
Yang Fluidization, Solids Handling, and Processing
.pdf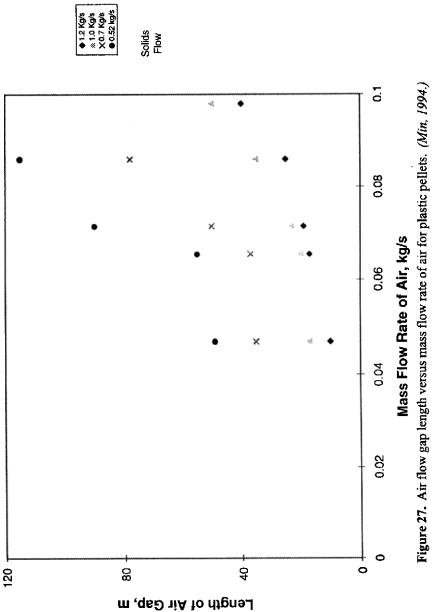
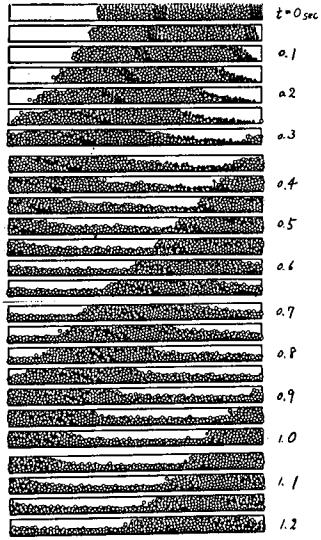
Dense Phase Conveying 707
There are several researchers who have addressed this operation. Of particular note is the modeling of Yang (1988) and the analysis of Knowlton (1994) for particularly large diameter units. Yang presented a model that describes the dynamics of a circulating fast fluidized bed. The dilute phase region was correlated with a set of equations he previously developed for this type of flow. The pressure drop in the dense phase with an annular region is given as
Eq. (17) |
P = ρ p (1− εave )L |
with the solids inventory in this region as
Eq. (18) |
I = ρ p (1 − ε ave )Ar L |
The height of the dense phase L is obtained by a pressure balance around the complete circulating fluidized bed loop. Good agreement is seen with this model and the existing data in the field.
Knowlton has cautioned on the difference between small diameter and large diameter systems for pressure losses. The difference between these systems is especially apparent for dense phase flow where recirculation occurs and wall friction differs considerably. Li and Kwauk (1989, 1989) have also studied the dense phase vertical transport in their analysis and approach to recirculating fluid beds. Li and Kwauk’s analysis included the dynamics of a vertical pneumatic moving bed upward transport using the basic solid mechanics formulation. Some noncircular geometries were treated including experimental verification. The flows have been characterized into packed and transition flows. Accurate prediction of the discharge rates from these systems has been obtained.
Vertical pneumatic moving bed transport was also explored with a theoretical and experimental study by Li and Kwauk (1989). A criterion was put forth for stable operations which include absence of bubbles, slugs and voidage pockets, and having a constant mean particle velocity. There should be a means of suppressing fluidization and bubbling and sufficient hydrodynamic drag to permit lower-layer particles to be lifted to the upper layers. With a pressure drop of 1.5 times that to overcome gravity, the critical pneumatic moving-bed transport can occur.
