
sbornik2011.pdf (страница 353) Скоромолов И.О
..pdf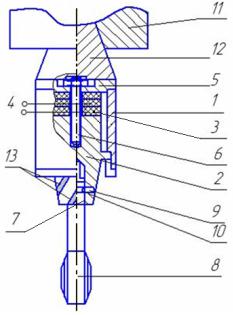
формируемые показатели качества поверхностного слоя резьбы, к которым относятся шероховатость, степень и глубина деформационного упрочнения, величина и знак остаточных напряжений и другие показатели, которые в существенной степени зависят от условий и характеристик процесса ультразвукового нарезания резьбы [2].
Как известно, основная работа при резании металла определяется пластической деформацией срезаемого слоя и внешним трением на рабочих гранях инструмента [3], а дополнительные ультразвуковые колебания, сообщаемые резьбонарезающему инструменту, оказывают влияние, как на пластическую деформацию материала, так и на величину внешнего трения. Процесс нарезания резьбы метчиком складывается из вращательного движения вокруг оси и поступательного движения вдоль оси, в связи с чем оптимальным было бы сообщение дополнительных ультразвуковых колебательных движений в тех же направлениях. Авторами разработано и изготовлено патентнозащищенное устройство [4] для наложения одновременно продольных и крутильных колебаний на метчик при нарезании резьбы, что способствует повышению эффективности ультразвукового воздействия.
Устройство для наложения ультразвуковых колебаний при нарезании резьбы изображено на рис. 1 (продольный разрез).
Рис.1 Устройство для наложения ультразвуковых колебаний при нарезании резьбы
Устройство для наложения ультразвуковых колебаний при нарезании резьбы содержит расположенный в корпусе 1 излучатель 2 ультразвуковых колебаний, представляющий собой концентратор механических колебаний, который одним торцом контактирует с пьезопреобразователем 3. Ультразвуковой преобразователь изготовлен из 4 пластин пьезокерамики осевой поляризации ЦТС-19 диаметром 60 мм, которые механически соединены последовательно, а электрически – параллельно. Пластины
100
пьезопреобразователя подключены к источнику питания 4, представляющего собой генератор электрических колебаний (на рисунке не показан) и плотно прижимаются крышкой 5 к излучателю. С помощью резьбовой шпильки 6 излучатель ультразвуковых колебаний, пьезопреобразователь и крышка соединены между собой. В другом торце излучателя 2 ультразвуковых колебаний выполнено глухое отверстие 7, расположенное в центре и предназначенное для размещения режущего инструмента 8, в частности, метчика. Метчик закрепляется в глухом отверстии помощью крепёжного элемента 9, например, винта, размещенного в отверстии 10, которое расположено перпендикулярно отверстию 7. Устройство устанавливается в патрон 11 станка посредством конуса Морзе 12. Смазочно-охлаждающая жидкость подается при обработке свободно падающей струёй или окунанием. Предлагаемое устройство работает следующим образом: в процессе нарезания резьбы электрические колебания ультразвуковой частоты источника питания преобразуются с помощью пьезопреобразователей 3 в упругие механические колебания. Ввиду того, что излучатель выполнен в виде конуса с пазами, то за счет наклонных кольцевых пазов 13 возникают дополнительные крутильные колебания, которые в совокупности с продольными колебаниями усиливают воздействие на метчик. В смазочноохлаждающей жидкости, проникшей в зазор между метчиком 8 и заготовкой (на чертеже не показана), возникают высокие мгновенные давления. Происходит образование и колебание газовых пузырьков, ударных волн, вызывающих макро- и микропотоки смазочно-охлаждающей жидкости, что позволяет смазочно-охлаждающей жидкости глубже проникать в отверстие обрабатываемой заготовки. При этом происходит снижение коэффициента трения между контактирующими в процессе резания объектами, улучшаются условия работы метчика, облегчается выход стружки, уменьшается температура в зоне резания.
