
8_Sposoby_szhigania_organicheskogo_topliva
.pdf191
Для сжигания кускового торфа для котлов паропроизводительностью до 10 т/ч рекомендуются шахтные топки, а для котлов паропроизводительностью 10–230 т/ч – шахтно-цепные топки.
8.2. Сжигание в кипящем слое
Эффективное сжигание твердого мелкозернистого топлива (0–20 мм) может быть достигнуто при использовании принципа кипящего (псевдоожи- женного) слоя, применение которого при газификации топлива, в энергетике, черной и цветной металлургии, химической и нефтеперерабатывающей, строительной и других отраслях промышленности позволило резко интенсифицировать ряд технологических процессов.
Кипящий слой характеризуется скоростью первичного воздуха, превышающей предел устойчивости плотного слоя, но далеко не достигающей скорости витания средних частиц. При этих условиях все частицы в слое интенсивно перемешиваются, двигаясь колебательно вверх и вниз, причем в целом слой имеет относительно четкую верхнюю границу. Для кипящего слоя твердого топлива характерны повышенная его концентрация в объеме камеры горения, а также повышенная относительная скорость в слое, что создает благоприятные условия для скоростного горения топлива. В отличие от плотного (неподвижного) слоя, аэродинамическое сопротивление которого с увеличением интенсивности дутья возрастает по степенному закону, в кипящем слое сопротивление от этого фактора не зависит.
При малой скорости дутья слой остается неподвижным и работает как фильтрующий. При достижении критической скорости дутья сила давления газового потока в слое становится равной силе тяжести частиц. Слой начинает расширяться, и при дальнейшем увеличении скорости воздуха частицы приходят в движение. Объем слоя увеличивается в 1,2–1,8 раза в зависимости от интенсивности дутья, формы и размеров частиц. Сопротивление кипящего слоя с изменением интенсивности дутья не изменяется, потому что при этом увеличивается расстояние между частицами, т.е. увеличивается проходное сечение для газа. При чрезмерном увеличении скорости дутья весь слой переходит во взвешенное состояние и может быть вынесен из рабочей камеры.
Для кипящего слоя подобно жидкости характерен линейный закон паде- ния давления по его высоте. Давление (сопротивление) в кипящем слое пропорционально его высоте и плотности «кипящего» материала. В отличие от аэровзвеси, где относительная скорость частиц и газа приближается к нулю, для кипящего слоя в отдельные периоды (при падении частиц) она доходит до нескольких метров в секунду.
Впервые использование принципа кипящего слоя в топочном устройстве было начато в 1944 г. работами Московского энергетического института применительно к малореакционным мелкозернистым топливом (АШ, коксовая мелочь), а в последующем и к бурым углям.
192
Характерной отличительной особенностью топок МЭИ является двухступенчатая схема организации процесса горения. В качестве первой ступени топки используется кипящий слой, где проводится интенсивная и глубокая тепловая подготовка топлива: прогрев, подсушка и выделение высокотемпературных горючих газов. Второй ступенью топки является камера дожигания горючего газа, выдаваемого кипящим слоем, и содержащихся в нем частиц термически подготовленного уноса.
При работе таких топок на АШ в слой подают около трети воздуха, необходимого для полного сгорания топлива. Газообразование в кипящем слое происходит подобно газообразованию в плотном слое, однако кислородная и восстановительная зоны имеют увеличенные толщины. Температуру кипящего слоя поддерживают на уровне, исключающем плавление золы, во избежание шлакования слоя. Это может быть достигнуто установкой в слое охлаждающих поверхностей, рециркуляцией дымовых газов и др.
В нормально работающем кипящем слое оплавленного шлака не получается.
Относительно высокая и достаточно равномерная температура по высоте слоя (при работе на АШ около 1000 °С), благоприятные гидродинамические условия, определяемые повышенной относительной скоростью газа, и наличие достаточно развитой поверхности окисления мелкозернистого топлива обеспечивают высокую производительность кипящего слоя как первой ступени полугазовой топки. В рассматриваемых условиях выходящий из слоя горючий газ имеет температуру около 1000 °С и теплоту сгорания 1,7– 2,5МДж/м3. Видимая плотность теплового потока на дутьевую решетку составляет qR = 4,7–7 МВт/м2.