708 Fluidization, Solids Handling, and Processing
Li (1994) has also studied the mechanics of arching in moving-bed standpipe flow. He was able, for this downflow situation, to obtain the critical arching span which agrees with reported data. The critical or minimum radius Rc for no arching is given as
|
|
|
|
|
|
|
|
|
|
|
|
|
|
|
Eq. (19) |
Rc |
= |
|
|
f c sin 2β ' |
|
|
|
|
1 |
||||
|
|
|
|
|
|
|
|
|
|
|
[ρb g + P/ h] |
|||
[1− k |
|
(1+ sin δ ) |
|
sin 2β ' |
] |
|||||||||
|
|
|
|
|
||||||||||
|
|
|
|
+ cos2β sin δ ) |
|
2 tanδ |
|
|||||||
|
|
(1 |
|
|
|
|
6.0BOOSTERS
The topic of boosters is often seen as either the salvation or demon of dense phase transport. The design of the appropriate placement of booster is still evasive. Often too many boosters are utilized such that the overall gas usage turns out to have a dilute phase system. The Waeschle Company has designed a unique booster system that has individual controls. This design can handle most situations; for example, if a long plug forms by the union of two plugs or other flow hindrances, the system responds by injecting air to assist in the transport. This action breaks the plug into more manageable plug lengths. Overall care must be taken in using the boosters. Boosters can help in the conveying of a variety of difficult materials. When the flow causes stresses to be built up at bends and other stress points, the proper application of a booster can provide the added air to permit troublefree conveyance. One needs to remember that a particular booster application that worked for one material will probably not work for another.
Secondary air injection for the transport of solids has seen little analysis in the literature despite the prevalence of this technology in industry. One exception is the recent work of Dhodapkar et al. (1995). This analysis employs the use of a sizable pilot unit for developing operational guidelines for Geldart type B and D, free flowing, plastic pellets and granular polymers. Booster air was shown to lower the average velocity, permit higher operating pressures, and reduce the unstable operation of the system. Pressure fluctuations were significantly reduced for the Geldart type B material when using boosters. They also found that flow can be initiated successfully in a full line at lower conveying pressures with booster air injection.
Dense Phase Conveying 709
NOTATIONS
A |
- Area |
C |
- Internal cohesion coefficient |
c´ |
- Cohesion coefficient |
cw |
- Wall cohesion coefficient |
D |
- Diameter of pipe |
dp |
- Particle diameter |
F |
- Stress at the front of the plug |
fs |
- Solids friction factor |
Fr |
- Froude Number |
g |
- Gravity constant |
K |
- Coefficient of internal friction (1-sin2f)/(1+sin2f) |
Kw |
- Coefficient of internal friction at the wall |
l |
- Length of sector at failure |
L |
- Length of plug or transport distance |
n |
- Number of plugs in the pipeline |
P |
- Pressure |
R |
- Gas law constant |
T |
- Temperature |
Ug |
- Superficial velocity |
Uf |
- Fluid velocity |
V- Volume
W- Solids flux
z - Distance
Greek
α- Angle of inclination
ε- Voidage
φ- Angle of internal friction
φw |
- |
Angle of wall friction |
θ |
- |
Sector angle at failure |
ρ- Gas density
ρb |
- Bulk density |
|
ρp |
- |
Particle density |
σ |
- |
Normal stress |
τ- Shear stress
τw |
- |
Wall shear stress |
μL |
- |
Solids loading |
sinω ~ sinφw/sinφ
710 Fluidization, Solids Handling, and Processing
Subscripts
C1 |
- section at failure |
i |
- integer, interfacial |
sp |
- plug |
T |
- total |
w |
- wall |
z |
- distance |
REFERENCES
Arnold, P., Personal communication (1992)
Aziz, Z. B., and Klinzing, G. E., “Plug Flow Transport of Cohesive Coal: Horizontal and Inclined Flows,” Powder Tech., 55:97–105 (1988)
