
- •ВЫЕМОЧНО-ПОГРУЗОЧНЫЕ МАШИНЫ
- •ВВЕДЕНИЕ
- •1.1. Экскаваторы цикличного действия
- •1.2. Экскаваторы непрерывного действия
- •1.3. Перспективные конструкции выемочно-погрузочных машин и горных комплексов
- •Порядок выполнения работы
- •Содержание отчета
- •Вопросы и задания для самопроверки
- •2.1. Классификация, область применения
- •2.2. Конструктивные схемы прямой напорной лопаты
- •2.3. Конструктивные схемы коленно-рычажной напорной лопаты
- •2.4. Конструктивная схема напорной лопаты с рабочим оборудованием «Суперфронт»
- •2.5. Конструктивная схема прямой гидравлической лопаты
- •2.6. Конструктивные схемы драглайна и грейфера
- •Порядок выполнения работы
- •Содержание отчета
- •Вопросы и задания для самопроверки
- •3.3. Конструктивные схемы роторных экскаваторов
- •3.4. Конструктивные схемы экскаваторов фрезерного типа
- •Порядок выполнения работы
- •Содержание отчета
- •Вопросы и задания для самопроверки
- •4.1. Назначение и состав рабочего оборудования
- •4.2. Рабочее оборудование механической лопаты
- •4.3. Рабочее оборудование драглайна
- •Порядок выполнения работы
- •Содержание отчета
- •Вопросы и задания для самопроверки
- •5.1. Назначение и состав рабочего оборудования
- •5.2. Рабочее оборудование цепных экскаваторов
- •5.3. Рабочее оборудование роторных экскаваторов
- •5.4. Ковши цепных и роторных экскаваторов
- •Порядок выполнения работы
- •Содержание отчета
- •Вопросы и задания для самопроверки
- •БИБЛИОГРАФИЧЕСКИЙ СПИСОК
- •ОГЛАВЛЕНИЕ
Машины приспособлены в основном к отработке сложноструктурных залежей горизонтального и слабонаклонного залегания при относительно небольших значениях мощностей отдельных пластов и породных пропластков. Их целесообразно использовать в сочетании с автотранспортом при относительно невысоких объемах горных работ либо введением в состав горнотранспортного оборудования дополнительного звена (перегружателя), осуществляющего связь между непрерывно перемещающейся экскавационной машиной и, например, линией ленточных конвейеров.
1.3. Перспективные конструкции выемочно-погрузочных машин и горных комплексов
Как отмечалось в п. 1.1, в России одним из ведущих производителей экскаваторной техники является компания ООО «ИЗ-КАРТЭКС». Она имеет более чем 50-летний опыт производства карьерных экскаваторов. Основу парков добычной техники всех крупных горных предприятий России, Казахстана, Украины и Узбекистана составляют машины ООО «ИЗ-КАРТЭКС». Это ЭКГ-8И, ЭКГ-10, ЭКГ-12,5, ЭКГ-15 и их модификации.
Сегодня стратегия компании направлена на разработку новой линейки экскаваторов с ковшами вместимостью 10–65 м3. Это ЭКГ-12К, ЭКГ-20, ЭКГ-30, ЭКГ-50. Каждый типоразмер экскаватора спроектирован под автосамосвал оптимальной грузоподъемности, исходя из условий их загрузки за 3–5 циклов экскаватора.
Новая линейка экскаваторов ИЗ-КАРТЭКС включает четыре типоразмерные группы [8, 14]:
К первой типоразмерной группе относится экскаватор ЭКГ-12К (рис. 1.6) [6] с ковшами вместимостью 10–16 м3, его базовый ковш 12 м3 рассчитан для тяжелых условий эксплуатации при разработке горных пород IV категории прочности. ЭКГ-12К предназначен для работы с автосамосвалами грузоподъемностью 75–110 т, он призван заменить в парках горных предприятий экскаваторы ЭКГ-8И и ЭКГ-10. Экскаватор ЭКГ-12К имеет традиционную для ОАО «Ижорские заводы» схему рабочего оборудования, в которой канатный напор сочетается с шарнирно-сочлененной двухбалочной стрелой и однобалочной рукоятью круглого сечения со встроенным механизмом демпфирования. Преимуществом этой схемы рабочего оборудования является разгруз-
26
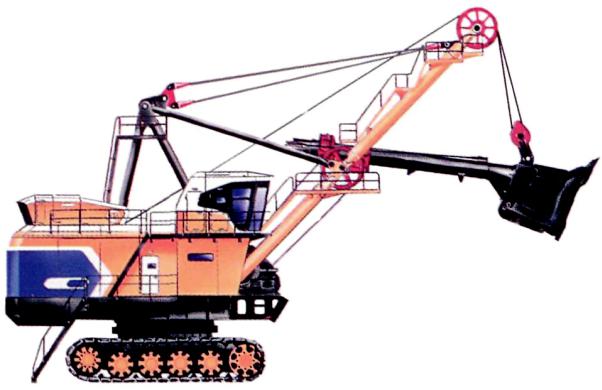
ка стрелы от изгиба (в вертикальной плоскости), а рукояти от кручения, что наряду со снижением динамических нагрузок в напорном механизме приводит к уменьшению веса рабочего оборудования.
Рис. 1.6. Перспективный экскаватор первой типоразмерной группы ЭКГ-12К (ООО «ИЗ-КАРТЭКС»)
Стрела длиной 14,35 м состоит из двух шарнирно-сочлененных секций: верхней и нижней. Секции стрелы двухбалочные с мощными поперечными связями между балками. В местах сочленения секций стрелы на напорной оси расположен седловой подшипник, в котором перемещается рукоять, а также направляющие блоки напорного и возвратного канатов.
Однобалочная трубчатая рукоять (по сравнению с двухбалочной) имеет существенно меньший вес, что позволяет увеличить усилие резания на зубьях ковша и продлить срок службы. В хвостовой части рукояти установлен механизм демпфирования двустороннего действия, который снижает динамические нагрузки на рукоять и механизм напора при встрече ковша с труднопреодолимым препятствием в забое и при ударе рукояти о седловой подшипник.
27
Передняя стенка и зубья ковша выполнены литыми из высокомарганцовистой, износостойкой стали. На козырьке ковша между зубьями предусмотрены клинообразные утолщения, существенно увеличивающие срок службы козырька. Для увеличения долговечности ковшей их корпус и днище армированы листовыми накладками, имеющими высокую твердость.
Экскаватор ЭКГ-12К в отличие от экскаватора ЭКГ-10 выполнен с бесполиспастным механизмом подъема ковша без коромысла и уравнительных блоков, что существенно улучшает условия копания, позволяет реализовать большие усилия на зубьях ковша, увеличивает высоту копания. По сравнению с ЭКГ-10 новый экскаватор имеет, соответственно, на 0,6 и 1,5 м большие радиус и высоту копания, на 0,7 и 1,4 м большие радиус и высоту разгрузки. Радиус копания на уровне стояния у экскаватора ЭКГ-12К на 1,4 м больше, что дает возможность отказаться от дополнительных машин при подготовке подошвы забоя.
Поворотная платформа экскаватора состоит из центральной части балочно-рамной конструкции и облегченных боковых площадок. Наиболее тяжелые узлы (электромашинный агрегат, лебедка подъема, механизмы поворота, шкафы электрооборудования и др.) смещены назад от оси вращения, что позволило уменьшить массу противовеса. Поворотная платформа ЭКГ-12К на 0,8 м шире, чем у экскаватора ЭКГ-10, что обеспечивает большие проходы между механизмами и улучшает условия обслуживания и ремонта.
Лебедки подъема и напора двухбарабанные с консольным расположением барабанов на выходном валу редуктора и с комбинированными планетарно-рядными редукторами. Используемое разделение силового потока обеспечивает установку зубчатых колес меньшего модуля, увеличение плавности хода, снижение шума и вибрации.
Гусеничное ходовое устройство унифицировано с ходовым устройством экскаватора ЭКГ-10. Привод хода на каждую гусеницу осуществляется раздельно через трехступенчатый редуктор и бортовую передачу. Экскаватор сможет преодолевать подъем до 12о.
