
Термореактивные полимеры
Фенолоформальдегидные смолы представляют собой продукты поликонденсации фенолов с формальдегидом. Выпускаются смолы ре-зольного и новолачного типа. Резольные смолы отверждаются путем нагревания, новолачные - при нагреве с отвердителем (уротропином, 6...14 % массы смолы). Фенолоформальдегидные смолы обладают высокими атмосферо- и термостойкостью, хорошими электроизоляционными свойствами, стойки к действию большинства кислот, за исключением концентрированной серной кислоты и кислот-окислителей (азотной, хромовой). Неотвержденные смолы растворимы в фенолах и растворах едких щелочей, а также в органических растворителях.
Эпоксидные смолы - олигомеры или мономеры, способные превращаться в полимеры пространственного строения посредством от-вердителей, в качестве которых могут использоваться мономерные, олигомерные и полимерные соединения различных классов.
Для холодного отверждения эпоксидных смол применяют в качестве отвердителей алифатические полиамины (полиэтиленполиа-мин, гексаметилендиамин, 5...15 % массы смолы). Длительность отверждения 24 ч (степень отверждения до 70 %). Для повышения степени отверждения желательна термообработка при температуре 60...120 °С в течение 12...2 ч. Применяются для отверждения также олигоаминоамиды, но в количестве 50...100 % массы смолы.
Для горячего отверждения применяют ароматические ди- и полиамины (15...50 % массы смолы). Отверждение проводят при температуре 100...180 °С в течение 16...4 ч. Прочность, химическая стойкость и теплостойкость эпоксидных компаундов при горячем отверждении выше, чем при холодном. Используют в качестве отвер-дителей также ангидриды дикарбоновых кислот и синтетические смолы (фенолоформальдегидные, мочевино- и меламиноформальдегид-ные и др.).
Эпоксидные смолы обладают высокой адгезией к металлам, стеклу, керамике и другим материалам. Отвержденные смолы имеют хорошие диэлектрические свойства, высокую химическую стойкость, исключая органические кислоты, кетоны и углеводороды, стойки к воздействию радиоактивного излучения.
Кремнийорганические полимеры отличаются высокой термостойкостью, стойкостью к воздействию агрессивных сред, хорошими диэлектрическими свойствами, однако обладают невысокой адгезией. Для повышения адгезионных свойств их модифицируют эпоксидны
ми, фенольными и полиэфирными смолами. Наиболее широкое применение для производства композиционных материалов, лаков, эмалей и клеев из кремнийорганических полимеров получили полиорга-носилоксаны.
Механические свойства ряда отвержденных термореактивных смол и кремнийорганических полимеров приведены в табл. 10.3.
10.4. Композиционные материалы
Композиционные материалы (композиты) представляют собой ге-терофазные системы, состоящие из двух и более разнородных компонентов, имеющих границы раздела между ними. Компонент, непрерывный по всему объему материала, обеспечивающий его монолитность, называется матрицей, или связующим. Компоненты, распределенные в матрице, называются наполнителями.
Наполнители в композиционные материал вводят с целью улучшения механических, теплофизических, электрических, магнитных и других свойств. В качестве наполнителей используют твердые, жидкие и газообразные вещества органического и неорганического происхождения.
В зависимости от характера взаимодействия наполнителя с материалом матрицы их подразделяют на инертные и активные (упрочняющие). Механизм взаимодействия матрицы с наполнителем определяется химической природой этих материалов и состоянием поверхности наполнителя. Наибольший эффект усиления достига-
ется при возникновении между наполнителем и материалом матрицы химических связей или значительного адгезионного взаимодействия. Наполнители, способные к такому взаимодействию с матрицей, называются активными. Инертными называются наполнители, не способные к этому взаимодействию. Последние применяют для облегчения переработки или снижения стоимости изделий.
По виду и структуре наполнителя композиты делятся на дисперсно-упрочненные, упрочненные волокнами, слоистые и газонаполненные.
В качестве дисперсных наполнителей широкое применение получили: древесная мука, сульфатная целлюлоза, графит, тальк, слюда, каолин, диоксид кремния, силикаты алюминия, кальция, магния, порошки металлов и сплавов. Некоторые металлические наполнители придают композитам специфические свойства. Например, железо и его сплавы - ферромагнитные; чешуйки алюминия, никеля, серебра -низкую газо- и паропроницаемость; порошки алюминия и меди - декоративность; свинца, кадмия, вольфрама - защитную способность при воздействии излучений высоких энергий.
Дисперсно-упрочненные композиционные материалы с равномерно распределенным в объеме материала наполнителем обладают изотропностью свойств, т. е. одинаковыми свойствами во всех направлениях. Для создания материалов антифрикционного назначения широко используются слоистые твердые смазки Мо82, Мо8е2, BN, СсЮ, СаБ2, графит и др., а также жидкие наполнители - минеральные масла.
В качестве волокнистых наполнителей используют хлопковые и льняные очесы, стекловолокно, асбест, углеродное волокно. Все более широкое применение получают синтетические волокна, в частности, полиамидные и полиэфирные. Пластмассы, содержащие синтетические волокна, характеризуются высокой коррозионной и химической стойкостью, малым коэффициентом трения и высокой износостойкостью, однако обладают низкой теплостойкостью (рис. 10.10). Современные композиционные материалы содержат в качестве наполнителей угольные и графитовые волокна, волокна бора и др.
Упрочненные волокнами материалы анизотропны, кроме случая хаотического расположения волокон. Упрочняющий эффект при наполнении волокнами диаметром 3...12 мкм сказывается уже при их длине 2... 4 мм, благодаря взаимному переплетению и снижению напряжений в связующем. С увеличением длины волокон увеличиваются прочность и ударная вязкость. В свою очередь, упрочняющие волокна в композитах
могут быть дискретными и непрерывными, а непрерывные волокна могут быть однонаправленными или направленными в разные стороны.
