
Начерталка_1 / Правила нанесения размеров
.pdf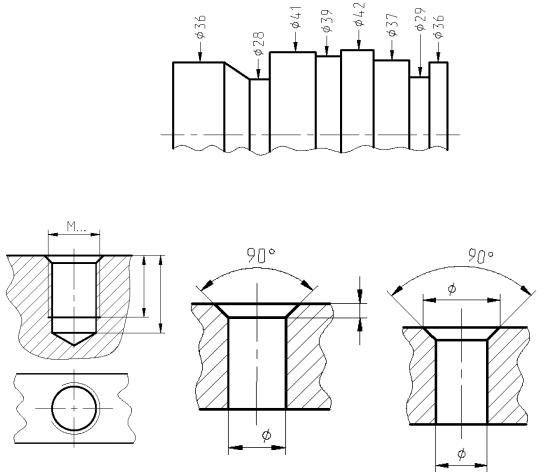
Рис. 61
Рис. 62 |
Рис. 63 |
Рис. 64 |
Некоторые элементы деталей зависят от формы режущего инструмента. Например, дно глухого отверстия получается коническим из-за формы
заточки сверла. Размер |
глубины таких отверстий проставляют на |
цилиндрической части |
|
(рис. 62). |
|
Размеры зенковок проставляют так, как показано на рис. 63, 64.
Если отверстия в детали расположены на осях ее симметрии, то угловые размеры проставлять не следует. Прочие же отверстия следует координировать угловым размером. При этом для отверстий, располагаемых по окружности на равных расстояниях, задается диаметр центровой окружности и задается надпись о количестве отверстий (рис. 65, 66).
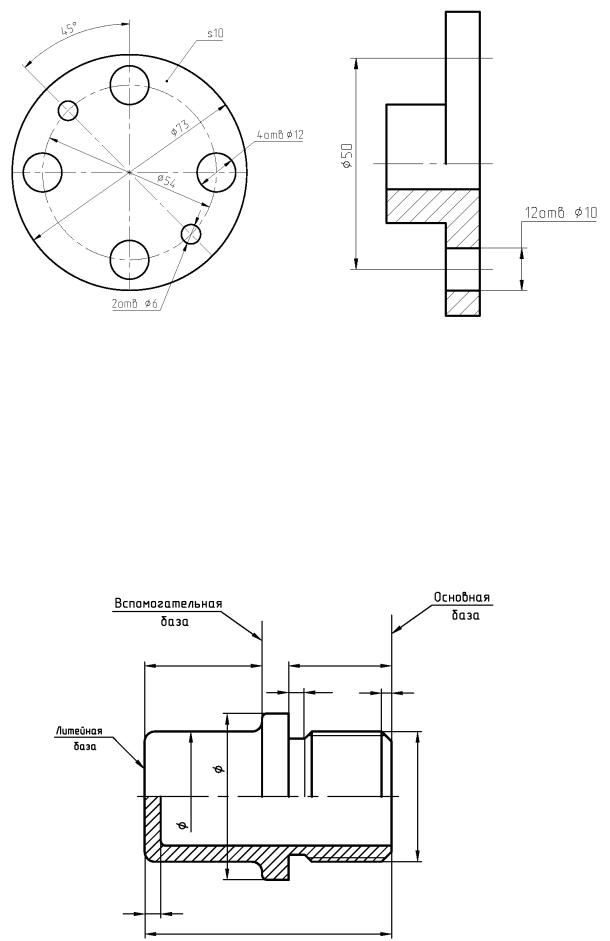
Рис. 65 |
Рис. 66 |
На чертежах литых деталей, требующих механической обработки, указывают размеры так, чтобы только один размер оказался проставленным между необработанной поверхностью – литейной базой и обработанной – основной размерной базой (рис. 67). На рис. 67 и 68 для сравнения приводятся примеры простановки размеров на чертеже литой детали и аналогичной детали, изготовляемой путем механической обработки.