На рис. 2 представлен экспериментальный образец устройства для наложения ультразвуковых колебаний при нарезании резьбы.
По результатам проведенных экспериментальных исследований ультразвукового нарезания резьбы крутящий момент уменьшился на 25–35%, производительность повысилась примерно в 2 раза, улучшилась чистота поверхности профиля резьбы. В ходе эксперимента нарезались, сквозные и глухие резьбы М10х1,5 в гайках и заготовках из стали 12Х18Н9Т и титанового сплава ВТ16. Метчику сообщались ультразвуковые колебания частотой 18–20 кГц и амплитудой 5–15 микрометров (в зависимости от требований технологического режима).
Таким образом, разработанное устройство за счет совместного воздействия продольных и крутильных колебаний, накладываемых на основные движения, позволяет расширить область применения и повысить эффективность ультразвукового воздействия при нарезании резьбы метчиками. Устройство может быть использовано для нарезания резьб как в ручном инструменте, так и в станках.
101
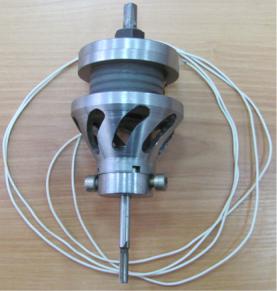
Рис. 2 Экспериментальный образец устройства для наложения ультразвуковых колебаний при нарезании резьбы
Литература
1. Марков, А.И. Ультразвуковая обработка материалов / А.И. Марков. – М.: Машиностроение, 1980. – 237 с.
2. Нерубай, М.С. Физико-химические методы обработки и сборки / М.С. Нерубай, В.В. Калашников, Б.Л. Штриков, С.И. Яресько. – М: Машиностроение-1, 2005. – 396 с.
3.Штриков, Б.Л., Повышение работоспособности резьбовых соединений путем применения ультразвука при обработке и сборке / Б.Л. Штриков, В.В. Головкин, В.Г. Шуваев, И.В. Шуваев – М.: Машиностроение-1, 2009.
– 137 с.
4.Патент РФ на полезную модель № 93323 МПК В25В 21/00 Устройство для наложения ультразвуковых колебаний при нарезании резьбы / Шуваев В.Г., Папшев В.А., Баев И.И. Опубликован 27.04.2010. Бюл. № 12.
М.А. Самсонов
ФОРМИРОВАНИЕ СЛОЖНОГО КОЛЕБАТЕЛЬНОГО ДВИЖЕНИЯ
РАБОЧЕГО ОРГАНА ДЛЯ ПОЗИЦИОНИРОВАНИЯ ДЕТАЛЕЙ ПРИ
АВТОМАТИЗИРОВАННОЙ СБОРКЕ
Самарскийгосударственныйтехническийуниверситет,г.Самара sgtu_vibro@mail.ru
Применение промышленных роботов при автоматизации сборочных операций сдерживается в настоящее время в связи со сложностью разработки и реализации: во-первых – алгоритмов пространственного ориентирования, во-вторых – условий начального контактирования и захода собираемых
102
деталей, что в реальных процессах сборки приводит к «закусыванию» деталей и необходимости повторного ориентирования и сопряжения деталей.
Одним из путей повышения производительности и расширения технологических возможностей за счет обеспечения пространственного относительного ориентирования собираемых деталей и увеличения скорости сборки является введение ультразвуковых колебаний в сборочный процесс. В работах [1, 2] используются возможности ультразвука для получения поискового движения при сборке прессовых соединений. Для автоматизации процессов сборки деталей типа «вал-втулка» с помощью манипуляторов и промышленных роботов разработано устройство [1], осуществляющее автоматическое позиционирование собираемых деталей за счет формирования сложного колебательного движения рабочего органа.
На рис. 1 представлено устройство для сообщения колебательных движений собираемым деталям, которое содержит рабочий орган 1 и соединенную с ним пружину 2, выполненную в виде спирали Архимеда. Второй конец пружины посредством пьезокерамического привода 4 колебательного движения закреплен на корпусе 3.