Вторую ступень топки для дожигания газа и выноса можно выполнить по различным вариантам. На рис. 8.27 показана компоновка однокамерной топки с кипящим слоем с водогрейным котлом; вторая ступень топки располагается непосредственно над слоем. Такая топка в производственных условиях работала на коксовой мелочи и подмосковном угле. Крупность топлива 0–20 мм. Тепловая мощность водогрейного отопительного котла около 5
МВт. При работе на коксовой мелочи ( Aр = 17,33%; W р = 19,85%) около 30% всего количества воздуха, необходимого для горения, поступает под решетку, имеющую живое сечение 3–4 %. Остальной воздух подается в топочную камеру над кипящим слоем через два ряда фурм. Необходимое охлаждение кипящего слоя топлива для осуществления бесшлаковочного режима (ϑ = 1000°С) достигается расположенными в кипящем слое водоохлаждаемыми поверхностями, включенными в систему циркуляции котла.
Коэффициент теплоотдачи от кипящего слоя к охлаждающей поверхности составляет около 250–400 Вт/(м2∙К). Был предусмотрен также впрыск воды непосредственно в кипящий слой для возможности регулирования его температуры в случае необходимости. При работе на подмосковном угле
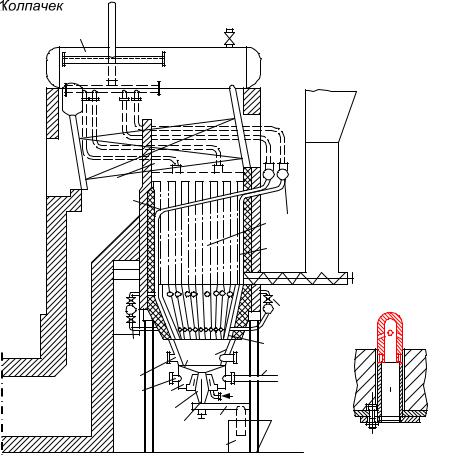
193
марки БМ ( Aр = 19,8%; W р = 33,84%) в слой подавалось около 50–60 % всего воздуха, температура слоя поддерживалась на уровне 900 °С.
Рис. 8.27. Компоновка топки с кипящим слоем с водогрейным котлом: 1 – топочная камера; 2 – конусная часть топки; 3 – дутьевая решетка; 4 – дутьевая коробка; 5 – камера дожигания выпавших частиц; 6 – шнек золоудаления; 7 – топливный шнек; 8 – шуровочный вал; 9 – экранные трубы; 10 – коллектор; 11 – барабан; 12 – конвективный пучок; 13 – топливная течка; 14 – фурмы вторичного дутья; 15 – бак с гидрозатвором для золы; 16 – подвод сетевой воды; 17 – подвод первичного дутья; 18 – подвод воздуха в камеру дожигания; 19
– зажигательный пояс
Поддержание желательной зольности слоя, исключающей его погасание и обеспечивающей небольшие потери от механического недожога с выгребом, осуществляется непрерывной или периодической «продувкой» слоя через выгребное устройство. Высота слоя в состоянии кипения поддерживается на уровне 600–800 мм. Необходимое давление воздуха под решеткой составляет 3400–3900 Па. При работе на коксовой мелочи расход топлива составляет около 0,3 кг/с, а при работе на подмосковном угле 0,5 кг/с. При этом видимая плотность теплового потока дутьевой решетки составляла qR = 4,8
МВт/м2 при объемной плотности тепловыделения на всю топочную камеру qV = 0,17МВт/м3.