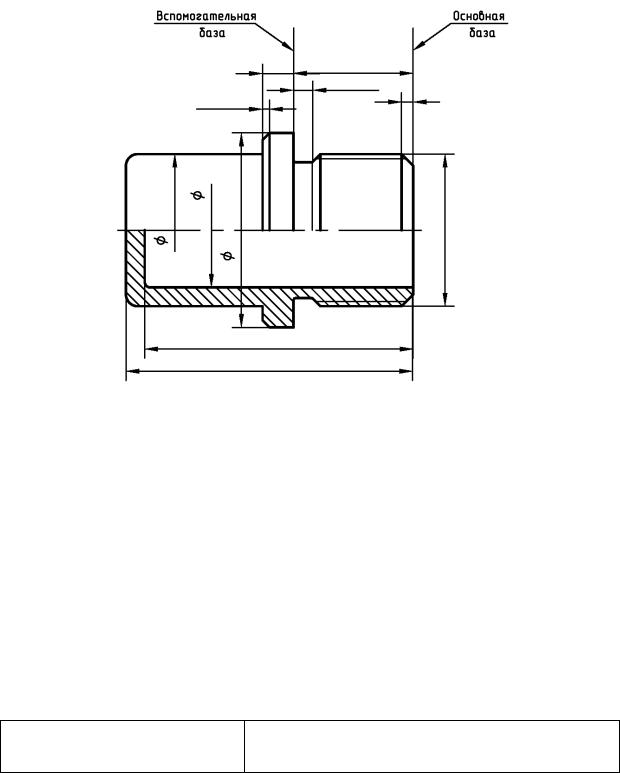
Рис. 67
Рис. 68
Размеры отверстий на чертежах допускается наносить упрощенно (по ГОСТ 2.318-81) (табл. 2.4) в следующих случаях:
▪диаметр отверстий на изображении – 2 мм и менее;
▪отсутствует изображение отверстий в разрезе (сечении) вдоль оси;
▪нанесение отверстий по общим правилам усложняет чтение чертежа.
Таблица 7
Упрощенное нанесение размеров на различные типы отверстий.
Тип отверстия
Пример упрощенного нанесения размеров отверстий
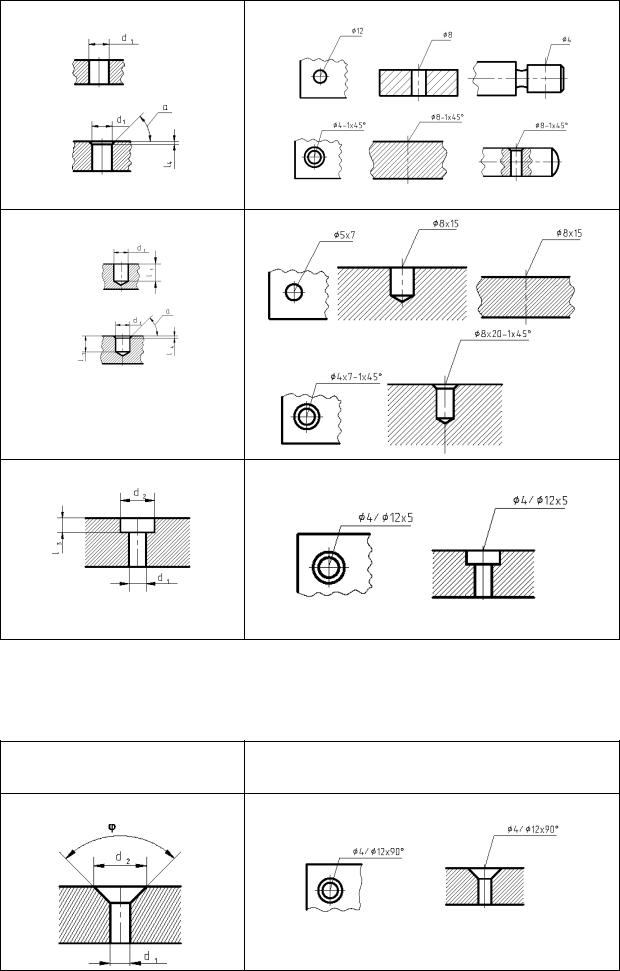
1
d1 x l1 –l4 x
2
d1x l1
d1 x l1 –l4 x
3
d1 /d2x l3
Продолжение табл. 7
Тип отверстия
Пример упрощенного нанесения размеров отверстий
4
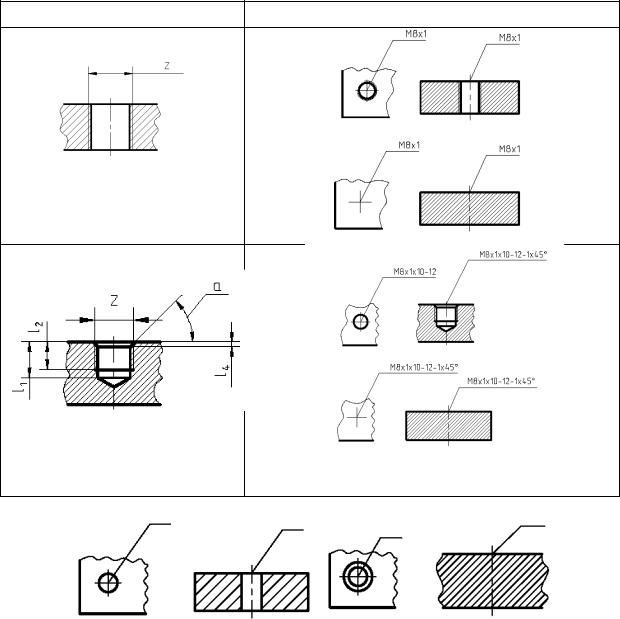
d1/d2x φ
5
6
Z x p x l2 – l1
Z x p x l2 – l1 – l4 x
Рис. 69