На экскаваторе использована современная цифровая процессорная система управления, обеспечивающая плавность рабочих движений при оптимальных механических характеристиках и высоком коэффициенте полезного действия (КПД). В состав этой системы входят специальные устройства контроля работы электроприводов и диагностики оборудования.
28
Машинист управляет экскаватором с помощью эргономичных двухкоординатных ручных командоконтроллеров (джойстиков), применение которых позволяет снизить утомляемость машиниста и увеличить точность управления механизмами экскаватора.
Управление экскаватором осуществляют из двухэтажной вибро- и шумозащищенной кабины. Верхний этаж кабины двухсекционный, включающий рабочее помещение и комфортабельное помещение для отдыха. На нижнем этаже кабины смонтирована установка регулирования микроклимата. В рабочем помещении установлено виброизолированное кресло-пульт. Кабина герметична, снабжена системой отопления, кондиционером, вентиляцией и обогревом стекол.
Вторая типоразмерная группа (рис. 1.7) представлена унифи-
цированным экскаватором ЭКГ-20 с ковшами вместимостью 16–24 м3 для работы в комплексе с автосамосвалами грузоподъемностью 120–150 т. Базовый ковш 18 м3 предназначен для машины с реечным напорным механизмом ЭКГ-18Р (рис. 1.7, а) и 20 м3 – для машины с канатным типом напорного механизма ЭКГ-20К (рис. 1.7, б). Экскаватор целесообразно использовать как для угольных, так и для рудных горнодобывающих предприятий при наращивании объемов добычи.
Третья типоразмерная группа (рис. 1.8) представлена унифици-
рованным экскаватором ЭКГ-30 с ковшами вместимостью 20–50 м3 для работы в комплексе с автосамосвалами грузоподъемностью 190– 240 т. Базовый ковш 32 м3 предназначен для машины с реечным напорным механизмом ЭКГ-32 Р (рис. 1.8, а) и 35 м3 – для машины с канатным напорным механизмом ЭКГ-35 К (рис. 1.8, б). Основные заказчики машины – активно развивающиеся угольные предприятия и горно-металлургические компании, осваивающие новые крупные месторождения полезных ископаемых.
Четвертая типоразмерная группа представлена экскаватором ЭКГ-50 (рис. 1.9) с ковшами вместимостью 40–65 м3 для работы в комплексе с автосамосвалами грузоподъемностью 280–340 т. Базовый ковш – 55 м3. Экскаватор предназначен для применения на мощных угольных разрезах и карьерах новых перспективных месторождений.
Эффективность применения новой линейки экскаваторов ИЗ-КАРТЭКС по сравнению с серийными машинами ЭКГ-10 и ЭКГ-15 обеспечивается:
унификацией машин одного класса в рамках единой платформы (уровень унификации достигает 80 %);
29

а
б
Рис. 1.7. Перспективные экскаваторы второй типоразмерной группы
ООО «ИЗ-КАРТЭКС»: а – ЭКГ-18Р; б – ЭКГ-20К
30
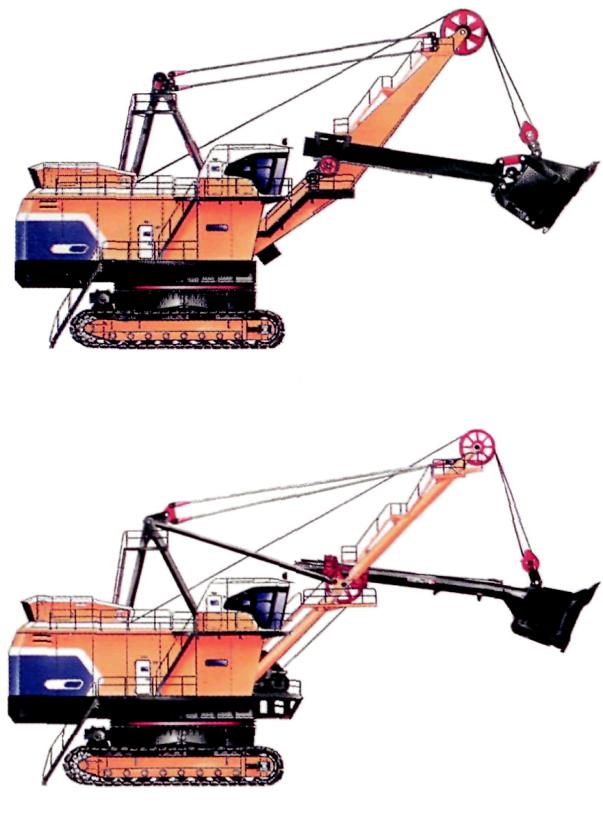
а
б
Рис. 1.8. Перспективные экскаваторы третьей типоразмерной группы
ООО «ИЗ-КАРТЭКС»: а – ЭКГ-32Р; б – ЭКГ-35К
31
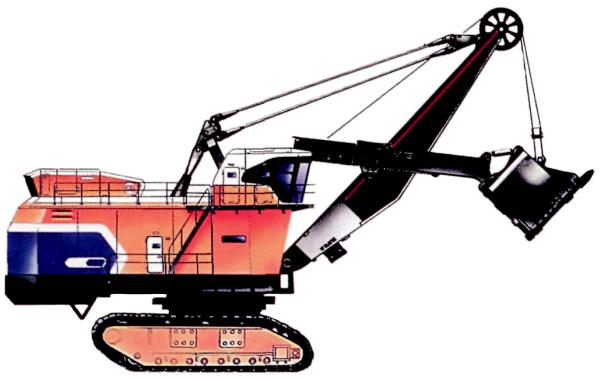
высокой производительностью и долговечностью машин за счет применения ковшей большей вместимости, бесполиспастной системы подвески ковша, большей надежности и долговечности редукторов и ходового механизма;
Рис. 1.9. Перспективный экскаватор четвертой типоразмерной группы ЭКГ-50 (ООО «ИЗ-КАРТЭКС»)
снижением расхода запчастей и трудоемкости технического обслуживания за счет увеличения ресурса основных механизмов и металлоконструкций, применения автоматической системы централизованной смазки, использования роликовых кругов с коническими роликами, установленными на втулках, не требующих смазки, современных канатов большой ходимости и других конструкторских новаций;
применением современной системы приводов, снижающих энергопотреблениеиувеличивающихсрокслужбыэлектрооборудования;
применением информационно-диагностической системы (ИДС), обеспечивающей диагностику и защиту механического и электрического оборудования, учет основных технологических параметров экскавации. ИДС позволяет выводить на дисплей основные параметры,
32
контролировать работу экскаватора в режиме реального времени. Машинист получает информацию о весе породы в ковше, количестве рабочих циклов, объеме отгруженной горной массы, времени полезной работы и расходе электроэнергии за смену. Не выходя из кабины, он сможет узнать о состоянии главных электроприводов, температуру обмоток и подшипников двигателей, давление в системах сжатого воздуха, уровень масла в редукторах, загрузку двигателей подъема, напора и поворота. Предусматривается система автоматических защит механического оборудования. ИДС должна сигнализировать о превышении контрольных величин усилий в подъемных канатах или механизме напора, о напряжениях в ответственных точках металлоконструкций и др.;
созданием комфортных условий труда экипажа за счет применения новой кабины, которая максимально удобна не только для работы машиниста, но и отдыха и приема пищи;
увеличением нормативного срока эксплуатации машины с 17 до
20 лет;
повышением эффективности использования автосамосвалов большой и особо большой грузоподъемности (120–250 т и более).
В мае 2009 г. на Талдинском разрезе ОАО «УК Кузбассразрезуголь» принят в эксплуатацию экскаватор ЭКГ-1500Р с ковшом вместимостью 18 м3, изготовленный в ООО «ИЗ-КАРТЭКС». Он подтвердил свои технические характеристики и показал среднюю часовую производительность 1 000–1 200 м3.
Воплощение новой стратегии ООО «ИЗ-КАРТЭКС» было начато с производства экскаватора ЭКГ-12К. В августе 2009 г. отгружен опытный образец для железорудного комбината ОАО «Олкон» (Се- версталь-Ресурс).