На рис. 8.28 показаны некоторые другие варианты второй ступени топки с кипящим слоем. На схеме а – вариант однокамерной топки с кипящим
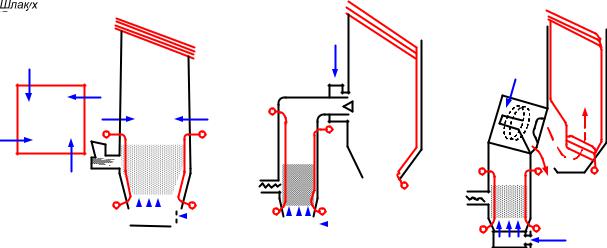
194
слоем, где для интенсификации сжигания выноса вторичный воздух подается тангенциально; на схеме б сочленение первой н второй ступеней двухкамерной топки осуществляется при помощи специальной турбулентной горелки; на схеме в в качестве второй ступени топки используется циклонная камера с жидким шлакоудалением.
|
|
|
|
|
|
|
|
|
|
|
|
|
|
|
|
|
|
|
|
|
|
|
|
|
|
|
|
|
|
|
|
|
|
|
|
а) |
|
б) |
|
|
|
|
|
|
|
в) |
|||||||
|
|
|
|
|
|
|
|
Рис. 8.28. Схемы организации второй ступени топки с кипящим слоем: а – топка с тангенциальным подводом вторичного воздуха; б – топка с турбулентной горелкой; в – топка с циклонной горелкой
В 50-х годах в СССР были построены и находились в эксплуатации три топки с кипящим слоем, показавшие возможность эффективного сжигания различных мелкозернистых топлив.
Особый интерес к организации сжигания топлив в кипящем слое вызван рядом обстоятельств. Для сжигания могут использоваться различные топлива, включая низкосортные, крупностью 0–20 мм. При этом значительно сокращаются расходы электроэнергии на топливоприготовление. Расположение поверхностей нагрева в кипящем слое, где коэффициент теплоотдачи составляет 200–300 Вт/(м2∙К), обеспечивает существенное снижение металлоемкости установки. Работа с относительно низкотемпературным слоем (800–1000 °С) приводит к значительному уменьшению загрязнения атмосферы соединениями серы, так как большая ее часть остается в слое и удаляется вместе с золой. Для повышения степени улавливания серы в кипящий слой может добавляться известь или доломит. Благодаря низкой температуре отходящие из кипящего слоя газы практически не содержат оксидов азота. Снижается также возгонка щелочных соединений золы топлива, что приводит к уменьшению загрязнения поверхностей нагрева.
Принципиальная схема котла с топкой кипящего слоя с размещением части поверхностей нагрева в слое показана на рис. 8.29. Предусмотрен возврат в топку уловленного выноса из кипящего слоя, содержащего обычно значительное количество невыгоревшего углерода. Возможна также схема с дожиганием выноса в специальном устройстве.
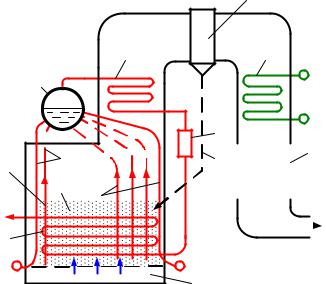
195
В настоящее время за рубежом и в России в эксплуатации находятся различные топки с кипящим слоем, в том числе для котлов большой паропроизводительности, а также работающие под давлением (до 1 МПа), что приводит к дальнейшей интенсификации процесса сжигания твердого топлива и улучшению технико-экономических показателей.
|
|
4 |
|
1 |
|
|
|
5 |
7 |
3 |
10 |
8 |
|
|
|
3 |
|
|
|
|
6 |
|
|
9 |
|
|
|
Наряду |
со |
сжиганием |
||
|
|
|
твердого |
топлива |
в |
кипящем |
||
2 |
|
|
слое |
может |
быть |
организовано |
||
|
|
высокоэффективное |
сжигание |
|||||
|
|
|
||||||
|
|
|
газового и жидкого топлив. Для |
|||||
|
|
|
этого |
над |
дутьевой |
решеткой |
||
|
|
|
создается |
кипящий |
слой из |
|||
|
|
11 инертного |
|
материала |
(песок, |
|||
|
|
|
||||||
|
|
|
кирпичная крошка и т. п.), в ко- |
|||||
|
|
|||||||
|
|
|
тором сжигается газ или жидкое |
|||||
|
|
|
топливо. В таком кипящем слое |
|||||
|
|
|
также |
могут |
быть |
установлены |
||
|
|
|
||||||
|
|
|
поверхности нагрева котла, что |
|||||
|
|
|
интенсифицирует |
теплопереда- |
||||
|
|
|
чу. |
|
|
|
|
|
Широкое распространение в промышленности находят также технологические топки с кипящим слоем, в частности для обжига различных серосодержащих материалов (колчедана, медных и цинковых концентратов и др.). Для поддержания температуры слоя на уровне, ис-
ключающем его шлакование, используют охлаждаемые элементы, располагаемые в кипящем слое и отнимающие избыточную теплоту. В этих элементах обычно вырабатывается пар.