При подаче напряжения питания на обкладки пьезокерамического привода 4 колебательного движения он, вследствие обратного пьезоэффекта, изменяет свои геометрические размеры и возбуждает в спиральной пружине 2 с закрепленным рабочим органом 1 механические колебания. Траектория возбуждаемых в рабочем органе колебаний имеют сложный характер, что определяется особенностями взаимодействия привода 4 колебательного движения и пружины 2 в виде спирали Архимеда. Так как привод установлен в плоскости спиральной пружины, то в ней возбуждается, во-первых, упругая волна продольных колебаний, формирующая амплитуду колебаний рабочего органа 1 в направлении, совпадающим с касательной в точке крепления рабочего органа к спиральной пружине (по оси ординат). Во-вторых, в силу спирального выполнения пружины в ней формируется изгибная волна колебаний с пучностью в месте крепления рабочего к спиральной пружине. Изгибная волна вызывает колебания рабочего органа в направлении, перпендикулярном обеспечиваемому продольной волной (по оси ординат).
Так как оба типа колебаний имеют одну частоту, а именно частоту колебательной системы, образованной рабочим органом, спиральной пружиной и приводом колебательного движения, то сложение амплитуд этих колебаний с взаимно перпендикулярными векторами вызывает, в общем случае, эллипсную траекторию движения рабочего органа. Эллипсность траектории движения обусловлена различием амплитуд колебаний (величина амплитуды изгибных колебаний в данном случае будет больше амплитуды колебаний, формируемой продольной волной).
Впродольных волнах движение происходит симметрично оси стержня
ипреобладает осевая (продольная) компонента смещения. В изгибных волнах ось стержня претерпевает изгиб и преобладает поперечная компонента смещения.
103

Рис. 1 Устройство для сообщения колебательных движений собираемым деталям
Изгибные волны представляют собой деформации изгиба, распространяющиеся в стержнях и пластинах. В стержне направлением распространения волны является его ось. При распространении изгибных волн каждый элемент стержня смещается перпендикулярно оси стержня. Изгибные волны малых амплитуд в стержне описываются следующими уравнениями [4]:
|
2u |
ER |
2 |
4u |
0, |
|
t |
2 |
|
z4 |
|||
|
|
|
|
где - плотность материала стержня, t- время, z- координата вдоль оси стержня, u- смещение элементов стержня, E- модуль Юнга, R- радиус инерции поперечного сечения стержня относительно оси, перпендикулярной плоскости изгиба и проходящей через нейтральную поверхность.
Фазовая скорость изгибной волны частоты в стержне равна
сизг 4ER2 /
.
Эта скорость много меньше фазовой скорости продольных волн в стержне. Фазовая скорость распространения продольных колебаний
определяется соотношением спр E/ .
Так как скорость распространения продольной волны в металлах почти в два раза выше скорости распространения изгибной волны, то возникающий
104
фазовый сдвиг (набег) приводит к вращению эллипсной траектории движения рабочего органа, за счет чего осуществляется автоматический поиск сопрягаемых деталей. При выключении напряжения питания привода 4 колебательного движения колебания спиральной пружины будут экспоненциально затухать, и траектория движения рабочего органа примет форму сходящейся спирали, что дает возможность автоматически осуществить центровку сопрягаемых деталей.
Литература
1.Бакшис, Б.П. Вибрационное позиционирование при автоматической сборке / Б.П. Бакшис, А-Б.Б. Повиленис, И.Ю. Скучас // Автоматизация сборочных процессов. – Рига: – 1987, №14. – С53–60.
2.Бакшис, Б.П. Вибрационное перемещение и автоматическая сборка с помощью стоячей упругой волны / Б.П. Бакшис, А-Б.Б. Повиленис, И.Ю. Скучас // Автоматизация сборочных процессов. – Рига: 1988, №15. – С42–49.