Завершены проектные работы по экскаваторам новой линейки ЭКГ-18Р и ЭКГ-32Р. Поставка этих машин начинается в 2011 г. на угольные разрезы ОАО «УК Кузбассразрезуголь». Переоснащение парков выемочно-погрузочной техники на предприятиях России, Казахстана, Украины, Узбекистана экскаваторами ООО «ИЗ-КАРТЭКС» диктуется все большей долей автосамосвалов грузоподъемностью 120–250 т и более в транспортных парках карьеров.
Другим направлением развития экскавационной техники явля-
ется создание карьерного гидравлического экскаватора с непрерывной разгрузкой горной массы (ЭГН) в ООО «ОМЗ-ГОиТ» (рис. 1.10,
табл. 1.11). Экскаватор предназначен для экскавации как связанных
33
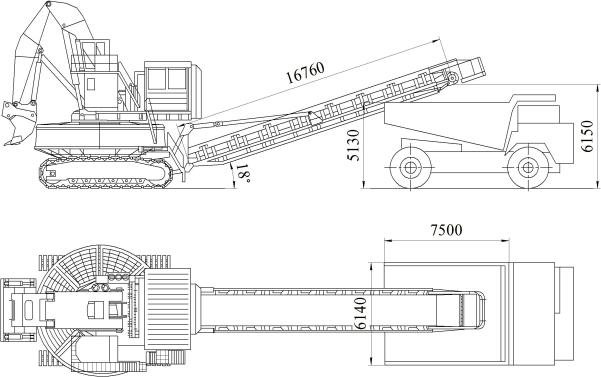
горных пород, так и взорванной горной массы. Рабочее оборудование ЭГН такое же, как у традиционных гидравлических экскаваторов типа «прямая лопата». Отличительной особенностью нового экскаватора является оснащение его кольцевым конвейером оригинальной конструкции, что позволяет преобразовать цикличный характер копания в непрерывный поток погружаемой породы. Общая компоновочная схема такой машины исключает необходимость поворота рабочего оборудования машины на разгрузку в процессе рабочего цикла. Разгрузка породы из ковша производится непосредственно в кольцевой конвейер в плоскости копания.
Рис. 1.10. Схема экскаватора ЭГН
По сравнению с гидравлическими экскаваторами традиционного исполнения новая экскавационная машина ЭГН обеспечивает:
повышение производительности за счет сокращения продолжительности рабочего цикла;
непрерывную погрузку экскавируемой горной массы в различные транспортные средства;
возможность использования экскаватора ЭГН в сочетании с перегружателем для погрузки экскавируемой горной массы как в сред-
34
ства железнодорожного транспорта (в думпкары и полувагоны), так и автомобильного, а также для работы в схемах циклично-поточной и бестранспортной технологии;
разгрузку горной массы из ковша в постоянное место, что позволяет автоматизировать часть рабочего цикла копания.
Таблица 1.11. Техническая характеристика экскаватора ЭГН
Показатель |
Значение |
|
|
Вместимость основного ковша, м3 |
10,0 |
Наибольшее усилие на зубе ковша, кН, не менее |
800 |
|
|
Радиус копания, м: |
|
наибольший |
14 |
на уровне стояния |
11 |
Наибольшая высота, м: |
|
копания |
15 |
разгрузки |
6 |
Расчетная продолжительность цикла копания, с, не более |
16 |
|
|
Скорость передвижения по подготовленной трассе, м/с (км/ч), не менее |
0,55 (1,5) |
Удельное давление на грунт при передвижении, МПа, не более |
0,22 |
|
|
Установленная мощность привода, кВт |
1 000 |
|
|
Масса, т, не более |
280 |
Теоретическая производительность, м3/ч, не менее |
2250 |
Производительность ЭГН с ковшом вместимостью 10 м3 эквивалентна производительности гидравлического экскаватора традиционного исполнения с ковшом вместимостью 15–16 м3.
Добычной комплекс (ДК) предназначен для экскавации полезных ископаемых и вскрышных пород с их погрузкой в автомобильные и железнодорожные транспортные средства, а также для работы в схемах циклично-поточной технологии, бестранспортной и транс- портно-отвальной системах разработки.
Добычной комплекс представляет собой сочетание различных видов горного оборудования с непременным присутствием в качестве разрабатывающей машины ЭГН. В ходе проектирования было предложено несколько вариантов исполнения добычного комплекса с различным сочетанием оборудования.
35

Из разнообразия вариантов наиболее экономичным на первой стадии является вариант добычного комплекса, состоящего из экскаватора и перегружателя. Существенное преимущество данного варианта заключается в том, что он легко вписывается в имеющуюся технологию разработки карьера и перспективен для использования на складах. Величина заходки при погрузке в железнодорожный транспорт составляет не менее 21 м, а при работе на складах – до 40 м (рис. 1.11). При увеличении параметров перегружателя или использовании дополнительных конвейеров можно довести величину заходки до необходимых заказчику размеров.
Рис. 1.11. Параметры заходки экскаватора ЭГН с перегружателем
Загрузка автосамосвалов осуществляется как с использованием перегружателя, так и непосредственно экскаватором ЭГН.
Расчеты показали, что сочетание экскаваторов типа ЭГН в бестранспортной технологии с драглайнами вместимостью 10–40 м3 и
36
отвалообразователями с радиусом разгрузки 120–150 м позволяет довести суммарную высоту вскрышных уступов до 50–60 м. Сравнительный технико-экономический анализ базовой и новой технологии в зависимости от вариантов технологических схем, параметров оборудования и объемов вскрышных работ свидетельствует о снижении стоимости оборудования до 21 %, численности основного эксплуатационногоперсоналадо70 %, годовыхэксплуатационныхзатратдо47 %.
Предложенная конструкция комплекса, позволяющая повысить эффективность добычных работ, накладывает следующие ограничения на подготовку горной массы: максимальные размеры куска горной массы не должны превышать 800 мм; содержание глины в породе не должно быть более 15 %.
Эксплуатация ЭГН связана с возникновением следующих эксплуатационных рисков:
появлением ударных нагрузок на ЭГН при разгрузке; дополнительным источником шума при перемещении горной
массы по кольцевому конвейеру; усложнением конструкции;
повышением требований к слаженности работы механизмов и автоматизации отдельных операций.
Комплекс оборудован автоматической системой управления, которая согласовывает взаимодействие работы механизмов и оборудования, экскавацию и транспортирование горной массы.
Ширина заходки ЭГН с погрузкой при использовании перегружателя в железнодорожный транспорт в 2–2,5 раза выше, чем при использовании экскаватора традиционного исполнения, что значительно снижает расходы на перемещения железнодорожных путей. Увеличенная удельная масса ЭГН позволяет реализовать большие усилия копания.
Использование ДК с погрузкой горной массы в железнодорожный транспорт с учетом увеличенной ширины заходки дает возможность снизить эксплуатационные расходы на 50–60 млн руб./год по сравнению с погрузкой в автомобильный транспорт. Следует отметить также и то, что поточный способ погрузки в транспорт обеспечивает наименьшее силовое воздействие на последний.
Представленный ООО «ОМЗ-ГОиТ» новый способ разработки горных пород с помощью экскаватора типа ЭГН позволяет не только сократить цикл копания и превратить цикличный процесс копания в поточную разгрузку и перемещение горной массы, но и повлиять на
37
развитие новой технологии добычи. Внедрение ДК дает возможность существенно повысить производительность, сократить суммарную численность обслуживающего персонала, получить значительный экономический эффект [5].
ВКрасноярске конструкторское бюро «Крастяжмаш» (КБ КТМ) работает над новыми конструкциями экскаваторов КТМ, которые ломают сложившуюся классификацию горных экскаваторов на канатные и гидравлические. Они представляют собой новый класс машин с приводом типа «механический толкатель» (МТ), в котором оптимальным образом соединены преимущества обоих классов и устранены все известные недостатки существующих моделей горных экскаваторов.
Экскаваторы КТМ – полноповоротные землеройные машины, построенные на базе универсальной платформы (УП), рис. 1.12. На поворотной универсальной платформе смонтирована кабина с органами управления, трансформатор (дизельный электрогенератор) и рабочее оборудование. Экскаваторы КТМ оборудованы системами управления, смазки, тормозной, самодиагностики и сигнализации, вентиляции, балансировкииразвесовки, бортовыхгрузоподъёмныхприспособлений.