В настоящее время внимание теплотехников привлекает циркулирующий кипящий слой, характеризуемый превышением второй критической скорости и приближением к режиму пневмотранспорта.
Этот вид топок используется для котлов тепловой мощностью от 20 до 500 МВт. Скорость в слое составляет 6–8 м/с, теплонапряжение поверхности слоя 7 МВт/м2, а расход электроэнергии на собственные нужды до 26 кВт/МВт.
С увеличением скорости ожижающей среды течение становится нестационарным и достигает границы пневматического транспорта. Твердые частицы при интенсивном перемешивании выносятся почти всеми продуктами сгорания из топки с кипящим слоем и возвращаются через золоулавливающие
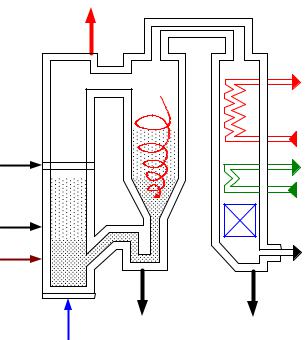
|
196 |
|
|
|
|
циклоны обратно в слой (см. рис. 8.30). При этом не образуется фиксирован- |
|||||
ный кипящий слой, а концентрация частиц в топке непрерывно падает от ре- |
|||||
шетки кипящего слоя до циклона. |
|
Горячая зола, отделенная |
|||
|
|
||||
2 |
|
в циклоне от продуктов сгора- |
|||
|
ния, частично возвращается в |
||||
|
|
||||
|
|
топку с кипящим слоем, а час- |
|||
|
3 |
тично направляется во внешние |
|||
|
|
охладители золы. Там она ох- |
|||
|
|
лаждается примерно на 400 °С |
|||
1 |
|
посредством погруженных теп- |
|||
4 |
лообменных поверхностей на- |
||||
|
|||||
|
|
грева и направляется обратно в |
|||
10 |
5 |
топку. |
За циклонами в потоке |
||
продуктов сгорания установле- |
|||||
|
|
||||
9 |
6 |
ны конвективные |
поверхности |
||
|
|
нагрева. |
|
||
7 |
7 |
Соотношение между зо- |
|||
лой, которая непосредственно |
|||||
8 |
|
из циклона возвращается в топ- |
|||
Рис. 8.30. Принципиальная схема котла с цирку- |
ку, и золой, охлажденной в ох- |
||||
лирующим кипящим слоем: 1 – вода; 2 – пар; 3 – |
ладителях, оказывает сущест- |
||||
пароперегреватель; 4 – экономайзер; 5 – воздухо- |
венное влияние на температуру |
||||
подогреватель; 6 – продукты сгорания; 7 – зола; 8 |
в топке: только при правильном |
||||
– воздух; 9 – топливо; 10 – присадки |
|
выборе |
этого |
соотношения |
|
можно обеспечить требуемую температуру (850 °С). Так как горячая возвра- |
|||||
щаемая зола практически не охлаждает слой, необходимо поддерживать по- |
|||||
вышенную циркуляцию золы. Следствием этого является хорошее выгорание |
|||||
топлива (почти 99%). С другой стороны, снижается расход электрической |
|||||
энергии на собственные нужды циркуляции (около 25 кВт/МВт). |
|
||||
Первый опыт работы котлов такого типа свидетельствует о том, что |
|||||
сжигание в циркулирующем кипящем слое в определенной степени нечувст- |
|||||
вительно к гранулометрическому составу топлива и риск пережога решетки |
|||||
кипящего слоя в результате падения крупных частиц топлива существенно |
|||||
меньший, чем у топок с обычным кипящим слоем. |
|
|
|||
Существенным недостатком топок с циркулирующим кипящим слоем |
|||||
является то, что оборудование, в котором циркулирует горячая зола (топка, |
|||||
циклоны, охладители), должно иметь соответствующую облицовку. Как пра- |
|||||
вило, нагрев не должен превышать 50 °С/ч, что приводит к длительному вре- |
|||||
мени пуска котла и к большому расходу благородных топлив при пуске. Из-за |
|||||
отсутствия опыта длительной эксплуатации котлов такого типа остается не- |
|||||
решенным также вопрос об износе отдельных его узлов. |
|
197
8.3. Выбор слоевых топок и основы их расчета
По действующим нормам слоевые топки целесообразно применять для котлов паропроизводительностью до 10 кг/с (35т/ч). Для установок большей производительности часто оказывается возможным применение как слоевых, так и камерных топок. В этом случае выбор способа сжигания решается на основе технико-экономических соображений.