3.А.с. СССР № 1804994, 30.03.93. Бюл. № 12, Устройство для сообщения колебательного движения собираемым деталям / Колокольцев В.М., Шуваев В.Г.
4.Ультразвук. Маленькая энциклопедия. Глав. ред. И.П. Голямина. – М.: «Советская энциклопедия», 1979. – 400 с.
5.Машиностроение. Энциклопедия / Ред. совет: К.В. Фролов (пред.) и др. М.: Машиностроение. Технология сборки в машиностроении. Т.III-5 / А.А. Гусев, В.В. Павлов, А.Г. Андреев и др.; Под общ. ред. Ю.М. Соломенцева. – 2006. 640 с.
А.К. Стрелков, О.А. Силкина
О ЦЕЛЕСООБРАЗНОСТИ ПРИМЕНЕНИЯ РЕЗЕРВУАРОВ
УСРЕДНИТЕЛЕЙ В СОСТАВЕ КАНАЛИЗАЦИОННЫХ ОЧИСТНЫХ
СООРУЖЕНИЙ МАЛОЙ ПРОИЗВОДИТЕЛЬНОСТИ
Научный руководитель: А.К. Стрелков, д.т.н., профессор
Самарский государственный архитектурно-строительный университет, г. Самара
На канализационных очистных сооружениях, в особенности небольшой производительности, наблюдается неравномерное поступление сточных вод. Как правило, сточные воды поступают в приемную камеру очистных сооружений от канализационной насосной станции, при этом приток сточных вод цикличный и зависит от емкости приемного резервуара на насосной станции и производительности насосов.
105
Неравномерное поступление сточных вод на очистные сооружения влияет на качество очистки как на сооружениях механической очистки (песколовки, первичные отстойники), так и на сооружения биологической очистки (аэротенки, вторичные отстойники). При неравномерной подаче сточных вод завышается размер сооружений, т.к. они рассчитываются не на средний расход, а на максимальный. Так, например, на станции производительностью 100 м3 /сут., средний расход составит 4,16 м3 /час, а максимальный расход будет равен 10,42 м3 /час, т.е. завышение объемов сооружений будет в 2,5 раза. Аналогично для очистных сооружений производительностью 1000 м3 /сут. – равномерный расход будет 41,66 м3 /час, а максимальный расход - 87,5 м3 /час, что в 2,1 раза выше.
Введение в состав сооружений резервуара усреднителя как по количеству, так и по качеству позволяет обеспечить бесперебойную и качественную очистку сточных вод. Емкость резервуара усреднителя определяется по графику притока и откачки сточных вод.
Литература
1.СНиП 2.04.03-85. Строительные нормы и правила. Канализация. Наружные сети и сооружения. - М.: ЦИТП, 1968. – 72с.
2.Яковлев С.В., Воронов Ю.В. Водоотведение и очистка сточных вод / Учебник для вузов. М.: АСВ, 2002. 704 с.
3.Яковлев С.В., Карелин Я.А., Ласков Ю.М., Калицун В.И. Водоотведение и очистка сточных вод: Учебник для вузов. - М.: Стройиздат, 1996. - 591 с.
А.И. Хлыстов, Ю.В. Медведев, А.Е. Божок, Н.Н. Кучер
НОВЫЕ ЭФФЕКТИВНЫЕ ЖАРОСТОЙКИЕ МАТЕРИАЛЫ НА БАЗЕ
ОТХОДОВ ПРОМЫШЛЕННОСТИ САМАРСКОЙ ОБЛАСТИ ДЛЯ
ФУТЕРОВОК ТЕПЛОВЫХ АГРЕГАТОВ
Научный руководитель: А.И. Хлыстов, д.т.н., профессор
Самарский государственный архитектурно-строительный университет, г. Самара
stepstolb@mail.ru
Общим направлением технического прогресса в строительстве является широкое применение новых видов материалов и изделий, снижение материалоёмкости, обеспечение индустриализации и механизации строительства, повышение эксплуатационных свойств изделий и конструкций, использование для изготовления строительных материалов отходов промышленности.