Экскаваторы КТМ имеют модульную компоновку, т.е. состоят из транспортных модулей (ТМ): КТМ-405Т – из четырех ТМ, КТМ-510Т – из пяти ТМ и т. д. Предварительная сборка и настройка ТМ и экскаватора в целом происходит на заводе-изготовителе, после чего машина разбирается на модули, каждый из которых приспособлен для транспортировки на стандартных авто- и железнодорожных платформах. После получения всех ТМ специалисты заказчика под руководством сертифицированного шеф-инженера производят сборку экскаватора в течение нескольких рабочих смен (от 2 для модели КТМ-400 до 7 для КТМ-600). Сразу же после сборки экскаватор КТМ будет готов к началу работы.
Впределах одного экскаватора на всех приводах применен один тип электродвигателя – переменного тока с частотным регулированием. Мощность привода достигается путем использования нужного количества электродвигателей, что с учетом резервирования мощности (до 160 %) позволяет сохранить работоспособность узла при выходе из строя одного или двух модулей «электродвигатель – привод».
Редукторы хода и поворота дифференциально-планетарного типа, являются собственной патентованной разработкой КБ КТМ, в течение эксплуатации в ремонте не нуждаются, т.е. имеют расчетный ресурс, сравнимый с ресурсом экскаватора в целом.
38
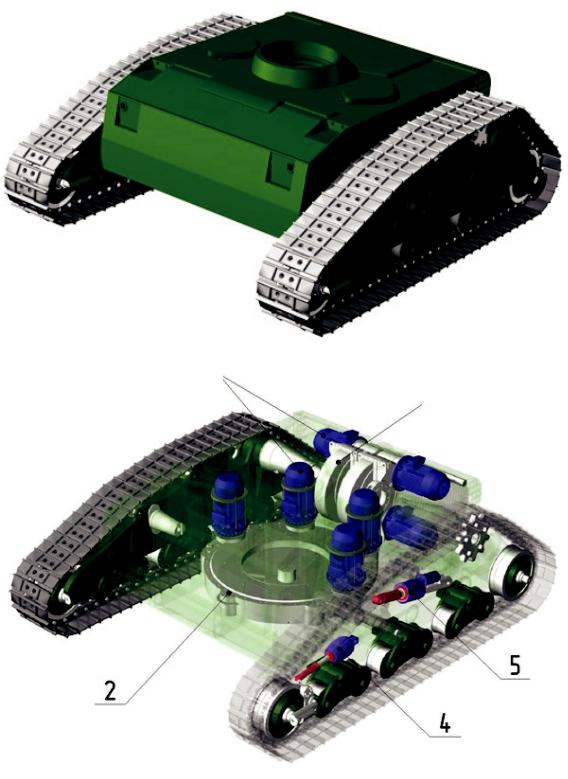
а
1
3
|
|
|
|
5 |
2 |
|
|
|
|
|
|
|
|
|
|
|
|
|
|
|
|
4 |
|
|
|
|
|
|
|
|
|
|
|
|
б
Рис. 1.12. Внешний вид (а) и строение (б) универсальной платформы КТМ-400: 1 – электродвигатели приводов хода и поворота; 2 – редуктор привода поворота; 3 – редуктор привода хода; 4 – механический толкатель натяжения гусеничной ленты МТ-50; 5 – механический толкатель угла установки гусеничной тележки, системы балансировки и развесовки МТ-100
39
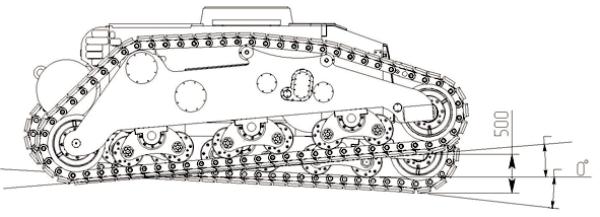
Питание в бортовую сеть подается от внешнего источника либо от бортового дизельного электрогенератора.
Универсальная платформа – силовая пространственная рама, закрытая съемными капотами, со смонтированными в ней приводами хода, поворота, силовым электрооборудованием. Опорно-поворотное устройство (ОПУ), расположенное в универсальной платформе, представляет собой конусную цапфу, установленную на серийные роликовые подшипники качения. С внешней стороны справа и слева УП на независимой подвеске смонтированы гусеничные тележки, на корме установлен кабельный барабан (300 м кабеля).
Гусеничные тележки (рис. 1.13) имеют свободный ход вокруг оси ведущего колеса с углом установки относительно УП ±4 %, что обеспечивает разницу высоты между правым и левым передним направляющими катками (например, УП КТМ-400 – до 0,5 м). Независимая подвеска в автоматическом режиме устанавливает опорные поверхности гусеничных тележек на четыре опорные точки, что исключает ударные нагрузки на силовые элементы конструкции («качание» экскаватора) во время копания.
4о
4о
Рис. 1.13. Схема гусеничных тележек КТМ
Гусеничные тележки оборудованы механическим токателем натяжения гусениц с ручным приводом. Гусеница разъемная, состоит из цепи и съемных башмаков (сталь 110Г13Л). Гусеничные тележки передвигаются по цепи гусеницы на опорных катках в балансирах, заднем направляющем и переднем направляющем натяжном катках. Усилие на цепь передается ведущим колесом, расположенным в верхней части гусеничной тележки. Между ведущим колесом и пе-
40
редним направляющим катком гусеницу поддерживают направляющие катки, исключающие избыточное провисание и растяжение гусеничной цепи.
Необходимо отметить, что универсальная платформа может выполнять функцию транспортной платформы для перемещения особо тяжелых и габаритных грузов, а также нести на себе иное оборудование (например, буровой станок, перегружатель, подъемный кран и т.д.).
Кабина рассчитана на двух членов экипажа с одним рабочим местом и зоной для отдыха, шумоизолирована, оборудована системами приточно-вытяжной вентиляции, пылеудаления, кондиционирования и вибропоглощения; оснащена защитным силовым козырьком, остеклением «триплекс», подогревом переднего стекла, дворником переднего стекла, боковой форточкой, круговым трапом для обслуживания, аудиоусилителем и высококачественными динамиками, системой громкой связи.
Рабочее место машиниста – эргономичное кресло с регулировками и подогревом, удобно расположенными органами управления типа «джойстик», ЖК-монитором с высоким разрешением, системами управления и диагностики-сигнализации, а также системой кругового видеообзора.
Зона для отдыха – откидной столик и встроенная тумбочка с холодильником, микроволновой печью и розетками ~220 В для чайника, а также эргономичное кресло для помощника машиниста.
Экскаваторы КТМ отличаются возможностью монтажа на универсальную платформу различных типов рабочего оборудования:
«П» (параллелограмм) – экскаватор – погрузчик прямая лопата; «О» – экскаватор – погрузчик обратная лопата; «Т» (треугольник) – экскаватор – прямая механическая лопата; «РК» (роторный комплекс); «Д» (драглайн);
«КП» (конвейерный перегружатель); «ПК» (подъемный кран).
Каждому классу УП соответствует рабочее оборудование, имеющее определенные параметры (табл. 1.12).
Привод рабочего оборудования осуществляется разработанным «КБ КТМ» патентованным приводом «механический толкатель» (рис. 1.14), представляющем собой подшипнико-винтовую пару оригинальной конструкции, заключенную в пыле- и влагонепроницаемый кожух. Этот линейный механический редуктор при массе от 6 до 15 т
41
создает нагрузку от 100 до 800 т в диапазоне от 2 до 8 м и обеспечивает линейную скорость хода толкателя до 2 м/с. Механизм сохраняет работоспособность даже при значительном неравномерном износе винта (до 1 мм на 1 м длины). Высокие ресурсные характеристики достигаются использованиемвкачествематериалавинтакованойсталиШХ-15.