Для сжигания в слое рекомендуются сортированные антрациты (АС и AM) и полуантрациты, а также грохоченые и рядовые каменные и бурые угли с содержанием мелочи от 0–6 до 60% с выходом летучих более 20%, кусковой торф, сланец, древесные отходы. Слоевые топки не рекомендуется применять для сжигания антрацитового штыба и рядовых антрацитов, тощих и бурых
высоковлажных углей с W п >> 3,35 %·кг/МДж, отходов углеобогащения и фрезерного торфа. Применение слоевых топок для указанных топлив не обеспечивает надежного и эффективного их сжигания. Слоевые топки с ручным обслуживанием допускаются для небольших паровых и водогрейных котлов паропроизводительностью до 0,3 кг/с (1 т/ч).
Для котлов паропроизводительностью до 1,8 кг/с (6,5 т/ч) при сжигании сортированных антрацитов АС и AM, каменных и бурых углей можно применять топки с неподвижной решеткой с опрокидными колосниками и пневмомеханическим забросом топлива. Длина колосниковой решетки должна быть при этом не более 3 м. Для котлов паропроизводительностью более 1,8 кг/с для сжигания антрацитов марок АС и AM рекомендуются топки с цепными решетками прямого хода, а для сжигания каменных и бурых углей – цепные решетки обратного хода с пневмомеханическими забрасывателями. Для сжигания сланца в котлах паропроизводительностью до 5,5 кг/с допускается применение топок с наклонно-переталкивающими решетками.
Для сжигания кускового торфа в котлах паропроизводительностью до 1,8 кг/с и древесных отходов в котлах паропроизводительностью до 2,8 кг/с рекомендуются простейшие шахтные топки с наклонной неподвижной решеткой, а для агрегатов большей производительности – шахтно-цепные топки с предтопками.
Работу слоевых топок характеризуют видимой плотностью теплового потока зеркала горения qR видимой объемной плотностью тепловыделения
qV коэффициентом избытка воздуха а, потерями теплоты от химической q3 и механической q4 неполноты сгорания. Допустимые значения qR и qV при слоевом сжигании различных топлив, а также значения α , q3 и q4 могут быть
приняты по [1].
Для выбранного способа сжигания топлива по указанным рекомендациям принимают значения qR = BрQнр R , qV = BрQнр
Vт , после чего по расходу
198
топлива Bр и его теплоте сгорания Qнр находят необходимые площадь зеркала горения R и топочный объем Vт .
При сжигании топлив на решетке за активную длину зеркала горения принимают: для топок с чешуйчатой цепной решеткой ТЧ – размер от регулятора слоя до наконечников шлакоснимателей, для топок с пневмомеханическими забрасывателями типов ТЧЗМ и ТЛЗМ – от фронтовой стенки до кирпичной кладки над задним колосником. Активная площадь решетки R равна произведению активной длины решетки на ее активную ширину. У топок с поворотными колосниками типа ЗП-РПК активная площадь решетки принимается равной площади поворотных колосников.
Высоту слоевой топочной камеры для котлов паропроизводительностью до 2,8 кг/с принимают 2,5–4 м, а для котлов производительностью 5,5– 9,7 кг/с – более 4 м.