Aziz, Z. B., and Klinzing, G. E., “Dense Phase Plug Flow Transfer: The 1-inch Horizontal Flow,” Powder Tech., 62:41–49 (1990)
Borzone, L. A., and Klinzing, G. E., “Dense Phase Transport: Vertical Plug Flow,” Powder Tech., 53:273 (1987)
Destoop, T., “Mathematical of Dense Phase Conveying Systems - A Revolutionary Move Towards ‘Smart’ System Control,” Proc. of 1994 Bulk Solids Handling Conf., Rosemont, IL (1994)
Destoop, T., and Russell, B., Proceedings of the Fluidization and Particle Systems Sessions of AIChE Annual Meeting, pp. 351–355, Miami, FL (1995)
Dhodapkar, S. V., Jacob, K., and Merrick, D., Proc. of the Fluidization and Particle Systems Sessions of AIChE Annual Meeting, Miami, FL (1995)
Dhodapkar, S. V., Personal communications (1991)
Gu, H., and Klinzing, G. E., “Vertical Plug Flow of Cohesive Coal in 2- and 4- Inch Pipes,” Powder Tech., 57:59-67 (1989)
Knowlton, T., “The Effect of the System Pressure/Pipe-Diameter/Mass Flux Interaction on Pressure Drop in Dilute Phase Pneumatic Conveying,” Proc. of Pneumatic Conveying Workshop, Powder Technol. Forum, AIChE, Denver (1994)
Konrad, K., “Dense Phase Pneumatic Conveying: A Review,” Powder Tech., 49:1
(1986)
Konrad, K., Harrison, D., Nedderman, R. M., and Davidson, J. F., Proc. of Pneumotransport 5, Paper E1, BHRA, p. 225, Cranfield, Bedford, UK (1980)
Dense Phase Conveying 711
Legel, D., and Swedes, J., “Investigation of Pneumatic Conveying of Plugs of Cohesionless Bulk Solids in Horizontal Pipes,” Bulk Solids Handling, 4(2):53– 59 (1984)
Li, H., “Mechanics of Arching in a Moving-Bed Standpipe with Interstitial Gas Flow,” Powder Tech., 78:179–18 (1994)
Li, H., and Kwauk, M., “Vertical Pneumatic Moving-Bed Transport - I. Analysis of Flow Dynamics,” Chem. Engr. Sci., 44:249–259 (1989)
Li, H., and Kwauk, M., “Vertical Pneumatic Moving-Bed Transport - II. Experimental Findings,” Chem. Engr. Sci., 44:261–271 (1989)
Lippert, A. “Die Staub-Luft-Forderung Pulvern und Schuttgutern mit hohen Konzentrationen im Gasstrom-ein neuer Fordergang,” Dissertation TH. Univ. of Karlsruhe (1965)
Marcus, R. D., Rizk, F., Klinzing, G. E., and Leung, M., “Pneumatic Conveying of Solids,” Chapman Hall (1990)
Mathur, M. P., and Klinzing, G. E., “The Dense and Extrusion Flow Regime in GasSolid Transport,” Can. J. of Chem. Engr., 59:590–594 (1981)
Molerus, O., and Siebenhaar, W., “Vibration Induced Pneumatic Conveying,” Pneumatech IV, p. 213, Glasgow, Scotland (1990)
Min, B., “Ph.D. Dissertation, University of Wollongong, Australia (1994)
Paul, K. D., “Dense Phase Pneumatic Conveying Improving Efficiency,” Powder and Bulk Engr., p. 41 (1991)
Peng, X., Tomita, Y., and Tashiro, H., “Effect of Particle-Particle Collision and Particle Rotation upon Floating Mechanism of Coarse Particles in Horizontal Pneumatic Pipe,” JSME Intl. J., Series B., 37(3):485–490 (1994)
Plasynski, S. I., Dhodapkar, S. V., and Klinzing, G. E., Powder Tech., 81:3–7 (1994)
Sinclair, J., Proc. of Pneumatic Conveying Workshop, Powder Technology Forum, AIChE., Denver (1994)
Stegmaier, W., Fordern und Heben, 28:363 (1978)
Tsuji, Y., Tanaka, T., and Ishida, T., “Graphic Simulation of Plug Conveying,”
Proc. of Pneumatech, 4:39–50 (1990)
Weber, M., ”Stromungs-Foerdertechnik,” Krausskopf Verlag, Mainz (1973)
Welschof, G., ”Pneumatische Forderung bei Grossen Fordergutkonzentrationen,” VDI-Forschungscheff, p. 492, VDI Verlag, Dusseldorf (1962)
Wen, C. Y., and Simons, H. P., AIChE J., 6:263–8 (1959)
Wirth, K. E., and Molerus, O., “Critical Velocity and Pressure Drop for Horizontal Flow,” 9:156–166 (1986)
Yang, W. C., “A Model for the Dynamics of a Circulating Fluidized Bed Loop,”
Second Int. Conf. on Circulating Fluidized Bed, Compiegne, France (1988)