Размеры отверстий следует указывать на полке линии-выноски, проведенной от оси отверстия (рис. 69).
2.3.2. Изображение, обозначение и нанесение размеров некоторых элементов деталей
Наиболее распространены следующие элементы: фаски, галтели, проточки (канавки), пазы и т.д.
Фаски – конические или плоские узкие срезы (притупления) острых кромок деталей – применяют для облегчения процесса сборки, предохранения рук от порезов острыми кромками (требования техники
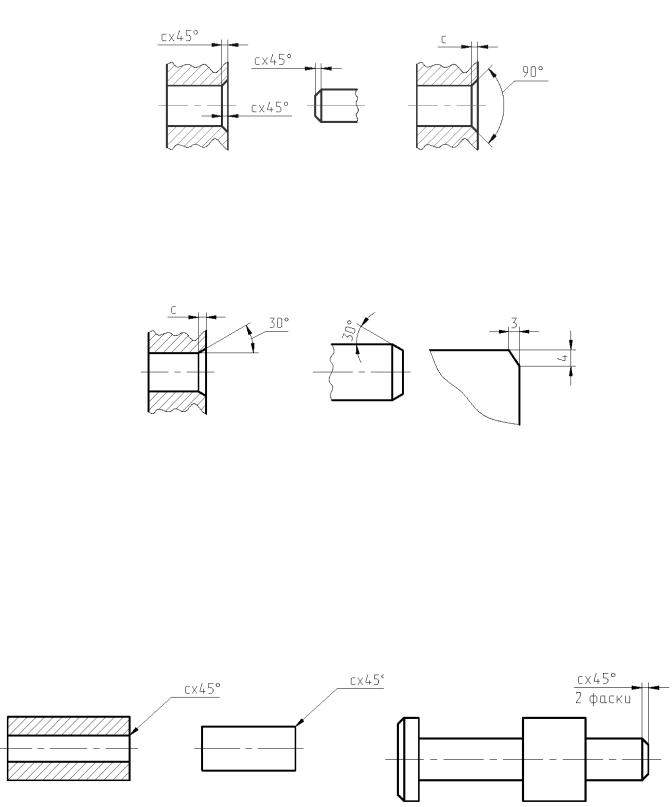
безопасности), придания изделиям более красивого вида (требования технической эстетики) и в других случаях.
Размеры фасок и правила их указания на чертежах стандартизированы. Согласно ГОСТ 2.307-68*, размеры фасок под углом 45о наносят так, как показано на рис. 70.