8.4.Факельное сжигание пылевидного топлива
Вэнергетике при большой тепловой мощности паровых котлов, получил широкое распространение факельный метод сжигания топлив, т. е. сжигание поступающего из горелок топлива в свободном объеме топочного устройства, ограниченного экранированными теплоизолирующими стенами, в виде объемного факела с различной его аэродинамикой внутри топочного объема. Подобное топочное устройство называется топочной камерой, а сжигание топлива – камерным или факельным. Наиболее распространенные виды топочных камер для сжигания твердых топлив показаны на рис. 8.31.
Топочные камеры называются открытыми, если топочный объем имеет вертикальные плоские стены, как это показано, например, на рис. 8.31, а. Топочные камеры с пережимом получаются, когда одна или две стены на определенной высоте имеют выступ внутрь топочного объема (см. рис. 8.31, 6), который условно разделяет топку на камеру сгорания (объем, где в основном происходит горение топлива) и камеру охлаждения (объем топки с открытыми экранами, где завершается горение и в основном происходит снижение температуры газов за счет интенсивного теплообмена). В практике находят применение двухкамерные топки, когда обе камеры (горение топлива и камера охлаждения газов) разделены поверхностью нагрева или перемычкой с узким проходом (переходом). Примеры таких топочных устройств показаны на рис. 8.31, в.
По принципу вывода шлаков в нижней части топки топочные камеры разделяются на топки с твердым шлакоудалением (рис. 8.31, а) и жидким шлакоудалением (рис. 8.31, б, в). Двухкамерные топки с первоначальным циклонным способом сжигания топлив (рис. 8.31, в) сегодня применяются редко из-за технологической сложности выполнения топок, недостаточной эксплуа-
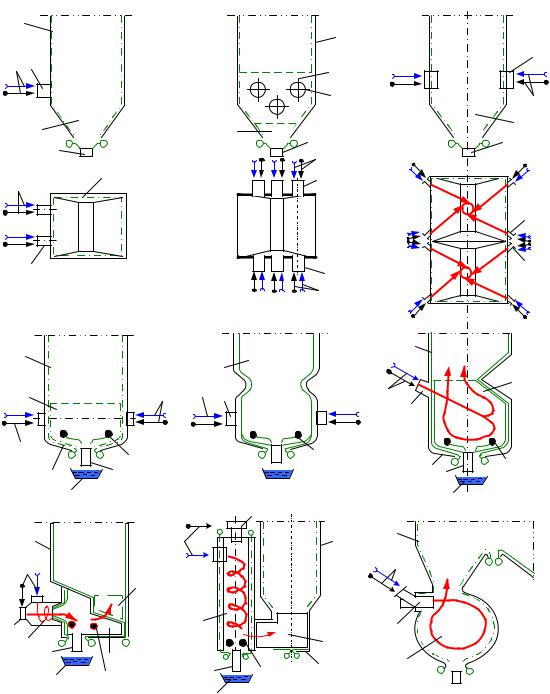
199
тационной надежности и повышенного образования вредных газов в зоне высоких температур горения.
1
|
1 |
4 2 |
3 |
|
2 |
9 |
11 |
|
9 |
11 |
|
|
|
||
|
|
|
4 |
|
|
|
1 |
|
|
4 |
|
|
2 |
|
|
|
|
2 |
2 |
|
4 |
|
2 |
|
4 |
|
9 |
4 |
11 |
|
2 |
|
2 |
1 |
|
|
|
|
|
|
1 |
|
|
|
3 |
|
|
|
|
|
|
|
|
|
|
|
|
|
8 |
|
3 |
4 |
4 |
2 |
|
|
|
4 |
|
|
|
|
|
|||||
|
|
|
|
|
|
|
2 |
|
4 |
14 |
|
13 |
|
14 |
|
|
|
|
|
|
|
|
14 |
|||
13 |
10 |
|
10 |
|
|
1310 |
||
|
|
|
|
|
||||
11 |
|
|
|
11 |
|
|
11 |
|
|
|
|
|
2 |
|
|
|
|
1 |
|
4 |
|
|
1 |
|
1 |
|
|
|
|
|
|
|
|||
4 |
|
|
|
|
|
|
4 |
|
|
3 |
|
|
|
|
|
|
|
2 6 |
|
6 |
|
|
|
|
2 |
|
|
|
|
|
7 |
|
|
||
|
|
|
|
|
|
|
||
10 |
7 |
10 |
14 |
12 |
|
5 |
|
|
11 |
14 а) |
б) |
|
в) |
||||
|
|
|
||||||
|
|
11 |
|
|
|
|
|
Рис. 8.31. Виды топочных устройств: а – однокамерные открытые с твердым шлакоудалением; б – однокамерные открытые и с пережимом для жидкого шлакоудаления; в – двухкамерные с циклонным методом сжигания топлива и жидким удалением шлаков; 1 – топочные экраны; 2 – горелка; 3 – зона утепленных (футерованных) экранов; 4 – подвод топлива и воздуха в горелку; 5 – вихревая камера горения; 6 – циклон; 7 – камера дожигания; 8 – гравитационный сепаратор топлива с открытой амбразурой в топку; 9 – холодная воронка; 10 – шлаковая летка; 11 – шлаковая ванна; 12 – горизонтальный охлаждаемый под; 13 – наклонный охлаждаемый под; 14 – выход жидкого шлака