В настоящее время футеровка тепловых агрегатов выполняется преимущественно из различных огнеупорных изделий, что требует больших
106

затрат ручного труда и не обеспечивает высокого качества. Слабым местом любой футеровки являются швы между штучными огнеупорами. Особенно сильно это явление наблюдается в металлургических, нагревательных, термических печах, где имеются расплавы металлов, флюсов и другие агрессивные среды, которые, проникая в швы, очень быстро выводят футеровку из строя. Поэтому в последнее время для футеровки различных тепловых агрегатов применяют крупноблочные элементы из жаростойких бетонов, использование которых позволяет свести до минимума количество швов, повысить стойкость и увеличить срок службы футеровки [1].
Жаростойкий бетон - это специальный бетон, способный не изменять требуемые физико-механические свойства при длительном воздействии высокой температуры (свыше 200°С). В зависимости от вяжущего вещества различают жаростойкие бетоны на портландцементе и шлакопортландцементе, на высокоглиноземистом и глиноземистом цементе и на жидком стекле.
, МПа |
60 |
|
|
|
сжатии |
50 |
|
|
|
|
|
|
|
|
при |
40 |
|
|
1 |
30 |
|
|
2 |
|
прочности |
|
|
||
|
|
3 |
||
20 |
|
|
||
|
|
|
||
|
|
|
4 |
|
|
|
|
|
|
Предел |
10 |
|
|
|
0 |
500 |
1000 |
1500 |
|
|
0 |
|||
|
|
Температура , С |
|
Рис. 1 Зависимость прочности на сжатие жаростойких бетонов от температуры нагрева и вида вяжущего
1-ПЦ+огнеупорная тонкомолотая добавка; 2-высокоглинозёмистый цемент; 3-жидкое стекло; 4-фосфатные связующие
Любая футеровка теплового агрегата состоит из двух частей: рабочая футеровка и теплоизоляционное пространство. Так как для теплоизоляционной части не требуется высокая прочность, поэтому в качестве вяжущего компонента был использован портландцемент с тонкомолотой добавкой – ИМ-2201, являющейся отходом нефтехимической промышленности [2].
К числу эффективных теплоизоляционных материалов относятся ячеистые бетоны (пенобетон и пеносиликат). Однако обычный теплоизоляционный пенобетон не обладает свойством жаростойкости, вследствие чего он применим только для теплоизоляции агрегатов и конструкций с температурами, не превышающими 200°С.
В связи с этим изыскание новых видов пенобетона, обладающих повышенной жаростойкостью, является важной народнохозяйственной задачей.
107
Влабораторных условиях проведены эксперименты по получению жаростойкого пенобетона на портландцементе и глиноземистом цементе с тонкомолотыми огнеупорными добавками, которые были взяты из числа высокоглиноземистых отходов промышленности.
ВСамарской области в большом количестве на предприятиях нефтехимии образуется алюмохромистый тонкодисперсный порошок, являющийся отработанным катализатором в производстве синтетического каучука.
Также на Самарском металлургическом заводе образуется нанопорошок
ввиде шлама в процессе щелочного травления алюминиевого листа. Огнеупорность вышеперечисленных высокоглиноземистых отходов превышает 2000°С, поэтому рациональной областью их применения являются безобжиговые жаростойкие материалы (бетон, растворы и др.).
Вкачестве пенообразователя использовался пенообразователь ПБНС, который представляет собой водный раствор анионных поверхностноактивных веществ со стабилизирующими добавками.
Исследования показали возможность получения жаростойкого пенобетона малой плотности при достаточной прочности. Отрицательным фактором является большая усадка такого ячеистого пенобетона (около 1%).
Огневая усадка пенобетона может быть снижена введением в бетонную смесь мелкого огнеупорного заполнителя (легкого керамзитового песка и тяжелого – шамотного).