Таблица 1.12. Возможные параметры
рабочего оборудования на базе УП КТМ
Рабочая |
|
Допус- |
Скорость |
Рабочее оборудование и его параметры |
||||
масса, т |
|
тимая |
передви- |
«П», «О», |
«Д», вме- |
«РК», про- |
«ПК», |
|
(вместе с |
УП |
масса |
жения по |
«Т», вме- |
стимость3 |
изводи- |
вылет |
|
рабочим |
|
перево- |
ровной по- |
стимость |
ковша, м |
тельность, |
стре- |
|
оборудо- |
|
зимого |
верхности, |
ковша, м |
3 |
/ вылет |
т/ч |
лы, м |
ванием) |
|
груза, т |
м/ч |
|
стрелы, м |
|||
120–210 |
КТМ-400 |
300 |
|
5–12 |
|
От 5/40 |
200–600 |
До 40 |
|
|
до 6/35 |
||||||
|
|
|
2 000 |
|
|
|
|
|
180–350 |
КТМ-500 |
600 |
6–20 |
|
От 6/70 |
600–1 000 |
До 70 |
|
|
|
|||||||
|
|
до 10/40 |
||||||
|
|
|
|
|
|
|
|
|
|
|
|
|
|
|
|
|
|
420–800 |
КТМ-600 |
1 200 |
1 500 |
6–30 |
|
От 10/80 |
1 200–2 000 |
До 120 |
|
до 15/60 |
|||||||
650–1 000 |
КТМ-800 |
2 000 |
1 000 |
25–40 |
|
От 15/90 |
2 500–4 000 |
До 160 |
|
до 25/70 |
Система управления диагностирует тип рабочего оборудования, смонтированного на УП, обеспечивает корректное управление всеми заявленными функциями, не допускает управления экскаватором без специального ключа. Она оборудована механическими и электронными ограничителями и предохранителями всех критических режимов эксплуатации. С помощью блока GPS или ГЛОНАСС система управления обеспечивает точную фиксацию местоположения экскаватора, позволяет передачу с помощью средств связи необходимых параметров в диспетчерскую, интуитивно понятно отображает в режиме реального времени происходящие процессы на ЖК-экранах с высоким разрешением (в том числе визуализирует положение центра тяжести, углы наклона гусеничных тележек, работу кинематики рабочего оборудования, положение рабочего органа, массу породы в ковше, состояние всех систем экскаватора). Кроме того, она позволяет проводить диагностику и своевременное выявление критических ре-
42
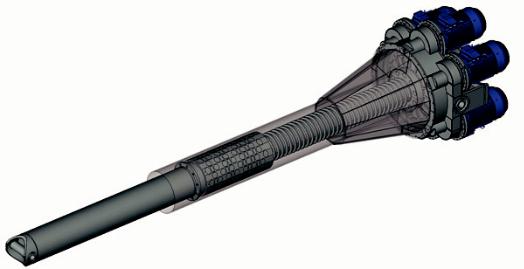
жимов эксплуатации и неисправностей, предупреждает о необходимых планово-предупредительном (ППР) и капитальном ремонте (КР), имеет специальный блок архивирования данных («черный ящик»), обеспечивающий фиксацию и запись всех режимов работы за заданный период времени с выдачей параметров по запросу. Также система управления измеряет, рассчитывает и записывает ряд показателей, например, таких, как количество циклов, масса погруженной породы, моточасы наработки каждого узла и экскаватора в целом, энергозатраты на погруженную тонну для каждого машиниста.
Рис. 1.14. Внешний вид механического толкателя
Система смазки экскаватора автоматическая, с системой фильтрации, самодиагностики и резервации, имеет два независимых контура – на поворотной платформе и внутри универсальной платформы. Смазка автоматически и точечно подается во все зоны трения всех вращающихся механизмов. Подшипники всех катков, сочленений стрелы выполнены по закрытой схеме и набиваются смазкой, рассчитанной на период между ППР. Каждый контур системы смазки включает маслостанцию, два маслонасоса (основной и резервный), масляные фильтры, систему диагностики и сигнализации (чистота, наличие стружки, температура, давление) работоспособности маслонасоса, механизм автоматического переключения на резервный маслонасос в случаеаварийнойостановкиосновного, трубыишлангимаслопроводов.
Система самодиагностики и сигнализации обеспечивает снятие необходимых параметров со всех датчиков всех узлов и механизмов,
43
диагностирует приближение критических режимов, передает необходимую информацию в систему управления, автоматически принимает экстренные контраварийные меры в случае бездействия экипажа (аварийное отключение электроэнергии, сверхнормативная нагрузка на рабочее оборудование, превышение безопасных углов наклона экскаватора, превышение лимитов ресурса узлов до ППР, КР, неисправность системы смазки, неисправность тормозной системы, превышение предельной температуры масла в системе смазки и воздуха в технологических отсеках), обеспечивает автоматическое выравнивание нагрузки на ходовое оборудование (управление домкратами качалок независимой подвески гусеничных тележек) во время копания.
Тормозная система экскаватора гидроэлектрическая. Тормозными механизмами (ремень с асбестовыми накладками по стальному барабану в масляной ванне) оборудованы все механические толкатели, редукторы поворота, хода (правый, левый), ротора (в случае роторного комплекса), тяговый и подъемный (в случае драглайна), приводного барабана (в случае конвейерного перегружателя). Тормозные механизмы «безремонтные», т.е. их ресурс рассчитан на весь срок службы экскаватора. Исполнительные механизмы системы торможения – серийные крановые электрогидротолкатели, имеющие встроенную систему автоматической блокировки при аварийном отключении электропитания.
Система вентиляции обеспечивает создание и поддержание заданной температуры и чистоты воздуха в технологических отсеках, а также кабине экскаватора.
Система балансировки и развесовки обеспечивает снятие параметров с датчиков нагрузки, автоматическое управление механическими толкателями качалок гусеничных тележек с целью выравнивания нагрузок, рассчитывает и передает в систему управления положение центра тяжести экскаватора относительно безопасной зоны.
Система бортовых грузоподъёмных приспособлений позволяет производить замену двигателей всех приводов, демонтаж и монтаж всех редукторов без привлечения специальной техники.
Семейство экскаваторов на базе УП КТМ-400 включает в себя все основные типы горных экскаваторов – прямую и обратную лопату, экскаватор-погрузчик с подвижным ковшом (рис. 1.15), драглайн. Экскаваторы этого семейства разрабатывались с учетом сложившейся за долгие годы практики и технологии добычи в первую очередь на территории стран бывшего СССР.
44
Базовая модификация платформы КТМ-405Т – прямая механическая лопата (рис. 1.16) с базовым ковшом 5 м, по основным параметрам копания аналогична самому распространенному на этой территории экскаватору типа ЭКГ-5. При этом она обладает значительно превосходящими ЭКГ-5 остальными параметрами и имеет уникальные дополнительные свойства, ранее никогда не использовавшиеся в области экскаваторостроения.
Предполагая, что экскаваторы КТМ могут быть использованы вне сложившейся технологии добычи (на складах, для перегрузки, на вновь формируемых участках добычи), специалисты «Крастяжмаша» разработали модификации с уменьшенным радиусом копания и увеличенным объемом ковша (7–10–12 м3, при удельной массе породы 2,2 т на 1 м3 и до 18 м3 при 0,9 т на 1 м3), экскаваторы с подвижным ковшом (5–8–12 м3) для селективной выемки, отработки наклонных пластов, обратную лопату, а также экскаватор-драглайн (рис. 1.17) и роторный комплекс (табл. 1.13).
Одним из узких мест традиционных схем открытой разработки твердых полезных ископаемых является жесткая зависимость высоты разрабатываемого уступа от линейных параметров карьерных экскаваторов. Это обстоятельство ограничивает высоту уступа – основного элемента транспортной системы разработки – в пределах 10–15 м, величина которой практически не меняется вот уже 30–40 лет, тогда как глубина разрезов увеличилась в 3–4 раза, вместимость ковшей карьерных экскаваторов увеличилась до 15–20 м3 и более, а объемы разрабатываемой горной массы возросли в 4–5 раз. В результате этого на разрезе работает мощная техника на небольших уступах. Так, например, на разрезе «Нерюнгринский» отработка вскрышных пород на глубину 300 м ведется уступами высотой 15 м с использованием экскаваторов ЭКГ-20. В рабочей зоне находится до 20 уступов, имеет место выполаживание рабочего борта до 15–16о. Общая длина фронта работ породных уступов превышает 50–60 км. Это приводит:
к необходимости выполнения дополнительного большого объема вскрышных работ;
низкому коэффициенту использования карьерных экскаваторов; снижению эффективности во всех звеньях горного производства – на экскавационных работах, транспортных, буровзрывных,
вспомогательных.