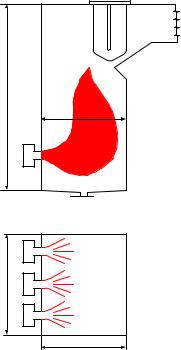
200
8.4.1.Основные размеры топочной камеры
ирасчетные тепловые напряжения
|
При конструировании топочной камеры ставится ряд условий, которым |
||||
она должна удовлетворять. Во-первых, топочная камера должна обеспечить в |
|||||
пределах ее объема наиболее полное сжигание топлива, так как за предела- |
|||||
ми топки горение топлива практически невозможно. Во-вторых, в пределах |
|||||
топочной камеры должно произойти охлаждение продуктов сгорания за счет |
|||||
отвода теплоты к экранам до экономически целесообразной и безопасной |
|||||
температуры на выходе из топочной камеры по условиям шлакования или |
|||||
перегрева металла труб. В-третьих, аэродинамика газовых потоков в объеме |
|||||
топочной камеры должна исключать явления и шлаковавания стен или пе- |
|||||
регрева металла экранов дельных зонах топки, что достигается выбором ти- |
|||||
па горелок и их размещением по стенам топочной камеры. |
|||||
|
Геометрически топочная камера характеризуется линейными размера- |
||||
|
|
ми: шириной фронта aт , глубиной bт и высотой hт |
|||
|
|
(рис. 8.32), размеры которых определяются тепло- |
|||
|
|
вой мощностью топки, тепловыми и физико- |
|||
|
|
химическими характеристиками топлива. Произ- |
|||
т |
|
|
|
2 |
сечение топочной ка- |
h |
bт |
ведение fт = aтbт , м , ecть, |
|||
|
меры, через которое с достаточно большой скоро- |
||||
|
|
||||
|
|
стью (7–12 м/с) проходят раскаленные топочные |
|||
|
|
газы. Ширина фронта топки паровых котлов элек- |
|||
|
|
тростанций составляет aт =9,5–31 м и зависит от |
|||
|
|
вида сжигаемого топлива, |
тепловой мощности |
||
|
|
(паропроизводительности) парового котла. С уве- |
|||
а |
|
личением мощности парового котла размер aт |
|||
|
растет, но не пропорционально росту мощности |
||||
т |
|
|
|
|
|
|
|
(см. рис. 8.33), характеризуя таким образом увели- |
|||
|
|
чение тепловых напряжений сечения топки и ско- |
|||
|
bт |
рости газов в ней. Оценочно ширину фронта aт , м, |
|||
|
можно определить по формуле |
||||
Рис. 8.32. Основные разме- |
|||||
ры топочной камеры |
a |
|
= m D0,5 |
(8.1) |
|
|
|
т |
|||
|
|
|
ф |
|
где D – паропроизводительность котла, кг/с; mф – числовой коэффициент,
изменяющийся от 1,1 до 1,4 с ростом паропроизводительности.
Глубина топочной камеры составляет bт = 6–10,5 м и определяется
размешением горелок на стенах топочной камеры и обеспечением свободного развития факела в сечении топки так, чтобы высокотемпературные языки факела не оказывали давление на охлаждающие настенные экраны. Глубина топки