Получена широкая гамма по средней плотности жаростойкого пенобетона от 400 до 800 кг/м3. Температура применения такого теплоизоляционного материала колеблется в пределах 900-1100°С.
Врабочей части футеровки промышленных печей вместо штучных огнеупоров используют в настоящее время жаростойкие бетоны. Жаростойкий бетон на основе жидкого стекла при обжиге показывает увеличение прочности и не даёт усадки, что делает его более долговечным в рабочей части футеровки.
Втрадиционном составе используются шамотные заполнители, кремнефтористый натрий, жидкое стекло и огнеупорный наполнитель в виде тонкомолотого магнезита, что приводит к значительному увеличению стоимости продукции. В предлагаемом составе была произведена замена тонкомолотого магнезита на отработанный катализатор ИМ-2201. Введение этой добавки приводит к снижению стоимости. Кроме выше перечисленных компонентов в состав были введены алюминиевые опилки, способствующие огневому росту.
Полученную композицию возможно использовать в виде сухой смеси для ремонта футеровок тепловых агрегатов с температурой до 1350°С.
Для большинства тепловых агрегатов, где осуществляется процесс нагрева металлических заготовок, возможно использование жаростойких бетонов на гидравлических вяжущих, в частности, на портландцементе.
Внаших исследованиях был использован шлам щелочного травления алюминия – отход металлургии, взятый с Самарского металлургического
108
завода. Содержание самого тугоплавкого оксида Al2O4 в шламе достигает 8992%, поэтому введение такого компонента в жаростойкие композиции гидравлического и жидкостекольного твердения способствует также и повышению таких физикотермических показателей как температура применения и термическая стойкость.
В результате исследований был разработан состав тяжелого жаростойкого бетона на портландцементе, включающего отработанный катализатор ИМ-2201, шамотные заполнители и шлам щелочного травления алюминия в количестве 5-10% от массы цемента, что позволило повысить остаточную прочность после обжига до 800°С до 45-50%, а термическую стойкость увеличить до 15-20 водных теплосмен.
Литература
1.Хлыстов А.И. Повышение эффективности и улучшение качества огнеупорных футеровочных материалов: Монография. Самарск. гос. арх.- строит. ун-т. Самара, 2004.-134с.
2.Шипулин В.И., Горин В.М. Применение алюмохромового продукта в жаростойких бетонах. Сборник трудов ВНИИстрома. Снижение материалоемкости производства пористых заполнителей и бетонов на их основе. М., 1983.- 102-110с.
3.А.с. 130675 СССР, МКИ3 Кл 40А, 9. Печь для плавки цветных металлов и сплавов. В.С. Сасса, К.Д. Некрасов, Н.И. Графас (СССР); Бюл. № 5, 1970.
Е.А. Хмелькова
ИССЛЕДОВАНИЕ ПРОЦЕССОВ КОАГУЛИРОВАНИЯ
ВЗВЕШЕННЫХ ВЕЩЕСТВ
Самарский государственный архитектурно-строительный университет, г. Самара
Коагулянт сульфат алюминия — A12(S04)3*H20 на данный момент является самым распространенным в технологии очистки воды. Однако, все чаще приходится отмечать его малую коагулирующую эффективность и зависимость от внешних факторов, неподдающихся регулированию. Это и явилось причиной изыскания, разработки, исследования и внедрения новых видов коагулирующих реагентов. За последние 10-15 лет был предложен целый ряд новых коагулянтов и флокулянтов. Особое внимание в настоящее время уделяется следующим модификациям коагулянта последнего поколения — полиоксихлорида алюминия «АКВА-АУРАТ™»: 10, 14, 18, 30, 105, 170, «СКИФ™300», «СКИФ™18» и «СКИФ™180».
В состав коагулянтов «АКВА-АУРАТ™105» и «АКВА-АУРАТ™170», кроме полигидрооксихлорида алюминия, входят сульфат алюминия и полигидрооксихлорсульфат алюминия, находящиеся в строго определенных
109