45
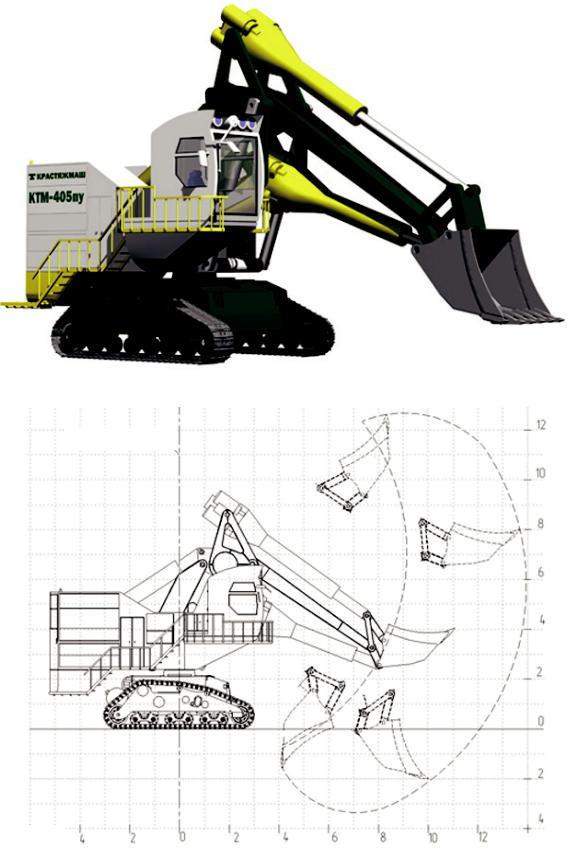
а
Высота, м
Ось вращения
Расстояние, м
б
Рис. 1.15. Внешний вид (а) и траектории копания (б) экскаватора КТМ-405ПУ
46
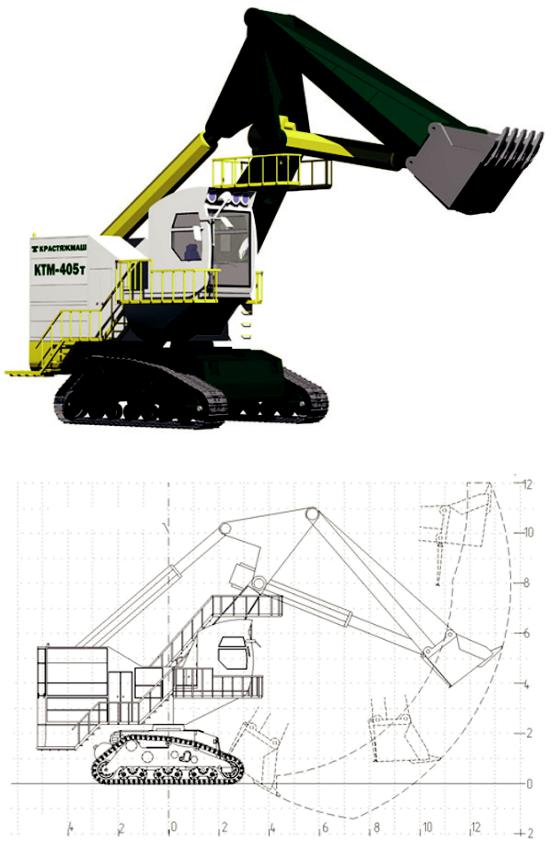
а
Высота, м
Ось вращения
Расстояние, м
б
Рис. 1.16. Внешний вид (а) и траектории копания (б) экскаватора КТМ-405Т
47
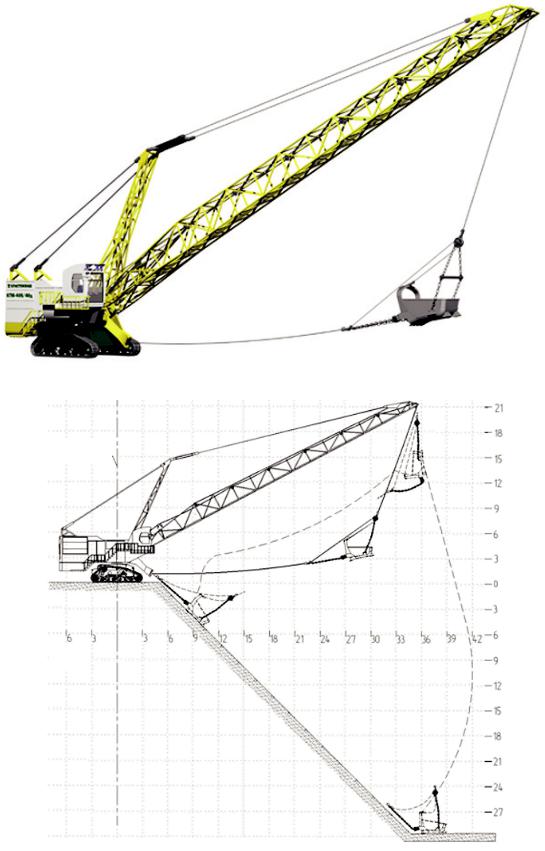
а
Расстояние, м
Ось вращения
Расстояние, м
б
Рис. 1.17. Внешний вид (а) и траектории копания (б) экскаватора КТМ-405/40Д
48
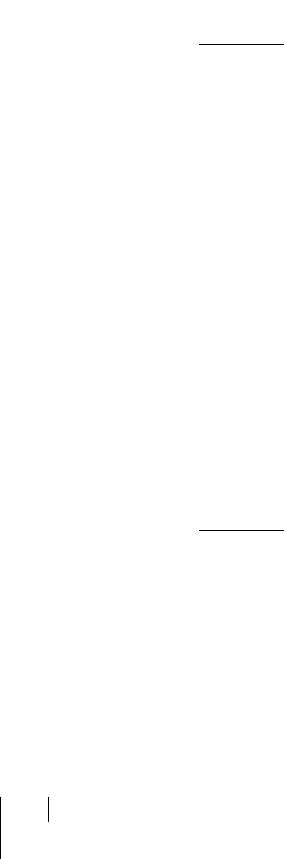
Таблица 1.13. Технологические параметры экскаваторов
|
|
на базе универсальной платформы КТМ-400 |
|
||||||||
|
|
|
|
|
|
|
|
|
|
|
|
Параметр |
|
КТМ- |
КТМ- |
КТМ- |
КТМ- |
КТМ- |
КТМ- |
КТМ-405О |
КТМ- |
||
|
405Т |
407Т |
410ТТ |
412ТТ |
405ПУ |
408П |
405/40Д |
||||
Вместимость сменно- |
|
|
|
|
|
|
|
|
|
||
го ковша, м3, при за- |
|
|
|
|
|
|
|
|
|
||
данной массе породы: |
5 |
7 |
|
10 |
12 |
5 |
8 |
5 |
|
||
2,2 т/м3 |
|
|
|
|
|||||||
1,7 т/м3 |
|
|
6 |
8 |
|
11 |
14 |
6 |
9 |
6 |
|
1,1 т/м3 |
|
|
8 |
10 |
|
12,5 |
16 |
8 |
11 |
8 |
|
0,9 т/м3 |
|
|
10 |
12 |
|
14 |
18 |
10 |
12 |
10 |
|
Тип рабочего обору- |
Прямая механическая |
Погрузчик – |
Погрузчик – |
Драг- |
|||||||
дования |
|
|
|
лопата |
|
прямая лопата |
обратная |
лайн |
|||
|
|
|
|
|
|
|
|
|
|
лопата |
|
Ширина базового |
2,5 |
2,8 |
|
3 |
3,5 |
2,5 |
2,8 |
2,5 |
|
||
ковша, м |
|
|
|
|
|||||||
|
|
|
|
|
|
|
|
|
|
|
|
Максимальный |
ради- |
|
|
|
|
|
|
|
|
|
|
ус, м: |
|
|
|
|
|
|
|
|
|
|
|
черпания |
|
14 |
12 |
|
14 |
12 |
14 |
12 |
14 |
35 |
|
разгрузки при мак- |
12 |
10 |
|
12 |
11 |
10 |
9 |
|
32 |
||
симальной высоте |
|
|
|||||||||
Максимальная |
высо- |
|
|
|
|
|
|
|
|
|
|
та, м: |
|
|
12 |
11 |
|
12 |
11 |
12 |
11 |
10 |
4 |
копанияэффективная |
|
||||||||||
разгрузки |
|
|
|
7 |
|
9 |
8 |
|
32 |
||
Максимальная глуби- |
|
|
|
|
|
|
|
|
|
||
на черпания ниже |
–1,4 |
–1 |
|
–1,4 |
–1 |
–3,4 |
–2,4 |
–6 |
–30 |
||
уровня стояния, м |
|
|
|
|
|
|
|
|
|
||
Расчетная |
продолжи- |
19 |
|
21 |
26 |
|
19 |
|
45 |
||
тельность цикла, с |
|
|
|
||||||||
|
|
|
|
|
|
|
|
|
|||
Скорость |
передвиже- |
|
|
|
|
|
|
|
|
|
|
ния по ровной по- |
|
|
|
|
|
2 000 |
|
|
|
||
верхности, м/ч, до |
|
|
|
|
|
|
|
|
|
||
Единичная |
мощность |
|
|
|
|
|
|
|
|
|
|
примененного электро- |
|
|
55 / ПЧ (с преобразователем частоты) |
|
|||||||
двигателя, кВт / тип |
|
|
|
|
|
|
|
|
|
||
Мощность |
привода, |
|
|
|
|
|
|
|
|
|
|
кВт (количество элек- |
|
|
|
|
|
|
|
|
|
||
тродвигателей, шт.): |
|
|
|
|
|
|
|
|
|
||
хода |
|
|
|
|
|
|
|
220 (4) |
|
|
|
поворота |
|
|
|
|
|
|
220 (4) |
|
|
|
|
|
|
|
|
|
|
||||||
подъема |
|
220 (4) |
275 (5)330 (6)385 (7) |
330 (6) |
385 (7) |
330 (6) |
110 (2) |
||||
напора тяговой ле- |
110 (2) |
165 (3) |
|
220 (4) |
|
||||||
бедки для драглайна |
|
|
|||||||||
|
|
|
|
|
|
|
|
|
49

Окончание табл. 1.13 |
|
|
|
|
|
|
|
|
|
|
|
|||||
|
|
|
|
|
|
|
|
|
|
|
|
|
||||
Параметр |
|
КТМ- |
КТМ- |
КТМ- |
КТМ- |
КТМ- |
КТМ- |
КТМ-405О |
КТМ- |
|||||||
|
|
|
|
405Т |
|
407Т |
410ТТ |
412ТТ |
405ПУ |
408П |
|
405/40Д |
||||
Номинальная |
|
мощ- |
|
|
|
|
|
|
|
|
|
|
|
|
|
|
ность |
трансформато- |
|
|
250 |
|
|
|
|
400 |
350 |
400 |
300 |
||||
ра, кВт |
|
|
|
|
|
|
|
|
|
|
|
|
|
|
|
|
Максимальнаясила, тс: |
|
|
|
|
|
|
|
|
|
|
|
|
|
|||
взлома |