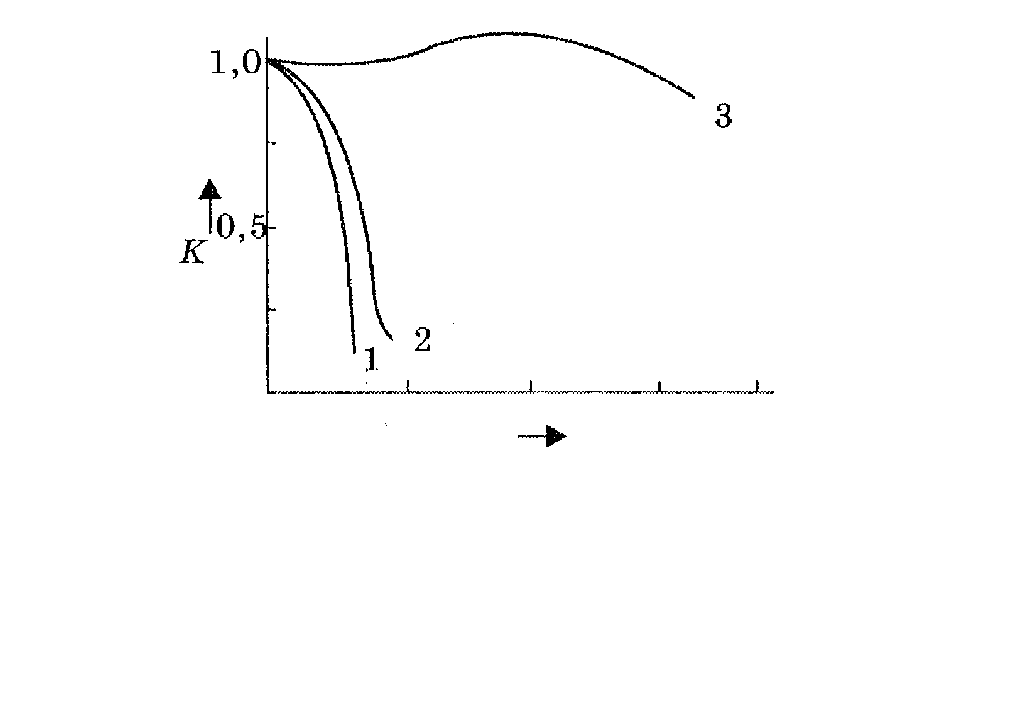
Из
слоистых
наполнителей применяются:
бумага (для получения гетинакса);
хлопчатобумажная ткань, стеклоткань,
асботкань, уг-леграфитная ткань (в
различного рода текстолитах); древесный
шпон (в древопластиках). Слоистые
(двухмерно-армированные) композиты
представляют собой набор слоев из
одинаковых или разных армирующих
материалов, пропитанных связующим.
Слоистые материалы отличаются анизотропией свойств: имеют высокую прочность при растяжении вдоль слоев армирующего наполнителя и низкую в перпендикулярном направлении. Этот недостаток отсутствует у объемно-тканых, или трехмерно-армированных материалов.
При создании поро- и пенопластов используют газообразные наполнители (углекислый газ, азот, воздух и инертные газы).
Различные сочетания матричного материала и наполнителя позволяют получать гибридные композиты с широким диапазоном характеристик, чего невозможно достичь на металлах и сплавах. Композиты выгодно отличаются от металлических сплавов своими удельными характеристиками: удельной прочностью ав / р и удельным модулем упругости E / р.
Композиты на основе полимерной матрицы обеспечивают работоспособность изделий при температурах до 200...300 °С, металлокомпозиты на основе алюминия и магния, армированные углеродными, борными и другими волокнами - до 400...500 °С. Керамические композиты на основе карбидов или нитридов кремния могут работать при температурах до 2000 °С.
Особенностью композитов является удачное сочетание высокой прочности с низкой плотностью и высокой химической стойкостью. Кроме того, в композитах зачастую в 10...100 раз ниже скорость распространения усталостных трещин, что обеспечивает большую долговечность изделий. Например, в слоистом материале алор на основе алюминиевых сплавов и органопластов скорость распространения усталостных трещин в 10 раз ниже, чем в алюминиевых сплавах. Удельная прочность и удельный модуль упругости композитов в 3...4 раза выше, чем сталей.
В настоящее время широкое применение получили стеклопластики, на смену которым приходят органопластики, в которых используют армирующие арамидные волокна, в частности, кевлар. Эти волокна при плотности 1500 кг/м и временном сопротивлении 4000...5000 МПа способны поглощать вибрации и ударные нагрузки. Из таких материалов изготавливают различные элементы конструкций в авиационной и космической технике, в судостроении.
Весьма перспективны углепластики, отличающиеся высокой радиационной стойкостью, тепло- и морозостойкостью, термостойкостью, термостабильностью свойств и геометрических размеров, высокой усталостной прочностью (в 1,5...2 раза выше, чем у стали, и в 8...9 раз - чем у алюминия). Применение углепластиков позволяет увеличить эксплуатационный ресурс в 1,5...2 раза, снизить массу конструкции на 20...25 % и трудоемкость производства изделий.
Углерод-углеродные композиты выдерживают температуру до 2500 °С, однако они хрупкие. Высокую термостойкость, жесткость, прочность, но и хрупкость имеют композиты на основе керамики. В качестве матрицы в керамических композитах используют оксиды алюминия, магния, циркония, нитриды бора и алюминия; упрочняющей фазой служат короткие волокна-усы и длинные термостойкие волокна. Такие материалы перспективны в авиации, ракетной технике, автомобилестроении, энергетике.