Рис. 70 Размеры фасок под другими углами (обычно 15, 30 и 60о ) указывают по
общим правилам: проставляют линейные и угловые размеры (рис. 71, а) или два линейных размера (рис. 71, б).
а |
б |
Рис. 71
Допускается указывать размеры не изображенной на чертеже фаски под углом 45о, размер которой в масштабе чертежа 1 мм и менее, на полке линиивыноски, как показано на рис. 72.
Размеры одинаковых фасок наносят один раз с указанием их количества
(рис. 73).
Рис. 72 |
Рис. 73 |

Размер высоты фаски с выбирают согласно ГОСТ 10948-64 (табл. 8). Таблица 8
Нормальные размеры фасок (ГОСТ 10948-64)
Угол |
|
|
|
|
|
|
|
|
|
|
|
|
|
|
|
|
|
|
|
фаск |
|
|
|
|
|
|
|
Высота фаски с |
|
|
|
|
|
|
|
||||
и |
|
|
|
|
|
|
|
|
|
|
|
|
|
|
|
|
|
|
|
|
|
|
|
|
|
|
|
|
|
|
|
|
|
|
|
|
|
|
|
45 |
0,5 |
0,7 |
0,8 |
1 |
1,2 |
1,5 |
1,8 |
2 |
2,5 |
3,5 |
4 |
4,5 |
5 |
6 |
7 |
8 |
9 |
10 |
15 |
и 60 |
|||||||||||||||||||
|
|
|
|
|
|
|
|
|
|
|
|
|
|
|
|
|
|
|
|
30 |
– |
– |
– |
1 |
– |
– |
– |
2 |
2,5 |
3 |
4 |
– |
5 |
6 |
7 |
8 |
9 |
10 |
15 |
|
|
|
|
|
|
|
|
|
|
|
|
|
|
|
|
|
|
|
|
П р и м е ч а н и е. Для неподвижных посадок следует принимать фаски: на конце вала 30о, в отверстии втулки 45о.
Галтели – скругления внешних и внутренних углов на деталях машин – широко применяют для облегчения изготовления деталей литьем, штамповкой, ковкой, повышения прочностных свойств валов, осей и других деталей в местах перехода от одного диаметра к другому. На рис. 74 буквой А отмечено место концентрации напряжений, могущей вызвать трещину или излом детали. Применение галтели устраняет эту опасность.
Рис. 74 Размеры галтелей берут из того же ряда чисел, что и для величины с
фаски.
Радиусы скруглений, размеры которых в масштабе чертежа 1 мм и меньше, не изображают и размеры их наносят, как показано на рис. 74.
Для получения резьбы полного профиля на всей длине стержня или отверстия делают проточку в конце резьбы для выхода инструмента. Проточки бывают двух исполнений. На чертеже детали проточку изображают упрощенно, а чертеж дополняют выносным элементом в увеличенном масштабе (рис. 49, 51). Форму и размеры проточек, размеры сбега и недореза устанавливает ГОСТ 10549-80 в зависимости от шага резьбы p.
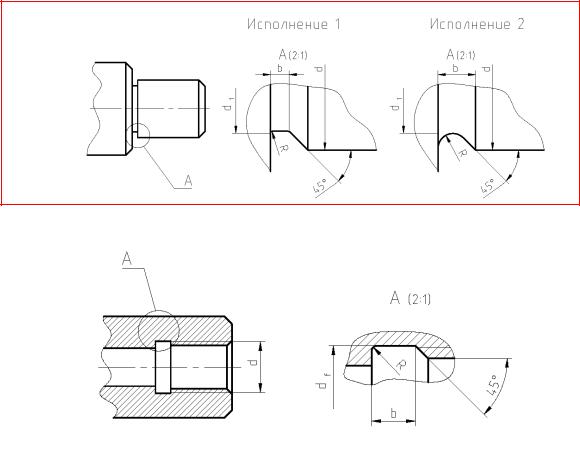
На рис. 75 приведен пример проточки для наружной метрической резьбы, а на рис. 76 – для внутренней метрической резьбы.