|
|
|
|
0 |
|
|
|
|
|
30 |
|
|
|||
подачи вперед |
|
25 |
|
|
|
|
35 |
|
|
|
40 |
35 |
|
|||
|
|
|
|
|
|
|
|
|
|
|
|
|
|
|
|
|
Усилие |
на |
зубьях |
35 |
|
45 |
|
50 |
|
|
|
40 |
|
|
|||
ковша, тс |
|
|
|
|
|
|
|
|
|
|||||||
|
|
|
|
|
|
|
|
|
|
|
|
|
|
|
||
Тип привода рабочего |
|
|
|
|
|
|
МТ |
|
|
|
Канат |
|||||
оборудования |
|
|
|
|
|
|
|
|
|
|
|
|||||
|
|
|
|
|
|
|
|
|
|
|
|
|
|
|
||
Длина кабеля в бара- |
|
|
|
|
|
|
|
|
|
300 |
|
|
|
|||
бане, м |
|
|
|
|
|
|
|
|
|
|
|
|
|
|
|
|
|
|
|
|
|
|
|
|
|
|
|
|
|
|
|
|
|
Количество |
опорных |
|
|
|
|
|
|
|
|
|
|
|
|
|
||
катков |
/ количество |
|
|
|
|
|
|
|
|
|
6/3 |
|
|
|
||
балансиров |
|
|
|
|
|
|
|
|
|
|
|
|
|
|
|
|
Напряжение |
питаю- |
|
|
|
|
|
|
|
|
|
6 |
|
|
|
||
щей сети, кВ |
|
|
|
|
|
|
|
|
|
|
|
|
|
|
||
|
|
|
|
|
|
|
|
|
|
|
|
|
|
|
||
Возможность |
приме- |
|
|
|
|
|
|
|
|
|
|
|
|
|
||
нения встроенного ди- |
|
|
|
|
|
|
|
|
|
Есть |
|
|
|
|||
зельного генератора |
|
|
|
|
|
|
|
|
|
|
|
|
|
|||
Масса рабочая, т |
|
120 |
|
135 |
|
140 |
|
|
125 |
135 |
125 |
160 |
||||
|
|
|
|
|
|
|
|
|
|
|
|
|
|
|||
Удельное давление на |
|
|
|
|
|
|
|
|
|
|
|
|
|
|||
грунт, кг/см2, при ши- |
|
|
|
|
|
|
|
|
|
|
|
|
|
|||
рине башмака |
гусе- |
|
|
|
|
|
|
|
|
|
|
|
|
|
||
ничной ленты: |
|
|
|
|
|
|
|
|
|
|
|
|
|
|
||
700 мм |
|
|
1,7 |
|
1,85 |
|
2 |
|
|
1,8 |
1,9 |
1,8 |
2,3 |
|||
800 мм |
|
|
1,5 |
|
1,64 |
|
1,75 |
|
|
1,56 |
1,7 |
1,56 |
2 |
|||
900 мм |
|
|
1,3 |
|
1,45 |
|
1,55 |
|
|
1,4 |
1,5 |
1,4 |
1,8 |
|||
Количество ТМ |
|
|
|
4 |
|
|
|
5 |
|
|
4 |
5 |
4 |
6 |
||
|
|
|
|
|
|
|
|
|
|
|
|
|
|
|||
Время сборки / разбор- |
|
|
|
|
|
|
|
|
|
|
|
|
|
|||
ки бригадой из 5 чел., |
|
|
|
|
|
|
|
|
|
3 |
|
|
|
|||
рабочихсменпо8 ч |
|
|
|
|
|
|
|
|
|
|
|
|
|
За последние 25–30 лет железорудные карьеры Кривбасса также углубились до 250–300 м. При этом высота уступа практически осталась прежней.
Попытки увеличить высоту уступов при транспортной системе разработки ограничивались следующим правилом: высота уступа не должна быть больше высоты черпания экскаватора.
50
В Институте проблем комплексного освоения недр Российской академии наук (ИПКОН РАН) и ФГУП «Национальный научный центр горного производства “Институт горного дела им. А. А. Скочинского”» (ФГУП ННЦ ГП ИГД им. А.А. Скочинского) [7] были выполнены НИР, в результате которых был предложен и разработан новый экскаватор-кранлайн с нижним черпанием и погрузкой горной массы ковшом с гибкой связью в транспорт на уровне своего стояния (рис. 1.18). При использовании этого экскаватора высота уступа может быть увеличена до 30–40 м.
Отличительной особенностью предложенного экскаватора от традиционных является то, что он имеет преимущество драглайна осуществлять выемку уступов нижним черпанием и преимущество мехлопаты осуществлять точную и безударную погрузку горной массы в транспортные средства.
Это удалось решить за счет применения двух дополнительных блоков канатов, установленных в средней части конструкции укороченной стрелы с целью фиксации ковша перед разгрузкой вблизи от кабины машиниста. Причем эти два блока расположены под углом 7–8о друг к другу, образуя V-образную связку с ковшом, и обеспечивают снижение поперечных колебаний ковша. Для этого применена дополнительная третья лебедка, котораянаходитсянаповоротнойплатформеэкскаватора.
