знаходяться у верхній частині L1-L6) показаний ланцюговий метод постановки розмірів на деталі вал. Однак за умовами виробництва реалізація цієї системи може виявитися скрутною. Її необхідно замінити на координатну систему (див. рисунок 5, розміри які знаходяться у нижній частині l1-l6) з відліком розмірів від лівого торця деталі. Тоді розміри L1-L6 не тільки замінюють на l1-l6, а й перераховують допуски. Особливо важливо знайти мінімальне значення допусків.
18
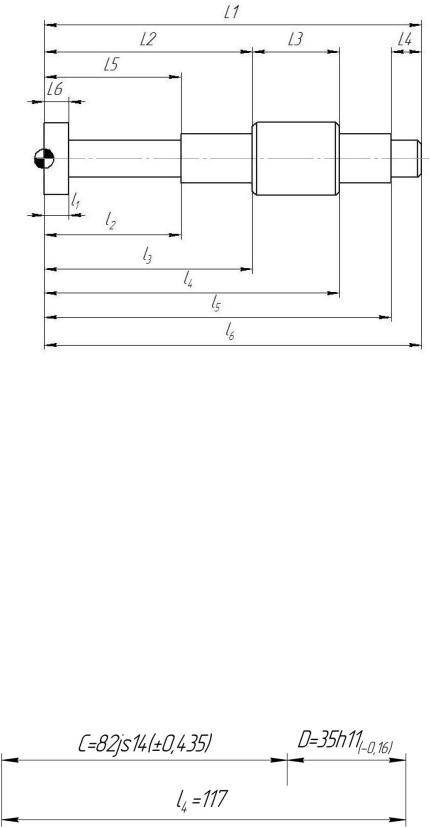
Рисунок 5 – Постановка конструкційних та технологічних розмірів на деталі «вал»
Особливу важливість точності розрахунків набувають при проектуванні технологічних процесів обробки деталей типу «тіло обертання» на верстатах з ЧПК. Установка валів виконується по упору в один з крайніх або проміжних торців деталі. Ця поверхня формує опорну технологічну базу валу. Лінійні розміри положення проміжних торців повинні бути встановлені від торця - опорної бази деталі. Для даних умов позначення розмірів необхідний аналіз точності і гарантії формування розмірів на верстатах, налаштованих на розмір (ЧПК, напівавтоматах, налаштованих універсальних верстатах).
Розглянемо схему розрахунку лінійних розмірів деталі "вал" за умови її обробки на верстаті з ЧПК за одним установом (рисунок 6).
Розрахунок розмірного ланцюга виконуємо імовірнісним методом (рисунок 7).
Рисунок 7 – Перший розмірний ланцюг
19