Рис. 75
Рис. 76 Размеры проточки выбирают из таблиц ГОСТ 10549-80 (см. прил. 5), их
можно также рассчитать по формулам.
Ниже приведены размеры проточек для наружной метрической резьбы:
b = 2,2 p, |
d f = d – 1,5 р, |
R = 0,6p; |
размеры проточек для внутренней метрической резьбы: |
||
b = 4 p, |
d f = d + 0,5 р, |
R = p. |
Кромки шлифовального круга всегда немного скруглены, поэтому в том месте детали, где нежелательно наличие отступа от кромок, делают канавку для выхода шлифовального круга.
Такую канавку на чертеже детали изображают упрощенно, а чертеж дополняют выносным элементом (рис. 77, 78).
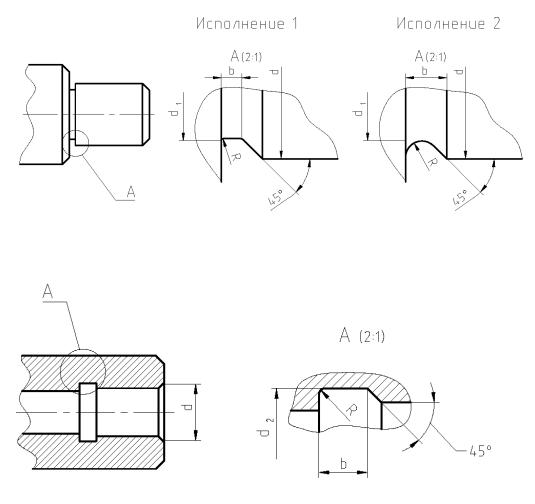
Рис. 77
Рис. 78.
Размеры канавок в зависимости от диаметра поверхности устанавливает ГОСТ 8820-69 (приложение 4).
Размеры канавок для выхода шлифовального круга можно рассчитать по
формулам (все размеры в мм): |
|
|
|
а) при d = 10÷50 мм |
b = 3, |
d1 = d –0,5, |
d2 = d + 0,5, |
h = 0,25; |
R = 1, |
R1 = 0,5; |
|
б) при d = 50 100 мм |
b = 5, |
d1 = d – 1, |
d2 = d + 1, |
h = 0,5; |
R = 1,5, |
R1 = 0,5. |
|
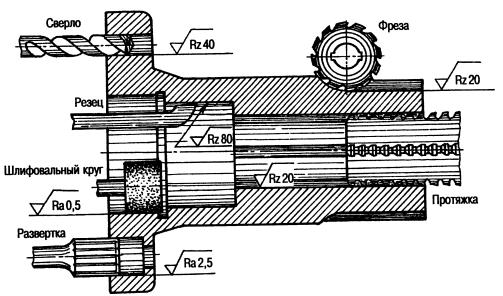
2.3.3. Шероховатость поверхностей детали
В зависимости от способа изготовления детали (рис. 79), ее поверхности могут иметь различную шероховатость (табл. 9, 10).
Рис. 79 Шероховатость поверхности – это совокупность микронеровностей
обработанной поверхности, рассматриваемых на участке стандартизированной длины (L).Эту длину называют базовой, она выбирается в зависимости от характера измеряемой поверхности. Чем больше высота микронеровностей, тем большей берется базовая длина.
Для определения шероховатости поверхности ГОСТ 2789-73 предусматривает шесть параметров.
Высотные: Ra – среднее арифметическое отклонение профиля; Rz – высота неровностей профиля по десяти точкам; Rmax – наибольшая высота профиля.
Шаговые: S – средний шаг местных выступов профиля; Sm – средний шаг неровностей; Ttp – относительная опорная длина, где p – значение уровня сечения профиля.
Наиболее распространенными в технической документации являются параметры Ra (среднее арифметическое отклонение профиля) и Rz (высота неровностей профиля по десяти точкам).
Зная форму профиля поверхности, определяемую профилографом на ее базовой длине L, можно построить диаграмму шероховатости (рис. 80),