При расположении ковша над транспортным средством в любой точке по его площади он, при полностью расслабленном тяговом канате лебедки, удерживается посредством подъемных канатов и каната лебедки его заброса и может быть опущен непосредственно в кузов транспортного средства для разгрузки.
Снабжение кранлайна отклоняющими блоками канатов подъемной лебедки, которые находятся у пяты стрелы, обеспечивает избирательность установки ковша над транспортным средством во время разгрузки. Расположение блока каната заброса ковша в концевой части стрелы уменьшает грузовой момент стрелы и этим ее металлоемкость и инертность, а также исключает возможность возникновения в канатах недопустимых усилий «растяжки». Данная конструкция существенно сокращает время цикла за счет уменьшения угла поворота и снижения инерционности экскаватора.
Исследования показали, что отработка высокими (до 30 м) уступами с использованием кранлайнов обеспечивает важные экономические преимущества по сравнению с традиционной технологией отработки 15-метровыми уступами:
51
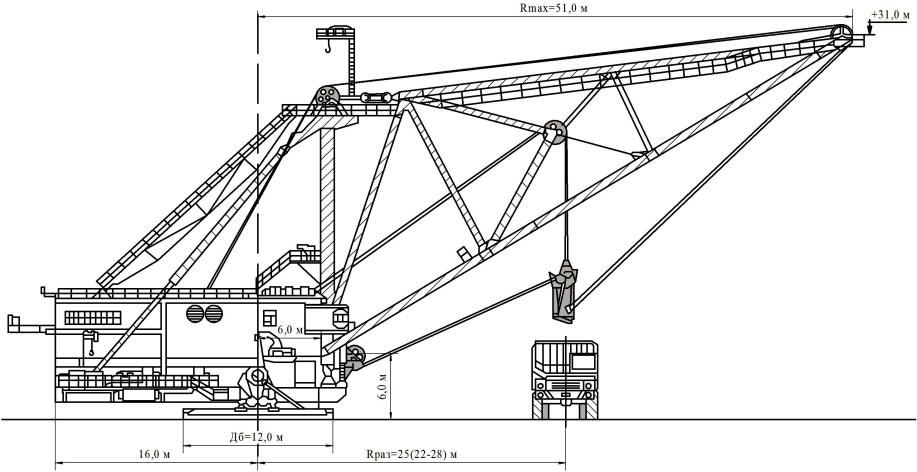
Рис. 1.18. Конструктивная схема экскаватора-кранлайна ДШП-20.50
52
увеличивается генеральный угол рабочего борта карьера, что позволяет снизить объемы вскрышных и вспомогательных работ;
сокращается количество уступов и транспортных горизонтов на карьере, что приводит к уменьшению длины транспортных коммуникаций и дальности транспортирования экскавируемой горной массы, а также уменьшению объемов путевых работ;
увеличивается производительность буровых станков из-за уменьшения времени на их переезды от скважины к скважине и улучшения их обслуживания и ремонта;
сокращается объем буровых работ за счет увеличения расстояния между скважинами и уменьшения объема перебуров;
повышается выход горной массы с одного погонного метра скважины;
сокращается количество взрывов в течение года, в целом уменьшаются затраты на буровые и взрывные работы;
повышается надежность электроснабжения и долговечность приключательных пунктов и питающих кабелей в 1,4–1,7 раза, а следовательно, сокращается потребность в указанных изделиях;
уменьшаются размеры территорий, отторгаемых открытыми разработками.
Развитие добычных комплексов, описанных выше, получило в работах Сибирского федерального университета [2]. Исходя из общей концепции ресурсосбережения, а также необходимости быстрого реагирования на изменение конъюнктуры рынка углепродукции и повышения конкурентоспособности получаемого углепродукта, к добывающему и перерабатывающему горному оборудованию выдвигаются следующие требования: оно должно базироваться на модульноблочном принципе построения и быть мобильным.
Учитывая особенности карьерного фонда, изобилующего разрезами малой и средней мощности, а также то, что на разрезах с большой производственной мощностью имеются пласты-спутники, которые в настоящее время ввиду несовершенства технологии зачастую отрабатываются в отвал, весьма перспективным становится более широкое применение мобильных экскаваторов фрезерного и фре- зерно-ковшового типа СМ, КСМ, КГФ и др.
Опыт эксплуатации экскаватора КСМ-2000РМ на разрезе «Талдинский» показал, что эти машины можно применять как на вскрышных, так и на добычных работах, а главное, они обеспечивают полноту выемки полезного ископаемого. Поэтому предлагается использо-
53
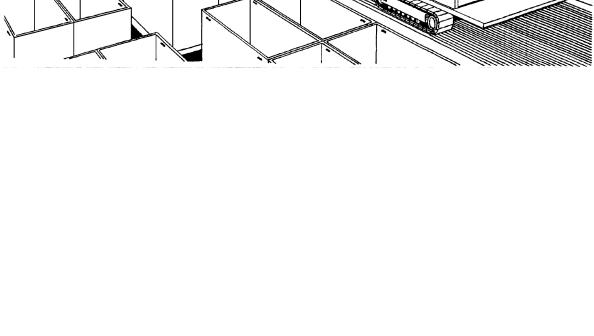
вать экскаватор типа КСМ вместе с другими горными машинами в составе горного комплекса-комбината (ГКК) по добыче и переработке угля.
На рис. 1.19 изображен экскаватор 1 типа СМ, работающий в технологической цепочке с мобильным сепарационно-сортировочным агрегатом 2 и мобильным упаковочно-брикетным комплексом (УБК) 3. Сортовой уголь и продукты углепереработки, в данном случае брикеты, отгружаются в контейнеры 4. Исходя из специфики конкретных разрезов и требований рынка возможно дополнительное включение или замена одного мобильного перерабатывающего оборудования на другое. Например, дополнительно к УБК можно разместить установку по производству сорбентов или при отработке некондиционных и сажистых углей в технологическую цепочку вместо УБК включить оборудование по микробиологической трансформации угля с получением гумусосодержащей суспензии в качестве компонента удобрения обедненных малогумусных почв.
4 |
|
1 |
|
2 |
|
3 |
Рис. 1.19. Комплекс карьерного горного оборудования в забое
Главными условиями использования ГКК являются мощность карьера и производительность участка, блока.
Показанная на рис. 1.19 технологическая цепочка лишь схема. Конечно, не на каждом разрезе горно-геологические условия дают
54
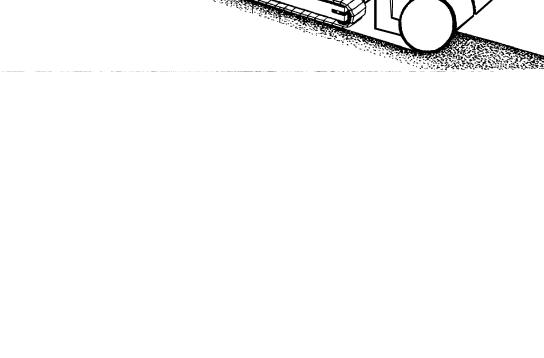
возможность разместить вслед за экскаватором шлейф перерабатывающего оборудования.
Однако, во-первых, перерабатывающее оборудование на мобильном шасси можно устанавливать вблизи добычного участка, связывая его с экскаватором внутрикарьерным транспортом, например межуступным перегружателем, и перемещать это мобильное оборудование по мере продвижения фронта работ. Это для малых разрезов будет выгоднее строительства стационарных перерабатывающих заводов ввиду больших затрат на капитальное строительство, высоких транспортных издержек, к тому же возможно изменение спроса на продукцию завода, что повышает коммерческий риск такого предложения.
|
|
|
|
|
|
|
|
|
4 |
5 |
3 |
2 |
1 |
Рис. 1.20. Горный карьерный комплекс для экскавации угля с получением высококачественных углепродуктов
Во-вторых, компактность и относительно малая материалоемкость экскаваторов фрезерного и фрезерно-ковшового типа могут послужить основой для создания ГКК по добыче и переработке угля на одном шасси.
На рис. 1.20 представлен вариант ГКК по добыче и переработке угля, который включает в себя экскавационное оборудование 1, сортировочный блок 2, блок брикетирования 3, грузоподъемное оборудо-
55